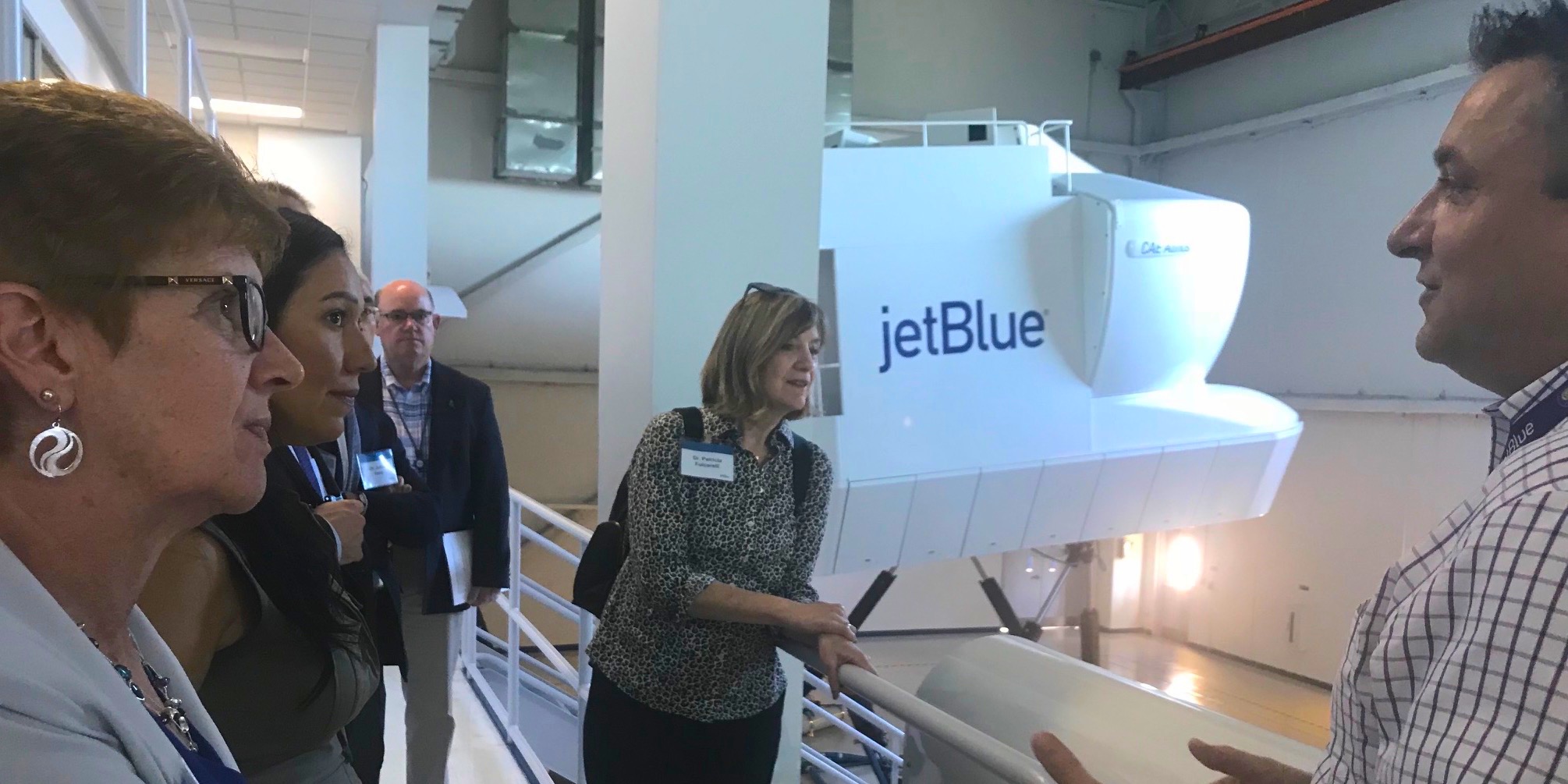
When a hospital meets an airline
FEATURE – In a bid to find inspiration and new ideas to achieve excellent outcomes in patient safety, a group from a Boston hospital flew to Orlando to visit JetBlue Airways.
Words: Patricia Folcarelli, VP of Health Care Quality, and Jennifer Stevens, MD, Director of the Center for Healthcare Delivery Science – Beth Israel Deaconess Medical Center, Boston
Sometimes, solving problems forces you to get out of your routine and go look for inspiration elsewhere. A few months ago, as Beth Israel Deaconess Medical Center looked at its work around patient safety and risk assessment (after receiving a grant from The Patrick and Catherine Weldon Donaghue Medical Research Foundation), we saw an opportunity to reach out to an organization operating in the ultra-safe airline industry.
We wrote to the VP for Safety at JetBlue Airways, asking him to come and meet us. Sure enough, he came to Boston and spent a few hours with us talking through the airline’s organizational structure around safety. A small group from Beth Israel then flew down to Orlando to meet his team at JetBlue University.
We spent a day there, during which the JetBlue team told us about their accountability structure, how they onboard people, how they orient staff and how they prioritize safety work. It was an incredible experience.
Those of you who are not too familiar with the healthcare industry might think of a hospital and an airline as a bit of an odd couple, but there are actually many similarities between these two industries.
First of all, both greatly value customer/patient safety: when we board an aircraft or step into a hospital, we put ourselves in the hands of professionals who carry the huge responsibility of looking after us and ensuring we reach our destination (whether it be the arrival gate or our discharge) safe and sound.
Secondly, hospitals have started to focus on patient experience and on ensuring the dignity of the patient is respected at all times. Because patients can now choose among several healthcare providers (much like passengers in the airline industry), the experience they have while they are at the hospital may determine where they go in the future.
Finally, there is now substantial discussion in the healthcare world about provider experience and team building – which, as we know, is a critical piece in any lean transformation.
JetBlue has an excellent track record in each of these areas, and we consider ourselves very lucky to have had an opportunity to learn from them.
JETBLUE AND SAFETY
At BIDMC, we were interested in building incident analysis and identification into our existing systems – both at leadership level and at the front line. We wanted to explore how we could establish a team-focused culture that has safety at its core.
When we arrived at JetBlue University, we thought we were going to talk more about incident analysis than about the type of organizational structure making patient safety easier to achieve. Instead, we had very interesting discussions about how to build the right culture in an organization.
Stepping into the beautiful JetBlue University building was very educational in itself. The airline has realized how important it is to invest in training and on-boarding to build its culture and brand. The state-of-the-art simulators were particularly interesting: offering a very realistic experience (one of them had a high-fidelity replica of the front half of the plane), they are used to teach flight attendants key skills – from dealing with difficult customers to being able to distinguish the smell of fuel from the smell of nail polish remover. No wonder they are being used 24/7!
Even more impressive is the weekly orientation organized for newly-hired employees in the JetBlue University auditorium, where senior leadership welcomes new hires to the company. During that orientation, pilots sit next to baggage handlers and cleaners. JetBlue spends a lot of time (and, surely, money) developing a culture of teamwork that engages everyone from the moment they join the company. We found it remarkable to learn that senior leadership directly address newcomers, which is testament to the focus the airline places on respecting people.
We were also told about JetBlue’s incredible work with safety, which involves people at a number of different levels. We learned a lot about how they understand safety “events”, respond to them and escalate problems, and we got a lot of ideas on how we could change the way we respond to our own incidents at Beth Israel Deaconess. It was particularly interesting to see how they structure event analysis: having been given access to extensive data, the team analyzing safety events can dig very deep into the factors that caused the problem and typically creates a beautifully laid out timeline of exactly what happened. When a problem occurs, they ask themselves about the type of training the people involved in the incident received or whether they were under pressure at the time. This is critical, and it is how a learning organization should think: what are the conditions we put the employee in, which allowed the event to occur? (A far cry from the traditional, archaic approach of pointing fingers.)
Furthermore, we saw that at JetBlue the response plans are developed at the front line (which also happens to be a key tenet of lean thinking). In the healthcare industry, there is a tendency for the safety experts to investigate and offer the countermeasure, but we should do a better job at involved the team that experienced the problem.
Also noteworthy is the airline’s strategic way to rank risk for certain events. Whereas in healthcare we are still spending more time on the real harm events (even when they don’t require a huge amount of investigation or are incredibly rare) than on serious near-misses, JetBlue has become very good at correctly prioritizing safety efforts. Since our visit to Orlando, we have begun to work on this at Beth Israel Deaconess, in a bid to be a little more strategic ourselves (for instance, we have begun to ring-fence time each week to more rigorously review all the near-misses related to medication administration).
Another important lesson learned that stemmed from our visit to JetBlue was on the role that senior leadership plays in managing safety. The airline stresses the importance of transparency among senior leaders and real ownership of operational risk management: this is why, ultimately, the responsibility for the safety plan sits with the leader, rather than the department he or she runs.
CROSS-POLLINATION FOR LEAN SUCCESS
There are definitely lessons to be learned by looking at other industries and at the similarities and differences in how they approach problems. It’s different from going to visit another hospital, in that it takes away the belief that there is only one way of doing things and shows people that the constraints we face are of our own making. (Every lean practitioner working in a healthcare environment has heard, at one point or another, the refrain “people are not cars” uttered in the attempt to reject lean change.)
Beth Israel Deaconess is not unique in looking for best practices in other sectors, but it is certainly one of the healthcare organizations that started to do this early on. This has been hugely beneficial for us over the years – in our industry, we have a pretty collegial approach to improving healthcare because we all know how hard it is – and our relationship with JetBlue is no exception.
THE AUTHORS
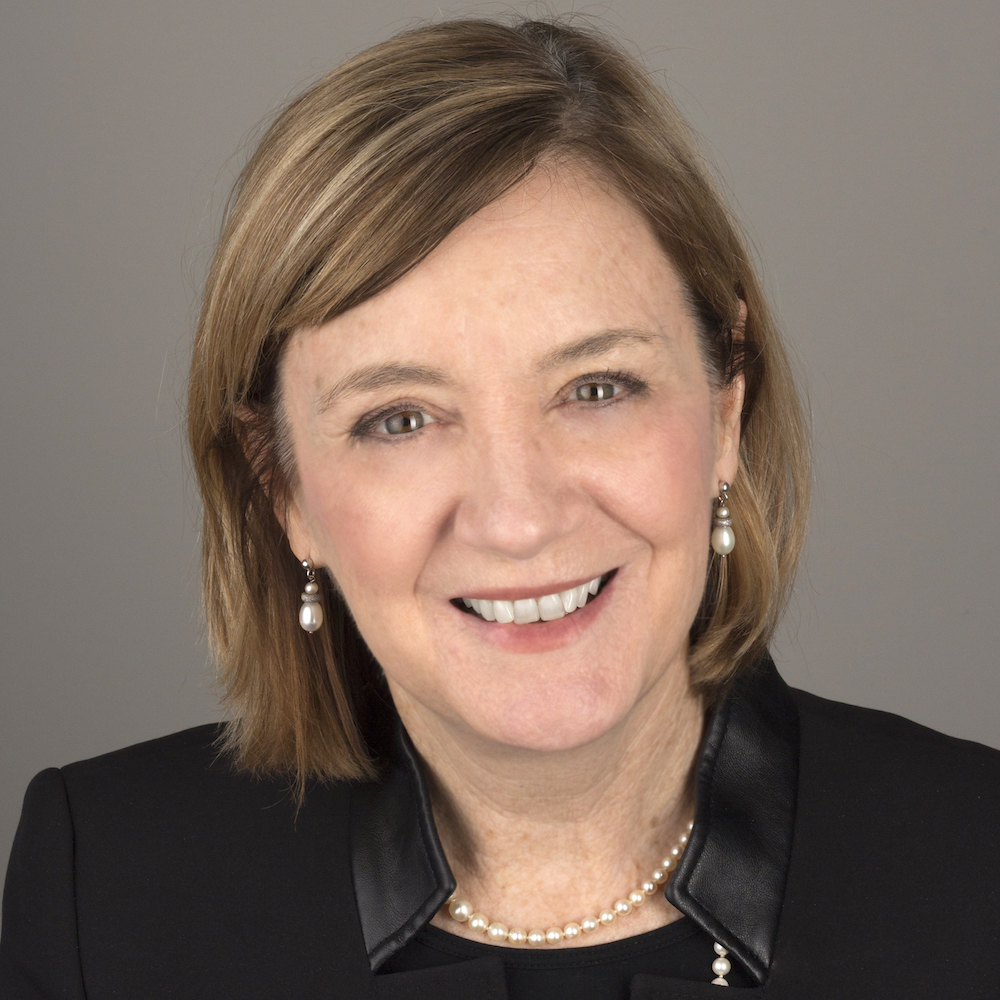
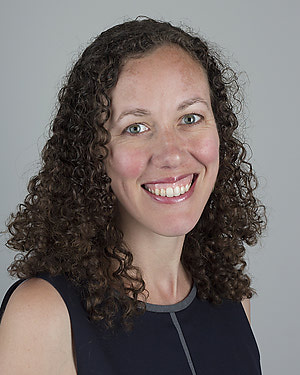
Read more
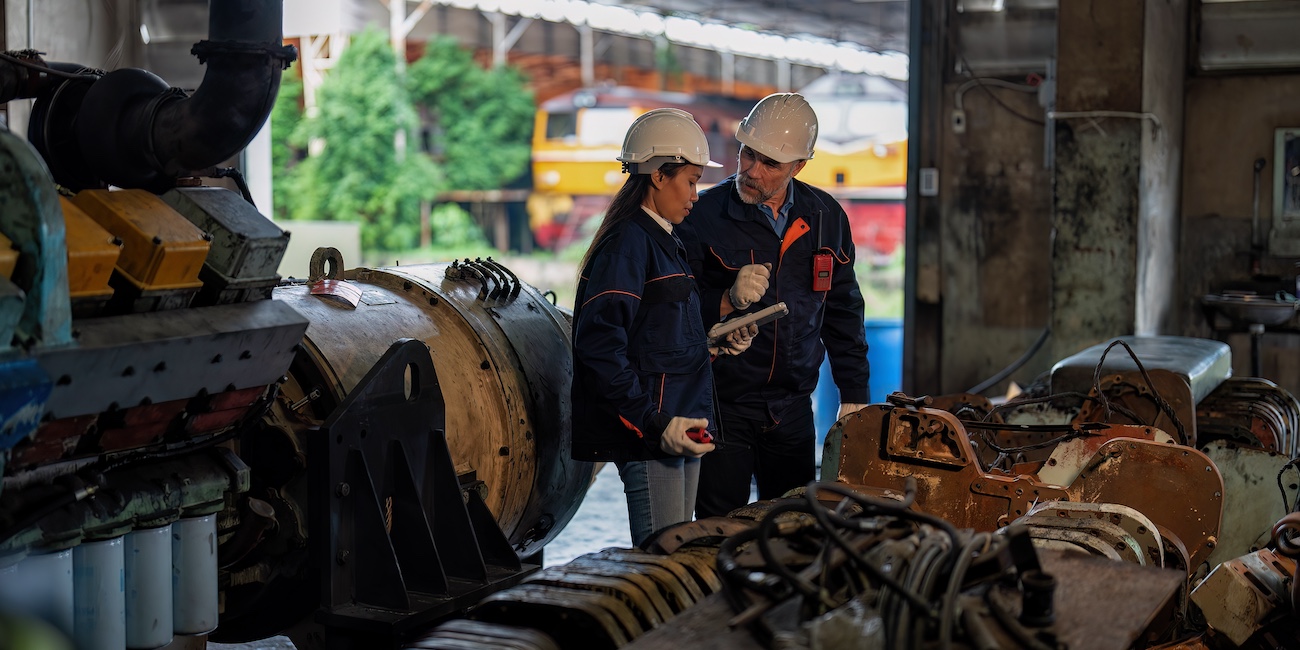
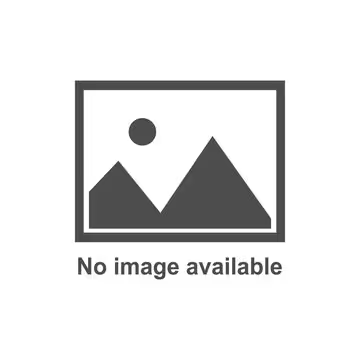
FEATURE – To accelerate learning and change, don’t copy blindly—observe, adapt, and apply with purpose. That’s how yokoten drives real transformation, argues the author.
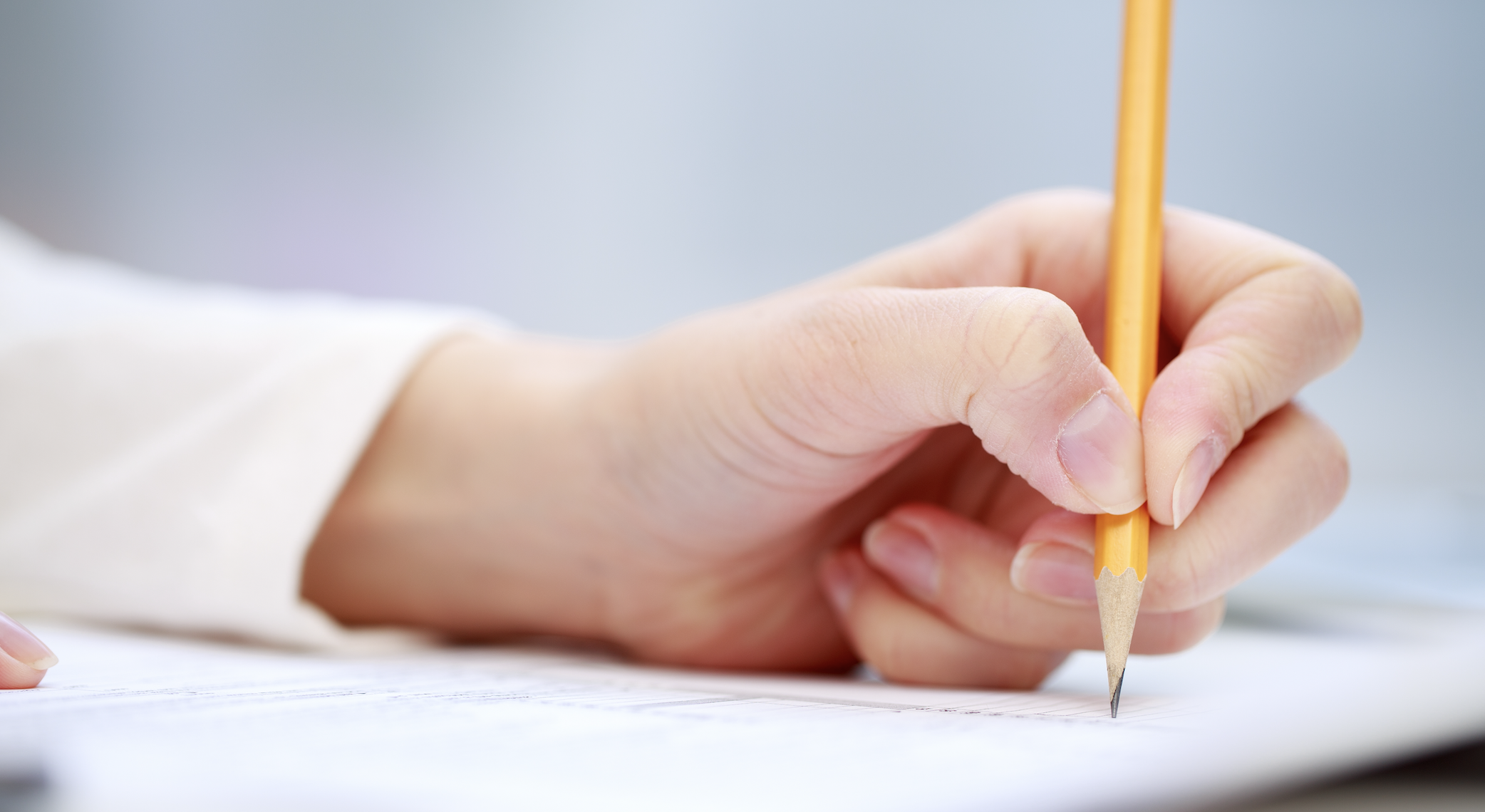
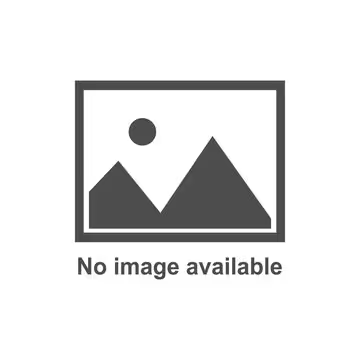
FEATURE – Using her distinctive narrative style, the author breaks down the A3 process to help you understand how it works and how you can tap into its potential.

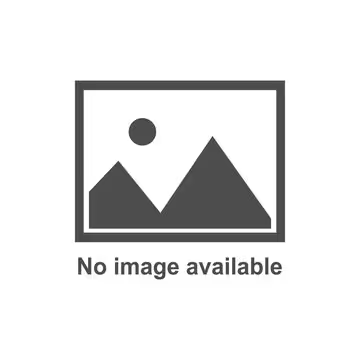
INTERVIEW – “Dr Fred” is an amazing leader, who led one of the most successful lean healthcare transformations this magazine has come across. In this Q&A, he talks to Planet Lean about his new book, which is result of over 15 years of lean learning.
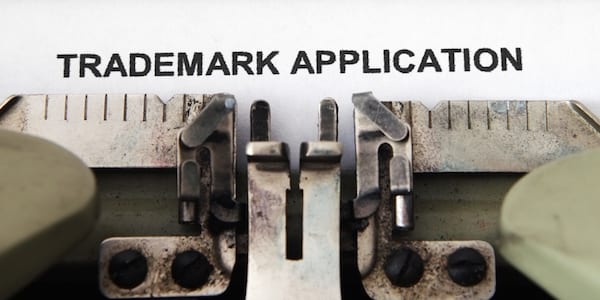
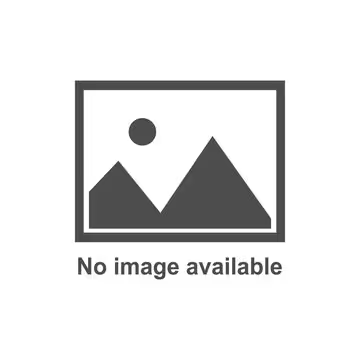
COLUMN – To develop a successful product or service an organization has to effectively manage the tension between the experts' specialization and the entrepreneur's flexible approach to innovation.