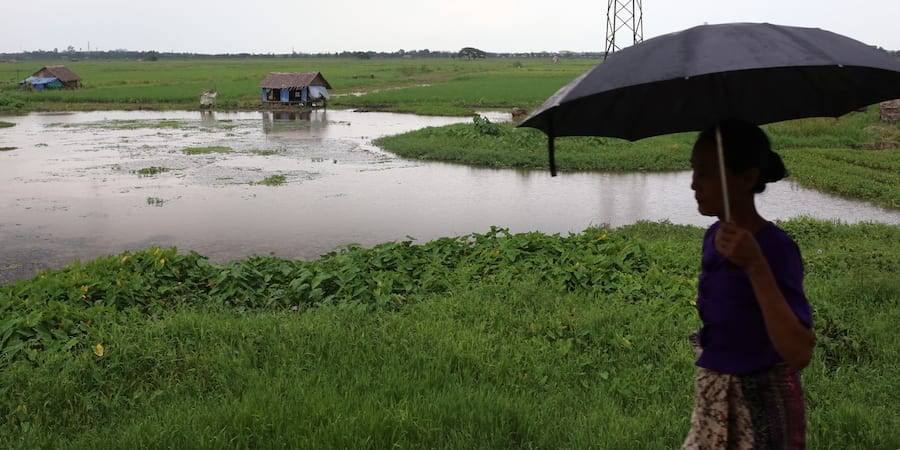
Lean project boosts sustainable development in Myanmar
FEATURE – A group of Italian researchers and professionals partnered with a NGO to prove how lean thinking can pave the way for the competitiveness and sustainable development of SMEs in Myanmar. Is this a new model for the developing world?
Words: Monica Rossi, Postdoctoral Associate on Lean Product Development, and Rossella Luglietti, Environmental Engineer, Politecnico di Milano; Giulia Donnici, former Corporate Social Responsibility Advisor, and Moung Kee Aung, Business Matchmaking Manager, Building Markets
In November 2015, Aung San Suu Kyi's National League for Democracy won a landslide victory in Myanmar. It was the country's first national vote since a nominally civilian government took over in 2011, ending nearly 50 years of military rule. The stunning Shwedagon Pagoda became a familiar image for many people all over the world who, before this historical event, hardly knew of the existence of Myanmar, a land located "where China meets India," – as the historian Thant Myint-U said – and used as the setting of memorable books and poems by Orwell and Kipling.

Myanmar's latest Human Development Index (HDI) value is 0.536, positioning "the Golden Land" at 148 out of 188 countries and territories – among the so-called Least Developed Countries (LDCs). However, despite its low HDI, Myanmar is also the world's fastest-growing economy, according to the International Monetary Fund, and its GDP is projected to grow by 8.6% this year.
In such a scenario, we see a huge opportunity arise for Myanmar and other LCDs: that to mold their growth in a sustainable way. In our so-called Most Developed Countries, many organizations are scrambling to re-design their business models and structures to take in concepts such as Life Cycle Thinking and Circular Economy, so wouldn't it be great (and easier) if LDCs – where the local industrial environment has yet to be shaped – managed to design and implement these approaches "right first time"?
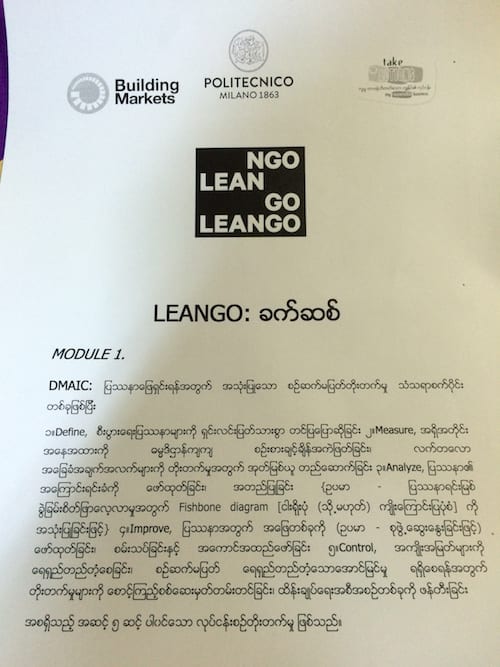
Since 2012, Myanmar has been observing a boom in the number of small- and medium-sized enterprises, as well as the appearance (or, rather, re-appearance) of international corporations. Because of international laws and standards on corruption, labour, human rights, and the environment, which are increasingly being absorbed by national legislations, and the voluntary and compulsory activities on Corporate Social Responsibility (CSR) or sustainability, multinational companies need to work with reliable local suppliers that can enforce at least minimum social and environmental standards.
There is an increasing interest on sustainable development in many LDCs, including Myanmar, and plenty of international NGOs and organizations working in this field. Nevertheless, the focus of many projects is often to improve the social and environmental performance of SMEs – which still tend to confuse CSR with charity – while their first short-term interest is to be as competitive and competent as possible.
LEANGO, or lean for sustainable development, was designed to overcome this dichotomy.
THE LEANGO PROGRAM
Create value and eliminate waste, respect and develop people, build on knowledge and learning, continuous improvement: these are some of the principles that have made lean thinking so successful in so many fields. They are also the concepts we had in mind when we launched LEANGO at Politecnico di Milano – a leading technical university in Italy – together with Building Markets, an NGO operating in Myanmar and many other developing countries.
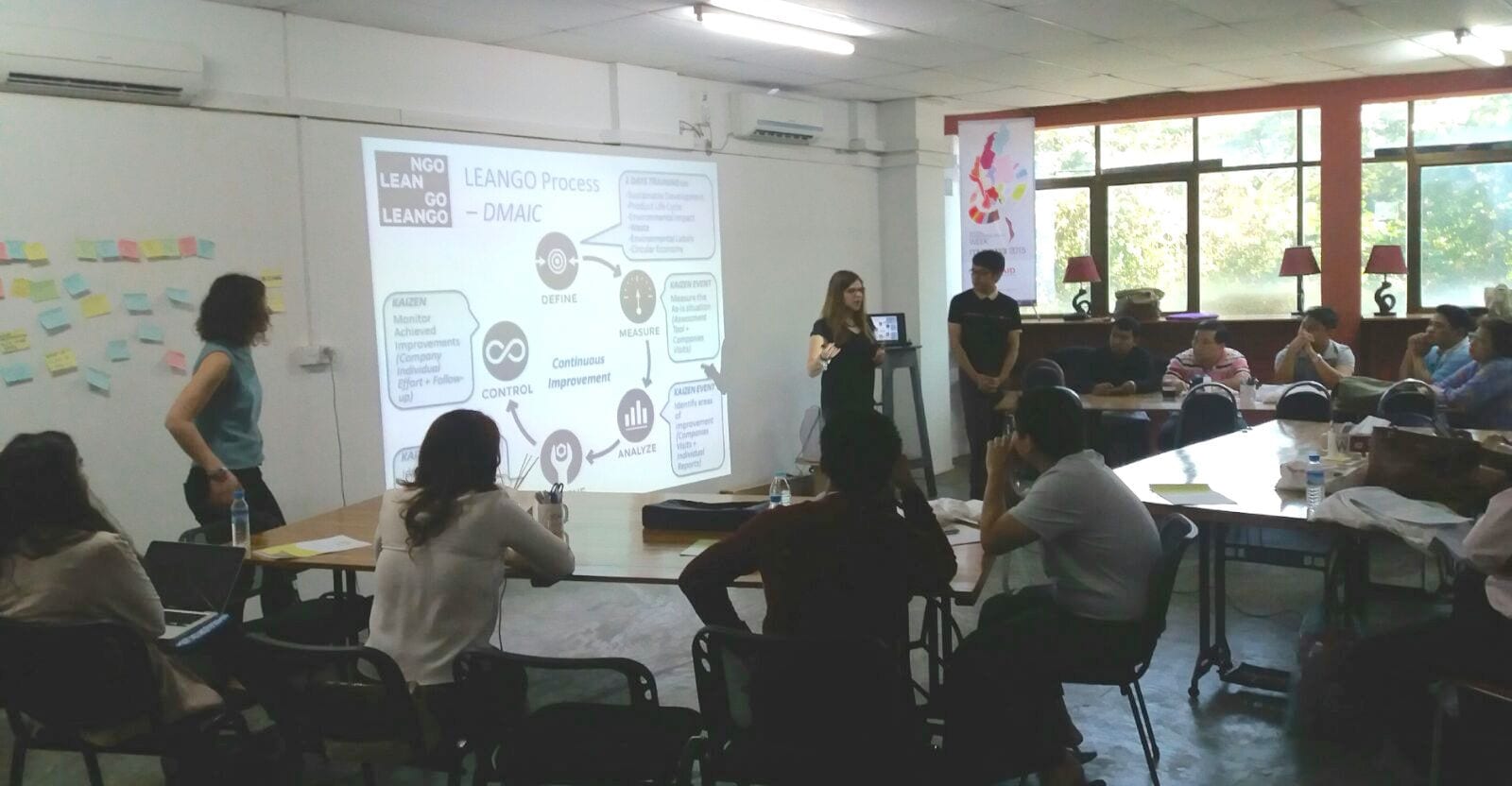
Last January we brought to Yangon – Myanmar's largest city – 18 SMEs from a number of cities and industrial sectors (including aluminum, textile, paper, carton and plastic) for a one-week training program designed to support companies on the upcoming challenge of sustainable development. We organized face-to-face lessons and hands-on activities to inform and create awareness – around product life cycle, sustainability, waste, environmental impact, circular economy, international labels – with the support of ad-hoc slides, facilitated discussions to foster learning and the exchange of best practices, and serious game on product life cycle. ("What's the impact on the environment of your daily cup of coffee?") We also had gemba walks and kaizen events – for which seven participants opened the doors of their companies to the entire LEANGO group – to allow everybody to go and see, propose and discuss improvement actions, and learn together.
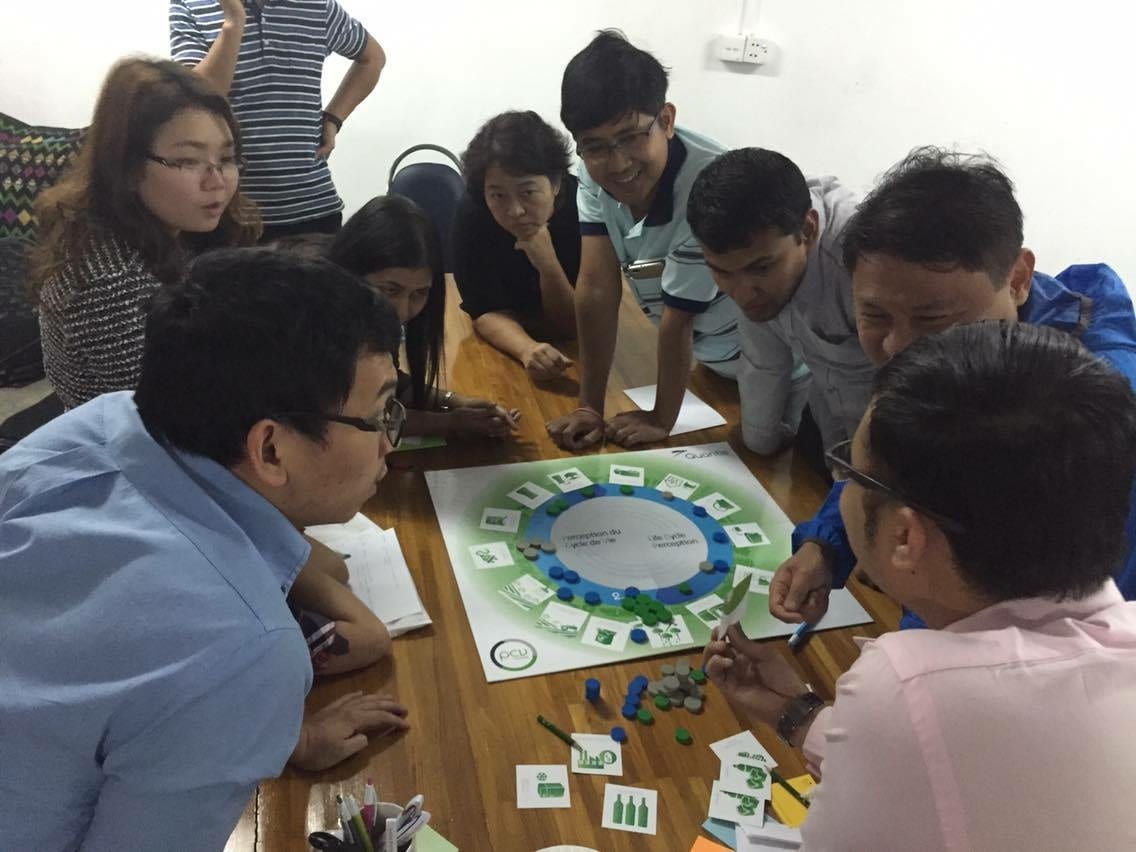
LEANGO's mission is to promote the elimination of waste, the improvement of quality, and the delivery of value to customers while achieving environmental performance goals following a continuous improvement logic. We developed four basic questions we ask the companies we work with, which are based on a simple but effective framework that relates value creation with resource saving:
- What is the purpose of my company (what is my value proposition)?
- Which wastes impact my process more (keeping me away from delivering value)?
- How can I improve my process (thus delivering more value)?
- Which resources will I be able to save (while delivering more value)?
LESS PROCESS WASTE, MORE QUALITY AND MORE... ECO-FRIENDLY!
At LEANGO we make the link between process, energy, and environmental waste explicit.
Let us share a couple of definitions before we continue:
- Energy inefficiencies occur when energy has not been used to produce a useful good. The activities where energy inefficiency are typically discovered are tied to the well-known lean wastes of over-production, inventory, transportation, motion, defects, over-processing, and waiting.
- Environmental waste is the unnecessary or excess use of resources or a substance released in the air, water, or land that could harm human health or the environment.
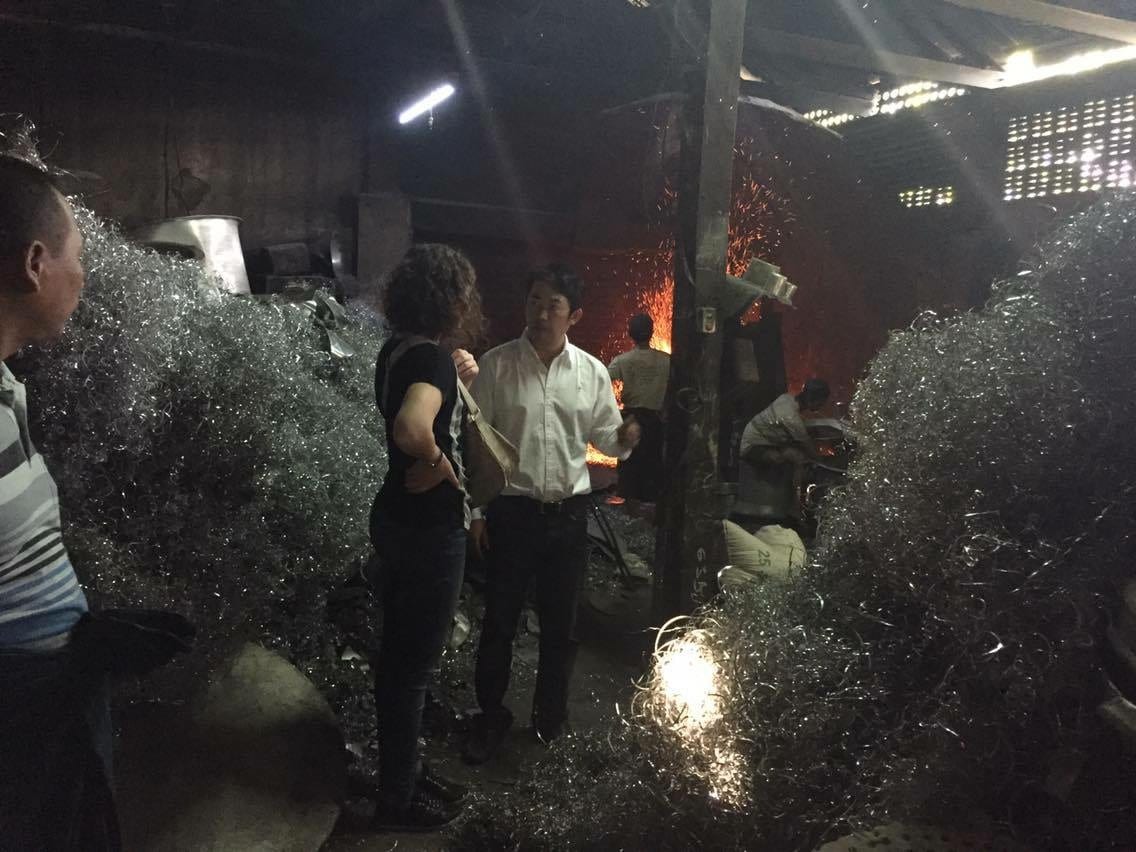
These forms of waste are all too common in companies across the world, and Myanmar is no exception. Due to their low contractual power – and in order to satisfy (every) customer request in a very short time – the country's SMEs generally over produce and store this stock of products in their facilities, with the risk that the customer might change his mind and finally modify the order, or not place it at all, without incurring any penalties. Such over production – besides representing inventory waste – determines an excessive consumption of raw materials and of energy to keep operating equipment running; the production of extra items that could become obsolete and require disposal; as well as the generation of extra emissions.
Brainstormed solutions with the LEANGO participants – who broadly complained about this type of waste in their organizations – included the introduction of a fragmented production plan to reduce the amount of pre-manufactured goods, together with a disjointed delivery schedule to drastically reduce inventory (and hence overproduction).
Indeed, small but very impactful changes can be made to reduce over engineering. For example, the owner of a juice company decided to redesign the labels reducing the number of colors, to lower the cost and the environmental impact of the labels while appealing more to customers.
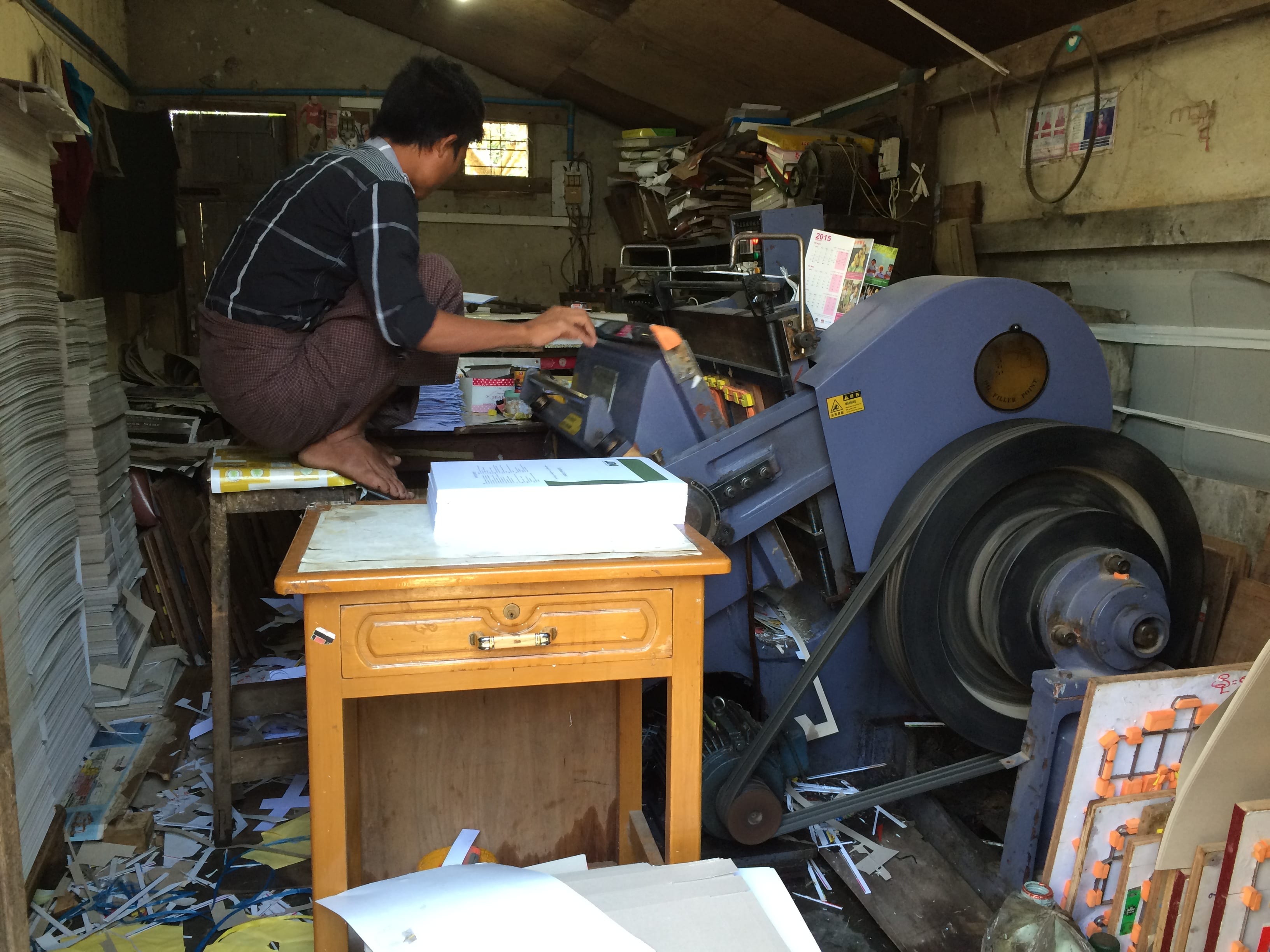
In manufacturing operations, which are heavily dependent on human labor – given the low cost of manpower in Myanmar – investing in new machines is seldom considered an option. But during the LEANGO training, we stressed the doing more with less "mantra" of lean thinking, which resulted in a plastic components producer opening a new factory in Mawlamyine. The owner said: "This is because in our factory in Yangon we started monitoring – and reducing – both labor working time and product wastes by acquiring new machines. This allowed us to save time and resources while producing products of a higher quality. The saved resources were invested in the new factory in Mawlamyine."
We saw the awareness on the impact that process wastes have on the environment grow in the minds of the participants to the LEANGO training session. "From now on, I'll always consider the environmental aspects of my production processes," said one. "The eight types of wastes are always on my mind and whatever I do in my business, I always strive to tackle them," said another. And there is more. We also noticed an increased attention to the final customer and quality delivered to them.
The program's strong emphasis on learning, knowledge sharing and people engagement in continuous improvement initiatives promoted by lean thinking proved extremely successful.
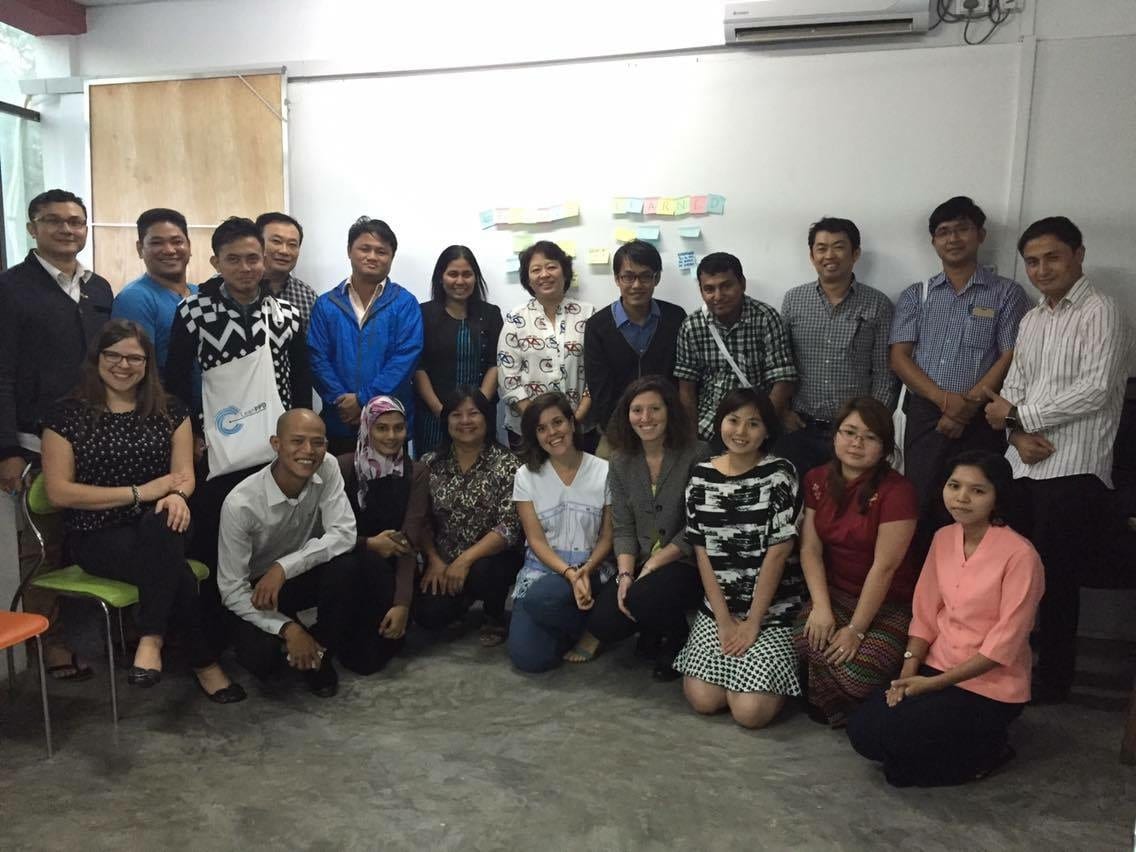
LET'S GO! LEANGO!
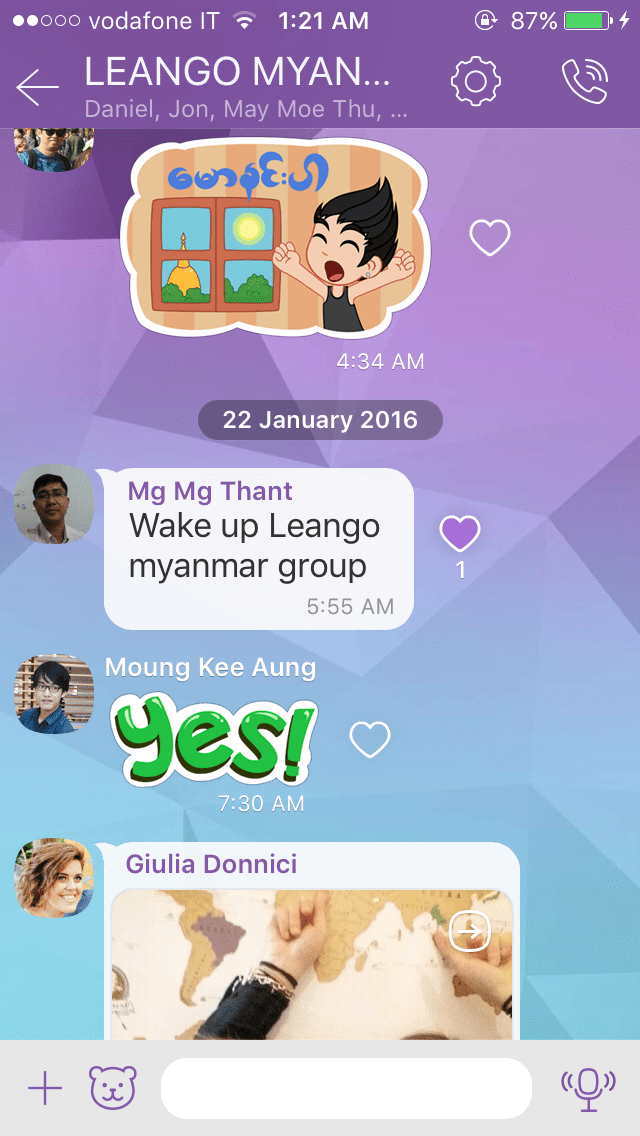
The LEANGO initiative did not end after the weekly program in January. Politecnico di Milano and Building Markets ensure continuous follow-up using both traditional and more modern tools (from face-to-face meetings and regular visits to video interviews and group chats). We constantly share articles and research on lean and sustainability, inform each other about interesting events in Yangon where the participants can possibly meet, and even ask each other questions on our businesses.
Reflecting back on the past nine months, we believe that the elements that contributed to the success of this initiative are:
- The extraordinarily cooperative, open and friendly attitude of the participants;
- The great motivation and unstoppable desire to learn, grow and innovate;
- The strong emphasis on learning;
- A relentless search for business opportunities;
- The courage to share with and benchmark against other companies – even Western ones.
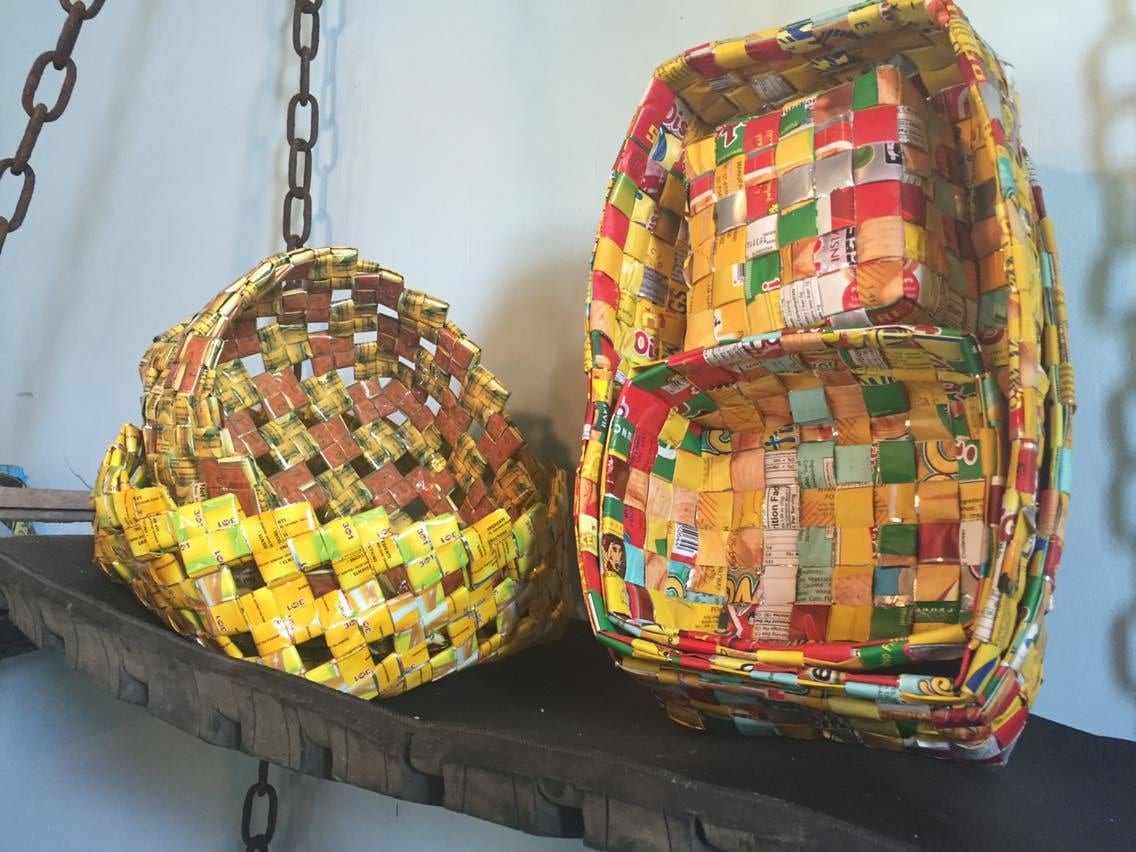
One of the most rewarding things about our work in the Golden Land is seeing that nine months after we started participants are still actively engaged and deeply involved in what is now known as the LEANGO Myanmar Community.
It's also been great to see important collaborations being established between the participants in order to build highly interconnected product life cycles. Within the LEANGO Myanmar Community, participating firms were often able to find direct customers and/or suppliers of assets, components/products, packaging, or even scrap. A great example comes from a company that produces and sells plastic products entirely made of recycled materials in Dala Township: it found in one of the LEANGO participants a source of raw materials that were otherwise going to be scrapped and somehow dispersed in the environment. The quick availability of input material to be recycled and reused to make final products, which encourages a circular economy attitude, is another tangible result achieved by our program.
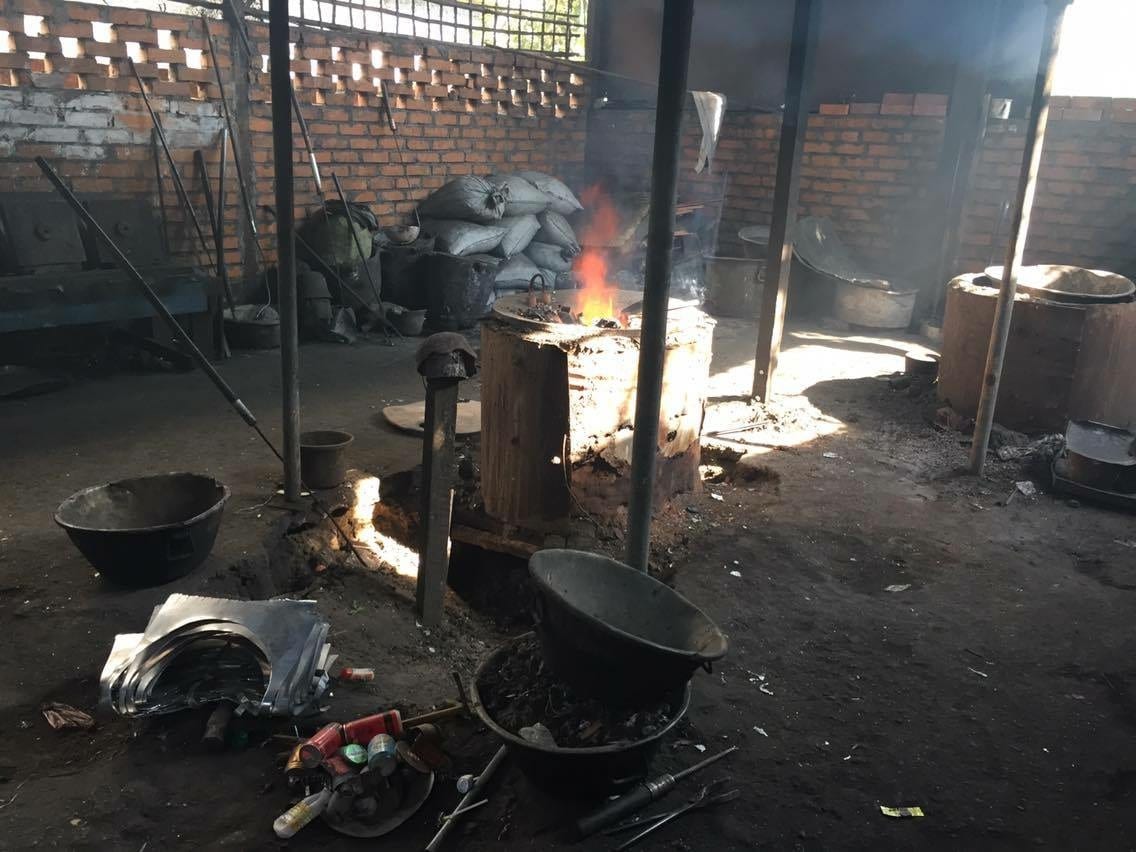
Companies were also able to share assets and acquire resources – usually too expensive to get otherwise. This is the case of two aluminum pans and covers producers, which are currently evaluating a joint investment on a furnace, in order to improve product quality, process efficiency and environmental impact of the aluminum-melting phase. Indeed, not only does this way of investing in machinery increase process efficiency and product quality – which obviously have a direct impact on a company's finances – but it also creates an eco-friendly image of the company, which can be leveraged to make sustainability the core of the strategy and a competitive differentiator both in the local market and abroad.
Our experience in Myanmar shows that developing countries have a unique opportunity to avoid the linear economy inefficiencies that are affecting Western organizations so badly and to strive for a more sustainable circular economy from the outset. LEANGO proved effective in promoting sustainable development and efficient growth through the basic, yet very practical lean principles of value creation, waste elimination, people development, learning and continuous improvement. Following this first very experiment, we at LEANGO are ready to try and replicate this success in other developing countries that, like Myanmar, are interested in developing in a smarter way.
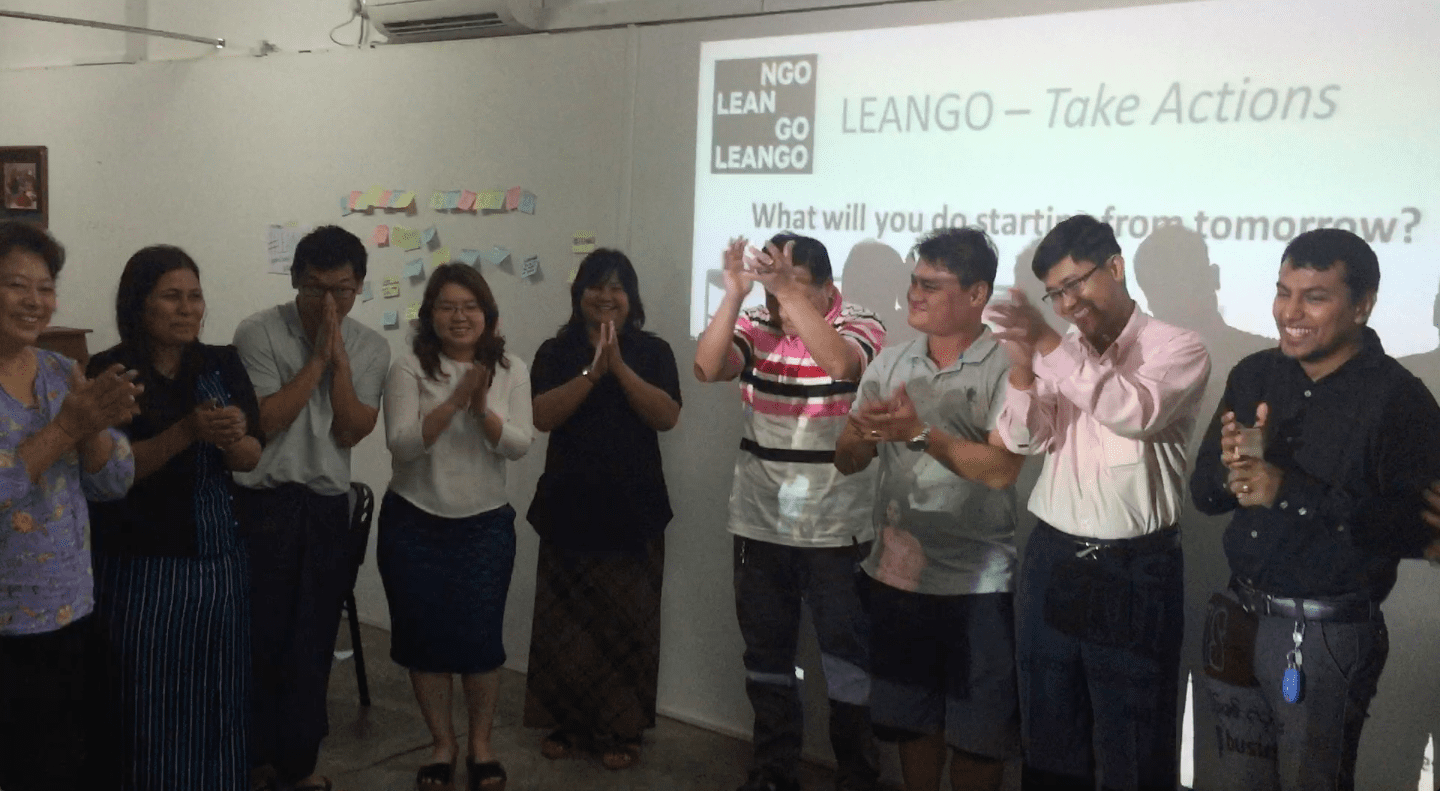
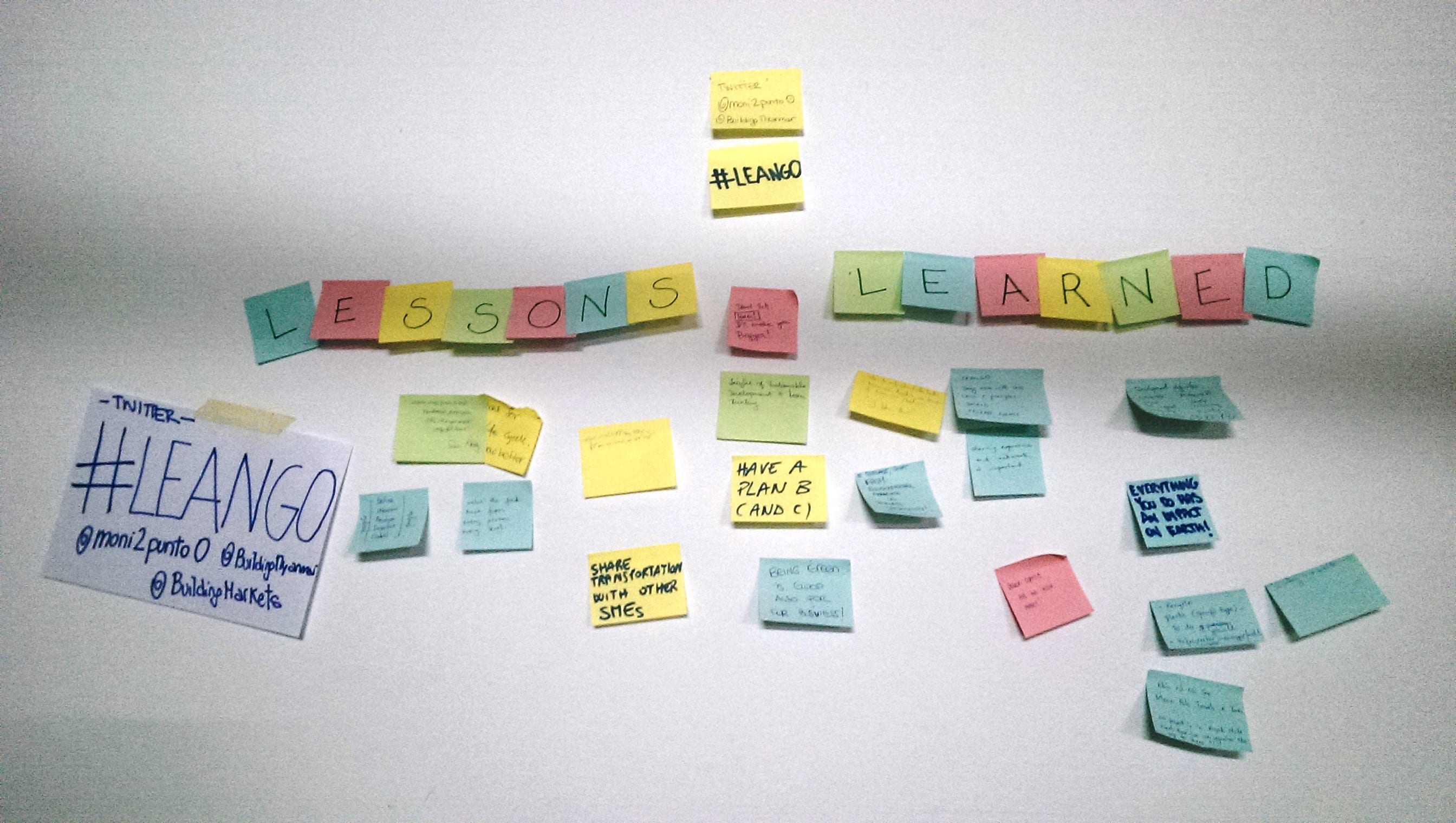
THE AUTHORS
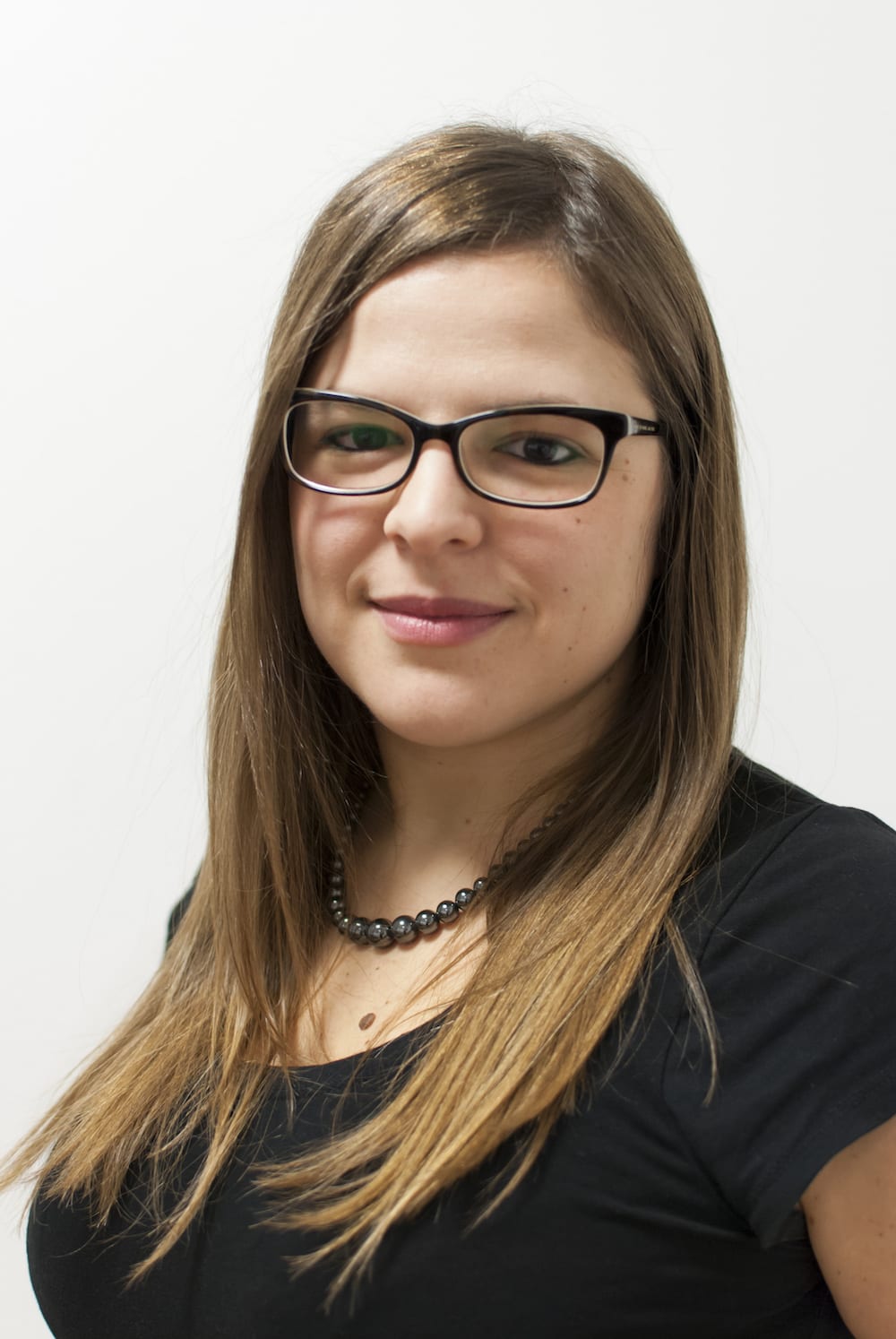
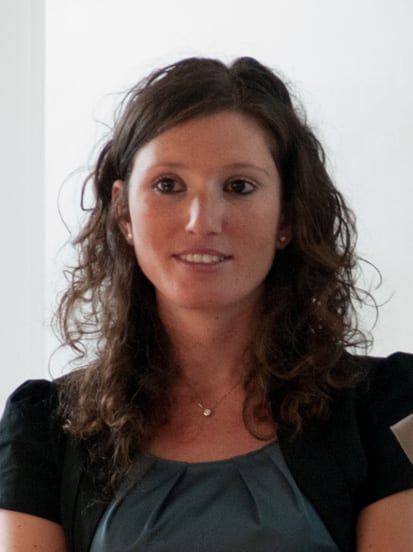
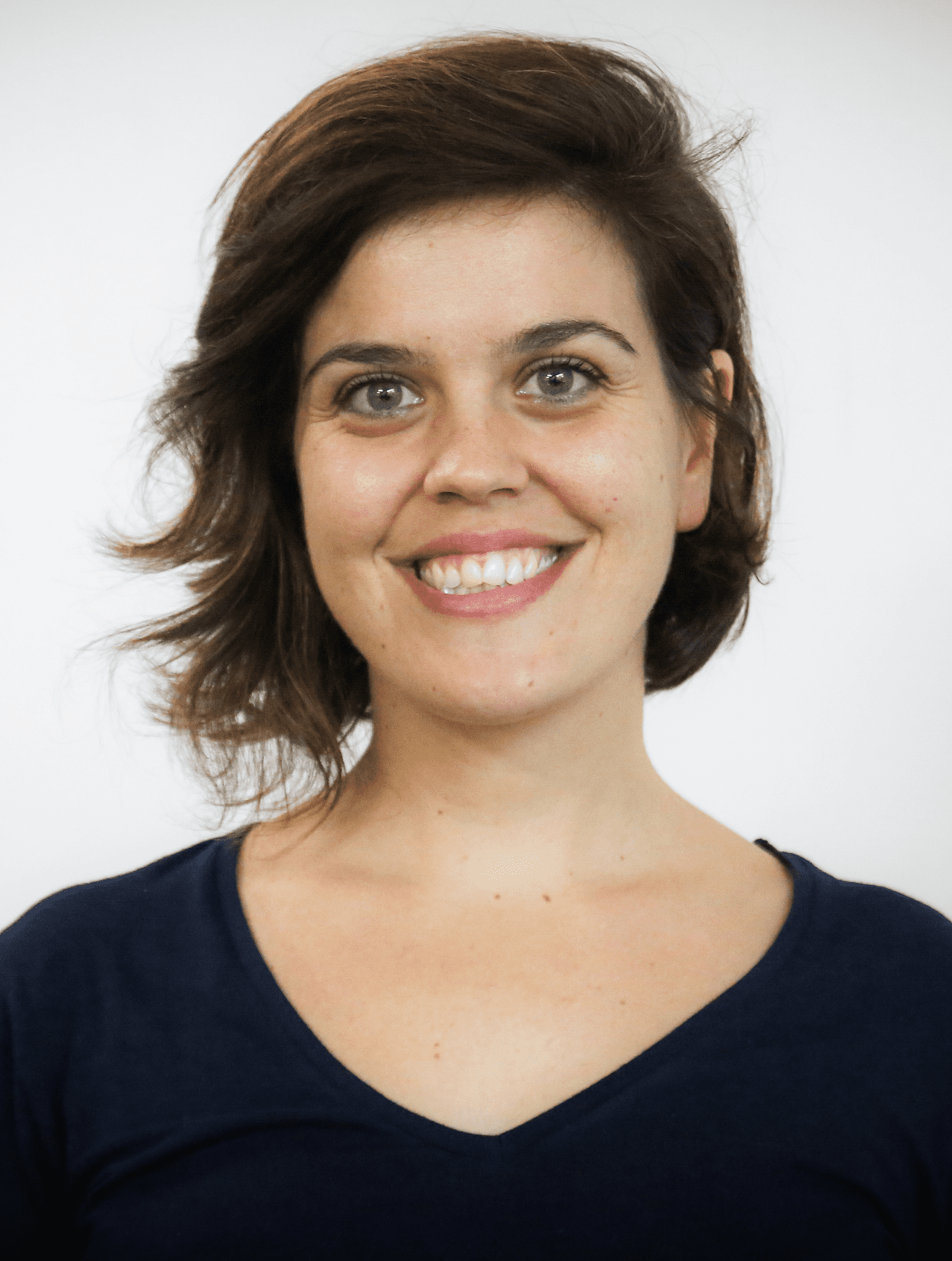
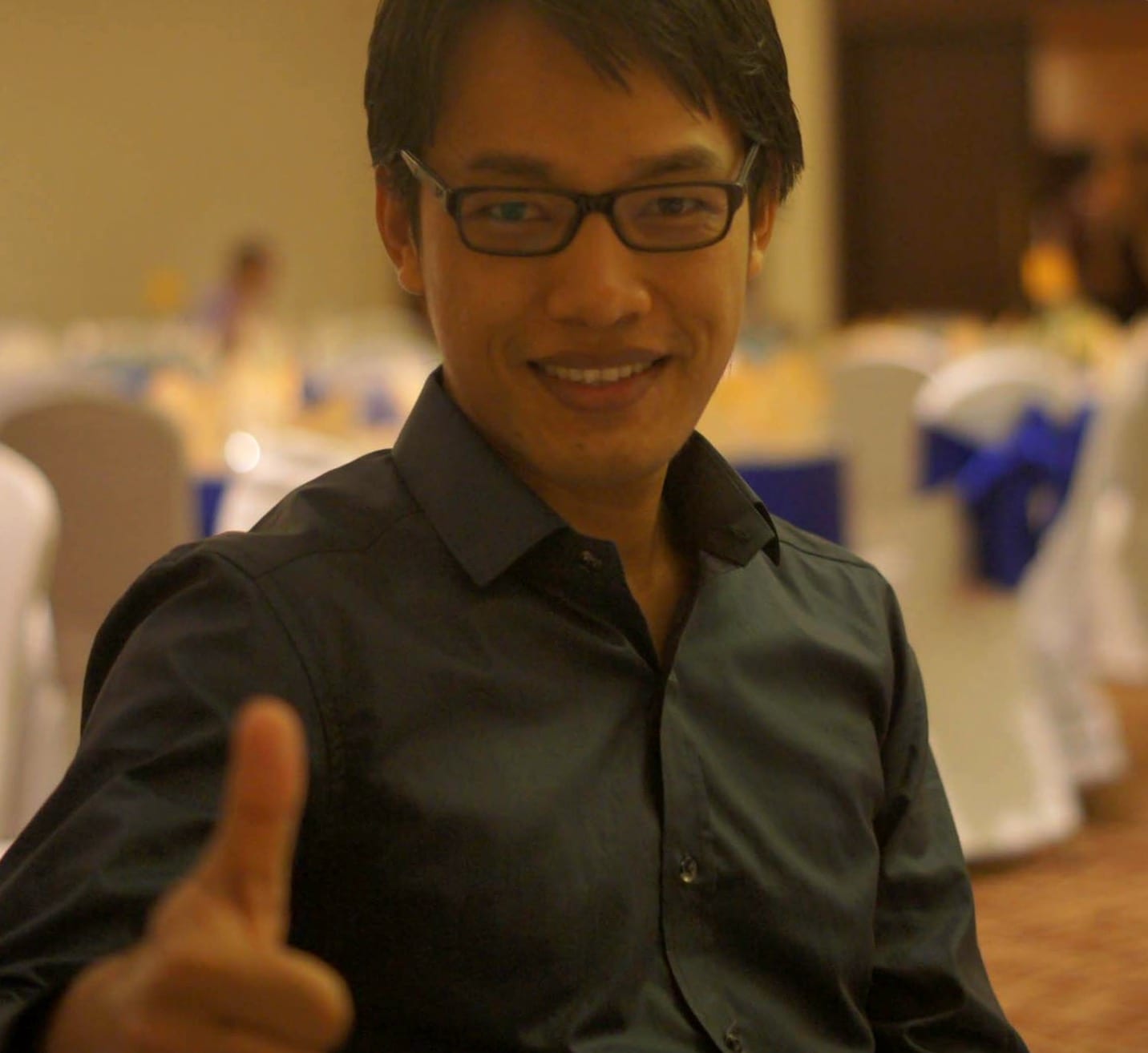
Read more
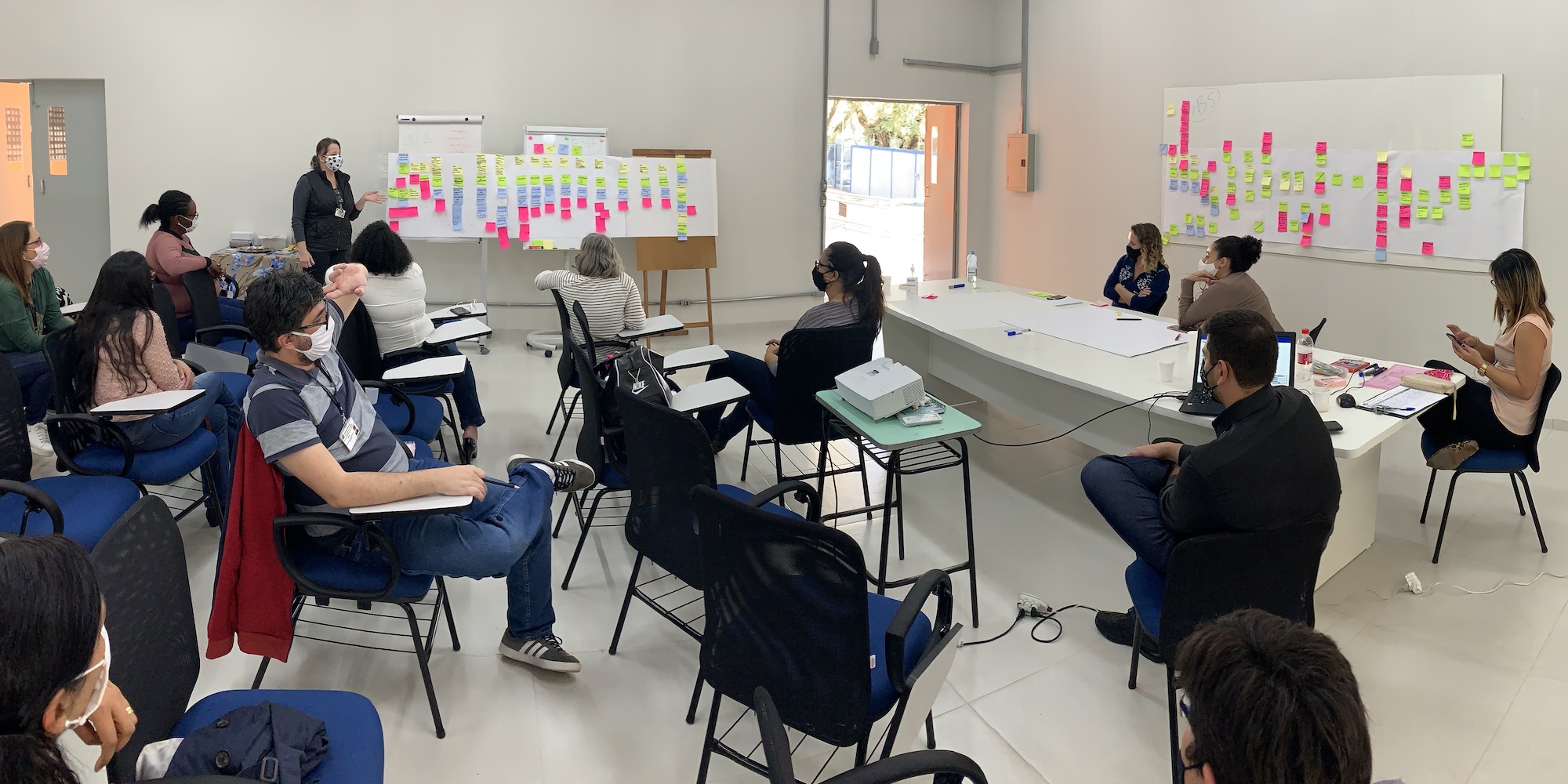
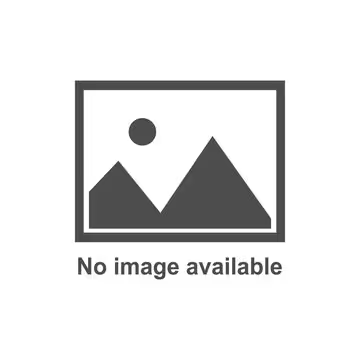
CASE STUDY – This project in Brazil, part of a city-wide effort to improve patient flows, led to impressive results in the waiting time to access cancer care.
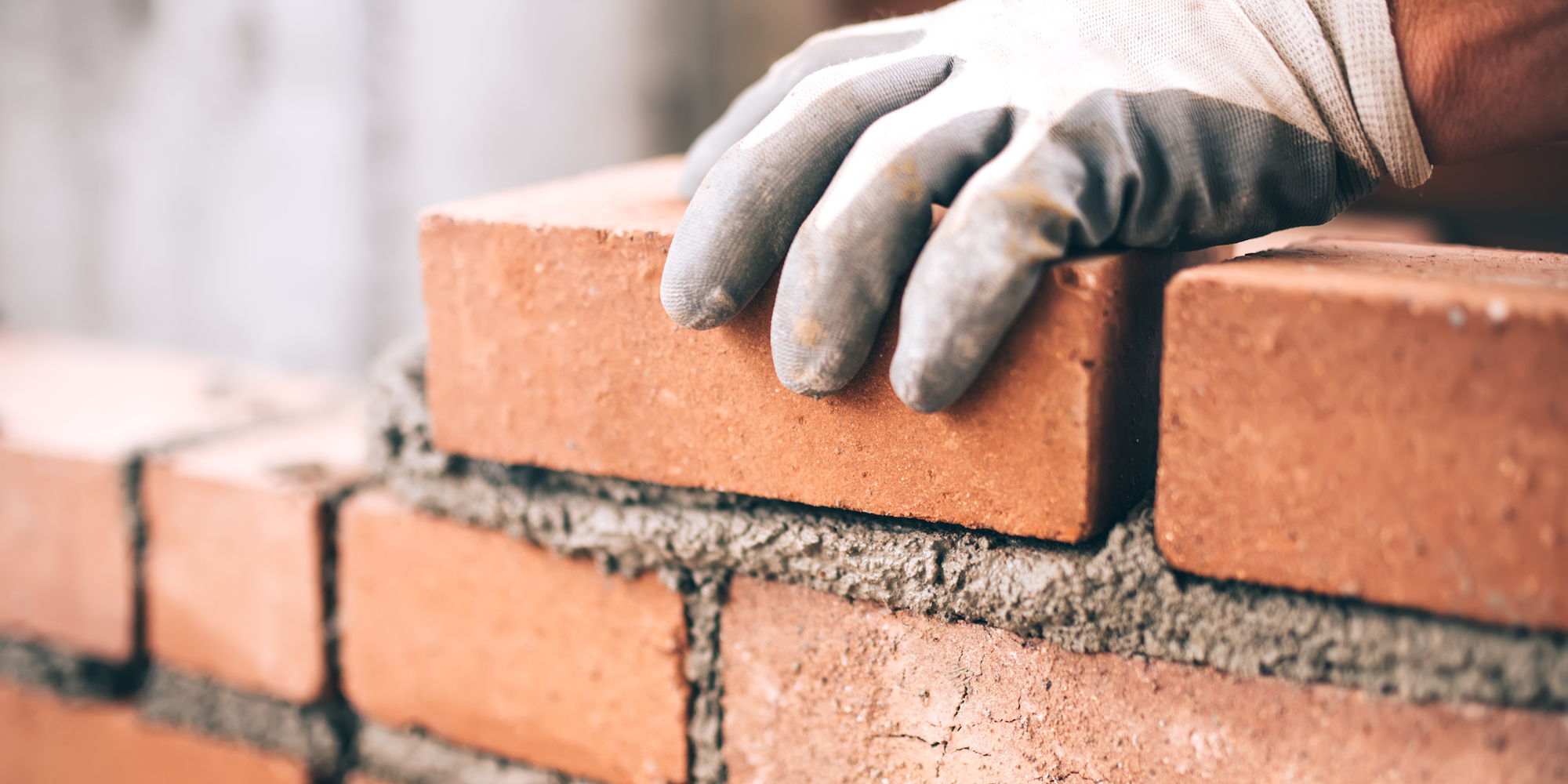
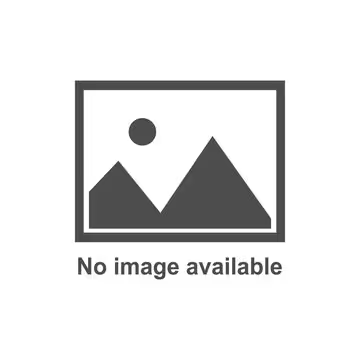
INTERVIEW – The editors of Planet Lean and Lean Post recently met with a senior executive of Turner Construction in New York City. Together, they discussed leadership development, respect for people, and the future of the industry.
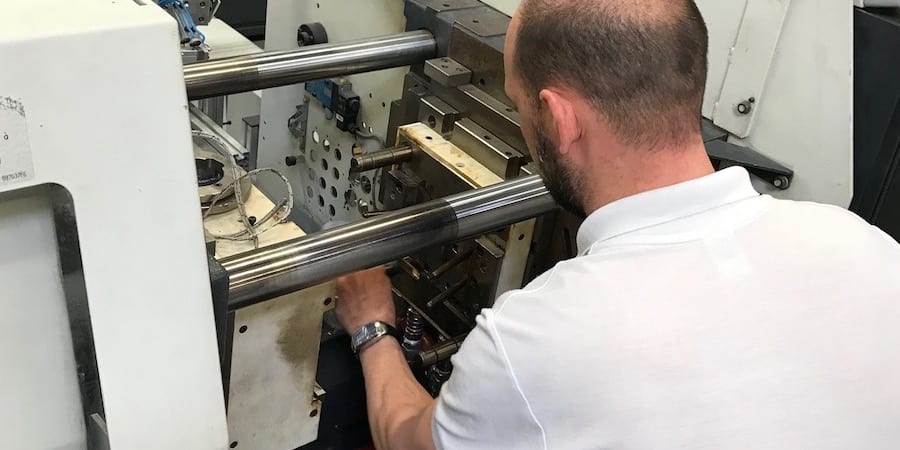
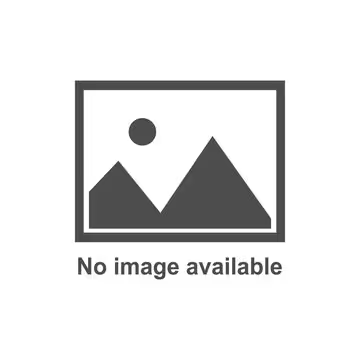
THE TOOLS CORNER – For the second article in our new series, the author offers a guide to the origins and use of one of lean's most important tools: SMED.
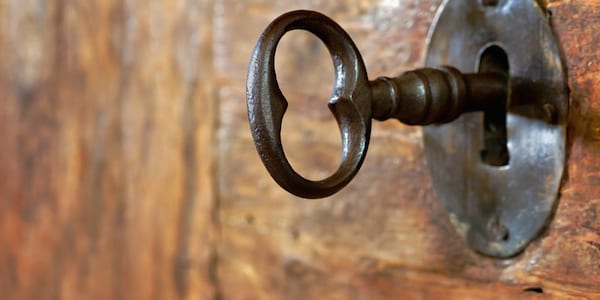
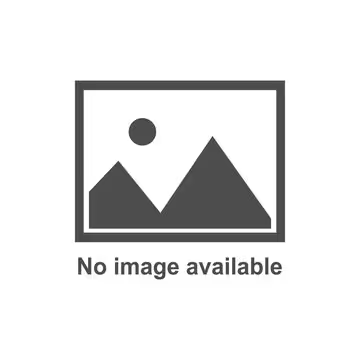
FEATURE – Lean management forces us to look at our IT service management from a different perspective and helps us to ensure it really supports our organizational needs.