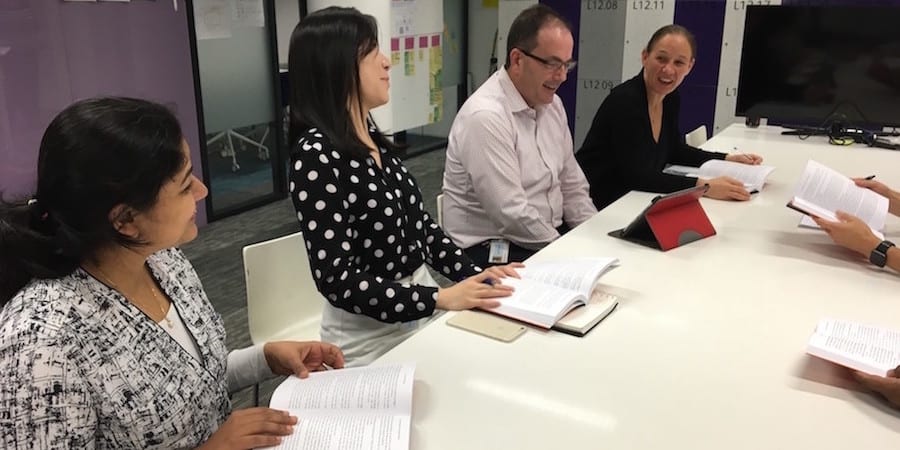
How a book club helped Fuji Xerox Australia support lean
FEATURE – Upon realizing they were struggling to engage people in continuous improvement, Fuji Xerox Australia’s IT team found a unique way to breathe new life into its lean efforts… a book club.
Words: Mike Schembri, Corporate Services Manager, Fuji Xerox Australia
In 2014 I took over the IT group at Fuji Xerox Australia. My vision was to transform it from a fairly traditional, hierarchal, top-down and somewhat insular structure to one characterized by individual empowerment and customer centricity. That’s how the Awesome IS(IT) strategy was born.
Initially, we focused on implementing agile methods within IT, engaging an agile coach, introducing huddles and tracking projects and performance metrics visually (using visual management tools).
The daily huddles, in particular, allowed us to make collaboration within IS a “way of life.” This expanded over time, so that for critical business events like month end, the Finance Team would join the IT ERP team huddle daily to understand the status of the work, raise any issues and take action in real time. This reduced the number of “surprises” I received: with problems being dealt with in real time, the instances of non-performance that had to be escalated went down to zero.
Over time, however, we realized that our huddles were still very much led by managers, with employees reporting what they were doing on a daily basis and awaiting directions.
We started to see problems with our visual management efforts, too. While boards effectively provided us with full visibility over our projects – helping our employees to hold themselves accountable and visualize their workload, while limiting the amount of tasks they could schedule at any one time due to the defined space available on the board – we found that visualizing tasks in high-volume low-complexity environments like the Help Desk just wasn’t working.
We were visibly improving. With huddles becoming more and more frequent, managers were able to course-correct more quickly and, as a consequence, the amount of projects delivered on time was going up, as were service level metrics and customer satisfaction. However, whenever managers were not around, the team seemed lost and often didn’t meet at all. Our team’ culture was still very top-down.
Upon reflection, we came to realize that huddles and visual management had simply become a more efficient way to run a top-down organization rather than a tool to transform our business and engage our people.
I knew we needed something more to truly change our organizational culture. I just didn’t know what.
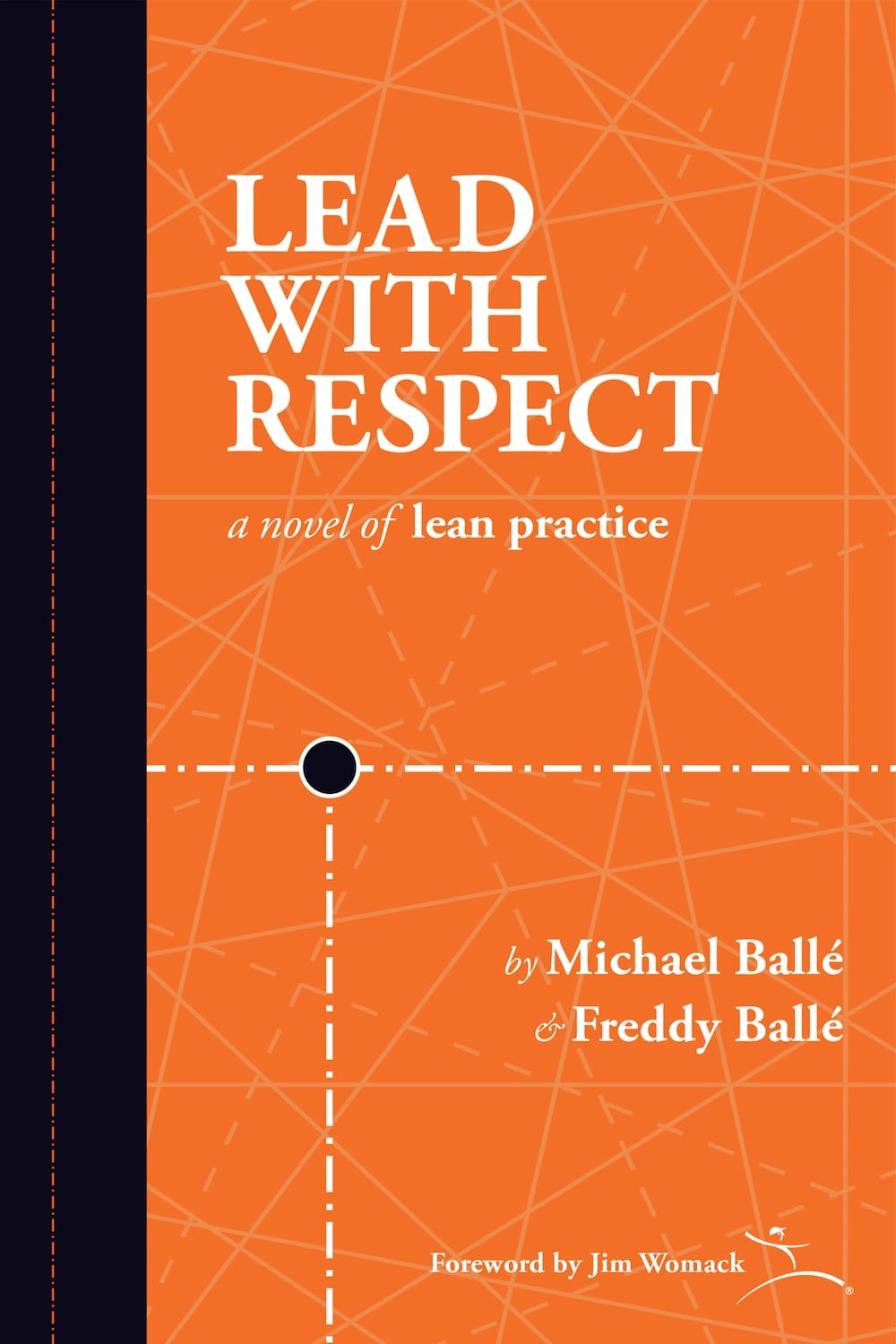
In early 2015, quite by accident, I was ordering some more copies of John Shook’s Managing to Learn, when I came across Michael Ballé’s trilogy of lean novels. With several international trips planned for that month, I decided to download the Goldmine trilogy to my device. I spent my time on the planes reading them, and I was completely hooked.
I found Lead with Respect (the third book in the trilogy) to be directly relevant to what we were trying to achieve at Fuji Xerox Australia. The novel tells the story of an IT company’s transformation, and teaches us that our people have a “right to succeed”and that we as leaders have a responsibility to create an environment that allows that to happen. This, I thought, was the ideal reference for leaders who are trying to grasp the real meaning of lean thinking and introduce its principles in their teams.
Upon returning from my trips overseas, I started a little Book Club with my Senior Leadership Team and began to study Lead with Respect with them, one chapter per week over the course of a few months. We then launched more book clubs, first for all IT Leaders and then for all IT Staff. We found this to be a great way to embed lean principles in the organization, and we are still using the book to develop lean leaders at all levels of the IT department (not just our managers).
Through our study and a number of discussions with Michael Ballé (who launched several of our book clubs), we came to see that visual management and huddles had indeed allowed us to “clean the window” and see the work more clearly, but had failed to engage our people in kaizen to improve that work.
That’s why our next focus became “bottom-up kaizen.” We wanted individuals and operational teams to drive their own step change improvements.
A small but culturally significant change we made at this time was the “re-ordering” of our huddles: senior leaders used to meet at 8:30am and huddles then cascaded down through the company’s structure, but we decided to reverse this so that operational teams could meet first and escalate any issues that might occur up until I met with senior leaders at 10:30 each morning. By that time we had a completely clear picture of the status of operations and of the issues of the day. What I noticed was that with this arrangement operational teams were much more likely to not only report issues, but also propose countermeasures and take action to fix them.
In addition, we have been running multiple experiments with teams to build small kaizen efforts themselves. Some have been immensely successful and others haven’t, of course, but we have learned from each and every one of them. I have seen our teams change and grow in the process.
Our group study of Lead with Respect and other lean books has changed our culture faster than I had expected, helping IT to define our True North and giving us a platform for having the sometimes difficult discussions about what is expected with our leaders and people. (Interestingly, some leaders and staff appeared to be uncomfortable with a bottom-up organizational culture and actively chose to leave the company.)
My team and I received much credit for the transformation of the IT group, as our colleagues across the business saw how we built a thinking team that could drive and deliver improvement organically. Many other FXA teams ended up adopting our lean/agile practices, and we still give away a couple of copies of Lead with Respect to visiting managers form other divisions each month.
I have recently gone on to lead FXA’s Corporate Services Group (IT, Billing and Procurement) and it will be interesting too see the impact of lean methods on a highly transactional environment like billing. What’s certain is that we will keep our focus on leading with respect and giving our employees the right to succeed… our book club in the new group has already been launched.
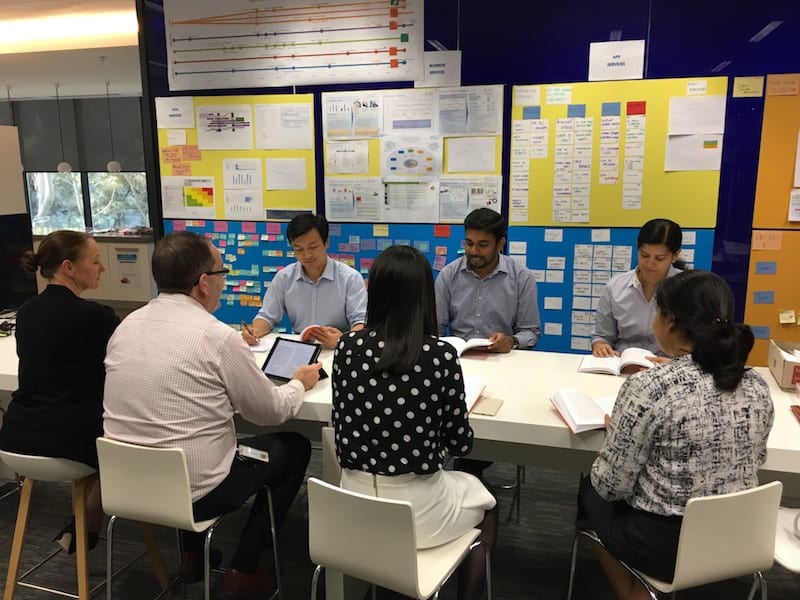
The views expressed in this article are mine and do not necessarily reflect the views of Fuji Xerox Australia
THE AUTHOR
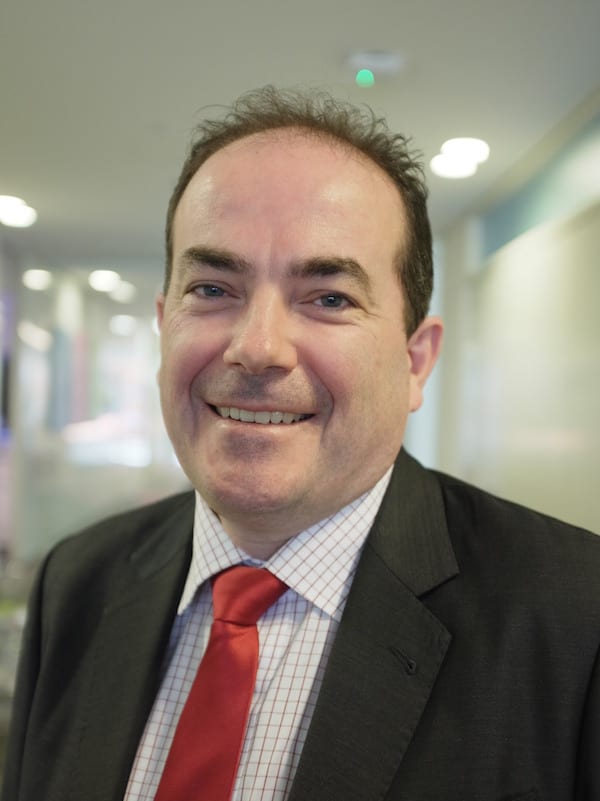
Read more
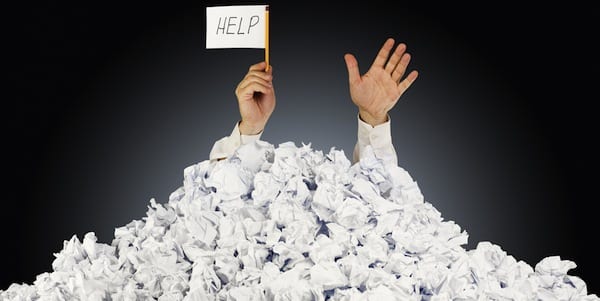
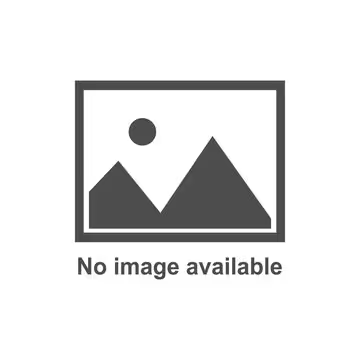
FEATURE - Develop your people if you want to develop a better (lean management) system in your business. This is the key message of this article, which looks at the role of management in an organization and in society.
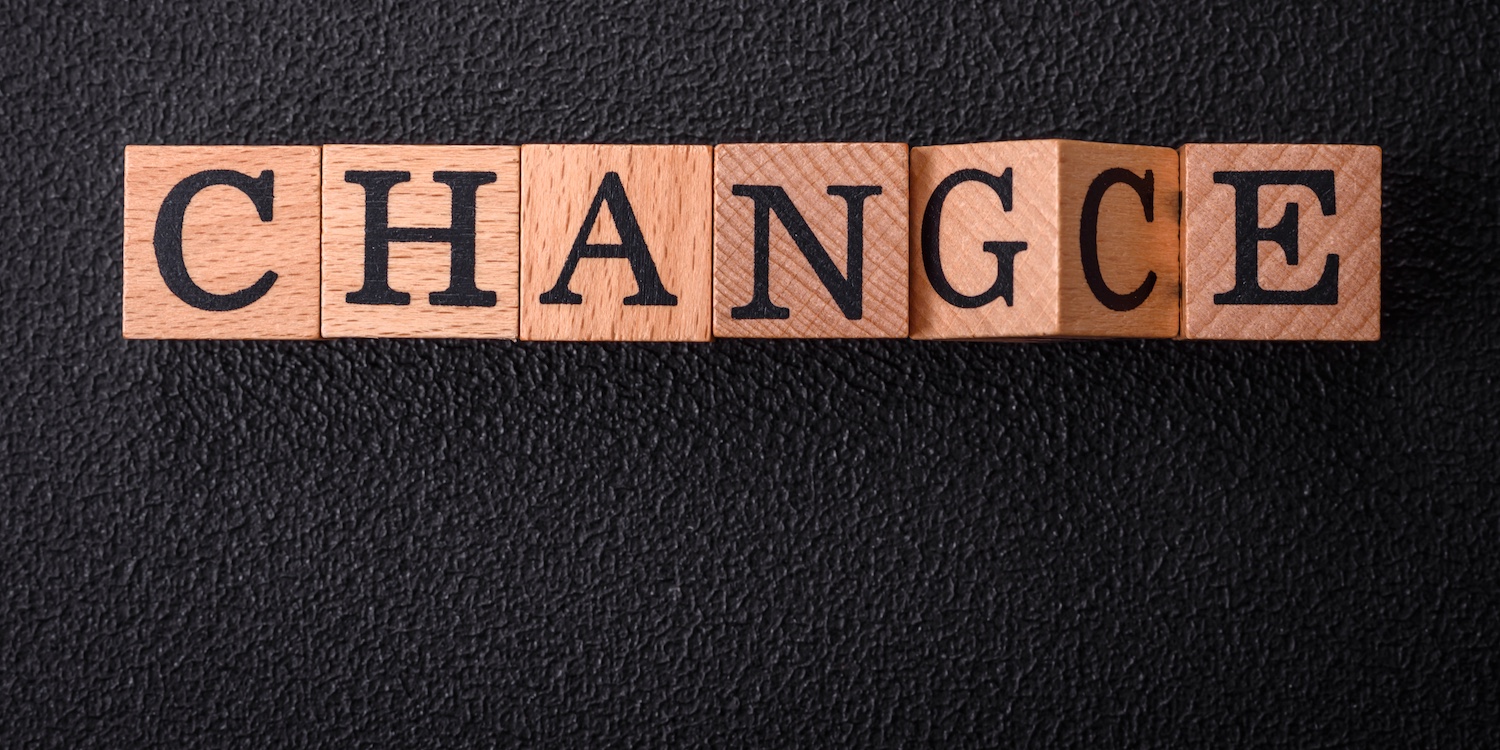
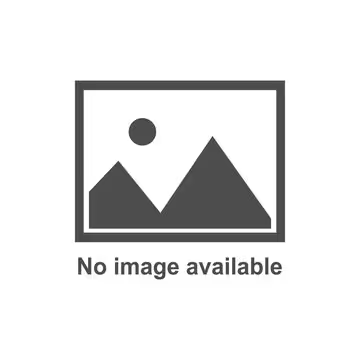
FEATURE – Ahead of his presentation at next week’s Lean Global Connection, Jim Womack explains why Lean is made for a world in turmoil but urges us to strike a balance between immediate response and thorough understanding of the problem.
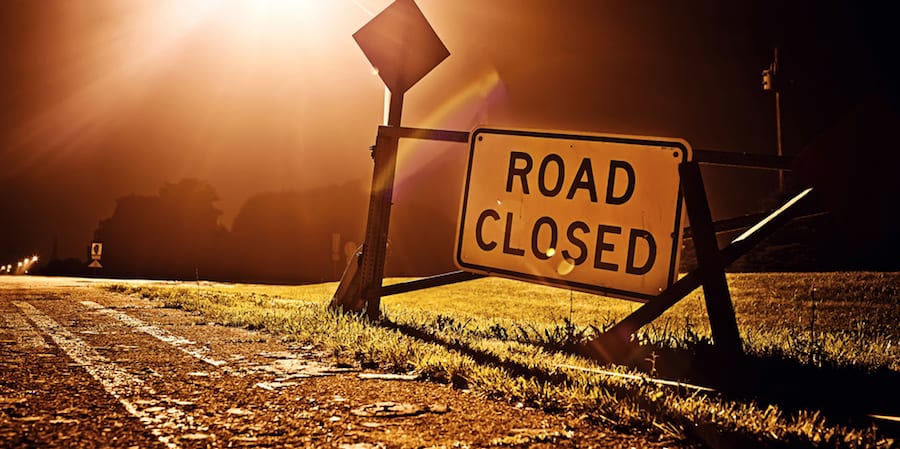
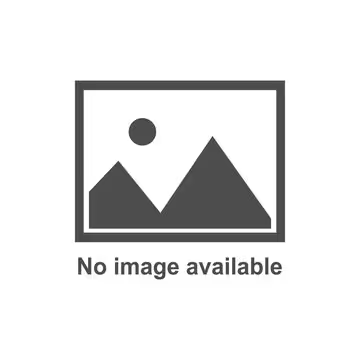
FEATURE – Is your organization experiencing any of the strategic planning problems described in this article? If so, it might be time to tap into the potential of hoshin kanri.

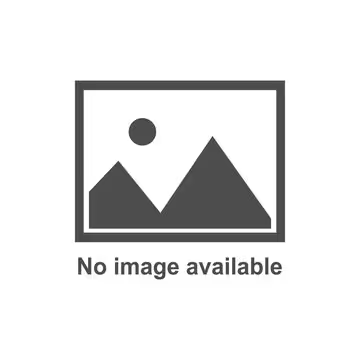
FEATURE – Introducing initial assessments by senior doctors and bedside diagnostics to improve the efficiency of the Emergency Department: a lean healthcare experiment in England.