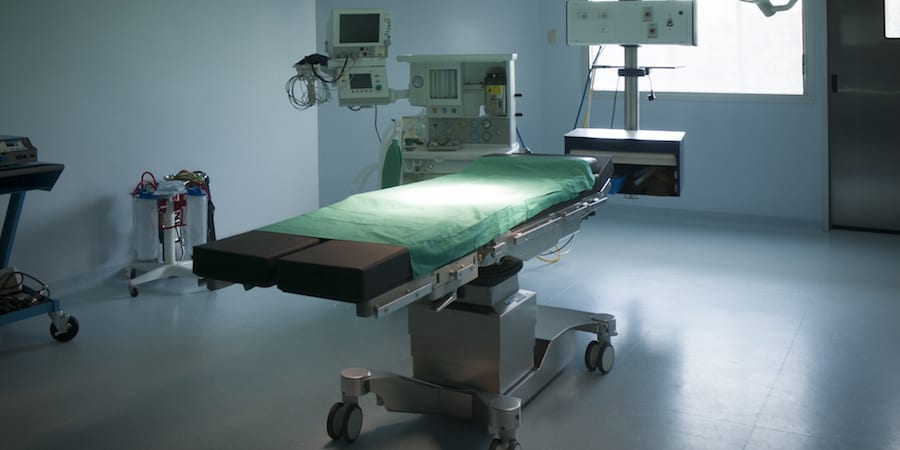
How the initiative of nurses transformed a whole department
FEATURE – We can't go wrong when we trust our people to take the initiative that we will improve their work... that's how Siena University Hospital cut its procurement lead-time in Surgery by two-thirds.
Words: Davide Lastrucci, surgical nurse for urgent procedures, and Carmela Sorriso, surgical nurse for planned procedures.
Our project, which we presented at the hospital's Lean Day last year, started shortly after, and on the back of, another initiative – larger in scope – that aimed at reorganizing the whole of the surgical department.
This idea is to provide care in dedicated areas of the hospital, depending on the type and intensity of treatment patients are to receive, the length of stay and the expected hospitalization regime – gradually moving away from all-too-common siloed approach that sees the provision of care take place in separate wards and towards a model that puts the patient at the heart of what we do and simplifies the clinical path accordingly.
The project kicked off in June 2014, with the simultaneous launch of two surgical paths: Planned Procedures (with 89 beds) and Emergencies & Traumatology (with 36 beds and a new dedicated surgical block). This massive change affected 11 operating units and the staff working there: 60 doctors, 120 nurses, 74 healthcare assistants and 5 nursing coordinators.
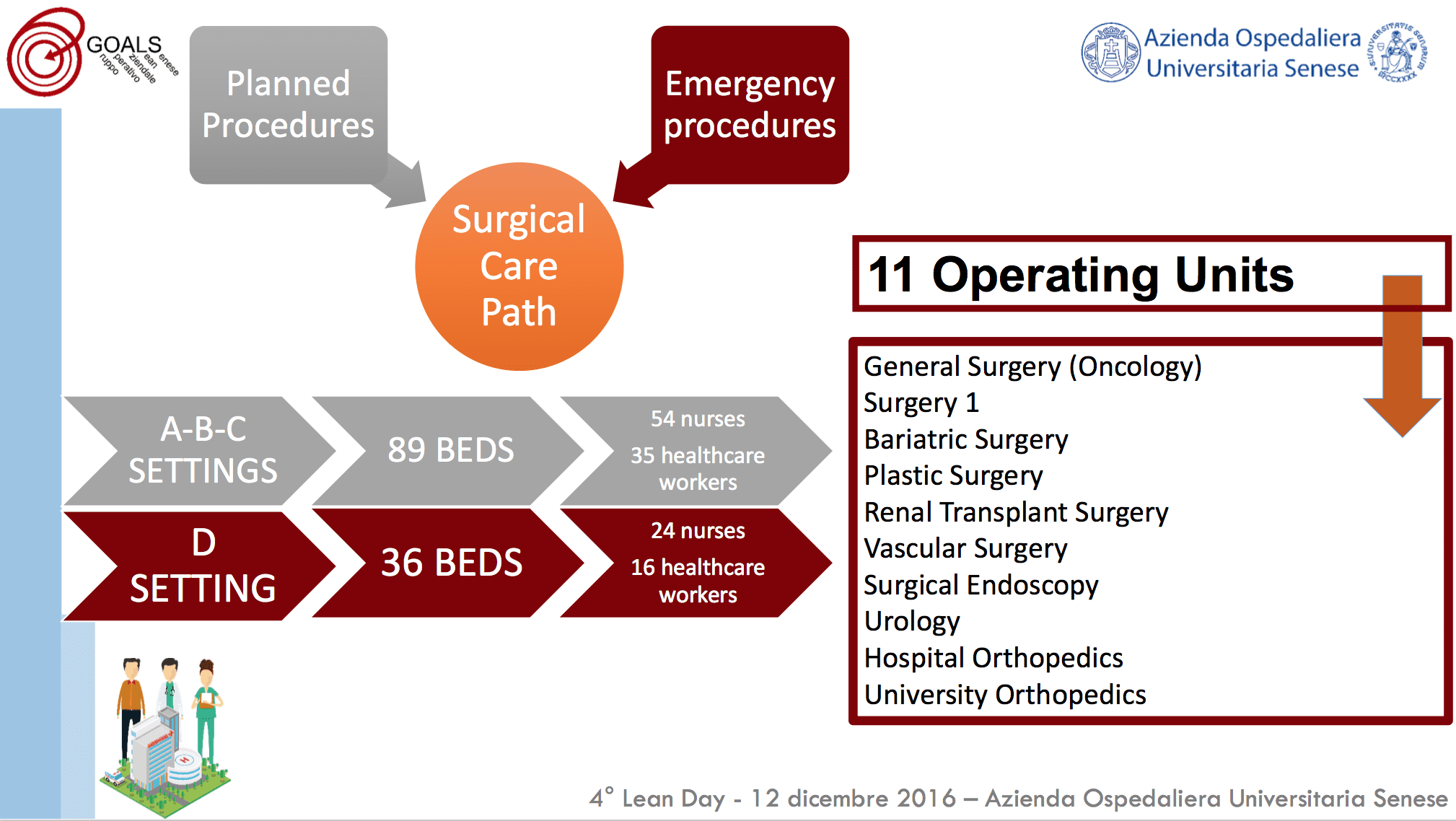
With the new system in place, we wanted to contribute to the creation of a lean organizational model that would allow for the continuous improvement of our work: to this end, we introduced the concepts of clinical path, hospitalization cell, and visual management. Both the physical characteristics of the Surgical Department (four areas located on different floors and blocks of the hospital) and the high number of people working there made it necessary to redesign the working space with standards and functionality as our main concerns.
The first push to change the way the department was organized came from our nurses, who know the healthcare processes and the layout of our work space better than anybody else. Their suggestion – fully supported by the Nursing Coordinators and by the hospital's Board – was to review the overall layout of the Surgical Department and to introduce the 5S technique in the warehouses, nurse stations and medical trolleys. Our Cell Design and 5S efforts had the objective of standardizing the processes, improving the work space, ensuring quality and safety, and more in general making it as easy as possible for our professionals to carry out their work.
Lean teaches us that value is created by removing waste, and that improvement stems from teamwork. With this in mind, we created two nursing work groups – one for the Planned Procedures and one for Emergencies – both supported by our in-house lean experts. 5S was applied in all the warehouses in the Surgical Department, as well as the nursing stations and the trolleys – wherever necessary, the layout was modified.
Below, you can see the maps of our areas – with the 5sed sections highlighted:
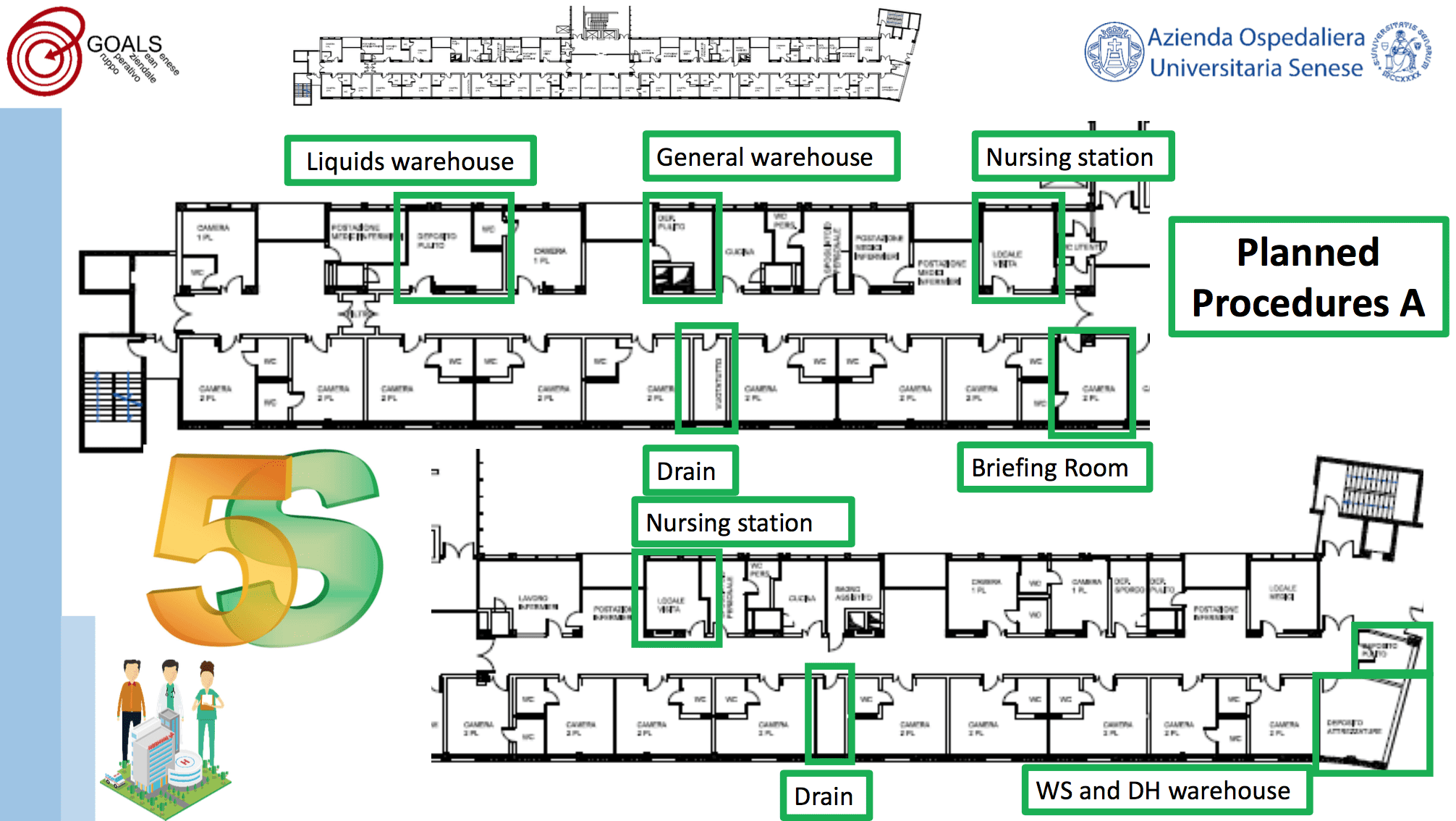
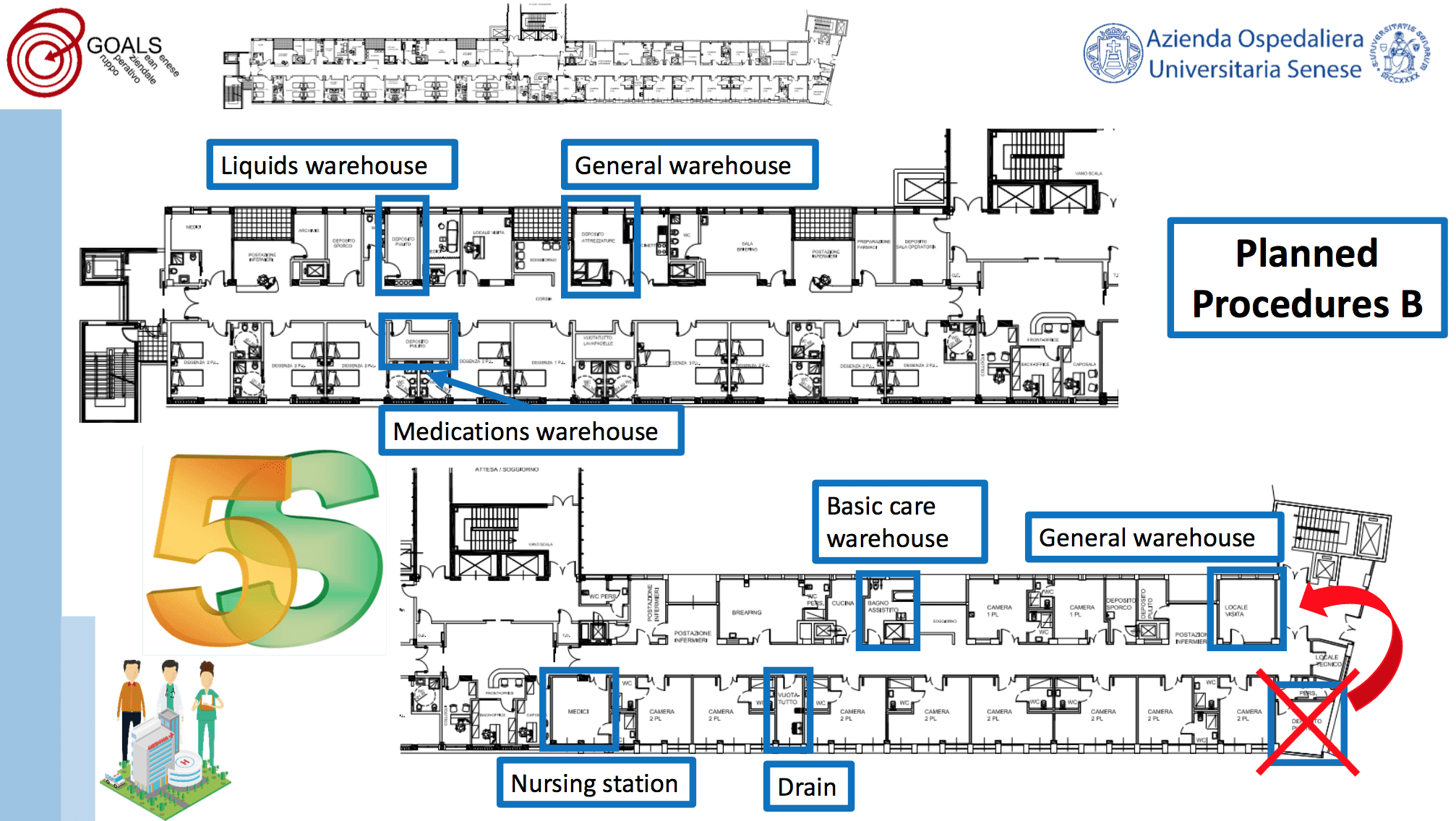
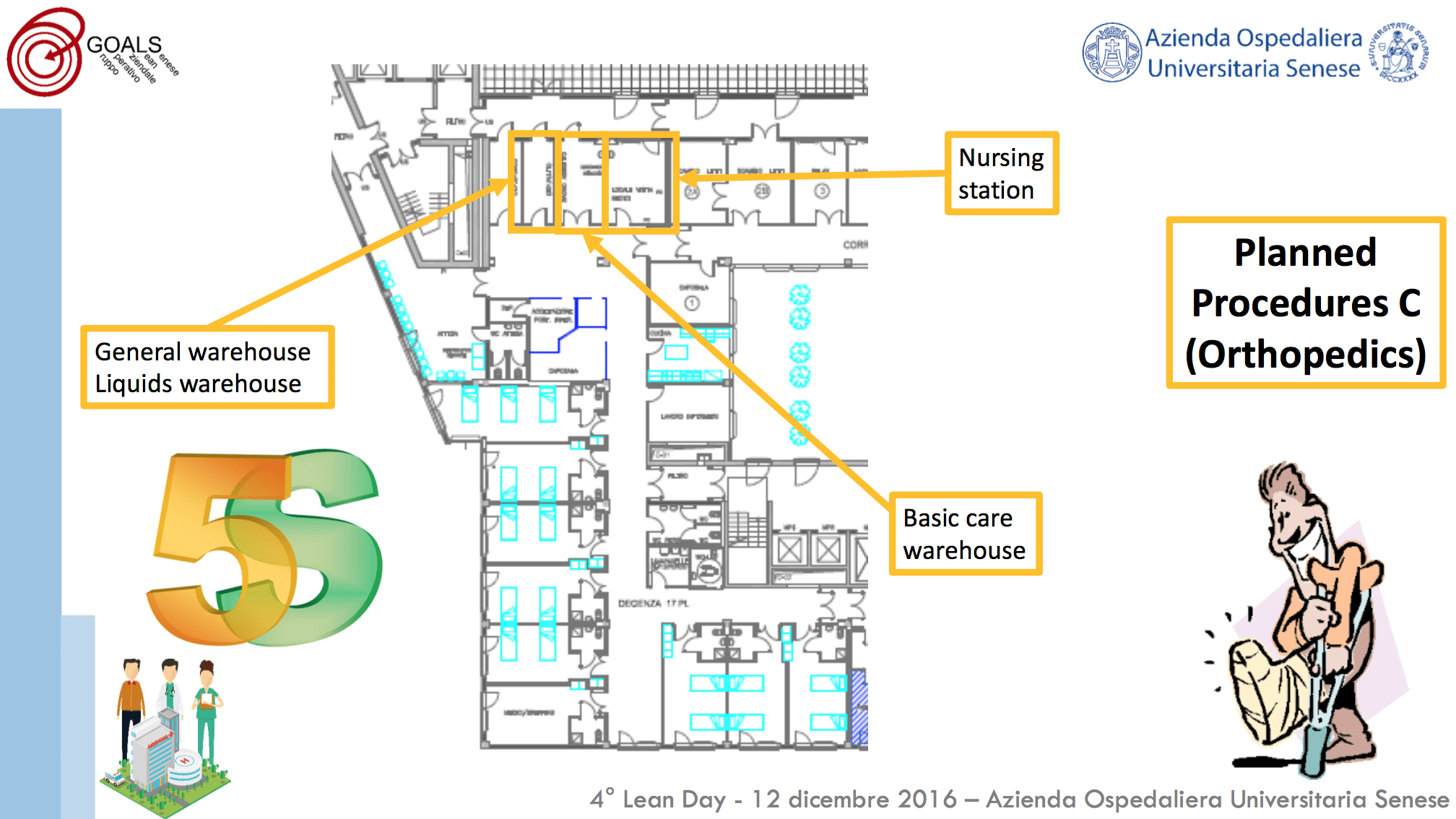
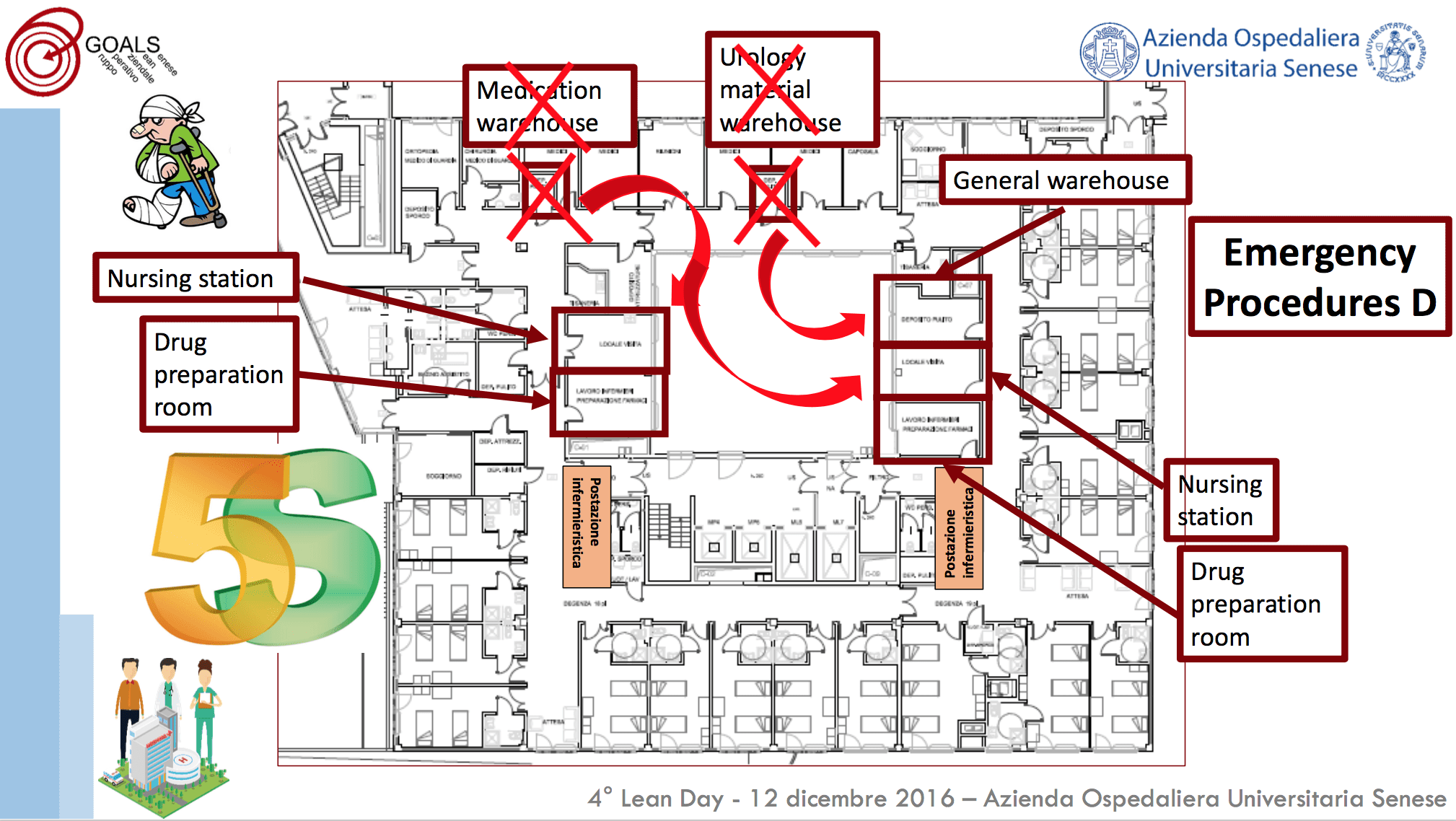
HOW WE DID IT
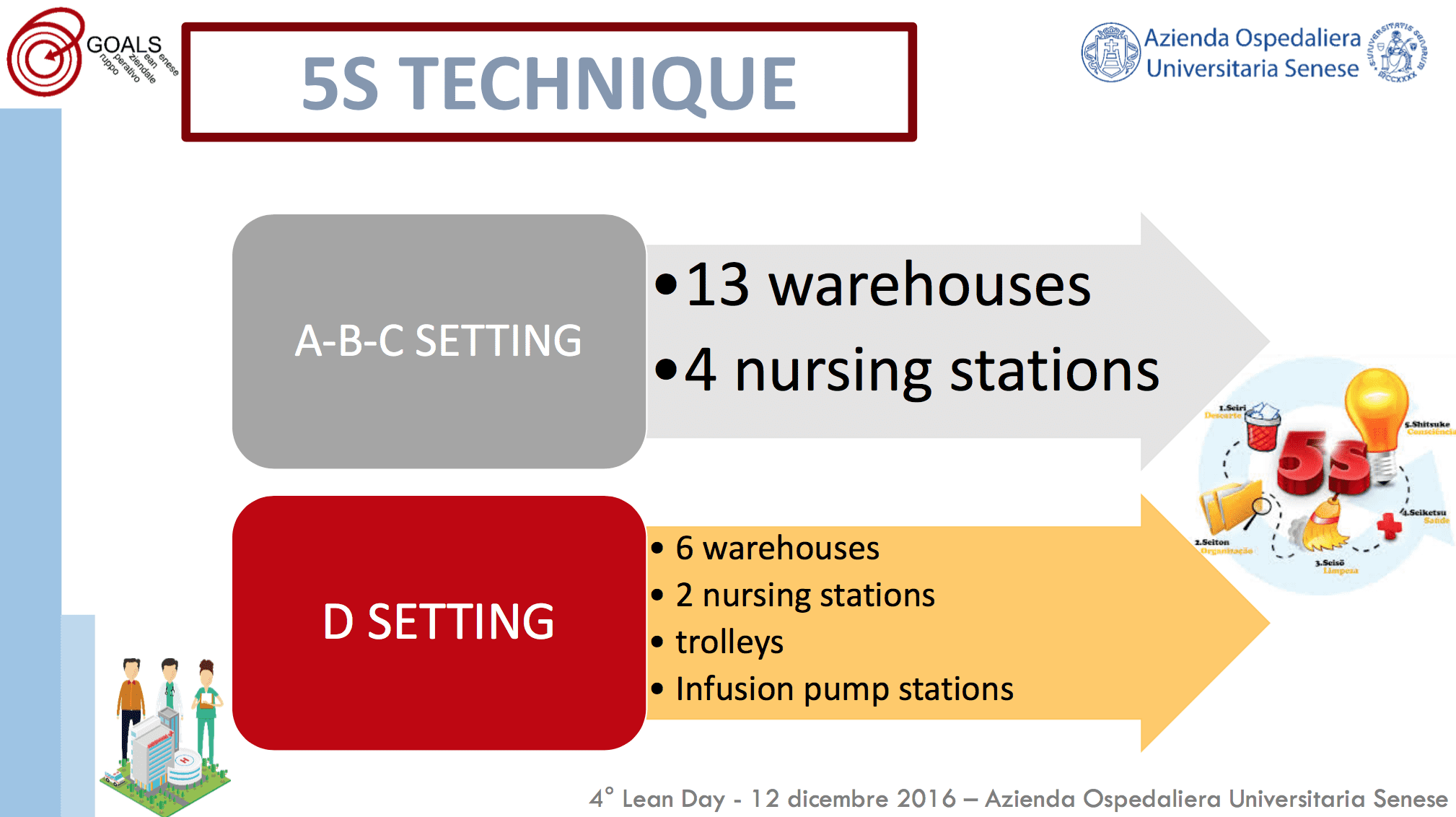
We approached our problem in the same way every problem should be approached: following A3 Thinking. We began by analyzing the current state, which revealed that the location of the nursing stations as well as the way the material was organized in the warehouses did not follow any logical pattern: we had been stocking (too many) products this way for years, without thinking about the unnecessary movement and the wastage that this generated, not to mention the huge amount of inventory we carried. No wonder we experienced so many delays in the sourcing of materials and so many interruptions in our work!
After that initial analysis, we set out to identify the root causes of our problem. We did so by using an Ishikawa diagram, which highlighted the four areas on which our focus would be: organization, staff, work space and materials. At this point, the team set two objectives:
- Cut the procurement lead-time by 50%;
- Cut the number of orders (materials and drugs) for the emergencies by 30%.
The potential countermeasures we came up with were, as we discussed, a review of the layout and the organization of supplies and instruments based on the Cell Design principles, the 5S techniques, visual management tools and kanban cards.
The review of our layout resulted in the relocation of a number of our warehouse, which , according to our analysis, were too far from the nursing stations. The use of 5S allowed us to standardize the work and reduce the lead-time for the procurement of materials, while the extensive employment of visual management made it very clear where materials are now kept. In turn, kanban cards and colored tape have made it much easier for us to manage our inventory: after calculating how much of any given product we had, we implemented checklists with minimal and optimal quantities of each item. For each item, we defined the minimal and the re-order quantities, considering the average delivery time for drugs (in our hospital, it is ward personnel that takes care of the orders, rather than the logistics department operating in other hospitals).
A few examples of before/after that will show you the impact of the workplace organization initiative:
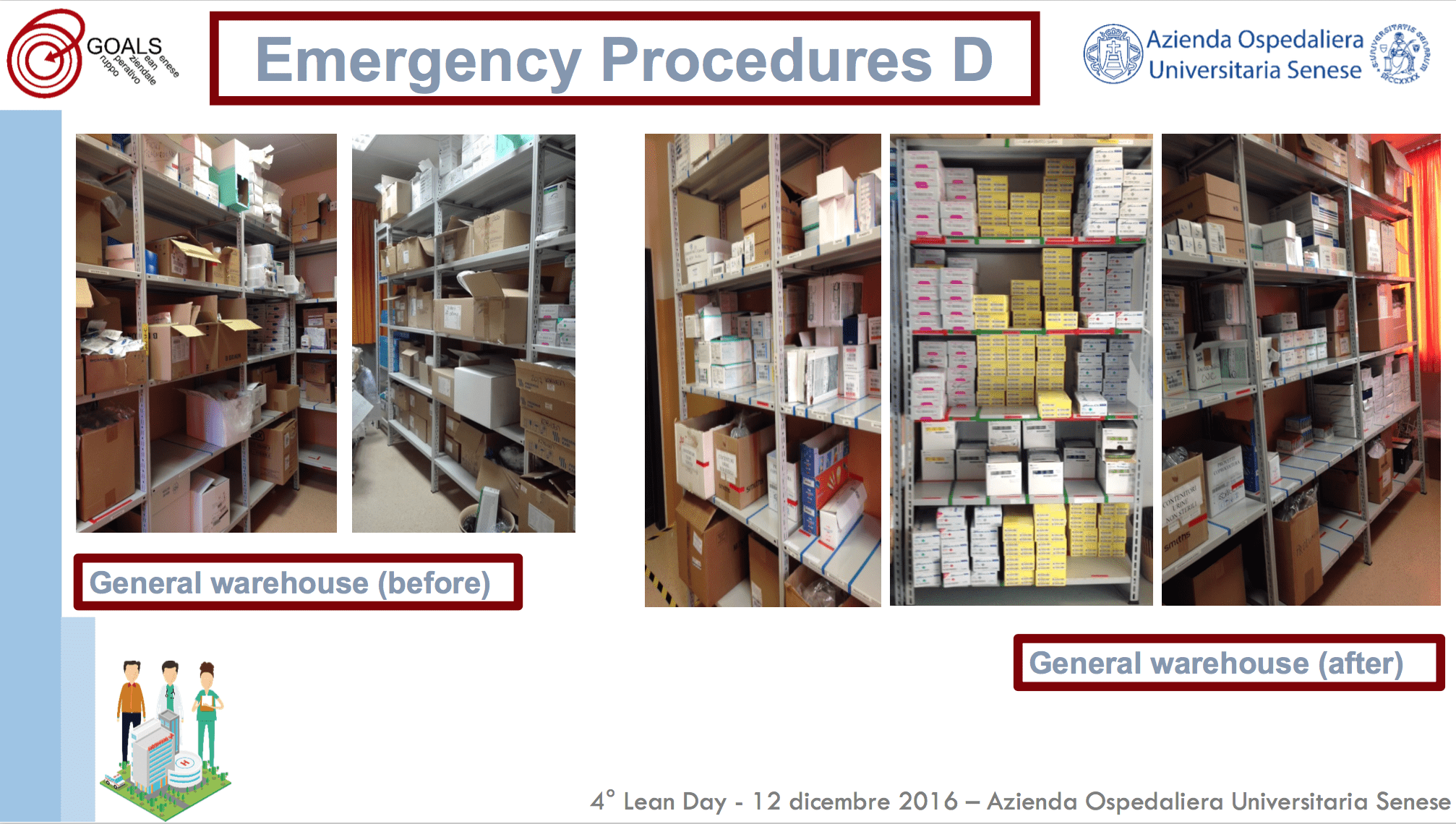
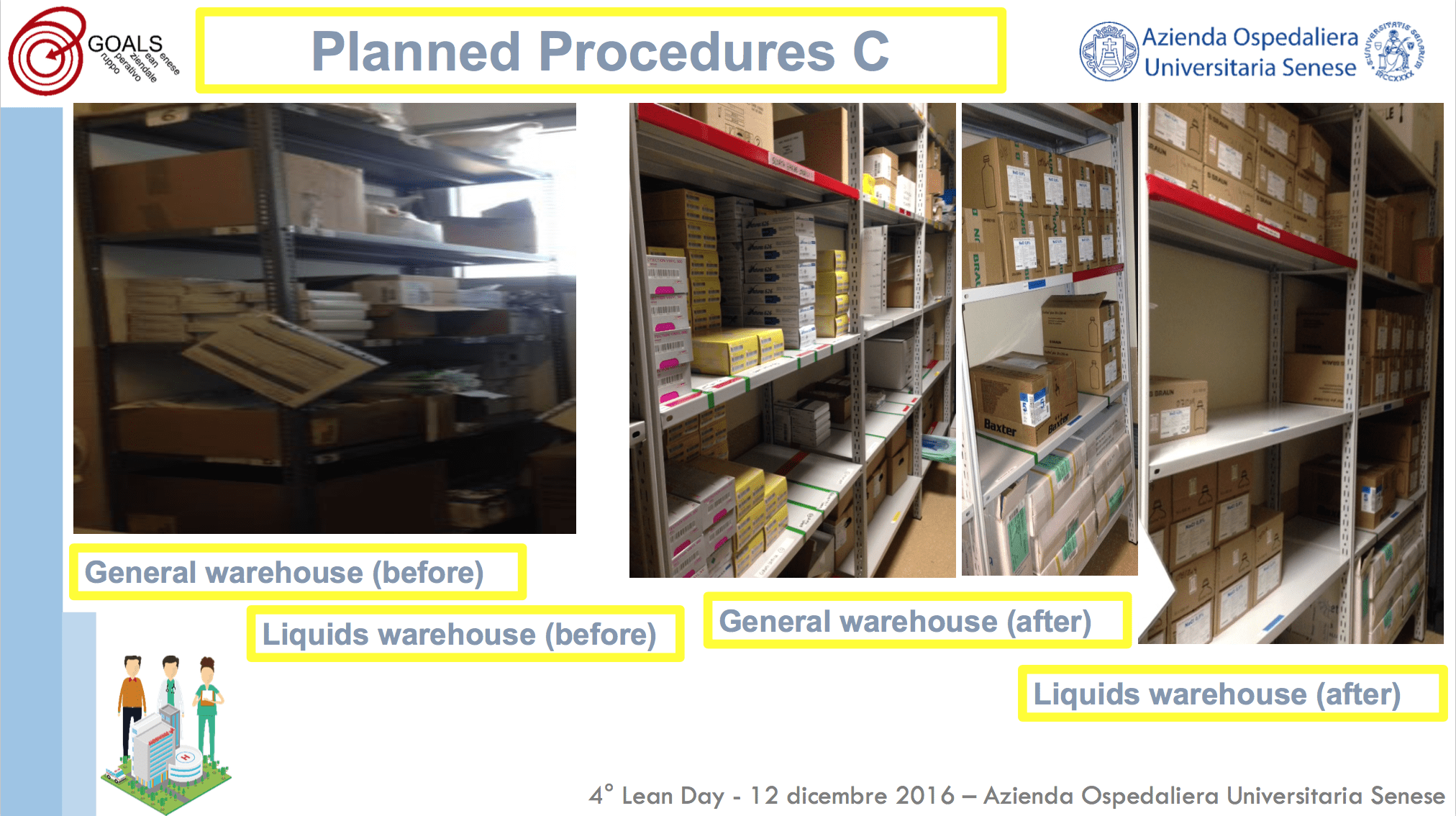
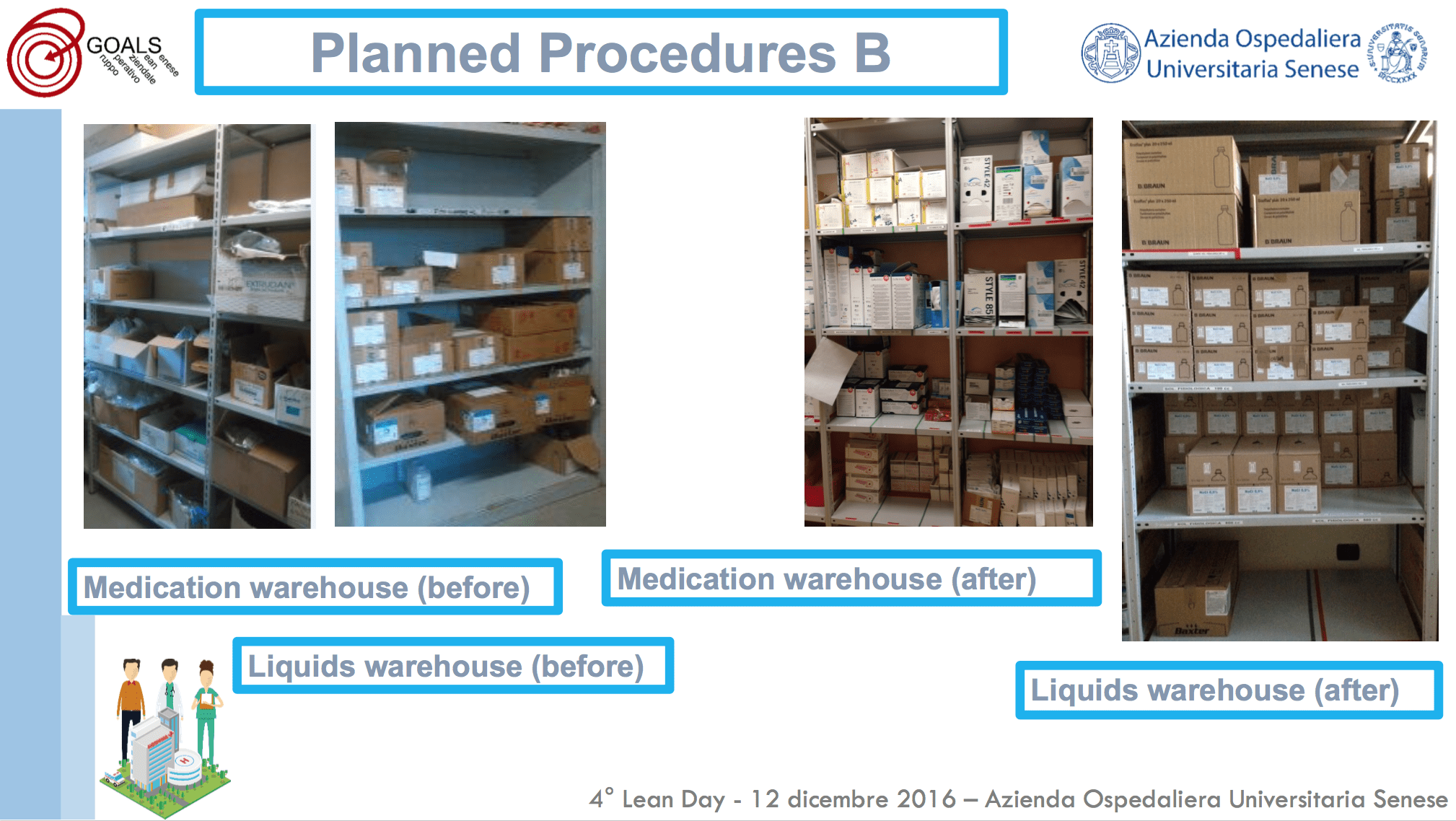
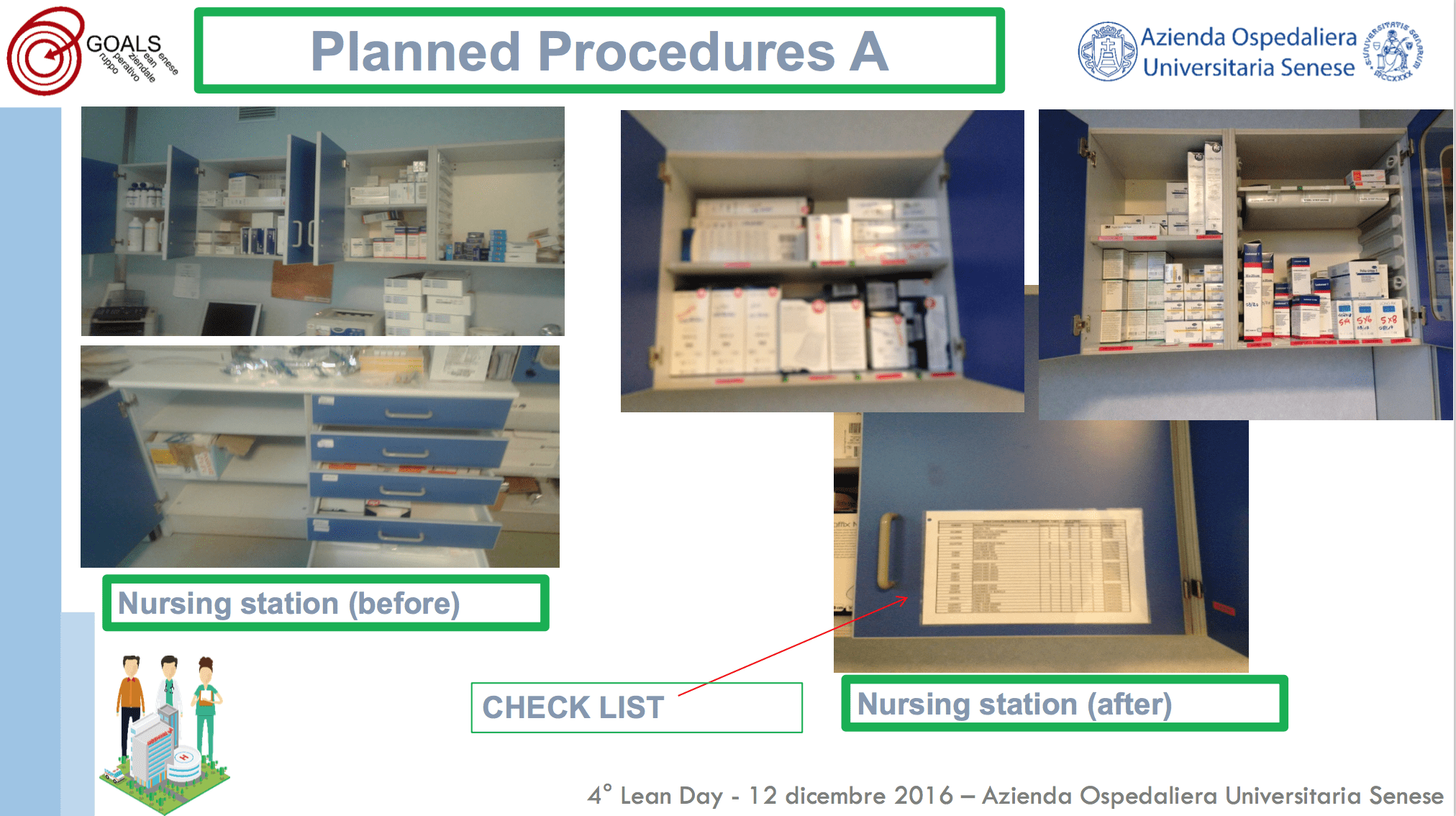
The results of this project have exceeded our expectations – and our targets. The number of orders has been reduced by 30% – in line with our objective – but the lead-time has been reduced by two-thirds, going from 30 minutes to 10 minutes. None of this would have been possible without the extraordinary work of our team, who has implemented the changes and, more importantly, sustained them over time.
THE AUTHORS
Davide Lastrucci and Carmela Sorriso are surgical nurses at Siena University Hospital
Read more
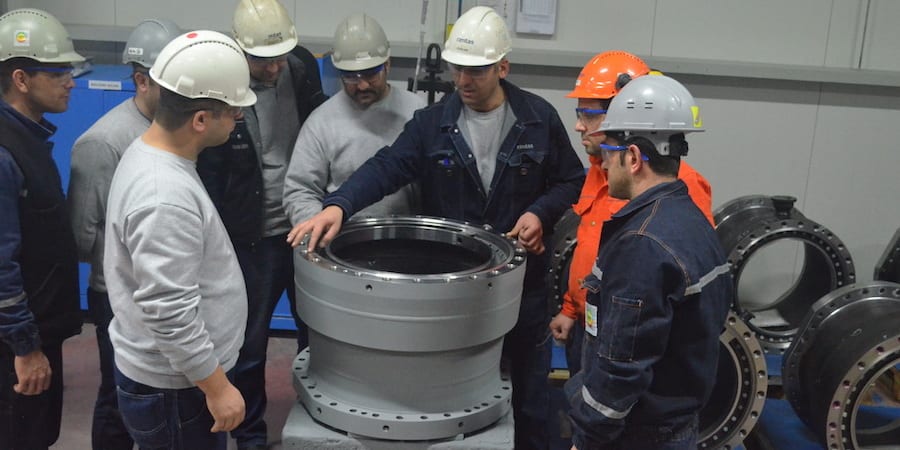
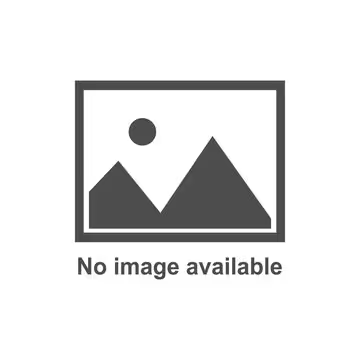
CASE STUDY – With plans to double capacity year on year in its new precision machining business, a Turkish company found in lean a way to control growth by stabilizing old processes while new ones are introduced.
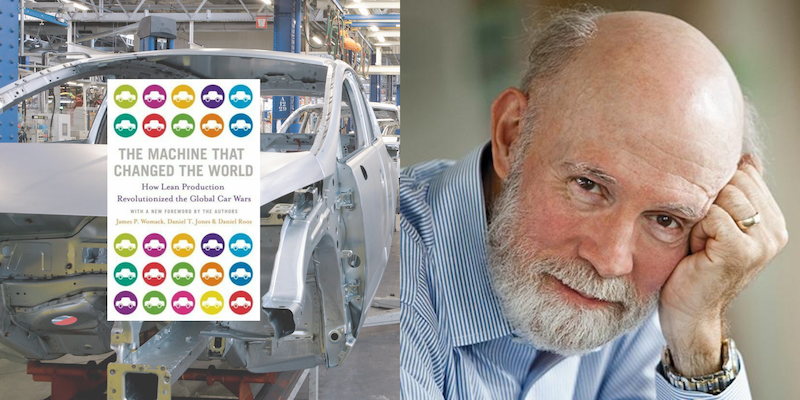
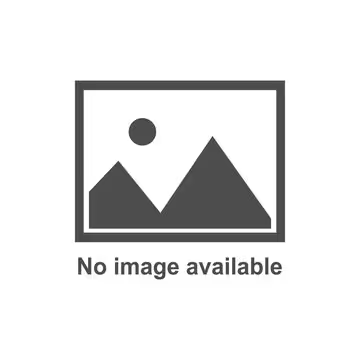
INTERVIEW – Thirty years ago, a book introduced lean thinking to the world, started a global movement and transformed business forever. Our editor caught up with one of the authors.
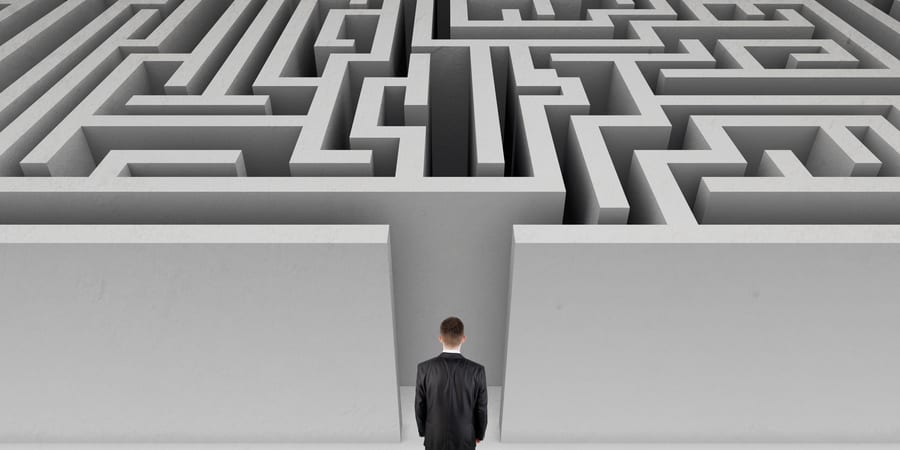
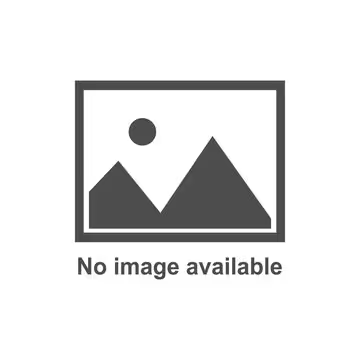
RESEARCH – The author explores the effectiveness of five common managerial practices in driving a corporate lean initiative forward, analyzing the data gathered while visiting 36 factories of a large corporation.
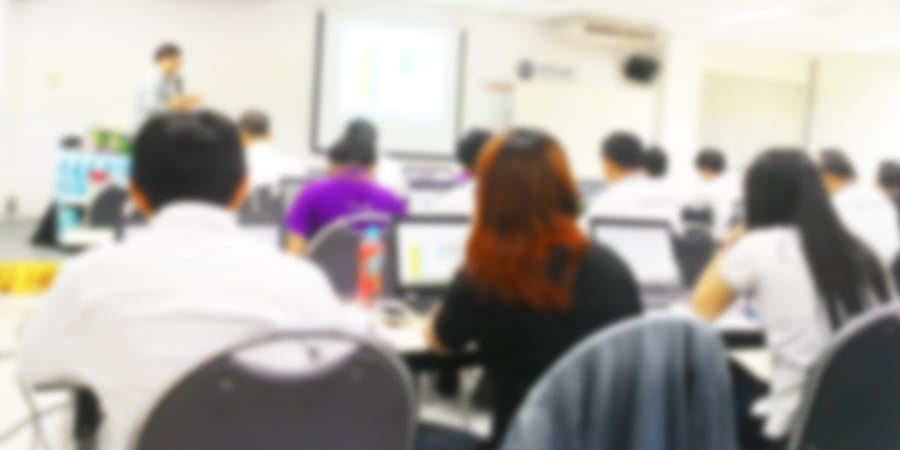
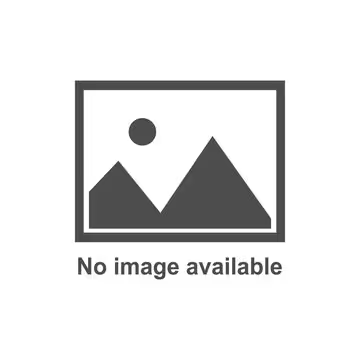
WOMACK’S YOKOTEN – Somehow surprisingly, management schools teach very little about management, and when they do all learning is classroom-based. Instead, they should go to the gemba.