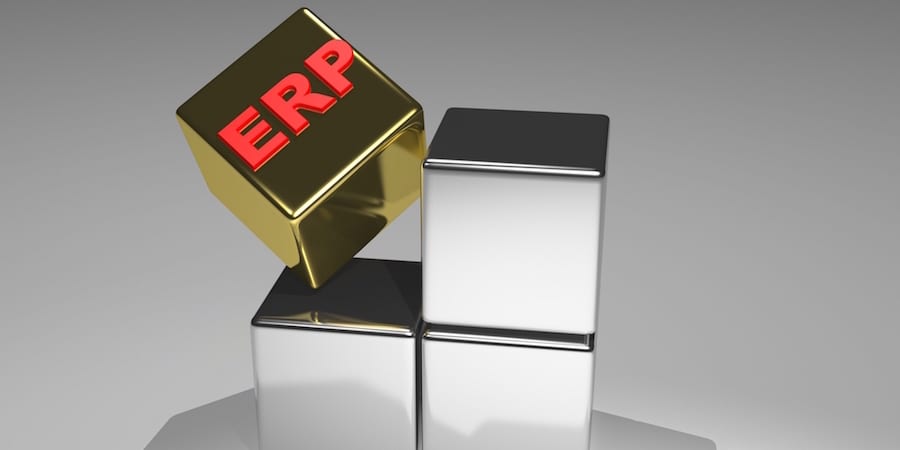
Is ERP at odds with lean management? Ian Glenday wonders
FEATURE – It might be widely used as a planning system, but ERP – Ian Glenday argues – is not conducive to an environment where lean thinking can thrive: because it is based on a batch logic, it always creates a different plan and, with it, instability.
Words: Ian Glenday, lean coach and author
Ask yourself these three questions. In your organization:
- Whenever a work schedule or plan is calculated – be it for materials, production, or distribution – is it different to the previous plan?
- Are plans ever changed after being issued?
- Is “fire-fighting” an appropriate term to describe the way things are sometimes done?
If you have answered, “yes” to one or more of the above questions – and most likely you have said, “yes” to all three – then you might want to read on.
ERP uses economic order quantities (=EOQ), also known as batch logic, to calculate what is required. It is the planning algorithm used by nearly every planning system. If all the planning systems used by most companies are based on this, it must be right, mustn’t it? Surely companies are not all using planning systems that are guaranteed to create instability?
Instability will occur if one gets a lot of changes coupled with unnecessary variability. ERP does both – very well – and here are the reasons why.
If the key underlying data has changed since the last time the plan was calculated, one will get a different result. The three key sets of data are:
- Sales forecast
- What was actually achieved vs what was planned
- Inventory levels
Now ask yourself three more questions about your organization:
- Are actual sales ever different to forecast?
- Is what was actually achieved ever a bit more or less than what was planned?
- Is the physical inventory ever different to what the computer shows?
Almost certainly it will again be “yes” to each question. If the data changes then a different plan every time is guaranteed. The chance of the data remaining unchanged from one plan to the next is zero. For the plan not to change would require 100% data accuracy all the time.
But that is never going to happen.
Sales will be different to forecast, actuals will be more or less than what was planned and inventory inaccuracies will occur. Of course companies should work hard to achieve data accuracy but they are never going to achieve 100% accuracy all the time. It is just not going to happen.
And the problem is getting worse.
Planning systems have become much faster, which some people see as a good thing. Plans can be re-calculated several times a week or even a day, which gives the illusion of being “responsive.” Plans tend to be calculated and re-calculated much more frequently nowadays and every time a different plan is issued. The result is fire-fighting. Not exactly a great situation for sustaining lean principles and practices.
Not only does ERP guarantee plan changes, it also creates unnecessary variability. EOQ logic rounds up to “economic” lot sizes. Fill the truck, make a whole tank full, hit the next sales volume discount are just a few examples. As a direct result of this rounding up at some point inventory will be too high so the planned quantity will need to be rounded down. This creates a series of peaks and troughs in the demand signal, or variability caused by the planning process that has nothing to do with actual demand. This is well recognized and even has a name – the bullwhip effect. Even if there was not the problem of data changing, as described above, EOQ would still produce a different plan every time it was calculated, which again results into unnecessary variability. Standards are a key lean principle but it is very difficult to maintain them when the plan volumes vary every time. Take changeovers, for example, an area to which many companies apply the SMED tool. With a different plan every time, when changeovers are due to happen will also be different, any time of the day or night. It’s not even possible to have the same number of people available to do the changeover in this situation. So how can one have standard SMED procedures?
In your company, are plans ever changed after they have been issued? Would fire-fighting be an appropriate term to describe the way things are often done? Do you find it hard to sustain lean?
Could it be that most companies are using a logic that is fundamentally flawed and guaranteed to create instability? As incredible as it may seem, the answer is “yes.” Just because everyone uses ERP based on EOQ, it does not mean that this is the right thing to do. It is not the first time, and neither will it be the last time, where conventional wisdom proves wrong.
How did Toyota overcome these issues? For a start they did not use EOQ logic as a basis for their planning. The foundation of the Toyota Production System was a planning approach called “levelled production,” a progressive five-step process (and probably the least understood aspect of TPS) that I will be discussing in my next article for Planet Lean.
To find out more about the five steps of levelling, read The magic of levelled scheduling. It is also explained in more detail in Lean RFS: putting the pieces together.
THE AUTHOR
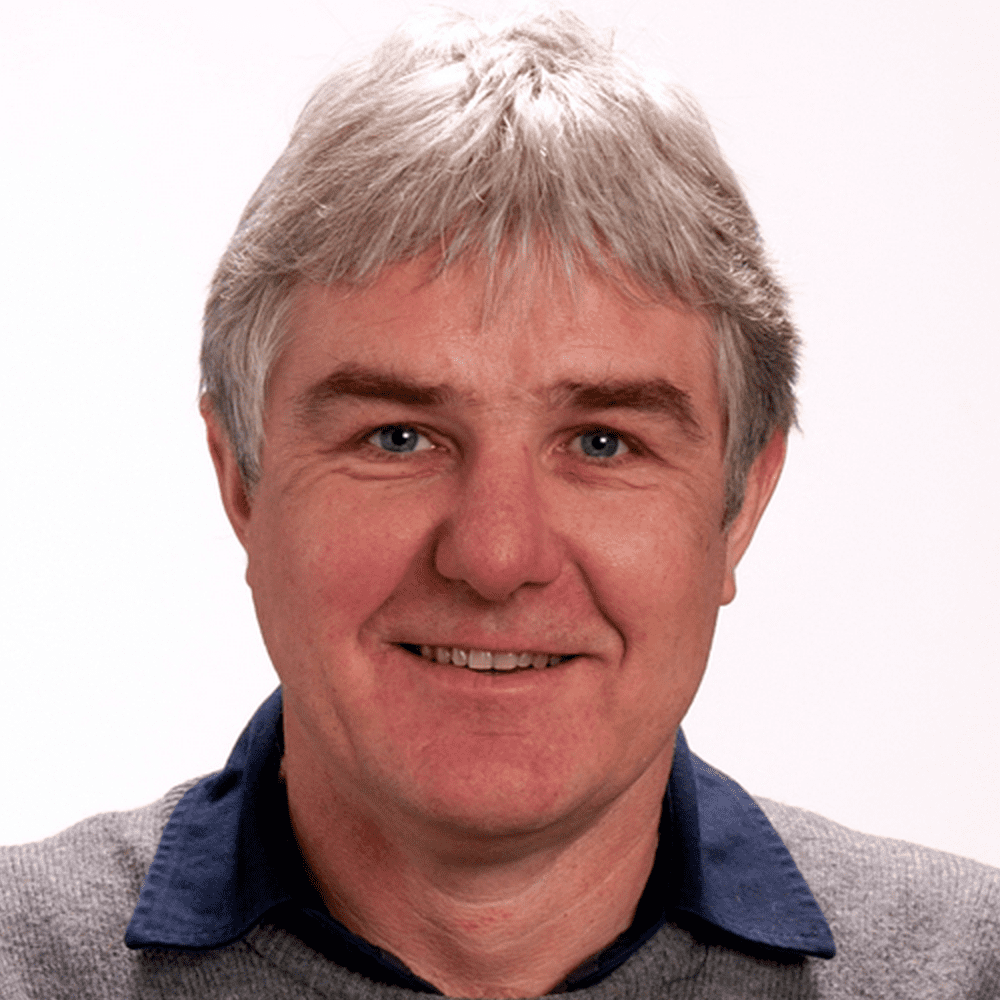
Ian Glenday is a lean coach and sensei with experience supporting change in several industries, including chemicals, food and drink, and pharmaceuticals. He started his lean journey in the late 1970s as a micro-biologist running a fermentation plant producing enzymes, where he first began developing Lean/RFS concepts and principles for application in process industries. He later joined Reckitt & Colman, later becoming Head of Policy Deployment based in Norwich, England where substantial increases in sales per employee, market share and profit margins were achieved by applying lean across the whole company. Ian is also author of two Shingo award winning books: Breaking through to flow and Lean/RFS: putting the pieces together.
Read more
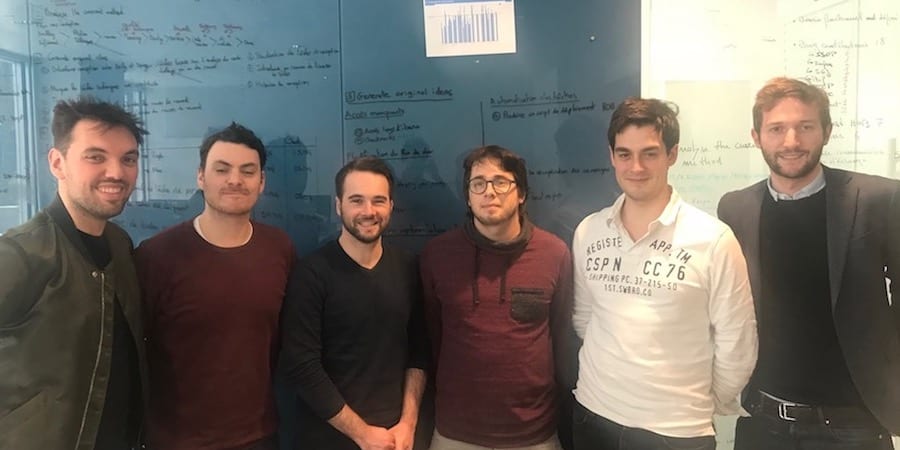
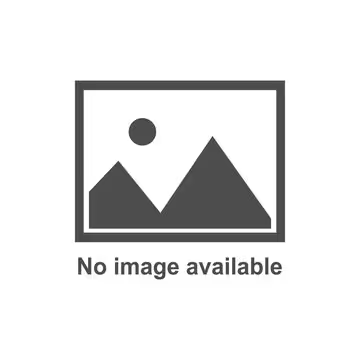
BUILDING BRIDGES – This month, a CTO explains how his software company borrowed the kaizen spirit – and the idea of a dojo – from an avionics factory and put it to good use.
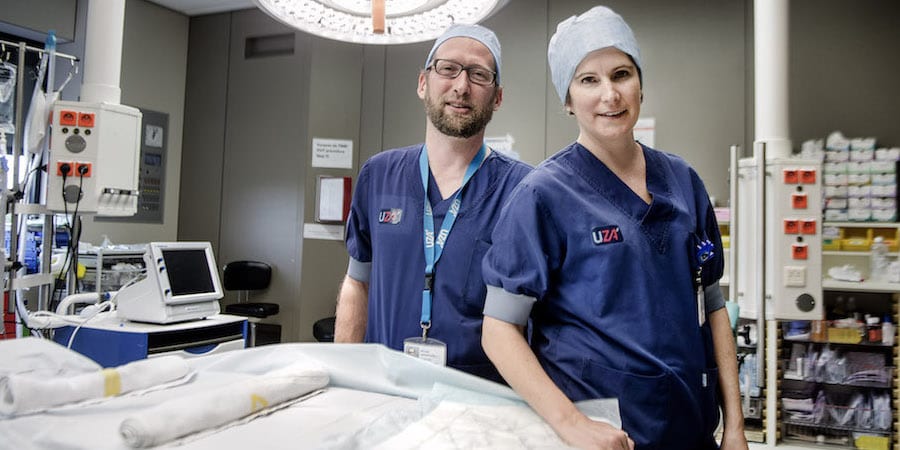
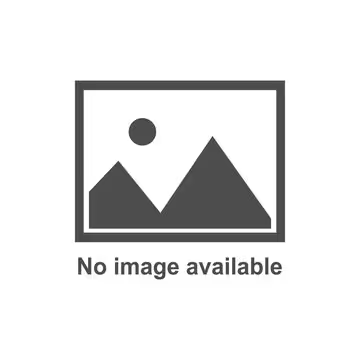
CASE STUDY – How an improvement program of the British national healthcare system inspired a Belgian hospital to launch an organization-wide lean transformation with the active support of the HR and nursing departments.
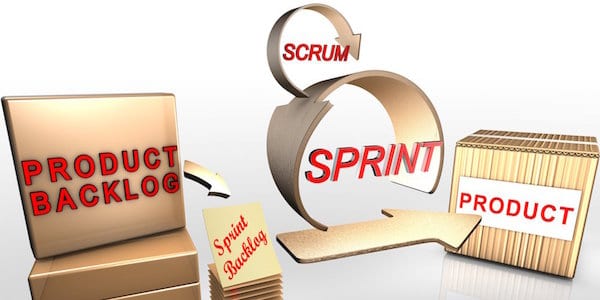
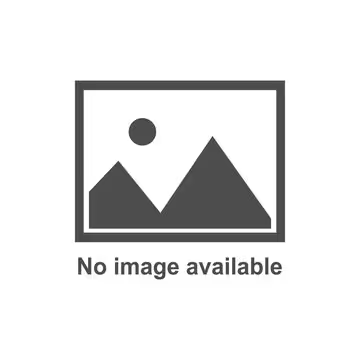
FEATURE – This piece analyzes the different elements of scrum, an agile software development framework, as seen from the point of view of traditional lean thinking.
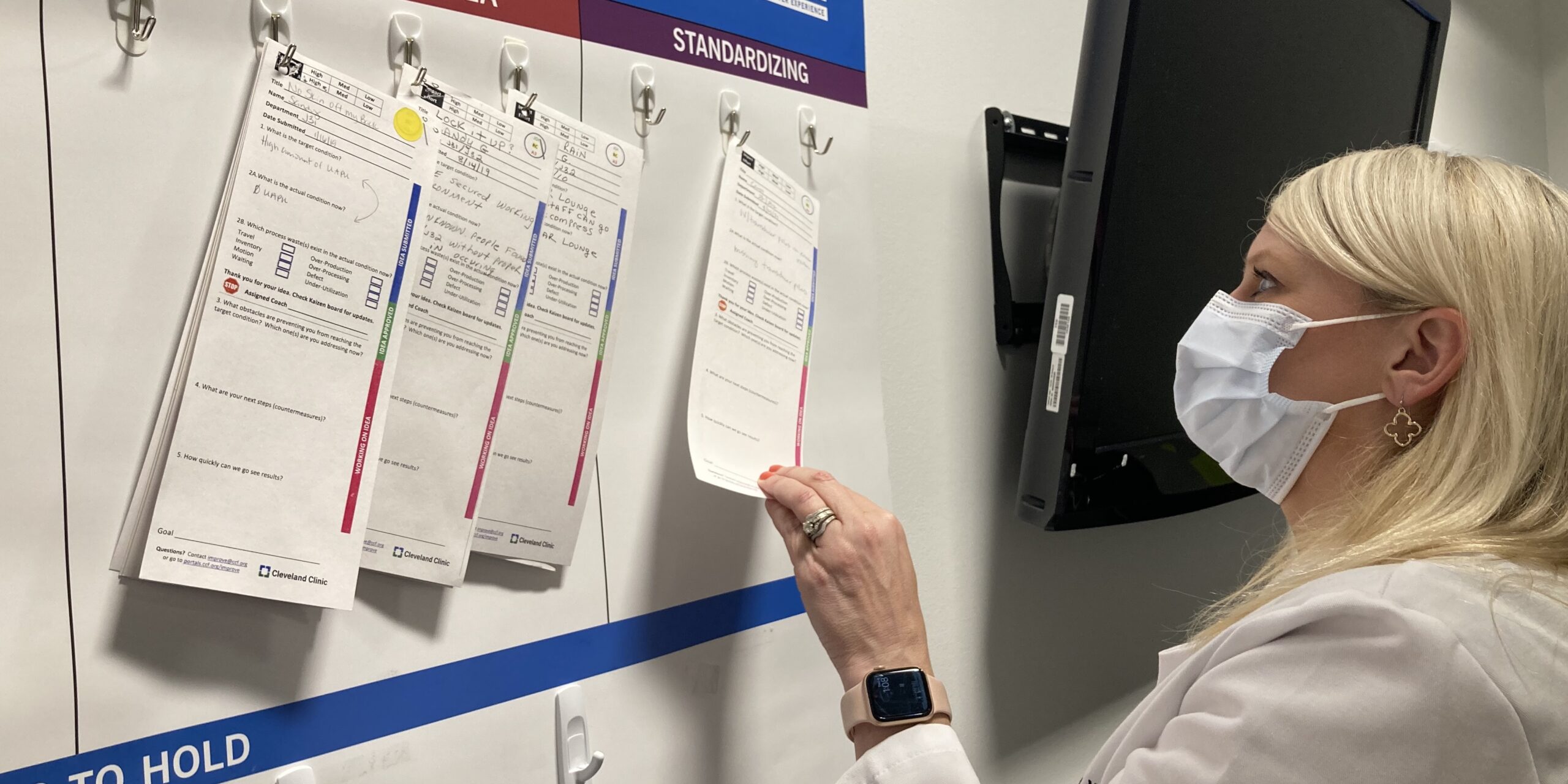
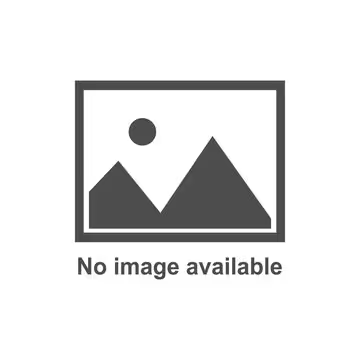
INTERVIEW – Cleveland Clinic has been on a lean journey for a few years now. In this interview, their Chief Improvement Officer and Chief Nursing Officer talk continuous improvement, metrics, and sustaining results.