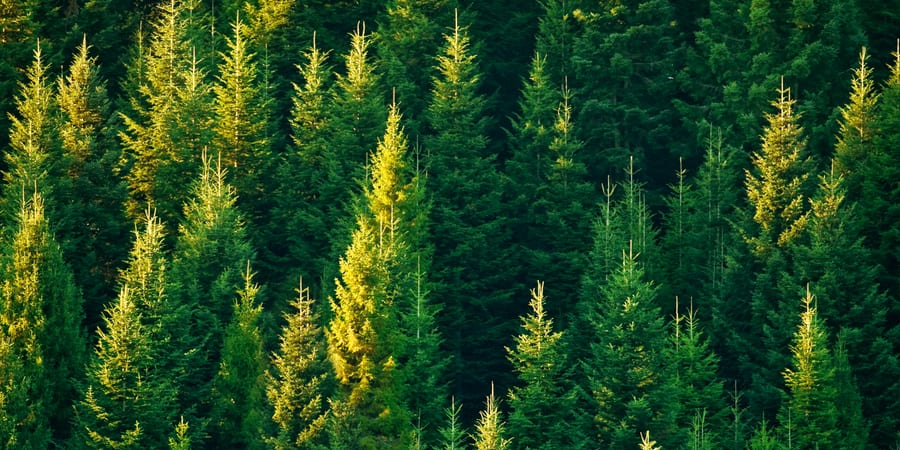
Learning about environmental concerns and strategy at Toyota
INTERVIEW – It might seem a paradox that the world’s largest automaker is setting the pace for corporate social responsibility. Then again, Toyota never really followed the status quo. Kelly Singer interviews Toyota's Steve Hope.
Interviewee: Steve Hope, General Manager, Environmental Affairs and Corporate Citizenship at Toyota Motor Europe
Interviewer: Kelly Singer, Director, Lean Green Institute and Board Member of Institut Lean France
Kelly Singer: Can you please introduce yourself and tell us about your career progression?
Steve Hope: I joined Toyota Motor Manufacturing UK in 1991 as we began construction of Toyota’s first, purpose-built vehicle plant in Europe. My first role was as the Manager of Facilities and Environment. I spent 15 years working in various roles, always striving to improve our performance and environmental impact. This led to me joining Toyota Motor Europe (based in Brussels) to perform a similar role across our growing manufacturing network in Europe. Since 2012 I have been responsible for Environmental Affairs and Corporate Citizenship. My team and I promote awareness and performance improvements across all Toyota Manufacturing, Sales and Aftersales operations in Europe.
KS: When did Toyota first start thinking about the environment?
SH: Toyota has a long and consistent history with its environment policy and goals. Here are some of the early milestones:
- The first Toyota Production Environment Committee was held in 1963;
- The first annual environmental promotion month was designated in June of 1973;
- The Global Guiding Principles and the Earth Charter were adopted in 1992 and the company-wide Environment Committee was established;
- The first mid-term Environmental Action plans were established;
- Toyota UK was the first UK car manufacturer to receive the Environmental Management System certification to ISO14001;
- The Toyota Life Cycle Assessment subcommittee was established in 1997.
The reason our environmental activities can achieve lasting success is that they are linked to and resonate with the company’s history, DNA, guiding principles and long term vision. The following graphic is a good representation of our environmental philosophy:
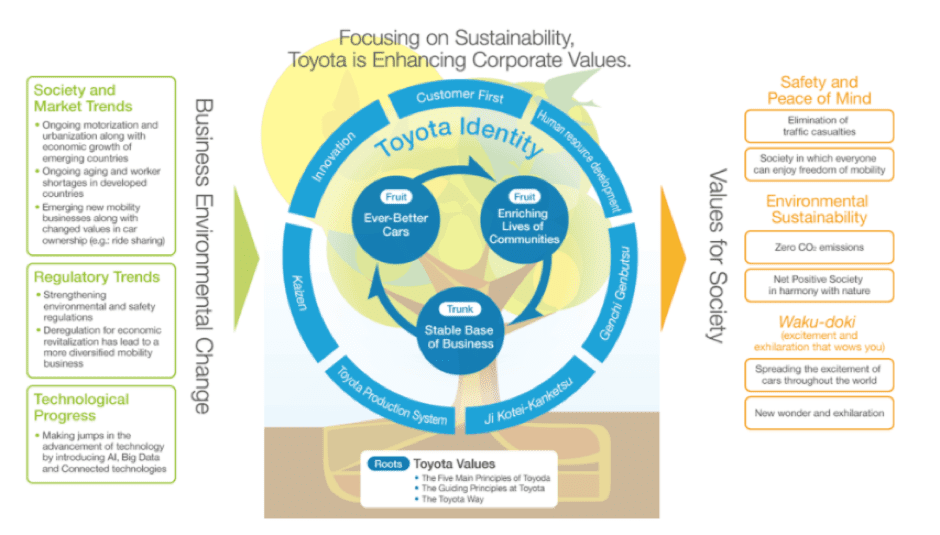
KS: In addition to environmental policy and compliance, does Toyota have specific environmental targets they hope to achieve?
SH: Yes. In 2015, we set six Environmental Challenges to be completed by the year 2050. The aim is to not only reduce our impact on society and the environment, but also produce a net-positive impact. We approach the Environmental Challenges with the same rigor as we would any other goal, because we are certain of the benefits that meeting them can bring and because we view them as making good business sense.
Here’s a graphic detailing the six Challenges in more detail, and you can read about them in length here.
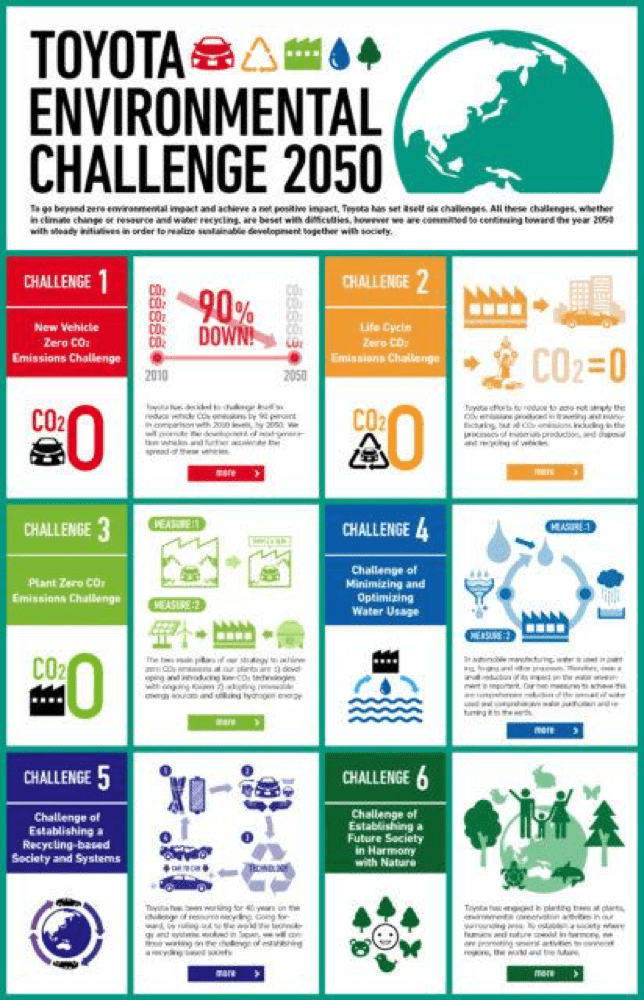
KS: How does Toyota incorporate the Challenges into the entire value chain?
SH: Toyota works with both the upstream and downstream value chain, sharing our business experiences, knowledge, technologies and best practices with willing partners. Our aim is to think with a 360-degree approach: not only considering a vehicle’s lifecycle, but also how that circular approach can continue through successive life cycles. That’s why we must work with partners representing each life phase of the vehicle.
The complexity of our Challenges means that one sector, or one company, cannot solve them in isolation – we need not only business partners, but also multi-company/sector collaborations between industry, governments and society. For example, the transformation of society to include hydrogen as a potential energy carrier and storage solution for excess renewable energy will include collaborations between energy providers, distributors, governments, municipalities and users. To this end, Toyota has already made over 5,600 hydrogen-related patents available for other partners to use, royalty-free.
Of course, we want to systematically reduce our direct environmental footprint, but we also want to share our technologies and knowledge with society at large. This allows us to deliver an even greater overall indirect benefit.
KS: How do the Environmental Challenges fit into Toyota’s long-term philosophy?
SH: It is clear that society is facing many challenges. To consider yourself a sustainable business, global societal challenges must be incorporated into your company’s philosophy and long-term strategy.
The Toyota 2050 Environmental Challenges attempt to tackle problems that need to be resolved in this timeframe: we focused on areas in which Toyota believes it can make a strong contribution, like CO2 emissions, climate change and air pollution, water, resource utilization and a recycling society (circular economy), and working in harmony with nature.
The vision of the ideal society of 2050 allows Toyota to “backcast” (as opposed to forecast), allowing us to construct intermediate targets and prioritize specific actions.
KS: It’s common now for multinational organizations to have carbon emissions, water, and landfill waste reduction goals. Toyota’s Challenge 6, Establish a Future Society in Harmony with Nature, however, is unique. How do you identify opportunities to meet the challenge?
SH: Indeed, this may seem a surprising challenge for a company in our sector. However, Toyota must always consider that the use of our products may have some negative impacts on the natural world.
We want to address these impacts. We try to work creatively with operational sites in our direct network and those of willing partners, to harvest natural resources (such as energy and water) in a sustainable way and promote the conservation and development of biodiversity through our Greenways programme. This way, our sites can form green spaces as part of extended networks and corridors for nature within the wider landscape.
We also promote biodiversity education for children through our partnerships with professional organizations across Europe. Finally, at a high level through our Today for Tomorrow Programme, Toyota provides global level grant support for specialist organizations. We chose partners working at the cutting edge of their subjects, such as the IUCN working on the RedList, WWF working on sustainable rubber production, and so on.
KS: How does Toyota engage its employees to think and act upon sustainability?
SH: Toyota applies the Toyota Way during these interactions with employees. We believe it is very important to create awareness, then a deeper understanding, before developing engagement and actions. To do this, education is critical, including the provision of context to each individual within their daily work activity (what’s in it for me?). This employee education and context is provided through a mix of conventional training, e-learning, knowledge sharing and a focus “Green Month”. Such activities support the integration of environmental goals and action planning within the normal business processes.
KS: What role does top management play in the global roll-out of the Environmental Challenges?
SH: Their role is, of course, critical. It was our executives who requested the development of this long-term vision. They were also involved in building the company-wide consensus required to face up to the challenges. Finally, they are involved in sharing our vision with stakeholders across the globe.
This framework ensures consistency of approach and allows priority setting in the case of conflicting directions or targets. Their personal commitment as company leaders is visualized and recognized both inside and outside Toyota.
KS: Another impressive goal is Challenge 2: Eliminating CO2 from the entire lifecycle of all company operations. Demanding the entire value chain be carbon free might seem more attainable given Toyota’s size and influence. Do you think the challenge is possible for smaller companies to achieve?
SH: This challenge can and should be tackled by all businesses, irrespective of size. The size and influence of a global company is helpful to get visibility for the challenge itself, but is not a guarantee in every region (as our market share varies around the world). Nor is size required to take positive actions in the supply chain – small individual steps do add up! (For example, the implementation of low-energy solutions such as LED lighting, green energy use or increasing recycled materials in a product.) All of these actions can be cost-effective as well as environmentally beneficial, if implemented at the appropriate timing with forward planning.
KS: What is your wildest dream about the Environmental Challenges? What would happen by 2020 that would be a proof that Toyota’s on the right track?
SH: I would like the Mirai Fuel Cell Hybrid car[editor note: Jim Womack recently drove the Mirai from Boston to Philly and shared a few reflections on lean and green here] to be seen by future generations as the trigger to step away from conventional fuels, to create a world that embraces hydrogen as a significant and complementary element of the future energy infrastructure. I hope it will open the door to convenient and emissions-free energy. This would address a wide range of societal needs: personal mobility, public transport logistics, industrial processes and domestic usage.
I would also like us to always consider the full life cycle: planning, producing, delivering, using and recovering products at the end of their lives to make personal mobility and the business of Toyota truly sustainable.
THE INTERVIEWEE
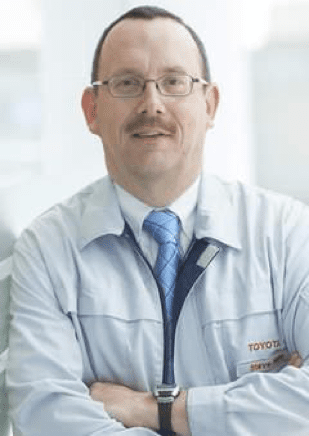
THE INTERVIEWER
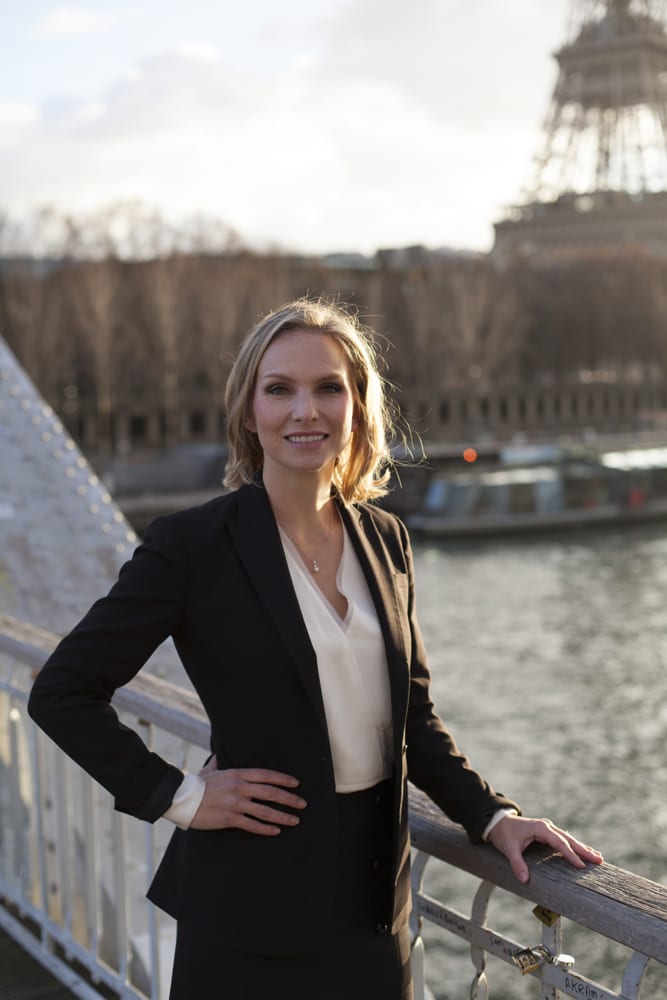
Read more
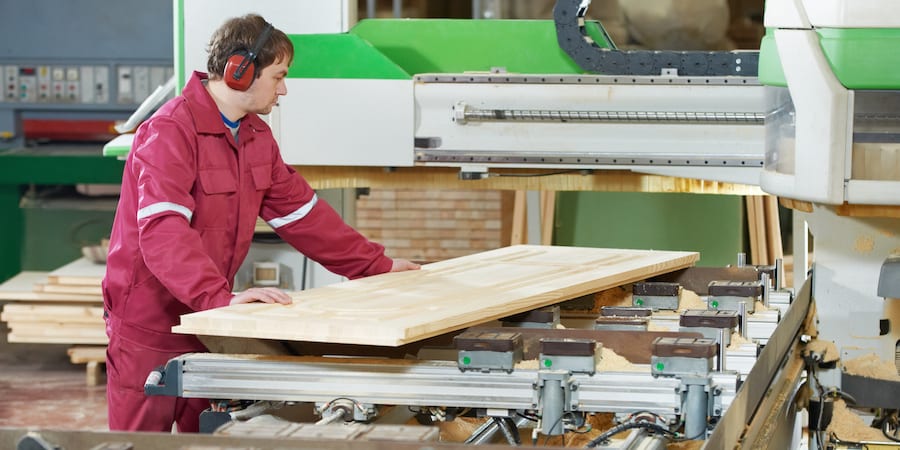
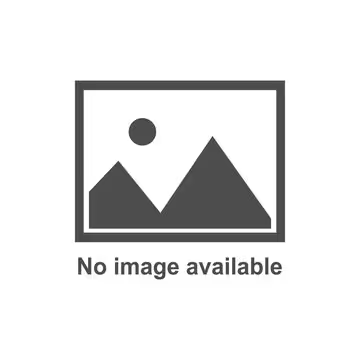
INTERVIEW – Planet Lean speaks with David Mann about the importance of combining the lean production and the lean management systems – the tools and the culture – to create sustainable results.
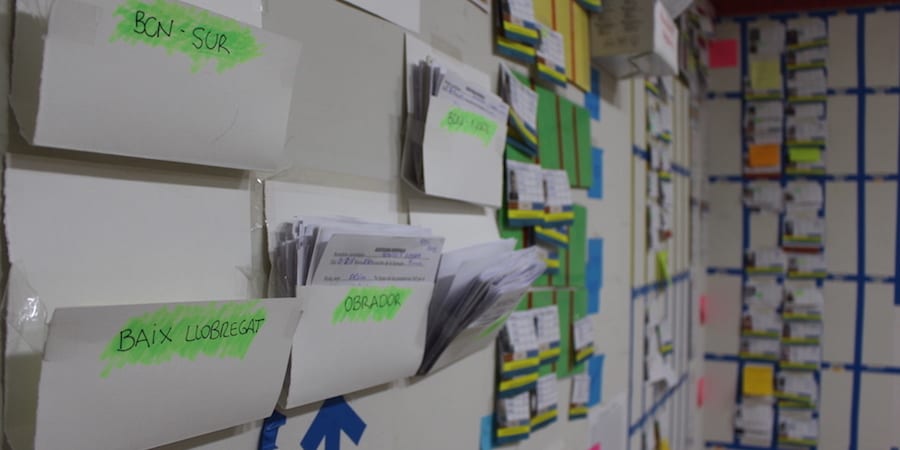
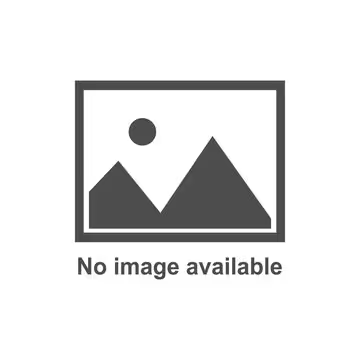
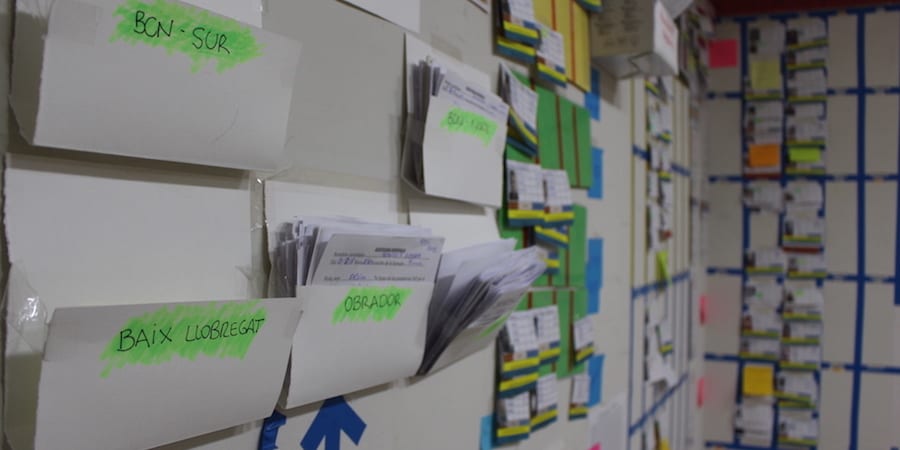
THE LEAN BAKERY – In the last episode of our video series, we learn how 365 is using an impressive visual management system to manage the accounting and human resources functions.
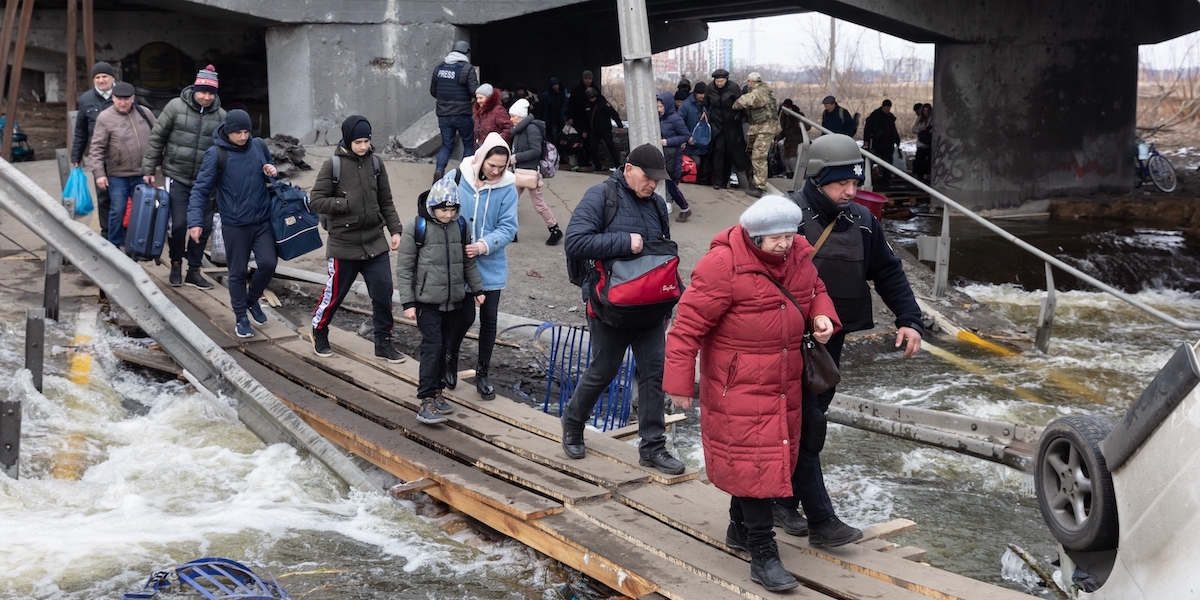
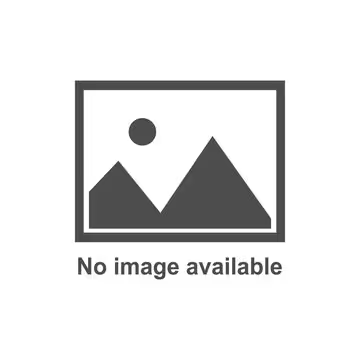
FEATURE – When the clouds gather, it’s tempting to throw in the towel and ask, “What is it all for?”. The author tells us why the kaizen spirit should be our beacon now more than ever.
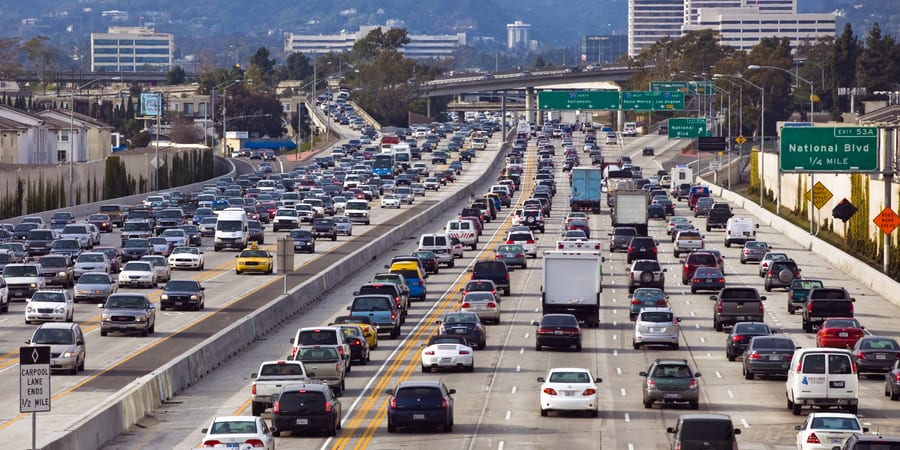
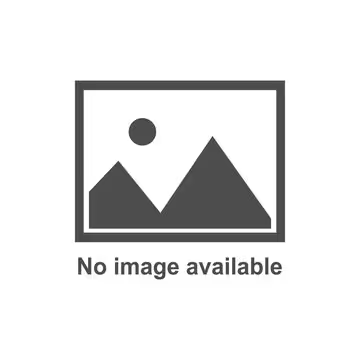
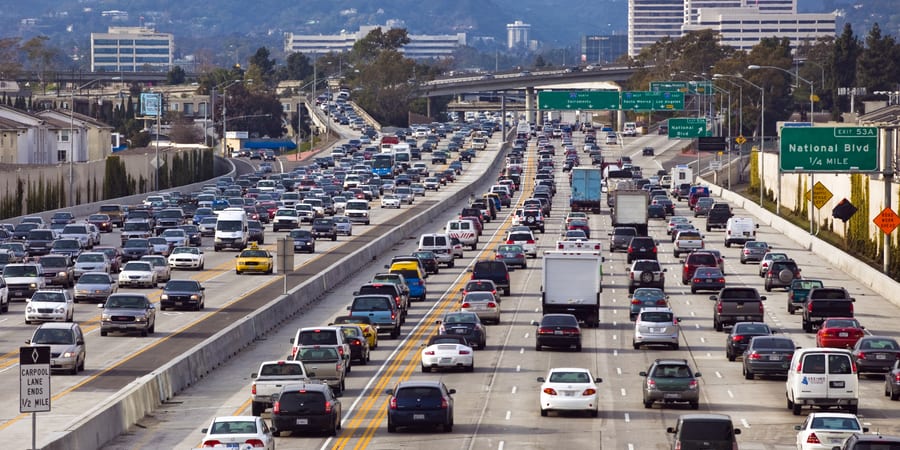
WOMACK’S YOKOTEN – In this month’s column, Jim shares an insightful analysis of the trends and dynamics of today’s automotive industry and looks at the opportunity that lean has to facilitate its next transformation.