Dojos change minds
CASE STUDY – Faced with safety and quality issues, this Brazilian manufacturing plant installed a dojo, and the results are very promising.
Words: Gabriel Oliveira with Nilson Rodrigues da Silva
A year and a half ago, our factory in Caxias do Sul, in southern Brazil – which manufactures fifth wheels for trucks, the part that connects the tractor to the trailer – was experiencing safety problems. JOST has clear safety guidelines in place, but people struggled to follow them. Whether it was crossing the aisles using the safety crossing and holding onto the handrail while going up or down the stairs, there was a clear lack of adherence to safety standards. This resulted in a number of accidents that, coupled with several quality issues, eventually led the organization to question its approach to training and people development.
Traditionally, our training method entailed taking people to a conference room, showing them some slides and assuming that would be enough for them to understand and interiorize the standards they were expected to follow in their daily work. Of course, it didn’t work. Even leaders failed to follow the safety rules, setting the wrong example and not living up to their responsibility towards front-line workers.
What could we do to make people part of the solution, transform their behaviors and, along the way, develop a more solid and effective approach to training? The solution came in the form of a dojo – a structured learning environment where employees practice and develop their skills through hands-on training and problem-solving activities. Knowing that Toyota, Embraer, and other excellent companies use dojos for their people development, we went on a few visits and ran a benchmark analysis. We realized we didn’t have the knowledge we needed to develop a dojo, so we partnered with Lean Institute Brasil.
LIB has developed an effective approach for this that is currently being used in many organizations. It is based on the key elements of three theories of learning – behaviorism, constructivism, and cognitivism – in conjunction with Training Within Industry practices.
The implementation of the dojo, as designed by LIB, follows a clear set of steps organized in three main stages: project structuring, development of dojo trainers and standard material, and creation of the actual dojo space (which has to be as similar as possible to the real environment at gemba).
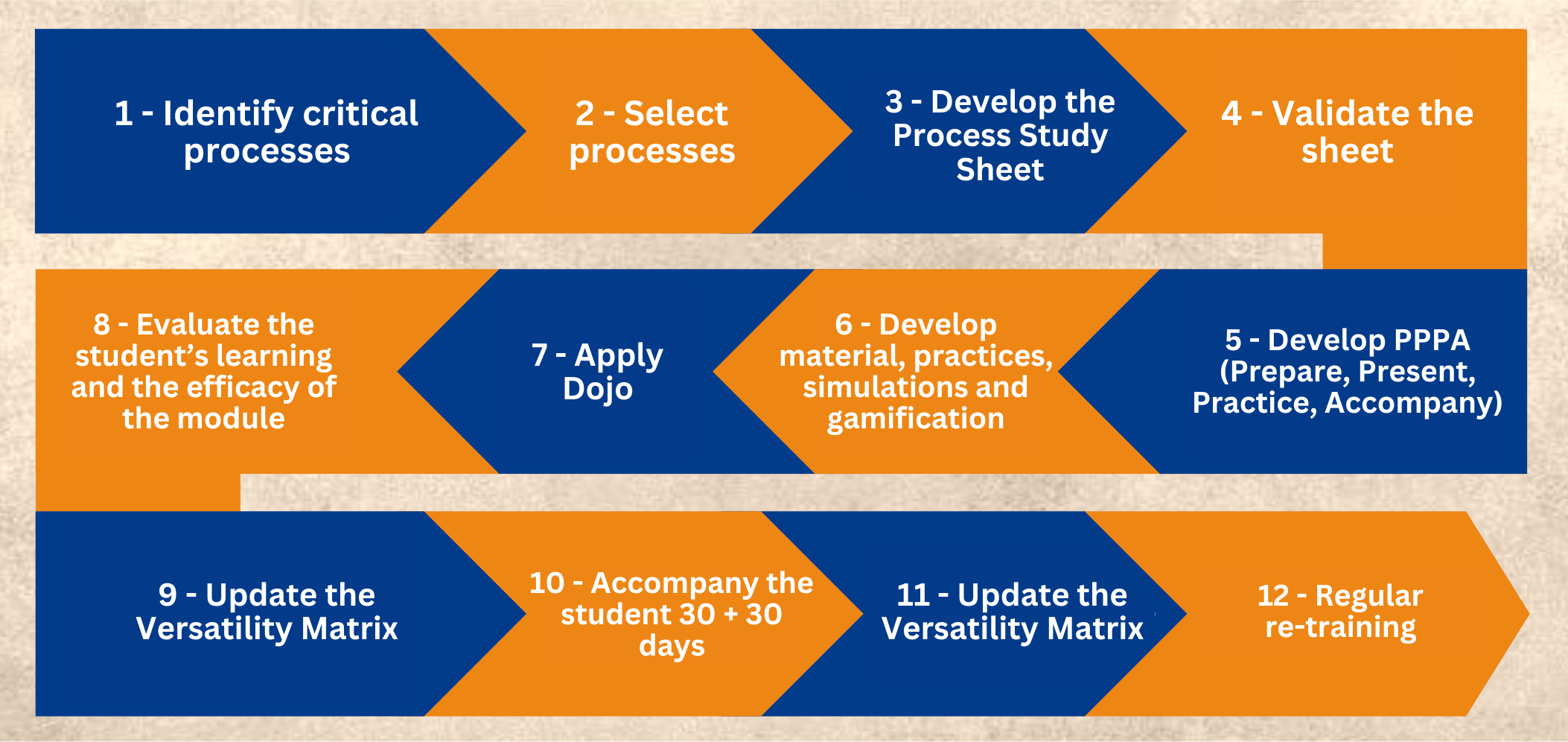
HOW DID IT WORK?
The first step for us was to create leadership awareness. We knew that top management had to sponsor the project, if it was to succeed. Once we secured that support, we were ready to run our first pilot.
This focused on the first three modules (there are 12 in total): dojo introduction; health, safety and environment; and operational excellence. Collectively, these entailed eight hours of training, during which roles and behaviors, safety, standardization, waste and chain of help were discussed.
.png)
With LIB’s help, for each module we address, we develop a process study sheet and identify each module’s key deliverables. Then, we decide how we prepare the dojo space to deliver the best training possible and ensure that people truly interiorize concepts and practices. A document is prepared that provides a script for people as they deal with each module.
The dojo space (which is, by definition, flexible and adapts to the specific needs of each organization) changes depending on the circumstances, with certain simulations or devices (like screens for quizzes that are meant to test people’s understanding of standards) taking center stage.
The first training we provided in the new space was for managers and the leadership team to make sure they were clear on the five golden rules. After that, we went full speed ahead. Since the initiative was launched in July 2023, a whopping 400 people have gone through the dojo training. This incredible spread of knowledge was a responsibility of four dojo instructors (to develop them, LIB provided a 16-hour training; previous experience with the processes was also a precondition), supported by a team of multipliers. As our implementation progressed, we started to delve deeper into activities – like welding – that were creating specific quality issues.
The four dojo instructors were selected based on the skills we had identified as necessary during our benchmarking exercise. We looked at how they communicate, what shop floor experience they have, and so on. We try to give those positions to internal people: one of our instructors, for example, has been working in the process for 10 years. That kind of experience is invaluable!
All new employees now go through the dojo when they join the company. I recently got a message from one of our team leaders, who told me that a newly hired person complained that a document that was supposed to be displayed at his workstation, as mentioned in the dojo, was not there. That’s a sign that the dojo is truly working. Indeed, onboarding has gotten much easier: we have had high turnover of staff in the past few months, and having a system to quickly and effectively onboarding people has proved very useful.
THE RESULTS
We are the first client LIB has used this approach with, and the results have been so impressive that we are currently introducing other departments to the use of the dojo. Safety accidents have disappeared, adherence to the five golden rules is increasing (something hard to measure but impossible to ignore today at JOST), and the number of quality defects has started to go down even before the team formally started to tackle quality. In the last trimester of 2023, compared the same time the previous year, the number of customer complaints dropped from 24 to 9. That’s how powerful behavior change can be! For example, at the end of 2022, 83% of the employees surveyed said they didn’t use the handrail when going up or down the stairs, whereas six months after the implementation of the dojo 93% stated that they always use it! Interestingly, the number of insecure conditions recorded by team members went up 110%, proof that their increased understanding of what constitutes a risk.
In the past few months, words on the success of our dojo spread and other companies in the JOST group have been visiting us in Caxias do Sul to see what we have been doing. Two of those companies have now started to implement their own dojos. Our German COO has also visited us and there is now talk of applying the dojo to the entire JOST group, worldwide.
Overall, we are reducing the time it takes to bring a team member to maturity when it comes to their understanding of standards. We are also noticing that our people are starting to ask questions about the work, a sign that the company culture is shifting. This is what we were hoping for. The dojo is a safe space to discuss problems, a fundamental part of that “showing respect” principle that is so pivotal in Lean Thinking.
As we look ahead, our next steps are clear. We will continue to tackle the modules of the dojo, gradually engaging with maintenance, ergonomics, and welding. By the end of the year, we plan to complete the 12 steps of the roadmap. We also plan to work more closely with leadership, reinforcing the message so we can truly change their behaviors.
People often assume the dojo is a place that works on people’s hands, their practical skills, but that’s only a part of it. It is in their minds that we are seeing the biggest change!
THE AUTHORS
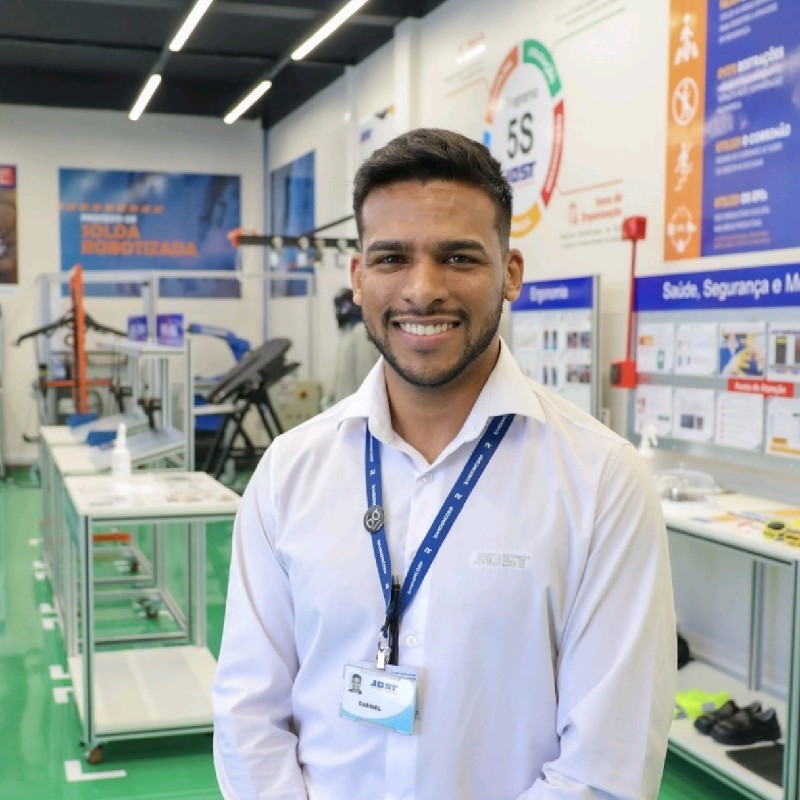
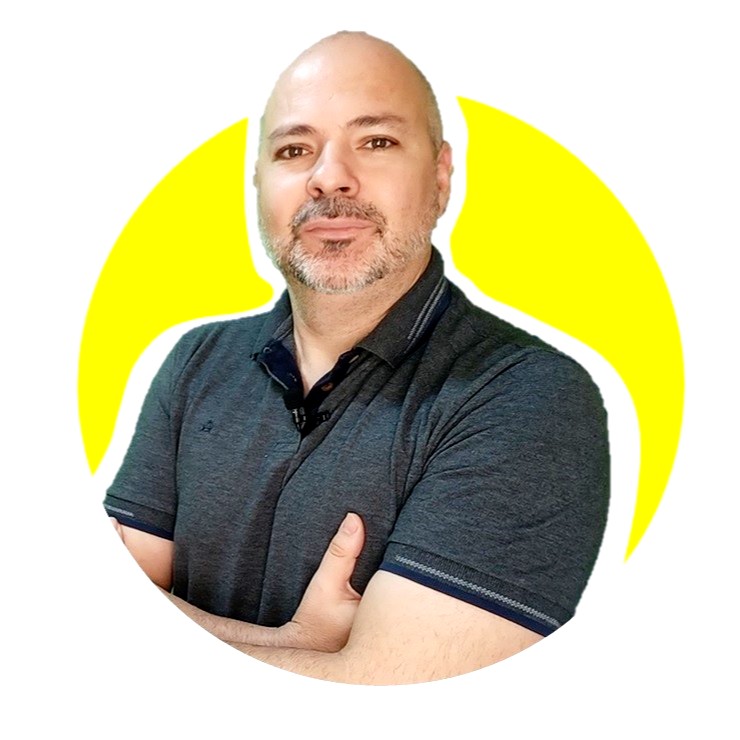
Read more
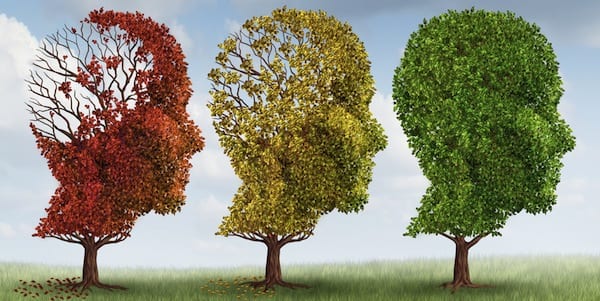
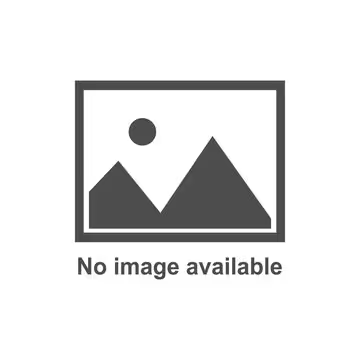
OPINION – How many times, in the early stages of kaizen events, have you thought about giving up? Hang in there. As frustrating as they can be, they will also teach you a lot, says our Danish colleague.
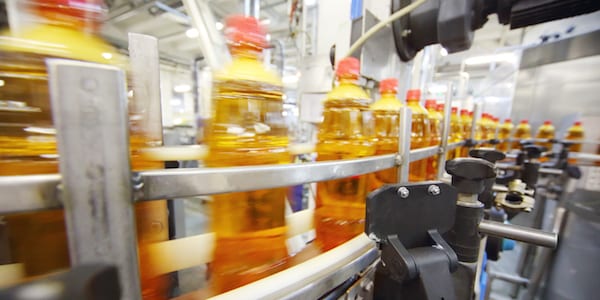
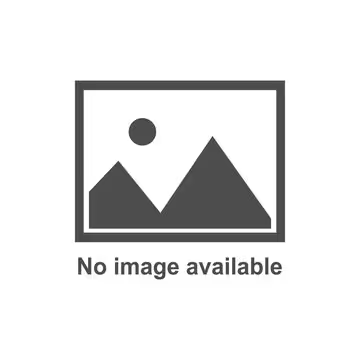
FEATURE – Effectively applying just-in-time and achieving flow is impossible without leveling production first. Yet, most companies seem to think this is impossible because demand is so variable… but is it really?
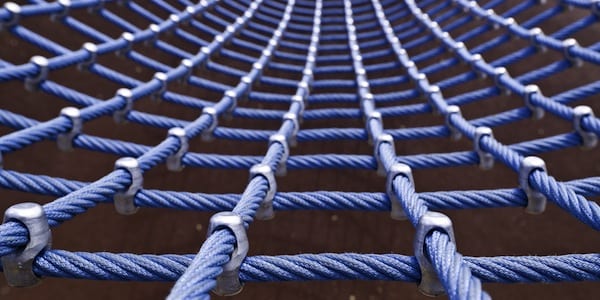
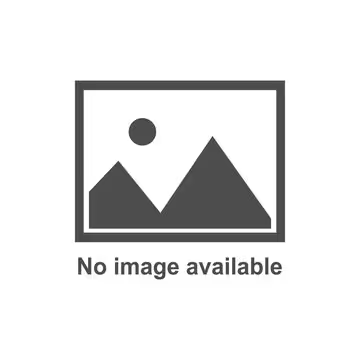
COLUMN - A lean transformation is not just a prerogative of top management, but a goal to be shared across an organization. Here's a few thoughts on how I.T. people specifically can contribute to a turnaround.
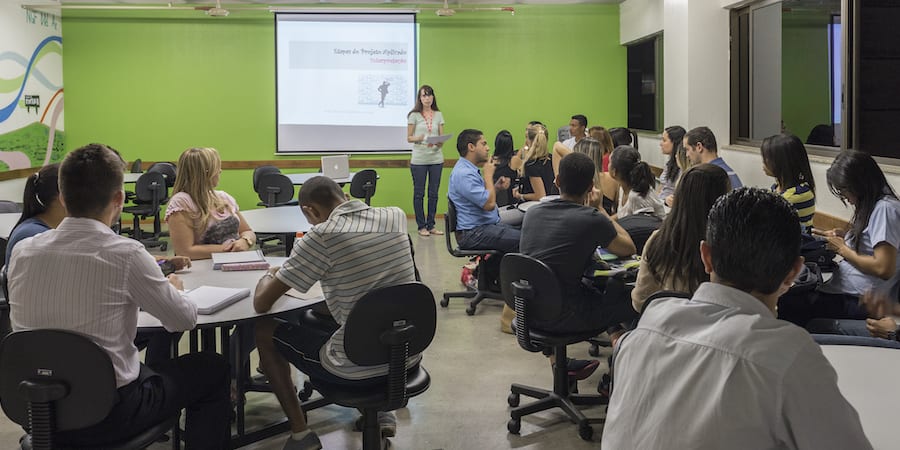
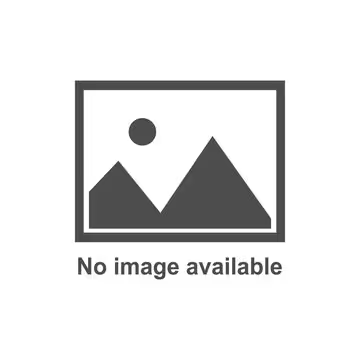
INTERVIEW – Grupo Anima, a Brazilian private education organization with almost 100,000 high-school students enrolled, has revolutionized its culture since introducing lean. But it all started with one project…
Read more
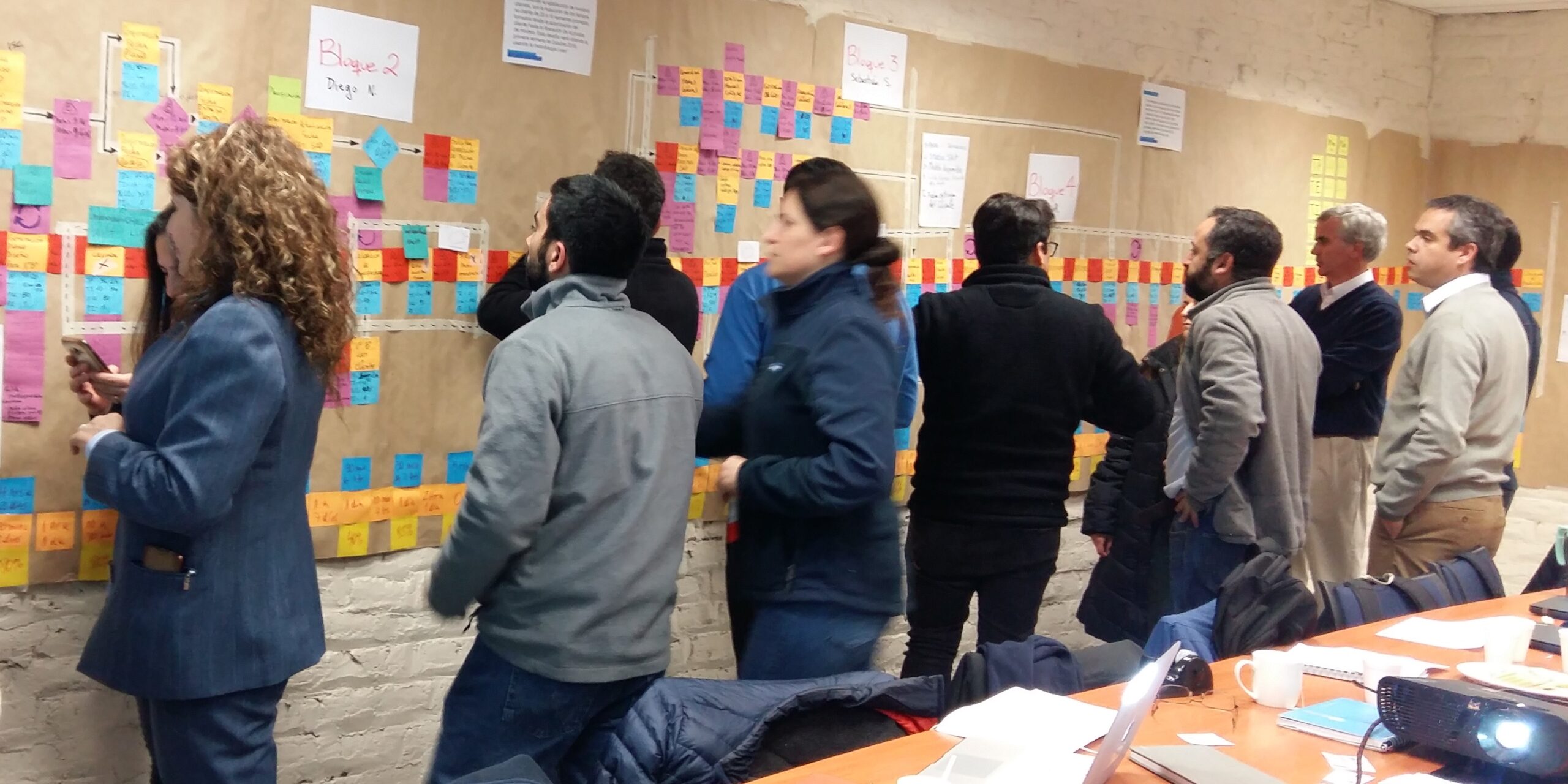
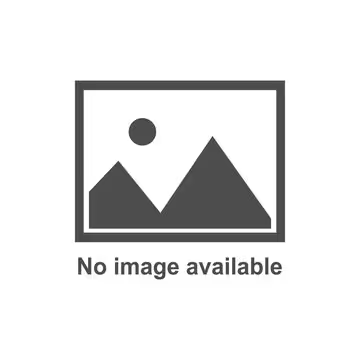
INTERVIEW – Top leaders at Chilean company Elecmetal talk to us about how lean has transformed their role in the organization and how capability development is fuelling change.
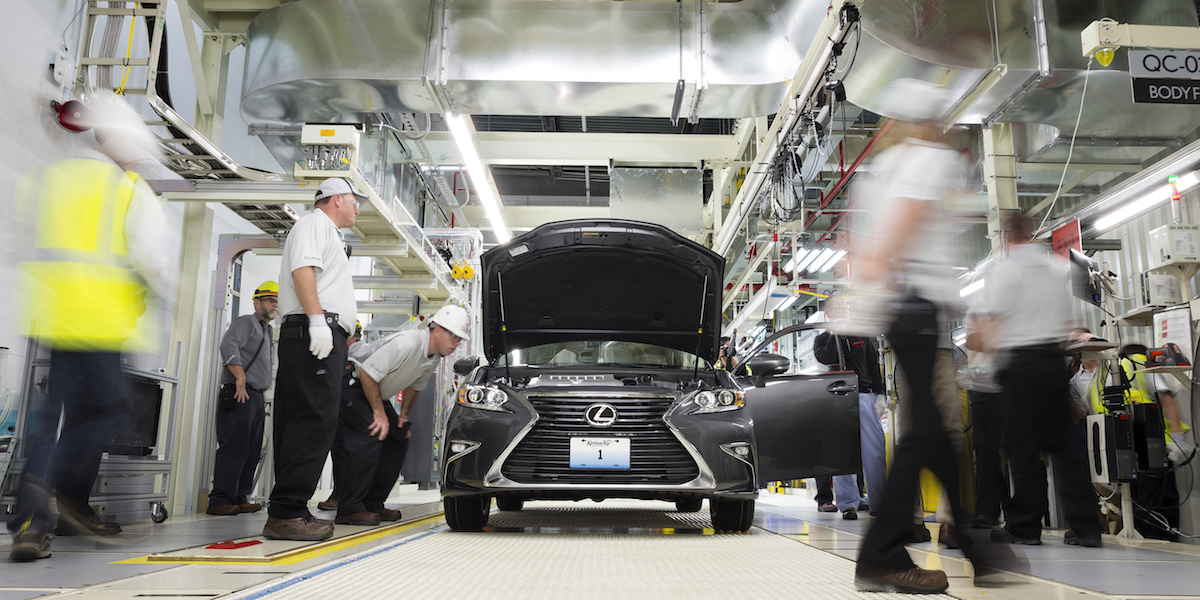
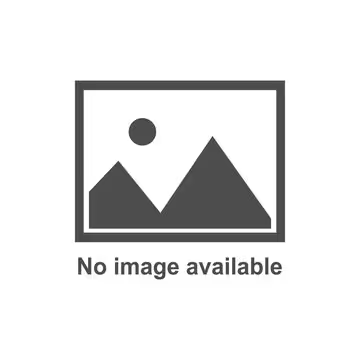
VIDEO - In this video from the recent European Lean Educator Conference, John Shook and Isao Yoshino draw on their experience at Toyota to reflect on the development of lean thinkers.

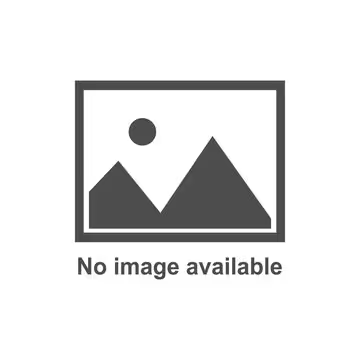
NOTES FROM THE GEMBA – This month, Catherine visits a metal injection moulding specialist and hears about the strong link between growing people’s capabilities with lean thinking and staying competitive in a complex market.
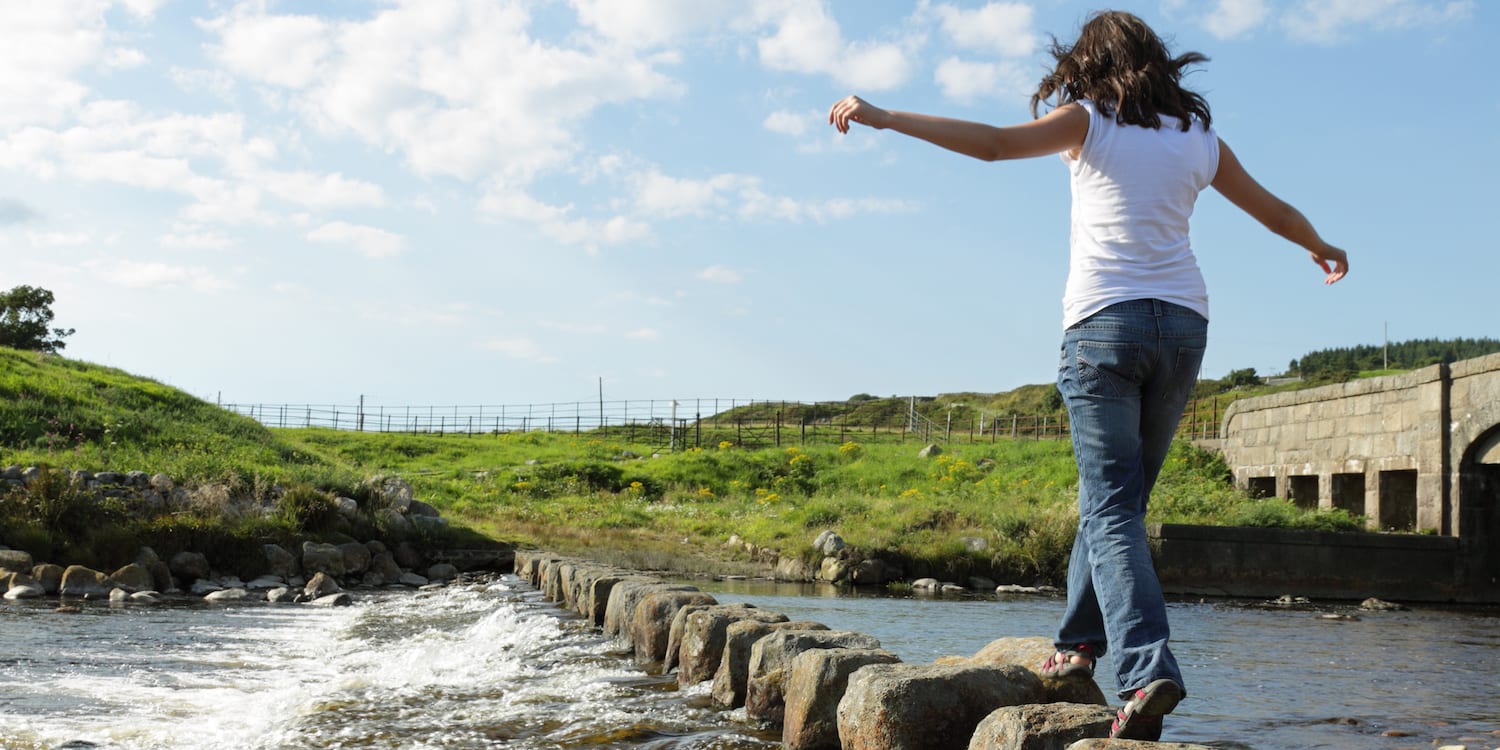
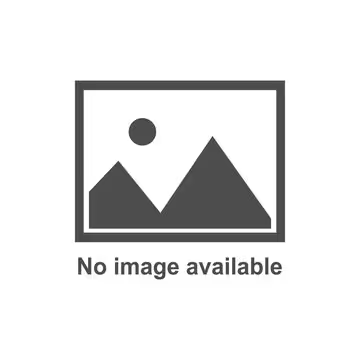
FEATURE – The continuous flow of developing people’s capabilities throughout their studies and careers is lacking, to say the least. It’s time we saw this as one big value chain.