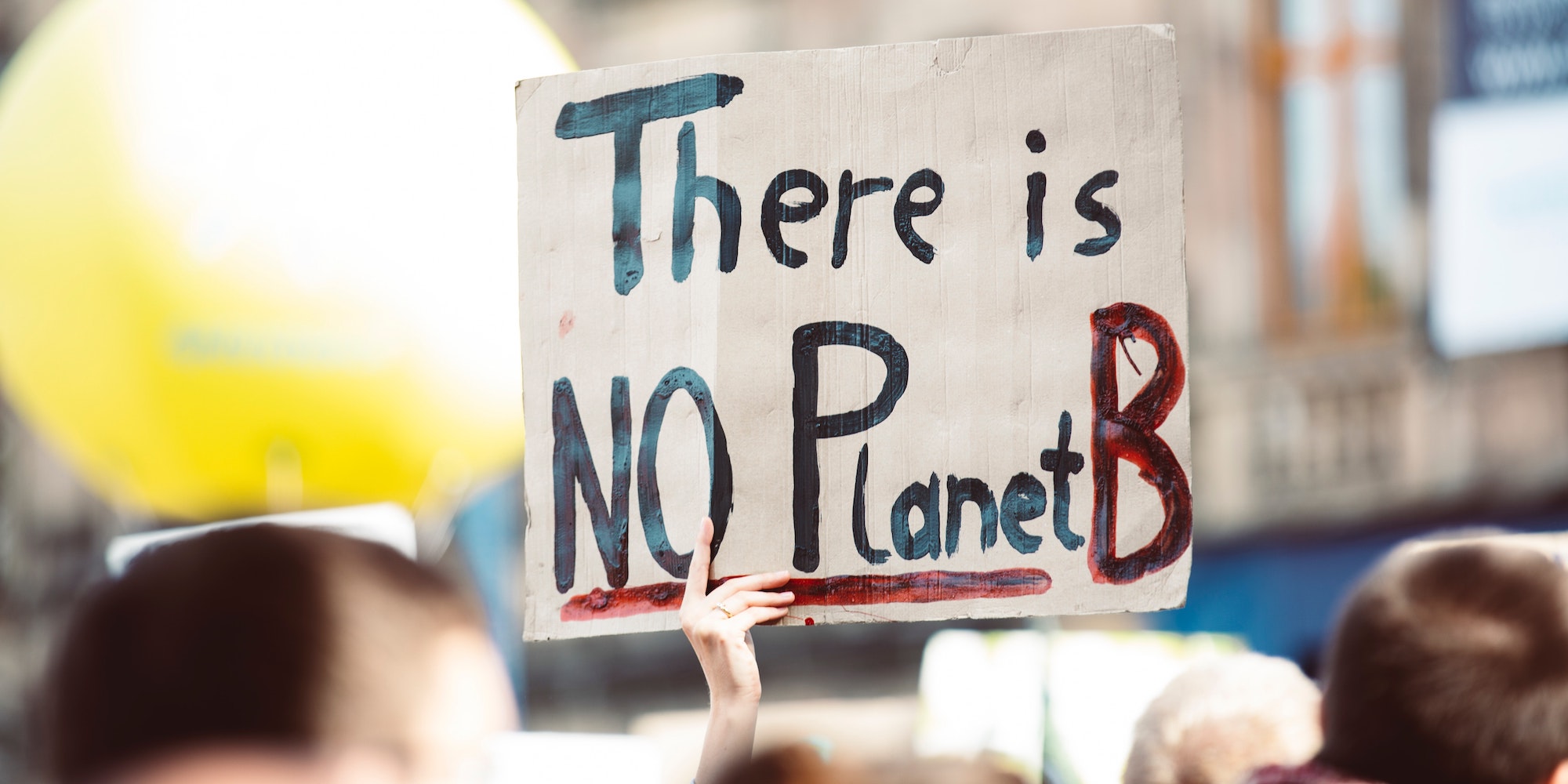
Lean lessons for the climate crisis
FEATURE – Tackling climate change forces us to rethink everything we do as a society. Here’s three lean lessons that can show us a way forward.
Words: Daniel T Jones, co-founder of the Lean Movement
FROM COMPETITIVENESS TO SURVIVAL
We live in very different times than when we first discovered lean over 30 years ago. We are in the midst of a climate crisis that threatens our very existence on this planet, and it is obvious this calls for a very different response than what we have done until now. Indeed, it is no longer about competitiveness, but about survival.
Rising to this crisis means rethinking everything we do – the technologies we use, the products and services we deliver, the energy sources we use, the supply chains we rely upon, the global footprint we produce and the management systems we have in place in our organizations. In the end, it is the decisions and actions by millions of companies and individuals that will determine how we survive this critical decade.
Lean is often perceived as a bottom-up method for increasing competitiveness by eliminating waste, but this is just a fraction of its true potential. So far, Lean Thinking has helped to improve many key processes in large operations of our biggest corporations – which I think of as the legacies of the mass production age. Industry leaders were keen to see step changes in performance, but many of them did not feel challenged enough to change their behaviors to sustain them.
Could the climate crisis force a more fundamental rethink of the way we think and act, unlocking the full potential of Lean Thinking? What lessons can we draw from our experiences with lean that can help us to address the climate emergency? I see three key lessons, which I outline below. But first, let’s summarize the fundamental changes brought about by Lean Thinking over the past three decades.
THE TOYOTA REVOLUTION
The post-war period saw the deployment of specialist knowledge within organizations, in functions and departments and in bigger machines, factories, warehouses etc. Each of these activities was “managed by the numbers” and by control systems (such as MRP, ERP and SAP) to optimize their use, keeping every activity busy. Likewise, each department developing new products handed off their work to the next department, and so on until launch. Strategy, therefore, focused on securing dominant positions in markets through branding and marketing. Externalities were the responsibility of governments and supply chains spun spiders’ webs across the world to take advantage of cheap transport and low-wage locations, including China. The vast amount of waste and lack of flexibility in these systems were largely ignored.
Over 30 years ago, Toyota showed the world how to go beyond this – to double productivity, eliminate quality defects, and design new products in half the time. On the one hand, they did so by integrating production activities into value streams and synchronizing these value streams with the needs of users. Making complicated integrated systems work depends on every step always being fully capable of completing the task and of responding quickly to interruptions or slippages. It also depends on being able to work to the pull of demand from users, rather than from a chain of forecasts that amplify the signal upstream. And on a shared commitment to collaborate to solve problems at one point that deliver benefits elsewhere in the system.
On the other hand, Toyota also integrated its development activities into a continuous process, designing new products at a regular cadence. Each product family is led by a powerful Chief Engineer, tasked with examining changing user needs, technology options and experiences from production to define the problems to be addressed in this generation product and the next. The Chief Engineer also articulates the resources required by the team to solve those problems and regularly reviews progress with the team in a visual project room or Obeya. Instead of jumping to solutions, the team explores alternative technical solutions simultaneously, so that the resulting design can then rapidly progress to launch. At each stage, learning is reviewed and captured for future use. Inspired by Toyota’s example, software development has gone through a similar progression, from Agile to Scrum and DevOps, with continuous improvement of modular design and testing enabling them to move from six monthly to daily releases.
LEARNING BY PROBLEM SOLVING
The first very important lesson we can draw from lean as we figure out the best way to address climate change is that integrated systems only work if all employees are engaged in stabilizing their work, responding to interruptions, and using scientific problem solving to make detailed improvements to the system. While routine steps can be automated, human decision-making is indispensable, particularly in unstable and rapidly changing times. Cumulative problem solving builds the capabilities to cope with changes, more complex tasks, and new challenges. This is a crucial input, together with feedback from users, in designing next-generation products and processes and rapidly scaling up new technologies through successive iterations.
Developing these capabilities through “learning by problem solving” does not just happen. It needs to be part of a structured improvement process in which team leaders and managers at every level are responsible for developing the capabilities of their subordinates, supported by a network of sensei (teachers) guiding learners – including senior executives – by asking questions and helping them to reflect on the lessons learned from each problem-solving cycle. This commitment to learning and personal development creates a culture of “Respect for People” and ownership instead of treating employees as disposable assets. How well these capabilities are mobilized will be a testament to how seriously leaders view the climate crisis.
SEEING THE WHOLE
The second lesson is the importance of seeing the performance and impact of the whole system and of the extended value stream with its main tributaries. I have helped executive teams to visualize their operations as a system of inter-connected processes. I have also “walked” many extended supply chains across the world and found the scale economies and labor cost advantages are more than offset by the gains from synchronization and co-development. For example, the parts for an automotive system made in 14 different plants in China, Japan, Brazil, and Europe took up to 630 days to reach a customer in the USA. The next-generation product was made with right-sized tools in process sequence in nine plants within trucking distance of the customer, reducing lead-time to 37 days and eliminating both shipping and expediting air freight.
Proximity is not enough, but it enables supply chain partners who commit to building the capabilities to continuously improve the synchronization of their joint operations. The purpose of “Just-in-Time” is to reveal the next problems for the teams to work on, rather than optimizing long-distance logistics, as is often erroneously reported. The climate crisis presents the opportunity to rethink the logic of location and to build dynamic supply complexes in each region. This also raises questions about the approach that will prevail in the future – whether centralizing production in large plants or distributing it in right-sized plants closer to customers. Seeing the whole system is also key to understanding its impact on the environment, and on the circular economy from recycling to reuse.
DECISION-MAKING USING SCIENCE
The third lesson is that the scientific method is the essential ingredient in managing integrated systems and “learning by problem solving”. Deming distilled the scientific method in his Plan Do Check Act (PDCA) problem solving cycle. Over time, Eiji Toyoda operationalized this into a complete business system. PDCA is the common language for making and executing decisions at every level, from strategy formulation and making big leaps to detailed incremental improvements. It is embedded in a performance management system tracking value stream progress, stability and capabilities, in the visualization of “planned” versus “actual” everywhere, in visual rooms for managing projects and strategic decision-making (Obeya), in a framework for planning and carrying out experiments to find solutions that work (A3), in a catch-ball dialogue up and down the organization aligning corporate performance gaps with proposed actions to close them (Hoshin), and in “chains of help” to escalate and remove obstacles to improvement.
This scientific approach also drives the strategic process for finding and defining which high-level problems the organization needs to focus on. This is particularly important during times of profound change, facing new problems that we don’t yet know how to solve, like surviving the climate crisis. This starts with what Toyota calls “problem awareness”, finding the right questions to be answered through detailed observation of the current situation and technical possibilities. These problems are then broken down into manageable pieces, establishing a measurement system for tracking progress and facing up to addressing them. Each problem is framed as a gap to be closed and proposals for doing so are solicited through the Hoshin catch-ball dialogue before many different experiments are conducted to discover what works and what does not. Finally, the knowledge gained is captured and shared with teams across the business.
This high-level problem-finding process is key to making the problem-solving architecture work and to harnessing the creative power of the organization. It is a challenge to leaders used to deciding on solutions, drawing up plans to hand over to experts to deploy across the business and then deal with the unintended consequences. This traditional approach to management stifles learning and inevitably leads to resistance to change and the protection of existing assets and markets. Conversely, a lean approach to strategy and learning provides a promising way of addressing the challenges of the climate crisis.
Science has been central in understanding what is happening to the global climate system and scientific thinking will be critical in responding to it, and to our survival. New technologies will be important, but so will our ability to scale them up fast enough and integrate them into our lives. Learning to use scientific problem solving at work will also give millions a direct experience of the importance of scientific thinking. This democratization of science might be one of the lasting legacies of Lean Thinking.
THE AUTHOR
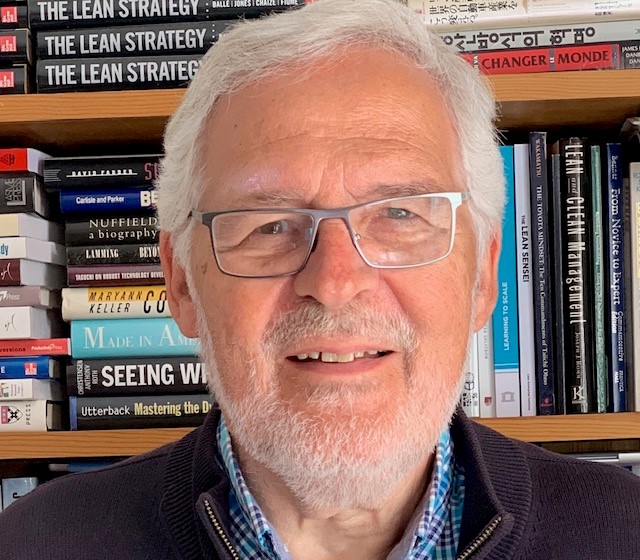
Read more
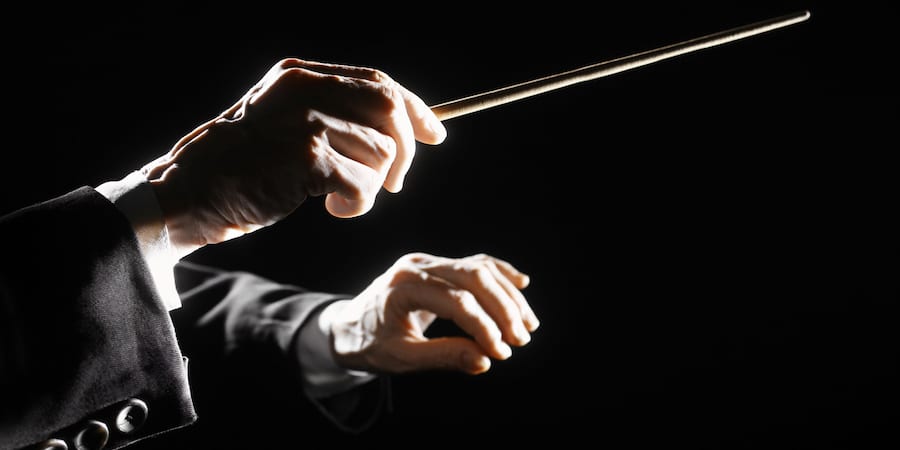
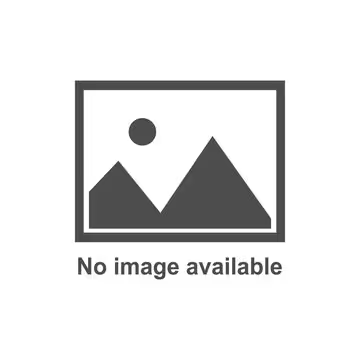
FEATURE – Do CEOs see lean as a strategy? The author – himself a CEO for many years – debunks the misconceptions often preventing senior leaders from doing so.
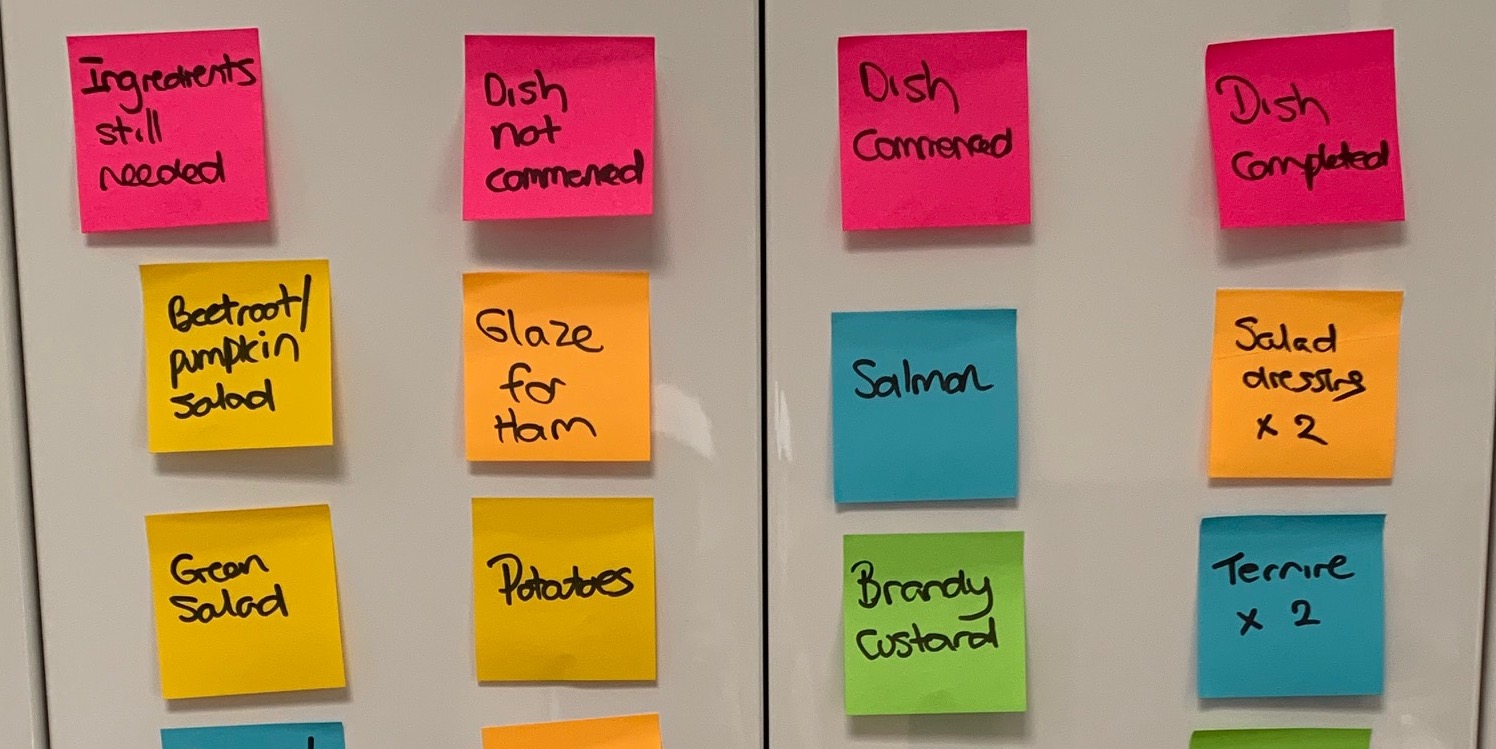
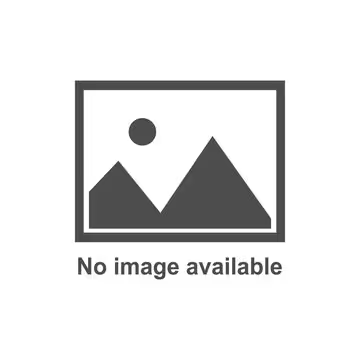
FEATURE – The holidays are a time for reflection. The author shares some her reflections on her experience with lean thinking and the role of leadership in a lean transformation.
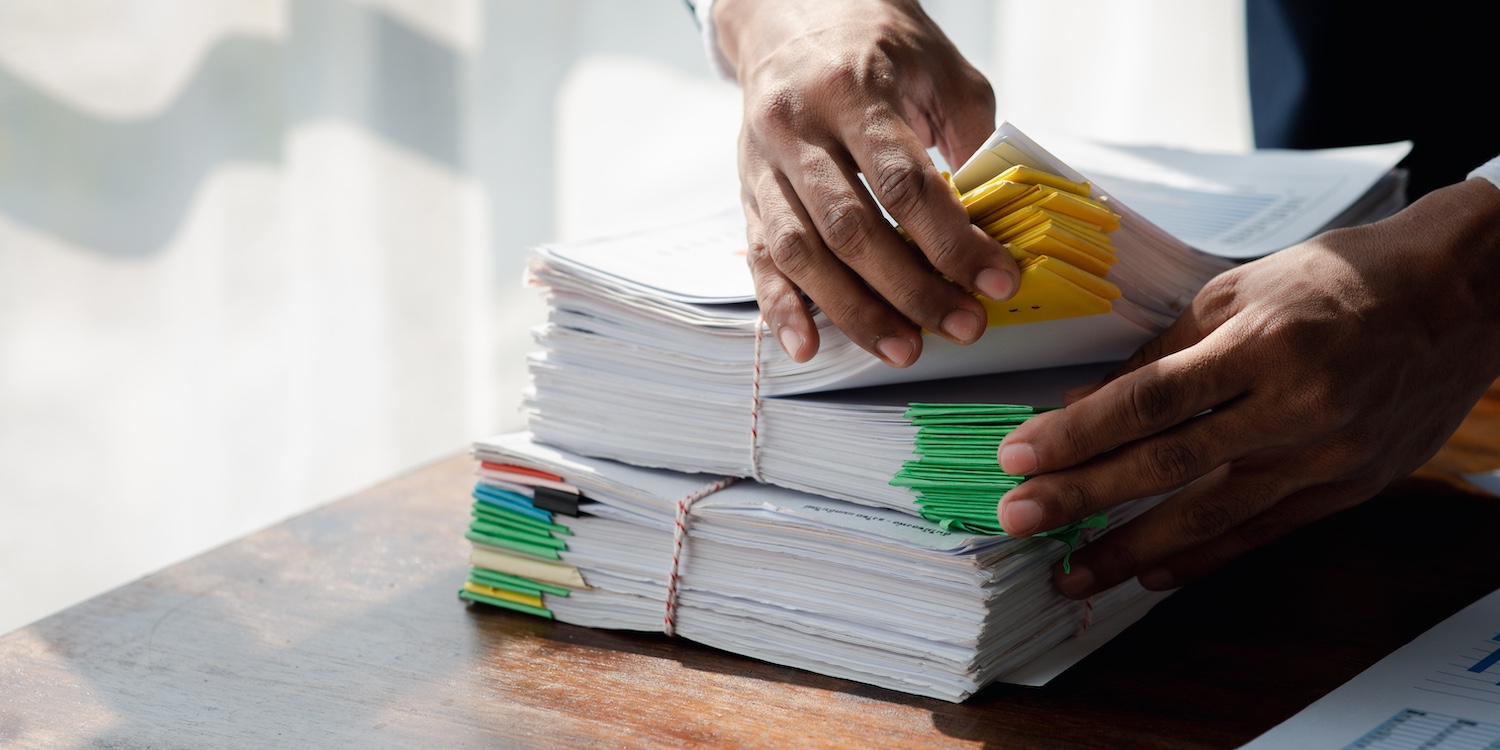
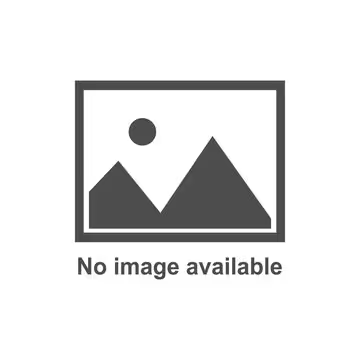
CASE STUDY – UK law firm Weightmans has transformed its new legal case intake process using the Lean Transformation Framework, revolutionizing both operations and people development.
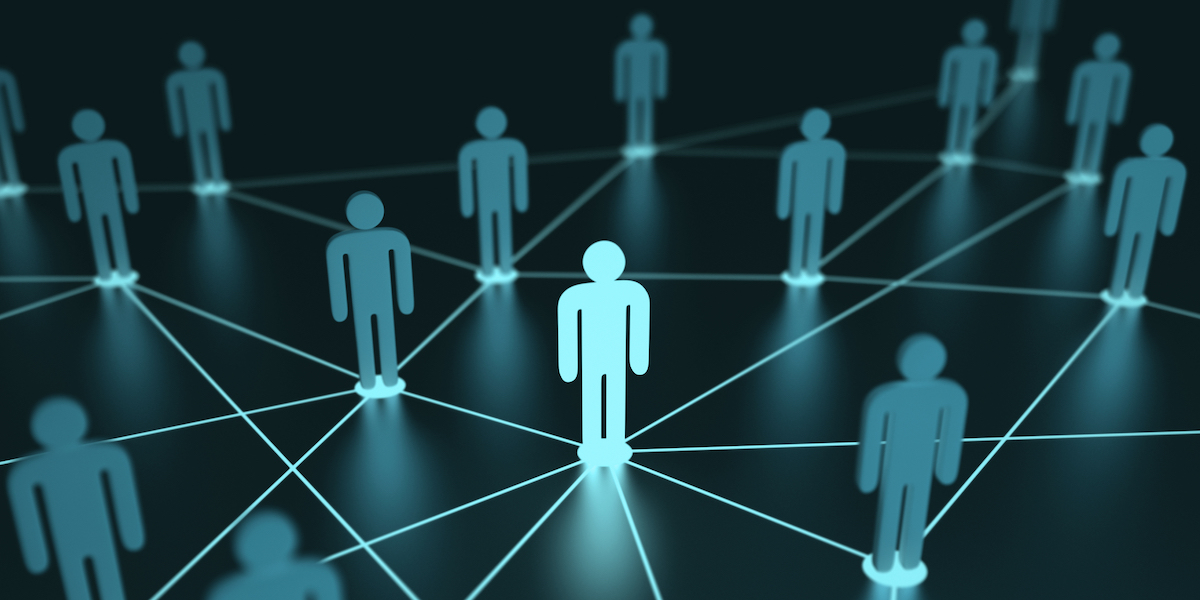
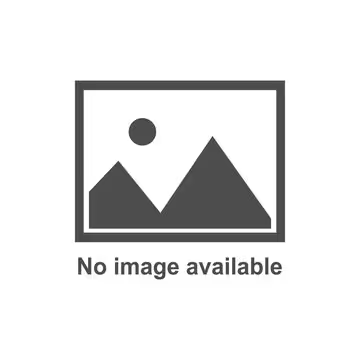
FEATURE – We tend to describe lean as a holistic approach to a transformation, but we won’t be able to truly embrace it until everyone starts to see the organization as a system.