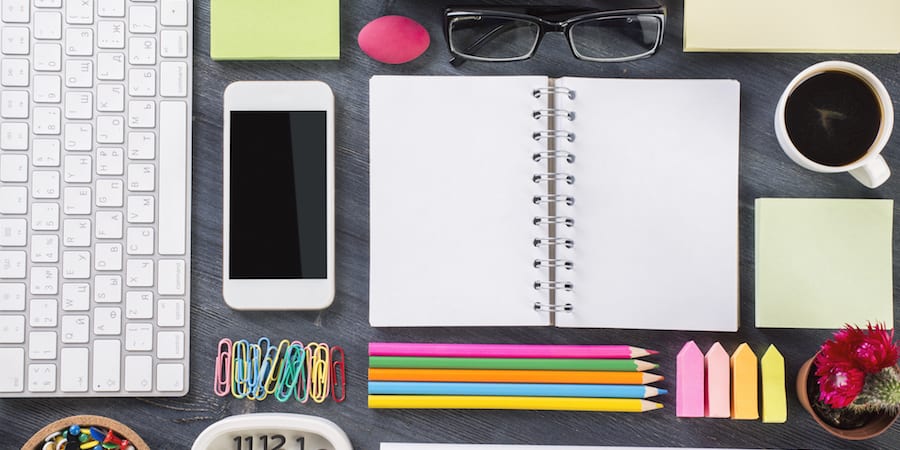
Jim Womack provides us with a few tips on how to sustain 5S
WOMACK’S YOKOTEN – 5S seems to mean different things to different people. What’s common, however, is the difficulty to sustain it. The author offers a few tips.
Words: Jim Womack, Founder and Senior Advisor, Lean Enterprise Institute
Recently I visited a company with the most comprehensive 5S program I have ever seen. Everything was in its well-marked place, down to the staplers on office desks surrounded by blue tape to indicate the right location. And the company’s lean audits start with 5S. This is great. But what is the purpose? What is being accomplished with this very considerable effort? And can it be sustained?
To think about this let’s go back to the origins of 5S, the practices named for five Japanese terms beginning with an “s” sound, translated to English as sort, straighten, shine, standardize and sustain. These practices were applied as a system in manufacturing companies in Japan in the 1950s, as they struggled to make products with perfect quality in long production processes with standardized work and precise, repeatable cycle times within takt time. The purpose of 5S was to make sure that nothing was in the way of getting the work done right within takt time, and that everything needed to do the work was in the right place with no need for “treasure hunting” – even for a second or two – by any worker in the process. As always, the developers of a lean tool – in this case 5S – started with the work to be done and worked backwards to devise practices to make it easier, better, safer and cheaper.
However, what many folks heard was often different as 5S spread from its point of origin in manufacturing in Japan. I frequently hear 5S advocated as some sort of “clean up, fix up” campaign, an “easy way to get started with lean”, raise morale, impress investors, impress customers, and, in general, create the appearance of a “world-class” company (whatever a “world class” company may be). That’s all fine, as long as 5S also accomplishes its key purpose: making good work possible and sustainable.
If there is confusion about the purpose of 5S in repetitive operations, it thickens as we get further from the factory and deeper into knowledge work in offices (and, increasingly, work without offices.) Do we really need to put blue tape around our staplers? Do we need to clean everything off our desks every day? Do we need to sort the supply room every week? Or does it just make us feel better to clean up our rooms as our mothers always told us?
The way to answer these questions is to start with the work to be done. What is it? What are the process steps? What is in the best currently-known way of performing each step with no interruptions and with no time out for treasure hunting? What materials and equipment are needed for each step and what is their standard position? How can 5S help, in what form, and audited with what amount of rigor? I find it is much harder to define the work outside of the factory than it is to create 5S in office environments. But 5S in the office – no matter how aesthetically pleasing – is not likely to be of much value without rigorous work design. So, again, we need to start with the work and work backwards.
Let’s suppose an organization is implementing 5S for the right reasons in the right ways to improve the work. It seems like this should be easy once the work is correctly specified. Just sort, straighten, shine, standardize and sustain the process! But the sustain part is actually very hard. In my experience, as an inadvertent industrial and organizational archeologist, I have often observed the remains of 5S implementations (e.g., the tattered blue tape around the empty space where tools or supplies should be and probably once were). These efforts seem to have a short half-life. But, really, “half life” is the wrong term because this term assumes degradation after a clean-up event but with a long tail before all 5S disappears into chaos. In practice, I observe that 5S has a different curve, with benefits often disappearing altogether in two short half-lives, one a steep decent and the second a nose dive. So how can we sustain 5S for the right purpose?
Here are the problems and potential countermeasures:
- 5S requires a focused investment of our time right now (when we are in a hurry after completing a work task or tired after a long day) to provide a diffuse reward at some later point in time, perhaps much later. So, doing 5S must be built directly into standardized work to a point that not performing the 5S cycle at the right time every time seems as strange as not installing a part on a product on an assembly line or skipping a coding step in software development.
- A 5S implementation, like implementation of any lean tool, requires cleaning up the management system as well. It’s the management system supporting 5S, with frequent audits and rapid correction of any deficiencies discovered, that determines 5S’s fate over time. So, workplace and management clean up must be tackled together. (The consequence is that sustainable 5S can never be an “easy way to get started,” but it can be a critical part of a long lean journey to achieve an important goal.)
- Lean tools work best in combination but 5S is often applied in isolation. Its companion methods of daily management and visual management need to be applied together to obtain and sustain the benefits of all three.
- 5S and the companion practices of visual and daily management need to be designed into every value-creating process during production system design rather than retrofitted later. What I almost always see is 5S programs being retrofitted on processes that are almost invisible due to the amount of junk that has built up. This rework can be avoided by broadening the task of the team designing every production system (which, of course, would like to avoid the focused effort now and let someone else worry later about the consequences as problems emerge.)
If we can apply all of these countermeasure to all of these problems, 5S for the right purpose can have a whole life that lasts indefinitely. I hope that we as a Lean Community will progressively tackle this challenge.
Let me add a final note on personal 5S: I’m not getting younger, I’ve got a lot on my mind, and I forget things. So my personal 5S after every interaction – when I leave my chair, a room, a building, or even the airplane as I debark in a new country – is a critical part of my life. If you someday see me wandering through your gemba while periodically checking the standard positions that I’ve created for reading glasses, keys, iPhone, wallet, passport, notebook, PC, chargers, jacket, and brief case, please understand that this is not a neurological problem or an empty lean ritual. I’m just trying to make sure that everything will be in the right place for me to get the next cycle of my work done without the need for the rework of treasure hunting or replacing lost items. I’m guessing that you may need some personal 5S as well. So, on future gemba walks perhaps we can do our personal 5S in unison.
THE AUTHOR
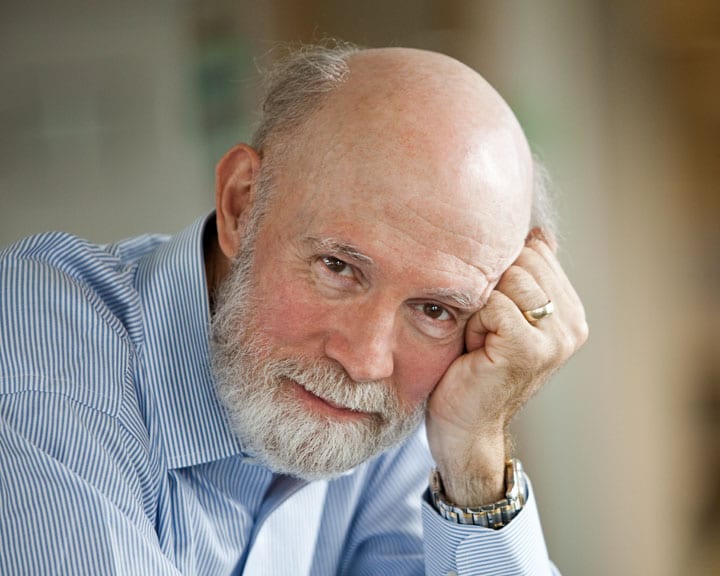
Read more
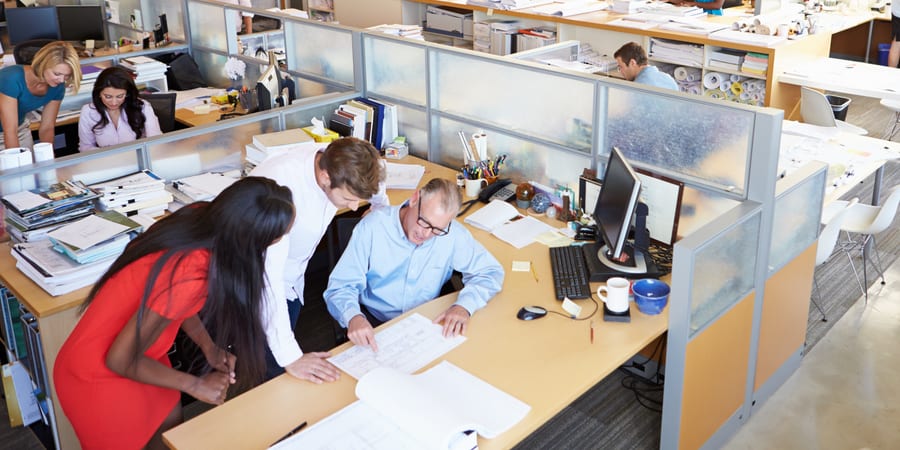
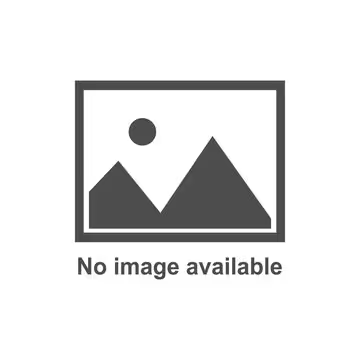
VIDEO – We constantly talk about the role of leadership, but perhaps we don't realize just how intertwined leadership transformation and business transformation really are. This short video discusses why.
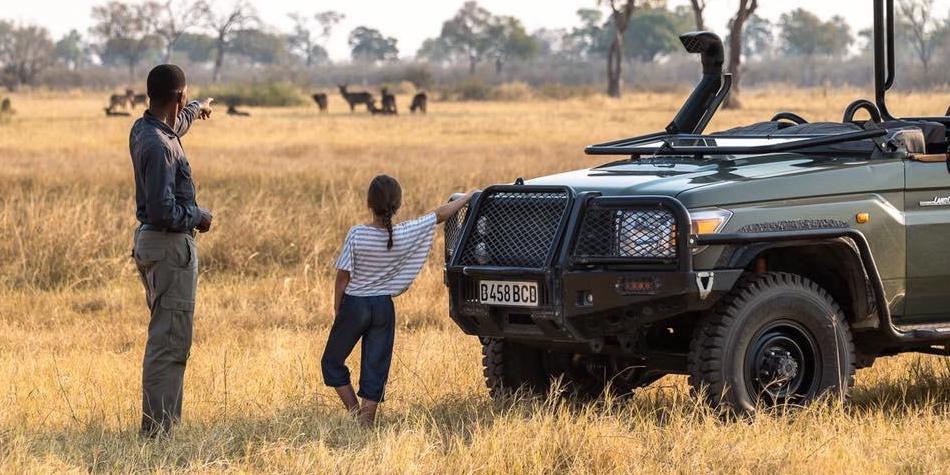
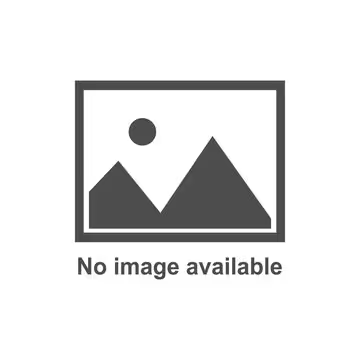
CASE STUDY – This company in Botswana has embraced lean thinking passionately to build the capacity and ability to deal with higher demand for its converted vehicles. The author tells us about their journey.
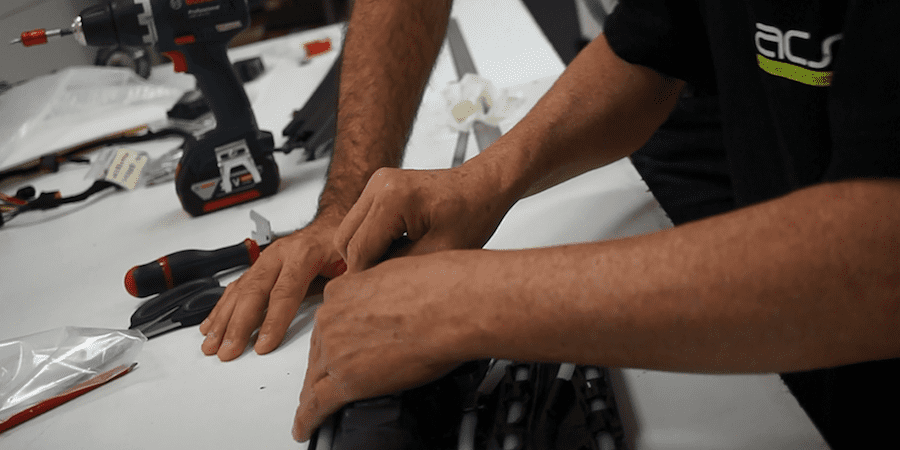
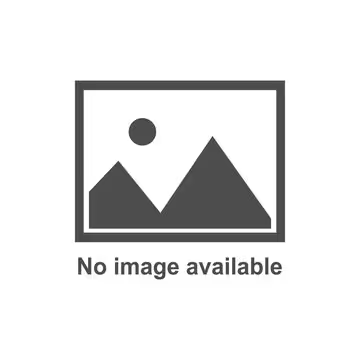
FEATURE – A French automotive supplier has been applying lean principles to transform its engineering department with great results. In the process, they have realized they could put in place a really effective system to build innovation.
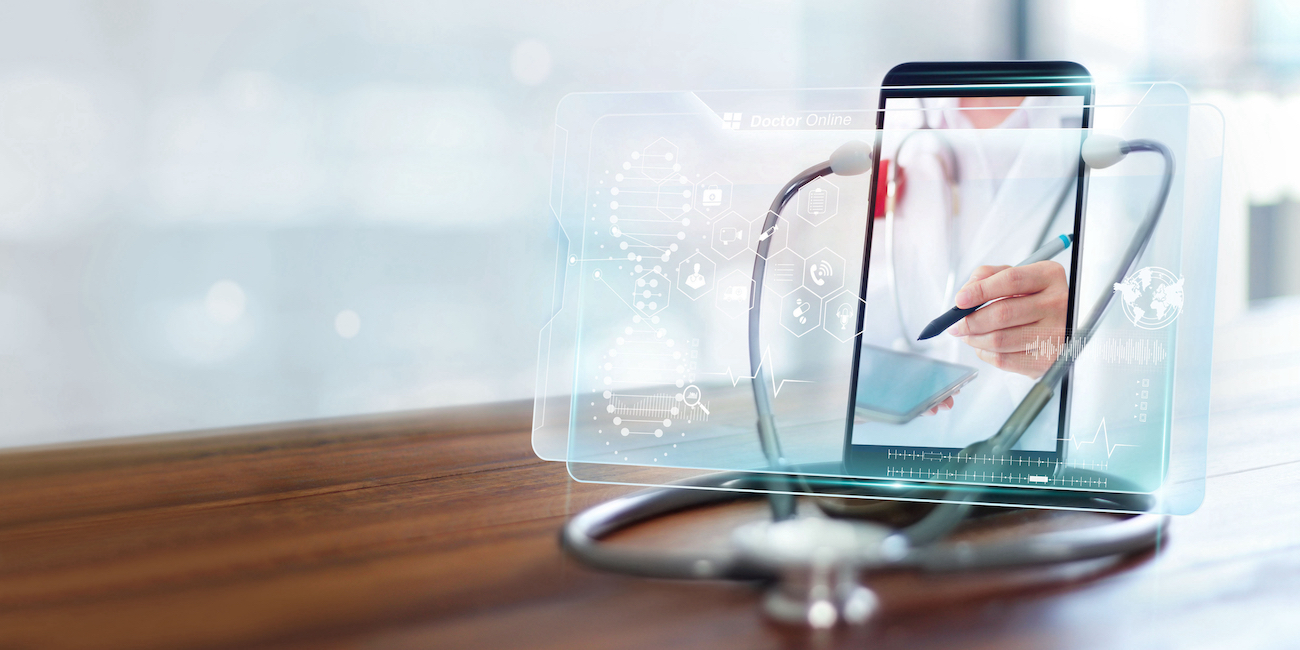
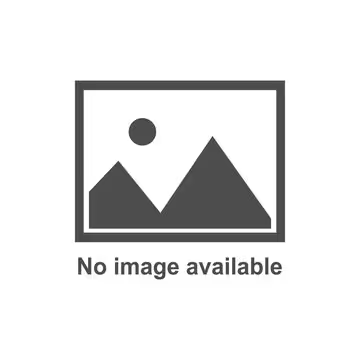
CASE STUDY – The Covid-19 pandemic has accelerated the application of Virtual Healthcare across the world. In South Australia, this has been implemented in urgent care.