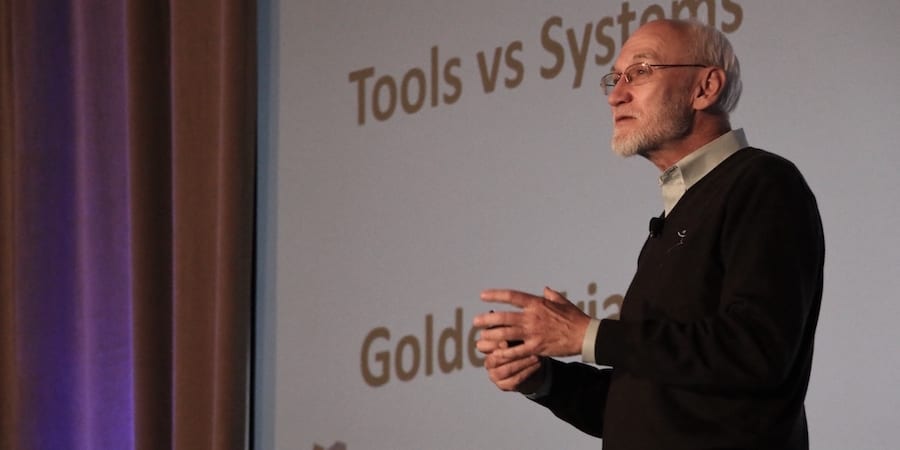
John Shook on failure, innovation and the resilience of lean
INTERVIEW – In this must-read Q&A, our editor sits down with lean guru John Shook to discuss the meaning of failure, lean innovation, and the resilience of our movement.
Interviewee: John Shook, CEO and Chairman, Lean Enterprise Institute
Roberto Priolo: What has kept lean relevant for so long when so many other improvement methodologies have all but disappeared?
John Shook: As we assess the state of lean 20 years after Womack and Jones first talked about it in their seminal book Lean Thinking, it certainly looks like it’s still thriving.
We can come up with several hypotheses on why that is, but I believe that the most important point is that lean is more than just an improvement methodology, like business process reengineering or six sigma, or a collection of tools. Lean is a profound and alternative way of thinking that we can use to approach any human endeavor, based upon questions that apply to any kind of work. By virtue of that, it is something that is very much alive.
The tools that other improvement methodologies have put forward can be compatible with a lean system – we can be quite agnostic about the tools – so long as they contain within them a means to tackle the problems people need to solve and the ownership of those problems.
Methodologies come and go, but there will always be problems to be solved, work to be done and value to be created – and that’s why lean thinking will continue to thrive.
RP: Indeed, lean continues to grow and we see examples of it everywhere we look these days. However, it’s also true that it often fails – something many critics ask us to acknowledge. What is your response to that?
JS: Change is all around us. It is unavoidable. We can choose to influence it in several ways, in order to bring about the version of it that we wish to see. Harnessing change means understanding its nuances, its pace, and its peaks and troughs, and learning from them. It is critical we continue to study both the success factors of lean and its failure modes, because there is great learning in them.
It’s worth noting, however, that as we move away from an implementation mindset into an experimentation mindset, the meaning of failure and success changes. People run experiments to fill the gap between where they are and where they want to be. Sometimes they exceed their objective; sometimes they come short of it. What matters most, however, is not the label we stick on the results of their experiment, but the reflection that follows it. If we structure this reflection well, there will always be some learning.
Say a company predicted a 100% improvement in productivity and only got 80%: is it more important to determine whether or not that’s a failure or to learn why things went a certain way and what they can do next time to achieve an even better result?
We tend to forget that science and experiments are not about making things work, based upon what we know already, but about finding out why they don’t. I have always loved Thomas Edison’s quote: “I haven’t failed. I’ve just found 10,000 ways that won’t work.” It is a wonderful sentiment. If we approach our work in terms of finding what doesn’t work, our whole attitude changes.
When people constantly experiment, there are bound to be “failures”. But if those failures are followed by reflection, there will also be learning.
Over the years, some consulting companies have tried to sell the idea that only 3-4% of lean transformations succeed, but how is that useful? Sure, we need to acknowledge failure modes, but if we start to see our lean work as experiments to understand the gap and learn from what went wrong in order to create what Al Ward calls “reusable knowledge”, the meaning of failure changes.
RP: Another common argument lean critics use is that the movement has not been able to find its second poster child. Is it even important that we find the “new Toyota”?
JS: There is no doubt Toyota will always have important insights for us, but do we have to find that second “poster child”? I am not too hung up on it. What we want to find, instead, is more and more companies that can be useful reference models for us as a community. And we already have a lot!
I recently spoke at the European Lean Summit in Barcelona, and there were so many inspiring organizations there. One of them was Spotify, which has been admired and emulated by many over the past few years for the way it manages its growth and for its “servant leadership” approach. Indeed, we can learn a lot from them and, even though we don’t know how impactful or lasting those lessons will be, I definitely see their work as a new manifestation of some of the “traditional” lean lessons, applied to a very different environment.
At the summit we also heard from 365.cafe, a 15-year-old chain of bakeries in Barcelona that has been experiencing very fast growth thanks to lean thinking. What they have put in place is admirable, and it is the kind of things others should want to draw inspiration from. Again, we don’t know where all of that will go, but everything I saw there is absolutely compatible with what we have learned about lean over the past two-and-a-half decades.
There are many ways in which we perceive success. One aspect of success is certainly longevity (had Toyota only done what they did for 10 years, we wouldn’t be talking about them in the same terms), but there is more than that: sometimes, we also need to look at the profound lessons that some of these organizations can teach us. That’s when we become more open to companies like Spotify or 365.
Another question that occurs to me as we talk about finding another Toyota is this: are we more interested in organizations changing or in individuals changing? I would love to see a historical longitudinal heat map of how people moved within the lean community, perhaps starting at Toyota or Wiremold and then taking what they learned elsewhere. It would be so interesting to see how this movement got ignited: understanding how lean ideas get out and go different places is more important to me than finding the next Toyota.
RP: The whole world seems to be talking about “innovation” these days… how does lean approach innovation compared to other movements like Lean Startup? Are we late to the game?
JS: As an innovation, lean thinking first emerged 25 years ago on the shop floor, in response to the large-scale problem we needed to solve back then: the poor performance of manufacturing firms. Later on, we began to see it as an enterprise-wide system (even though Toyota’s approach had been holistic from the start, spanning manufacturing, sales and product development). Then, about 10 years ago, a number of entrepreneurs (especially in California) started what came to be known as the Lean Startup movement.
What we often fail to see is that this movement is absolutely part of the lean community. They have found a process for running experiments on customer needs, and in that a way to apply lean thinking in fast-moving environments characterized by high levels of uncertainty. But their method, which they call Design-Build-Measure, is 100% PDCA – reframed to apply to a very different setting.
Our movement has seen incremental innovation all along, even though for many years we just picked up on the production side of lean because productivity was the most prominent issue we faced at the time. In reality, lean thinking and lean startup stem from the same need to understand the work and provide more value to the customer.
It is a common misconception to see them as separate entities: startups around the world, from Silicon Valley to Tel Aviv, from Cambridge to Barcelona, are creating innovation that we perceive as “breakthrough” – I recently tried a pair of the latest virtual reality goggles, so I can see why we do – when in reality it isn’t. Much like a fixture that makes the work easier on the production line, the coolest App or gadget is also the result of small incremental innovations over many years.
With this in mind, it’s easy to see how the genesis of the two movements is the same – PDCA – and why they are both legitimate parts of the wider community.
So, are we as lean folks late to the game? I don’t think so, even though it is true that many, more “traditional” lean thinkers have had their heads stuck on the shop floor for a long time. Once we learned to look past it and be open to other forms of innovation, we found that lean startup actually talks about the same things. And now we are seeing an amalgamation of these two approaches in environments like LPPD – Lean Product and Process Development – with its very effective set-based concurrent engineering, for example.
RP: What are the biggest challenges for the lean movement right now?
JS: First of all, the challenge that doesn’t go away: the human tendency of copying and pasting “best practices”. We have already fallen into the trap of blindly copying what Toyota does – and learned it leads nowhere – so we must remain vigilant to ensure it doesn’t happen again. Tools are not important; PDCA and learning are.
Secondly, lean thinking has much more depth to it than meets the eye. It is all too easy to trivialize it. By focusing on the tools, we ourselves have been guilty of this in the past. As a consequence, companies have done the easy work of implementing the techniques, gotten some results, but failed to initiate a real transformation. If this kind of failure gets attached to lean’s name, and we continue to confuse the tools with the underlying thinking, then the movement might be under threat.
This is not a problem so long as whatever movement comes after it has the same ideas and thinking at its core. There is a risk it might not, however, and that’s why we need to define lean properly, explain it, and find examples people can learn from. As we look at the world to find more and more reference models, we must keep an open mind and develop synergies with like-minded people, organizations and movements that share our same consciousness of problems – no matter what “community” they belong to. And that, as a challenge, is quite exciting.
THE INTERVIEWEE
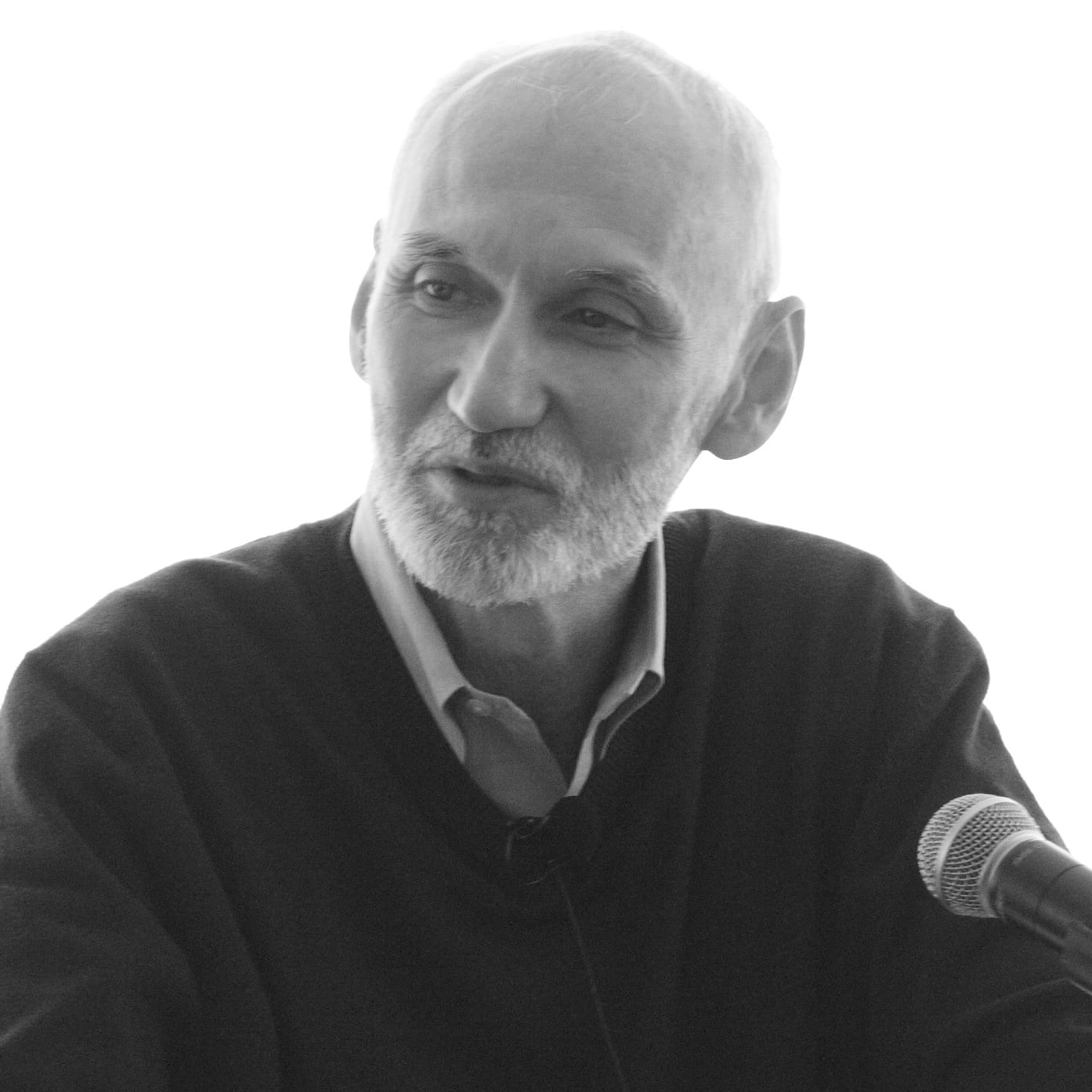
Read more
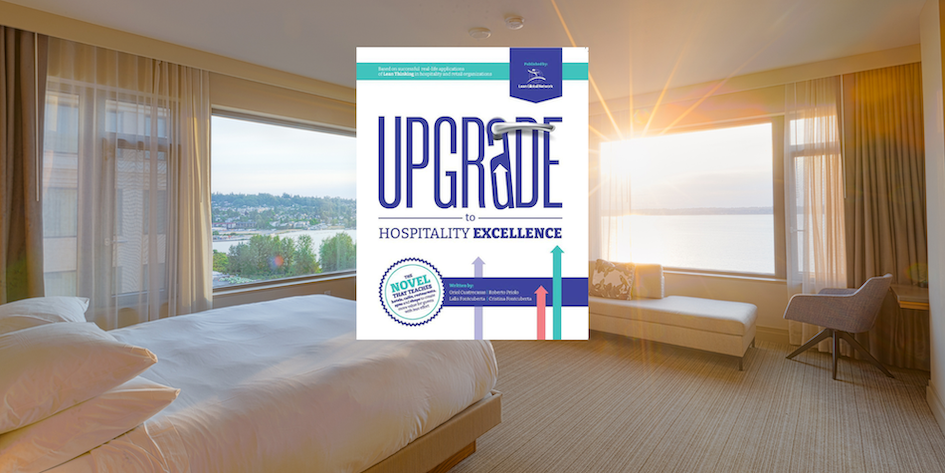
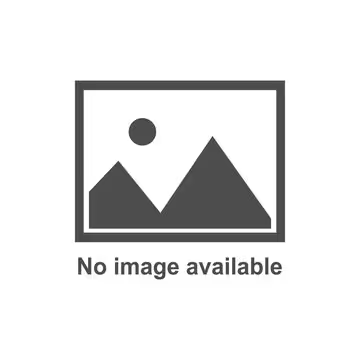
BOOK EXCERPT – These are the opening paragraphs of Chapter 1 of the new Lean Global Network book about applying Lean Thinking in a resort hotel.
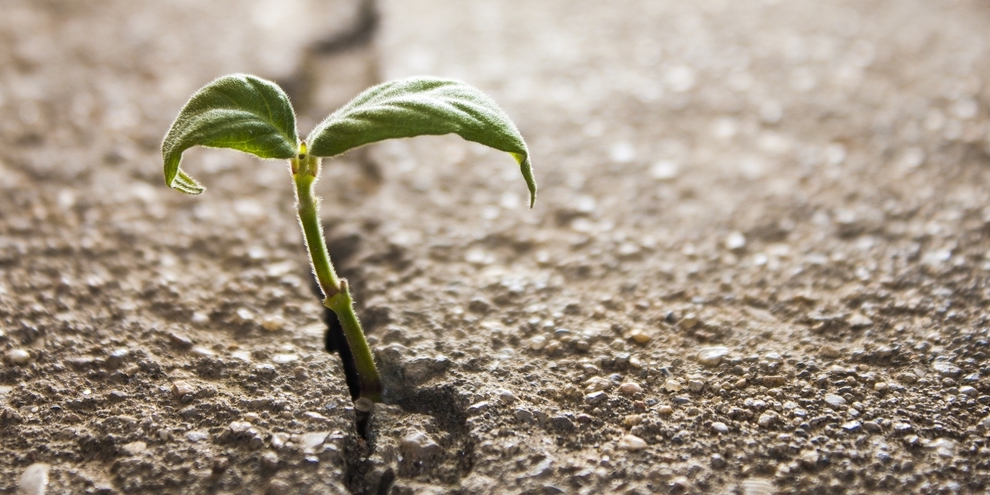
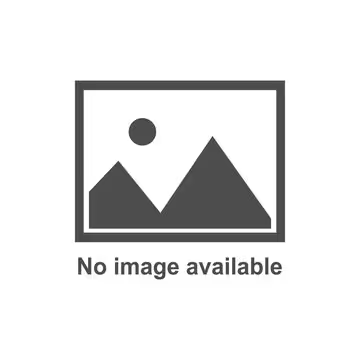
ROUNDUP – Our editor looks back at the best articles explaining how Lean Thinking can help in a crisis and bring an organization back from the brink of disaster.
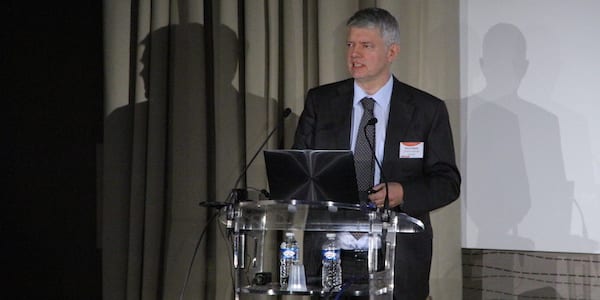
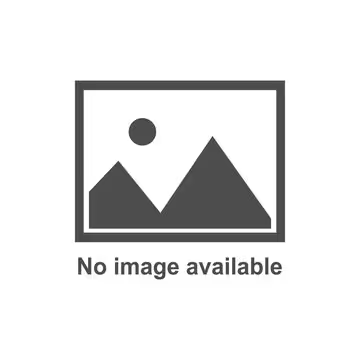
VIDEO INTERVIEW - We spoke with Toyota Motor Europe's CIO at the Lean IT Summit about hoshin and IT, the application of the agile methodology, and the power of coaching.
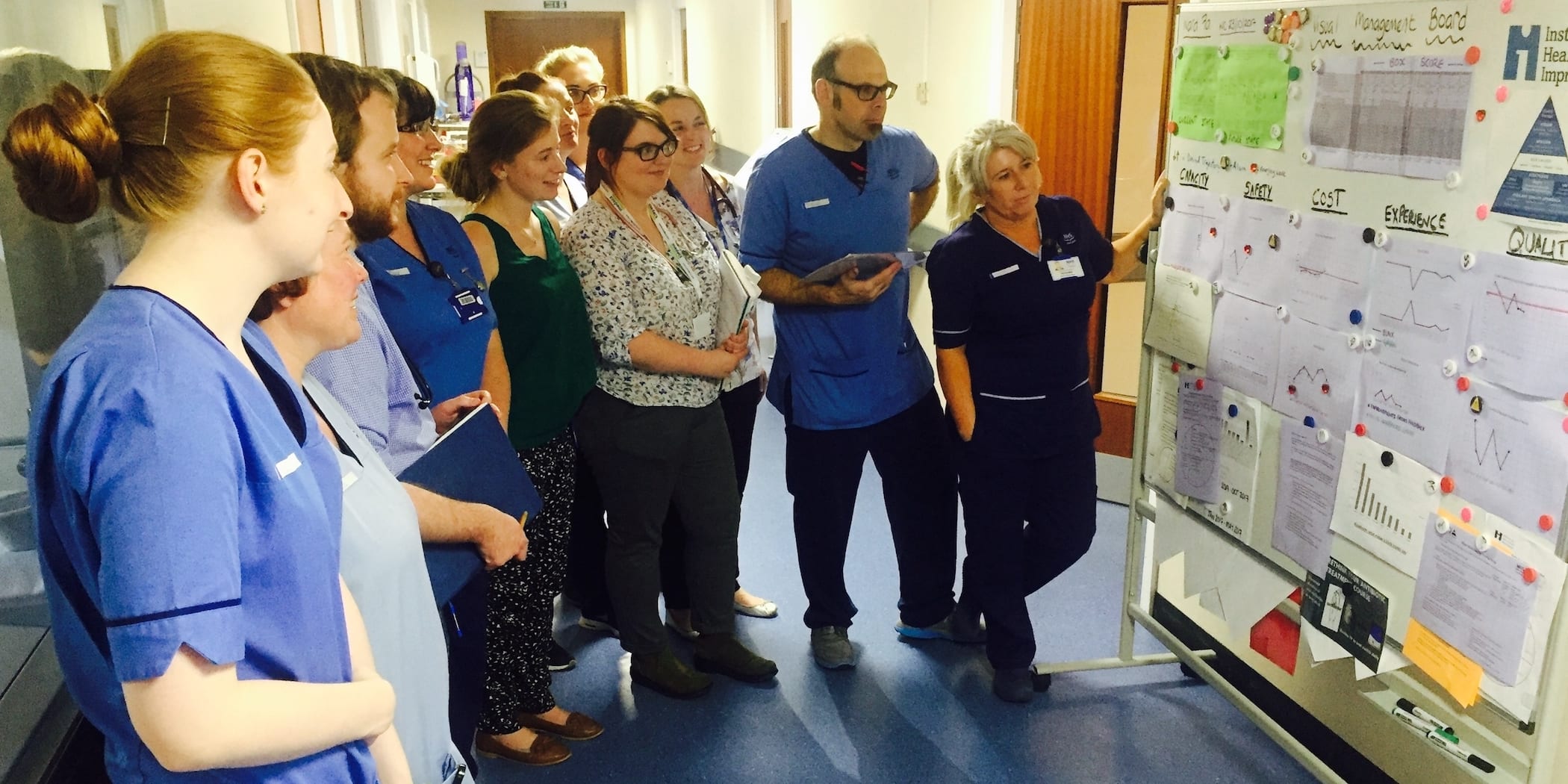
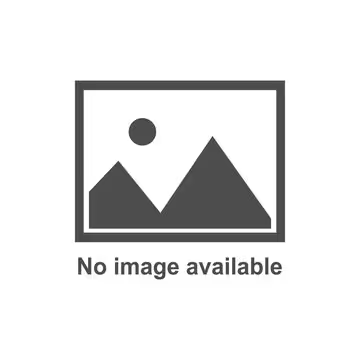
INTERVIEW – The CEO of a Scottish health board takes us through the organization’s long lean journey, reminding us that allowing people to take the initiative often leads to the most impressive discoveries.