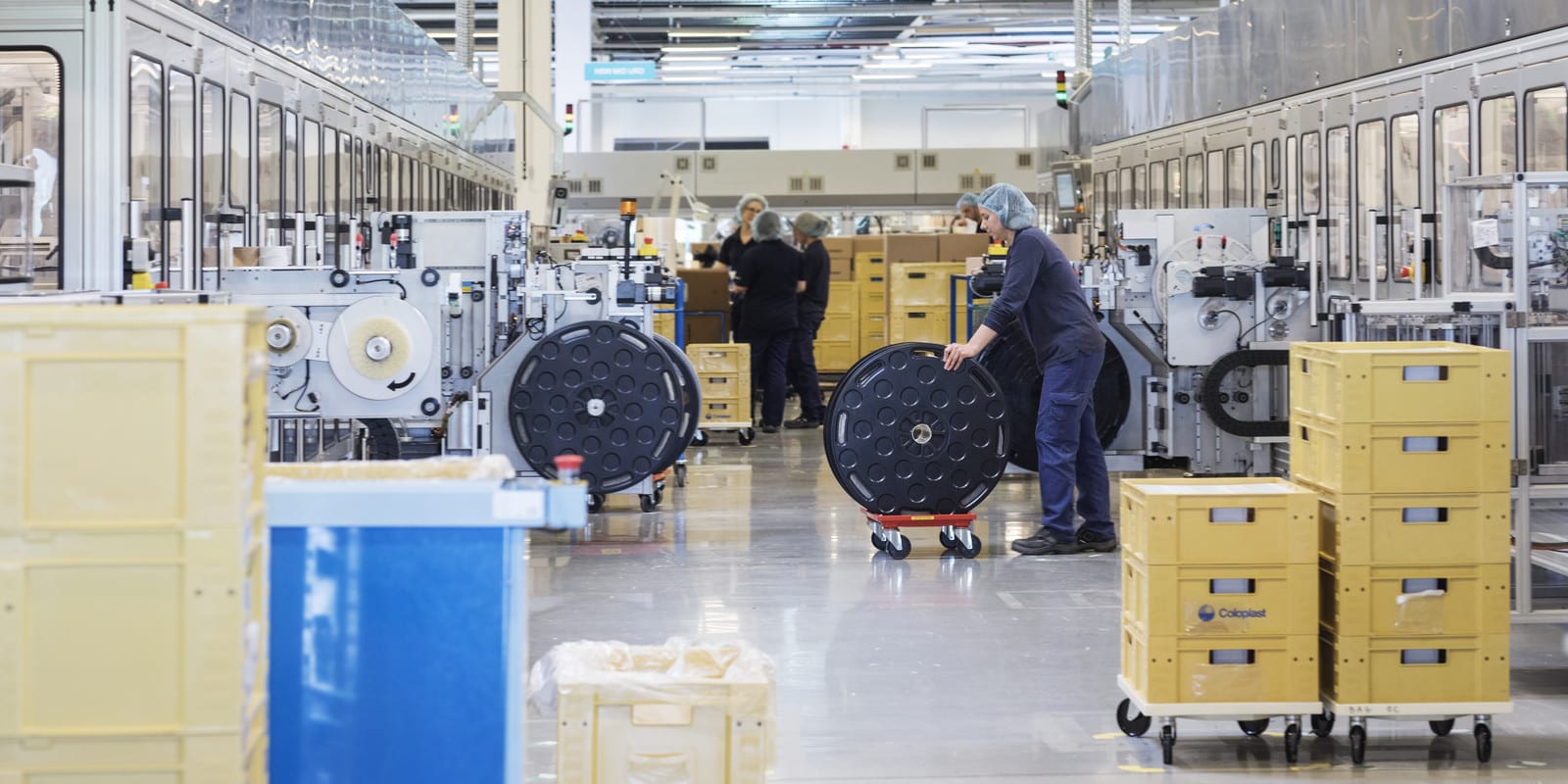
Keeping the spirit of care alive
CASE STUDY – The author looks back at the impressive lean transformation of the Hungarian plant of Coloplast, a Danish company offering medical devices and services.
Words: Péter Szarka, Plant Manager, Coloplast – Tatabanya, Hungary
In the spring of 1954, Thora Sørensen was diagnosed with cancer. She was 32. Her colostomy was successful, but the aftermath proved particularly hard to deal with. Without support or the proper equipment, she had to learn to live with the smell, the discomfort and the constant fear of leakage that colostomy patients coped with back then.
But Thora’s sister Elise, a visiting nurse, had other plans. Tired of seeing Thora struggle so much, Elise thought of an alternative use of the newly-invented plastic bag – a simple, disposable and practical item: making it stick to her sister’s skin, she thought, would prevent the stoma from leaking. Elise experimented until she found a way, realizing the potential for this invention was huge. There were many people in Thora’s situation (both in Denmark and abroad) whose lives the colostomy bag could change.
Once she found a manufacturer willing to produce the bag, Elise Sørensen’s idea took flight. Coloplast was born.
To this day, Elise Sørensen inspires us, shaping the way we think about our customers and our employees. As a medtech company with a long history, we are fully aware of the fact that ostomy care products are a very personal thing. They represent a basic need, and we must never forget that: without our products, many of our customers wouldn’t even leave their houses. We allow them to have a normal life, and that’s why we feel such a strong sense of responsibility.
Our commitment to customers goes back to the days of Elise Sørensen, but it is in the last fourteen years or so that we have begun to leverage lean thinking to fulfil our mission. I remember when I was hired at the Coloplast plant here in Tatabanya in 2003: back then, the company was launching a lean initiative promoted by the Danish HQ and was therefore looking for the capabilities that could support it (I came from automotive). The reason behind the decision to adopt lean thinking was not a crisis, but a genuine desire of top management to improve the organization. We were lucky we could take our time to learn lean well.
As it often happens, the first step our leaders in the HQ took was hiring a consulting firm. Their main focus seemed to be on running as many improvement events as possible, without really worrying much about the quality of those events (their KPI was the number of lean events run against the number of employees – with 500 workers, you had to have 50 five-day Rapid Improvement Events a year). It didn’t take us long to realize this wasn’t the right way. After this false start, we in Tatabánya tried again in 2005 with a new consultancy – Szabolcs Molnar’s old company – and a new plan.
THE MILESTONES IN OUR JOURNEY
First of all, we had to organize the training of hundreds of people to give them an idea of what lean is. We scheduled one-day training sessions for operators and three-day training sessions for leaders, and we began with our first lean experiments immediately after.
We started to work with 5S (adding a sixth “S” for Safety) and to optimize our processes. We looked at how we could change quickly from one product to another on our machines, and at how we could use kanban cards or supermarkets for raw material replenishment.
In 2007, our sister plant in Nyírbátor opened, becoming fully operational the year after. (Together, the two sites employ 4,000 people.) To bring lean thinking to the new plant and to harmonize our most basic improvement activities, the Tatabanya site was appointed as a Key Competency Center for Hungary: we documented a number of cases on why problems were solved a certain way and we created manuals on techniques like SMED or kanban.
Interestingly, at the time we had a Lean Department, led by a Lean Manager and with a Lean Specialists. Later on, however, we decided to embed lean capabilities into the process itself by placing our lean specialists under production managers and directors. Moving from external to built-in expertise was a pivotal moment for us: it was the only way for us to ensure all low- and middle-level managers would be able to switch on their “lean view” whenever necessary.
Our approach to developing the capabilities of our people starts with their onboarding, during which five hours in their three-day training sessions are devoted to lean training. We want lean to be taught from the very beginning. We know, however, that lean can only be learned on the job, which is why we ask our Lean Specialists to meet with people regularly and involve them in the improvement work.
This is typically when our Specialists encounter some resistance. If explaining to people how they will benefit from the changes is not enough, area managers are asked to get involved to encourage them to get onboard. This was a key lesson for us: leadership support at different levels is absolutely critical.
One of the most important steps in our lean journey was the introduction of the TWI (Training Within Industry) methodology around two years ago. The need for a new approach had become particularly pressing, as we realized that the skills level of new employees didn’t match that of older operators. This meant that, in order to become more efficient, we had to spend more time training people and find faster ways to teach them how to operate complex machinery.
So, around one year ago we started to run a series of TWI workshops organized by LEI Hungary. Even top management participated, which is probably one of the reasons why the impact of TWI on the work was so great. Before TWI, whenever an operator checked a product but wasn't 100% sure of what sort of defect she was had to look out for, she simply chucked the product. They didn’t think they were doing anything wrong, and indeed they weren’t doing anything more than work the only way they knew how. Once we introduced a clear standard (breaking down the process steps and introducing visual checks), thus enabling operators to make informed decisions on quality, our scrap rate went down.
The most significant lean project we undertook was a substantial layout change in our factory. When Coloplast started production in Hungary, it transferred machines from Denmark. All we did was learning to use them and starting producing. Over time, this created a situation whereby we had a number of “sub-factories” that were producing different sub-assemblies that came together at the end. We decided to rearrange the machines, moving them right next to the final product assembly line. Doing so, we saved 2,000 square meters and reduced intermediate stock levels in the factory.
This is also when we introduced Kanban cards between the sub-assembly machines and the machine producing the finished good and we learned to do quick changeovers using SMED. Looking back, there is no doubt that changing the layout to enable flow was by far the biggest change we ever implemented at Tatabanya. Thanks to this, we were able to simplify the process, we implemented flow, we reduced stock in the warehouse and movement around the factory. The work is now visible, and seeing how much stock there is in our process is easier than ever before.
THE MOST IMPORTANT LESSONS WE LEARNED
We believe it is our commitment to continuously improving ourselves that will help us build on what we have achieved so far and meet our future challenges (starting with our increasing costs, which makes it necessary to increase our productivity by 3% each year).
One thing that has become evident is that we are great at trying new things, but not yet at sustaining our results. That’s definitely the hardest part. There is always something happening after an improvement is completed that distracts us and overrides our ability to sustain a result, which forces us to constantly go back to reinforce the message and bring the process back to standard. This happens at every level: every time you move a machine, things slide, so imagine when we moved 46 in the 21 months following our move to the new factory. We invest a lot of time in supporting operators over time and ensure their work sticks to the standard.
We have also realized that other parts of the business could benefit from more standardization. One example is maintenance (very important at Coloplast, as we run a highly automated process), and we are curious to see what the lessons learned are in the pilot area that is adopting a structured approach to it – TPM.
At a time when the debate on automation rages on, our story is proof that maintaining the dignity of human labor in an environment full of machines is possible. We have learned that so far as technology benefits people, they won’t have a problem with it. In fact, our experience with automation is quite good so far. Here’s an example: we have recently implemented a new packing machine that takes the tiring job of visually checking and packing 30 pieces per minute away from them. What the operator is expected to do now is to inspect the machine, not to perform a repetitive and draining task. (As we continue to automate, we will need 40 to 60 operators less than we currently do, but because we are a growing production operation there will be plenty for them to do. We don’t lay people off!)
Naturally, our commitment to people includes our customers. Just like Elise Sørensen was a visiting nurse who cherished the dialogue she had with her patients, we at Coloplast make an effort to talk to our clients as often as we can. That’s when we ask them how they lead their lives, how they use our products, how they cope with their condition, and so on. It is this ongoing interaction with users – another lean idea – that has enabled us to incrementally improve our products over time. Our bags have changed a lot over the years (even though if you put different generations on a table in front of you, you would struggle to see any differences): from the materials we use to filter capacity, from the way that the bag keeps in the odor to how the sticky part can now adhere to any body type, innovation of Coloplast products has been steady. We have learned that lean supports our ability to innovate, which is why we have now started to facilitate a closer collaboration between our R&D and production departments. We are embracing the Design for Manufacturing principles.
Lean thinking infuses everything we do with the same humanity and care for people’s wellbeing that led Elise Sørensen to come up with the colostomy bag concept.
This article is also available in Hungarian here.
THE AUTHOR
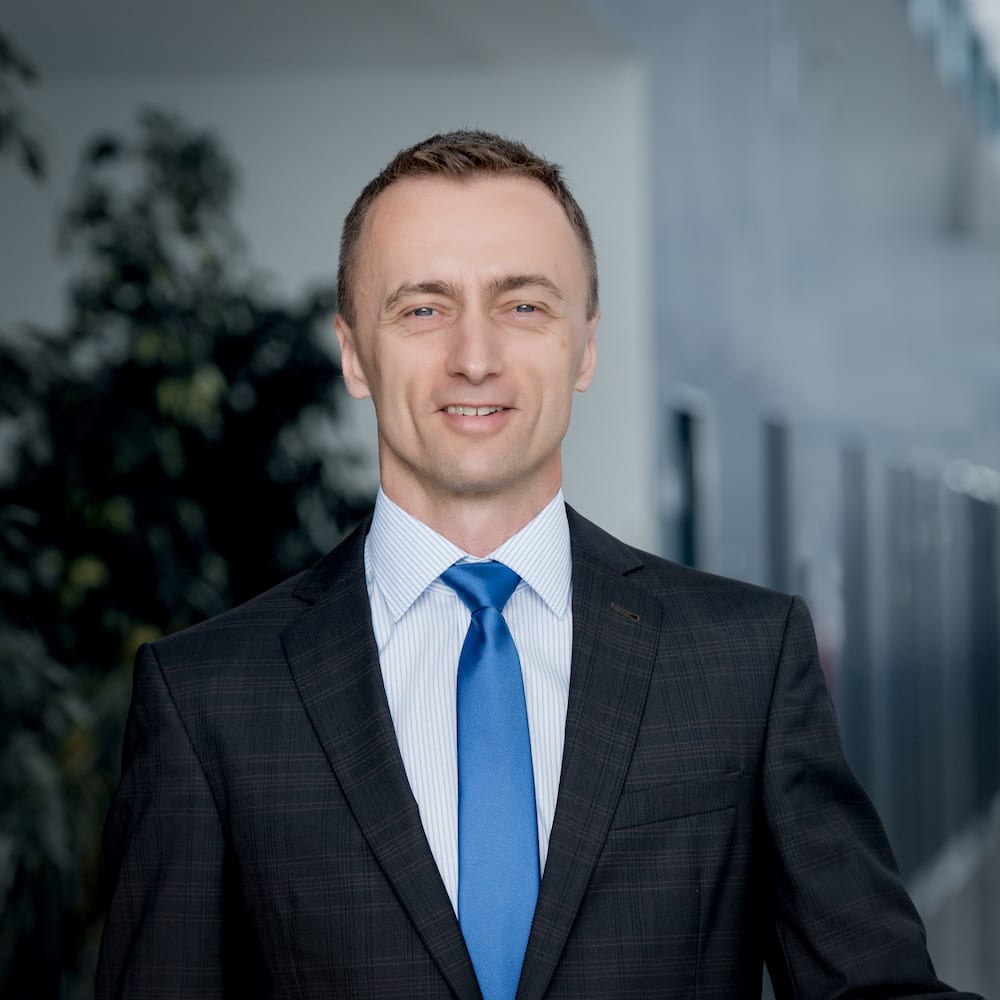
Read more
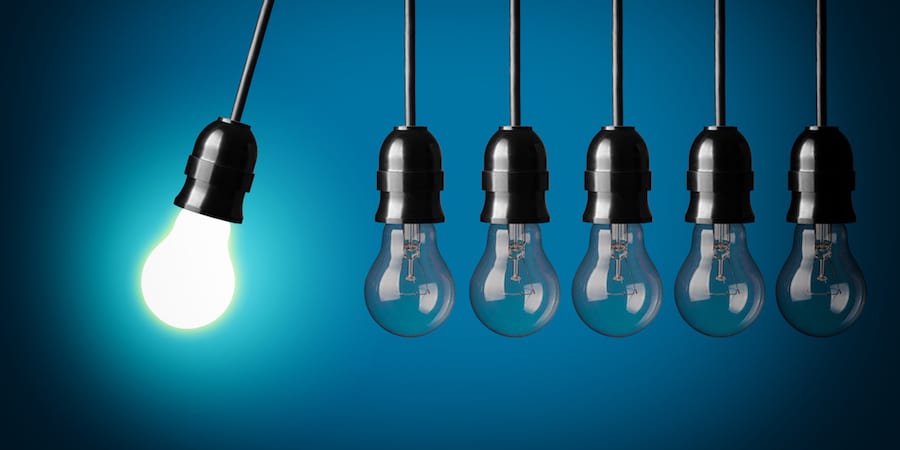
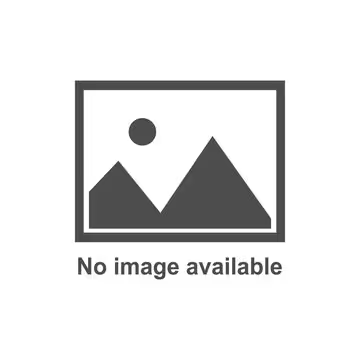
FEATURE – For this new monthly article, we will be asking five lean practitioners the same question and share their answers with you. We started by asking them about their biggest lean mistake.
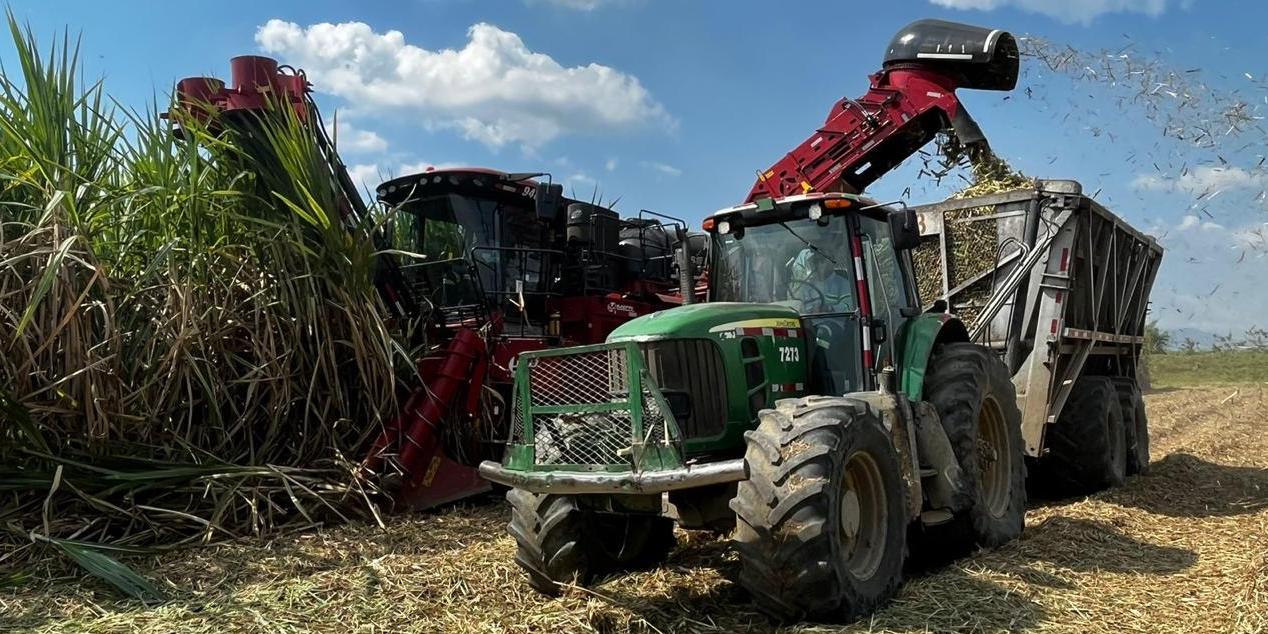
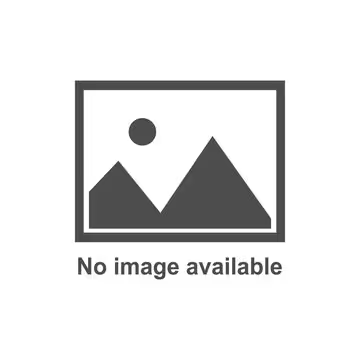
CASE STUDY – Manuelita Sugar Mill in Colombia adopted Daily Management to bolster leadership effectiveness and operational outcomes, addressing siloed thinking and communication challenges.
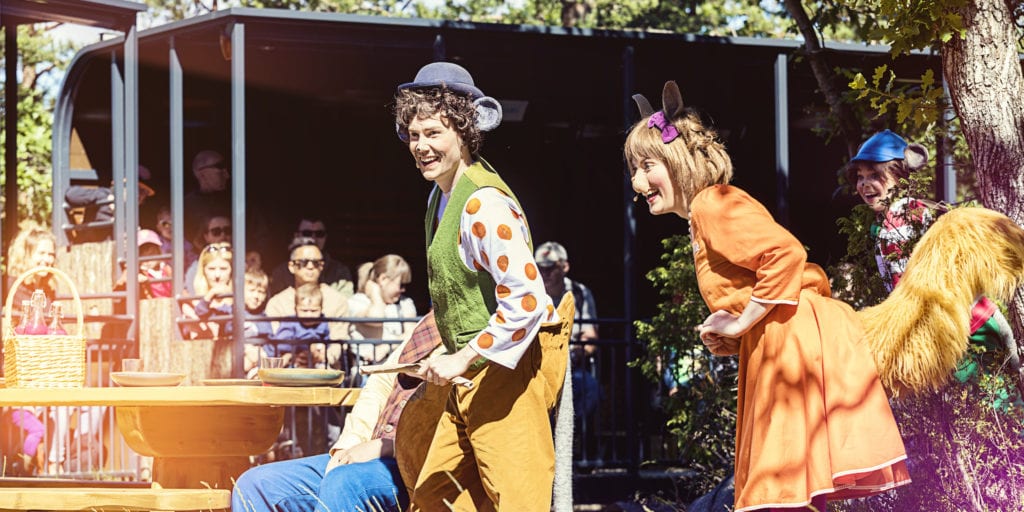
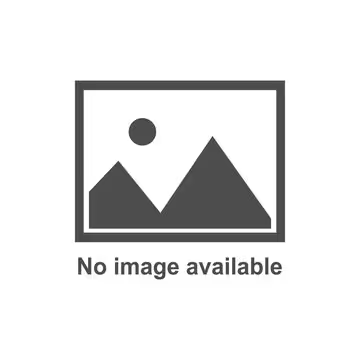
FEATURE – How an amusement park in Norway is using lean visual management to support actors during their busy schedule and to give visitors an experience they will never forget.
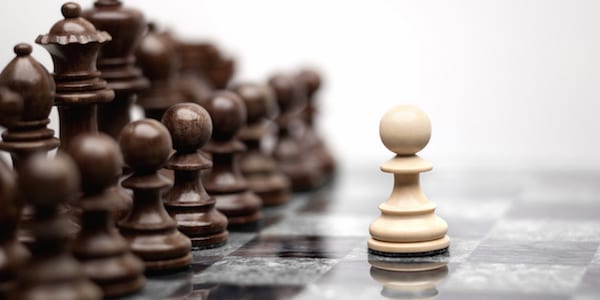
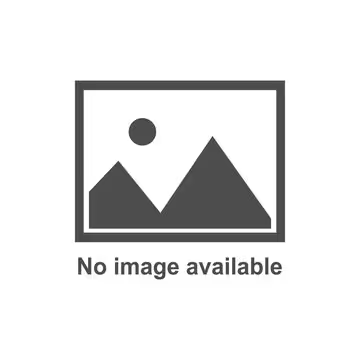
INTERVIEW – During a chat with Planet Lean, Darril Wilburn explains why courage and humility are necessary elements to establish a culture based on continuous improvement.