
An eye for improvement
INTERVIEW – At last month’s International Lean Summit in Hungary, our editor sat down with the manager of a CooperVision site that is gradually converting its operations to make them leaner.
Interviewee: Balázs Sebestyén, Managing Director and Plant Manager, CooperVision Hungary
Roberto Priolo: The manufacturing process for disposable contact lenses is very interesting. Can you briefly describe it for our readers?
Balázs Sebestyén: The first step is the creation of a liquid lens material which is a complex mixture for which CooperVision has its own “special recipe”. In truth, however, the key step in the manufacture of soft contact lenses is injection molding. We have two molds between which the monomer is injected. This is the step in the process in which the contact lens is given its shape, depending on the type of prescription we are producing. (Naturally, there are lots of variation there, hence our high number of SKUs).
Once the monomer is injected between the two shapes, we utilize a curing process to create a polymer. From this process comes a semi-rigid polymer contact lens that we then further process to obtain the contact lens in its final form. After that, we package the lenses in two steps: first, we place them in plastic holders and then we place the holders in the cardboard containers people can buy at the optician.
RP: Thanks to lean, the site you run – located outside of Budapest – is going through a lot of change. Can you tell us about the problems with the traditional design?
BS: The process in our site was designed for a different era, when the company wanted to minimize the amount of working capital tied up and maximizing equipment utilization inside the controlled environment (clean rooms are notoriously expensive to run, so it makes a lot of sense to try and make the most of space and resources within them). However, it wasn’t about efficiency or productivity, which is striving to boost by redesigning the process with Lean Thinking in mind.
The main problem with our traditional process is that our controlled environments are not conducive to effective problem solving. The layout and configuration of the clean rooms make it hard to train people, limits their ability to solve problems, and is far from the visual factory we’d like to work in. One of our biggest issues is inventory: within the controlled environment, the manufacturing process takes one week and there is a lot of stock all around. This inventory prevents us from seeing issues and ultimately makes it very challenging to improve our performance. So, we decided to change our approach drastically.
RP: What is the new, lean process like?
BS: We have begun two years ago by converting one of our three controlled environments (with the help of Lean Enterprise Institute Hungary), making it more operator friendly. We raised the ceiling, placed windows to make the process transparent, and created dedicated transportation routes so that material movement could be automated (using AMRs, Autonomous Mobile Robots). The deployment of robots forced us to standardize logistics flows and the trigger that goes out to the warehouse whenever materials are needed on the production line. More importantly, the new process follows the logic of flow, with better visibility of the end-to-end process and less stock.
We also created a value stream organization, to “shake things up” and encourage people to step out of their comfort zones. They are engaging more, and along the way, we are reacting to problems faster thanks to a smoother information flow. We are learning by doing, “lowering the water level” – so to speak – so we can expose more and more problems.
With each clean room taking 12 months to convert, this is clearly an ambitious project. There is no doubt, however, that the new system is more efficient than the traditional one.
RP: With such a tech-heavy process, what are your thoughts on the coexistence between technology and human activity in the context of this lean turnaround?
BS: This is a heavily automated process indeed. CooperVision has been strong in the past on the automation of our core technologies and the lean conversion of the clean room has hardly touched any of that. All we did was joining the molding step with what we call fill-and-close. The greatest changes are happening on the industrial engineering and lean side of things – material movement, visualization, standardization in storage and material handling, stock levels, stopping the line when defects are detected, and so on. I personally believe that high levels of automation and Lean Thinking can coexist perfectly.
RP: Speaking of lean, how did people react to these changes?
BS: This plant has been operating for a decade with the same mindset: growing by expanding capacity. The new approach is completely different and entails a lot of change management. As we implemented the lean changes to one of our three clean rooms, there was concern among the operators. The workplace was changing drastically, and they were somewhat anxious. Within a month or two, however, concerns faded away and the atmosphere rapidly turned very positive.
I think there are two reasons behind that: we were very transparent about the reasons we are doing this, and we heavily involved people in the redesign. We asked them what physical changes to the layout they wanted to see, to make their job easier. Here’s an example: once the curing is over, operators need to walk to the ovens to remove the polymer contact lenses. In the old process, they had to walk by each chamber to check whether the curing was complete or not. Now that we installed a big screen which monitors the state of the curing process for each of the 36 ovens, they don’t need to walk as much. Their time is not being wasted anymore. It was a simple change, but it made their lives so much easier. There is no better way to fight resistance and make change self-sustaining than showing people how the changes we are implementing will benefit them.
RP: What is your timeline for the conversion of the rest of the plant?
BS: As I mentioned, our manufacturing site has three controlled environments, of which we have converted one for now. The plan is to convert the rest over the next three years. This is a one-year process that has to be planned carefully because in order to rearrange operations we need to take capacity out.
We are currently busy observing the converted clean room to see how it performs at full capacity, stress-testing it. It’s kind of like a model line for us! We are trying to understand what we missed, what parts of its layout can be further improved, so that the other two controlled environments can be better iterations of the process.
This article is also available in Hungarian here
THE INTERVIEWEE
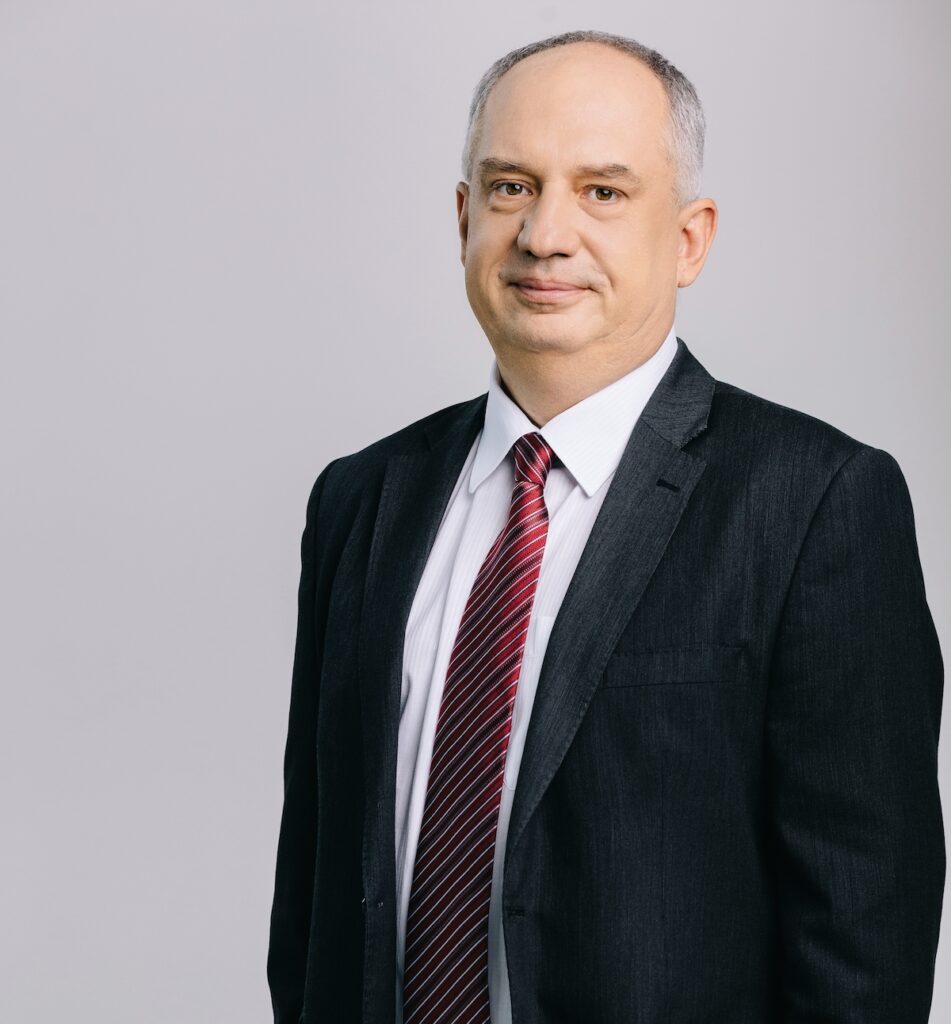
Read more
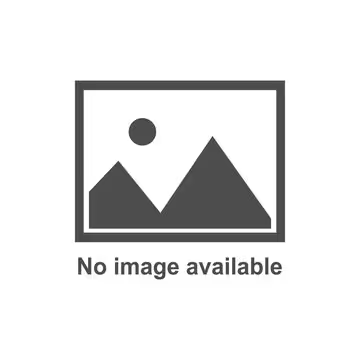
CASE STUDY – Faced with safety and quality issues, this Brazilian manufacturing plant installed a dojo, and the results are very promising.
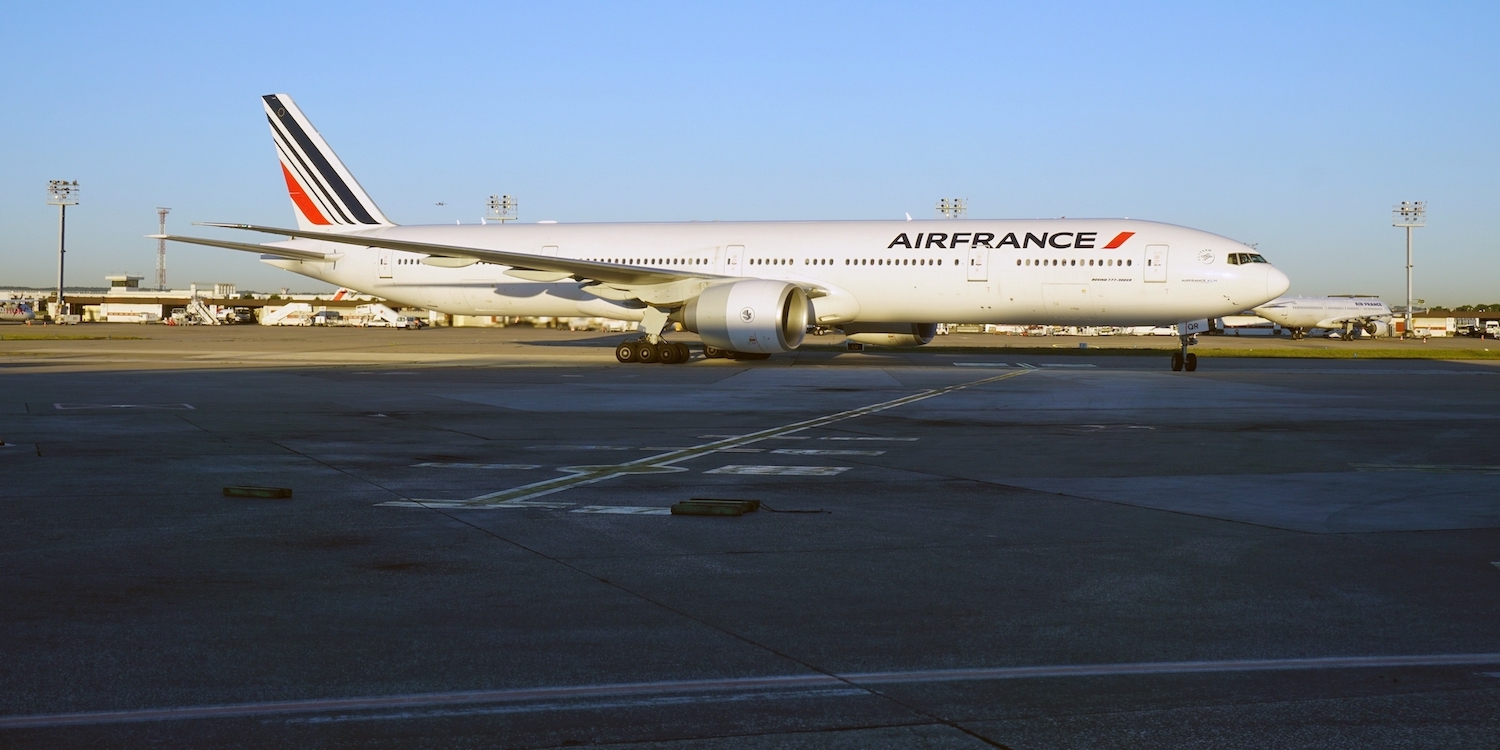
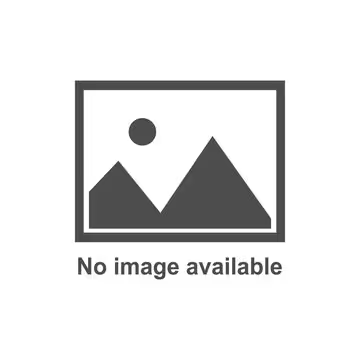
NOTES FROM THE GEMBA – The author visits the Parisian airport of Orly to learn about a pilot project (pun intended) that aims to tackle the late departure of flights using lean thinking.
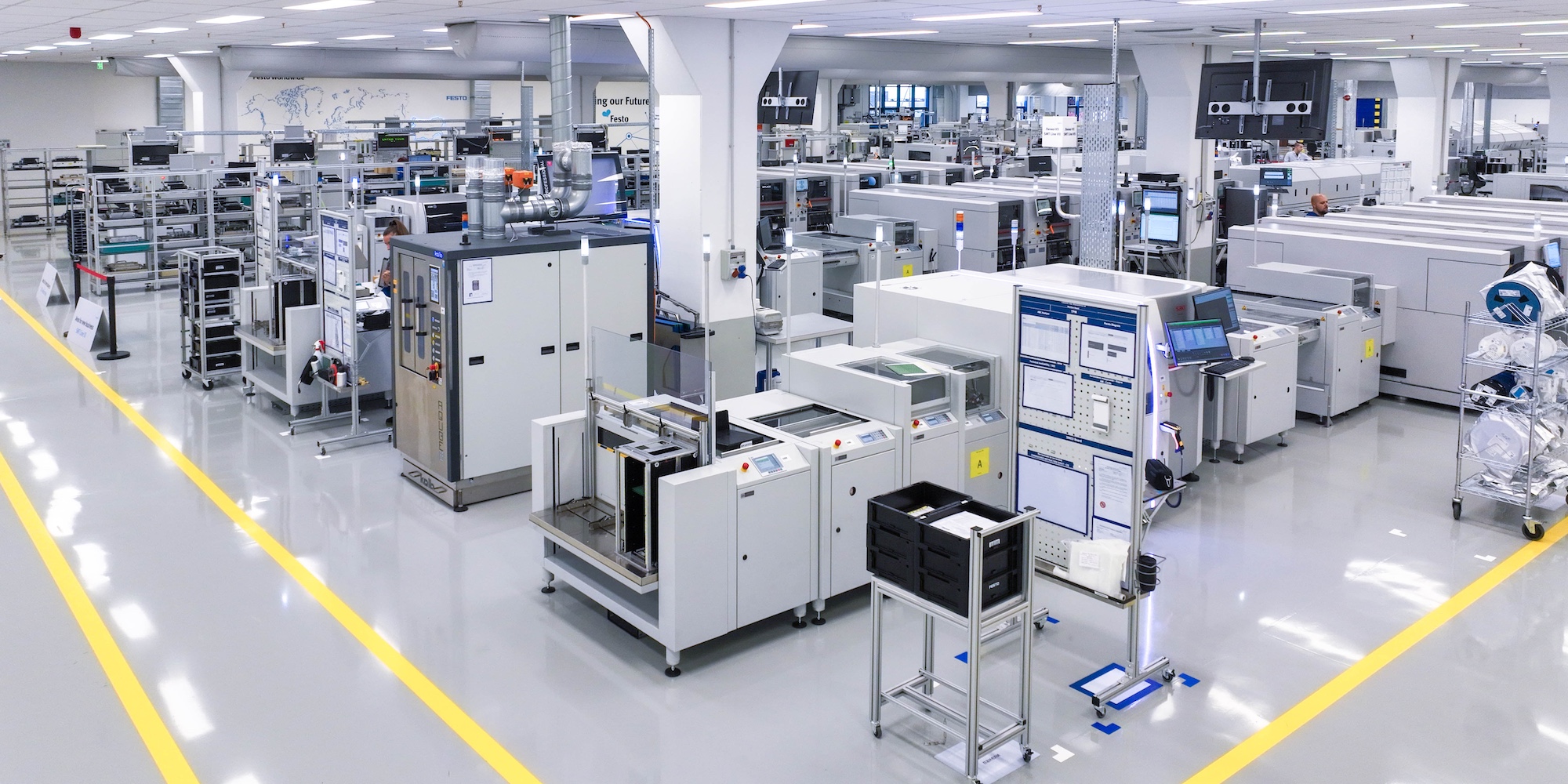
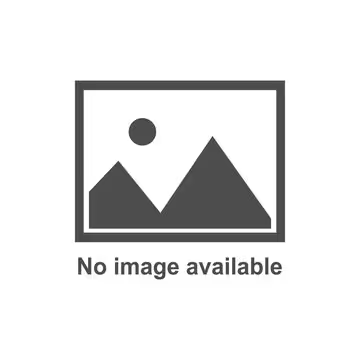
INTERVIEW - Festo’s lean journey improved competitiveness by embedding Lean into daily operations, strengthening leadership engagement, accelerating innovation, and turning Bulgaria into an internal hub for innovation.
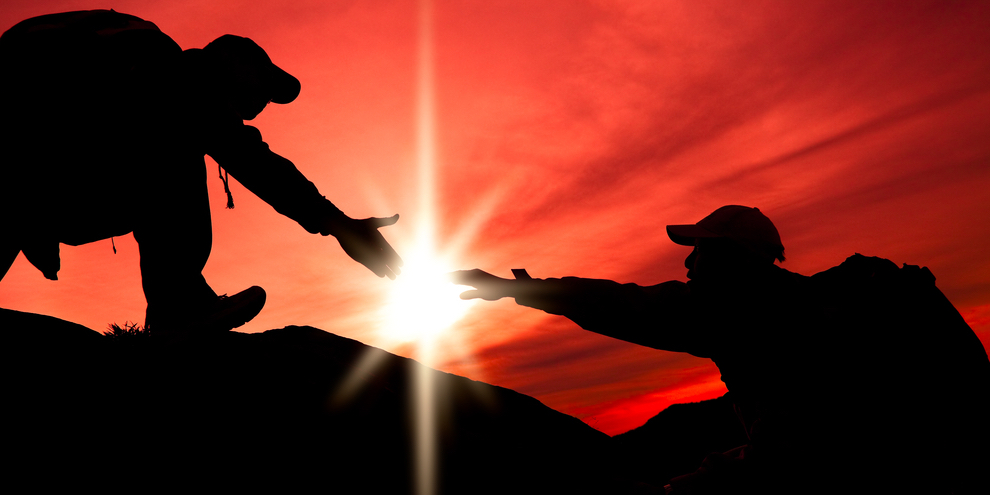
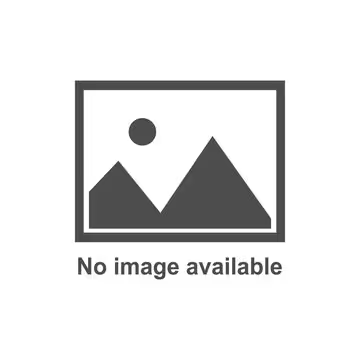
FEATURE – Our disposition towards learning changes depending on the amount of things we don’t know. The author explores this topic and the role of the sensei in enabling learning.