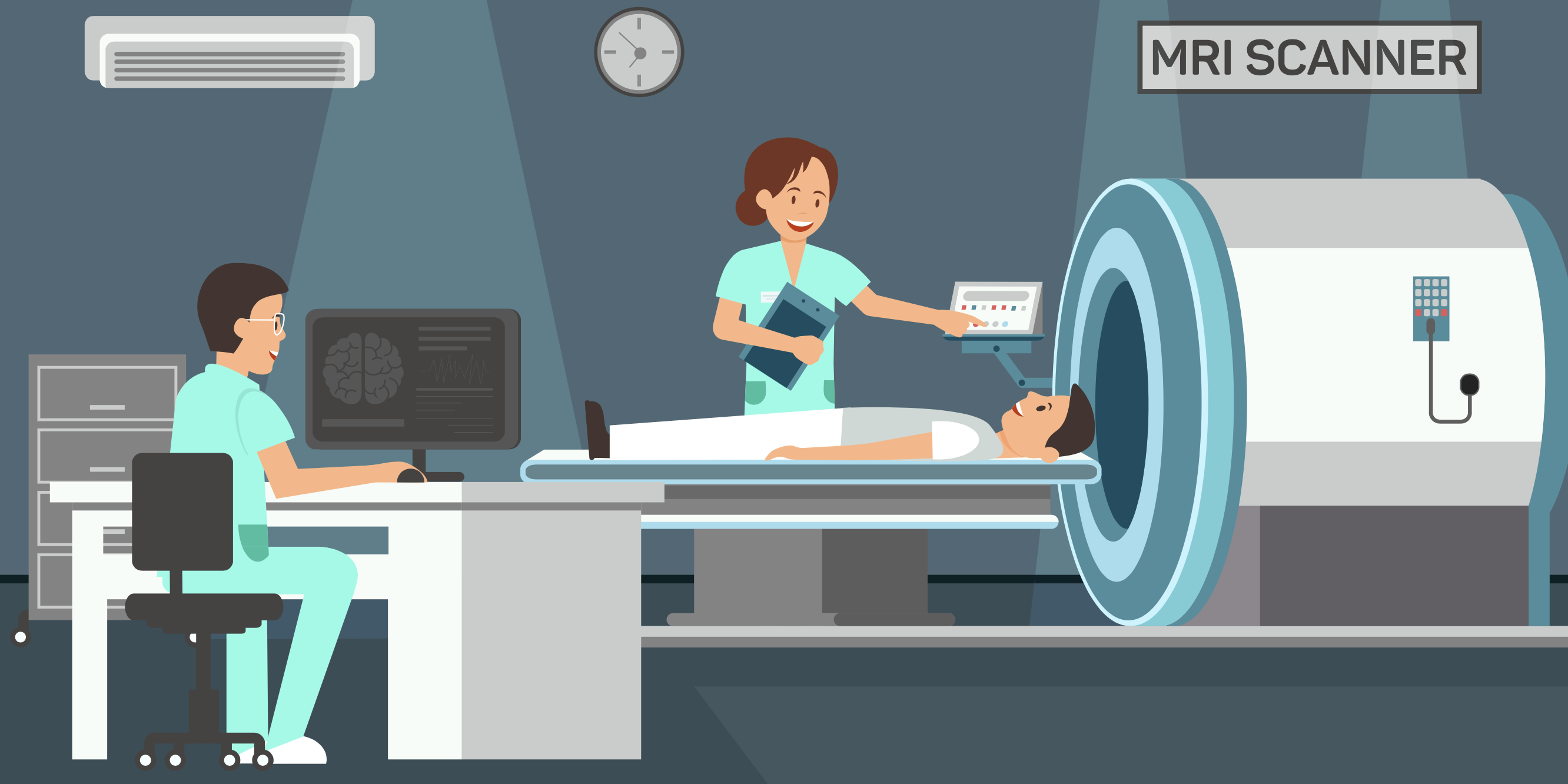
Enabling change with a value stream Jishuken
FEATURE – In March 2019, this hospital partnered with the Lean Global Network on a two-day Jishuken event. Nearly two years later, the authors reflect on the legacy of that initiative.
Words: Linda Lam, Performance Improvement Manager, and Denise Bennett, Lean Coach, Lean Global Network
LINDA LAM, PERFORMANCE IMPROVEMENT MANAGER
In March 2019, Stanford Children’s Health partnered with the Lean Global Network to host a two-day value stream Jishuken event in the MRI department. It was incredibly productive and fast-paced, filled with gemba, coaching, and experimentation. The combination of concentrated time to work together, with the views and ideas from a diverse group of participants – ranging from front line team members to project sponsors and lean coaches from across the globe – was key to the event’s success.
The two-day workshop kicked off three workgroups that used the momentum of the event to trial and learn from experiments across the value stream. The event created energy and excitement in the group, and people were able to see and learn things that could not be seen in the mire of day-to-day operations. You can learn about the event in this video:
While we were successful with a few trials after the event, the department experienced staffing challenges and leadership turnover which created instability and challenged our ability to progress and sustain the work. Experimenting on this unstable foundation made it impossible to truly study improvement results and adjust. We could only get so far without the front wheel of the Packard Quality Management System bicycle – the daily management system that is supported by standard work, visual practice, tiered huddles, and leader standard work (LSW). So we pivoted.
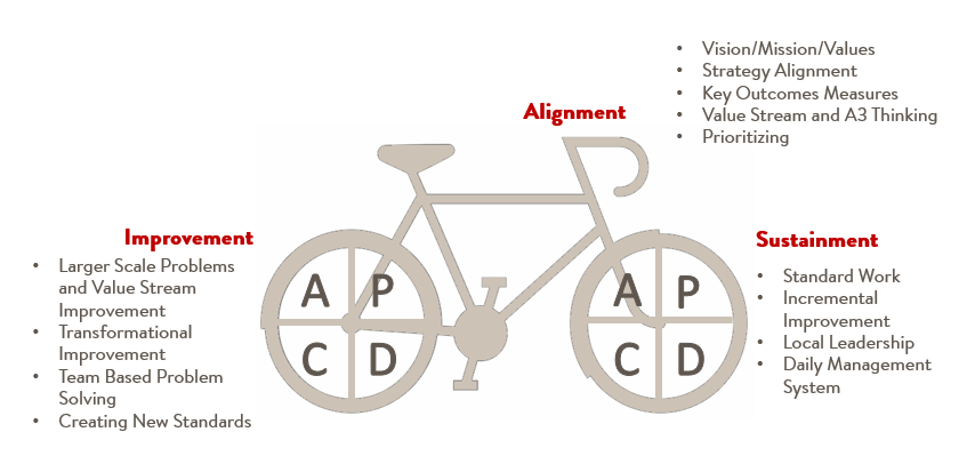
Our front-line leaders have implemented a daily morning huddle involving front-line staff from multiple disciplines (technologists, nurses, radiologists, anaesthesiologists, child life specialists, and radiology schedulers) to cover daily readiness, recognition, and daily problem solving. A year ago, same-day issues – often linked to overlapping concerns – would arise throughout the day in separate professional group huddles for separate roles and stakeholders at varying levels would jump in in a disjointed yet well intended effort to extinguish fires. And yet the problem would still snowball. One year later, consistent multidisciplinary huddles twice daily have become part of our way of working. The team can rely on this platform to raise and escalate concerns, troubleshoot issues, and triage larger problems appropriately.
This effort to build the management system included an iteration and revitalization of the Everyday Improvement Idea (EII) system for Radiology. This leverages the knowledge and ideas of the front-line staff to drive improvements and creates a venue for the front-line leaders to practice their coaching skills with their staff on problem solving. To further build the lean capabilities of the leaders, our Performance Improvement team coached the front-line leaders in their development of leader standard work (LSW). It created structure for them to practice reflection on their role in daily operational support with a focus on work prioritization, flow management, gemba, problem solving, coaching, and monitoring performance metrics like First Case On Time Starts (FCOTS). This, together with the rigor and consistency of the daily huddles, created more bandwidth for mid-level managers to shift the focus of their LSW to developing the team and supporting the team to achieve goals. At the peak of their commitment to LSW, the FCOTS average increased from 40% (September 2019 – November 2019) to 62% (November 2019 to March 2020), showing what impact this can have on department goals.
The path to developing this stable management system for MRI was not direct, but the collective journey towards it fostered the buy-in and engagement needed for this to be a solid foundation amidst a pandemic and for future larger value stream improvements efforts.
DENISE BENNETT, LEAN COACH
The improvement journey of the MRI team at Stanford Children’s Health has not taken the route we expected, but that isn’t to say that Jishuken-style value stream improvement event we ran in March 2019 was not important for the organization.
First of all, it’s important to highlight one critical difference between a Jishuken event and a Kaizen event, which lies in the involvement of senior leaders. In a Jishuken activity, managers immerse themselves in the whole event program to help the team understand the problems, learn and develop their problem-solving capability, rather than just supporting and endorsing whatever suggestions may come from the front line. The inclusion of clinical and non-clinical senior leaders was fundamental to the design of our event at Stanford Children’s Health. They worked “hands-on”, together and at gemba to learn deeply about their value stream and each other’s perspectives. They were also exposed to new problem-solving techniques and ways of analyzing and redesigning a value stream. With the dedicated two days offline, they could give the improvement work their full attention. Their involvement and passion for the work is evident in the video above.
It had been some time since Stanford Children’s Health had focused on value stream improvement. Much of the work in the organization in recent years had focused on strengthening the management system, building improvement capability and a couple of large and important improvement initiatives. The intentional focus on an end-to-end value stream created the environment to get back to the basics of Lean Thinking and Practice and reinvigorate the improvement team by teaching some infrequently used skills. The coming together of four diversely experienced healthcare coaches was phenomenal and we all, including the coaches, learned a lot. Much of the future state design thinking that was developed in the Jishuken activity has not yet reached implementation, but many of the concepts have been integrated in the work that has taken place. Other design ideas will likely be re-visited in the future as team stability increases.
The work of the improvement team and leadership in recognizing the need for and committing to front-line leader standard work (LSW) has been an experience of rich learning. In fact, it has likely been the deepest learning experience in LSW in the organization to date and one that has resulted in these methods being shared in other areas, like pharmacy and peri-operative services – what we refer to as “cross-pollination”.
This Jishuken event was helpful in many ways. It brought key people together to learn, understand and commit to moving forward. The work that the team has done benefited both patients and staff. And those involved in the improvement have developed their skills and coaching capability as a consequence of the experience.
THE AUTHORS
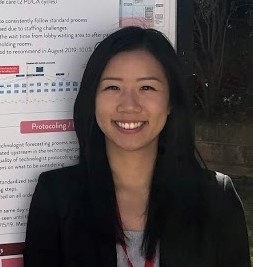
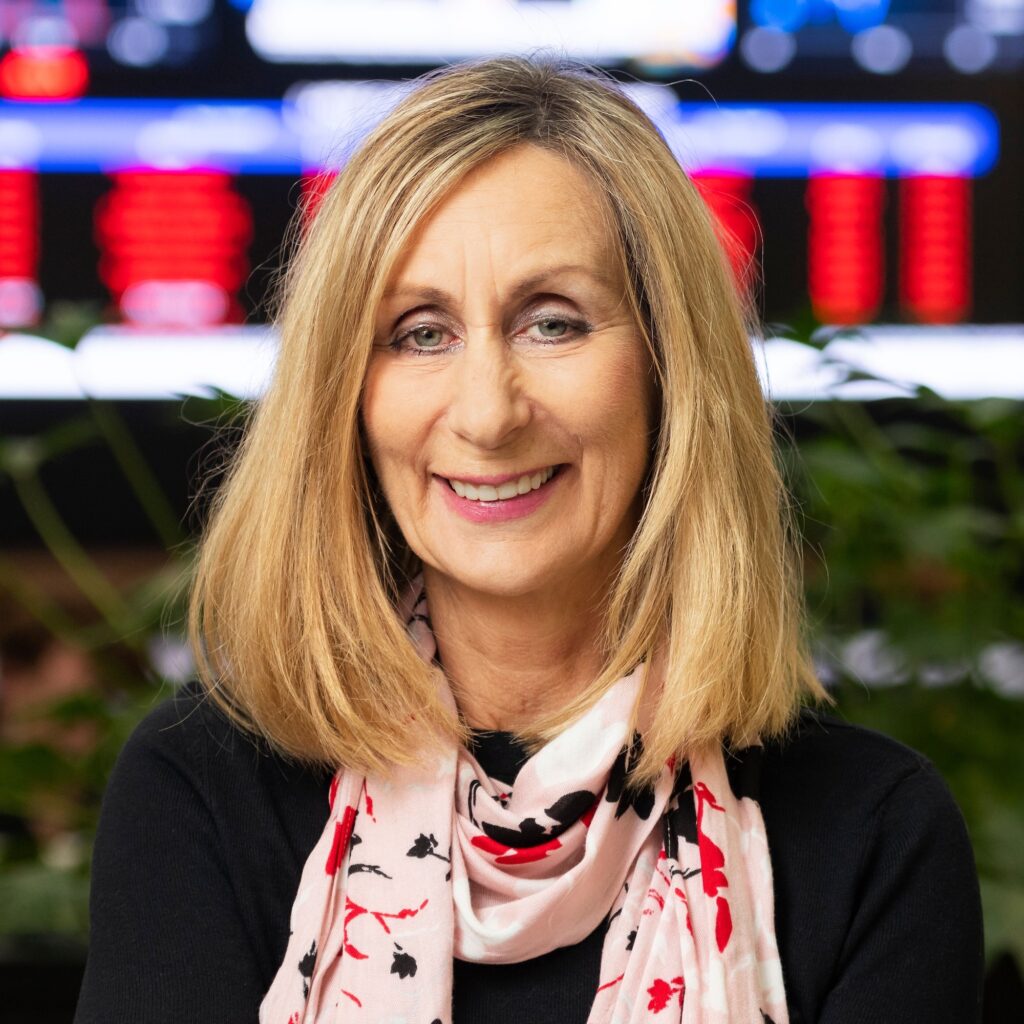
Read more
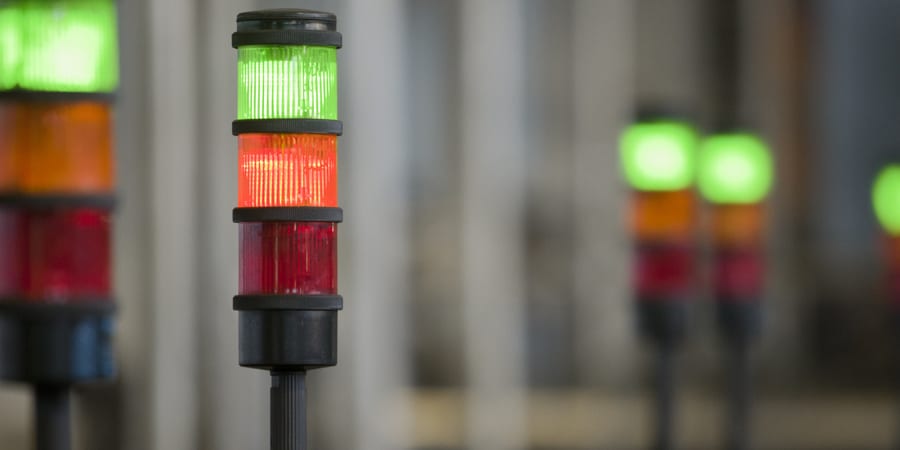
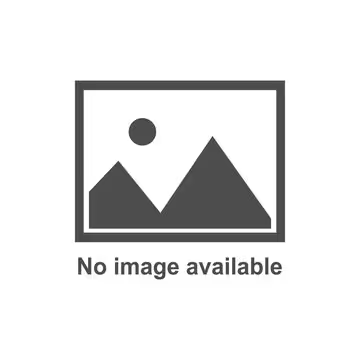
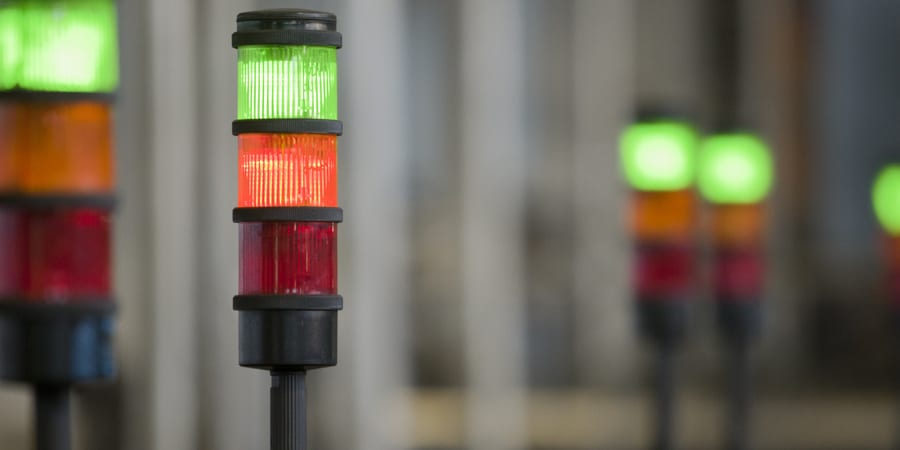
VIDEO - The author of Lean with Lean explains why he published a collection of papers rather than a business novel - his signature writing style - or a manual. Experience lean through the eyes of one of its greatest students... one a-ha moment at a time.
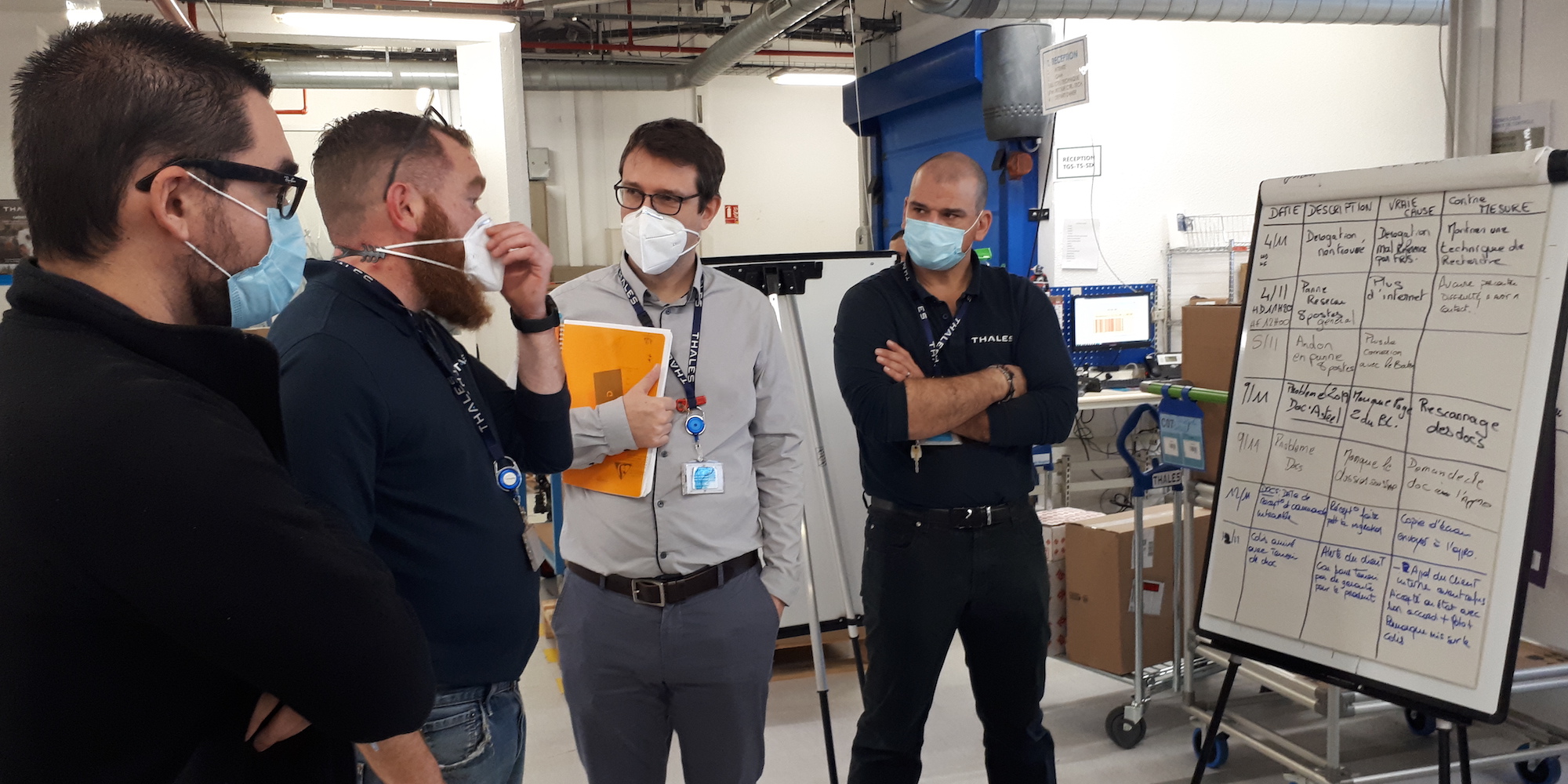
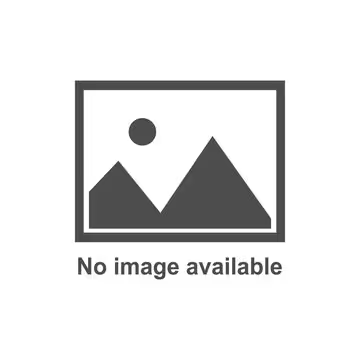
NOTES FROM THE GEMBA – Thanks to the effective application of Just-in-time and Jidoka, Thales LAS has managed to turn around its logistics department. Catherine Chabiron reports.
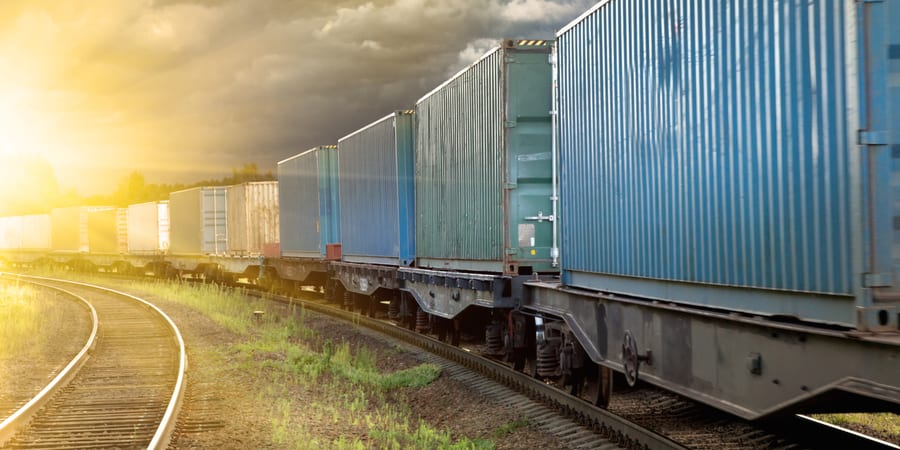
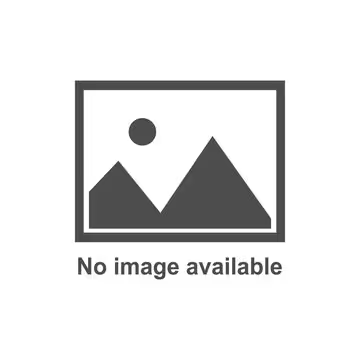
FEATURE – Starting off a lean journey is no easy feat, and existing models won’t tell you what the next steps are. That’s why you should go back to basics and let the Toyota Production System “house” from the mid-1980s show you the way.
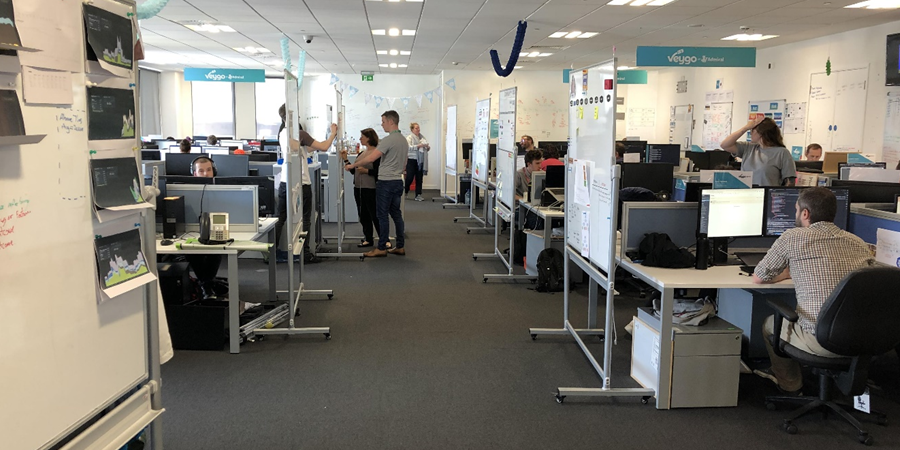
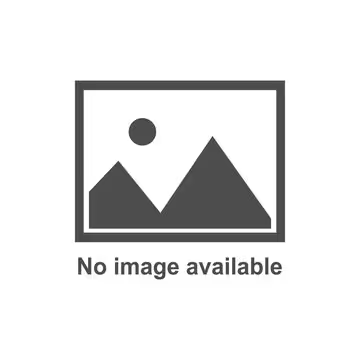
NOTES FROM THE (VIRTUAL) GEMBA – This week, the author chats with an innovative insurance company as it relies on its lean learnings to ensure business continuity and switch to remote working during the Covid-19 crisis.