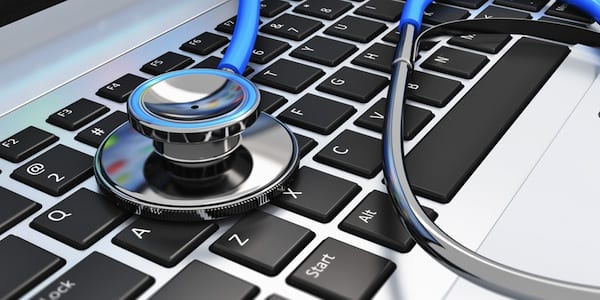
Bringing lean change to the Garraf hospital
COLUMN - In the third article of our series, the CEO of a healthcare institution in Catalonia, Spain, discusses the implementation of lean as a mindset that has its foundations in continuous improvement.
Words: Josep Lluís Ibáñez Pardos, CEO, Consorci Sanitari del Garraf
The Consorci Sanitari del Garraf is a young healthcare organization and rehabilitation center created in 2009 from the union of two hospitals in the Catalan region of Garraf. To read more about the implementation of lean at CSG click here.
The Spanish economy has been in the news a lot in the past few years. The downturn, like in many other countries in the European Union, has had repercussions in every sector of the economy: for a while, austerity and cuts were the norm across Catalonia and the rest of Spain.
Our group of hospitals, the Consorci Sanitari del Garraf, was not spared and saw its budget slashed by 17-18%. One of our goals was to become a trusted provider of integrated healthcare to which people here in our region would turn to. This meant we had to look for tools that would help us to set our strategy and improve our processes more quickly and effectively.
I had already had some experience with lean in 2003-2004, when the hospital I was working for at the time (I sat on the board) decided to start to apply it with the help of a consultancy firm.
But it was only after taking a one-week course at the Instituto Lean Management that I became fully convinced and decided to “do lean” in a different way, engaging the front line and encouraging them to play an active role in the transformation. Lean seemed the ideal methodology to guide us through the merger and help us to stabilize our processes (the consolidation of internal processes and the desire to drive continuous improvement and patient safety represented two of our first challenges).
Lean has taught us how to work in a different way, focusing on the value in the process. The success of the implementation at CSG is a result of the fact that lean was introduced as a culture of continuous improvement, which meant that everybody had to be involved in the process. Our consultant, Instituto Lean Management, provided us with vital help too, acting as our partner throughout the journey.
As we set off to introduce lean thinking, we realized we had to develop the right processes and the right people, and to ensure that the implementation would not result in any head count reductions. That would have prevented any change from happening.
The focus was on the cultural transformation, not on short-term savings. In time we managed to make lean part of mechanism of CSG, part of its DNA, by orientating ourselves towards our core business: the quality of care, and being good doctors and nurses.
Even though in recent months we have won several awards, I believe that the reason behind our success was that we never aimed to be “the best hospital” but just to lay the foundations for a new way of working.
The most important thing is that lean is not perceived as a two-year thing, as a fashion trend, but as a continuous drive towards improvement. Everybody at CSG is now starting to understand what the methodology is all about, and see it as a precious ally in their efforts to help the organization to survive and thrive.
Hospitals are complex organizations in which introducing lean can sometimes be extremely difficult. Change often is. However, I am happy to say that we are now at a point where many people and departments are interested in going down the lean route, and it is our aim to expand the implementation across the corporation. But it must happen in small steps.
Right now I see lean spreading like a virus, inside CSG and beyond (senior executives from other hospitals often ask me about our efforts). It’s a great opportunity that should not be wasted, but we need to do things right. If you apply lean badly, then you may as well not even start; but if you do it right, making it part of your long-term strategy, then you will see great improvement.
There are a few things a hospital cannot go without, and one of them is the quality of care. This can only happen with smart and efficient processes in place, and lean is the best methodology we have out there to get those processes running.
And while the decision to apply lean and the push should be vertical (coming from the board) and see the involvement of leadership, the execution should happen horizontally across the business. We are not there yet at CSG, but we will. Our plan is to complete the projects we have started, and to sustain and build on the results we achieved. So far we have created behaviors and practices in a number of areas, from the emergency department to the operating rooms.
Critical to the horizontal application of lean is mid-management, of course. We are lucky because our mid-managers and our lean manager, Rosa Simon, were totally involved. They know our processes inside out and have a vision for the future of the hospital.
My role as CEO of the Consorci Sanitari del Garraf is to back them and to be available whenever a problem arises. It is my responsibility, after all, to encourage people across the organization to embrace the methodology and to create a sense of need for change. In order to do that, a CEO must be fully committed and convinced – if not, getting others on board will be impossible.
We are not a big hospital but we want to be a great hospital. And it is our duty: to work lean to work better.
THE AUTHOR
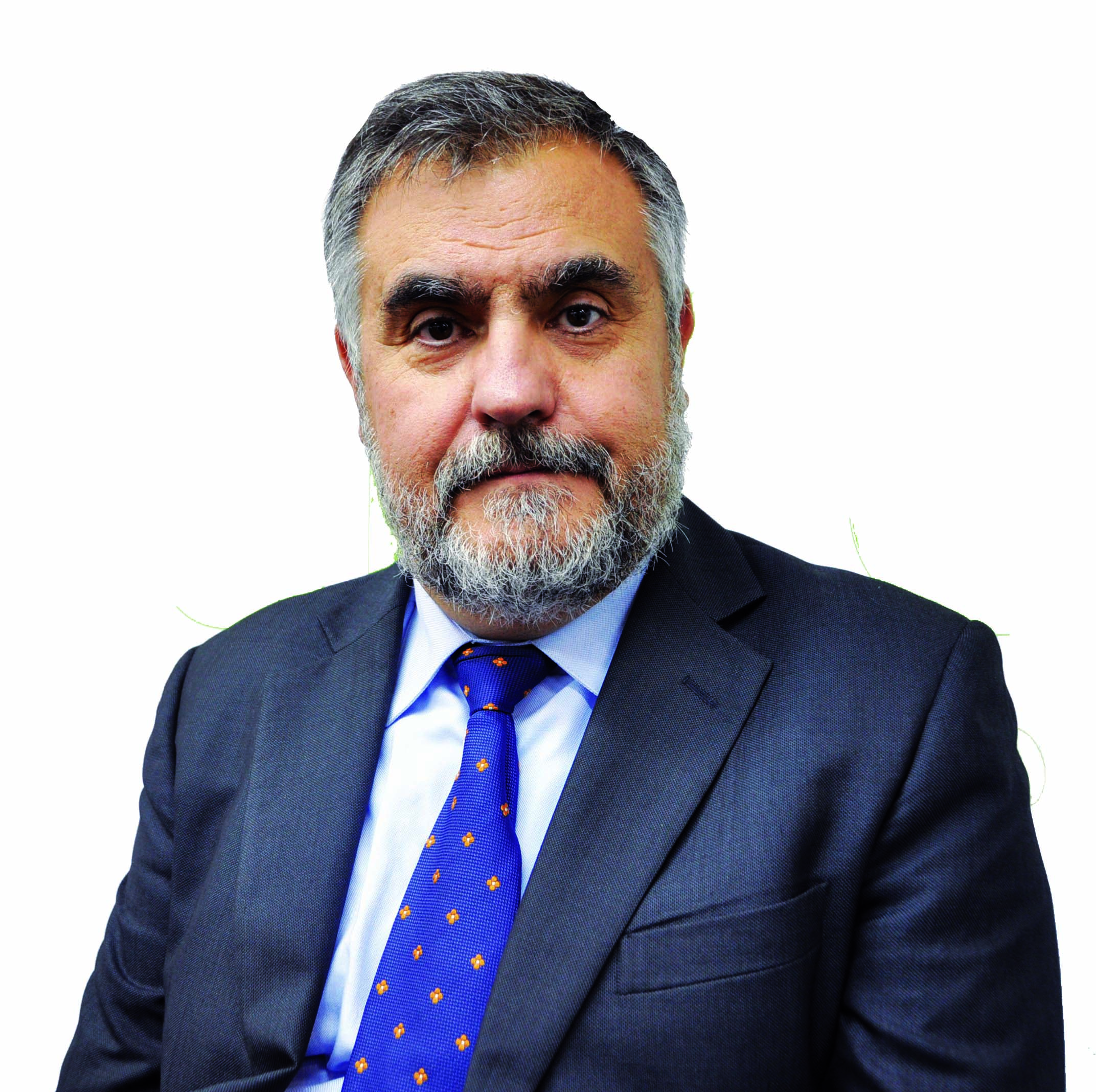
Read more
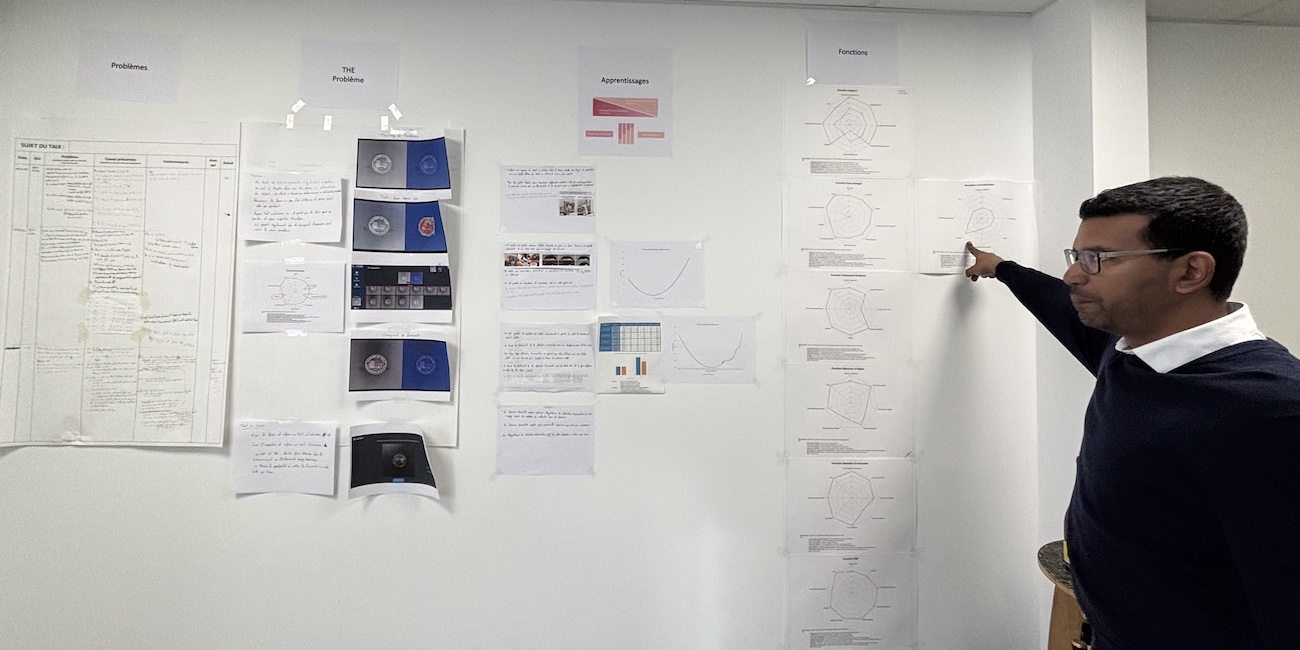
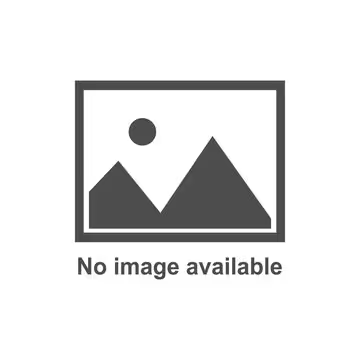
CASE STUDY – This French firm transformed its engineering approach through continuous learning, radical redesign, and user-driven innovation, evolving into a lean, resilient company with a strong culture of development.
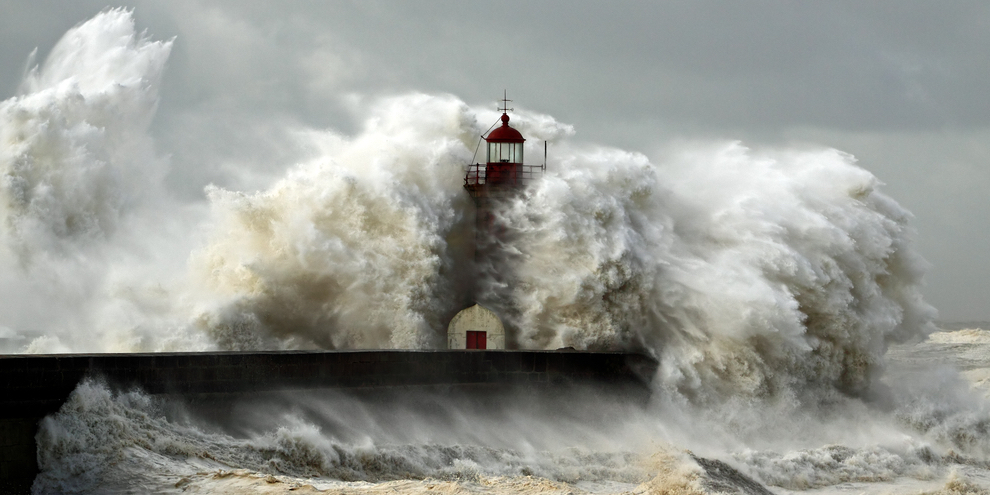
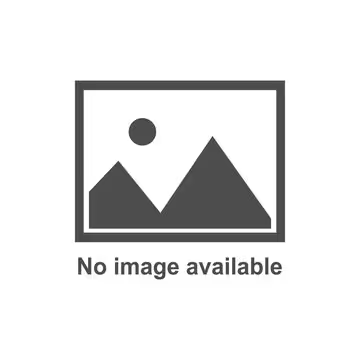
FEATURE – The author discusses the impact of the Covid-19 pandemic on the companies and the needs of individuals in her town of Maun, Botswana, and wonders what role lean can play in their lives.
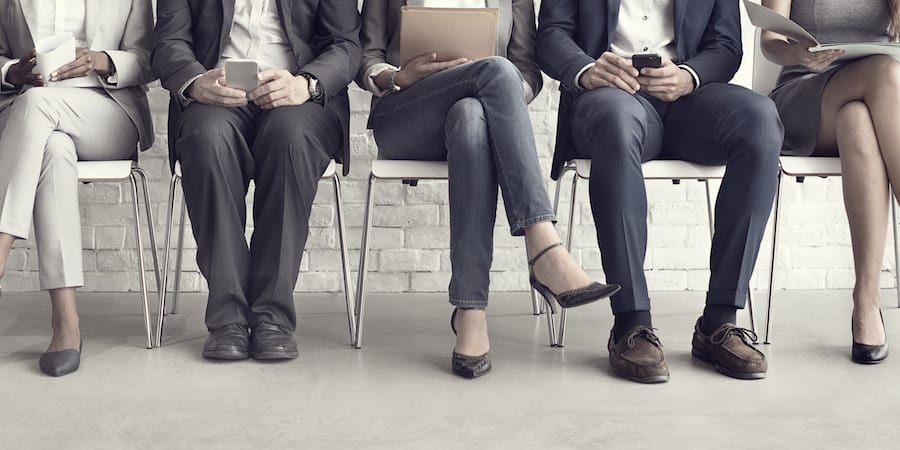
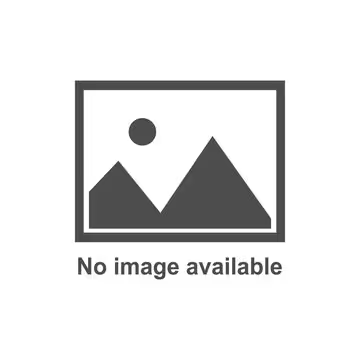
FEATURE – In most organizations on a lean journey, the people management function is not very involved. So, how should HR change, if it is to effectively support a lean transformation?
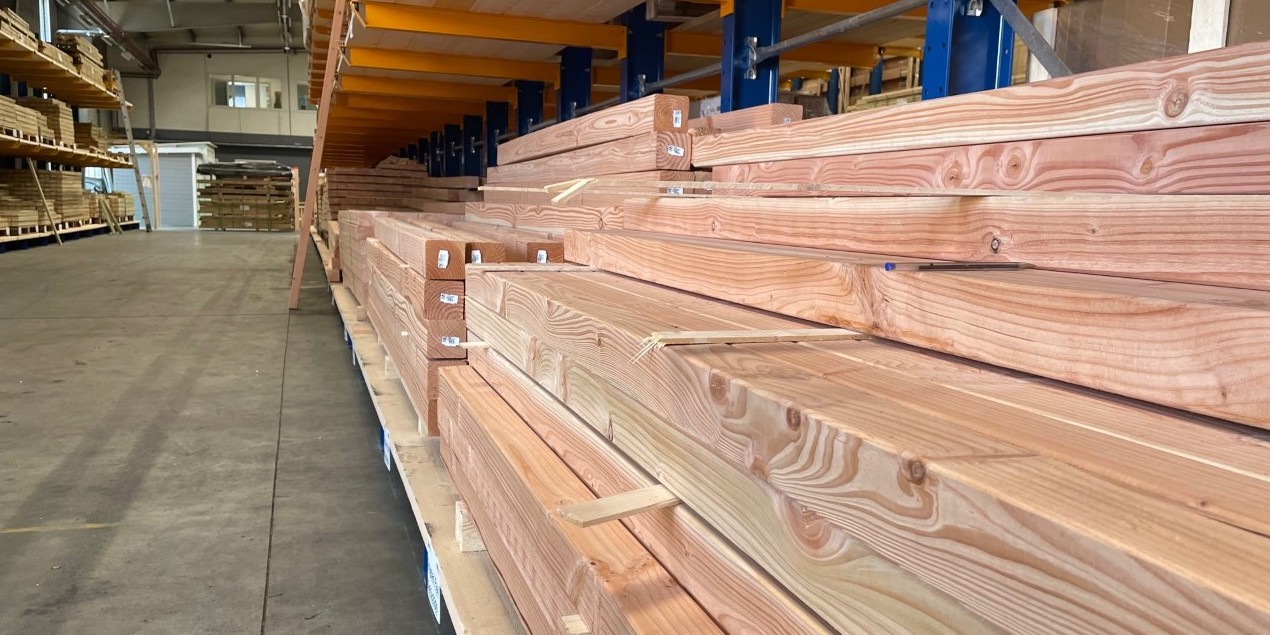
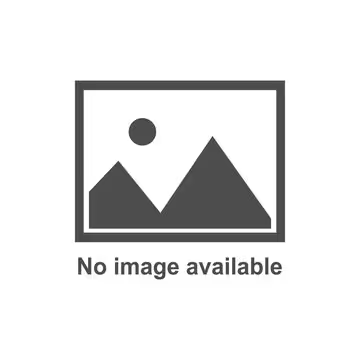
CASE STUDY – This Dutch SME is transforming its picking operation – partly with the introduction of a U-shaped design – to increase the number of orders it can fulfil every day.