
Sensing the lean shift
INTERVIEW - Our editor sits down with the General Manager of Sensata Technologies to learn how they have been blending culture, leadership, and digital tech to drive agility in global sensor manufacturing.
Interviewee: Tommy Ver Elst
Roberto Priolo: How did Sensata Technologies begin its Lean journey?
Tommy Ver Elst: It’s hard to pinpoint an exact start date because Lean is a continuous journey, not a project with a deadline. That said, about 12 years ago, we began introducing basic Lean tools focused on waste elimination. At first, we trained our management and gradually cascaded that learning down to the shop floor. We made it a point to train our line and shift leaders alongside management, which helped build a one-team culture from the start. It was never just about the tools – we were creating a mindset.
RP: What did those early efforts evolve into over time?
TVE: They matured into more structured systems. We started developing standard ways for people to generate and act on ideas. Then we moved into data collection – initially with handwritten boards and tier meetings. Eventually, we digitalized those tier meetings and created real-time data displays, so operators could immediately see how their work was performing. This involvement helped them feel part of the journey. Now, we’re integrating AI and advanced visual control systems to further enhance quality and responsiveness.
RP: Can you talk more about the shift to digital and AI tools?
TVE: It started with simple automation – basic pick-and-place tools that freed up operators to focus on higher-value work. Now we’re using cobots and applying AI to visual inspections. The AI learns over time and eventually handles quality checks with minimal human input. But we're also looking at how AI can handle data analysis, so our engineers can focus on creative problem-solving instead of data wrangling. Internal logistics is also a growing focus, and all of this fits into broader concerns like CO2 reduction and sustainability.
RP: What’s the relationship between Lean and all this tech like?
TVE: There is no doubt our understanding of Lean Thinking has deepened tremendously since those early days. We now understand that Lean is about adaptability, mindset, and solving real problems, and technology just enhances that. The goal is still the same: create value without waste, and help people do their best work. Today, Lean touches everything from culture to strategy to how we use technology.
RP: COVID marked a turning point for a lot of business. Did it do so for Sensata as well?
TVE: Absolutely. It forced us to realize how volatile the environment could be. It pushed us to be more agile. We stopped pretending the world was stable and instead started asking, “What does this challenge mean for us?” We adopted what I call transitional leadership – not commanding from the top, but empowering people to navigate change. We trained our managers to stop seeing themselves as victims of circumstance and start translating external disruptions into internal opportunities. That cultural shift was huge.
RP: What does transitional leadership look like in practice?
TVE: It’s about creating psychological safety. Leaders must give people space to speak up and feel empowered to solve problems. Instead of dictating, we build environments where people feel supported and motivated. This kind of leadership helps us stay resilient even during crises.
RP: Speaking of crises, Sensata suffered a cyberattack in April this year. What can you tell me about that experience?
TVE: That event was a real test. On a Sunday, I got the call: our whole global network was affected. But what stood out was the response. We didn’t need to instruct people to help each other – they just did. Operators, engineers, maintenance, IT – everyone formed cross-functional teams on the fly. It was like a beehive of problem solvers. We were back online in 36 hours. The experience taught us about the power of culture: people knew the positive impact their work could have and acted with shared purpose.
RP: How do you keep technology from overwhelming the human side of Lean?
TVE: That’s a critical balance. Lean teaches us that technology should serve people, not the other way around. AI and digital tools must make work easier, not more stressful. It’s interesting to notice a generational divide: younger employees often push for more tech, while older ones may need more support and training. That’s why you need a bespoke approach for each. In both cases, we believe it’s about guiding people, protecting data, and ensuring everyone feels confident using new tools.

RP: Let’s talk about bureaucracy. How do you stay agile as you grow?
TVE: It’s a journey, to be honest, and every time there is a point of inflection. As companies grow, some bureaucracy is necessary to ensure consistency and compliance. But we’ve made mistakes – sometimes we created too many restrictions and ended up hurting productivity, even though we thought we were doing the right thing. The key is self-reflection. We ask: Are we still listening to people? Are we creating space for innovation? You need an environment where people can speak up when something isn’t working. That’s how we avoid becoming rigid.
RP: Final thoughts on Lean as a stabilizing force?
TVE: I still believe Lean is a beacon of stability. It makes the work predictable, which creates peace of mind in uncertain times. And even though we keep challenging ourselves and evolving our processes and technology, the core values stay the same. Lean helps us stay grounded, no matter what comes our way.
THE INTERVIEWEE

Read more

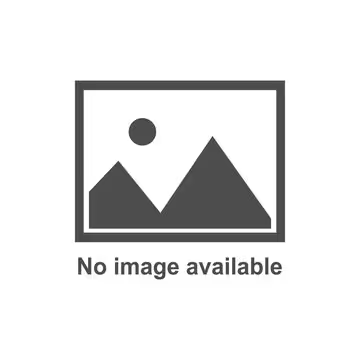
FEATURE – Sometimes you just need to get creative: as part of its flexible manufacturing model, Esquel introduced a new role on its shop floor – the “mangineer”.

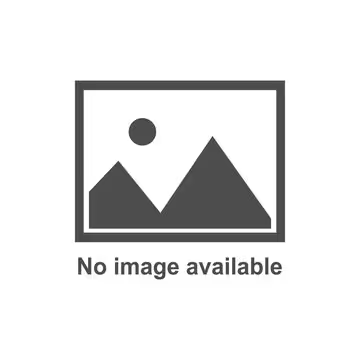
INTERVIEW – Ben Hartman has used lean in his micro-farm in Indiana for six years. Not only did he find in it a way to support his family doing what he loves, he might have also discovered how to transform our food system.
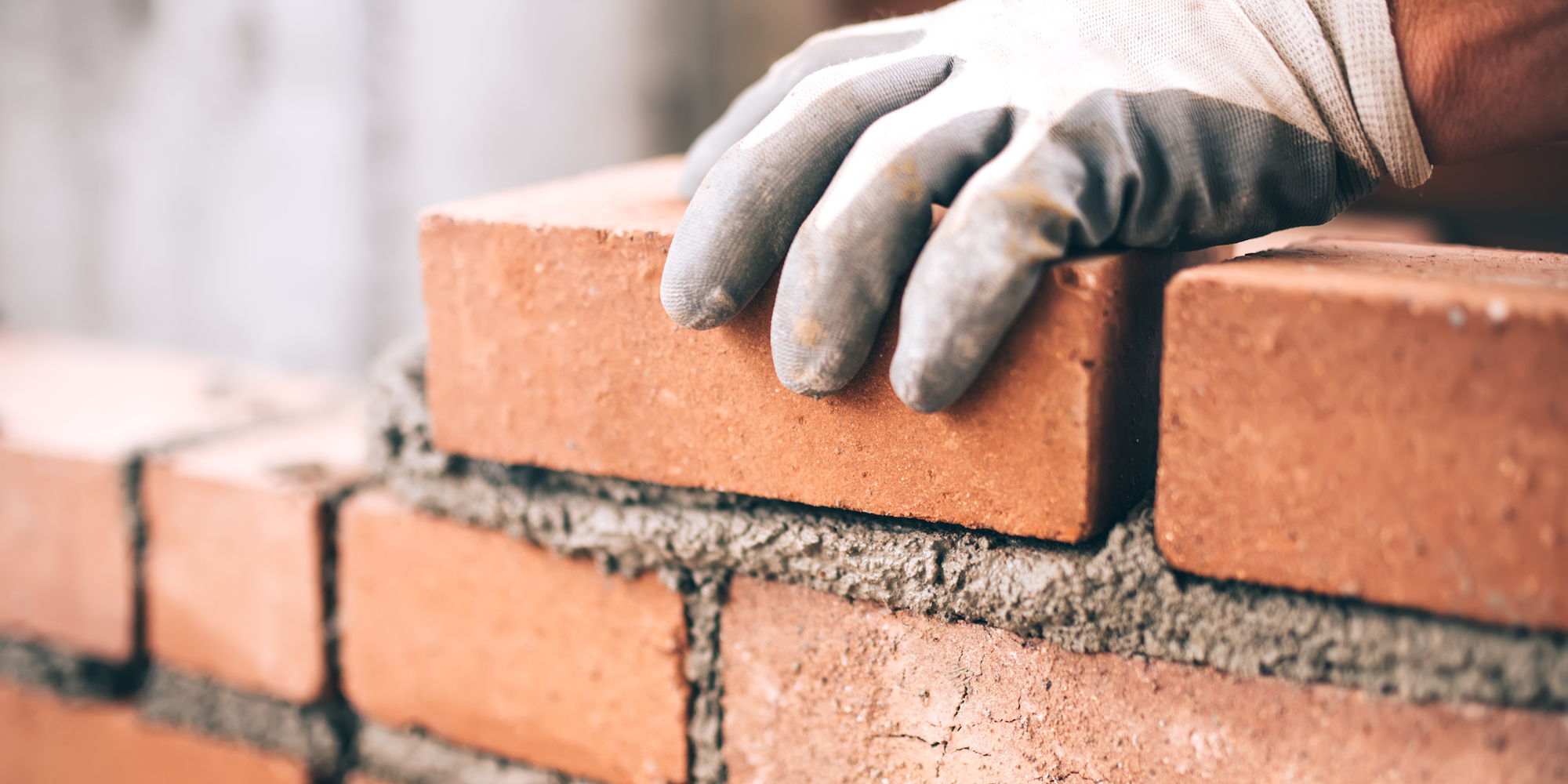
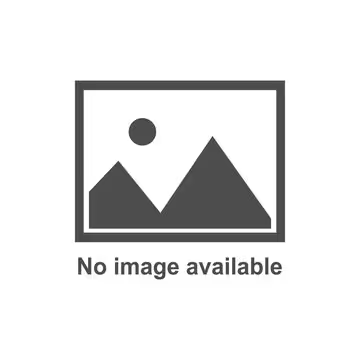
INTERVIEW – The editors of Planet Lean and Lean Post recently met with a senior executive of Turner Construction in New York City. Together, they discussed leadership development, respect for people, and the future of the industry.

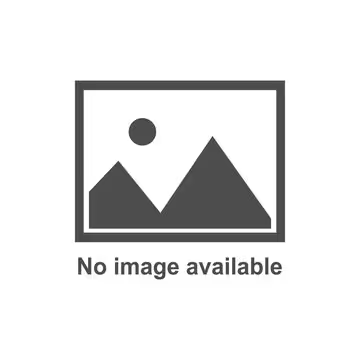

PROFILE - When years of hard work to re-organize Patria's IT operations led to disappointing results, Sari Torkkola didn't throw in the towel. Instead, she started to build her department's understanding of lean.
Read more
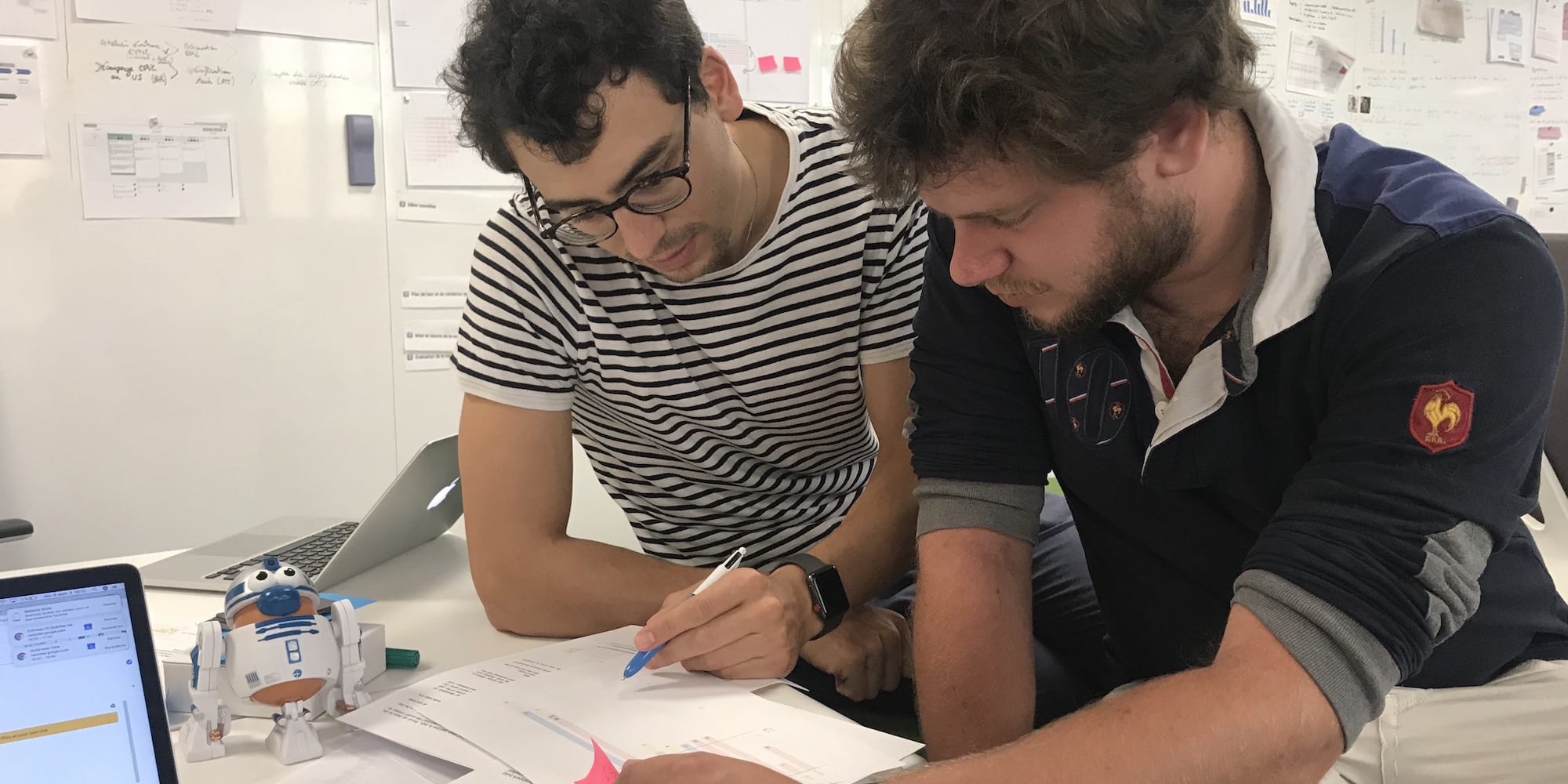
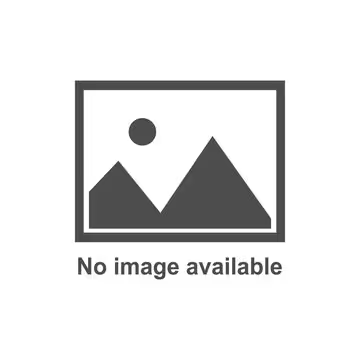
BUILDING BRIDGES – In another article for their series, lean digital company Theodo tells us about their efforts to measure and reduce its lead-time to deliver product features.
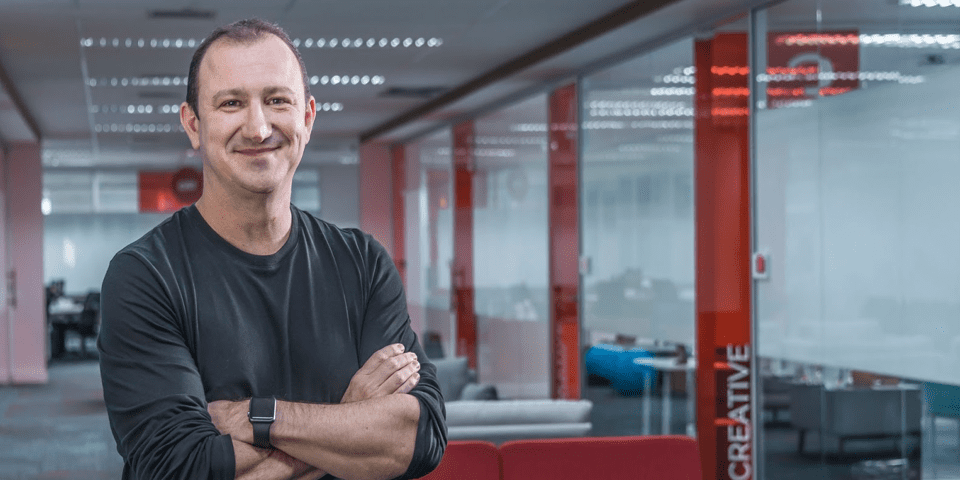
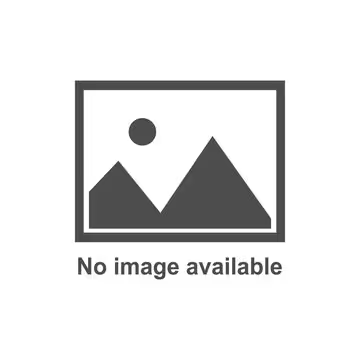
INTERVIEW – At last month’s Lean Digital Summit in Lisbon, César Gon told attendees how, with lean digital, we have an opportunity to finally get the attention of CEOs and business leaders.
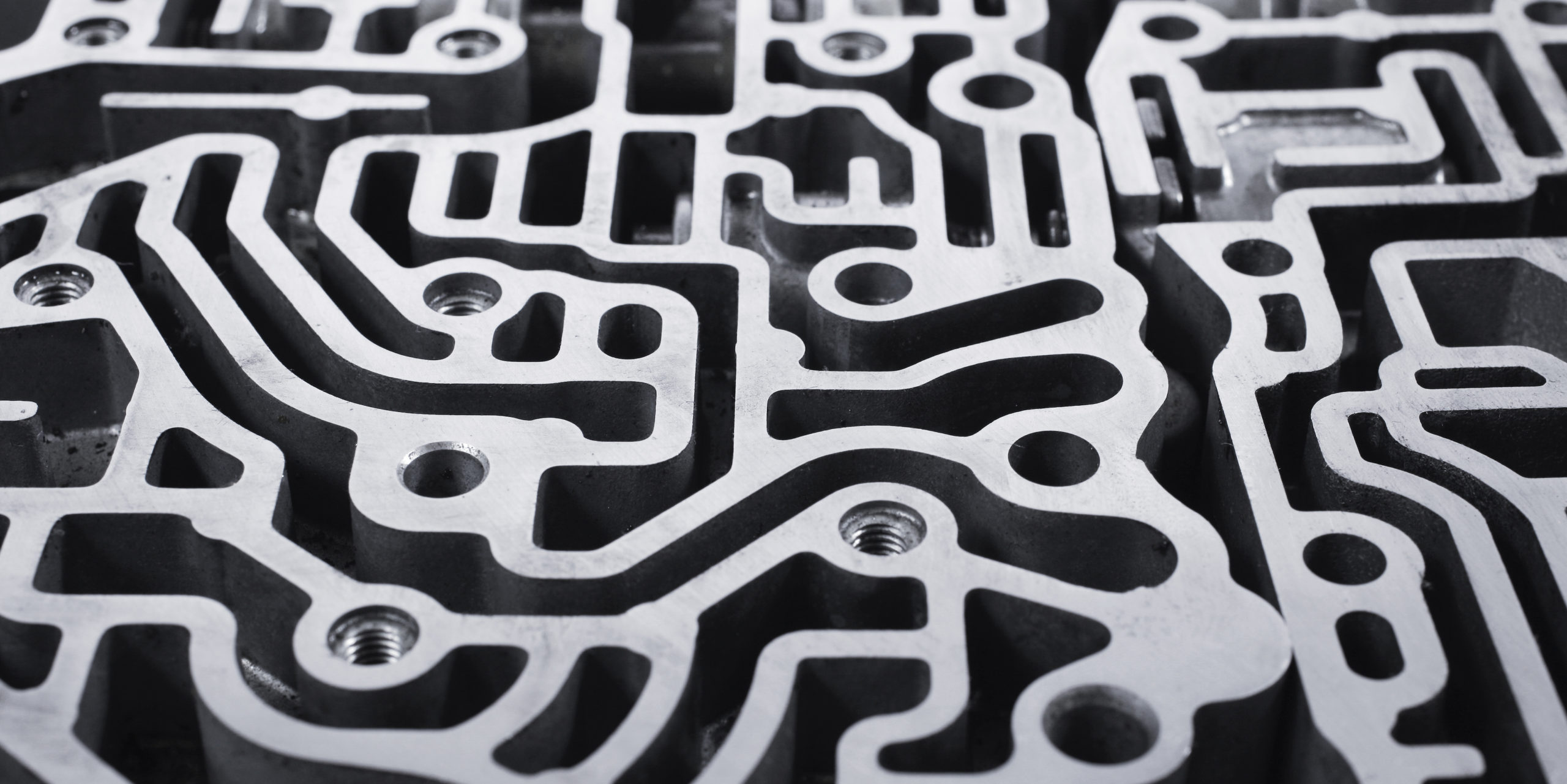
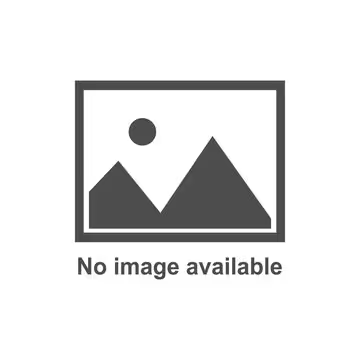
FEATURE – In a market where products become obsolete very fast, this Toyota supplier has learned the importance of staying true to its heritage and developing know-how and people’s capabilities.

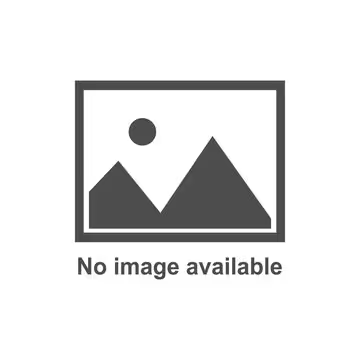
OPINION – A new publicly owned open-source technology promises to make direct, unmediated trade relations trustworthy, opening the door to an era of democratization and cooperation in global commerce.