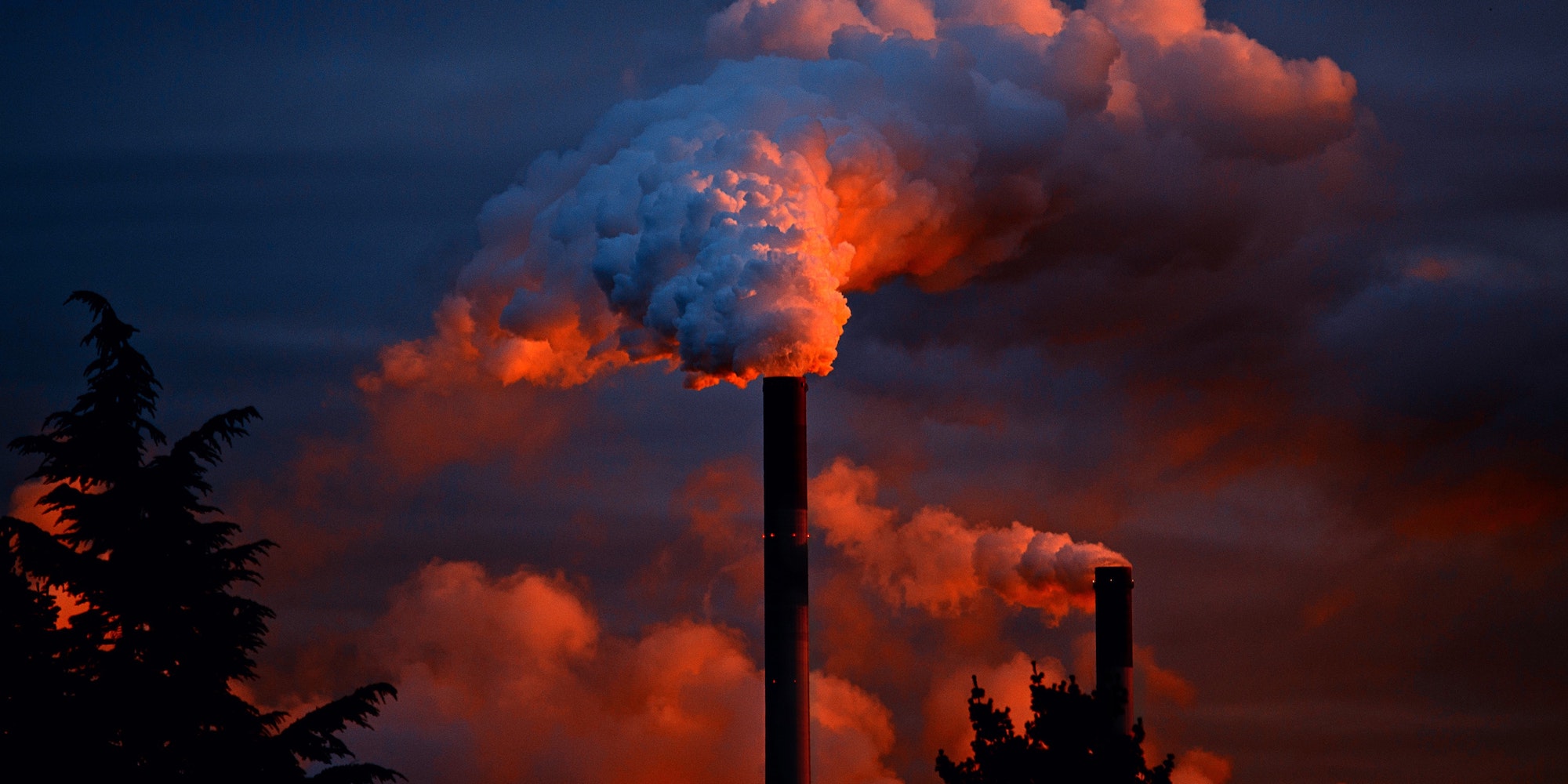
Pathways to reduce emissions
FEATURE - Imagine targeting a quarter of the world’s greenhouse gas emissions by setting our lean minds to it? The authors discuss building better, circular supply chains and designing sustainable products.
Words: Gary Cundill, Rose Heathcote and Katrina Appell
THE STRUGGLE IS REAL
It felt a little embarrassing. The person seated at the end of the boardroom table was Yvo de Boer. In his previous, job he had served as the Executive Secretary for the United Nations Framework Convention on Climate Change. And the chief executive sitting next to one of the authors had just asked him how much truth there was to this whole climate change thing. Perhaps de Boer was tempted to roll his eyes, questioning what he’d spent four years of his life doing at the UN. But he didn’t even blink, consummate diplomat that he is, and quietly and politely laid out some of the evidence for climate change. He must have done that before. Probably a hundred times.
That was a decade ago, and it would be cheering to think that a conversation like that couldn’t happen today. Sadly, climate change denialism is still in rude health, often nurtured by the actions of vested interests. Perhaps equally sadly, the evidence base for global warming has grown ever more convincing. And by evidence we don’t mean the breathless reports by wide-eyed television news announcers describing the latest flood or heatwave – bad weather is not the same thing as climate change.
The gold standard for reporting on the evidence is the output of the Intergovernmental Panel on Climate Change (IPCC). Its weighty assessment reports are issued at intervals of several years, and in August it published The Physical Science Basis, the first section of its sixth major report. Scientists are known for using language carefully, and good scientists don’t make claims that go beyond what their evidence can support. This can open opportunities for climate sceptics to mockingly ask: “Well, we just don’t know, do we?” So, what do the IPCC’s scientists have to say?
NO QUIBBLE, WE DID IT
“It is unequivocal that human influence has warmed the atmosphere, ocean and land,” says the IPCC report. Not much wriggle-room there. And they go on to detail some of the implications of this warming. The popular press already presents us with stories almost every week of the impact that climate change is having in vulnerable areas. The IPCC’s modelling provides us with projections of what we can expect to see in the future. Already arid areas will see soil moisture levels fall further, negatively impacting agricultural output. Flooding will increase, in Africa and Asia in particular, extinguishing lives and wrecking infrastructure. Sea levels will continue to rise, displacing many coastal communities.
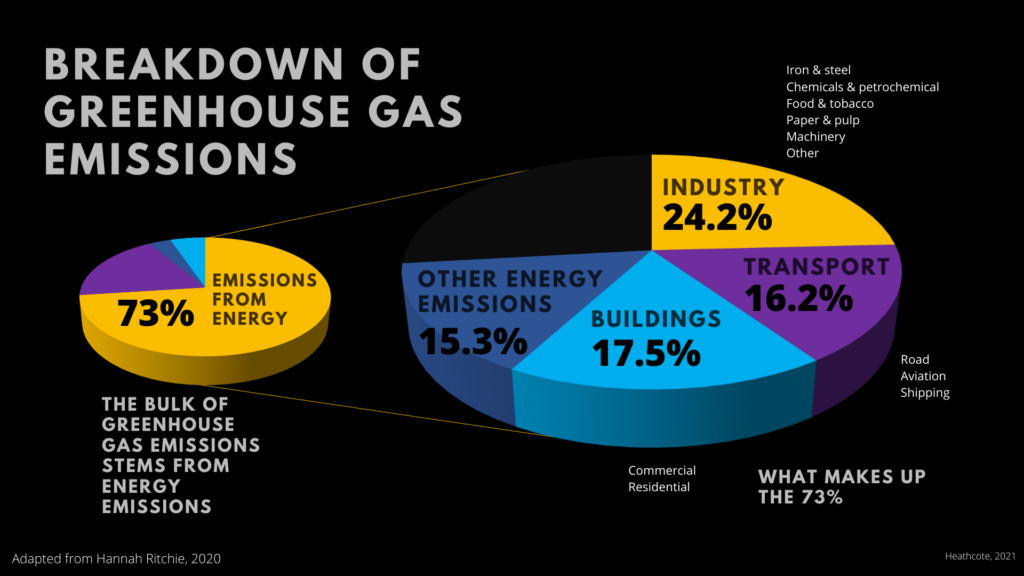
The largest contributor to global warming is carbon dioxide emissions, with smaller roles being played by methane, nitrous oxide, and fluorinated gases. Many of these emissions arise from activities such as transport and agriculture, economic sectors in which lean practitioners are increasingly involved and having significant impact. But a quarter of these emissions are a direct consequence of industry’s energy use. And industry is where perhaps the majority of lean practitioners spend most of their working days. The environmental impact of manufacturing is largely derived from upstream material production and direct energy usage to make products. The chance to make an impact on that quarter of the world’s greenhouse gas emissions is the opportunity that lies before us now.
THE HEAT IS ON
It’s evident that some industry players are taking this very seriously. While walking the gemba at a large international manufacturer, a sustainability leader recently explained how they’re adapting the business model to a circular one. They’re improving product designs and optimizing supply chain operations to reduce greenhouse gas emissions. It’s encouraging to see them connect environmental goals and everyday action on the ground. The leader says that “no supply chain is truly sustainable as long as you’re consuming” and challenges whether all demand is necessary – or could it instead reflect responsible, true consumption? Great question.
She openly admits they’re hit from all angles. Emerging policies force their hand to step up environmental performance. Regulations are changing and becoming more stringent. Take the “plastics tax”, for example. Plastic is derived from materials made from fossil fuels. According to the WWF Australia, “the process of extracting and transporting those fuels, then manufacturing plastic creates billions of tons of greenhouse gases” (more on this here). That’s significant. The company acknowledges that the new tax is a good thing even if it makes them sweat. Then there are bans on chemicals such as PVC, mandatory labeling (or green passporting), greener procurement and extending their responsibility down the product lifecycle – compelling them to act. Not all of these are, strictly speaking, greenhouse gas emissions-related, but some have indirect side effects.
Their customers are pushing, too. They want visibility of the company’s carbon footprint and more importantly, they want to know what the company plans to do about it. They want precise figures on recycled content and how it’s being reused, prolonging material lifespan. Customers want to know that if they buy the product, the supplier will come collect it later using eco-transport and recycle it. And they’re all-consumed with audits, compliance checks, reporting, and data analysis. Temperatures are certainly rising. Prioritizing becomes all the more important.
PICK YOUR BATTLES
Sustainability transformation is no walk in the park. And there’s a lot more to it than climate change. But, once you’ve set sights on the sustainability goals, such as reducing emissions, you’ll need to pick your battles. There are things you can do now and later to bring greenhouse gas emissions down across the supply chain. To figure this out, take a critical look at the emissions you produce when you make, use, and bury things. Make it transparent. Understand it.
Figure 2 is a bird’s eye view of some of the areas you might consider – and many impact emissions. Perhaps you want to cycle used components back into the process and you’re working on your logistics operations to support it. Maybe collaborating with your network to share assets such as space or transport is on the cards. Or you’re talking about how one company’s trash is another’s treasure and negotiate a slick barter. Or maybe servitization is working in your favor. Where you lease or sell a service as opposed to a tangible product, taking on end-of-life fully. Take a look at your big picture view, but then roll up your sleeves and direct your attention to the gritty details.
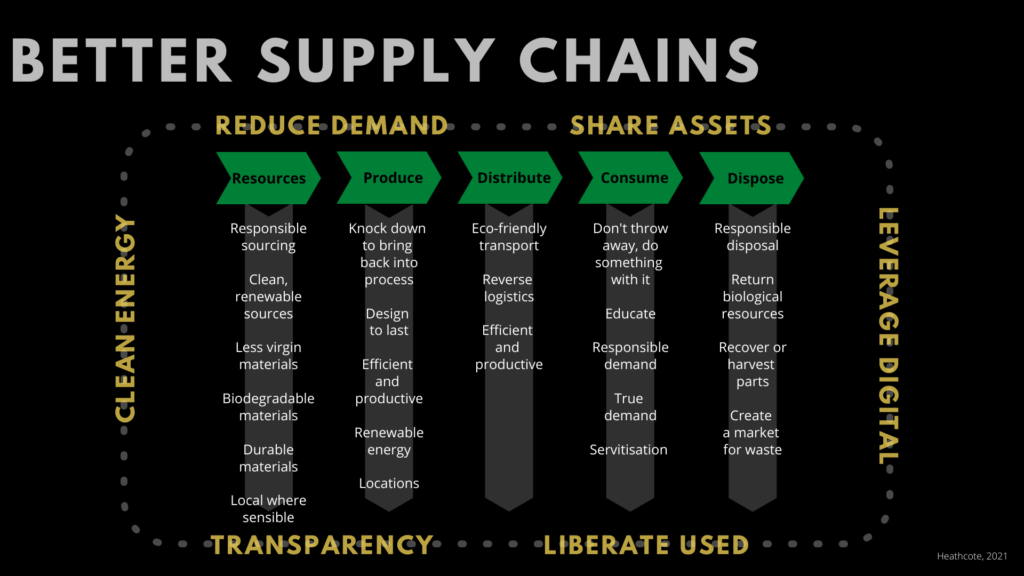
STEP INTO THE GRITTY DETAIL
Let’s narrow in on terms those attuned to lean are familiar with: efficiency and productivity. But what does efficient and productive look like? We want valuable work expending the least amount of energy. The best possible output from scarce inputs. Because with fewer inputs, there will be fewer emissions. “Doing more with more” – rather than “more with less” – pumps extra emissions into the atmosphere. Conversely, if you reduce energy consumption and improve yield, greenhouse gas emissions will decrease. There’s a massive 73% piece of the energy emissions pie to be sliced – 24% if you’re an industry player. Set your lean mind to it and challenge the current state:
- Making more product than needed: too much or too soon consumes resources, energy, and capacity. In its worst form, the product goes to waste without being used at all.
- When we hold excessive stock, we have to house and manage it. More space, more transport, more emissions.
- When we produce poor quality, we consume resources fixing it. More energy, more materials, more emissions.
- Machine downtime and variation steals capacity. Catching up on lost capacity by adding capacity uses more energy.
- Layouts, motion, locations and routes influence transport. Optimizing lowers the strain on transport energy.
- Good yield from inputs uses less materials and energy.
Unfortunately, optimizing is fairly reactive in nature. This is the downside of “fixing” the existing set-up you’re faced with. Still, it plays a crucial role in nurturing eco-minded teams. Perhaps the greatest advantage of improving front-line operations is the positive influence on mindset. Cycles of experiments, leading to learning, leading to iterative change is impressive when it challenges how people think about their work and helps them see what they’re capable of. This is the true value of lean. It is a learning system, a problem-solving confidence-builder. In this setting, building confidence to tackle even bigger problems that matter. Even if you design sustainable operations from scratch, there will always be a need for continuous improvement as problems emerge, performance regresses, or innovations come to light.
So, this leads us to the next question. How can we be proactive? Designing for lower greenhouse gas emissions is proactive in nature and a critical chapter in the transformation story.
GET IT RIGHT EARLIER
To have the biggest impact in reducing emissions we need to design sustainable value streams from the start. It is the decisions we make in product development that lock in a significant portion of the greenhouse gas emissions across the entire value stream. Unfortunately, material and energy utilization, which have the biggest environmental impact in manufacturing, are rarely considered in the development process or are only considered late in the process when little can be done to influence the design.
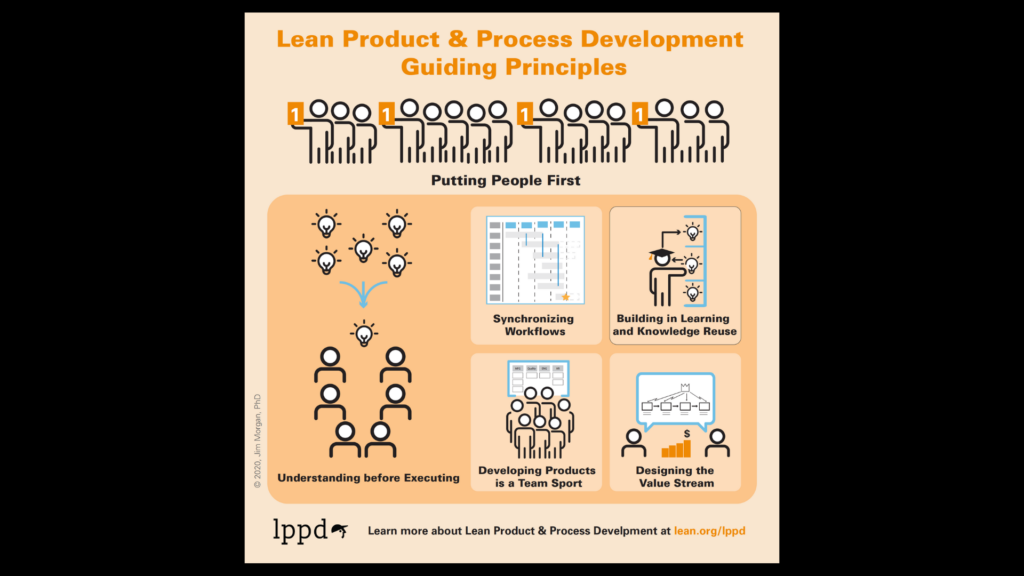
The guiding principles of lean product and process development can enable us to build sustainability into our value streams. We can design the value stream for better material and energy utilization if we consciously focus on doing so early in the development process, when the decisions we make have the biggest influence.
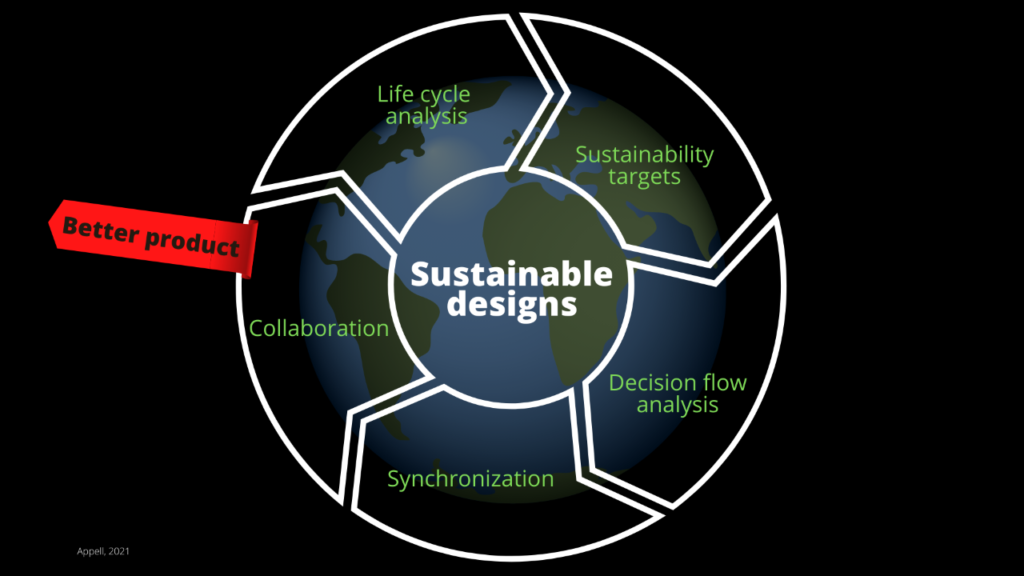
Life cycle analysis can be used to understand the biggest environmental impacts and opportunities to reduce those impacts, including greenhouse gas emissions, across the product life cycle and value stream. A concept paper can be used to effectively build cross-functional team alignment, including with sustainability experts, to set the vision and sustainability targets, including material and energy utilization, for the product during the study phase. Once we make sustainability a key decision criterion, we can use decision flow analysis to understand the decisions that have the greatest impact on sustainability, what we need to learn to make those decisions, who needs to be involved based on their knowledge and expertise, and when the decisions need to be made. This understanding enables the team to synchronize their work. Synchronizing their work and clear targets for material and energy utilization set the team up to effectively collaborate to reduce greenhouse gas emissions throughout the execution of the product and process development, using obeyas with glide-paths to see when and where help is needed.
Lean product and process development principles and practices allow us to put people first by enabling the entire product development team, including sustainability experts, to design value streams with lower greenhouse gas emissions. Making it easier for the product development team to make better decisions for the business and the environment can create the conditions for people to do more meaningful work, perform better, and even reach their full potential. People perform better and get more satisfaction from their work when they have purpose, autonomy, and mastery. Enabling people to understand the impact of their decisions while offering the support to lower greenhouse gas emissions can provide for people’s need for purpose. Allowing people to organize their work through decision flows, visual schedules, and obeyas can meet their need for autonomy. Creating the opportunities for learning about the environmental impacts of decisions, the other functions that you should be collaborating with, and practices that support the development process can help them to meet their need for mastery. Lean product and process development principles and practices enable us to concurrently develop people and products with lower greenhouse gas emissions.
Our planet matters. Elon Musk’s plans aside, it’s the only one we have. Right now, our failure to take climate change sufficiently seriously is compromising the ability of the world’s population to live well and to prosper in the years to come. As lean practitioners we have the ability to impact our planet for good. With that ability comes the responsibility to follow those pathways that lead to lower greenhouse gas emissions.
THE AUTHORS
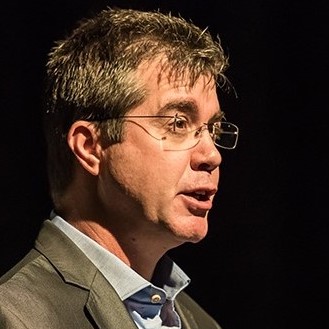
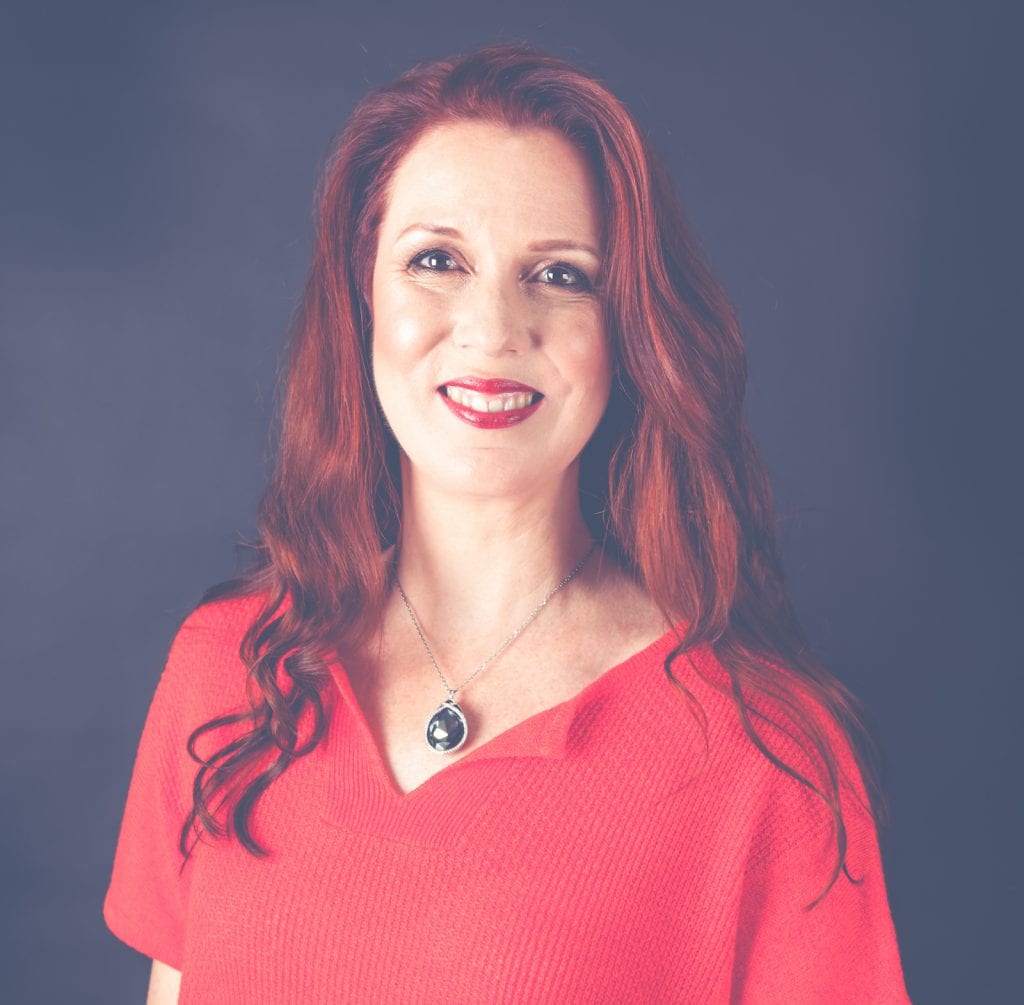
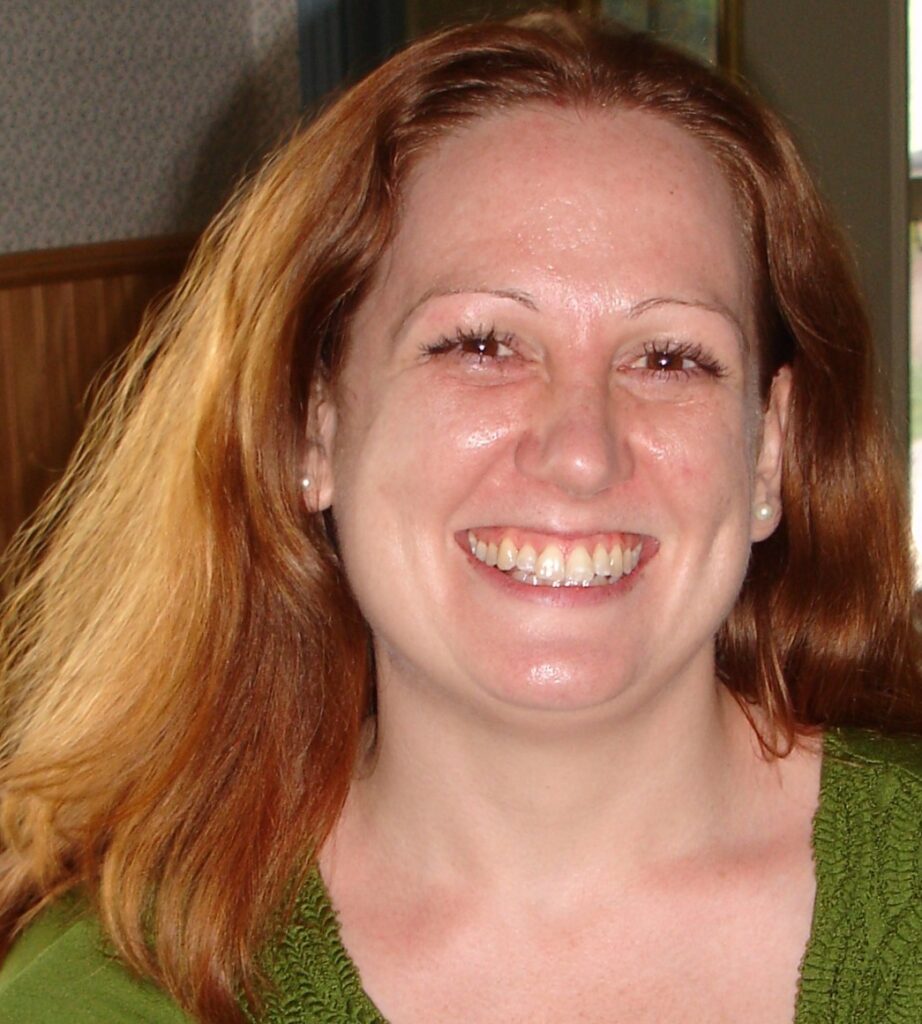
Read more
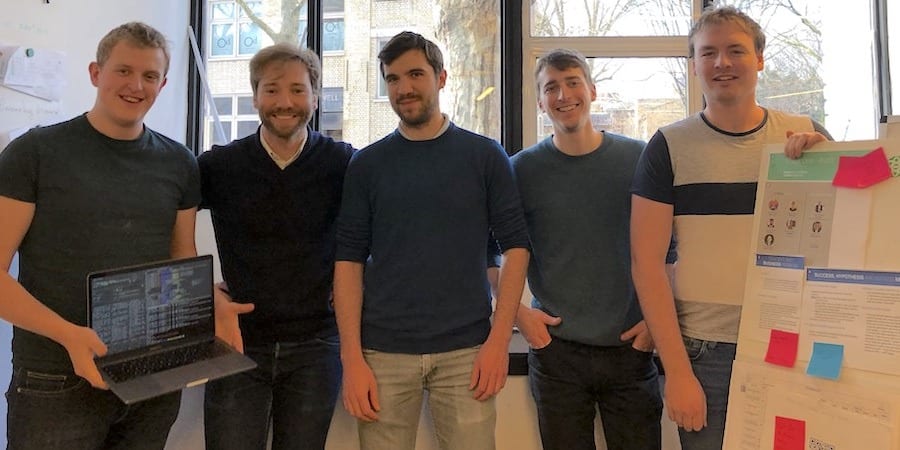
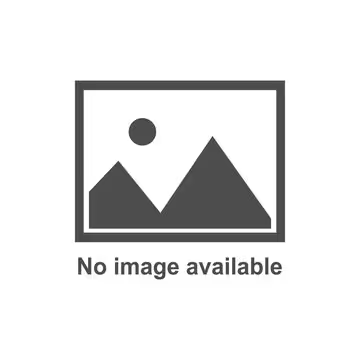
BUILDING BRIDGES – Struggling to scale a new product past its MVP phase, Theodo tried a number of things before realizing that the only way to retain quality and speed is kaizen.
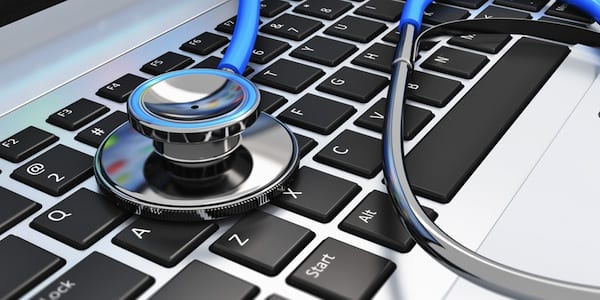
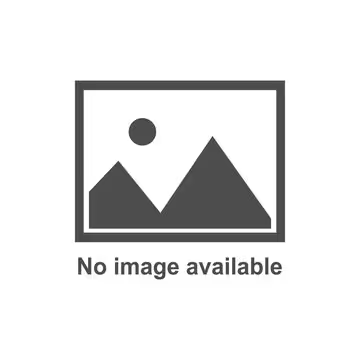
COLUMN - In the third article of our series, the CEO of a healthcare institution in Catalonia, Spain, discusses the implementation of lean as a mindset that has its foundations in continuous improvement.
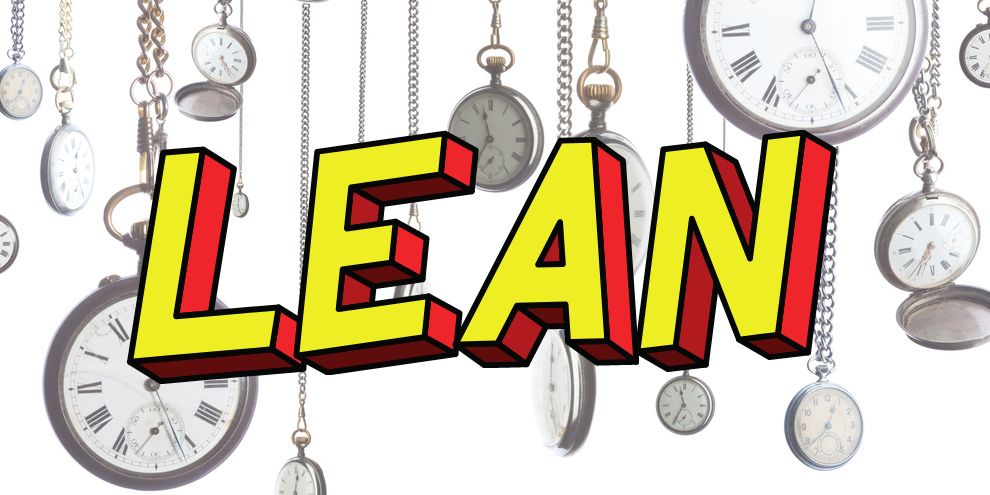
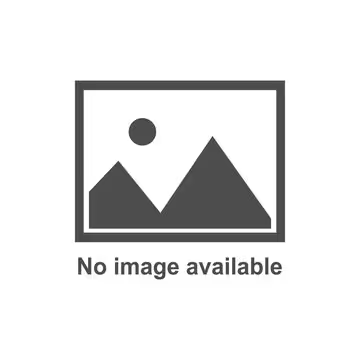
FEATURE – With one of the biggest lean events of the year just four days away, John Shook tells you why you should participate and what you can expect.
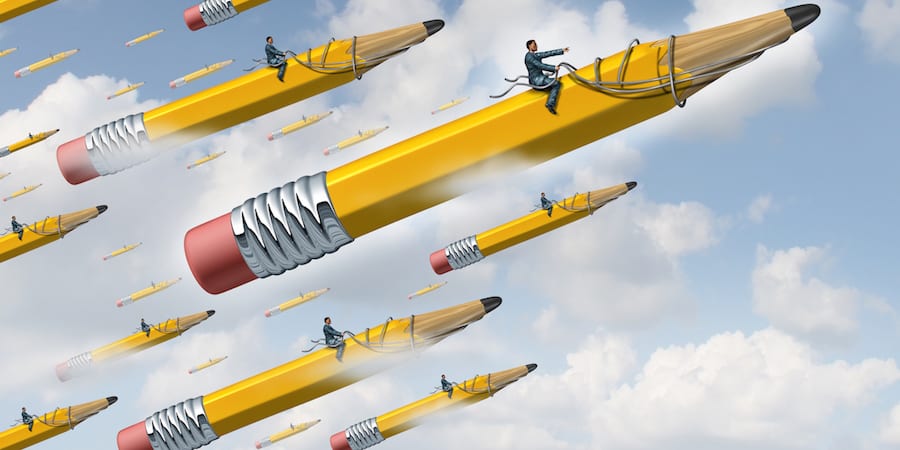
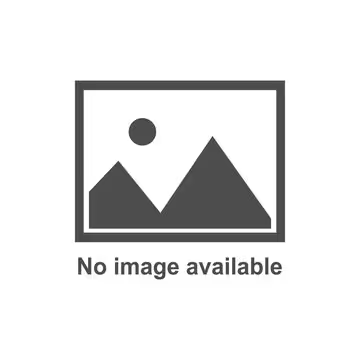
FEATURE – This powerful article explains why we should place learning at the heart of our lean strategy to build better products – something Toyota has always done – and how management fits in the picture.