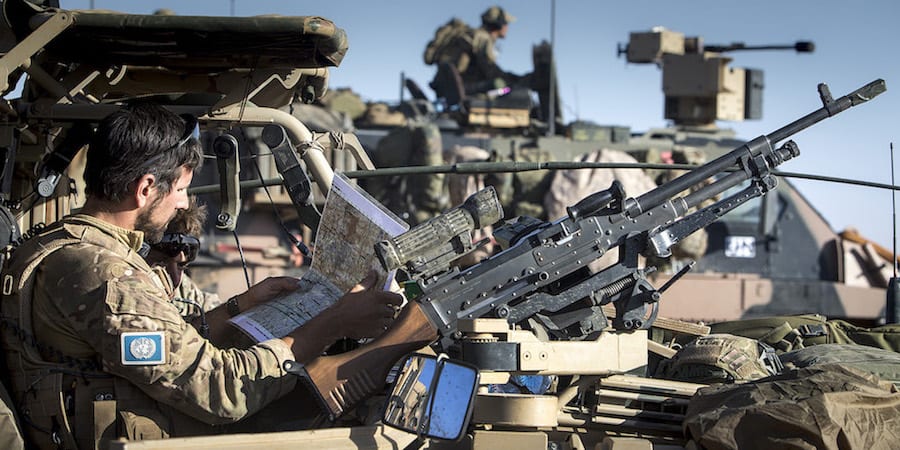
How the Dutch Special Forces apply lean without realizing it
FEATURE – Teamwork, value stream mapping, 5S, kaizen – a former officer in the Dutch Special Forces reflects on how lean thinking is unconsciously embedded in Special Operations practices.
Words: Eric Pasman, lean coach and former officer in the Dutch Special Forces
During the daily all-staff briefing the company commander of 104 Special Operations Land Task Group entered the briefing room and said: “A UN convoy of the Niger battalion is under attack by terrorists. We know that there are dead and wounded, but we have no further details. Prepare to set them free. Your helicopters leave within the hour.”
When we arrived at the location shortly after, we soon noticed that the ambush had ended. Nine colleagues were killed. An improvised explosive device was found. Four hours after the company commander had given us the order, we were back at our mother base in Gao and had handed over the killed soldiers to our medical staff. Not a single shot was fired.
For many years, I’ve had the privilege to serve as an officer in the Dutch Special Forces (Korps Commandotroepen). When I switched to a business life, I got to learn about operations management and lean thinking. These principles suddenly opened my eyes and I realized that Special Operations were in fact all about lean. We just didn’t know.
In this article, I will explain five lean principles and practices that are still being applied in Special Operations worldwide.
An example of a lean practice within Special Forces is the way we standardize our equipment and working procedures. In lean, this is called 5S. Special Forces – elite units that form the ‘guerilla’ element of an army – are all about the basics. During my Advanced Special Forces Course, we studied camouflage and covert infiltration from the basic soldier handbook. “Why study the basic stuff from a regular army soldier, when I am in Special Forces now?” I asked myself. During the field exercise that followed, I realized that 80% of the skills and drills of Special Forces aren’t special at all: they’re just basic skills mastered to perfection.
We worked according to the 5S principle with our materials as well. Everywhere we deployed, we first made sure that we established a team storage location for our weapons and equipment (this could be either a tent, a building or a container) – whether we were training in the United States or on a mission in the Middle East. We always did it in the same way.
This way of working also helped us in Mali, when we got the order to board the helicopters within 60 minutes. Because we had standardized the storage of our weapons, gear and provisions, we could grab all the necessary equipment in the blink of an eye. We were battle-ready within 15 minutes, which meant we could use the remaining 45 minutes to brief the team, drive to the airstrip and huddle with the helicopter crew.
The second important lean principle that is used in Special Forces is value stream mapping. Special Operations are usually conducted behind enemy lines. During the preparation phase, we had to prevent information from leaking (something that can easily jeopardize the mission and put the team in danger). Therefore, we prepared our missions in a confined area that only our team was allowed to access – the Isolation Room. We then prepared and hang to the walls a 30-foot-long value stream map of our operation that ran all around the room. Sheets, posters, maps, timeframes, sketches, logistic plans – with a quick glance, even an outsider could see the progress, critical points, procedures and bottlenecks. Over the years, this method has proven to be indispensable for Special Operations planning.
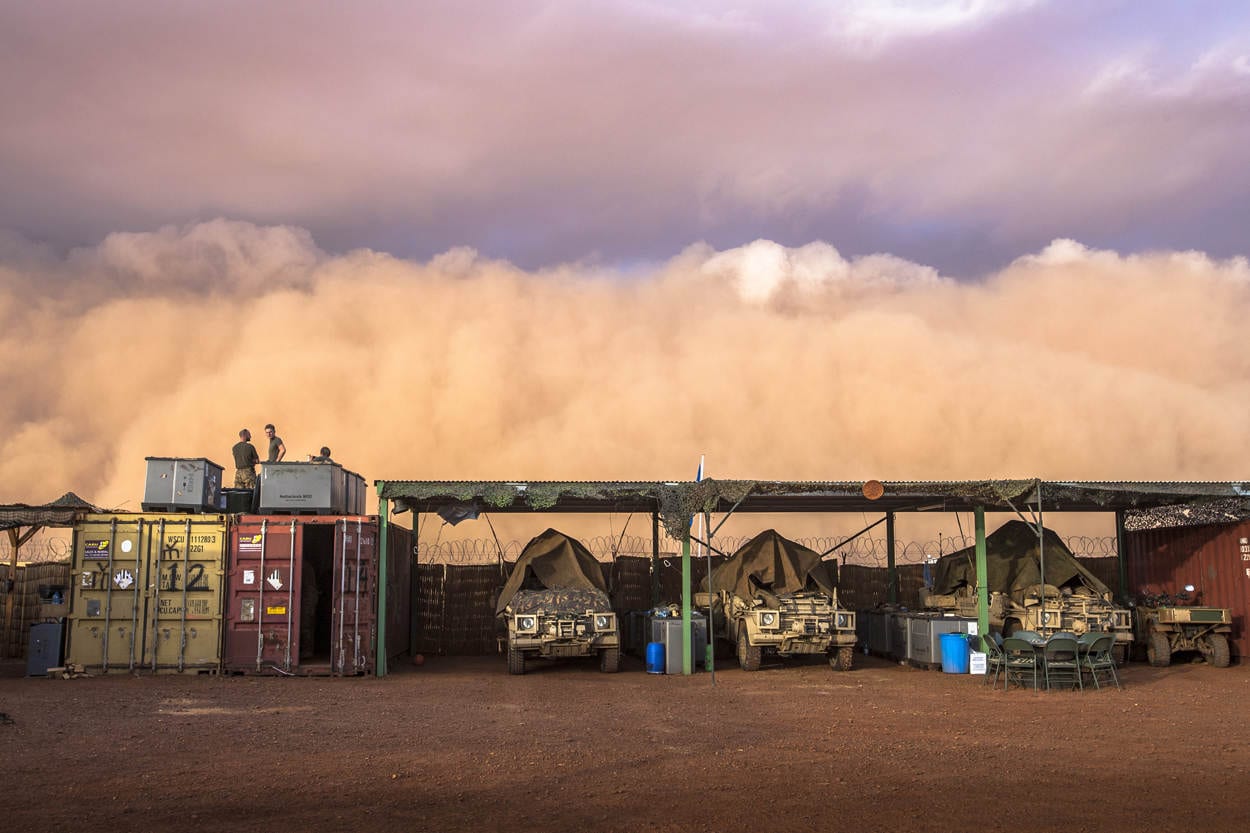
The third lean principle that we find in Special Operations is kaizen. When I coach leadership teams, I always say that reflection on their process is a success-multiplier for future results. The answer I usually get is: “That’s great for the Army, but in a business environment we have no time to reflect because of our revenue goals.” It’s too bad reflection is often neglected because it is seen as a time-consuming activity, because I have actually learned that, when done correctly, it doesn’t have to take a huge amount of time. And the results it can bring in terms of performance are great.
Reflection is deeply ingrained in the Social Forces’ way of working. For example, when we returned from our operation to evacuate the KIA colleagues in Mali, we easily could have returned to “business as usual” – there were many more operations coming up and time was of the essence. Instead, we decided to take the time to reflect on the operation we had just completed. At least six small, but very practical improvements resulted from this session. One example was the usage of a medical radio-net during the deployment, which hadn’t worked out as planned, causing two of our operators to miss a lot of radio communication while on the ground. In the future, this easy-to-solve problem -could have easily led to major issues – and we never would have unearthed it without reflection.
Last but definitely not least, teamwork is another important practice in the Special Operations. There is one major important difference between Special Forces teams and every-day teams in business: in Special Forces, we don’t let egos get in the way of performance. Here’s an example. As an officer, I had to lead a group of “soon-to-be commandos” on a 17-kilometer march along the Dutch coastline during the last week of our Commando Selection Course. We had to stick together as a team, while the sergeant-major at the front of the group constantly speeded up. Each time we failed to stick together, the sergeant-major turned around and led us back a couple hundred meters through the dunes to repeat that part of the march.
This happened a few times, but I was still feeling reasonably well (leading the group was keeping me busy and distracting me from the open wounds I had in my feet). Everything changed in a second, when the sergeant-major decided to take us back once again. This time he wanted us to march in the water rather than on the dunes. We followed him without hesitation, but as soon as the sea water touched my wounds I felt a biting pain. I will never forget what happened next.
The pain was crushing me. Eight weeks of Special Forces Selection and just two days before the end, I felt I couldn’t do it. I started crying and couldn’t put together a sentence. The guy to my left, an experienced former marine, noticed me and realized that the group had lost its leader. Within seconds, a couple of corporals had taken the lead at the front and at the back, and the former marine was supporting me. He did it for about 15 minutes, until I recovered and could resume the march.
My example is not unique. During the selection course, every Special Forces operator has had at least one of these moments. Because of this, we all know that it is okay to have vulnerability as a professional and as a human being. Being open about your weak spots makes it possible to deepen your professional and personal relationships, which results in excellent teamwork in moments when tension runs high. This to me is not too far from what happens in a business, when problems are embraced and people are encouraged to flag them up.
I find it remarkable that, in my previous life in the Special Forces, I was already applying lean principles and practices with my colleagues without knowing. To me, this is the definitive proof that lean thinking applies to any kind of environment, situation or organization.
If I compare my time in the Special Forces with what I observe in the companies I visit, I realize that that most lean principles and techniques (like 5S or value stream mapping) are relatively easy to implement. There is one major exception – teamwork. Teamwork cannot be “implemented”: you can change processes and procedures systematically, but it will still take time to build trust and mutual understanding among people. We should always take the time to foster teamwork and create opportunities for people to bond and grow.
THE AUTHOR
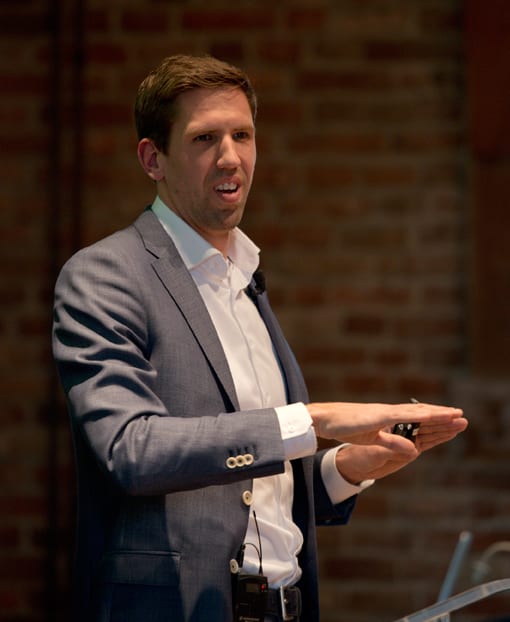
Read more
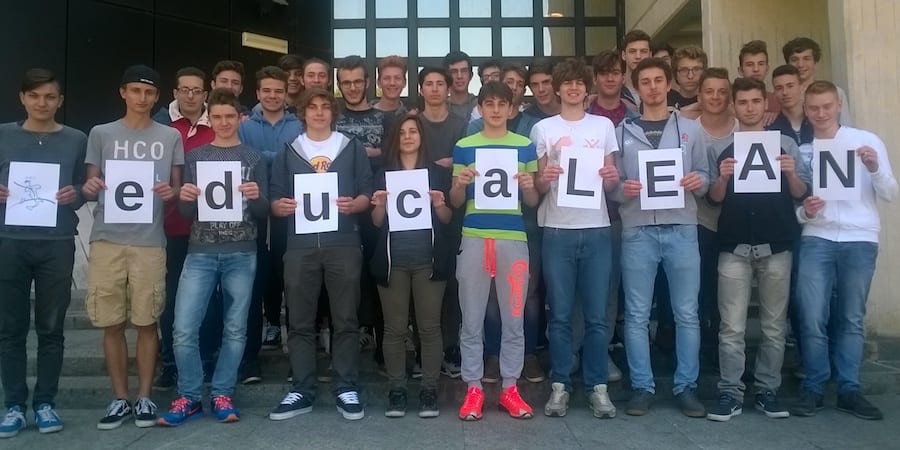
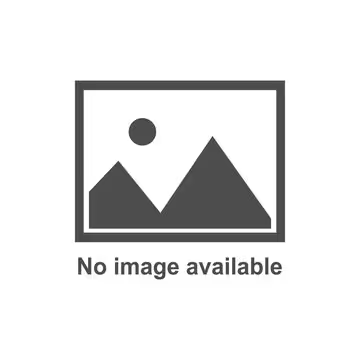
FEATURE – Is the traditional teaching model used in our schools obsolete? A high school in Italy has been experimenting with lean thinking and Scrum applied to students’ learning, and the results have been enlightening.
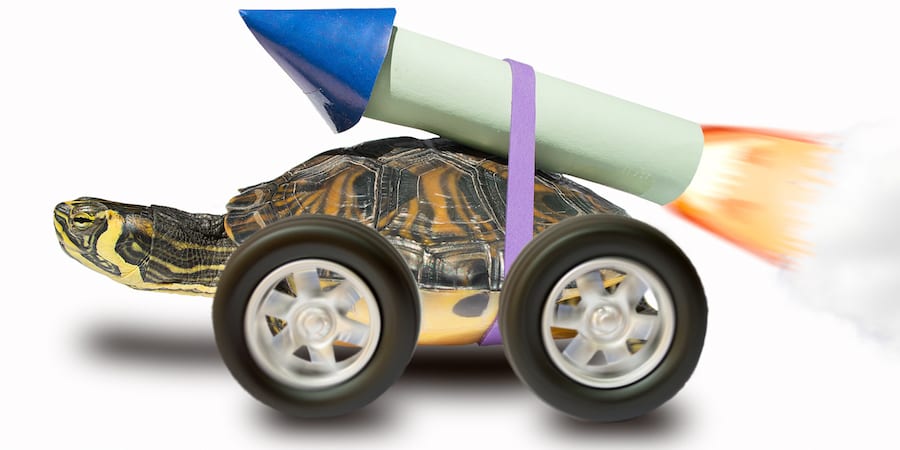
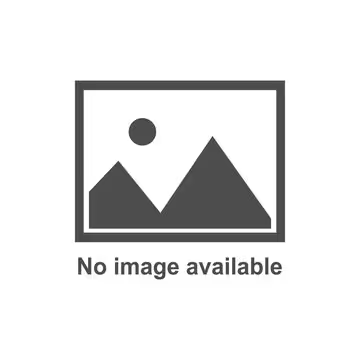
WOMACK'S YOKOTEN – How it is that some ideas and innovations spread like wildfire while others are slower to take roots? It is clear that lean thinking belongs to the latter category, but how can we speed up its diffusion?
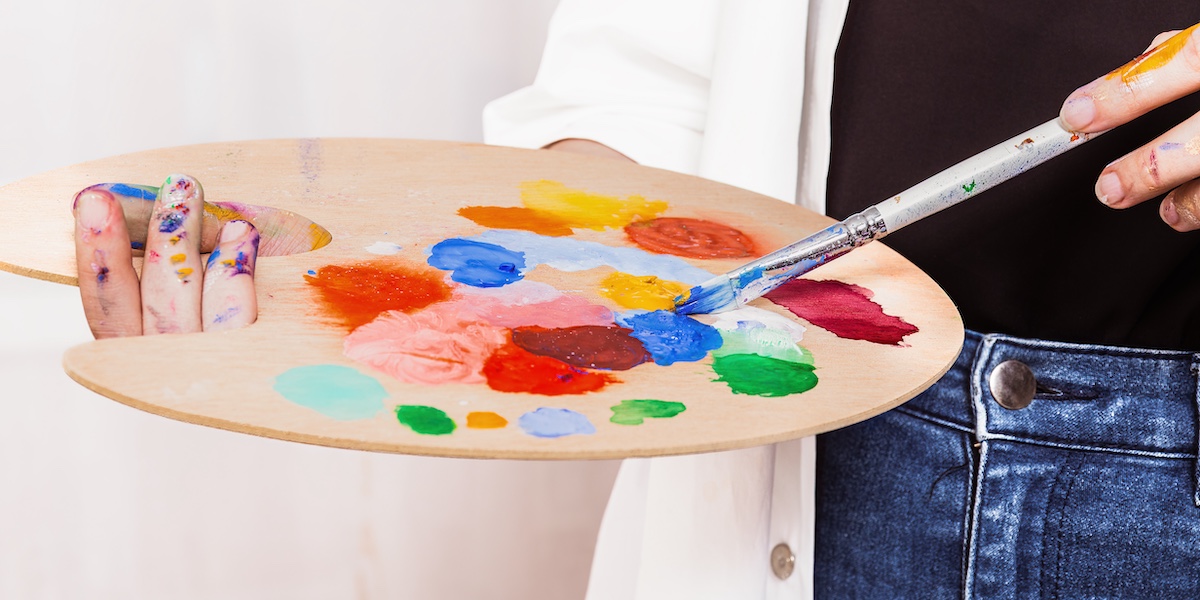
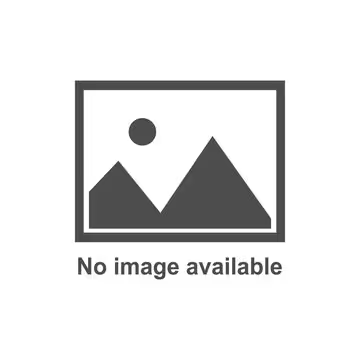
FEATURE – Embracing lean is like painting: tools are colors, respect for people is the brush, and true change blends both with intention.
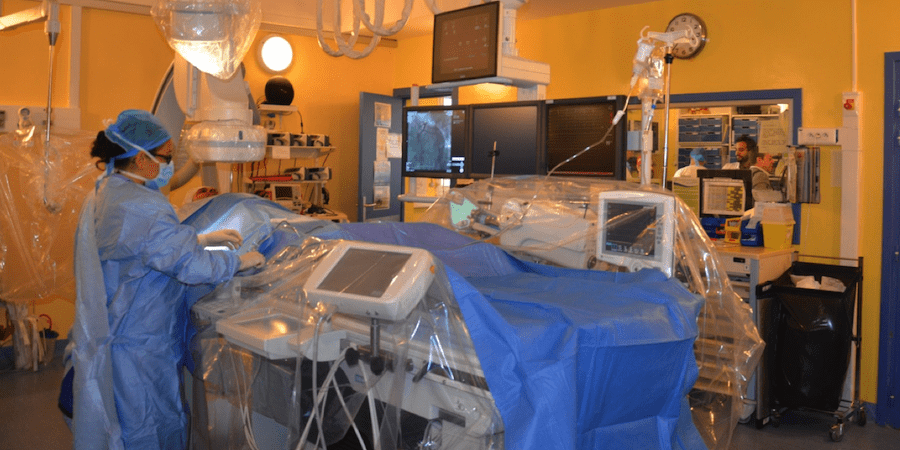
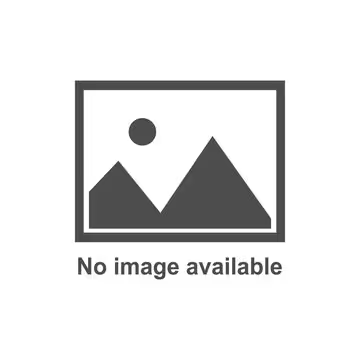
NOTES FROM THE GEMBA – On this gemba walk in the cardiology department of a Parisian hospital, the author discovers how the team is changing its internal dynamics and processes to make lean their way of thinking.