
Alice Lee's story - why lean learning and teaching coexist
PROFILE – While pioneering the application of lean thinking in healthcare, Alice Lee realized that you should always approach teaching as you do problem solving: scientifically, situationally, and with the humility of a learner.
Profile on: Alice Lee, Executive Director, Lean Enterprise Institute
Words: Roberto Priolo, Editor, Planet Lean
In the fall of 2004, Alice Lee was driving around New England, “cold calling” a number of manufacturing firms. Her CEO at Beth Israel Deaconess Medical Center in Boston had asked her to take on a new role and improve the productivity of the medical center. She was completely at a loss with what that meant until she learned from her network of colleagues that high-performing companies in non-healthcare sectors were using something called lean or Toyota Production System to improve their productivity. She had never heard anything about these, but hoped to learn more through her visits.
At the time, Lee had just moved into the newly created role of Special Assistant to the President and realized how daunting her new assignment would be. “The constraints were many and I was, frankly, very concerned,” Lee admits. “The organization was in serious financial trouble, productivity was very low and the CEO noted that there was little business process thinking to improve things. He thought I was the right person to bring some structure to our operations, even though I saw myself as ‘an IT person.’ I was stunned but excited and accepted this assignment.”
Lee gave herself 30 days to research business improvement methods and understand her options. With only her thinking and experience to rely upon, Lee decided to pick up the phone and contact her former colleagues at Ernst & Young, where she had worked as a management consultant for two and half years between 1996 and 1998.
Certain themes came out of those conversations, and six sigma, the Toyota Production System, and lean kept flowing to the top. Lee immediately thought six sigma would have too steep a learning curve and knew she wouldn’t have the time to learn and teach it all given the mandate to act quickly, so she decided to go for what she then thought was the easiest route: lean. Little did she know!
“Try to google lean healthcare today and you will get thousands of results, but back then there was nothing: applications of the thinking methodology in hospitals and clinics were almost unheard of,” Lee recalls.
“I felt the urge to go see this ‘lean’ in action,” Lee explains. “I wanted to visit companies that were applying lean principles in earnest, but there were no hospitals I could go to, or at least I didn’t know of any. So I started to reach out to manufacturing organizations all around New England. Some of them thought I was crazy when I told them I wanted to bring lean to healthcare, but some of them were intrigued and happy to let me in.”
Upon entering those factories Lee was surprised to notice that she was able to understand the processes right away, despite having never worked in a manufacturing environment. The artifacts those organizations were using, like production cells for example, resonated with her and the people that had enthusiastically agreed to help her had become her teachers. Ironically, over time, as her teachers joined her on problem solving teams in her organization, they also became students as Lee taught them the language and processes in healthcare.
Lee says: “I was so surprised to see how calm things were on the shop floor, and I couldn’t believe how clean many of these places were! There was no chaos – something we are used to in healthcare – and it felt like things were predictable. More than anything else, it was great to see supervisors out in the field supporting and assisting their teams as problems came up. That I could understand what was going on was incredible to me! Visiting those manufacturing firms was my big breakthrough moment.”
WRITTEN IN THE STARS?
It is no coincidence that Lee ended up becoming a lean leader. Never afraid of trying new things, over the years she went from one step into the unknown to another. These included abandoning IT for business improvement at Beth Israel Deaconess Medical Center, but also – earlier in her career – taking on a large federal project to design a bespoke electronic medical record system for public hospitals for veterans.
“I have a track record of taking on things that are a bit scary with unknown pathways. I find that very exciting and it energizes me to be part of making things much better for people who deserve much better. That gives me impetus to get started and just try,” she explains.
Lee’s approach has always been very practical, which also explains why her studies at Northeastern University were in laboratory science: out of all the lab fields, microbiology is perhaps the most hands-on and head-on, which Lee enjoyed immensely.
After her work with federal programmers to design a new IT system, Lee joined Ernst & Young LLP. The management consulting firm found her curiosity and her ability to work at both the front line and with executives of great interest, and recruited her. That’s when her career as an IT consultant and coach really began.
Lee says: “I am really fortunate I had that experience. Working for E&Y is really like getting an applied MBA, and some of the smartest people I have ever met worked there. Even though their approach to consulting is quite traditional compared to what lean coaches tend to do – E&Y consultants are very much seen as the ‘experts’ going into a firm to help it fix its problems – I learned a great deal during my time there. In particular, I learned how see the whole system and to break problems down.”
Lee’s experience at E&Y proved very valuable, especially when she was tasked with implementing and integrating more than a hundred IT systems within Beth Israel. The secret to success here was visually depicting the layers of the processes: using see-through sheets laid on top of each other, Lee was able to show why things didn’t flow in the organization. “Most work is not designed, but layered! People often don’t see this, so I tried to show a 3D model of why processes were bottlenecking everywhere,” Lee states.
During her time as VP of Information System at Beth Israel, Lee confidently directed a number of Medical Center-wide projects and oversaw all aspects of clinical systems – design, R&D, project planning, systems selection, implementation and conversion, training, and support. A defining moment for Lee was when all IT systems went down for days in the fall of 2002 – one of the worst healthcare IT crises in history. The entire hospital had to revert to manual processes for days and operated as if it was 1978 again, pre-computer age. Lee played an integral role in ensuring patient care continued as key processes had to move back to paper.
GIVING UP IS NOT AN OPTION
The leap of faith she took when she moved away from IT and into business improvement proved more difficult than anything else Lee had done until then.
Despite her best effort, she encountered a lot of resistance and trying to bring lean to a large organization by herself seemed impossible. Despite some early success and a satisfied senior team, in 2007 she was ready to give up and quit her job.
The truth is that nobody can do this alone, which is the exact same thing author and publisher Norman Bodek told Lee when she met him at the International Shingo conference, where they were both speaking.
“At lunch, Norman told me that what I was doing was very important for healthcare and also for my own learning, and urged me not to give up,” Lee recalls. “He invited me to go to Japan on a lean study group, which I did. It was a wonderful learning experience, which pushed my thinking and reinvigorated me. I came back to Boston and explained to the CEO that if lean was to work he, as CEO, would have to own it.”
With the CEO’s support, Lee developed a course for the executive leaders, including the physician executives from Harvard Medical School. She invited 12 executives to the first class, including the CEO, COO, and several physician chairs from the medical school.
“That became one of my biggest accomplishments at Beth Israel,” continues Lee. “We got all senior leaders, administrators and physicians to participate in hands-on, practical training on the concepts and principles of lean while provoking them to think and learn together. As a teaching hospital, this approach was a natural extension of our education mission.”
Every week included visible gemba activities for these executive leaders, which sent a strong message that lean thinking and practice was important to top management and the organization. On one of the sessions, the exercise was for these executive lean students to learn why it took so long to get lunch at the Medical Center – a flow exercise. “We went to the cafeteria to grasp the situation and staff couldn’t believe their eyes when they saw a physician chief behind the counter with the meatloaf. It was a very humbling and special moment,” Lee recalls.
As the executives learned and practiced lean, they started to change how they ran the business. Lee’s determination and desire to try new things had once again paid off.
BECOMING A TEACHER
These days, Lee works as Executive Director of the Lean Enterprise Institute and seems to have completely embraced her role as a lean teacher and coach. Over the years, she has taught lean thinking to executives and physicians in the United States, Australia, England and Egypt. She is also a coaching faculty at Fisher College of Business at Ohio State and sits on the Strategic Advisory Board of the Worcester Polytechnic Institute.
If becoming a good leader is difficult, however, becoming a good lean leader is an even harder task because it entails learning how to teach and coach people.
Lee explains: “My training style is always based on the idea of understanding the learner’s perspective. If you have 12 of your top leaders in a class, they are bound to feel vulnerable and you need to account for the fact that they might be feeling threatened by you trying to teach them something. I consider learning situational and that must be kept in mind when teaching: I worry when I see teachers not adapting their styles to the students sitting in front of them.”
A teacher must honor what has been learned before, according to Lee, and build a bridge to that learning with the person they are developing.
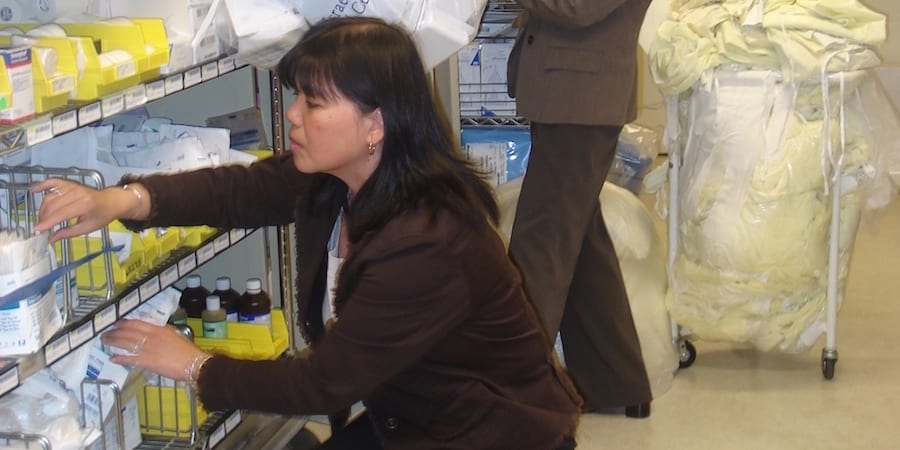
When she first introduced lean at Beth Israel Deaconess Medical Center, Lee experienced a certain level of resistance. In particular, it was hard for senior physician leaders to trust a non-physician to teach them, and they worried that that this new methodology was nothing but a way to try and get them to see more patients in the same time.
Lee acknowledged their doubts and tried to build a relationship with her students, rather than imposing a new way of thinking. She didn’t talk about A3s, but asked them how they normally solve a problem when a patient shows up with a mysterious illness.
“I listened to them, and later explained that A3 thinking is exactly what physicians do when they assess and treat a patient. ‘You are natural lean thinkers, ’ I told them, and then they got it,” Lee says.
But building that bridge is not always a smooth process, and some commotion is to be expected. One time Lee was working with a Department, with a Chief who was very critical of what she was trying to do and thought lean was “unscientific.”
One of the department’s main issues was an abnormally high number of blood specimen defects (the red cells tended to burst before they reached the laboratory). Lee worked with the team to approach the problem scientifically, as you do when you are a lean thinker, and they realized that its root-cause was the way some nurses were drawing blood.
She recalls: “At one point, the chief was sharing his nonbelief that we could solve this ‘unsolvable’ problem. The department had been experiencing that problem for 30 years, and he couldn’t understand how we could possibly fix it. I kept calm and explained that the faulty blood tests were keeping patients in the area for an extra 70 minutes on average. For him to be able to connect that problem with one of his business goals was a revelation, and he suddenly understood what lean is all about. He then became a staunch supporter of the methodology and ended up creating his own lean team led by an attending physician! Watching that transition was fascinating and rewarding. You have to respect the learning and change process for each individual.”
Lee’s incredible ability to communicate lean effectively becomes even more extraordinary when one considers that, at least at the beginning, she had no one to talk to and nowhere to turn to as she learned how lean could be applied to and taught in an environment as complex as healthcare.
Yet, Lee believes that she was lucky she had no one to follow. At a time when everyone is looking for the “secret sauce” for business success, Lee benefits from the invaluable experience she gained while having to stay the course and find ways to understand something as complicated and nuanced as lean almost entirely by herself.
“I am a very curious person, and I think lean works with my personality,” she concludes. “When you think about something in a lean framework, you are always in discovery mode, and I love that. I love being able to constantly learn while I teach, and lean is one of the few areas where you can do both things at the same time.”
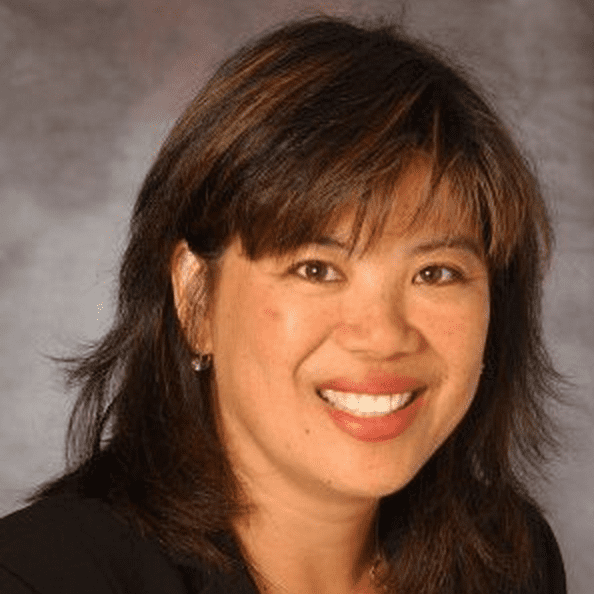
Alice Lee has been a leader in the lean healthcare community for over 10 years, most recently leading transformations in Systems, Technology, and Operations at Beth Israel Deaconess Medical Center in Boston. Alice is Executive Director of Lean Enterprise Institute and a leader-teacher who regularly speaks on lean thinking and practice in healthcare at universities, roundtables, and industry conferences. She is a strategic advisor for the Healthcare Delivery Institute at Worcester Polytechnic Institute and the ThedaCare Center for Healthcare Value. She is also a coaching faculty at the Fisher College of Business at The Ohio State University. Alice has also worked as a management consultant for Ernst & Young.
Read more
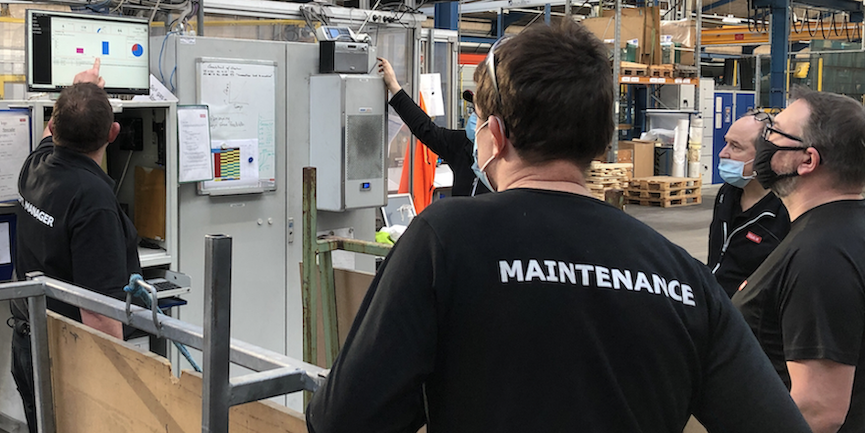
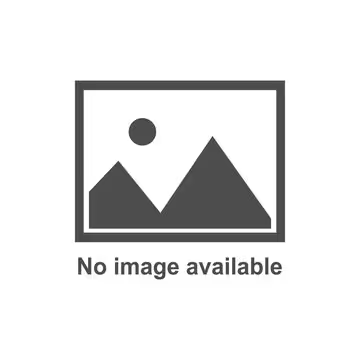
CASE STUDY – The authors discuss how rooftop window producer VELUX harnessed Lean Thinking and Industry 4.0 to empower shop floor workers, after rediscovering the kaizen spirit following a digitalization initiative that didn’t work out.
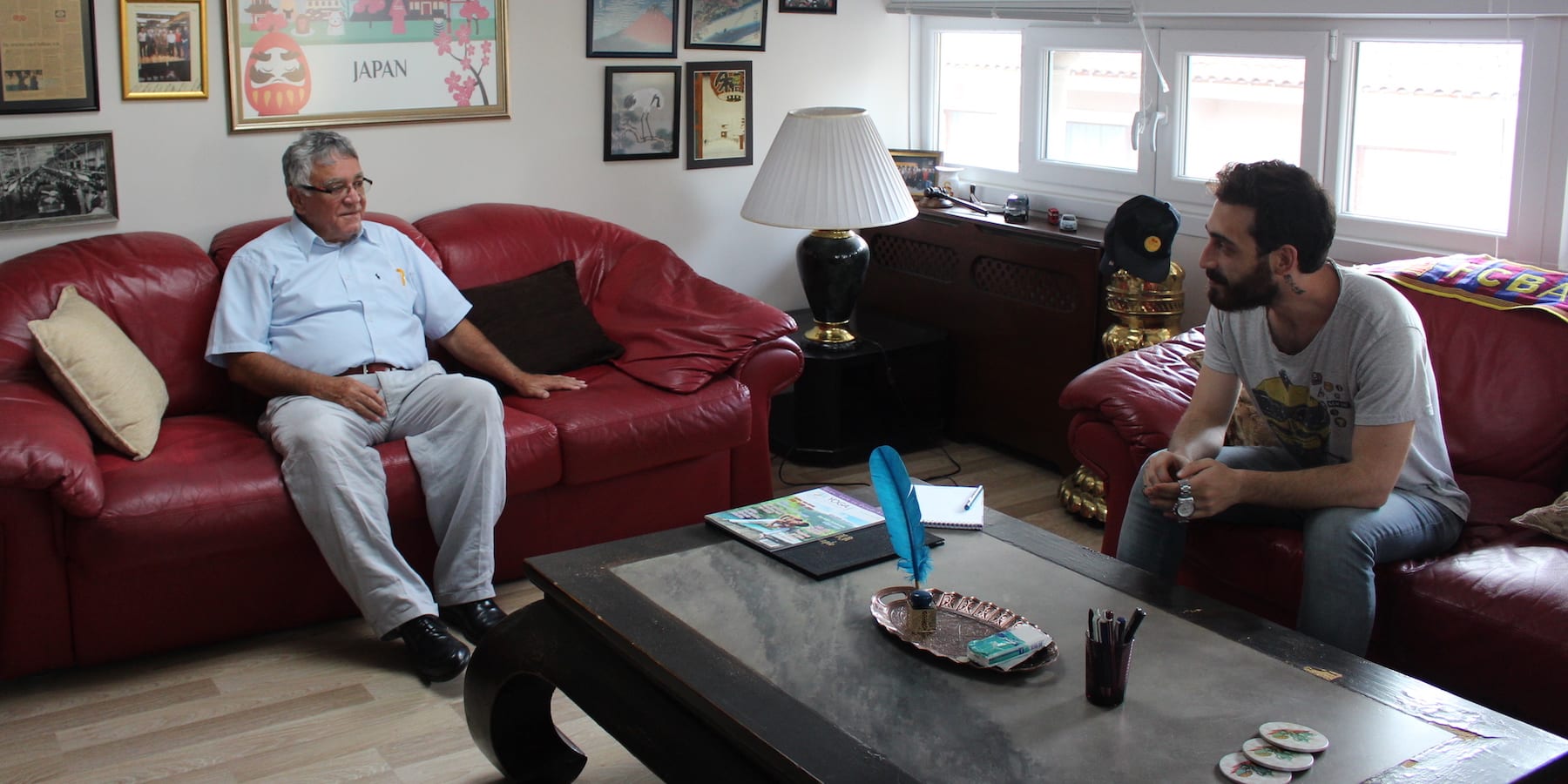
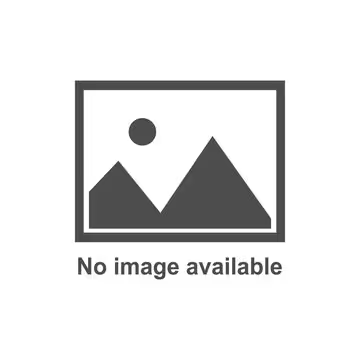
GETTING TO KNOW US – Earlier this month, our editor visited Istanbul to learn about the work Lean Institute Turkey is doing to spread lean in Turkey and beyond. He sat down with the institute’s President for a chat.
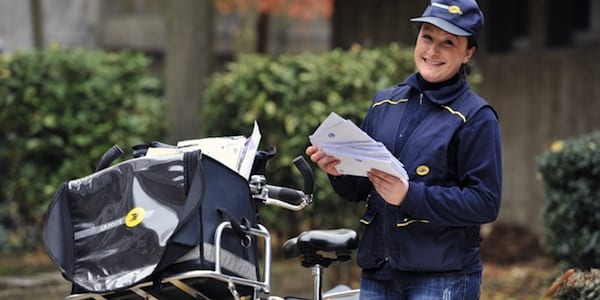
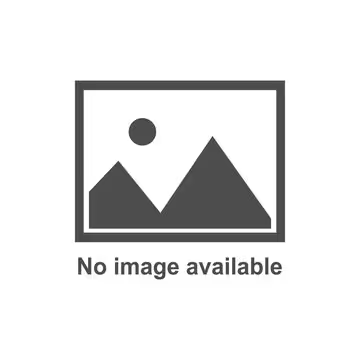
INTERVIEW – How do you communicate a consistent message to thousands of employees working across a fragmented and extremely diverse network? Catherine Blay, from French postal service La Poste, tells us.
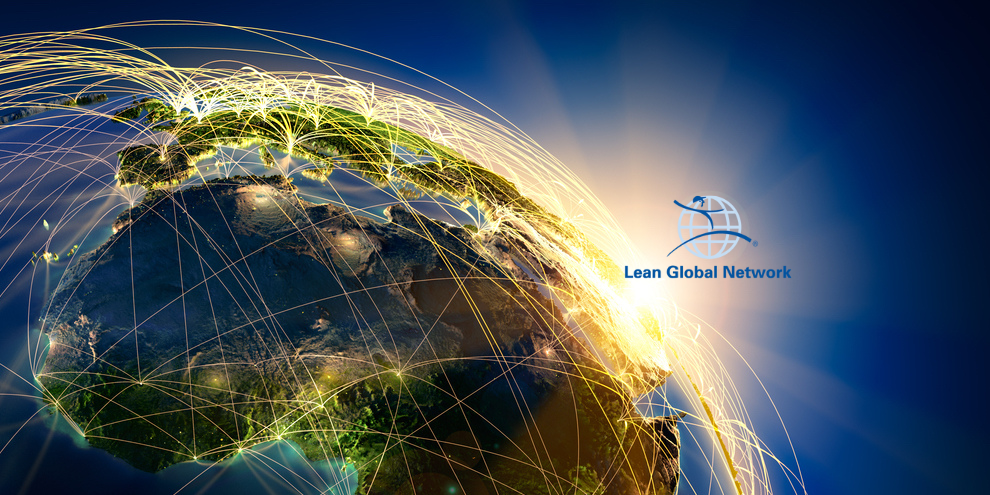
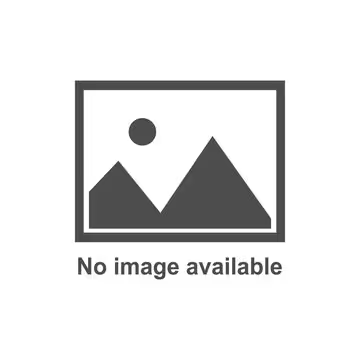
VIDEO INTERVIEW - In this conversation with our editor, John Shook discusses Lean Thinking post-pandemic and its role tackling large-scale problems, and introduces an upcoming free event you don't want to miss.