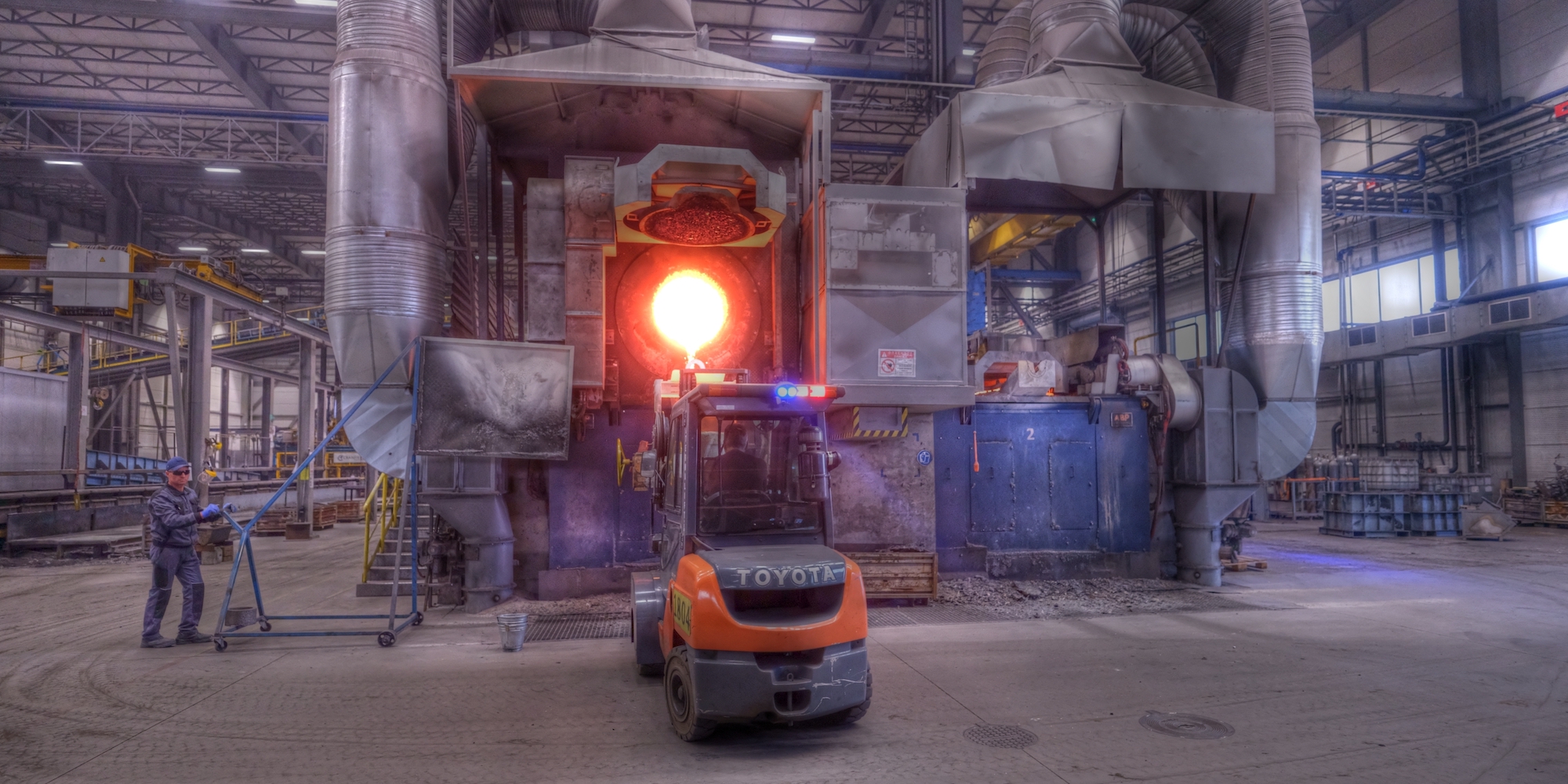
How we built a lean foundry from scratch
INTERVIEW – Ahead of this week’s Lean Global Connection, we talk to one of the speakers, who is trying to create a foundry that is lean from the start.
Interviewee: Dariusz Dziuba, General Manager, Cranfield Foundry
Planet Lean: Can you please introduce Cranfield Foundry to our readers?
Dariusz Dziuba: We are modern and environmentally friendly iron foundry that was recently built from scratch in sunny Macedonia. We cast quality ductile and gray iron castings for clients in Europe and are currently expanding to serve clients in the Middle East region. Our goal is to be “an easy to work with” foundry that customers can trust.
PL: What was the reason for turning to Lean Thinking?
DD: To be successful as a foundry, especially in Europe, one must get many things right. It is virtually impossible to run a profitable business, if the foundry is inefficient and does not continuously adapt its way of working to changing customer needs. At the start, we did not have enough know-how and we soon realized that the only way to be successful would be to build a team who can continuously learn and quickly solve problems. Thus, we decided that lean might be the best option for us.
PL: A lean greenfield! How is lean enabling you to develop your business?
DD: As a sort of “start-up”, when we began our journey, we did not have much – no customers, no facility, no team. It was a blank sheet. The only thing we had was a desire to build a lean foundry and the capital to do it (although, as it turned out, much less than what we actually needed). We truly believe that, while capital and technology are incredibly important, at the end of the day it is people who can make things happen – especially when they work as a team. Our biggest and hardest challenge was trying to become lean without having a fully developed lean culture.
PL: How has Lean Thinking helped you so far.
DD: We are only at the beginning of our journey, but even just the fact that we are still around as a business despite Covid-19, the Russian aggression of Ukraine, and sky-rocketing energy and raw materials prices is testament to the fact that Lean Thinking has allowed us to build enough agility in our company to navigate an extremely challenging environment. Something we are very proud of is our LeanShaman system. We see that it is helping us to implement changes and improvements at a speed that we do not see in other companies. Thanks to this very smart software, many decisions at Cranfield Foundry are made by team leaders and supervisors.
PL: In your opinion, what makes for a cultural transformation?
DD: Culture is a result of so many factors and it is so complex that, in my opinion, trying to manage it or change it directly is nearly impossible. What we can change is the processes and systems that shape that culture. Perhaps this is the reason we decided to go down the lean route. Lean enables us to shape our thinking, environment, standards, and way of working. Over time, little by little, this builds culture. LeanShaman helps us here, too, as it provides us with countless opportunities to coach, learn, and build culture. This process will never end.
PL: What are the main lean tools and techniques you are using?
DD: We tried a lot of things at the beginning, and that was a mistake. After some time, we started thinking that we only really needed two things: people with open mind and a handful of basic tools. So, we began to use 5S, problem solving, and standardization. But even that did not work well. That’s when we decided to follow the recommendation of Mr. Masaaki Imai, which he gave us at a conference – “Just focus on tiny improvements,” he told us. And this is what we did. We introduced a system called DAMIS – Daily Micro Improvement System (in hindsight, that was yet another mistake) – which then became LeanShaman. Today, this is one of our most powerful weapons. We use LeanShaman to build our 5S and our problem-solving system, to Standardize, and to improve.
PL: What can attendees expect to learn from your presentation at the Lean Global Connection?
DD: Our approach to lean is very pragmatic and we believe that people will appreciate our presentation, especially those who operate or work in smaller companies like ours (50 to 500 empployees) with physical operations and an uncertain business context. We will try to show how – contrarily to what most consultants will tell you – a good “sensei” (in our case, Małgorzata Jakubik of Lean Enterprise Institute Poland) and a smart system, like LeanShaman, are more than enough to kick off your lean transformation, building efficient yet flexible operations and ingraining Lean Thinking in the organization.
THE INTERVIEWEE
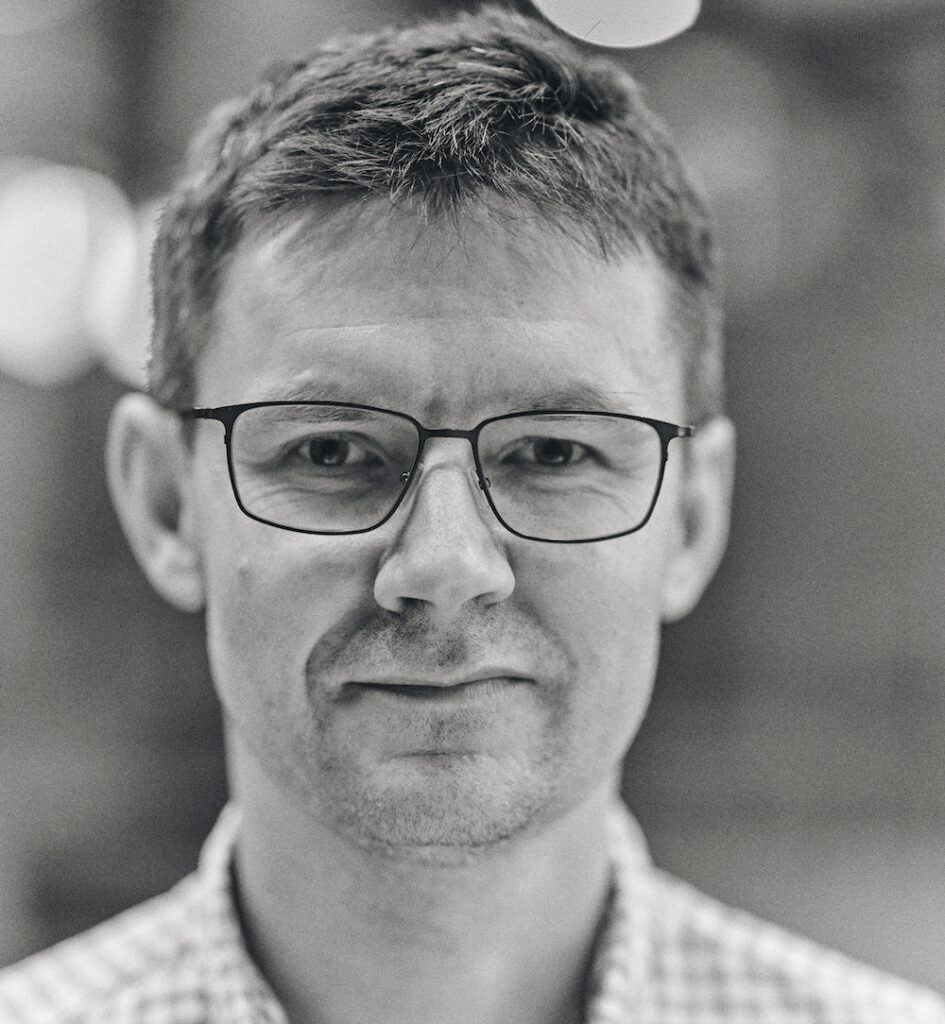
Read more
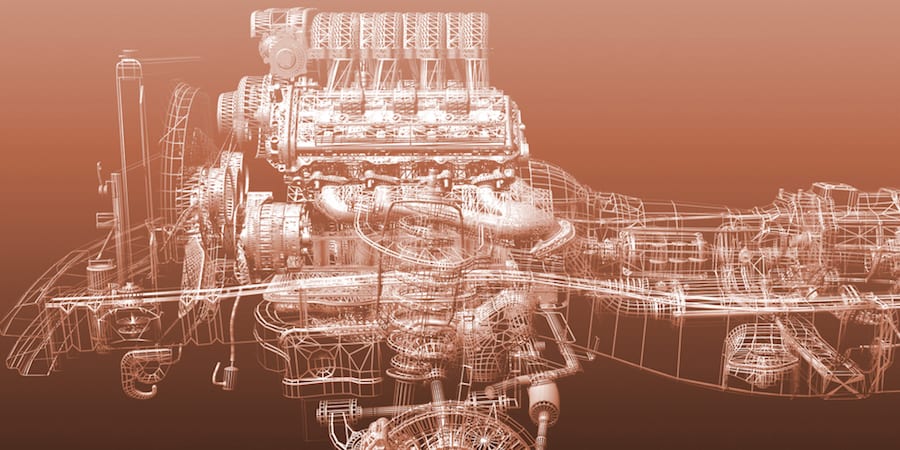
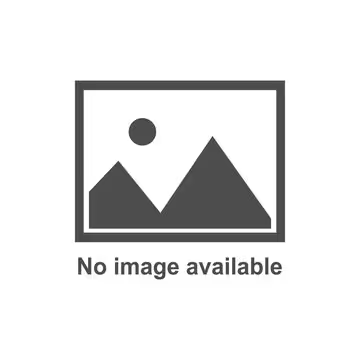
OPINION – Our systems to develop new products are slow and inadequate for the ever-changing markets we have to work in. The author describes the three lean elements that will unlock your potential to innovate.

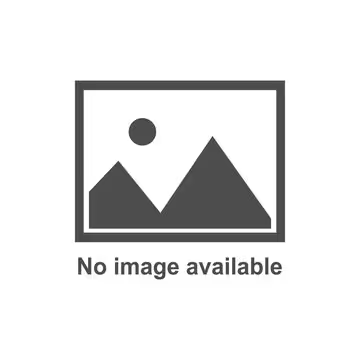
FEATURE – Reflecting on Nomura-san’s recently published book on radical quality improvement, the author encourages us to embrace the spirit of “Dantotsu” to meet the challenges we face as a society.
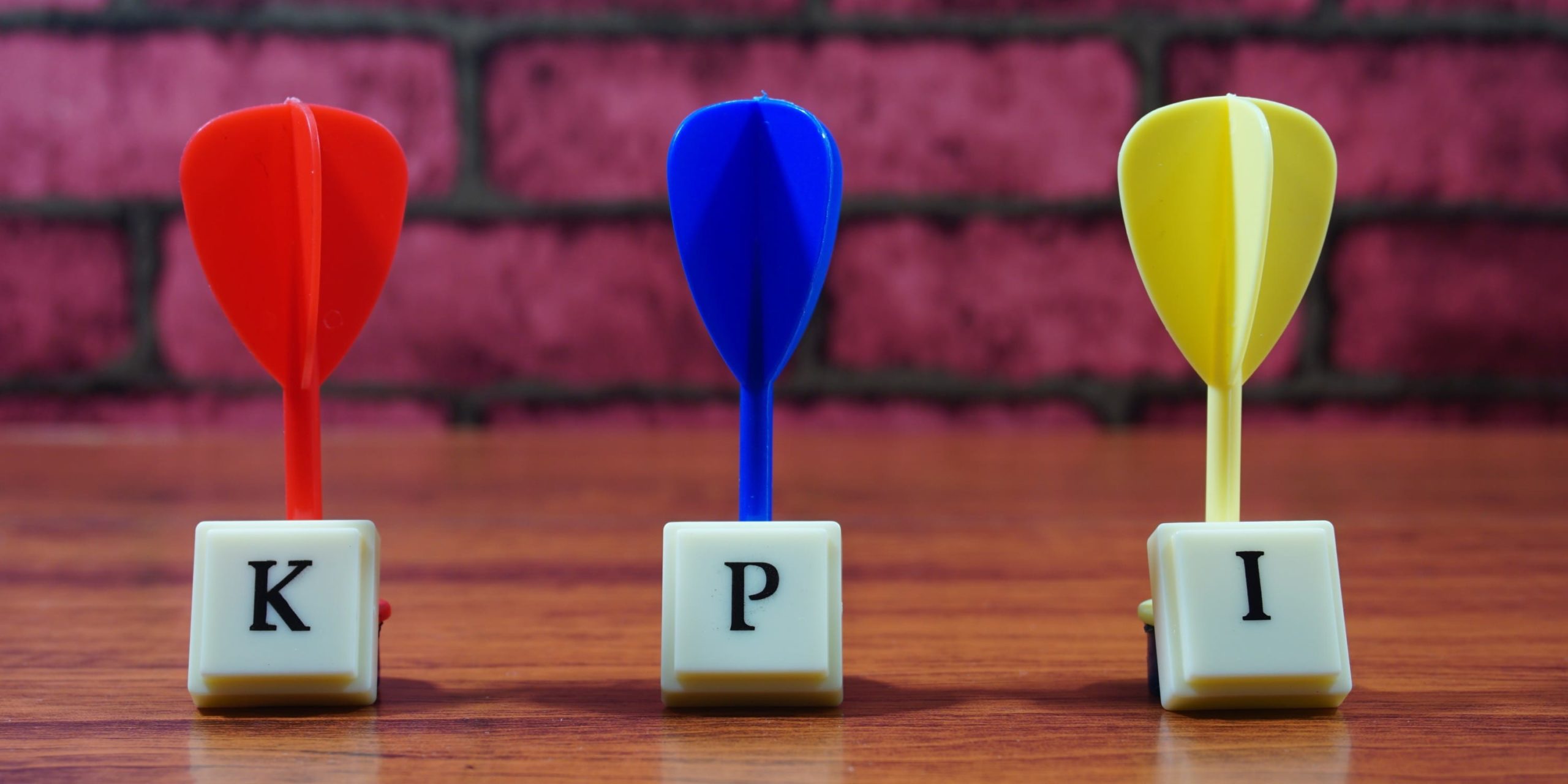
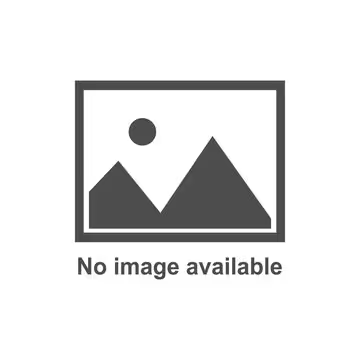
INTERVIEW – In this thought-provoking conversation, Michael Ballé and Mark Graban discuss metrics and the managerial attitude towards tracking them.

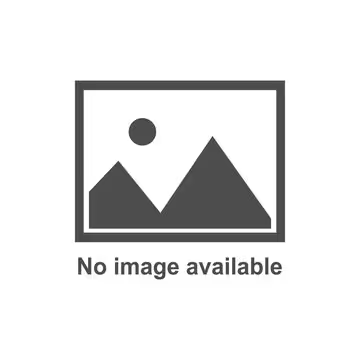
CASE STUDY – Lean allowed NGNY to evolve from creative improvisation to structured performance by redesigning operations and standardizing processes – achieving reliable deliveries, built-in quality, and a cultural transformation.