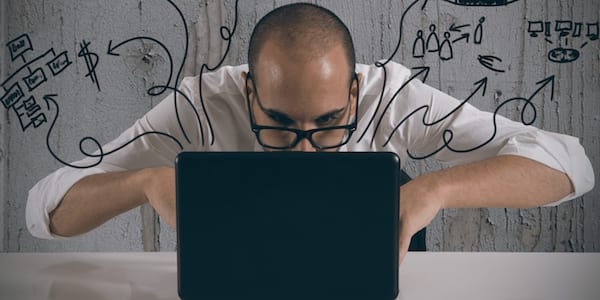
Why lean thinking is invaluable to IT leaders
COLUMN - In the first installment of her new column, the CIO of Finnish defense company Patria shares her thoughts on what makes lean management so critical in the life of the leader of an IT department.
Words: Sari Torkkola, CIO, Patria
As CIOs we are in charge of complex systems that are influenced by people, technology, and business needs. We use command-and-control management when cause-effect correlations in our environment are chaotic and unpredictable. However, transforming reactive operations into stable and proactive ones requires an understanding of the laws of nature (like Little's law or Kingsman's formula), psychology and statistical thinking. In this sense, lean thinking is invaluable to the leaders of IT functions.
I have applied lean in IT operations at Patria, a defense company in Finland, for three years now – and there are a few key lessons that I would like to share with you.
#1 - Customers demand shorter response times
The removal of waste that lean enables is critical to shortening lead-times, which helps a company to meet customer expectations. Customers complain that our times of response are too long and unpredictable, and - sadly - the explanation they offer is too often related to problems with IT staff. Personally, I prefer Dr Deming's way of looking at things: "A bad system will beat a good person every time."
Lean provides principles, methods and tools to understand and fix
system-level inadequacies in IT operations. And there are only few people in
an organization who have the power to bring system-level change: the CIO is one of them.
#2 - Exhaustion hurts service
IT systems do not run reliably without people. IT professionals solve
problems, advise customers, design, build and maintain systems. It is quite obvious to me that if people are not feeling well, the services they provide will not be at the level they could be.
Working in IT is demanding: considering the rate of change in technology, one needs to be in shape to keep learning the latest developments in the industry year after year.
Instead, we are caught up in fighting fires and juggling too many tasks. Unsurprisingly, lean recognizes overburden of people as one of the main forms of waste (one that can have a very detrimental effect on lead-times).
As we tried to tackle this, I was surprised by how positively people reacted to experiments such as A3, kanban, oobeya, X-matrix and daily flash meetings. What I found is that lean tools have a clear psychological effect on people. Human behaviour on the job had previously been a mystery to me, but now I consider it too critical to leave to chance.
Lean has decreased overburden in several ways at Patria, for example by increasing communication, removing rework and providing clear priorities. In addition, practicing KATA coaching and other lean methods has turned me and my managers into better leaders.
#3 - If you recognize the laws of nature, you're in control
As an engineer, it has been enlightening for me to study the laws of nature and the mechanisms that affect operations. Being used to IT service providers, who report meaningless monthly averages, it has been a revolution to measure variation instead.
The more skilled you become at minimizing variation, the less
time, capacity and inventory you need. In other words, you decrease costs, which is on every CIO's agenda.
Little's law and Kingman's formula, among others, establish a set of rules of thumb, when looking at the current state of processes, and when setting the
direction for improvements. For example, Little's law states that lead-time is
directly proportional to the amount of work-in-process (WIP). Measuring and
controlling work-in-process, therefore, provided me with new ways to influence teams, processes and subcontractors.
At Patria lean made us perceive WIP tasks as flow units (in IT they are somehow invisible, as work-in-process is rarely in the form of physical inventory). These units could correspond to, for example, customer requests to the services desk, IT projects or IT contracts under negotiation. They
all have a lead-time that impacts the customer, and they flow through
several teams in order to be completed.
Measuring variation of these flow-units introduced me the SPC (Statistical
Process Control) chart, now an appreciated part of our lean management system. As a CIO, I can now grasp the situation in seconds, just by looking at the visual boards, and I quickly come up with the right questions to ask my team. This leads to constructive, positive discussions on the problems we face.
Managing complex systems requires knowledge of laws of nature and
statistical thinking. Being a CIO without them is like being the captain of a large ship with no visibility, maps or understanding of tidal forces, and solely relying on intuition and luck.
#4 - Radical improvements are repeatable
When you understand lean principles, you get an insight into why and
how results are achieved. Suddenly, success is possible to replicate in other environments.
Thanks to lean, in the past three years we have shortened customer request queuing time from days to minutes, IT project lead-time from years to months, the lead-time for completing customer requests from days to hours, reduced the IT budget significantly, cut sick-leaves in half, and, finally, created trustworthy relationships with internal business customers.
The results were such that these days I recommend lean to every CIO I meet.
I only wish I had known all of this 10 years ago.
To watch PL's video interview with Sari Torkkola at last year's Lean IT Summit, click here.
THE AUTHOR
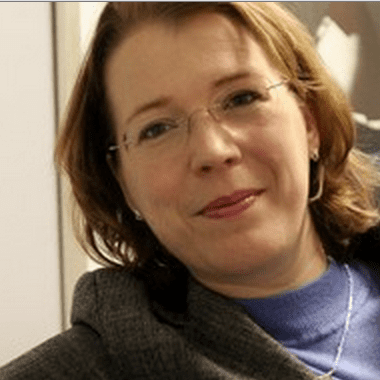
Read more
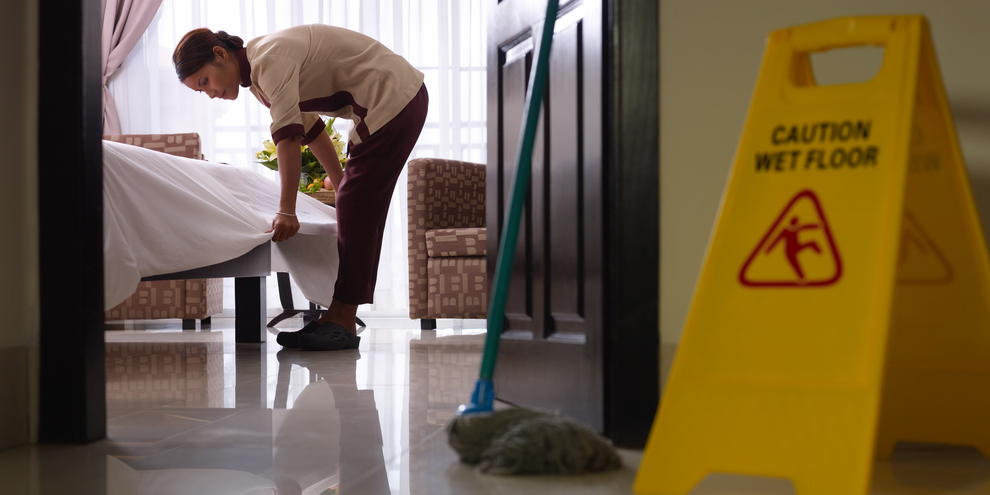
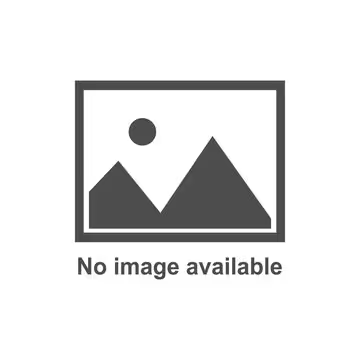
CASE STUDY – Hotels of the Palladium Group are implementing Lean Thinking in their housekeeping departments to improve efficiency and service quality.
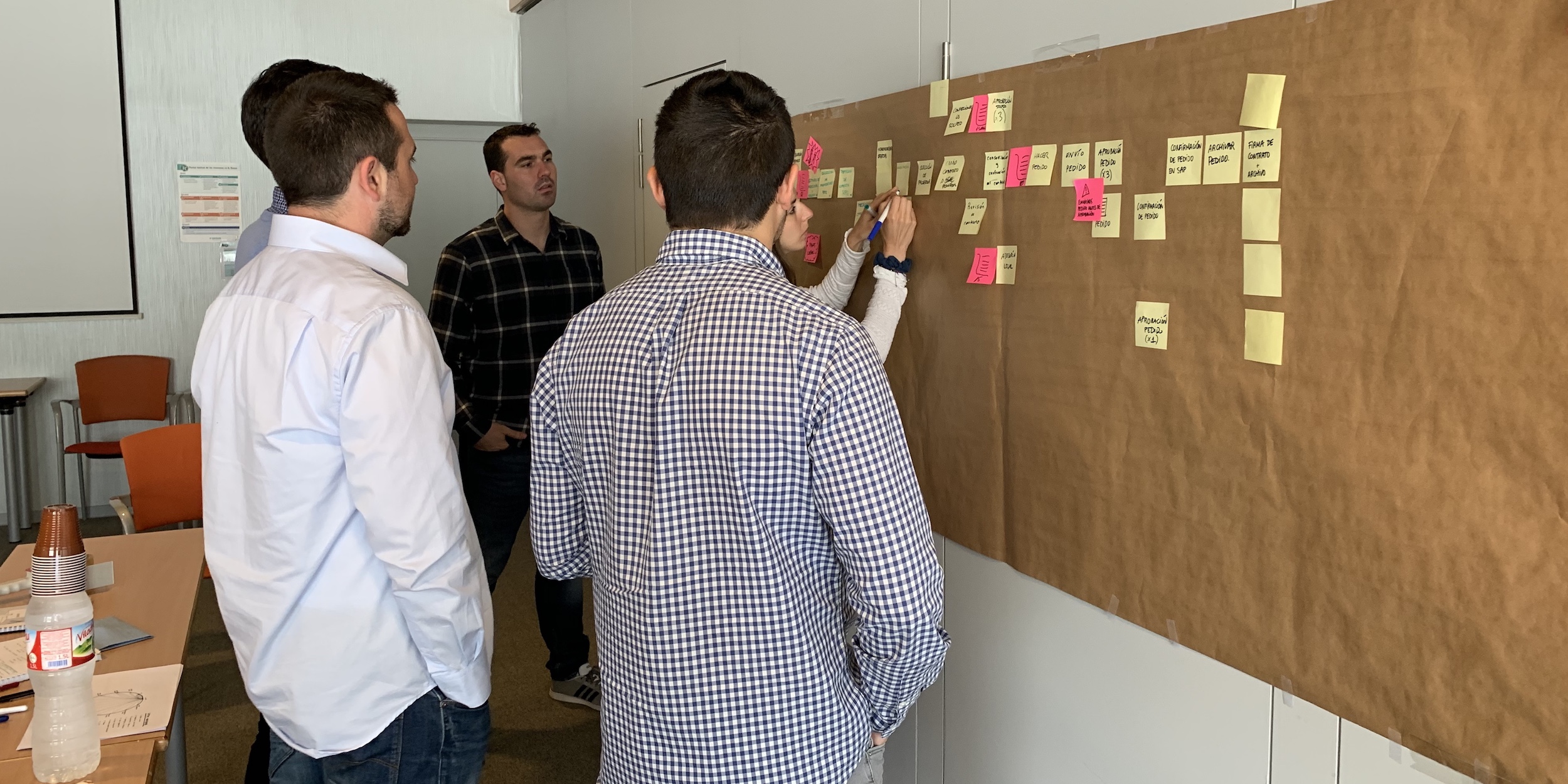
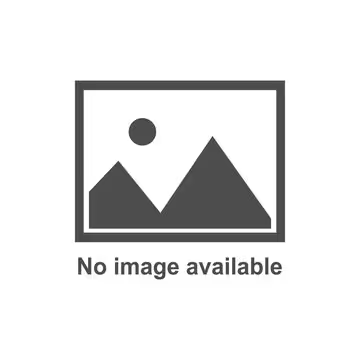
THE NAKED GEMBA – Value stream mapping is a fundamental tool in any lean transformation. The author takes us the most common mistakes companies make using it, so that you can avoid the pitfalls.
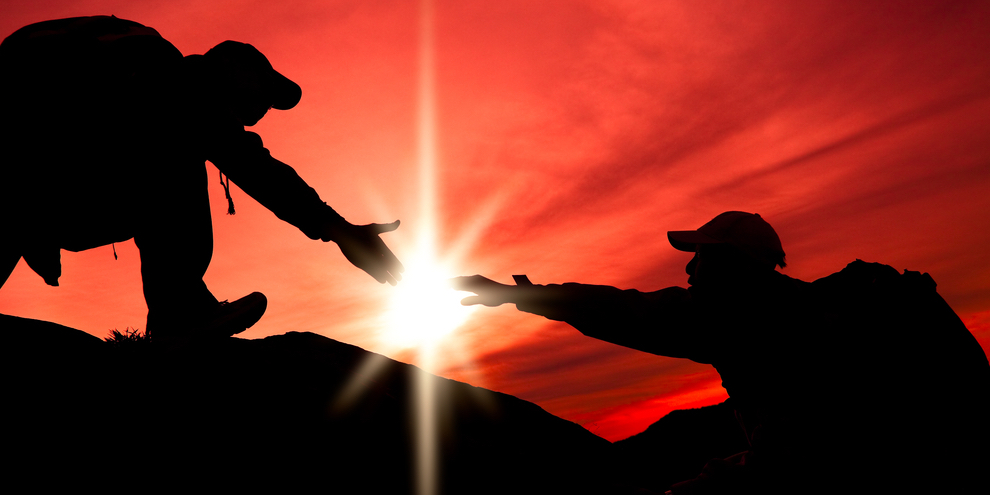
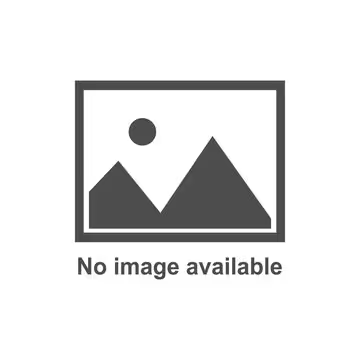
FEATURE – What does it mean to be a lean leader? Our editor tries to answer this question by searching the Planet Lean archives for the best nuggets of wisdom from our authors.
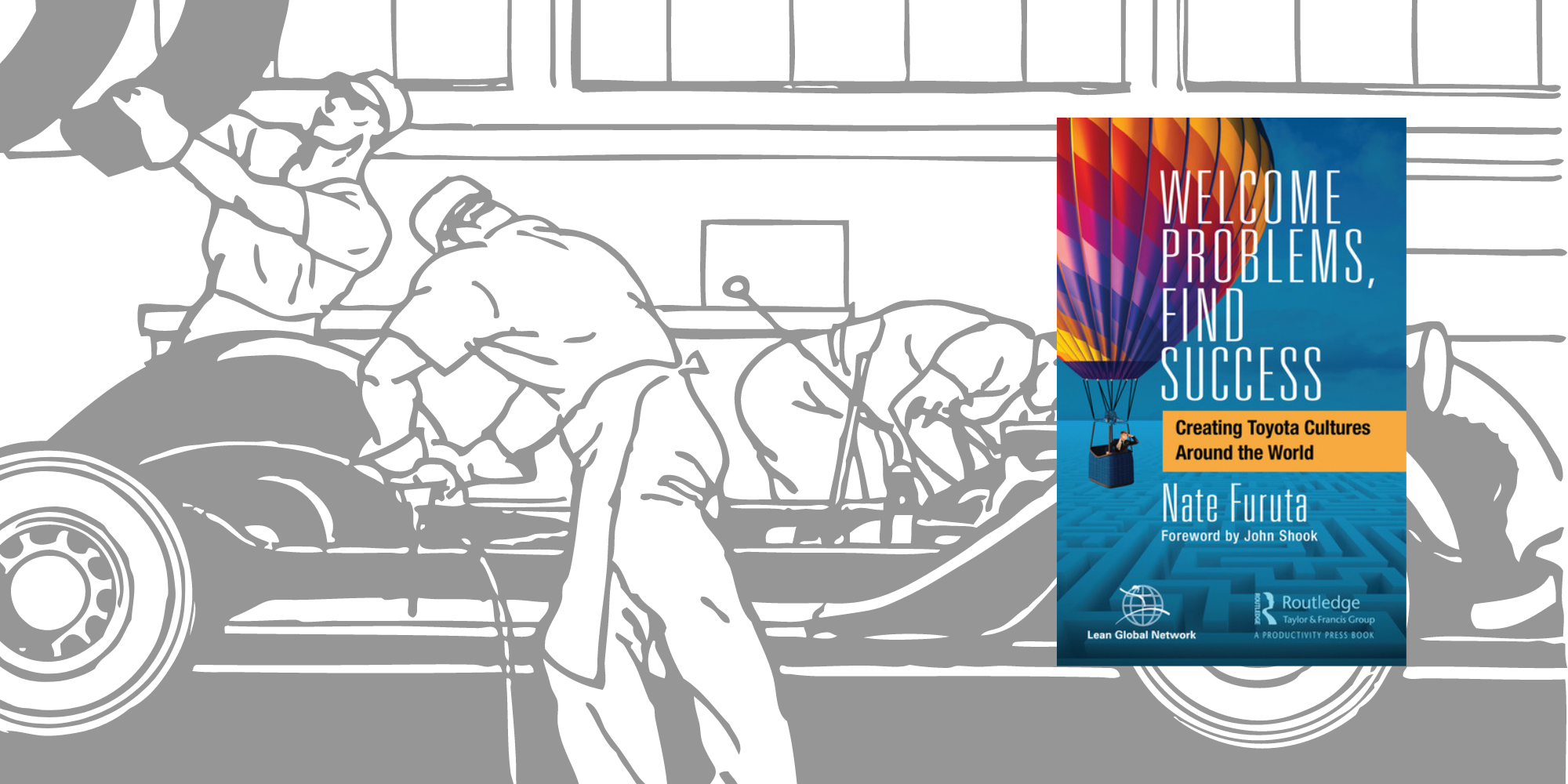
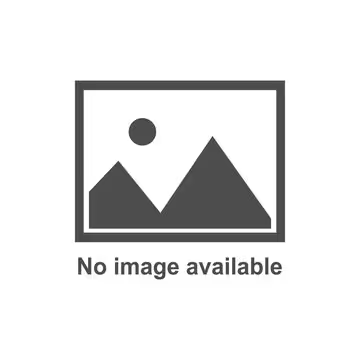
FEATURE – The Lean Global Network just published a new book by Kiyoshi “Nate” Furuta sharing compelling examples of how Toyota principles and culture can be effectively spread to new environments.