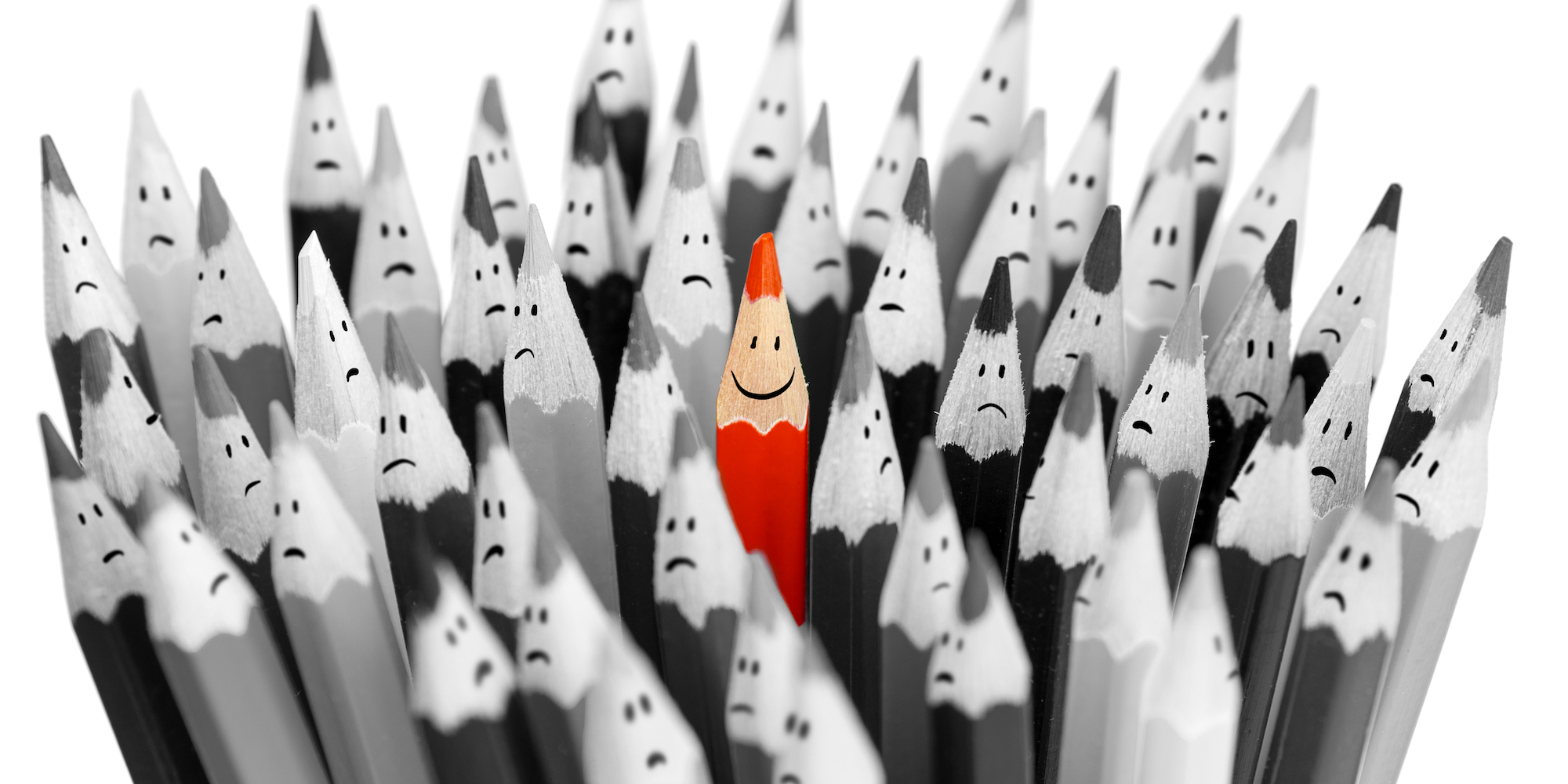
Toyota: differentiation and vitality
FEATURE – Toyota recently achieved the #1 spot in sales in the United States after 90 years of leadership by GM, which shows how capable the lean management philosophy is to overcome difficult circumstances in the market.
Words: Flavio Picchi, President, Lean Institute Brasil
From time to time, we are publicly reminded that Lean Thinking is not just another fad destined to be wiped out by the next “innovation” in management. Increasingly, lean is proving it is here to stay.
We have seen this again in recent weeks, when Toyota, the organization where the fundamentals of lean originated, surpassed General Motors in car sales in the United States. GM has been in the lead for nearly a century in the lead, and in dethroning it Toyota showed us one more time how it stands out from the crowd.
The factors behind this historic achievement are several.
One of them is the way in which the Japanese carmaker dealt with the semiconductor supply crisis. While several GM factories had to stop, Toyota’s were able to maintain a minimum stability in production.
This speaks volume about the solidity of the lean system. Even in the face of profound social changes and market difficulties, lean management has confirmed its vitality and resilience. In other words, lean doesn't seem to age.
It might be interesting to look one more time into the mental model that supports lean, which seems defy time and, when put into practice efficiently, can ensure the sustainability of a business.
FOCUS ON THE CUSTOMER
This priciple lies at the heart of Lean Thinking and has to constantly permeate every area of the business. The idea that every action that is carried out in an organization – from tightening a screw to building a new unit – should be done with an eye to positively impacting the customer.
In other words, it is necessary to always ask and confirm with data that the work we do and plan to do will generate a real added value for the customer. The “value for customer” concept is certainly not new – it’s informed the strategy of lean organizations for decades – but today it’s often repackaged and “rebranded”. User experience (UX) is an example, representing the user’s interaction with the product and/or service and the positive or negative perception that will stem from that interaction.
In lean management, the customer needs to represent the beginning, the middle, and the end of everything we do. With this mindset, any activity that consumes resources without adding value for the customer needs to be reviewed, changed, or even eliminated, as it is waste.
VALUE FLOW
In a lean system, one thing always leads to another. So, how to ensure that everything that is done in an organization focuses on customer value? A good way to do this is to maintain daily practices that monitor and continuously improve the flow of processes along the production chain for the generation of value.
All work that takes place in an organization exists within a process. Together, processes represent a flow that unfolds until it is completed – for example, from customer service through to the generation of the contracted service and the delivery or provision of what was promised, etc.
It is in such flows that real value, as expected by the customer, or waste are generated.
Analyzing and improving the “customer journey” on a daily basis is one of the pillars of Lean Thinking. Regardless of how difficult external circumstances might be, continuous improvement will always keep the foundations of any business solid.
APPRECIATION AND RESPECT FOR PEOPLE
Again, one thing leads to another. What is the main element that guarantees the aggregation of value in our flows? Is it machines? Is it technology? Is it the methodologies we use?
Of course, all these can contribute, but the single most powerful element in the generation of value is people. If a company’s “human capital” is not properly valued and leveraged, nothing else will guarantee success.
It is people who can analyze flows in depth, with intelligence and sensitivity, identify bottlenecks, reveal deviations, devise and implement solutions based on the scientific method, measure results. Only they can do all this daily, improving the process continuously.
An example of respect for people is the way Toyota treats employees when closing a plant. The company has recently announced it is closing the São Bernardo do Campo plant, near São Paulo here in Brazil. This factory has been producing the famous Bandeirantes utility vehicle for decades, as well as parts for assembly in other, more modern units. Bucking the trend of the sector, Toyota has committed to offering positions to 100% of the employees in other units. [The same commitment it showed its Australian employees when the Altona plant closed in 2017. More on this here.]
As advanced as technologies can get, they are still “tools”. Only individuals can make a difference. Care for them – the strongest foundation of your lean system – and you will help your organization navigate the storm raging outside.
COLLABORATION, FLEXIBILITY, ADAPTABILITY AND PARTNERSHIP
If people are the most important element in the transformation of flows for the generation of value, it is also necessary to remember that typically this only materializes with collaborative work, done in a lean way.
In lean management, the strength of people is only enhanced if they make improvements together. This is the way to solve problems, eliminate waste and boost value creation to quickly adjust our thinking and work to face up to whatever challenges we are faced with.
Key to this is development of our ability to see and treat each other as true "partners" - regardless of whether we are leaders, front-line staff, suppliers. I choose the word “partners” because the success of a business can only come from everyone joining forces, collaborating, and rallying around the same objective, which is the generation of value for customers.
These are just a few examples of lean system foundations that seem to be perennial. These recent facts that involve Toyota in the world only reinforce that lean fundamentals are here to stay.
THE AUTHOR
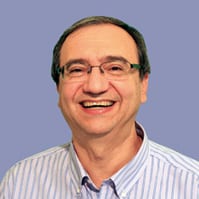
Read more
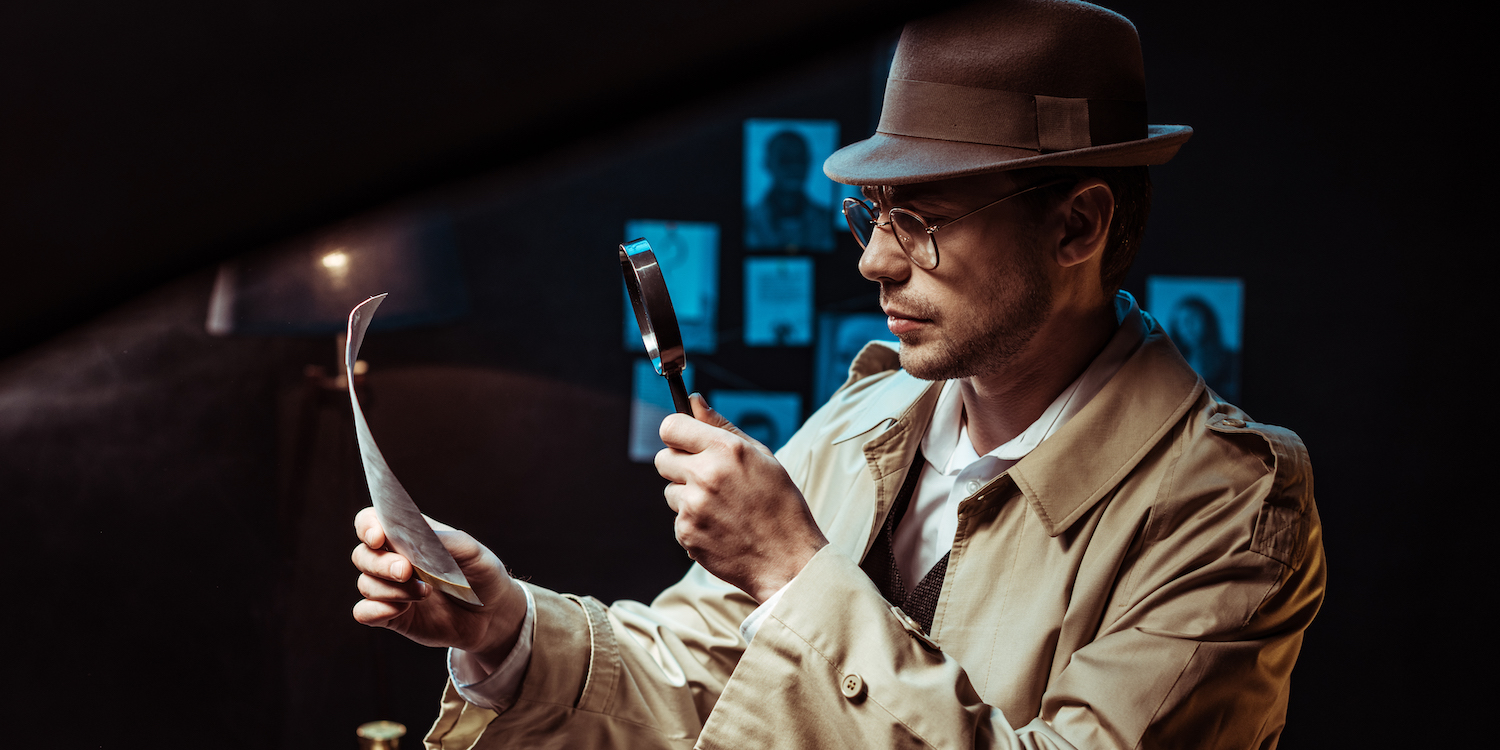
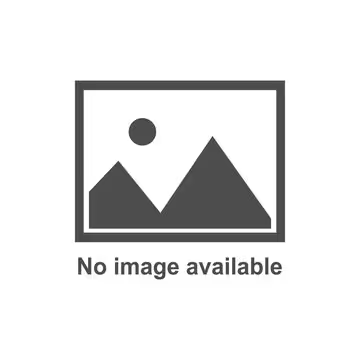
FEATURE – This insightful piece explores the true meaning of problem solving, looking at the common mistakes leaders make when they adopt some of its key practices.
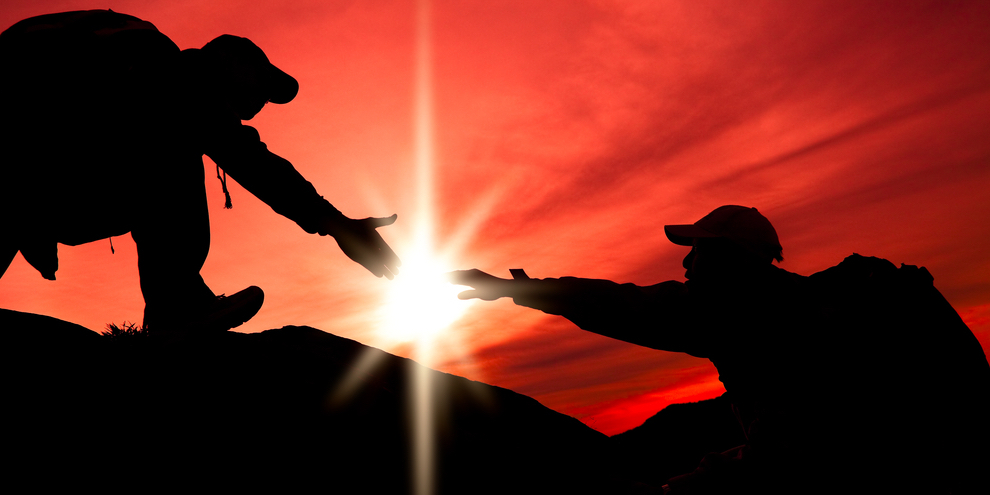
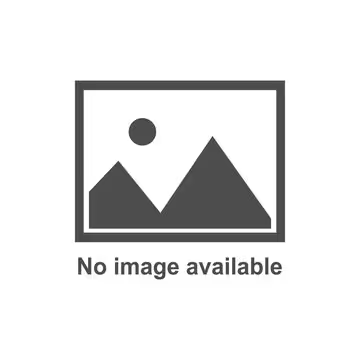
FEATURE – Why do lean transformations benefit from the support of a sensei? Michael Ballé discusses how we typically need help to take the emotions out of the work and go down uncomfortable paths.
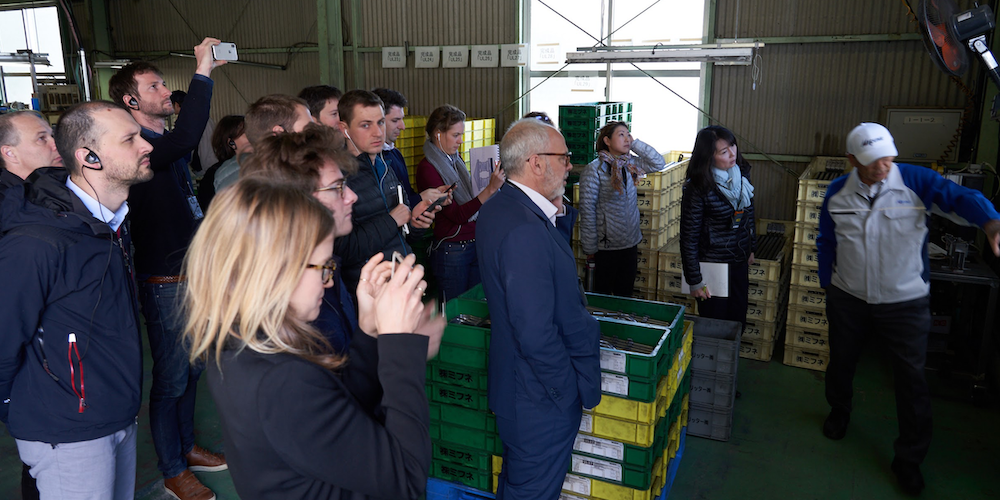
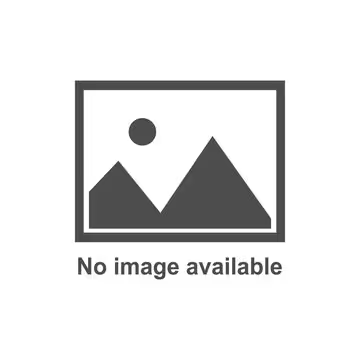
FEATURE – Digital organizations are starting to recognize that Toyota’s unique approach can show them the way forward, just like it does “traditional” organizations. Here, we hear from a few startup CEOs following their trip to Japan.
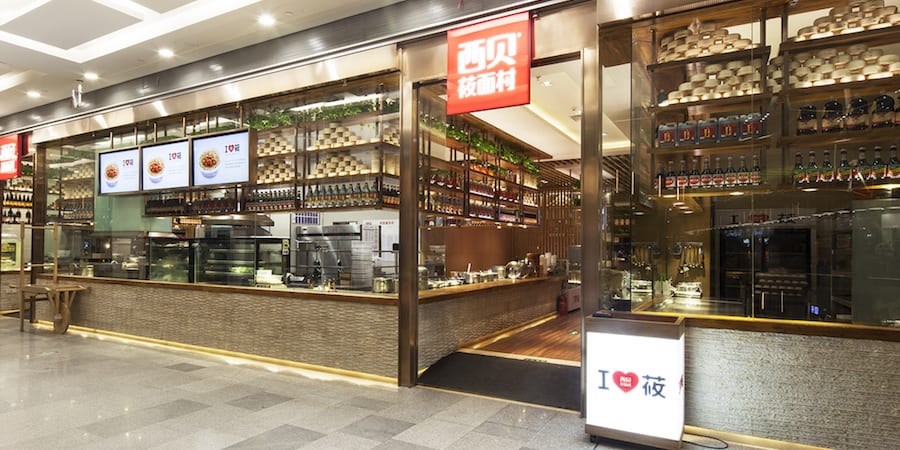
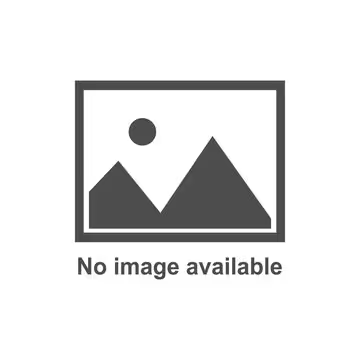
CASE STUDY – An entire restaurant chain going lean is not something you see every day. Coming all the way from China, Xibei's story of cultural change will inspire you to never forget the fundamentals of lean, from standardization to quality.