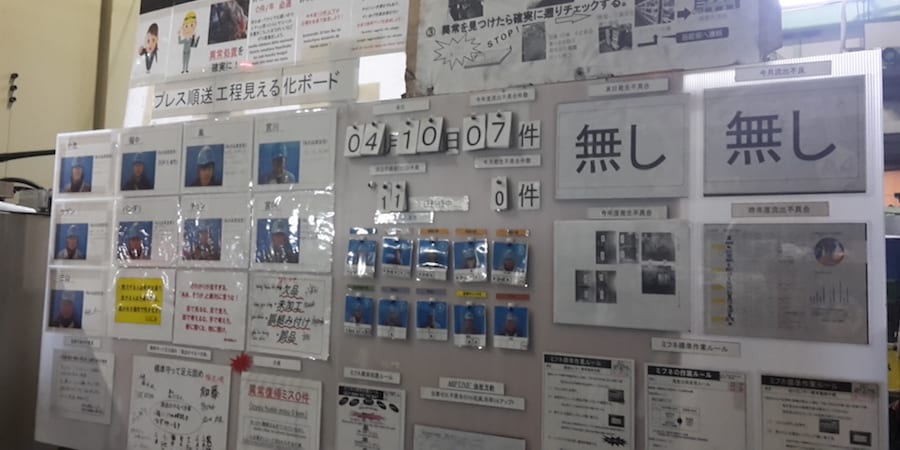
Walking the gemba at a Toyota parts supplier in Japan
NOTES FROM THE GEMBA – This month, the author shares her account of a recent gemba walk at a Tier 2 Toyota supplier, which has achieved impressive results by applying TPS.
Words: Catherine Chabiron, lean coach and member of Institut Lean France
Interpreter at Mifune: Mami Takeda
Presses were stamping parts in one-piece flow, row after row. Each part went through four successive steps, with automated and swift transfers between each press.
I was walking the gemba at Mifune, a Tier 2 supplier of Toyota, together with company chairman Umemura-san. “Every time I hear this thump or I see a flash at welding, I know I am making money. The rest is just muda,” Umemura-san said. A former Toyota Auto Body employee, Mr Umemura founded Mifune in 1978 in the region of Nagoya, not far from Toyota City. Today, the organization employs just over 100 people.
Mifune produces 1,500 different parts for instrument panels, fuel tanks and seats, through stamping and welding. These components are designed by Toyota, while Mifune takes care of the design of all the stamping dies.
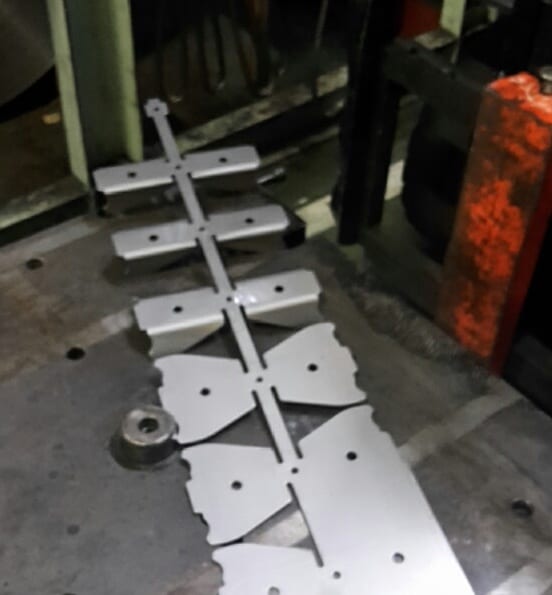
Even though his son is already set to take over, Mr Umemura continues to walk his plant every day, using his very keen eye to spot waste. He normally sees four to five new mudas every day and his challenge, he told me, is “to upgrade the level of supervisors so they can see the same muda”. Needless to say, I saw my visit to Mifune a few months ago as a fantastic opportunity to see real Toyota Production System in action. What a privilege to walk the gemba with someone who has been living and breathing TPS for four decades!
From the beginning of our walk, I noticed how dense the plant is. Circulation is limited to narrow corridors, and I couldn’t see a square inch that wasn’t being used for some value-added activity or minimal stock. “One step represents 0.5 seconds and, because our job is to reduce lead-time, we keep things tight on purpose,” Umemura-san explained. A somewhat brutal, but effective measure.
But the best was yet to come: a changeover of dies, since no press is specific to a part. Talk about flexibility and capex optimization! The next dies had already been prepared on trolleys with roller wheels, which would then move from one press to another on rails.
At the signal, the presses stopped. Dies were unplugged and unclipped (to release hydraulic pressure), moved onto the empty trolleys and replaced with the new dies. Once these were plugged in and clipped, the trolleys moved over to the next press, while a second operator took care of the next two presses. All of this was done in five minutes, not counting the time to check the first part after changeover. Amazing! Repetitive kaizen has allowed the people at Mifune to reduce the changeover time from 30 minutes to 5. Thanks to this very efficient SMED, Mifune can complete 10 to 12 changeovers a day, running on an average customer consumption batch of 90 minutes. Operators essentially focus on the SMED preparation between two changeovers, while the machines continue running their 3,000 parts per hour – a clear application of the principle of separating human and machine.
Like all Toyota suppliers, Mifune runs on strict pulled flows. Toyota and, in turn, its Tier 1 suppliers issue daily e-kanban cards that are printed at Mifune and placed on the Heijunka Board. Mifune receives forecasts for the upcoming two months – they are 80% reliable – and a definitive forecast for the ongoing month. Umemura-san doesn’t want to seek other customers, as Toyota commits to not exceed 30% variability from one day to another and normally enables continuous production at Mifune.
The result of the use of pulled flows is a very low level of inventories (five days of sales). Count your finished goods inventory and compare.
Visual management is everywhere at Mifune. Umemura-san insists on the fact that no computer should be installed within the plant, to prevent supervisors from checking data using reports rather than by going to the gemba. For the same reason, communication between team leaders and supervisors happens by radio rather than smartphone – a one-to-one communication device – in order to foster collective information-sharing and collaboration.
JIDOKA AT PLAY
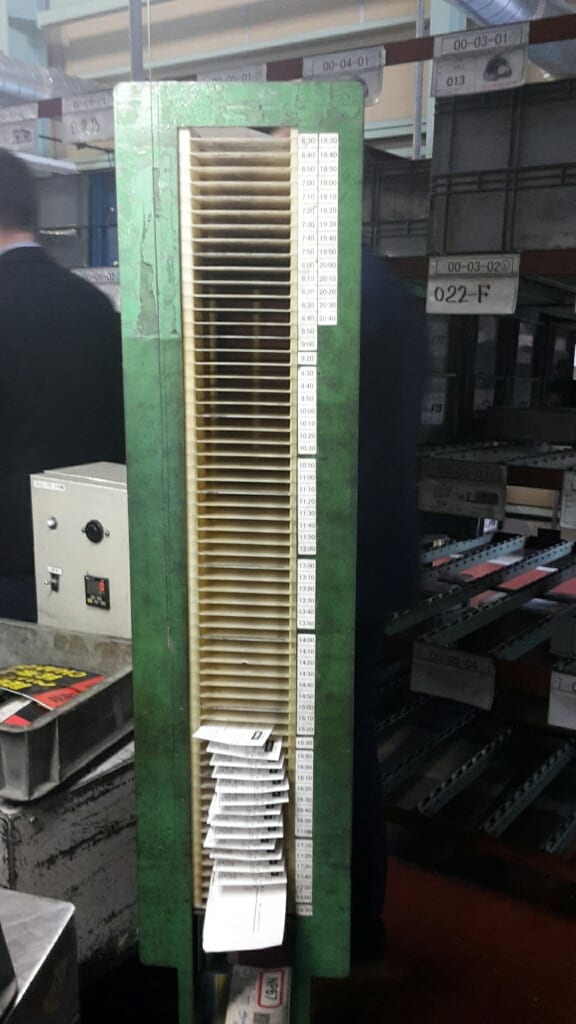
Our gemba walk continued in the welding area. No robots here, just individual workstations where kanban launchers and the parts production board have been replaced by a heijunka board divided in 10-minute intervals. This enables both the operator and the team leader to see whether the kanban cards have been produced on time – a very visual way to track both lead-time and productivity.
Like in stamping, the set-up of the welding area is extremely dense, with limited motions. It was clear that regular 5S at the workstations and on-the-job training had been carried out.
At Mifune, components are brought to the operators (in the past they used to go and collect them, with a 20% productivity improvement achieved when a feeder joined the team). As we walked around, we witnessed a mishappening: an andon lighting up (with a musical jingle playing) after an operator had run out of parts. Jidoka at work.
Jidoka at the plant is not limited to human operations, though. Press automation includes checks like sensing the number of metal sheets fed to the first press, with the machine stopping if two sheets are supplied to the machine instead of one. Automation with a human touch, as Ohno said.
I asked Umemura-san whether jidoka is hard to apply with machines and he confirmed that persistency is required: “At first, the machine stops a lot, but each stop is an opportunity to do kaizen. You can then eliminate one problem after the other. You just have to stick to it until it works.”
As we moved over to shipping, it became obvious that no final inspection takes place after welding. The customer doesn’t do any incoming inspection either, which means it is up to operators and machines to perform their own controls, with the help of poka-yoke. Mifune’s objective is 0 defect passed to the customer: from 98 defects in 2012, they have already managed to get the defect number to 12 as of October 2017. Pretty darn good, considering the plant ships some 8 million units per year. We are talking of 2 defective part per million this year! It’s impressive what 40 years of kaizen, lean thinking and teamwork can achieve.
Mifune sends a truck out every 30 minutes. Eight-thousand kanban cards are checked every day against the shipped production labels, to prevent delivery mistakes. As you would expect, mistakes (if any) are tracked and tacled using the PDCA approach: the team board displays the last three mistakes that occurred, with pictures of the part meant to be shipped and the part actually shipped. Looking at the pictures helps operators and their team leader understand the causes (similar numbers, parts looking alike, and so on) and define the right countermeasures (store them in different areas so as to prevent mix-up, for example).
Checks on labels are done in this rather mysterious, very Japanese way: pointing the finger at the fields being checked while reciting the checked items as a mantra (you can see train attendants in railway stations do the same on their operational checks). Repetition and intent drastically reduce the number of mistakes at Mifune.
You could object that a bit of barcoding and flashing would solve the issue, but barcode labels can be misplaced and Mifune does not believe in excessive capex when human touch can do it.
Umemura-san has his own approach to maintain the level of concentration and focus of his operators at the right level: from time to time, box labels are switched intentionally to trick them. They, however, regularly pass the test.
DEVELOPING SKILLS AND REWARDING IMPROVEMENT
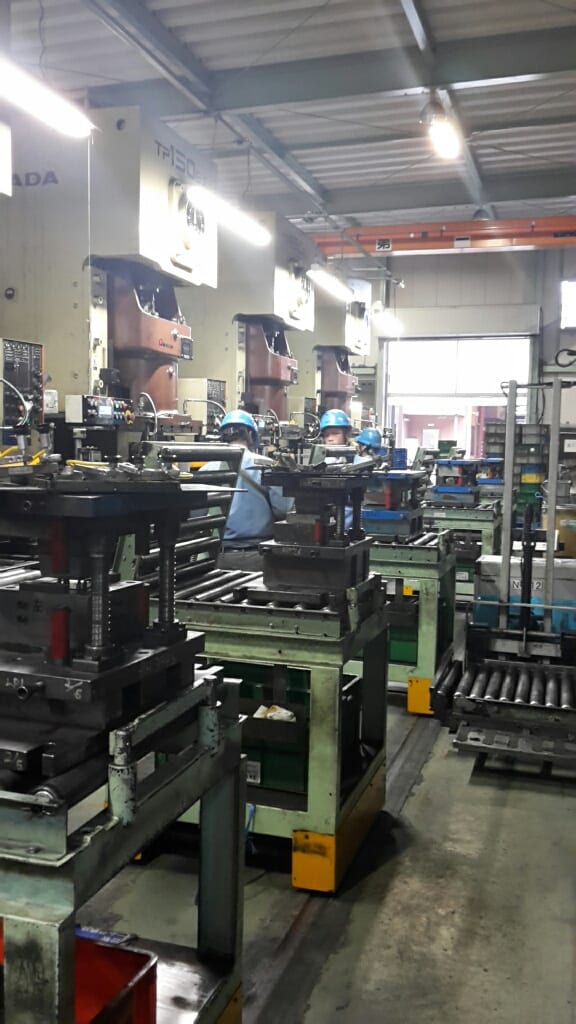
At this stage, you may rightly ask yourself whether this very efficient and extremely “kaizened” environment is not too tough on operators. After all, the thumping of the presses or the flashes of the welding may not sound or look as good to them as they do to Umemura-san. If I add that defect rates are measured not at team level but individually, with the operators’ pictures posted on the wall with the number of days each of them has gone without a defect being passed to the customer, you might be excused for thinking that Mifune is great for machines but hell for humans.
Don’t forget that TPS is just a tool to trigger skills development and lean thinking. To avoid continuous improvement happening from the top down, operators are consistently trained and rotate jobs regularly. (Job rotation schedules and skills matrix confirmed this.) There is more: every new operator is trained for a full month at the workstation before moving on to production, and a thorough control takes place in the following three months to ensure their skills set is solid enough.
Cumulative gains from kaizen or improvement ideas are posted on the wall, re-enforcing the recognition of the team’s efforts. Each employee can also be rewarded between $5 to $1,000 when suggesting improvements for their workstations. Umemura-san also believes that bonus and salary should be linked to creativity. “If you don’t change the way you work over the years, why should your salary change?” he commented during my visit.
At the end point, our conversation moved on to the topic of people development. “Everything is linked to humans, as only they can find and solve problems.” Indeed, the development of employees is critical, and this ongoing challenge teaches them to enjoy change:
- First, through the improvement of individual skills (understand, master the technical ability, learn from seniors).
- Secondly, through creativity and improvement ideas – cultivate the ability to think about the ideal workplace. Operators know operations very well and have ideas on how to improve. Toyota Motor Company is by the way requesting one new idea per month from each employee.
- Finally, through Quality Control Circles, small group activities in the workplace to practice kaizen and eliminate muda by means of PDCA.
One thing that struck me in Japan and that I was grateful to witness was the very common belief that you should “respect” your workplace and keep it clean. Kids are taught early on at school to clean both their classroom and the common areas. White-collar workers clean their desks every evening and are expected to put the chairs back and take garbage out after each meeting. The workplace should be as clean when you leave as it was when you arrived. It’s hard not to see a connection between this commonly shared concept and 5S and, through it, the desire to improve it (kaizen). This means making one’s work easier and more enjoyable, while improving productivity.
KAIZEN TO SURVIVE
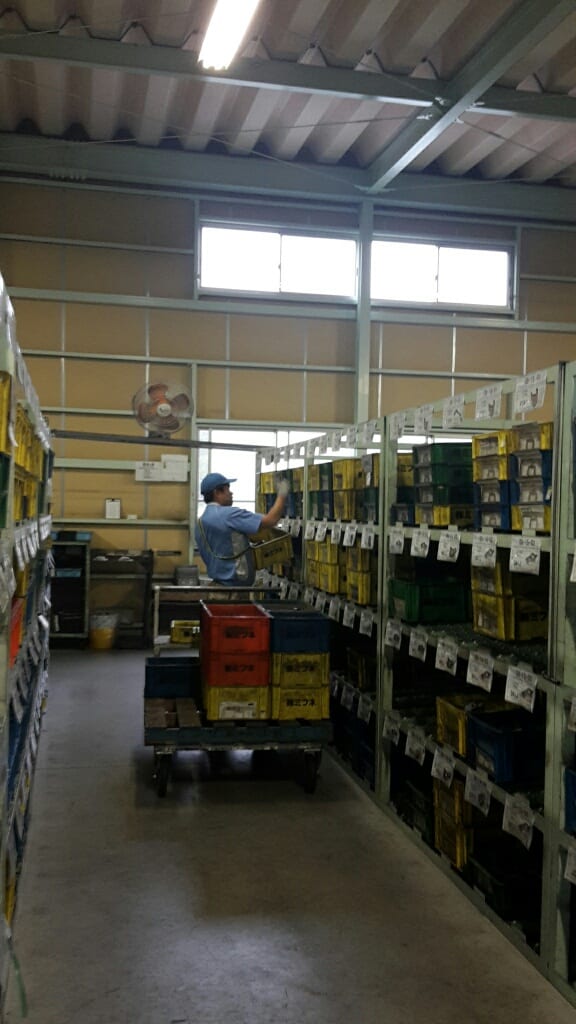
Umemura-san believes in small, every-day kaizen as the way to face up to big challenges and enable the company’s growth. And Mifune has its share of challenges, which are outlined on the giant hoshin kanri board in the middle of plant. Not surprisingly, the company’s focus is on safety, quality and productivity – with progress being checked every four months. Even though sales doubled in 10 years, Mifune had to survive a major economic setback in 2006 in Japan and the impact of Fukushima in 2011 (when Toyota production had to stop). Around that time, Toyota asked their suppliers to reduce sales prices of new products by 30%, which Mifune did (only 5 suppliers remained on Toyota’s panel out of the original 25).
Due to the highly competitive nature of the automotive industry, the plant is also asked to reduce its costs by 1 to 2% per year through engineering and kaizen. By the end of a car model’s life-cycle (5-6 years), a supplier is typically expected to cut 20% of its costs. Only kaizen can achieve this.
But that is not the end of it. This doesn’t appear to be a problem yet (Mifune’s employee turnover is low), but Japan’s aging workforce and its reluctance to open doors to immigration will likely make it difficult for Japanese companies to recruit talent.
Indeed, the future might look a bit scary for automotive suppliers: with the development of electric vehicles, there is no doubt that the number of car components is going to be greatly reduced (with suppliers such as Mifune asked to provide kaizen ideas on design). Surely, this is where the long-lasting bond between Toyota and its Tier 1 and Tier 2 suppliers – characterized by trust, shared values and a long-term vision – pays off.
This article is also available in Hungarian here.
THE AUTHOR
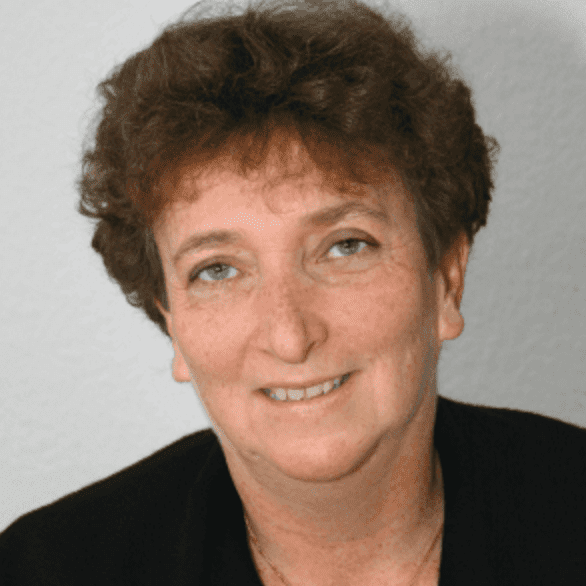
Read more
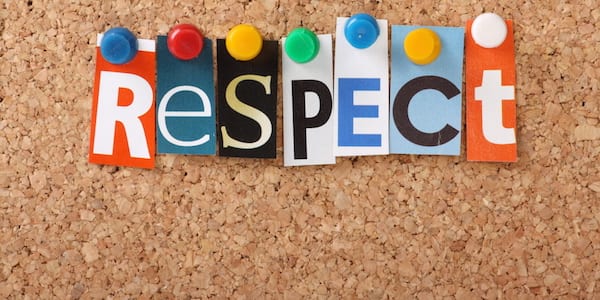
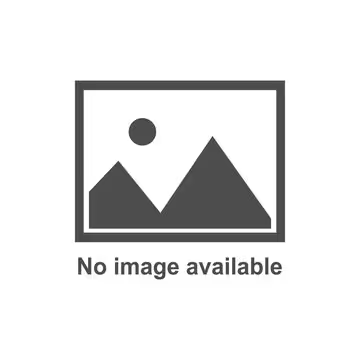
FEATURE - Mission creep, silos and a disengaged workforce are some of the negative effects of traditional management. Michael Ballé offers an alternative based on the respect for people principle of lean thinking.
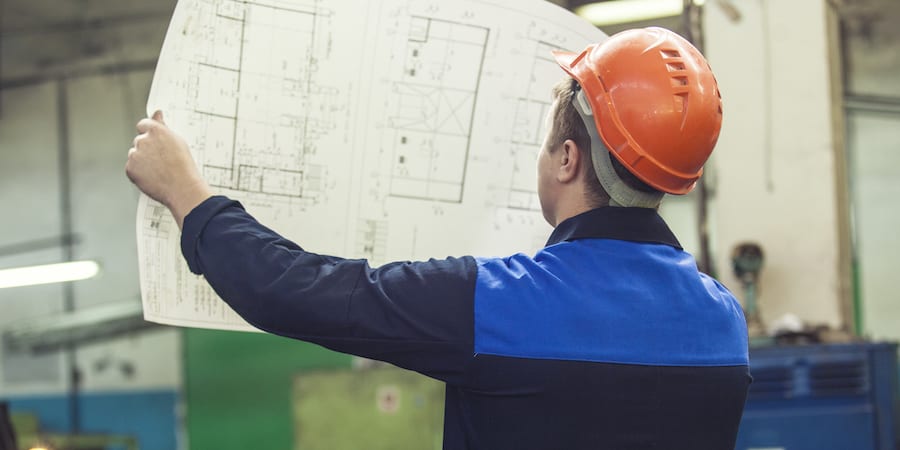
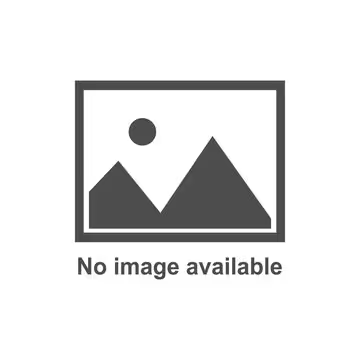
WOMACK'S YOKOTEN - Kaizen or kaikaku? This is the problem. When it comes to the pace of change, should we carry on with small, incremental improvements or aim at more revolutionary changes instead?
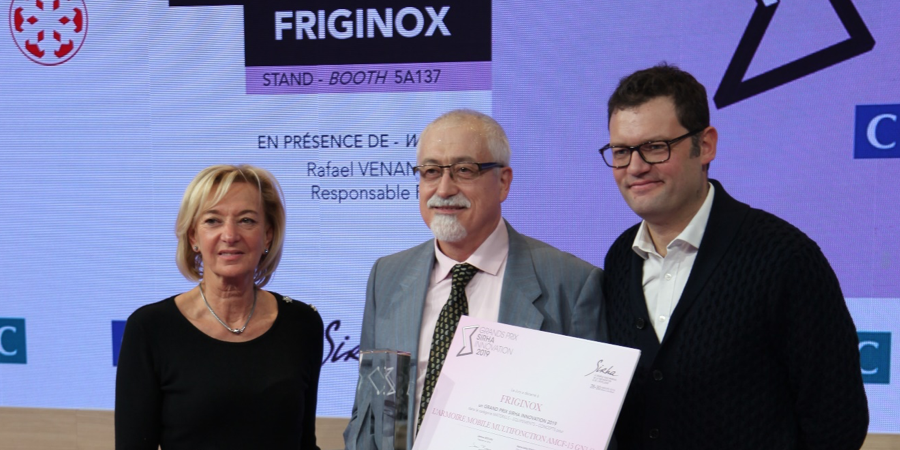
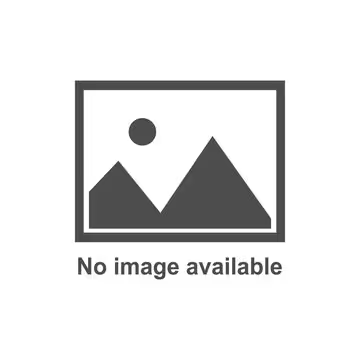
NOTES FROM THE GEMBA – This French company has completely transformed its approach to designing and introducing new products to market by embracing lean product development ideas.
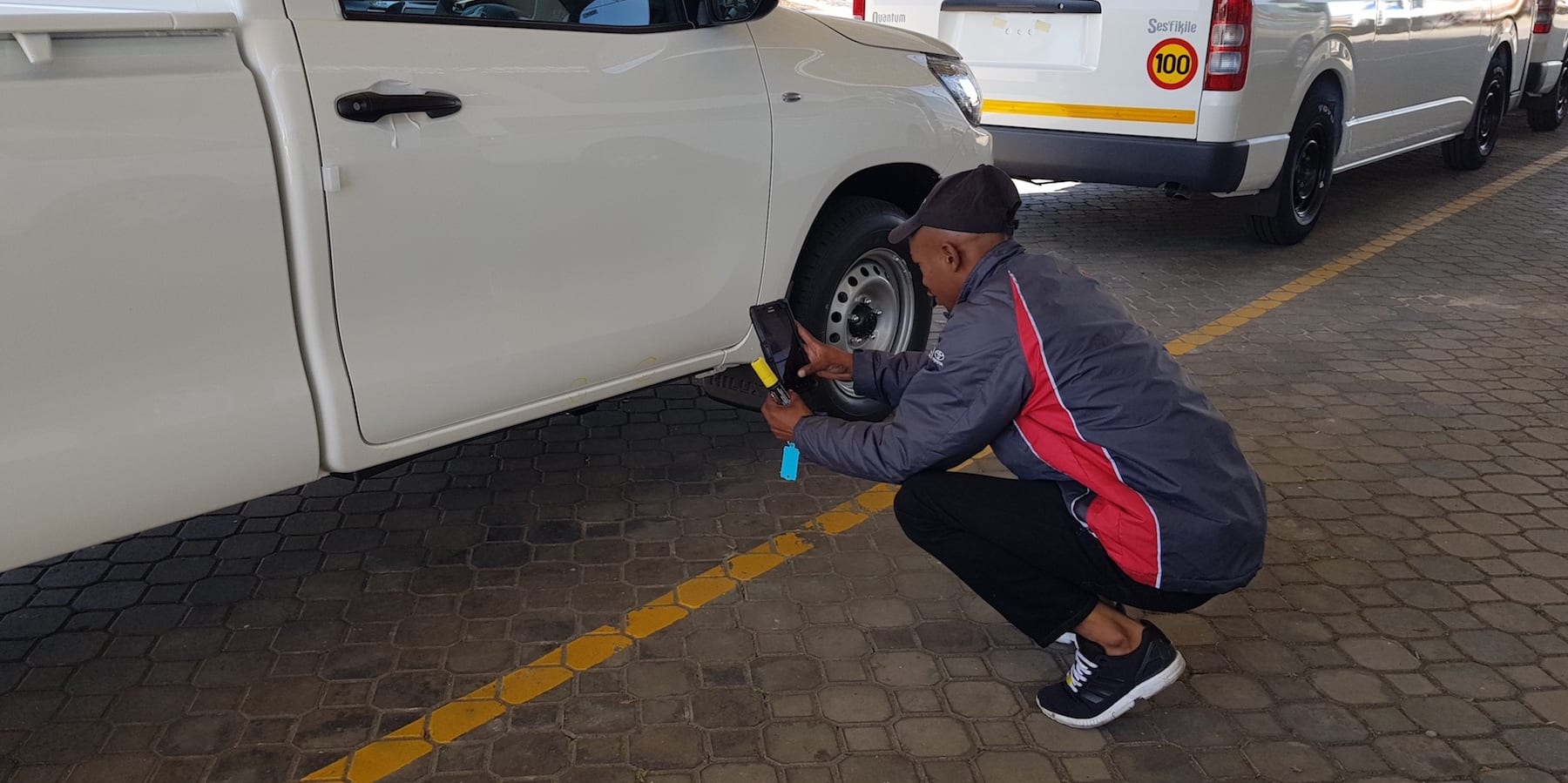
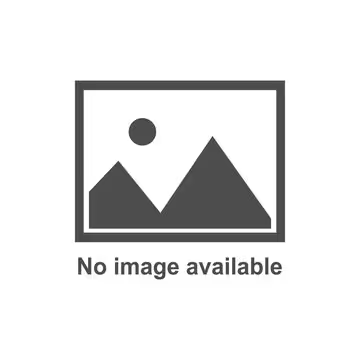
FEATURE – Technology should help people in their work, and it is with this in mind that the general manager of this car preparation center decided to learn to develop Apps.