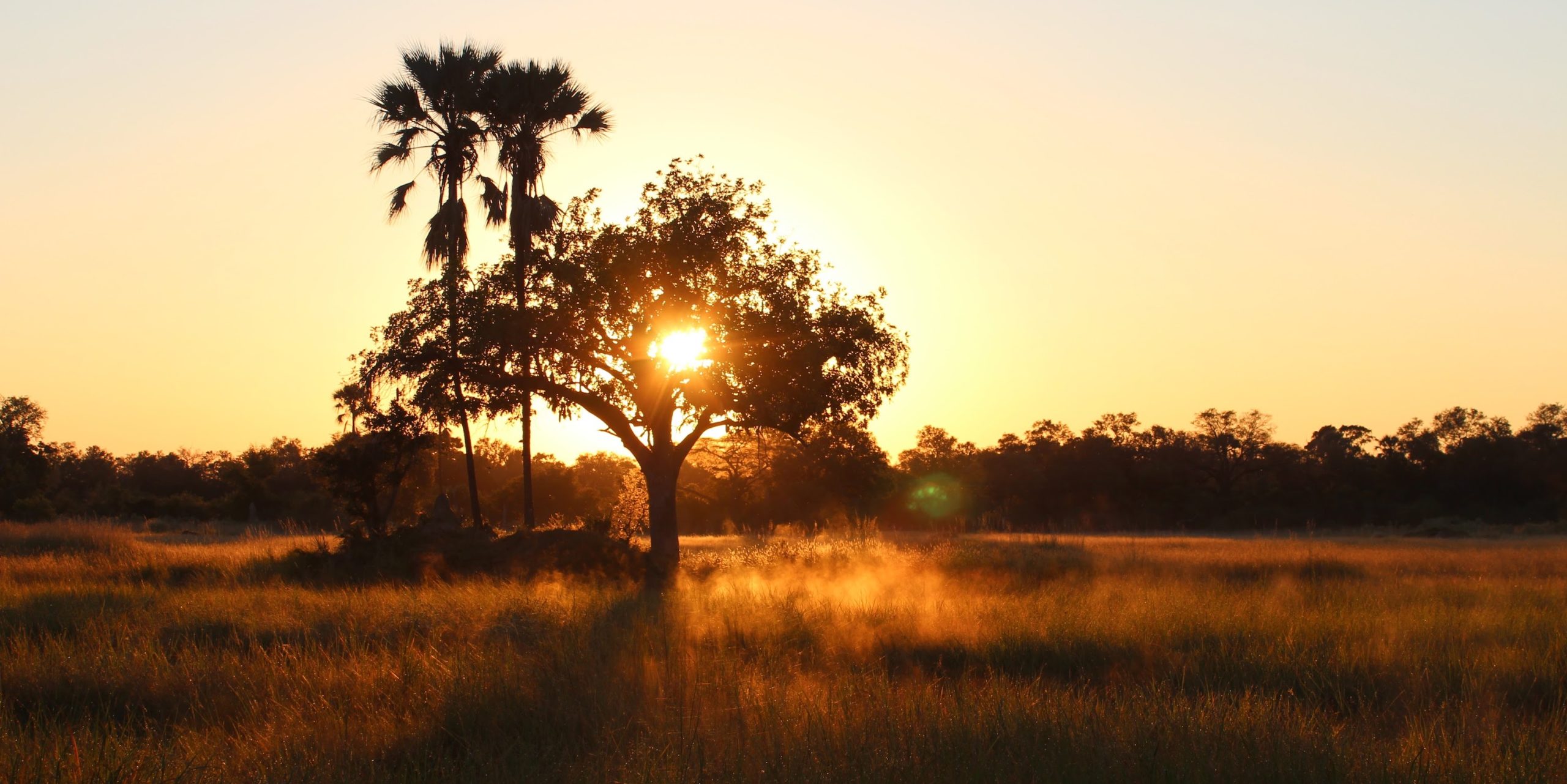
Were we born for a time such as this?
FEATURE – This time of crisis is a perfect opportunity to use Lean Thinking to review processes, improve standards and prepare ourselves for the “reconstruction”, says Sharon Visser.
Words: Sharon Visser, CEO, Lean Academy Botswana
Some of us have found their passion for lean young in life, perhaps in university; others did while working at Toyota or other lean organizations; others still, like myself, were pushed into it by circumstances that were beyond their control.
Whatever your circumstances, this passion has likely blossomed in you after your business successfully made the switch to flow – all lean people have felt this. Now that we are hooked, it’s what pulls is forward, through good times and bad times, and makes us feel the need to share with the world the lessons we learn and the benefits we reap.
But getting there is not easy. Lean transformations are not easy. As a lean coach, I have heard time and time again the same old tune sung, loudly, by the people and organizations I was trying to help: “We don't have time for this”. Every time I hear these words, I wince and remember how I was in the bad old days before lean.
To counter this push back (we typically call it “resistance to change”), we try to convince people to make time for improvement, showing them quick wins and financial gains to persuade them that lean is worth the effort. We coach them on the importance of making sure that the work is visible and that it is easy to recognize normal from abnormal. We teach them about the eight wastes and how to spot them. We get them to experience flow. We coach them about the right way to solve problems using the A3 process so valued at Toyota, so they don't jump to conclusions but find the root cause and the right countermeasures.
As the fear of Covid-19 grips the world, with many of us are forced into lockdown, businesses close their doors, wondering if they will ever open again. Beware the fear that ensues, as it threatens to bring back the “tune of resistance” and frustrate your efforts to transform.
Even though Botswana has so far recorded less than 10 cases of Covid-19, the consequences of the pandemic are already evident here. Our country has dealt with pandemics before – in 2018, the prevalence of HIV among adults aged 15 to 49 was over 20% – but the threat posed by Covid-19 is completely different. It has overwhelmed decision makers and the problem-solving response has been erratic (and, I might add, in desperate need of A3 assistance).
The tourism industry is in serious difficulties and it is estimated it will take around 12 months for it to recover once the emergency is over. There is no doubt that our region – Ngamiland – will not survive this blow easily (it relies heavily on tourists coming to visit the Okavango Delta) and we can only hope that the high-end market will still have funds and want to travel to Africa.
With the lockdown and the prospect of no visitors coming to Maun for safaris in the Delta, many of the companies I am supporting are currently closed. They are trying to get to grips with the situation and simply trying to make it through each day.
When this is all over (it will pass as all things pass), getting back to normal business life will be hard and might take some time. Skilled staff who no longer have jobs will have moved elsewhere, to take on positions that were still available. Some employees will have lost the ability to be loyal and trusting as the companies they served rushed to lay them off, and they will not return to work for them. New staff will need training and returning staff will need to get back into the rhythm of the work. Sadly, some employees will no longer be with us.
To get ahead of this as a lean community, we need to encourage our community to fight their fears and use the time they now have abundantly available to document and improve their standard work. Now is the time to move the equipment around to improve flow, to bring in your most experienced people to look at the work and develop the processes for when things go back to normal.
Delta Meat Deli, which provides food for the camps in the Delta and is therefore severely impacted by this crisis, is doing just that – proactively reviewing its processes in a bid to soften the blow. They are currently busy moving their shop into their factory to save on rent and are looking at becoming more of a manufacturer of specialist items (like cold meats, frozen pastries, frozen meals, pita bread, etc). They are also pushing their online presence and delivery capabilities over this period.
South Africa-based Super Trade group, which I am also supporting, took my advice very seriously and is with total dedication working through their standard work. They are doing this throughout the crisis and have awed me with their focus. I am not allowed to travel over the border, so I can't go to see them, but I am getting a lot of heartwarming photos on WhatsApp.
When Covid-19 is an event of the past, it is organizations like these that will have the upper hand: they will be ready, with all the tools they need, to get up and operational and meet deadlines (that will surely be brutal as the world economy starts to demand products and services again). They will be able to rely on the good standard work and strong processes and visuals they have developed during this forced hiatus to fill the skill gaps and maintain quality in the workplace.
This is the time to develop our passion for Lean Thinking and this is how we can help the world right now: bringing people the hope of better days by helping them prepare for what comes next. They say that lean works best in a time of crisis and so I say to you: we were born for a time like this!
THE AUTHOR
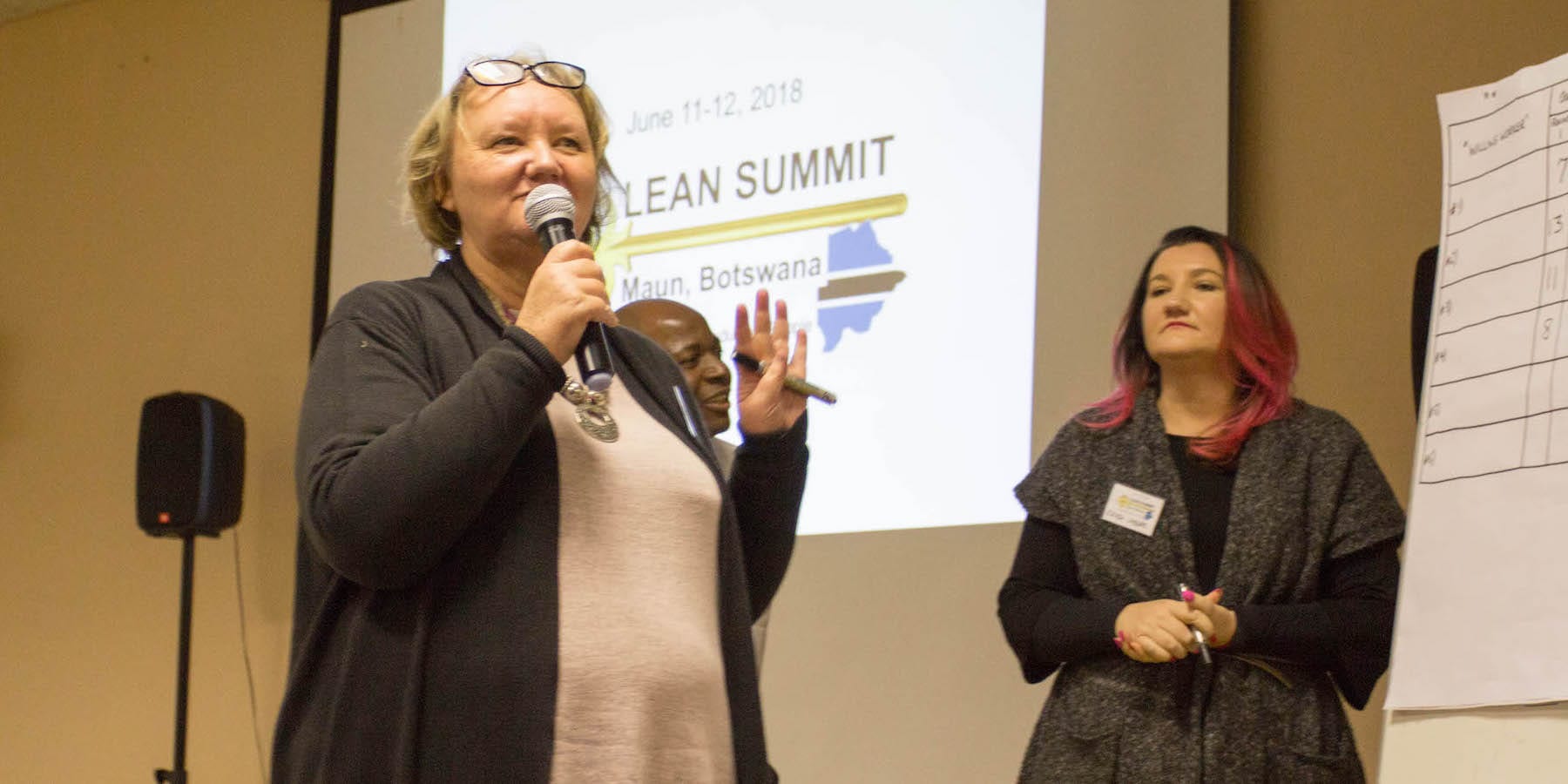
Read more
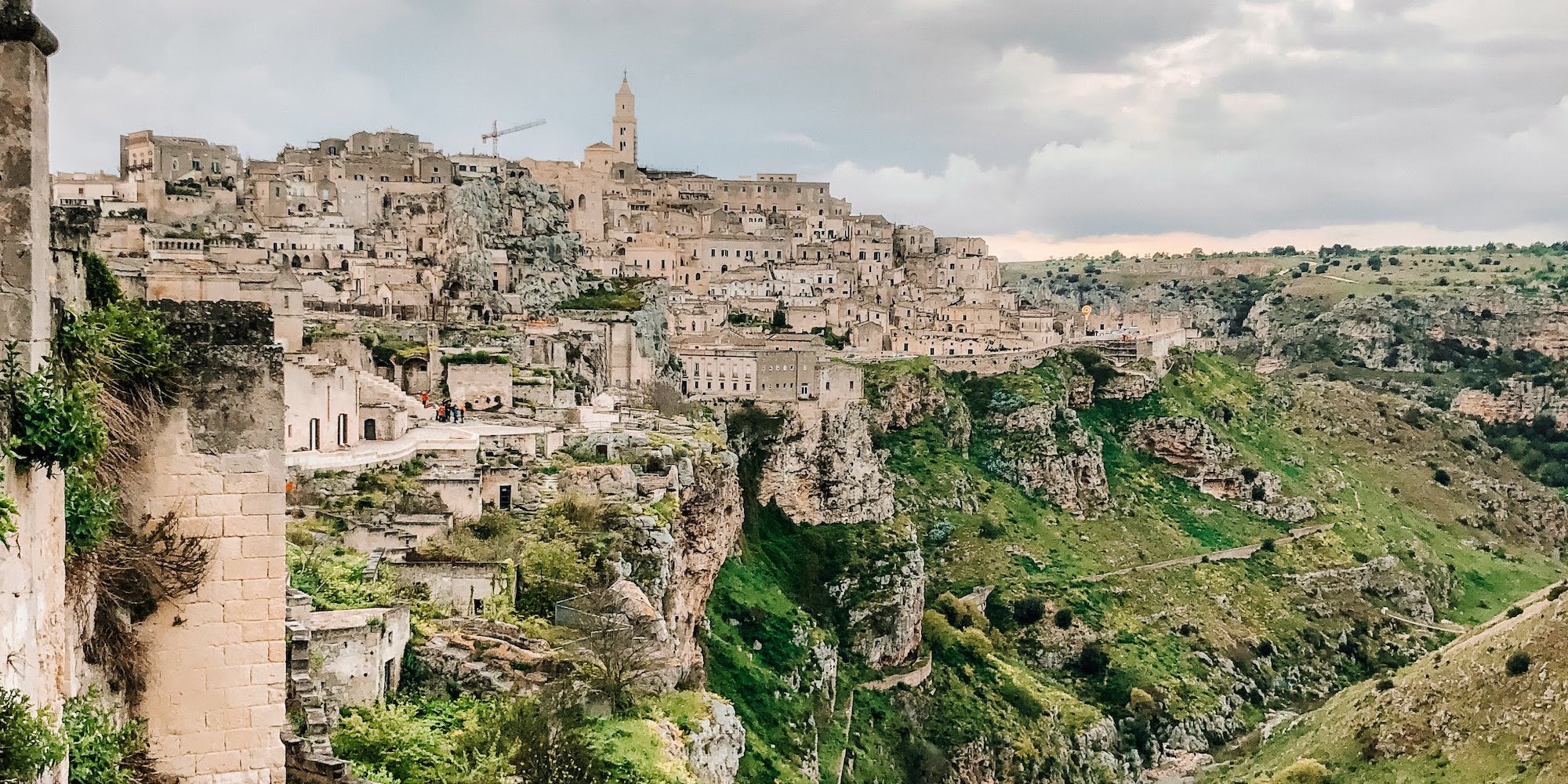
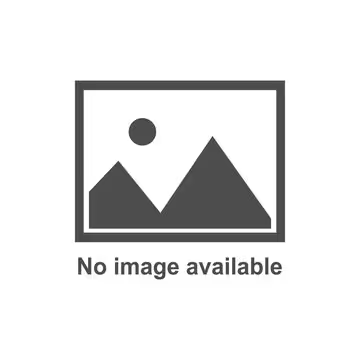
FEATURE – Using lean marketing principles, an entrepreneur in southern Italy was able to pivot from a potentially bad investment and create a unique customer experience instead.
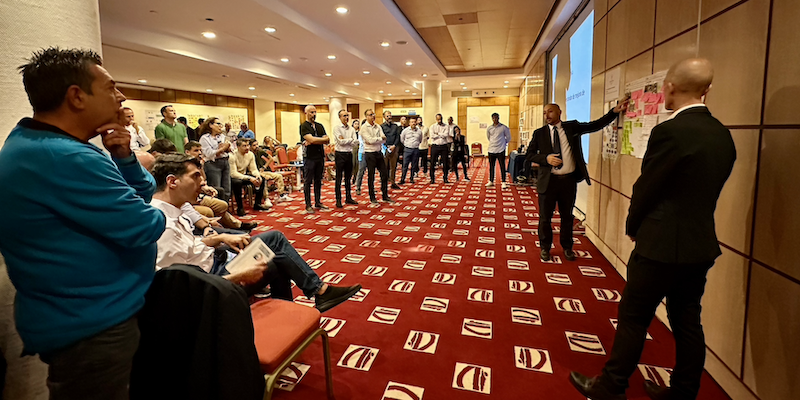
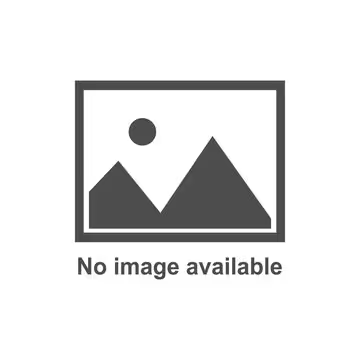
FEATURE – Our editor attends a Lean Day at Dreamplace Hotels & Resorts in Tenerife. In this report, he shares his thoughts about team building, following up on improvements, and yokoten.
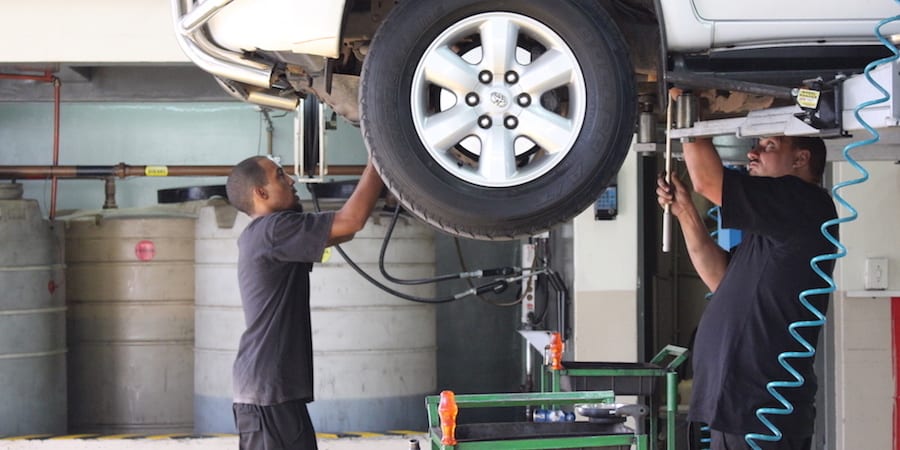
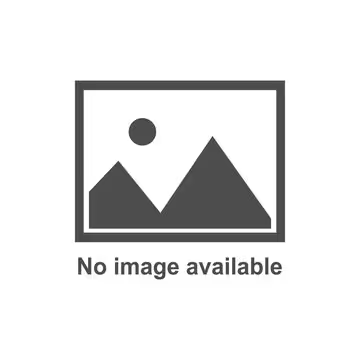
DOCUMENTARY – In PL’s first ever documentary, we share the story of a chain of car dealerships in Africa. Watch and learn how people development and lean leadership made for one of the best turnarounds you’ll ever encounter.
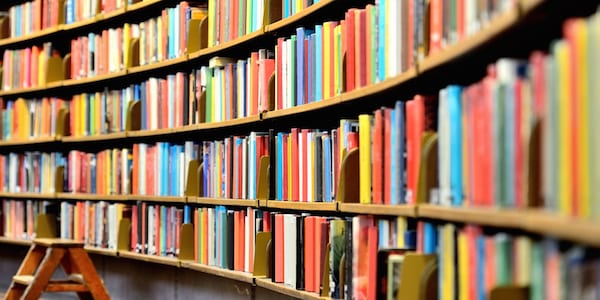
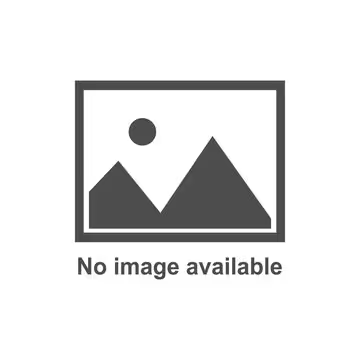
INTERVIEW - Are you a manager who needs to brush up on lean but has little time to do it? A new book by Cécile Roche comes to the rescue: A Little Lean Guide for the Use of Managers.