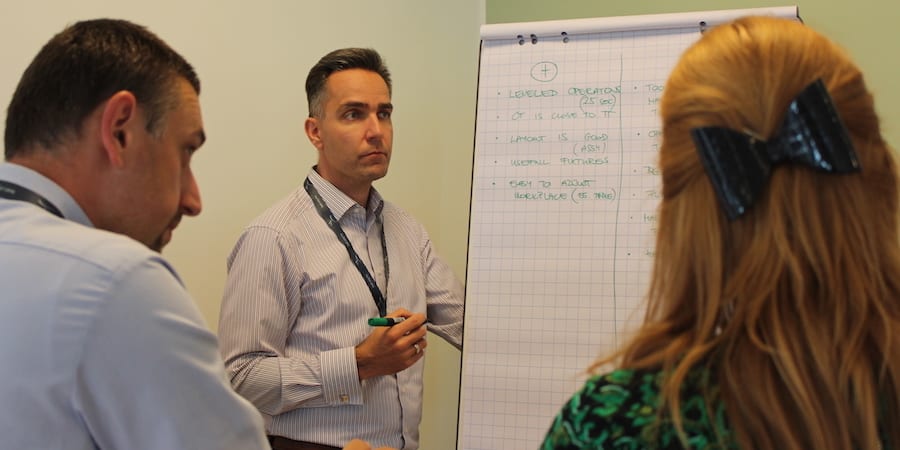
Hungary needs lean thinking, we think we can help
GETTING TO KNOW US – We travel to Hungary to meet the President of our affiliate institute in Hungary. He tells us his country’s need for good workers and how lean can make the difference.
Interviewee: Szabolcs Molnár, President, Lean Enterprise Institute Hungary
Roberto Priolo: Earlier this month, I was lucky to spend a couple of days with Lean Enterprise Institute Hungary. What I have seen is a vibrant community of practitioners from all kinds of sectors. What’s the state of lean in the country?
Szabolcs Molnár: Lean thinking has gone a long way in this country, even though we still have a lot of work to do. One of the biggest challenges we are experiencing – and I am sure we are not the only ones – is the fact that in the many multinationals we have in Hungary, lean is still viewed as a program. People on the floor tend to get it as a “package” from Headquarters – in the form of a set of guidelines and deadlines to implement tools, from kanban to SMED. HQs should take responsibility for how they perceive lean and communicate it, and for how they roll it out.
At LEI Hungary, we are trying to build a community of practitioners who understand that lean is an alternative and superior way to managing organizations which requires a fundamental cultural shift. We find that the Lean Transformation Framework really helps with showing people what lean is really about. Books and events are also critical vehicles for knowledge sharing, as are the relationships we encourage between practitioners in the country. We are lucky to have some great people around us, and we have recently started collaborating more closely with our friends and neighbors from Lean Institute Slovakia.
RP: Your own career started in multinationals. Did you have that same experience of lean being presented as a program?
SM: Very much so. Over the years, I have worked for many multinationals, in several locations – Mexico, US, Germany and Hungary – and roles – from project management to top management. The first time I heard the word “lean” was in the year 2000 at outdoor equipment company MTD, when we were transferring production lines from the United States to Hungary. We set up the lines and one of our American colleagues told us there was “muda” everywhere. We had no idea what he meant, but we got a sense that we had screwed something up. The Americans had been on a lean journey for a couple of years already, and we got the same consulting company supporting them to help us. I later became the Lean Manager at the multinational without really knowing what lean was. I learned along the way with the help of our coach, who spent one week a month at our plant helping us with Rapid Improvement Events.
We did a lot back then, but looking back I now realize we were only focusing on the tools. We were auditing 5S and measuring the number of kaizen events we ran each year: for 800 employees, for example, we had to run 80 one-week kaizen events. At the end of the year, however, we could only be proud of a couple of them. We weren’t able to sustain, and the improvements weren’t linked to actual business problems. We were implementing lean, but we weren’t solving real business problems. I eventually left in 2005 to start a consulting firm.
RP: How did you get to found LEI Hungary?
SM: At the new business, besides hunting for clients, we had a desire for spreading lean thinking and practice in our country. At the time, there was no literature about lean in Hungarian, so we bought the rights to Lean Thinking and translated it in Hungarian in 2009. It was the first book on lean in our language. For the publication, we organized a summit and invited Dan Jones to speak. On that occasion, I began a conversation with Dan (which opened my eyes to how little I actually knew about lean) about the possibility of creating a Lean Global Network institute in Hungary. Around two years later, in 2011, Lean Enterprise Institute Hungary was born. The Polish institute would be mentoring us throughout our two-year probation period.
The Lean Global Network was a great match for us. I consider the roots of the movement to be something we can never forget, and I have always wanted to work with the fathers of the lean movement and their network.
RP: How did your business model evolve over time?
SM: We are a not-for-profit association with 148 members, including 96 private people and 52 companies. For a yearly fee, they get discounts and free services, like our Lean Manager Roundtables (one-day events that combine gemba walks, learning on a specific lean topic and networking) taking place three times a year.
At first, the institute focused on bringing foreign experts to the country – either for summits or workshops – but we quickly started to develop our own capability-development activities, like A3 workshops, Toyota Kata, TWI, Lean Practitioner Program. We are now more focused on projects with organizations, helping them to solve their business problems and learning with them along the way. Learning material is also fundamental, so we try to publish at least one book a year. We are now publishing the ninth lean book in Hungarian – The Lean Bakery. We are also working with universities: for instance, we are co-founders of Bosch Lean Academy (more on it soon on Planet Lean) also hold classes at Corvinus University of Budapest (starting in September, we will run a post-graduate course there) and the University of Pannonia in Veszprém (the town where our institute is located).
We have been growing consistently for the past seven years, and we now have 10 people (two in the office and eight in the field).
RP: What are the sectors in which LEI Hungary is currently more active and what do you think should be your next focus?
SM: Retail is a big one for us. We have been working with Auchan, the French retail chain, for a while now, and a year and a half ago we began supporting a chain of DIY stores called Praktiker. There is a lot of potential in this sector.
Looking ahead, I think our institute should increase its focus on Shared Service Centers, which employ over 40,000 people in Hungary.
RP: The theme of the Lean Manager Roundtable I attended during my visit was Training Within Industry (TWI). Why such a strong focus on it?
SM: The Hungarian economy is booming: companies are hiring a lot, investing in new infrastructure and machinery, but there aren’t enough skilled people to sustain this growth. The country has been suffering from brain drain and our countries are struggling to identify, develop and retain talent. That’s why TWI is so important: it can really help us to train people more quickly and to a higher standard, so that they can perform better on the job.
THE INTERVIEWEE
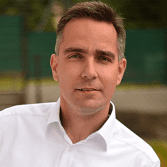
Read more
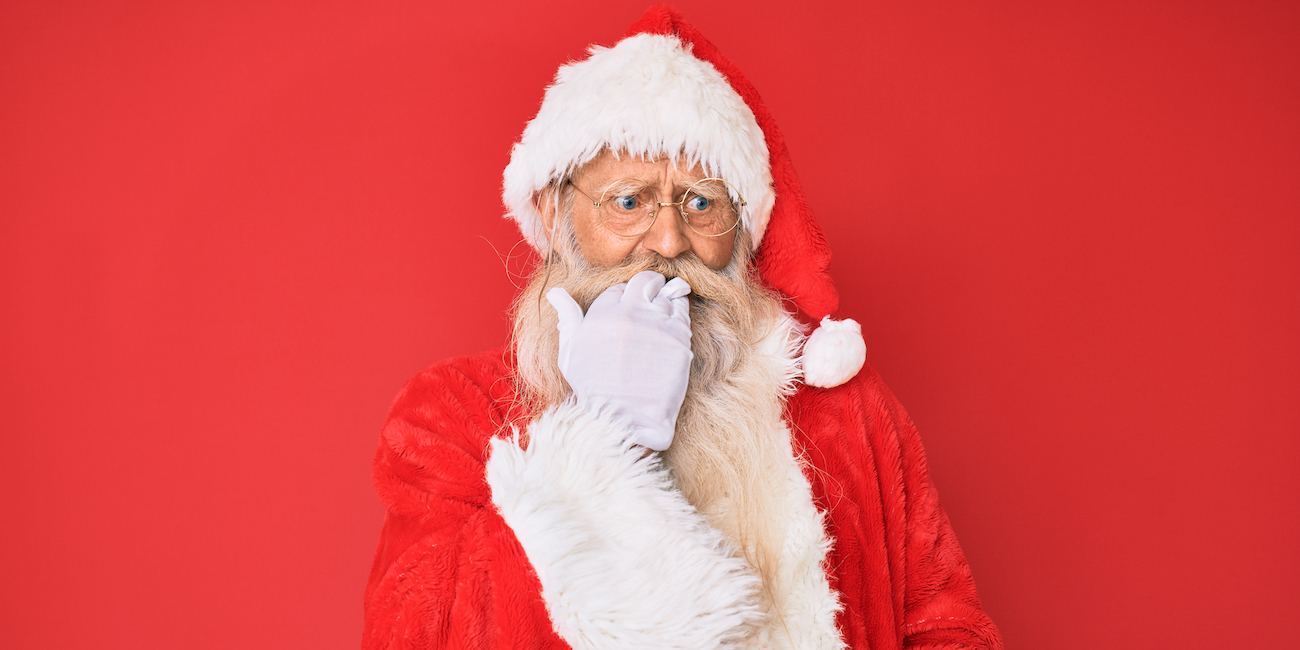
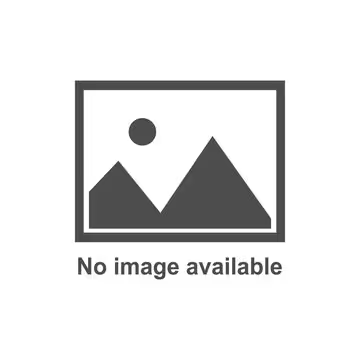
FICTION – The pandemic is throwing curveballs to us all, including a certain bearded gentleman who lives in the North Pole – until a magic “time-bending” solution is presented to him, that is.
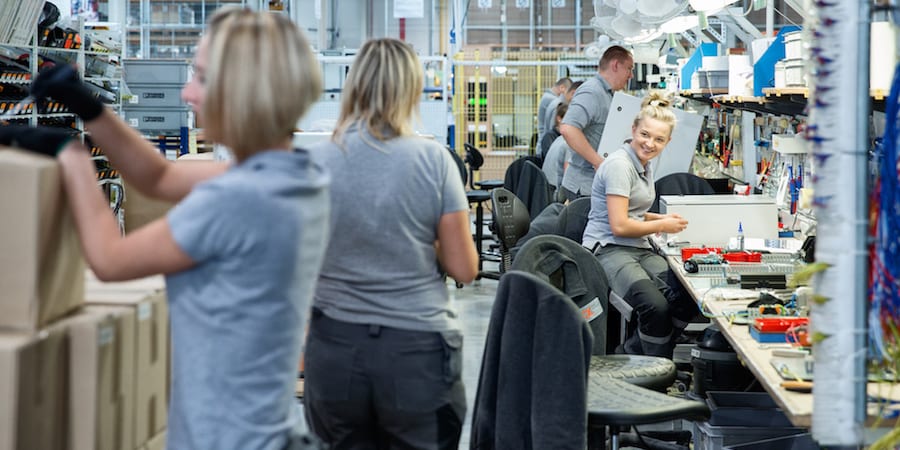
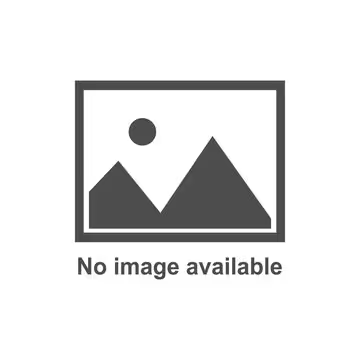
FEATURE – When you are hiring 20-30 people in a week, getting them up to speed with the company’s way of working becomes critical. But how to do it effectively? A Polish factory found the answer in TWI.
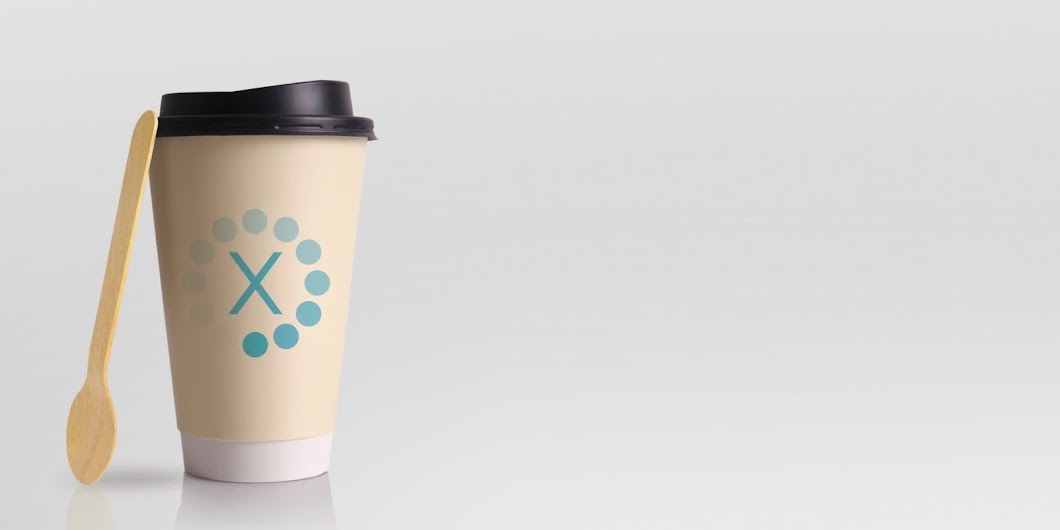
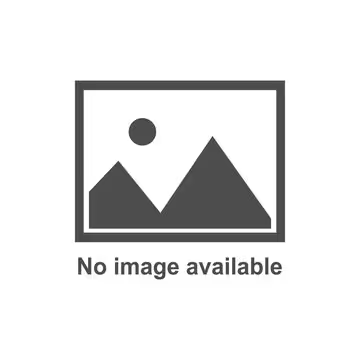
CASE STUDY – This digital organization has embarked on a cultural transformation that is allowing them to become more agile while keeping people and stimulating interactions at the heart of their work.
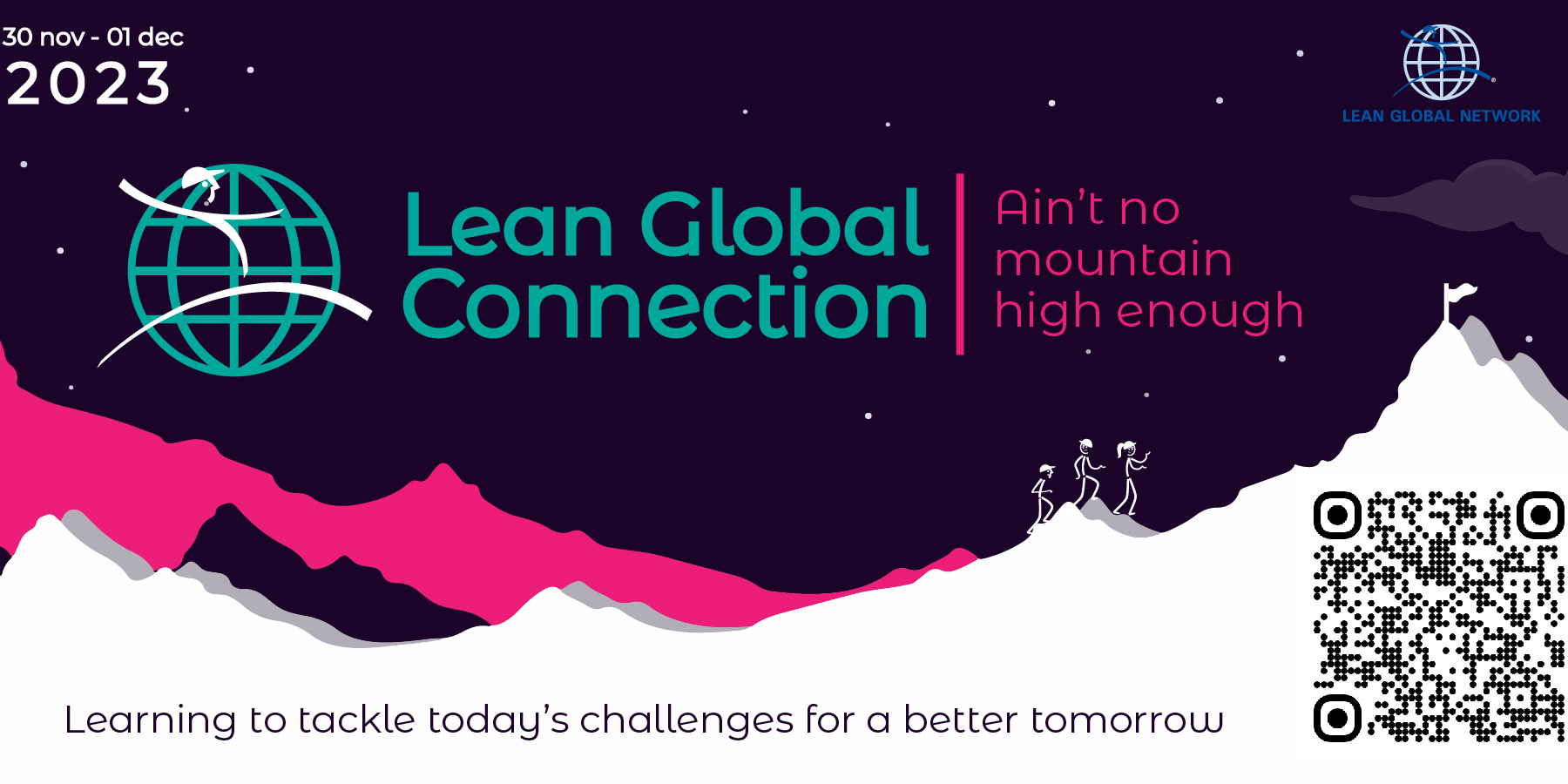
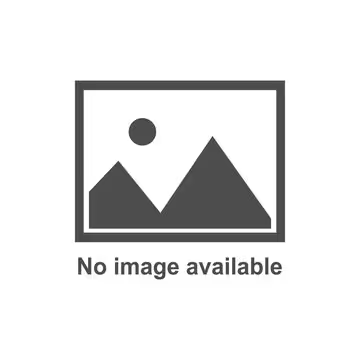
EVENT - The Lean Global Connection is around the corner! Our editor takes you through some of the key highlights you can expect and reminds us of the idea behind the largest online lean event in the world.