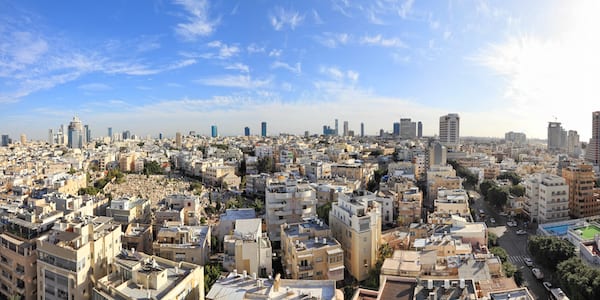
Josh Howell of LEI reports on his visit to Tel Aviv
OPINION – Lean Global Network institutes regularly collaborate on education. Josh Howell of Lean Enterprise Institute recently visited our Israeli affiliate to deliver a couple of workshops.
By: Joshua Howell, Senior Coach, Lean Enterprise Institute
After spending the holiday break with my family in Indiana, three flights brought me to Tel Aviv. Admittedly, as this was my first visit to Israel, I had some anxiety about it all. This was the result of seeing many, many overly sensationalized stories in the media and being very, very far away from the real situation, the gemba (hmmm, sounds familiar...) But I arrived safely and travelled to Zikhron Ya'Akov, a sleepy town near Haifa where Boaz Tamir, President of Israel Lean Enterprise, lives and has located the institute (an affiliate of Lean Global Network).
On my first day, I visited the institute, finished preparing for the two workshops I would facilitate over the coming days, and got to better know Boaz and the rest of the team - training expert Naomi Steinitz and lean expert Shlomo Migdal. This time included good conversation about how LEI, mostly through our co-learning projects, is experimenting with using the Lean Transformation Model.
On day two, after a good night's sleep, I facilitated a version of LEI's Lean Transformation Model workshop. I have helped develop this workshop, along with John Shook and Darlene Dumont, yet this was my first time facilitating it on my own. And once again, using an experience from my time at Starbucks as a "case study" to illustrate how the model can be applied worked very well. Participants were very engaged with the story, asked great questions, challenged the approach and thought about its lessons relative to their own unique situations. With good reflection came good learning, and I look forward to running the workshop again soon.
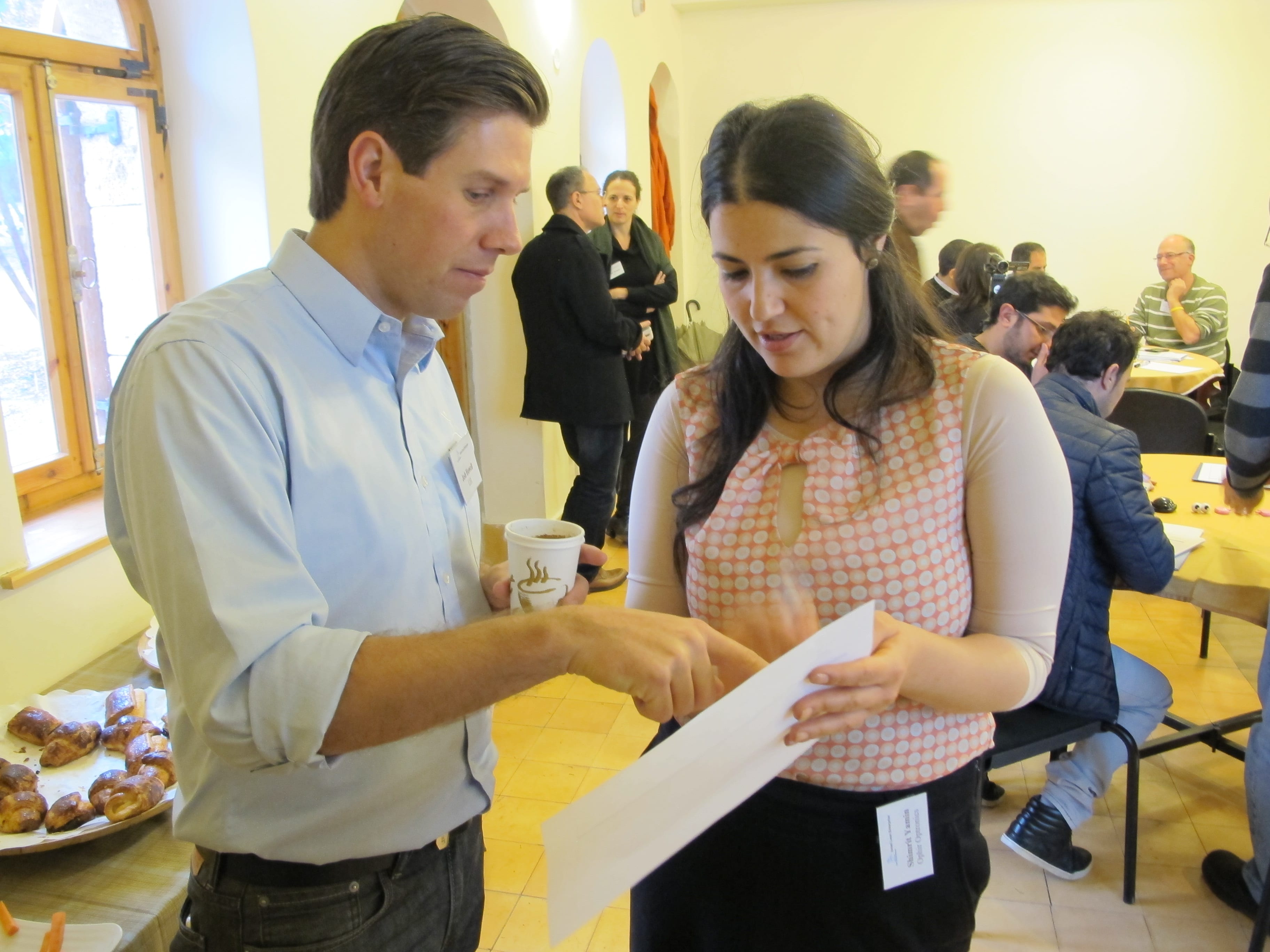
For a workshop on day three, I brought out Mr Potato Head. This workshop, titled Manager as Coach: Start with the Work, took the group through what I would describe as a full improvement and coaching cycle. We started by watching different ways to assemble the toy, with different outputs. Understanding the customer's requirements, and the need to improve (relative to takt time), led us to observe the work in greater detail using a Process Timing Sheet and by creating a "work story." After making some initial improvements, we created a "routine" that could be trained. This, of course, especially for those who know my practice, led to a lesson on TWI's Job Instruction. Lastly, I introduced a slight variation on Job Methods' improvement technique (ERACS = Eliminate, Rearrange, Add/Subtract, Combine, Simplify), which starts by questioning every detail of the routine. This process, I suggested, touches on all aspects of what it is like to be a lean coach - assessing the problem, assessing the learner, giving instruction, and offering open counsel.
Day four brought me back to Tel Aviv.
Boaz and I visited one of the three major cellular companies in the country, which has been struggling since the industry was deregulated several years ago (losing market share quite rapidly, especially to more nimble start-ups). After a successful "pilot" project led by Shlomo, helping to increase the conversion rate of cellular towers to LTE technology, Boaz is encouraging top management to consider a more complete transformation, starting with asking, "What is our value-creating purpose as an organization?"
I shared a case study with their top management, which touched on each dimension of the Lean Transformation Model - starting with the company's purpose, then taking a situational problem to solve, defining and understanding how to improve the work, learning how to build organizational and individual capabilities, clarifying the needed elements of a management system for achieving the change, and lastly, a discussion of the underlying principles that guided the effort. They seemed interested. Only time will tell...
Another activity I would like to mention, other than experiencing Israel's security apparatus when preparing to leave the country (a story for another time), is the visit to a simulation center Israel Lean Enterprise is using. Here, individuals enter into a scenario with an actor in order to practice some skills. In my case, I was practicing a "coaching kata" the institute has been developing. The simulation experience includes observations by colleagues and/or managers through a two-way mirror, video taping of your behavior, feedback from an experienced teacher and practitioner (Naomi) and a fact-based reflection afterwards. Honestly, I entered into this with some apprehension but ended up really enjoying the experience. I found the exercise to be quite valuable, especially reviewing the video footage. As Naomi says, "How do dancers improve? They practice in front of a mirror. For us as coaches, the video can be our mirror." Good point.
My visit to Israel was an amazing experience all around. My one regret, I suppose, is not having set aside any time to tour the country. Indeed, what little I saw and those I met were chock-full of character and offered much to learn for a young man born in the Midwest.
THE AUTHOR
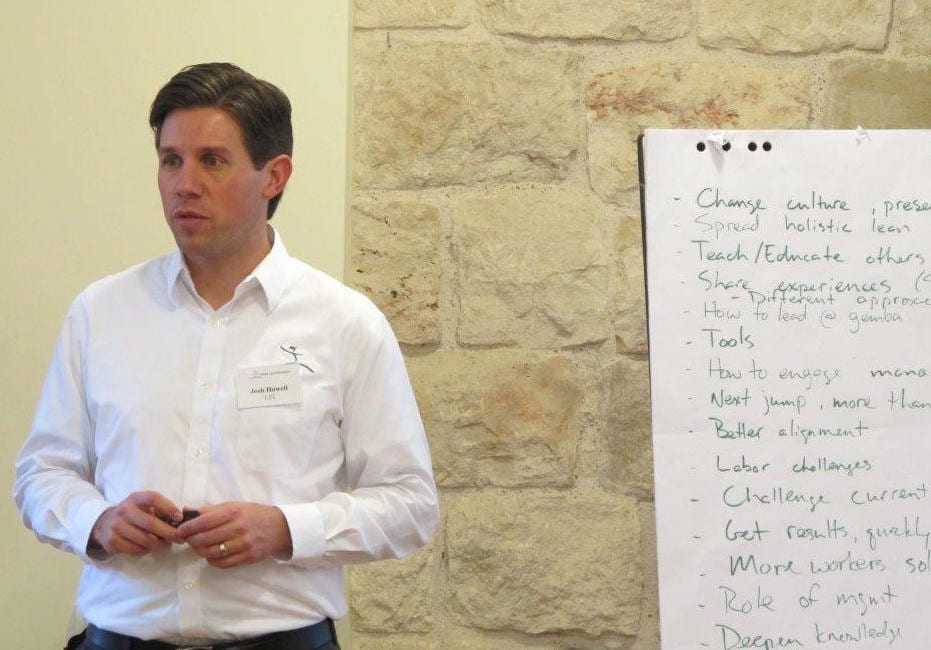
Read more
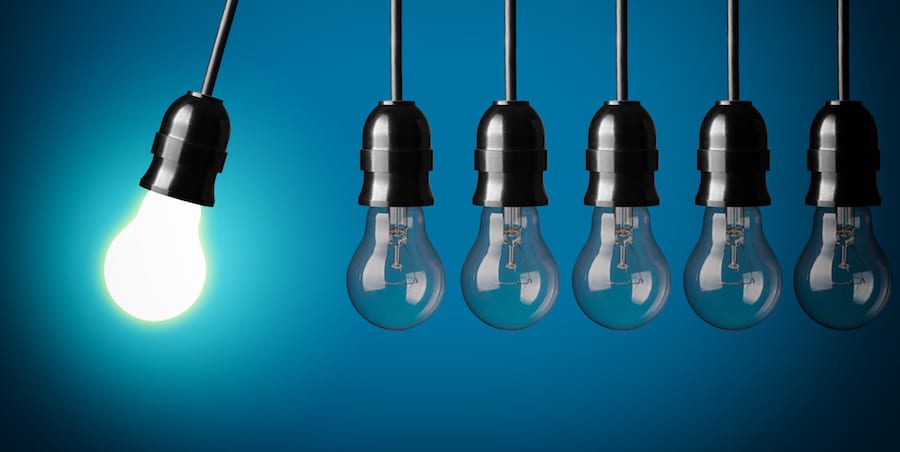
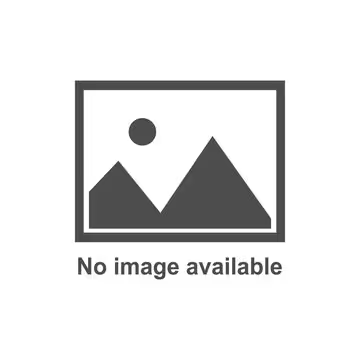
ONE QUESTION, FIVE ANSWERS – With this month’s question we try to understand what lean idea or principle our interviewees would have liked to learn sooner or better in their journey. So, heads up… You might be in a similar situation.
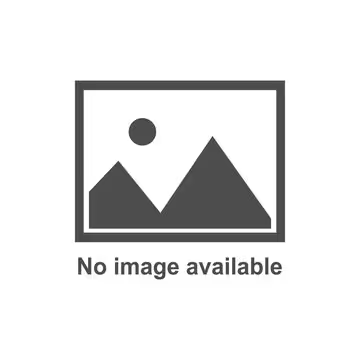
INTERVIEW – The UK Lean Summit 2024 is coming up in April. We speak to Dave Brunt to hear about the event and what we can expect from the presentations.
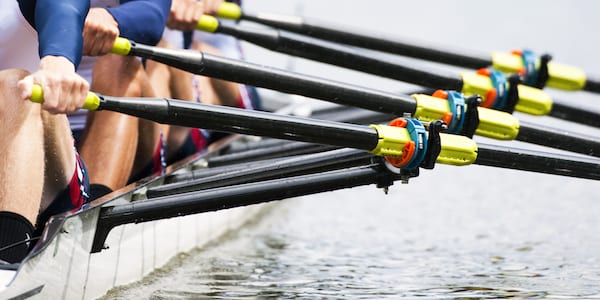
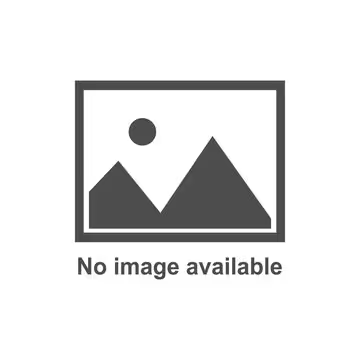
FEATURE – René Aernoudts discusses how to use standardized work in an organization, providing a lowdown of the techniques available to the lean practitioner.
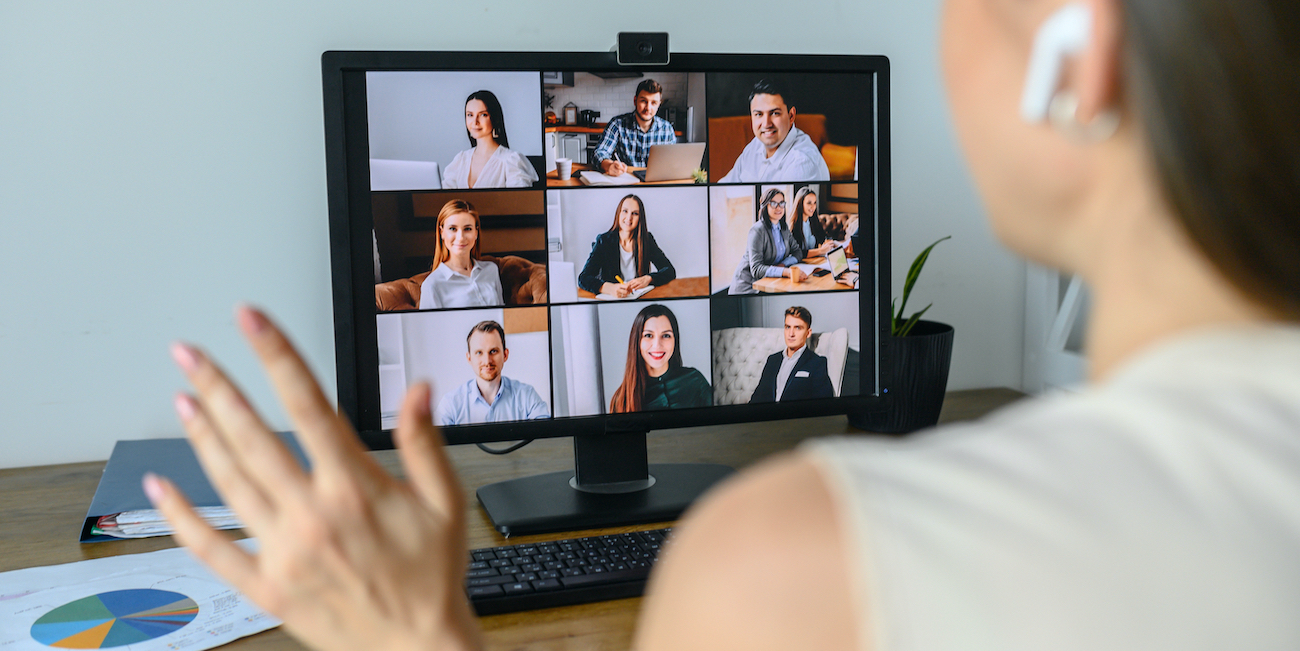
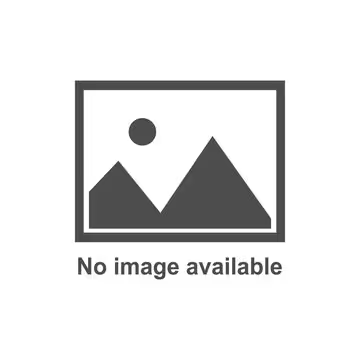
FEATURE – The Covid-19 pandemic has reminded us all that the nature of the work has changed forever. The author discusses remote work and how Lean Thinking can help you make the most of it.