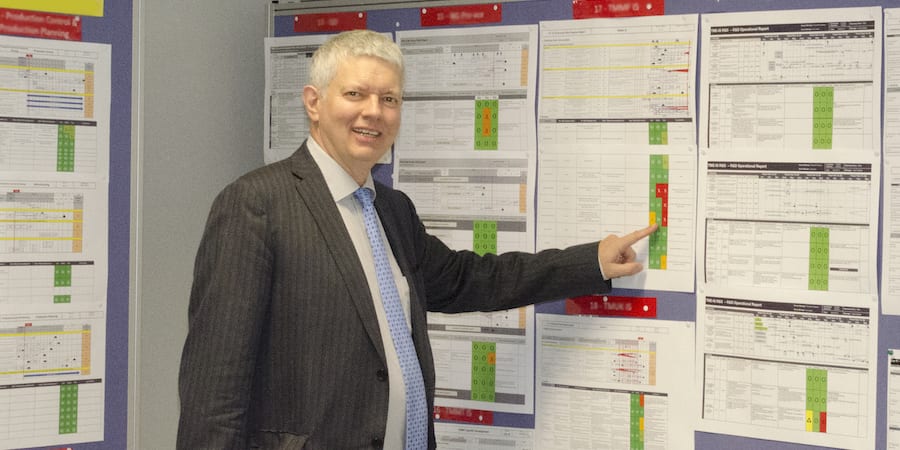
Polyglot and TPS student – a profile of Toyota Europe's CIO
PROFILE – A commitment to learning and the humility to understand we never really know enough have led a Belgian mathematician to become a polyglot… and the CIO of Toyota Motor Europe.
Profile on: Pierre Masai, CIO, Toyota Motor Europe
Words: Roberto Priolo, Editor, Planet Lean
Have you ever learned a language? If you have, then you surely know how difficult it is and how much of a commitment it requires. Watching movies, reading books, taking a course – no matter how you decide to do it, learning to speak a language that is not yours takes time and effort. That’s why whenever I meet a polyglot I am normally completely awe-struck.
I recently had the pleasure to have an hour-long Skype conversation with Pierre Masai, a polyglot who also happens to be the CIO of Toyota Motor Europe – which made him all the more interesting to talk to.
Having been born in Brussels, the bilingual capital of Belgium where French and Dutch are spoken, perhaps Masai had a bit of a headstart – basically, as a child he already spoke as many languages as I do at 32 – but this does not make his language resume any less impressive.
“I have always been interested in languages, at first for their structure,” he tells me. “Later on, my interest grew even stronger as I realized that languages would allow me to make contact and forge bonds with people from different cultures.”
Masai’s fascination with language structure is not surprising, considering that he studied as a mathematician. While working on theory of numbers, Masai started using computers to support his research and got interested in IT. By the time he was 24, he had two master’s degrees: one in mathematics, one in IT.
At the time, getting a job in the IT world was easy. “Companies would come look for you and hire you fresh off of university,” Masai recalls.
So he became an IT guy, working initially for a French services company that was later acquired by Capgemini. Two years later he moved on to Volkswagen, working in the company’s Brussels factory (today they make Audis there). Masai comments: “The reason I was hired was that I spoke German. It was my father who had suggested I learned German as my first foreign language. He said English is too easy, and that I would learn to speak it anyway once I learned German.”
Volkswagen was where Masai first learned about the automotive world and the car-making process. He was there for 13 years, starting as an analyst and ending up becoming IT director. Critically, at Volkswagen he was also exposed to the Toyota Way for the first time.
He says: “Everybody was very interested in the way the Japanese – mainly Toyota – made cars. At the end of the 1980s and beginning of the 1990s, Western automakers were notoriously behind Toyota and were studying the company in detail. Volkswagen even had a joint venture with Toyota to make utility vehicles in Hanover at one point.”
In the factory a lot of what we call lean principles were in use, not to mention Japanese terms. Before long, Masai became extremely curious about Japanese culture and began to attend evening courses to learn the language. However, he admits he is “not very good at it, being only at the second or ‘intermediate’ level.” I have the same problem… my Japanese is a bit rusty.
OFF TO ASIA
For a few years, Masai had wanted to see more of the world. In 1998, the opportunity arose to support VW operations in the city of Changchun, in northern China – a place where temperatures drop to -25C degrees in the winter, which made it slightly difficult for the company to find people interested in the post. But Masai was and he ended up spending two years in China as a senior manager in charge of Organization and IT.
Needless to say, while working at the factory in China – where his team only spoke a little bit of English – Masai learned Mandarin.
After his stint in Asia, Masai caught the attention of global leadership and was sent to Europcar in Paris (back then, and until 2006, the rental company was fully owned by Volkswagen) as global CIO. “As an IT executive who spoke French and had international experience, I ticked all the boxes. The global perspective of the job intrigued me,” Masai comments.
Yet, he didn’t stay with Europcar for long. Two years later, in 2002, Masai became CIO of a logistics company – Hays Logistics – based in the French capital. However, this old company – founded on the banks of the River Thames in 1867 – decided to sell their logistics branch shortly after Masai joined them.
In a period of transition for the organization, Masai worked as global CIO in Paris, but also as CEO of the German subsidiary in Düsseldorf from January 2004. “Occasionally, I would even get to stop in Brussels, half way between the two cities, to say hello to my wife and kids,” he jokes, although he admits that was a difficult time for him.
Eventually, Hays was acquired by a venture capitalist. Masai, however, didn’t stick around to see that. By 2005, he was back in Brussels and he was offered a job at Toyota Motor Europe.
He comments: “At the time, I felt like the pieces of the puzzle were coming together – I had observed what Toyota was doing from the Volkswagen factory, I had deepened my understanding of the automotive industry for nearly two decades and I had even learned Japanese! I thought that I had been working all my life towards this job – a perfect match!”
THE REAL DEAL
Masai started at Toyota on February 1, 2005. He was hired in sales IT, partly because of his manufacturing background. TME’s objective at the time was to merge the IT department of R&D, manufacturing and sales into one. Masai was leading the merge, but he wasn’t CIO yet.
It didn’t take long for him to realize that what he had learned by observing Toyota and studying the Toyota Way from the outside had merely scratched the surface. His mentor told him that he was “a seed under ground that he would help grow into a plant” and that he didn’t know the Toyota Way well enough to be CIO yet. He coached him every day until, in early 2011, Masai was eventually ready for the role he still holds.
“Of course, I continue to learn every day. I joined Toyota precisely because I wanted to know more,” Masai tells me. “What I have found is that most companies trying to copy Toyota focus on the tools but forget about the principles. You see many bold mission statements and lots of values on company websites, but I have never seen a company live and breathe its principles as much as Toyota does. They guide everything we do.”
His sensei once told Masai that so long as he understood and applied PDCA, he would never struggle, because in the face of a problem he would automatically reflect and try to make things better. As hard as they might be to apply consistently, the concepts are more important than the tools – a lesson we too often forget. “Learn the fundamentals and you will have leverage,” Masai says, “You need to understand the underlying reasons behind the introduction of each of the lean tools, and then you can apply them better. You are not just following a book, but truly understanding what you are applying and why – that’s what makes working at Toyota so great.”
In most organization the use of tools is prevalent and the understanding of the principles superficial at best. Masai shared an example: “You can do a lot of scrum in your firm but still have product owners that don’t necessarily start from the real customer needs. However, we found that by combining scrum/agile with one of our lean fundamentals – hoshin kanri – you immediately understand what really makes sense for the company. Doing agile alone doesn’t ensure efficiency. The tool is nothing but an enabler to help the company apply the principles.”
LEAN HAS TWO COMPONENTS
What I always found interesting about lean thinking is how it brings together the scientific approach and the need to work with human beings. Indeed, applying the methodology successfully requires finding a way to strike a balance between these two elements.
When I ask Masai if the scientific component of lean immediately appealed to his mathematical mind, he tells me: “Certainly. To me, A3 problem solving is so close to the mathematical problem solving! Truth is, we all tend to jump to conclusions, rather than understanding the current situation and analyzing a problem in the order we should – an A3 must be filled left to right, top to bottom. As people we don’t always act logically, because we – thankfully – have emotions. So yes, it’s important to strike that balance if we are to learn systematically as an organization.”
NEVER STOP LEARNING
Masai’s sensei once told him that after 35 years at Toyota he had only scratched the surface. Indeed, the CIO of Toyota Motor Europe really seems to believe that the more you learn, the less you seem to know. Having being at the company for “only 11 years,” Masai calls himself “a relatively young student of TPS” and speaks with the humility of a newbie – which is sort of funny, because it makes us wonder if and how we will ever get it. I asked Professor Dan Jones to share a couple of thoughts on Masai as a lean leader, and he told me: “Pierre is unique in combining an intellectual curiosity and passion for learning with humble respect for learning by doing, which is how you really understand TPS and the Toyota Way.”
But Masai’s extraordinary commitment to expanding his knowledge doesn’t stop at Toyota. As if having learned to speak eight languages (French, English, Dutch, German, Italian, Spanish, Chinese and Japanese) weren’t enough, Masai is currently working on a PhD at the University of Strasbourg – something he has always wanted to do – where he was first invited to teach a lean IT course three years ago. The PhD has given him the opportunity to re-learn some of the IT concepts and practices that he knew when he was 20 and that he had since then forgotten. More importantly, it has given him the chance to work closely with developers, which increased his understanding of their every-day struggles.
He concludes: “I will be 58 next month. If I want to inspire people to never stop learning, I have to do it myself. I must lead by example.”
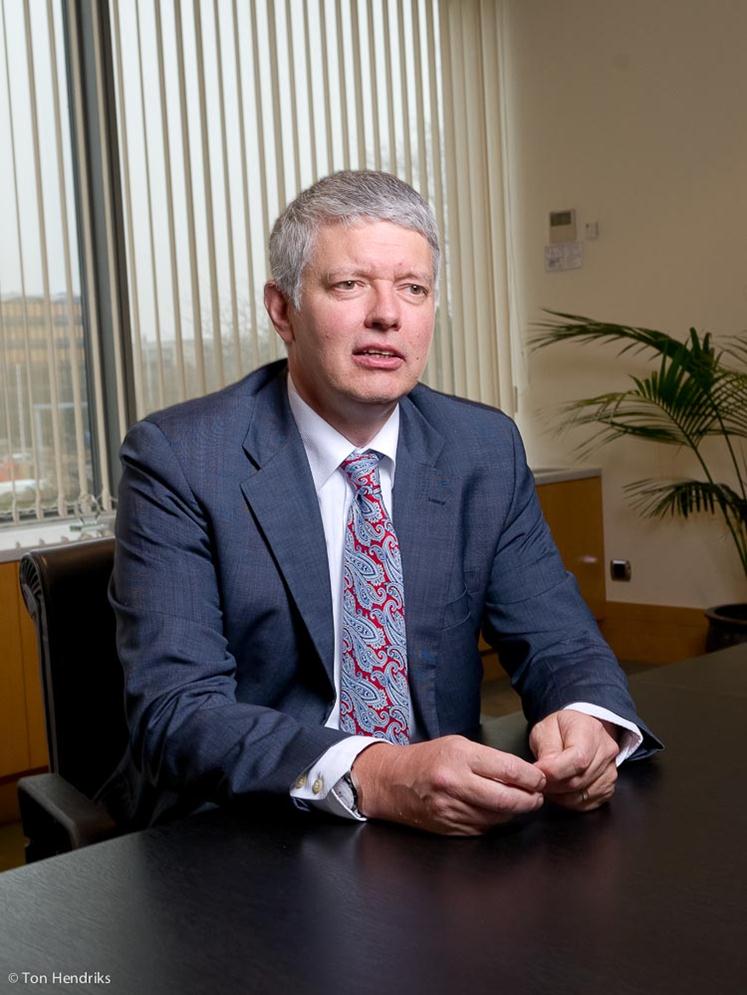
Read more
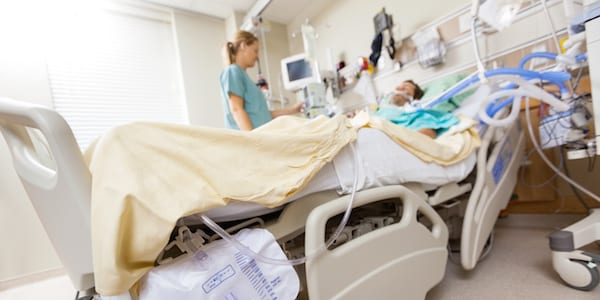
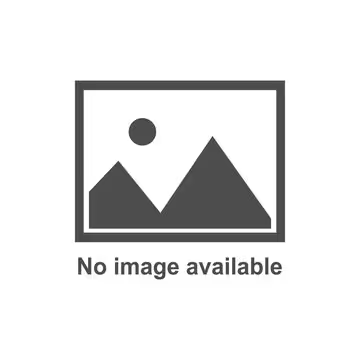
FEATURE – No healthcare transformation can succeed without a system-wide approach to change. In this article, Dr. John Toussaint, offers his take on the issue, providing a guide for healthcare executives.

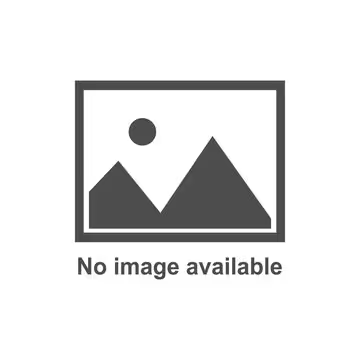
INTERVIEW – If we truly believe lean can change society, then we should use it as a lens through which to look into different aspects of our lives – even when those associations are hard to make. This month, we discuss the world of media.
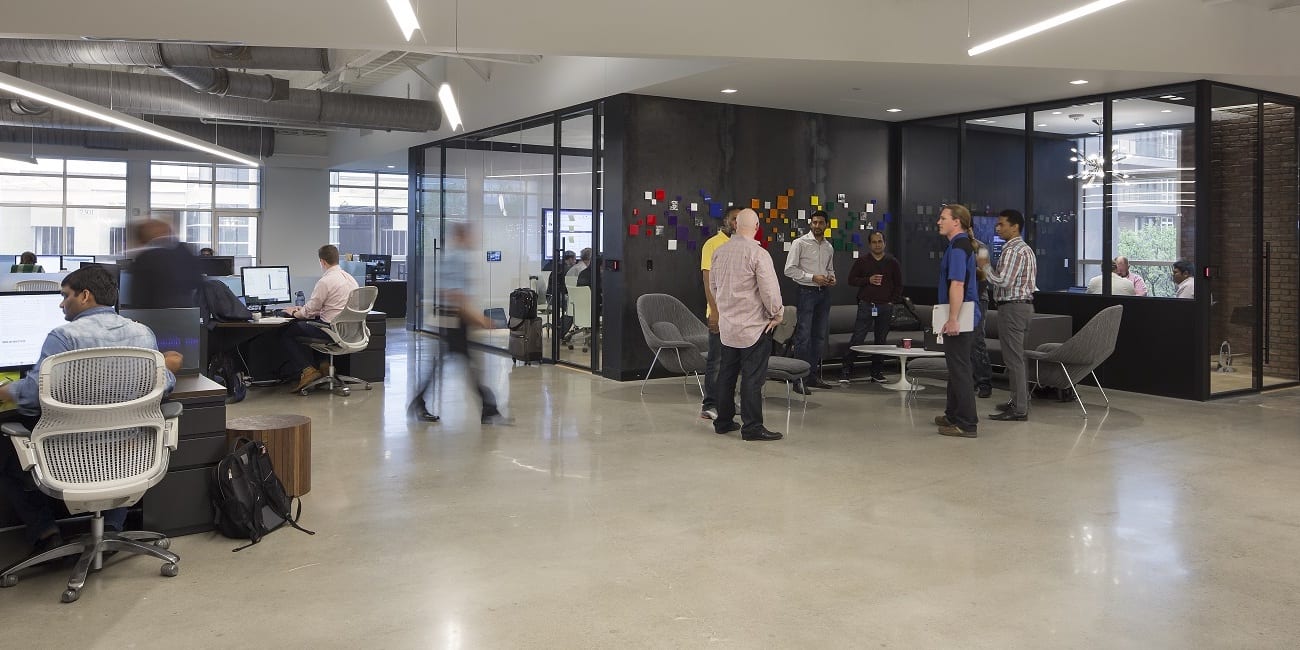
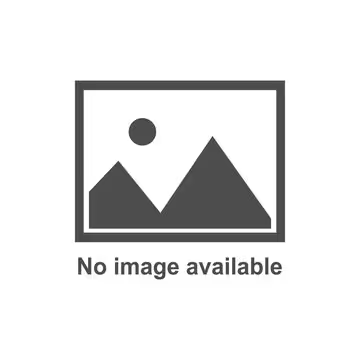
INTERVIEW – The Chief of Agile at Toyota Connected tells us about the agility journey of Toyota and explains why the divide between lean thinking and Agile has no reason to exist.
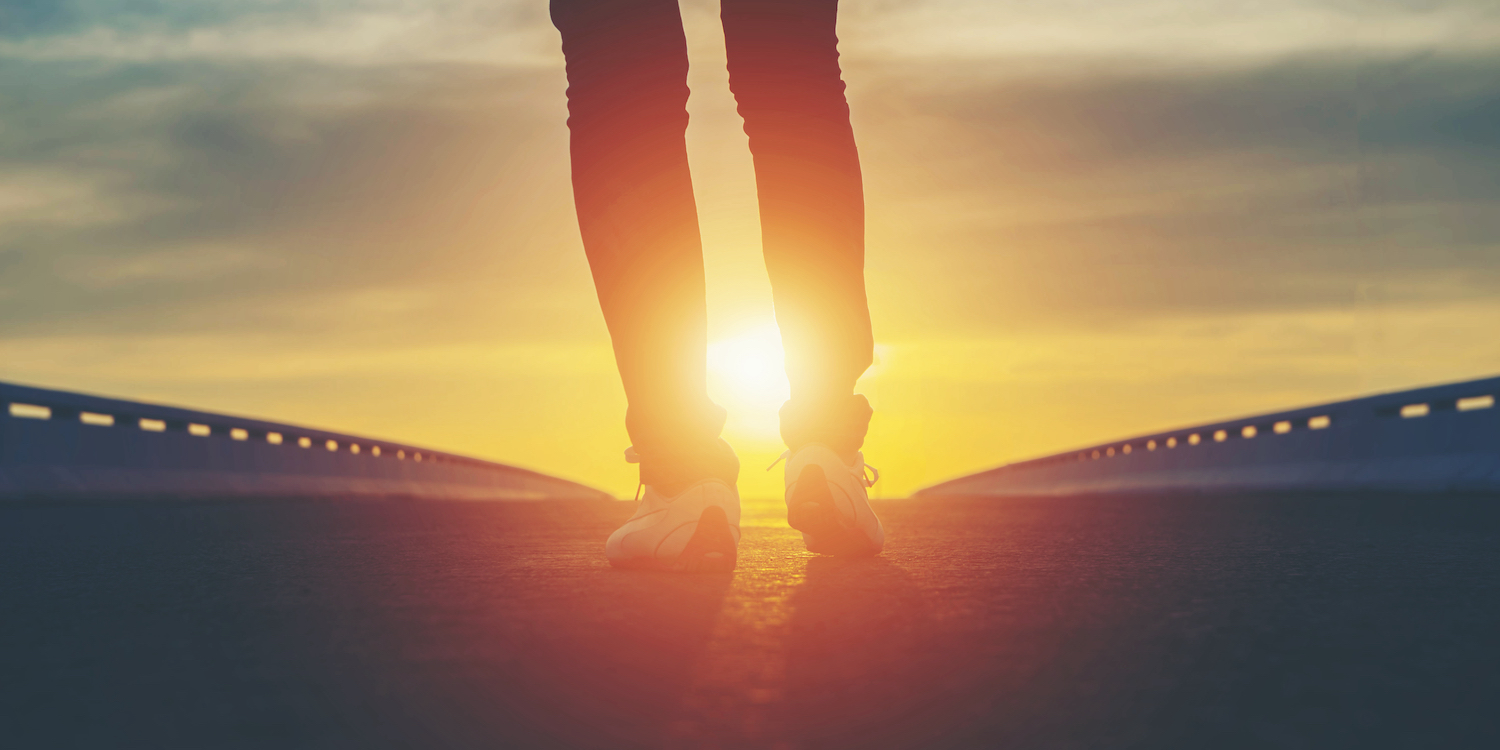
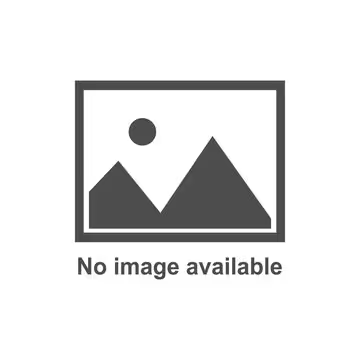
FEATURE – Can lean relieve some of the pain and fear people experience in this crazy world? It can, says the author, because amid so much noise lean carries one truth.