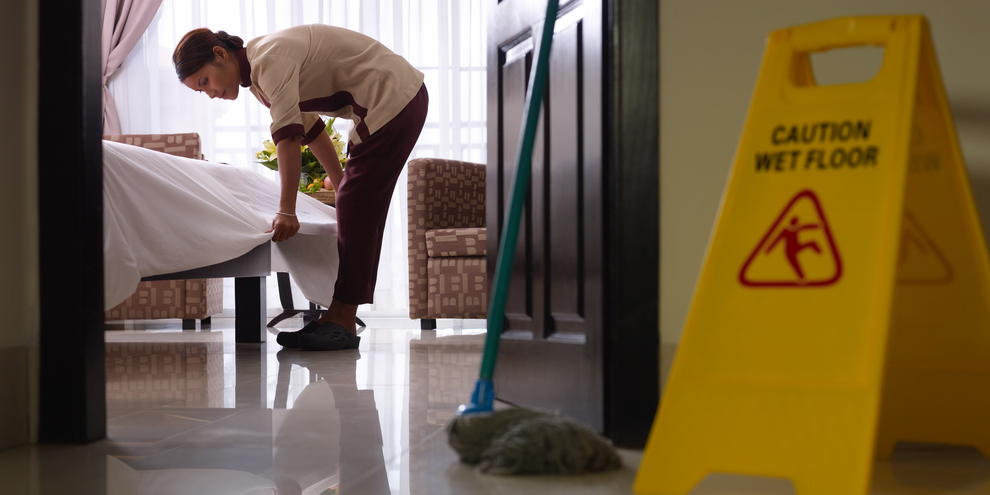
A leaner housekeeping
CASE STUDY – Hotels of the Palladium Group are implementing Lean Thinking in their housekeeping departments to improve efficiency and service quality.
Words: César Sancho, lean coach
One of the things we pay attention to when choosing a hotel or stepping into a hotel room is cleanliness. Indeed, housekeeping plays a key role in hotels, in that it directly impacts the delivery of value to guests.
These days, rating on booking websites from guest reviews are a major factor in the success of a hotel, which is why the work and performance of housekeeping staff and the cleanliness of a room throughout a guest’s stay are things we can’t afford to underestimate.
The tough working conditions housekeepers often have to endure are well known in the sector. Safety and hygiene surveys have revealed that, in carrying out their work, they constantly face short turnaround times, overtime, a considerable physical effort, straining positions, and repetitive movements. Except for some pioneering lean hotels, the work of housekeeping staff has largely been the same for decades.
Aware of this problem, the Palladium Hotel Group has launched a pilot lean project in Housekeeping in 2020 in the Hard Rock Hotel Tenerife, in Spain’s Canary Islands, with the idea of then spreading good practices across its network of 5-star hotels and group-owned laundries every month thereafter. After several months of shutdown due to the pandemic, the work has resumed at the end of 2021, with more and more implementations across the group and follow-up work ensuring the projects are progressing as expected.
The main objectives of the hotel chain were the improvement of work safety and hygiene, a reduction of lead-times and costs, an increase in right-first-time quality of the service provided to guests.
IMPROVING HOUSEKEEPING
With the application of Lean Thinking, the organization aims to tackle the difficult situations hotels around the world encounter every day: unexpected events, inefficiency in the use of resources, variability in the work, the lack of clear standards, and the risk of accidents among others.
As they take their first lean steps, teams typically wonder how they can improve the cleaning time without compromising quality. The focus of this exercise is not to shorten the cleaning time itself, but to optimize the available time while improving service quality to provide more value to guests. Focusing on time reduction alone can have negative effects, like poor cleaning (the meet the time goals “no matter what”), excessive supervision by different levels of management, or early wear-and-tear of equipment. What lean teaches us is to build quality into the process rather than having to check it constantly.
TEAM DEVELOPMENT
People development is one of the most important elements of a lean transformation. To provide people with the skills, tools, and information they need to do their work well, identify improvement opportunities, and make those improvements is indeed fundamental, and it is sure to lead to remarkable results in terms of productivity and efficiency.
Another success factor is, without a doubt, the creation of culture of teamwork to reach common goals. In the Palladium Hotel Group, we put a lot of emphasis on ensuring that each project is aligned with the corporate strategy and the objectives of each hotel, and on supporting each employee in their learning journey and in the development of their problem-solving skills.
Changes to the work or culture of an organization are often met with resistance at first, but what we have found after we launched these projects is that the reluctance some people displayed typically disappeared after they saw with their own eyes how the improvements – no matter how small – helped them in their daily life at work. When we rationalize the “itinerary” housekeepers follow to clean a room, for example, to avoid having them walk for miles and to optimize the use of their time, we see great engagement from them.
When they understand “what’s in it for them”, teams become very motivated and open to learning new way of working. As they further develop their lean capabilities, some of them have become so enthusiastic that they have started to implement lean in their own personal lives!
THE RESULTS WE ACHIEVED
Using Lean Thinking in Housekeeping, the Palladium Hotel Group has achieved very positive results across the SQDCP framework.
With regards to work safety, for example, we reduced the risk of accidents (caused by the fact that some housekeepers weren’t using the proper IPE or were performing wrong and potentially dangerous movements while cleaning).
After introducing the concept of right-first time and changing the cleaning process, we were able to improve our quality by 50% on average. The Global Review Index of the department improved by 30% and the NPS by 20%. These numbers were reflected in both external and internal audits, which reported an average quality improvement of 40%.
Delivery also saw significant improvements. Rooms are available to new guests in half the time these days, and cleaning during a guest’s stay is 60% faster. On average, the time it takes to clean a room has gone from 80 to 50 minutes.
Cost-wise, on average we have reduced water consumption by around 50% and chemicals consumption by around 30%. Thanks to a better “supply” of linens and towels to and from the laundries used across the chain, we have also seen a reduction in the cost they incur.
Finally, the people side of things. Staff turnover went down 30% and guest satisfaction has improved by 40% largely thanks to the employees’ newly acquired flair for solving problems. Housekeepers now enjoy better career and development opportunities.
The hotel sector is in desperate need for change and, with such results, the Palladium Hotel Group – just like other hotels that have successfully introduced and embraced the methodology – has proved that lean is the way forward. Not just because it helps an organization to make inroads in the way it manages resources to provide better quality and increase customer satisfaction, but also because of the culture of continuous improvement it promotes.
THE AUTHOR

Read more
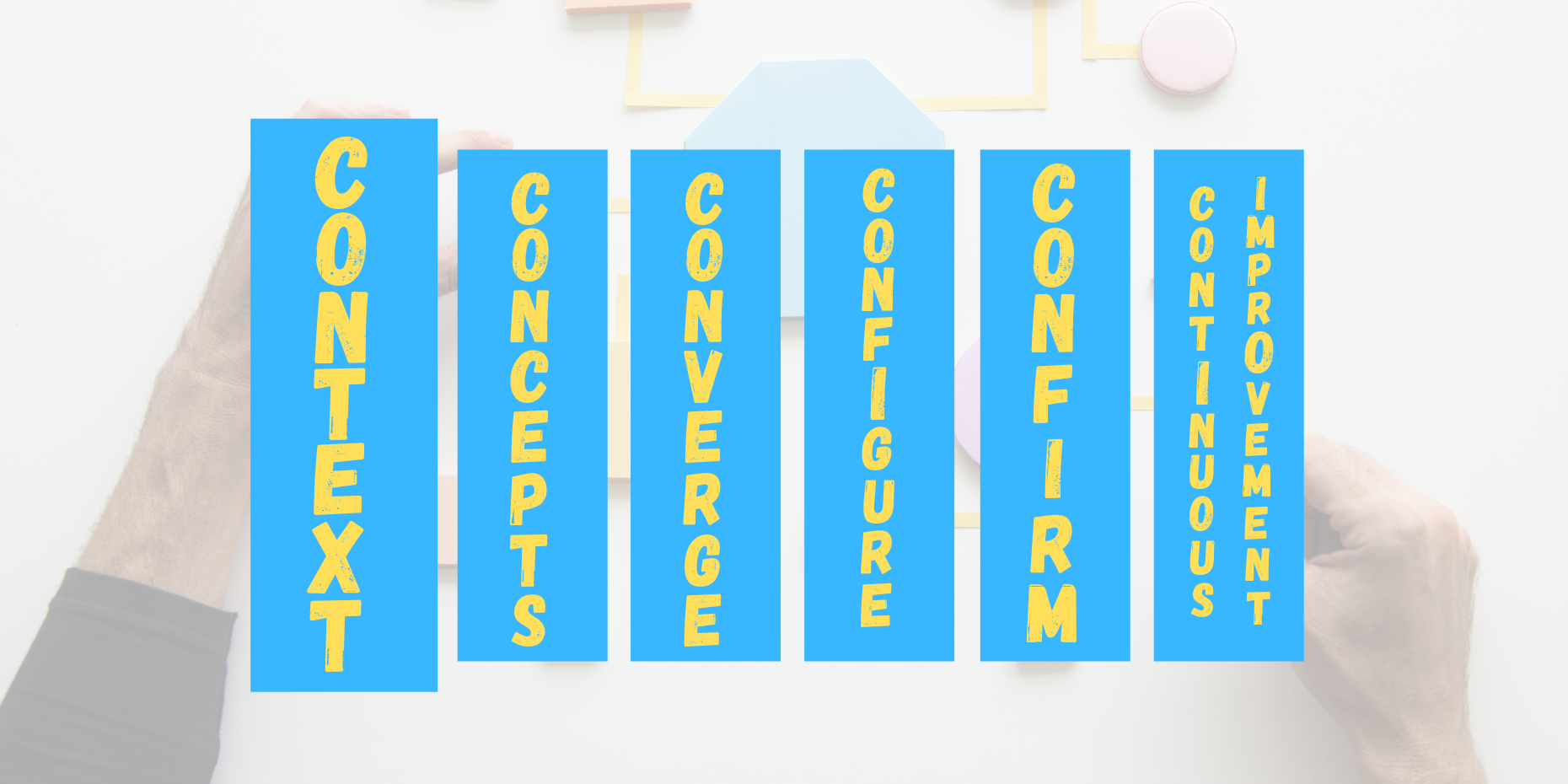
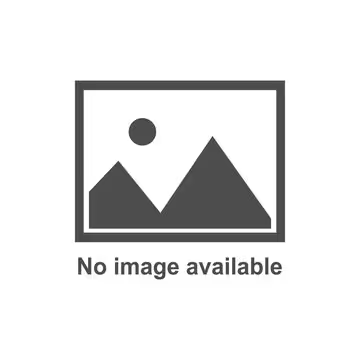
SERIES – The authors discuss the first of six elements in their process development model – Context – highlighting the importance of gaining clarity on the objectives of the process being created.

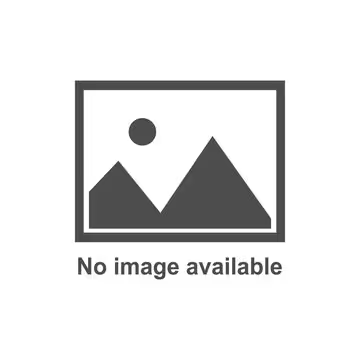
ROUND-UP – Looking back at the year that just ended, our editor Roberto Priolo reflects on the power and reach of lean thinking, and offers us a round-up of the best content from 2017.
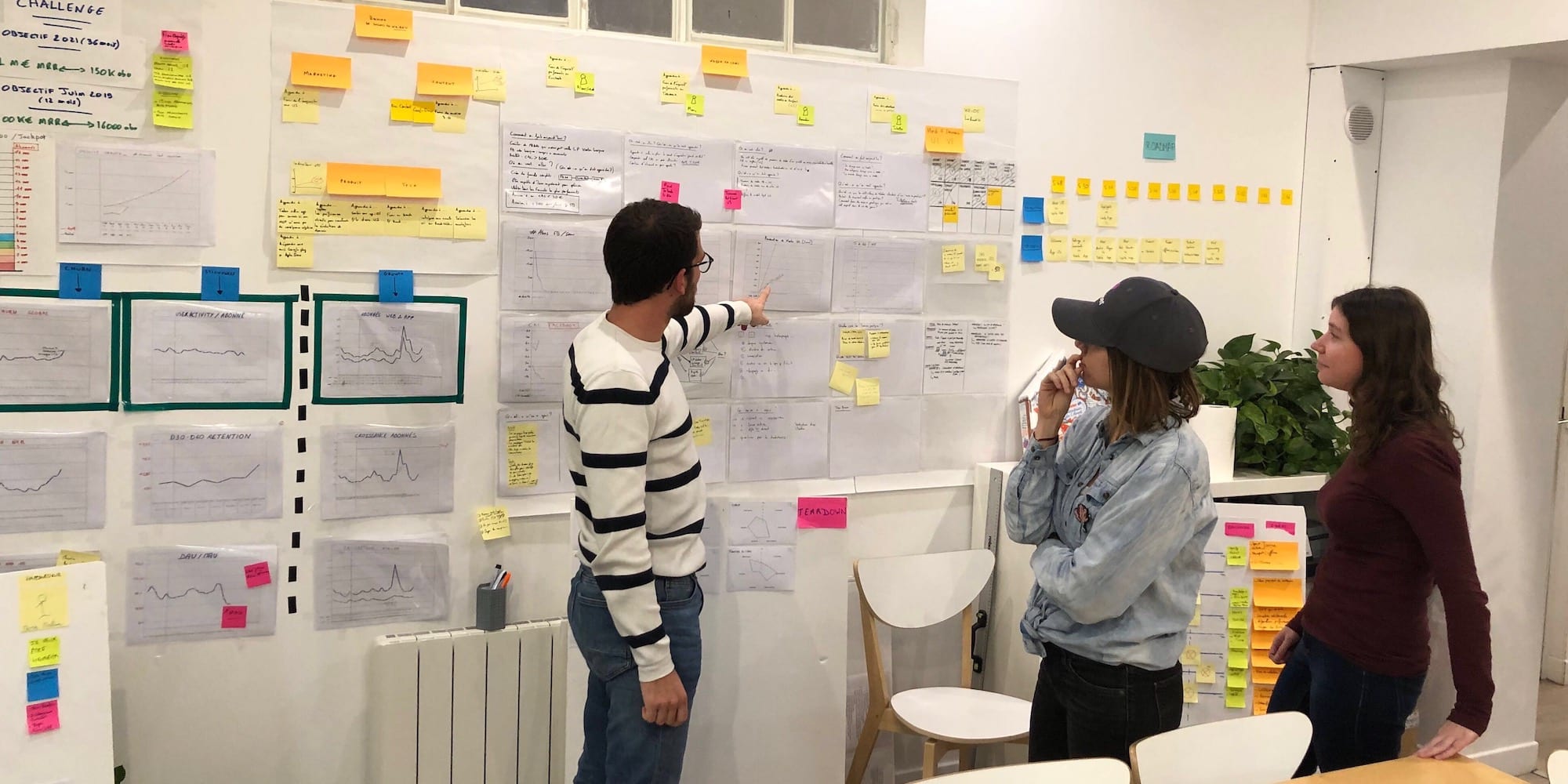
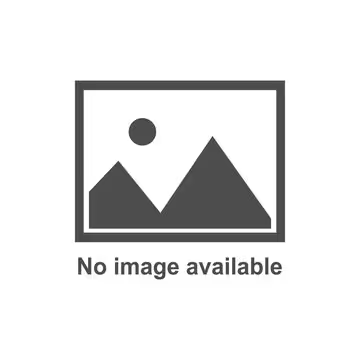
FEATURE – The obeya room limits the number of unknowns before we start developing a product. In this sense, it’s a tool for discovery more than it is for delivery.
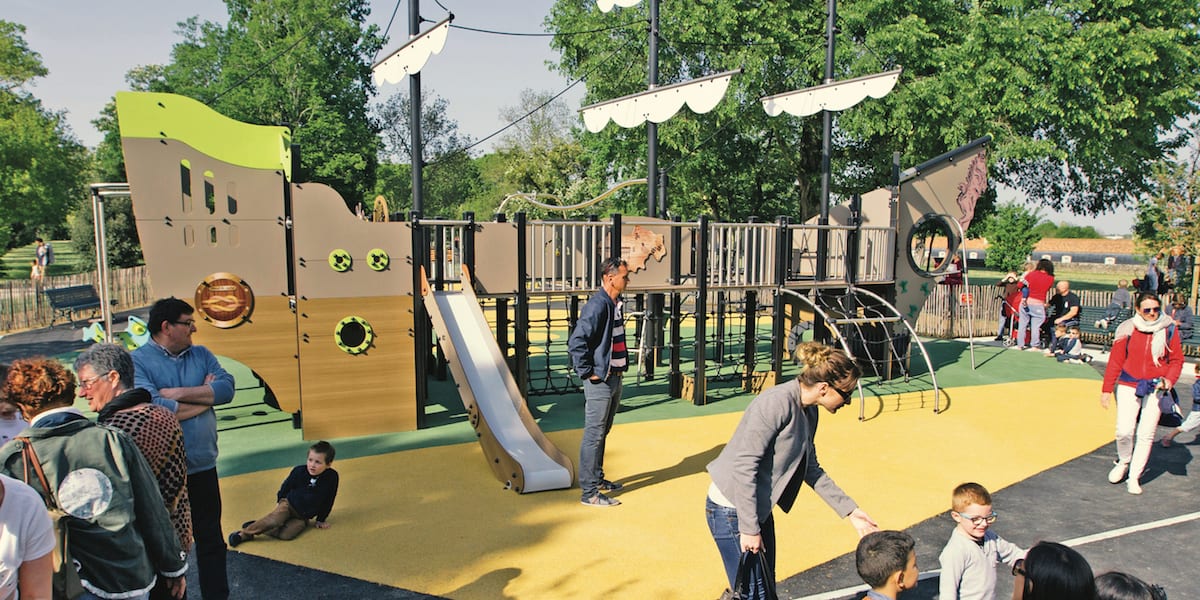
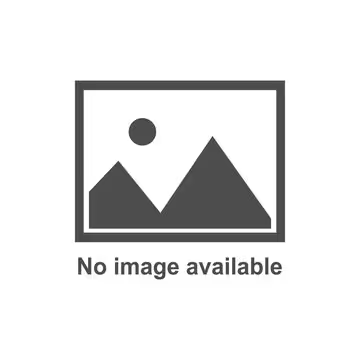
FEATURE – Enabling its people to think autonomously about problems and fostering collaboration among departments is allowing a French company that makes and installs playgrounds to thrive.