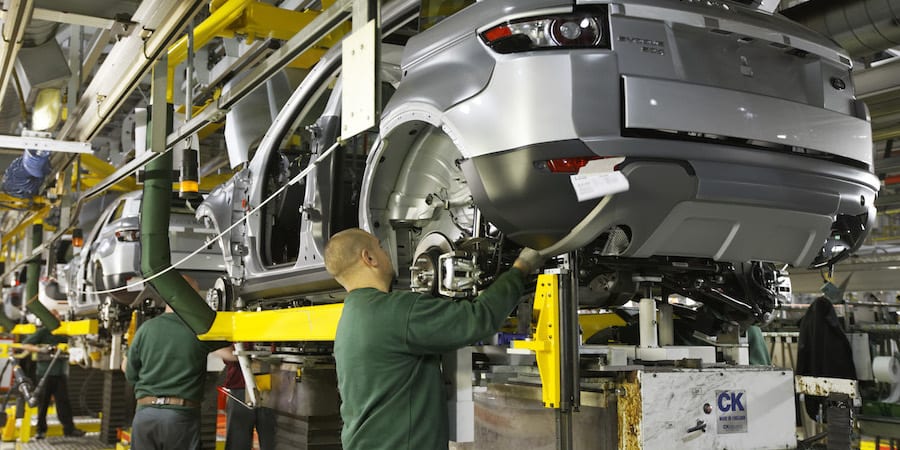
Lean product development for new Jaguar Land Rover vehicles
INTERVIEW – Following two successful experiments with kanban boards, Jaguar Land Rover decided to extend the reach of its lean product development activities to include all new vehicle programs. Here’s how the story unfolded.
Interviewee: Hamish McMinn, Automotive and IT Project Manager, Jaguar Land Rover
Planet Lean: Jaguar Land Rover has recently started to apply lean principles to its product development activities. Tell us about this experience.
The pace of innovation is accelerating and developments in vehicle technologies add to increasing complexity. These converging trends present exciting engineering challenges and require increasingly rapid product development capability. We see great opportunities in borrowing ideas from the agile software community and adapting them to new vehicle development. We began in earnest in 2014 by tracking CAD progression on a kanban board.
We really knew we were onto something, with significant results about six months in, when an external report captured the positive effects these changes were having on the vehicle program. A year after we started, we looked back and found more evidence of the difference lean product development was making: with a team 30% smaller than usual, we were seeing CAD quality up and delivery times improved, despite massive late changes imposed.
A second program gave even better improvements in quality and delivery times and now we have a remit to apply to all new vehicle programs.
PL: Can you share some of the results? What are the main benefits you have seen?
HM: We use the kanban board to give everyone real-time visibility of design progression, blockers, WIP, issues, etc. This increases our cross-functional bandwidth enormously, accelerating collaboration and issue resolution. We have focused on shortening feedback loops to get much earlier detection and correction of errors. The design phase is made up of quality loops, typically 12 weeks in length, resulting in a data freeze for analysis. Ordinarily, many design problems go undetected until after a data freeze, causing delays.
Long feedback loops, combined with freezing all options and variants of the vehicle, creates massive batches and unstable delivery. By applying lean principles, we have shortened the feedback loops from 12 weeks down to a few days: geometry checks now happen overnight and are carried out independently.
The changes we have implemented have made a huge difference, allowing us to detect and correct problems before a freeze event resulting in much better quality in the frozen data.
PL: Many of the principles popularized by the Lean Startup movement have found an application in lean product development, but it is often hard to understand how. For instance, how does the idea of minimum viable product apply to an organization like Jaguar Land Rover?
HM: In software development, an MVP is something that you can actually ship to the customer – a beta-version, or embryonic version of your product that you can use to market test your value proposition with real customers. Future, incremental improvements are then shipped to the customer.
We haven’t used the MVP concept at Jaguar Land Rover yet, as it is clear that we can’t ship small increments of a car – it has to be homologated and tested, and must be complete when it reaches the customer.
So, we can’t borrow the concept of MVP wholesale, but we can use the idea – in the three-four years of development, from concept to production launch, there are many intermediate stages and thousands of “client-supplier” relationships, hand-offs and deliveries. If we think in terms of those value streams and the (internal) customers in those data transfers, we can then apply the concept many times over.
It’s about decomposing large batches into smaller ones. If we ask our internal data customers what they need in a data freeze, many will say they need the whole vehicle. But in many cases a few critical sub-systems are enough. We are optimizing our delivery of test properties for validation so that we get rapid feedback with confidence. This relies on greater coordination, and visual management using kanban gives us this capability.
PL: How do you ensure communication is effective and problems are dealt with?
HM: The kanban boards themselves are our main communication media. They are visible and editable by everyone and are updated by users in real time giving accurate status in great detail. This is augmented through our daily standup meetings – the first 15 minutes focus on the kanban board, engineering heads highlight the things holding them up and what help they need to progress. Problems are referred either to ad hoc meetings or within existing meeting formats (like a package review or a must-resolve meeting). The real key to success is ensuring that the team recognizes and responds promptly to the signals the board provides. We are rapidly gaining advocates and they are driving the improvements we see.
THE INTERVIEWEE
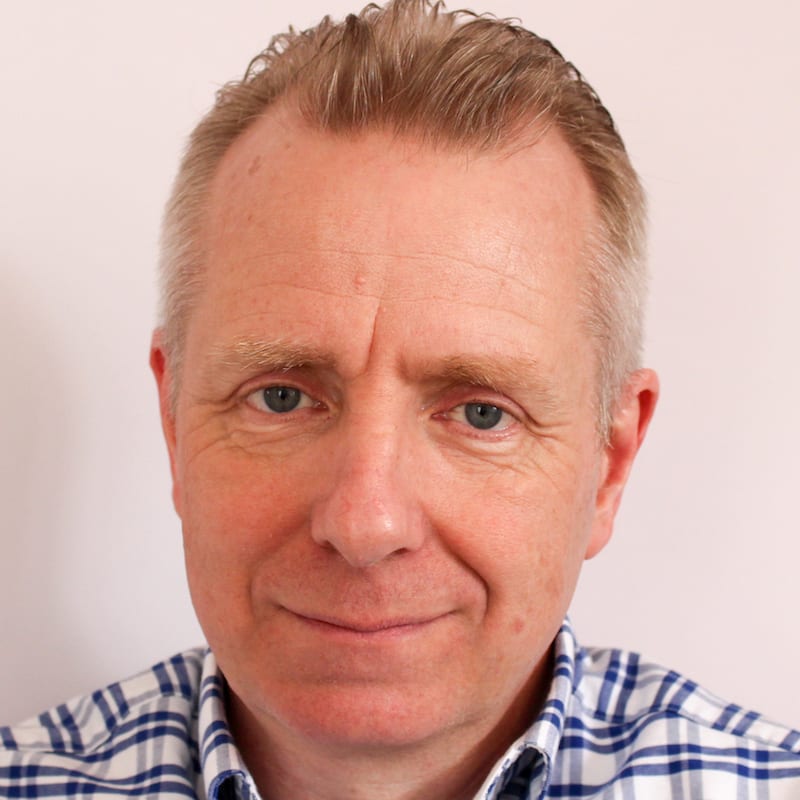
Read more
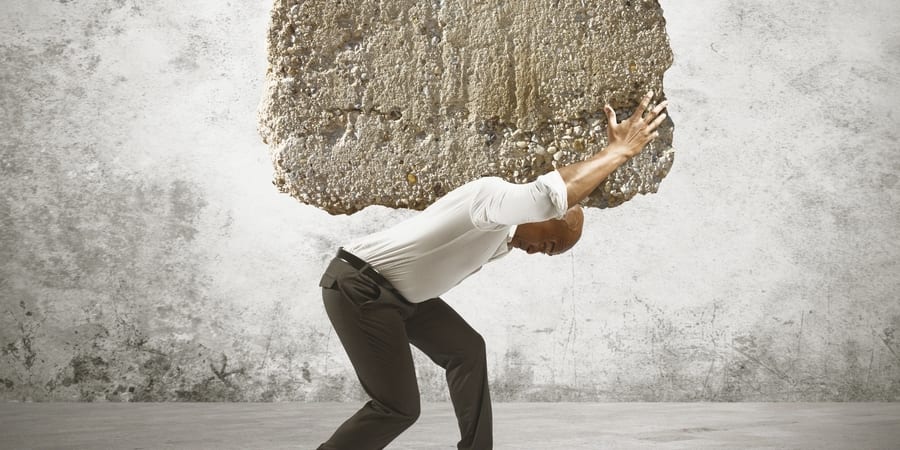
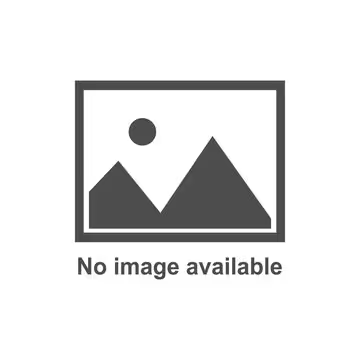
FEATURE - Stressed and overwhelmed by workload? Once again, lean thinking comes to the rescue, offering us a way to approach our work that helps us eliminate waste, save time, and avert breakdowns.
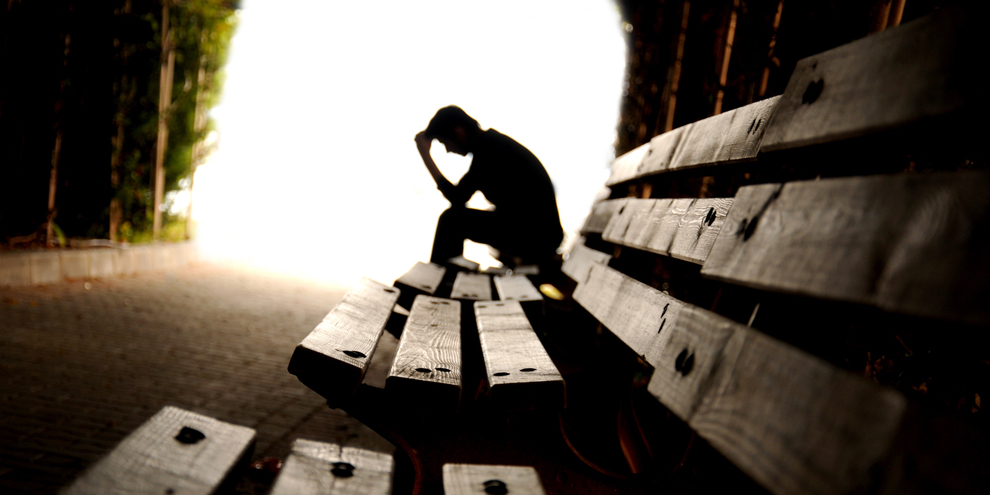
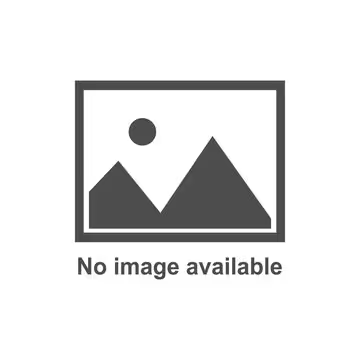
FEATURE – In the face of uncertainty, when it’s hard to see the road ahead, we can still make things better day after day by embracing kaizen – until we are out of the woods.
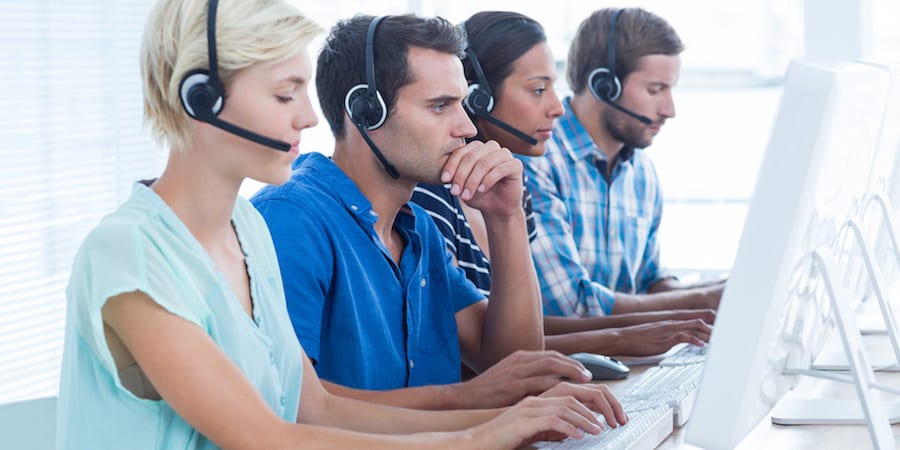
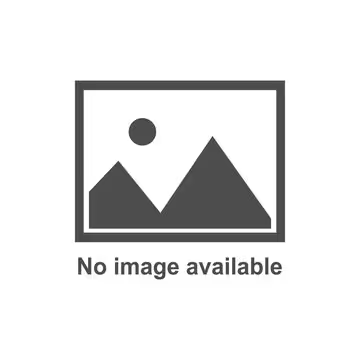
INTERVIEW – With more and more organizations in the service sector adopting lean thinking to turn around their modus operandi, it only makes sense to highlight the struggles and misconceptions they still encounter.
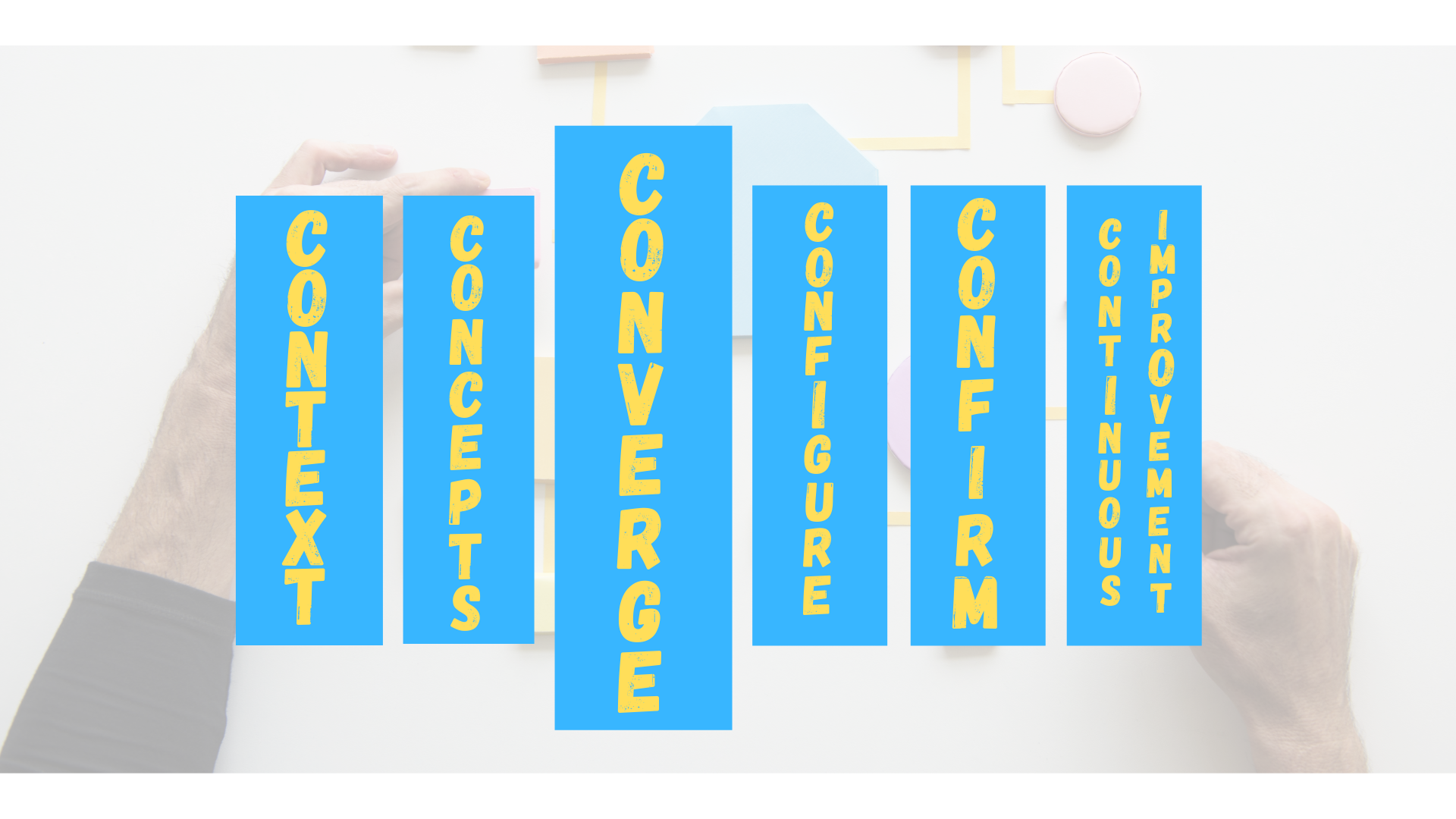
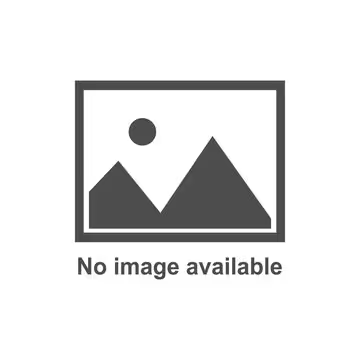
SERIES – The authors discuss the third of six elements in their process development model – Converge – using experiments to test key aspects of different ideas, while objectively working towards a single design concept slated for refinement and implementation.