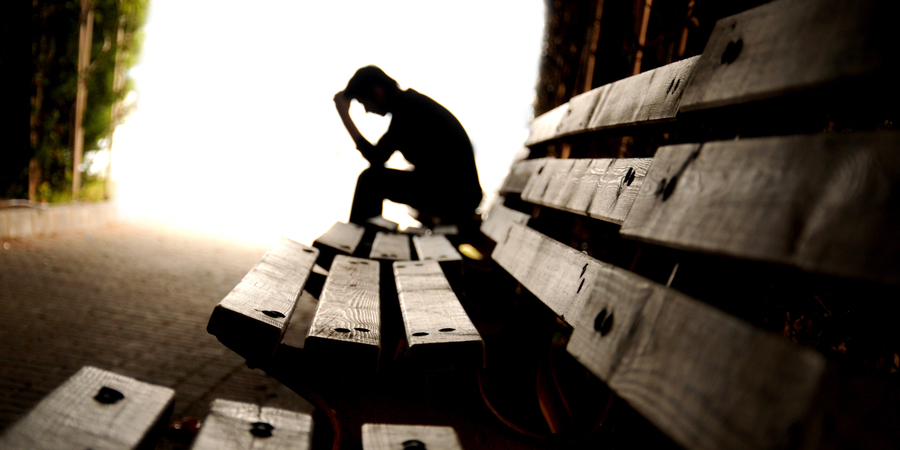
Three key business challenges lean can tackle
FEATURE – Ahead of the annual lean conference of LEI Polska, the authors reflect on a recent survey they ran with their clients on the key business challenges they face.
Words: Tomasz Koch, President, and Remigiusz Horbal, member of the Management Board, Lean Enterprise Institute Polska
At the end of 2018, the Lean Enterprise Institute Polska conducted several dozen interviews with the directors of companies embracing lean thinking and with managers or experts in continuous improvement. We asked them what the biggest challenges in their work are and how these relate to lean management.
It was interesting to see their responses clearly focused on three topics: how to effectively involve managers in the change of a business; the role of lean thinking in the digital era; and how to retain skilled and talented people by leveraging lean. (These are important issues in today’s business world, even though the third problem is perhaps more specific to the Polish labor market.)
In the light of this, we decided to focus the content of our upcoming Lean Management Conference on these topics. This article is an introduction to these challenges, which will be discussed in detail during the event.
ENGAGING MANAGERS IN EFFECTING CHANGES
This is problem not just for lean organization, but for any business that is trying to change its processes or culture – at a time when the pace of change all around us is increasing at mind-boggling speed. In this section of the article, we will discuss a few approaches that we consider valuable.
In our experience, for example, John Kotter’s famous 8-step change model (developed based on surveys with companies that successfully implemented large change programs and with those that failed at them) can really help you in your pursuit of a lean transformation. Interestingly, these eight steps are not commonly used in the lean community.
Let's look at a couple of them in the Polish context. The first one is about creating a sense of urgency, to convince people that changes are necessary for the survival of the company. In many Polish branches of international corporations, the implementation of lean is simply commissioned from the Head Office as a task. This means that people (with the exception of the lean coordinator, perhaps) often don’t consider lean to be that critical. In such a scenario, we can’t expect management to enthusiastically embrace the new way of working.
The next step, as defined by Kotter, is building a group that leads the change and includes key people in the company. But then why we often find that the head of the Polish branch is not included in the change team? Why does her or his support end at the “anointment” of the lean manager and at a declaration of support?
We only mentioned two of Kotter’s eight steps here, but sadly the situation is not better with the rest of them. Therefore LEI Polska aims to get closer to Kotter's approach by collaborating with his coworker and engagement leadership expert Céline Schillinger (previously responsible for corporate change programs in Sanofi Pasteur). At our conference, Céline will share her latest knowledge in the field of change management and information on its practical application.
Another good practice that helps us win over management is to start our improvement efforts with a small-scale pilot project and then grow from there. It is much easier to start off in a department where difficult challenges exist and people already have the sense of urgency Kotter talks about (and the manager is motivated). But is it possible to completely transform such an area? Can we change the way managers think and act, instead of just streamlining the process? Absolutely, so long as we understand that lean is more than a toolbox. Lean thinking requires a cultural shift, which cannot be dictated from the top or through a training or a certification. Learning in a lean environment happens on the gemba, on the job. This approach is most effective with one or a few teams at first, before expanding to the entire company. Over the last few years, our Lean Institute has worked with our partners in the manufacturing and service industry on the Lean Team Transformation program (LTT), which allows to transform one or more selected teams relatively quickly, including the internal transformation in the way managers think and act. This year, we have invited Randstad (where this approach was successfully applied) to speak at our Lean Management Conference. They will be joined by Velux (who will discuss how to increase the involvement of managers using hoshin kanri) and by DB Schenker (who will share their experience about the engaging leaders in building a lean culture). The topic of engaging managers in effecting changes will be discussed also by John Burton (former vice president of Fiat Chrysler China and former general director of several General Motors plants in Europe) and executive coach and lean author Michael Ballé.
LEAN IN THE DIGITAL ERA
The digital revolution is happening. According to research, scores of companies have tried to implement digital technologies to harness the potential of the 4th Industrial Revolution (Industry 4.0), but few have managed to achieve a significant improvement in their results – including financial ones. At the same time, a January 2019 study by the World Economic Forum found that the 4th Industrial Revolution has enormous potential for improvement in a range of KPIs. Sixteen companies that were successful leveraging Industry 4.0 technologies, selected from among 1,000 that took part in the research, reported incredible results – with, for instance, increases in productivity ranging between 5 and 160%, reduction in quality costs between 5 and 90%, or reduction in changeover times between 30 and 70%.
But are so few companies achieving such results?
We had the opportunity to visit a couple of companies that successfully combined the benefits of lean thinking with those of the digital revolution. With their help, we would like to test the following hypothesis: that lean helps companies to take on digital technologies much faster and to therefore gain competitive advantage. We have invited a few of them to share their experience at our event in June.
For example, GKN Driveline, a company that has been on a lean journey for many years, has used digital technologies to increase the efficiency of business management. Mariusz Karolewski, president of the Management Board will tell us all about it. Another interesting example is WABCO, whose lean six sigma program has been combined with investment in Robotic Process Automation, Big Data Management, Augmented Reality, AGV and collaborative robots. CEO Paweł Pałubiński also agreed to present at the conference, where he will explain how the implementation of Industry 4.0 technologies forced a change in the way of thinking, changed the role of the top management, and strengthened continuous improvement. Andrzej Marcinek, managing director of GEDIA, will answer a very important question: can people dealing with lean processes benefit from the digital revolution? Gedia, an experienced lean company, has been using Big Data and Industry 4.0 for continuous improvement. We will then have Eurobank, who will tell us about robotization of service and office processes.
Because technology impacts the every-day lives of each and every one of us, we cannot forget the importance of continuing our discussion on the relationship between man and machine. Recently, the concept of Human 4.0 was born and Karol Kundzicz (co-founder of the Think Tank Human 4.0 Foundation) will join us in Wrocław to discuss this.
USING LEAN TO RETAIN SKILLED AND TALENTED PEOPLE
In today's labor market – characterized by demanding employees and a difficulty to attract and retain talent – solid recruitment processes are more important than ever. Enterprises are outdoing each other, offering higher salaries and better "benefits” to try and poach talent from their competitors. Keeping our employees has become a huge challenge for organization (a problem compounded by a labor market still tied to traditional work but full of millennials, who have a completely different set of values and must be engaged with differently).
What does lean have to do with this? On the one hand, continuous improvement requires committed and motivated employees. On the other hand, people development and better management (both promises of a lean thinking) make for more a motivating working environment. Let’s take millennials as an example: among other things, they typically expect continuous feedback, support in career development, self-fulfilment, freedom of action, partner relations with superiors, and a management team open to discussing their ideas. Doesn’t this all sound like lean to you? It does to us! Lean thinking encourages communication based on daily meetings and visual boards, offers a systematic and well thought-out approach to employee development, awards decision-making power to people at the lower levels of management, asks them to actively participate in improving their work, and advocates for servant leadership. In our minds, lean is perfectly compatible with the needs of today’s employees.
Toyota's vast experience can help us in this area, as well. It is no coincidence that in the autumn of 2018 we published the Polish edition of The Toyota Engagement Equation by Tracey and Ernie Richardson, whom we have invited to attend (in a live streaming way) our June conference.
We have many other examples closer to home. Here in Poland, companies like GEDIA, Dovista, BSH (Bosch and Siemens Home Appliances) and Grupa Żywiec are making great progress exploring innovative ways to engage employees and create better working environments. Together with LEI Polska’s lean coaches, these organizations will explain how underestimated the role of management is in building employee engagement and share insights on how to boost it.
THE AUTHORS
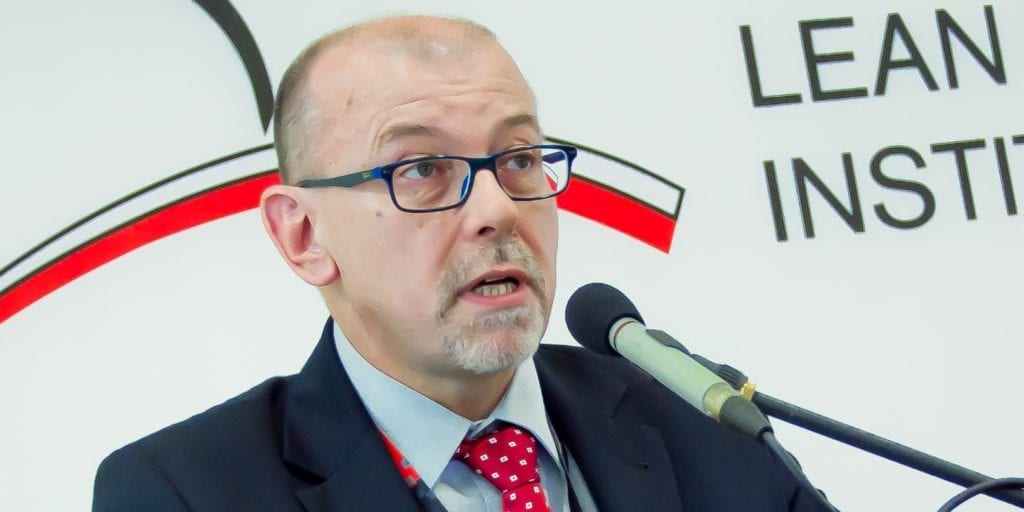
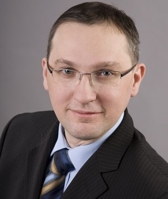
Read more
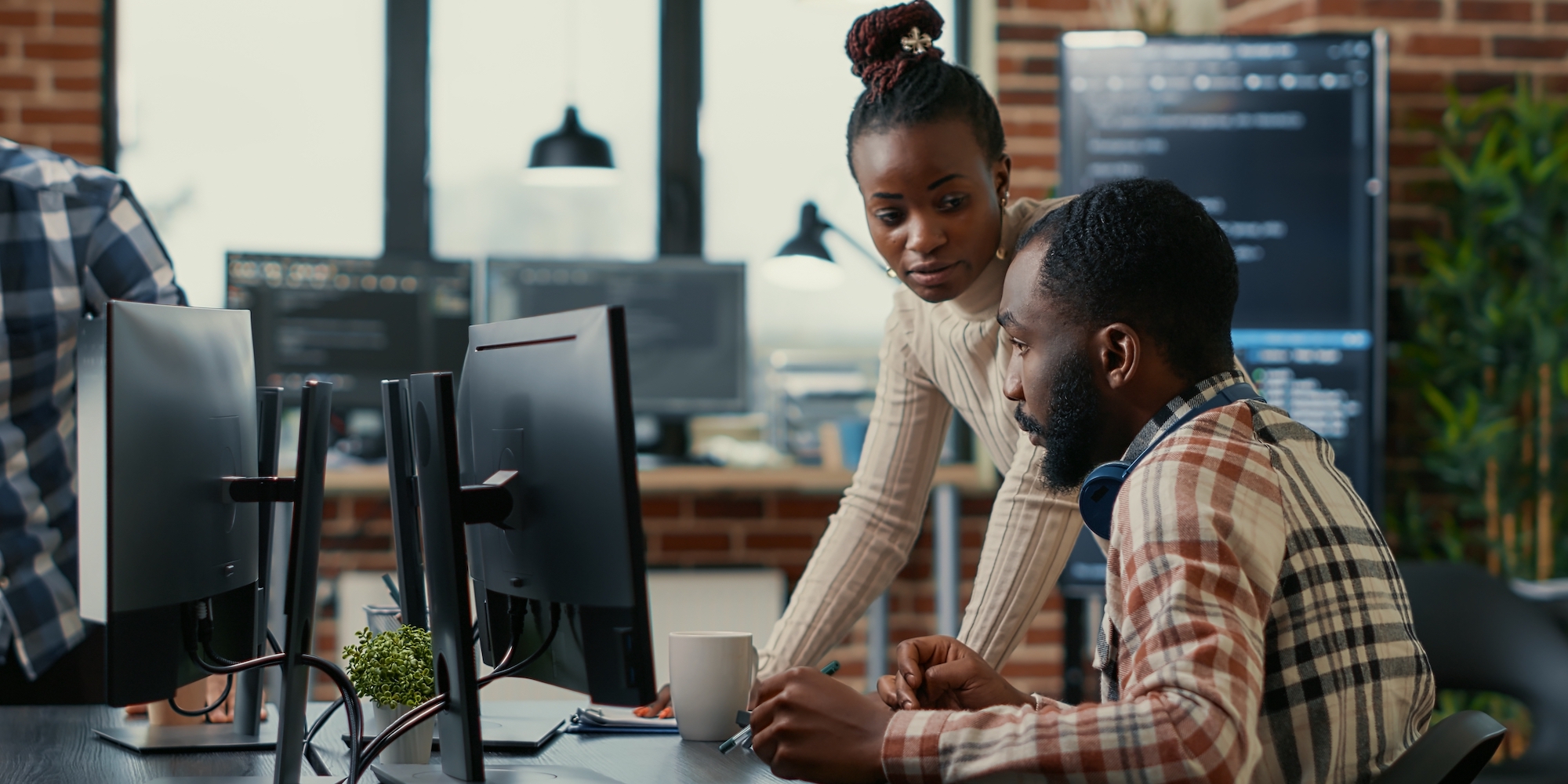
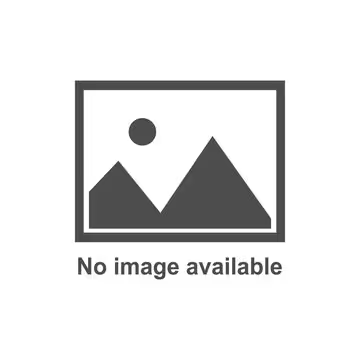
FEATURE – BRQ Digital Solutions shows that effective customer-focused improvement must happen from the inside out, with team development aligned with the pillars of lean digital transformation.
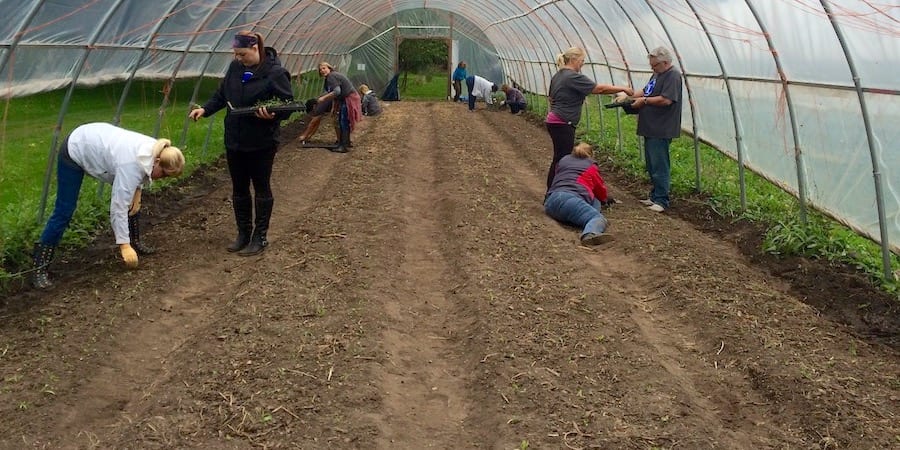
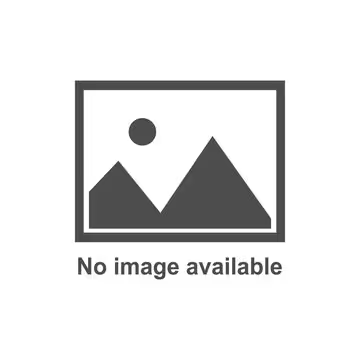
FEATURE – Riverview Gardens in an NGO striving to build prosperity for the community around it through capability development. The authors suggest this should be the goal for the lean community as a whole.
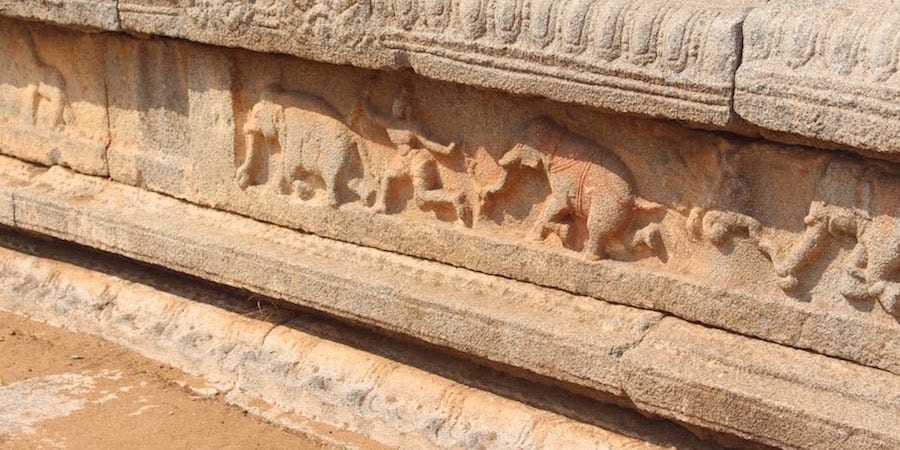
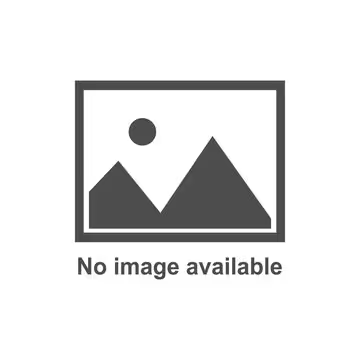
FEATURE – Is there such a thing as a lean plan? There is, but it's not an off-the-shelf solution that will appease your boss – and that's why traditional, bureaucratic organizations continue to exist.

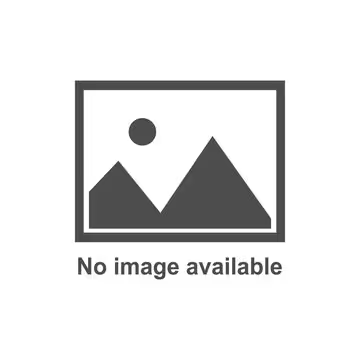
FEATURE – In business, the word “turnaround” refers to radical changes in the direction a company is moving toward. Here’s why Lean Thinking can increase the chances of success of such endeavors.