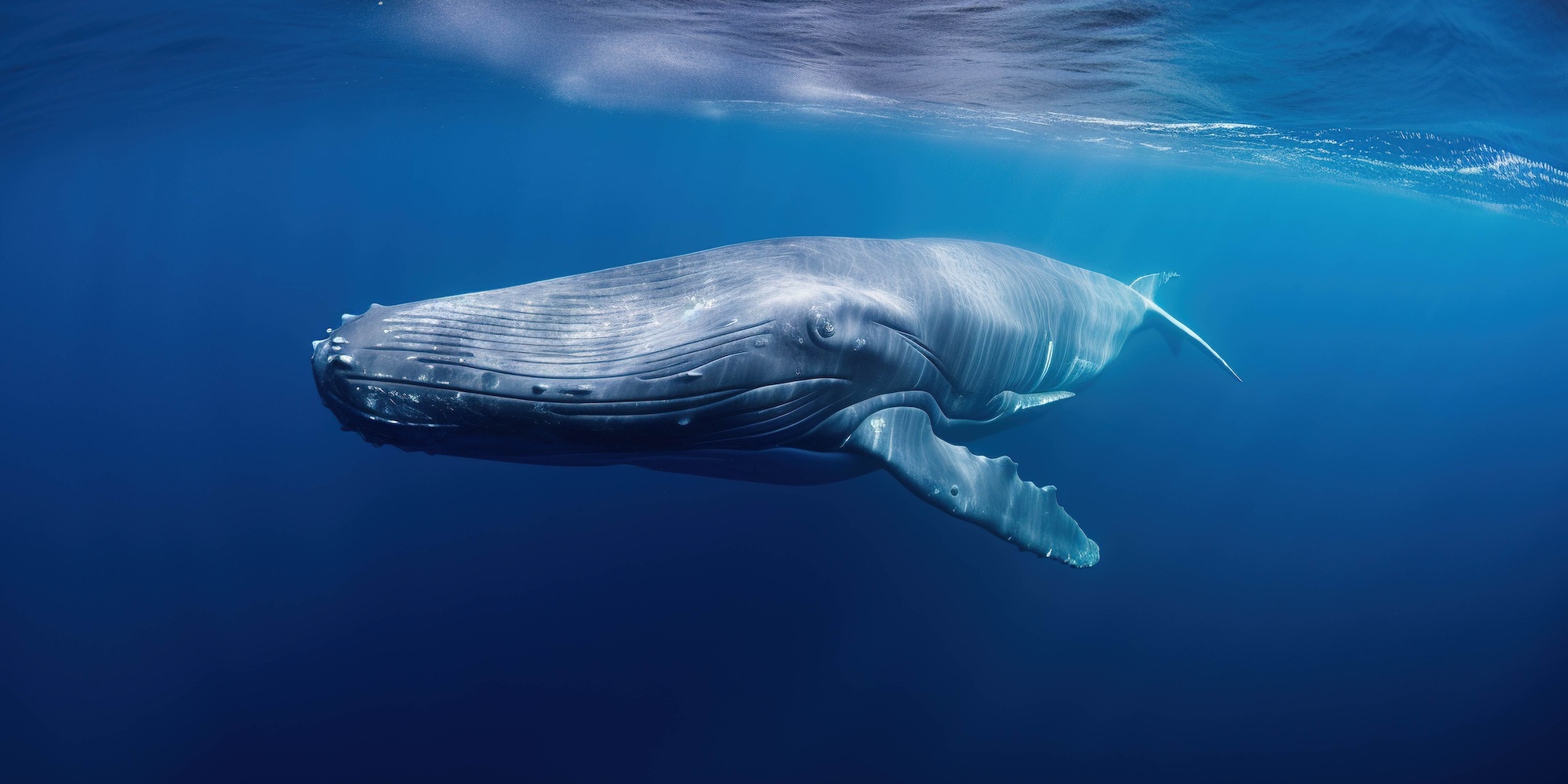
Did DeepSeek just pull a Toyota-style revolution in AI?
OPINION – DeepSeek’s AI innovations can be compared to the disruption Toyota brought to automotive, showcasing efficiency, problem-solving, and value-driven adaptability over resource-intensive methods.
Words: Sergio Caldeirinha
Sources and inspiration for this article came from several research papers and an interview with Moacyr Galo, Chief AI Officer (CAIO) at sa.global
The recent breakthroughs in AI, particularly with DeepSeek’s R1 model, offer a fascinating parallel to the transformation that the Toyota Production System (TPS) brought to manufacturing after World War II. Just as TPS revolutionized production by challenging the dominant paradigms of GM, Ford, and Chrysler – rooted in massive capital, labor, and inventory – DeepSeek’s approach to AI challenges the prevailing trends of brute-force, resource-intensive models like ChatGPT. For lean practitioners, this comparison provides valuable insights into how AI can be integrated into lean practices, corporate learning, and daily problem-solving.
THE TPS REVOLUTION: A LEAN BREAKTHROUGH
In the mid-20th century, Toyota faced significant constraints: limited capital, scarce resources, and a fragmented market. Instead of adopting the mass production methods of American automakers, which relied on large inventories, specialized machinery, and economies of scale, Toyota developed a system that emphasized flexibility, efficiency, and continuous improvement. TPS introduced principles like just-in-time production, jidoka (automation with a human touch), and kaizen (continuous improvement), which focused on eliminating waste, empowering workers, and delivering value to customers.
The key to TPS was its ability to achieve superior results with fewer resources by optimizing processes, fostering a culture of problem-solving, and relentlessly focusing on value creation. This stood in stark contrast to the American model, which prioritized scale and standardization over adaptability and efficiency.
DEEPSEEK: A LEAN APPROACH TO AI
DeepSeek’s R1 model represents a similar paradigm shift in AI development. While models like ChatGPT rely on massive datasets, enormous computational power, and increasingly larger architectures, DeepSeek has taken a leaner, more targeted approach. By focusing on efficiency, optimization, and systematic reasoning, DeepSeek demonstrates that AI can achieve state-of-the-art results without the resource-intensive practices that dominate the field.
1. Constraint-driven innovation
Just as Toyota turned resource constraints into opportunities for innovation, DeepSeek’s team optimized their models under hardware limitations imposed by US sanctions. By programming 20 of the 132 processing units on each H800 GPU specifically for cross-chip communication, they achieved remarkable efficiency. This mirrors TPS’s emphasis on making the most of available resources and continuously improving processes.
2. Focused, efficient architectures
DeepSeek’s success with smaller 7B and 14B parameter models challenges the trend of ever-larger AI models. Instead of trying to build a “jack-of-all-trades” system, DeepSeek focused on developing models that excel in specific domains through targeted training and reinforcement learning. This aligns with TPS’s principle of delivering value by focusing on what truly matters, rather than overproducing or overengineering.
3. Systematic reasoning and problem-solving
One of DeepSeek’s most significant breakthroughs is its use of reinforcement learning to teach models step-by-step reasoning. This approach mirrors the systematic problem-solving methods at the heart of TPS, where workers are trained to break down complex problems into manageable steps, analyze root causes, and implement solutions. By shifting from uncertain “next token prediction” to confident, methodical reasoning, DeepSeek’s models embody the same disciplined thinking that drives lean practices.
4. Eliminating waste in training
DeepSeek’s Group Relative Policy Optimization (GRPO) eliminates the need for a separate critic model, reducing computational overhead and streamlining training. This is akin to TPS’s focus on eliminating waste (muda) in production processes. By simplifying the reward system and focusing on group-based comparisons, DeepSeek achieves faster, more scalable training – a lean approach to AI development.
IMPLICATIONS FOR LEAN PRACTITIONERS
The parallels between DeepSeek and TPS offer several lessons for lean practitioners looking to integrate AI into their practices:
1. Embrace constraints as opportunities
Just as Toyota and DeepSeek turned limitations into strengths, lean organizations can use AI to optimize processes under resource constraints. AI can help identify inefficiencies, predict bottlenecks, and suggest improvements, enabling continuous improvement even in challenging environments.
2. Focus on value, not scale
DeepSeek’s targeted approach demonstrates that bigger isn’t always better. Lean practitioners should focus on deploying AI solutions that address specific pain points and deliver measurable value, rather than pursuing overly complex or resource-intensive systems.
3. Foster systematic problem-solving
DeepSeek’s step-by-step reasoning capabilities highlight the importance of structured thinking. Lean organizations can use AI to enhance problem-solving by breaking down complex challenges, analyzing data systematically, and developing actionable insights.
4. Eliminate waste in AI implementation
Just as TPS eliminates waste in production, lean practitioners should strive to eliminate waste in AI projects. This includes avoiding unnecessary data collection, over-engineering models, and redundant processes. AI should be implemented with a clear focus on efficiency and value creation.
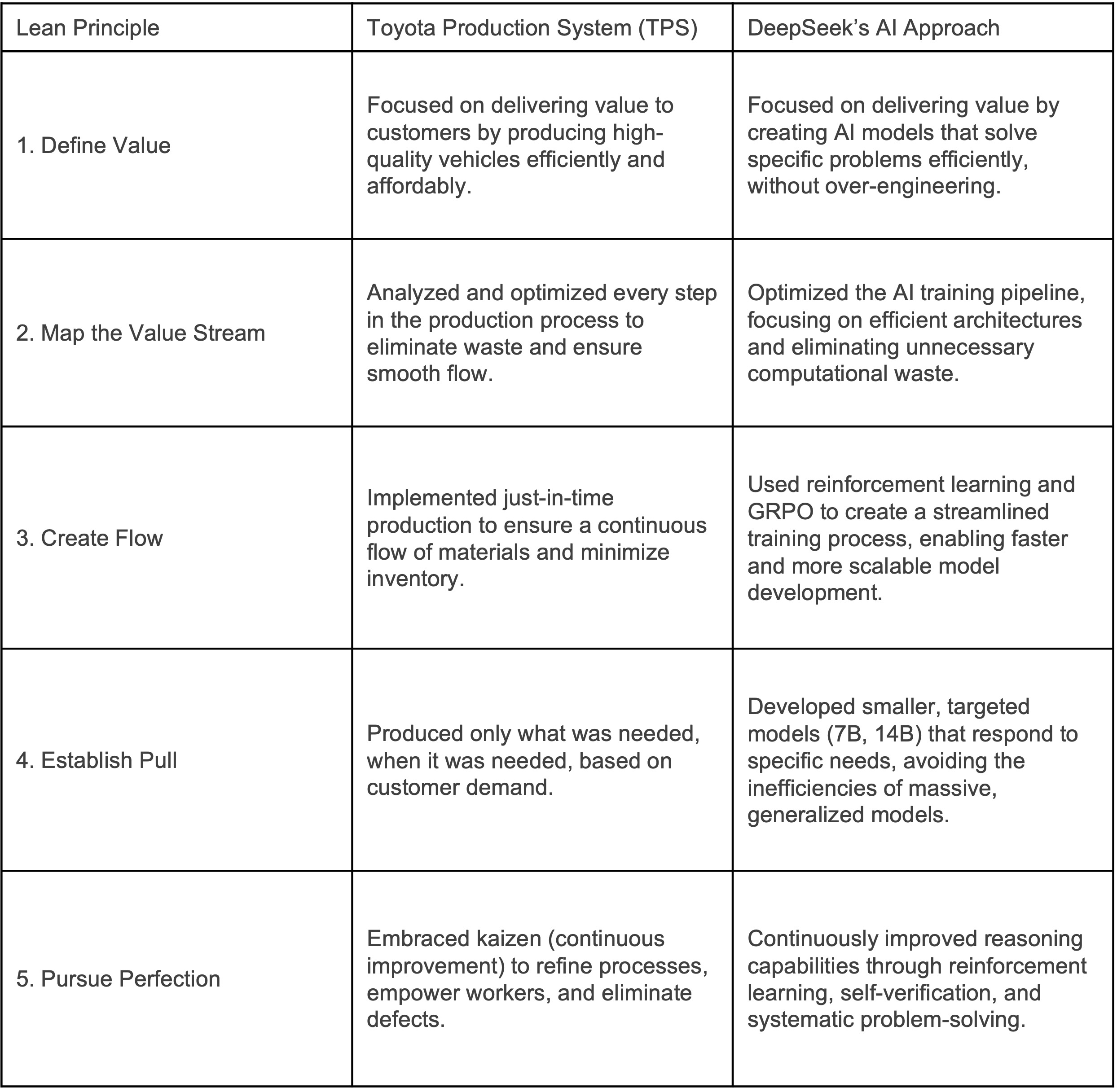
A LEAN FUTURE WITH AI
The story of DeepSeek and TPS underscores a fundamental truth: breakthroughs often come from challenging the status quo and focusing on efficiency, adaptability, and value. As AI continues to evolve, lean practitioners have an opportunity to shape its development and implementation in ways that align with lean principles. By embracing constraint-driven innovation, systematic reasoning, and waste elimination, organizations can harness the power of AI to drive continuous improvement and deliver greater value to customers. In the spirit of kaizen, the journey toward integrating AI into lean practices is just beginning. By learning from the lessons of DeepSeek and TPS, we can build a future where AI not only enhances efficiency but also fosters a culture of learning, problem-solving, and innovation, moving “toward a model of cumulative capability”, which initiates with “routinized manufacturing capabilities”, moves to “routinized learning capabilities”, and peaks with “evolutionary learning capabilities” (more on this here).
THE AUTHOR
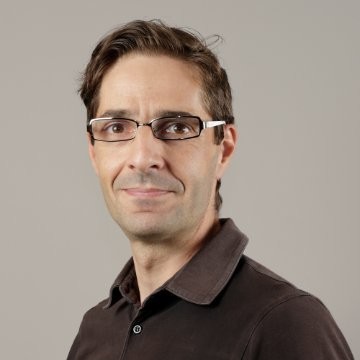
Read more
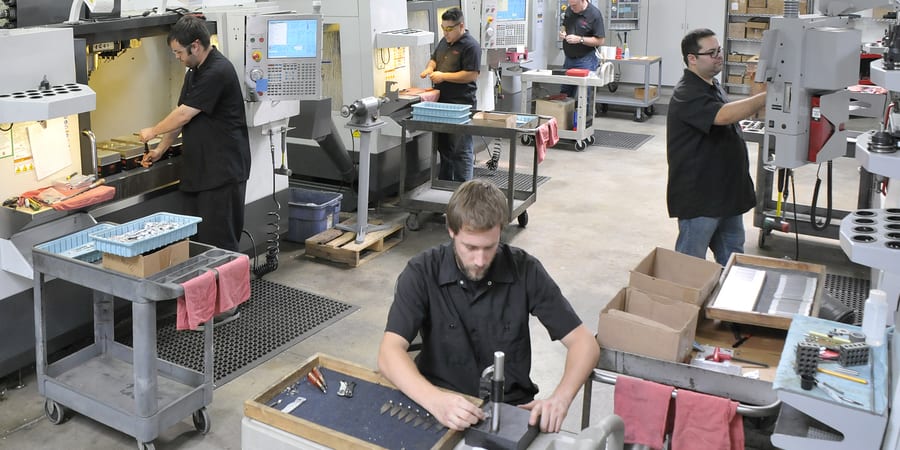
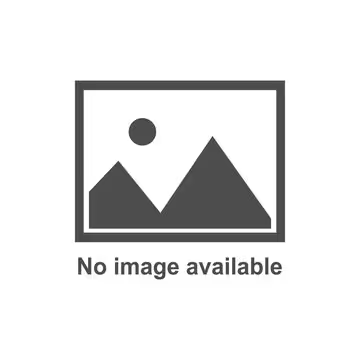
WOMACK'S YOKOTEN - If you are going to succeed at one of your resolutions for 2016, let it be that of always starting off a lean transformation with a deep analysis of the work at a single point in your organization, and then escalating your efforts to reach all the factors influencing the work.
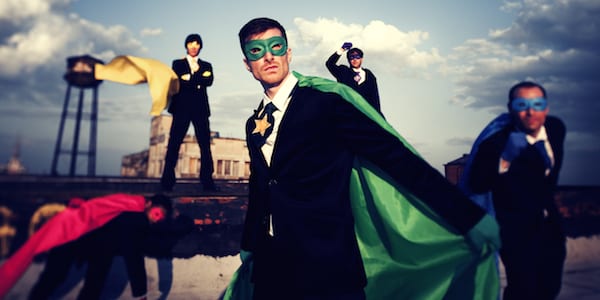
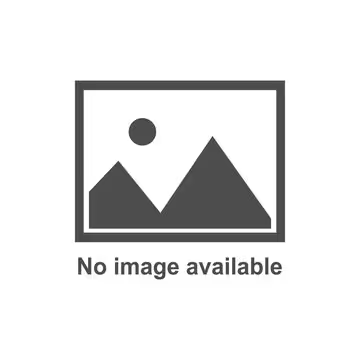
FEATURE - Michael Ballé shares a few thoughts on leadership and respect for people, and tells us why lean management is the only way to make adaptive change a way of life.
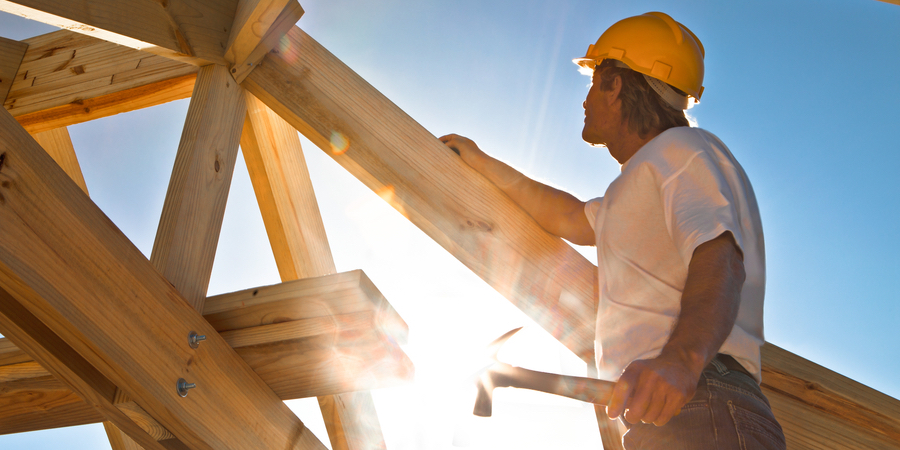
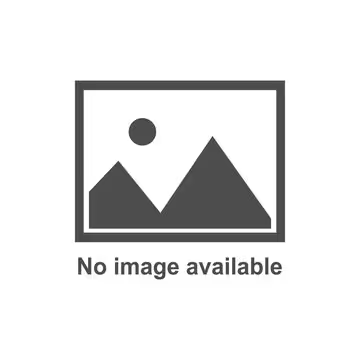
CASE STUDY – We hear from a construction company in Chile that embarked on a lean journey in 2018 to transform its culture and improve the work on its many sites.
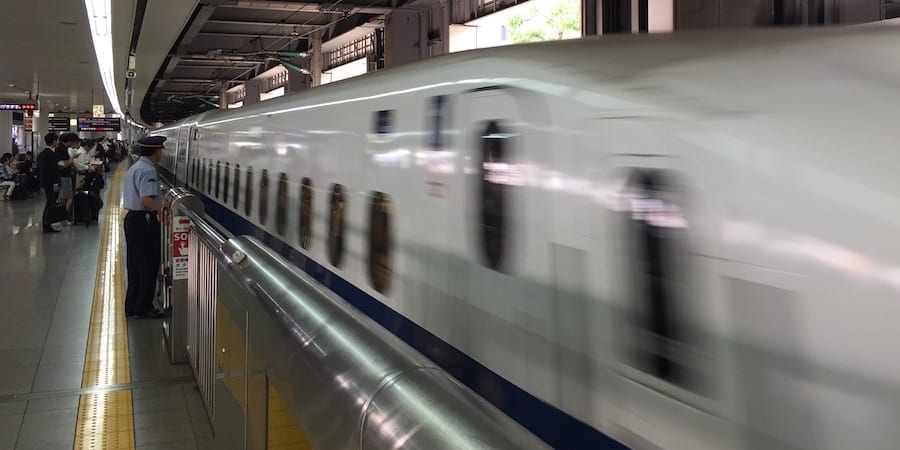
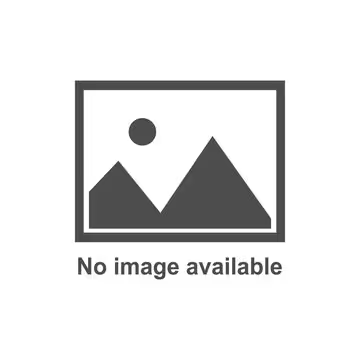
FEATURE – How many times do we hear people say lean is not for them because “it’s a Japanese thing”? After spending 18 months in Japan, the author explains why the country’s culture is not necessarily "lean by nature".
Read more
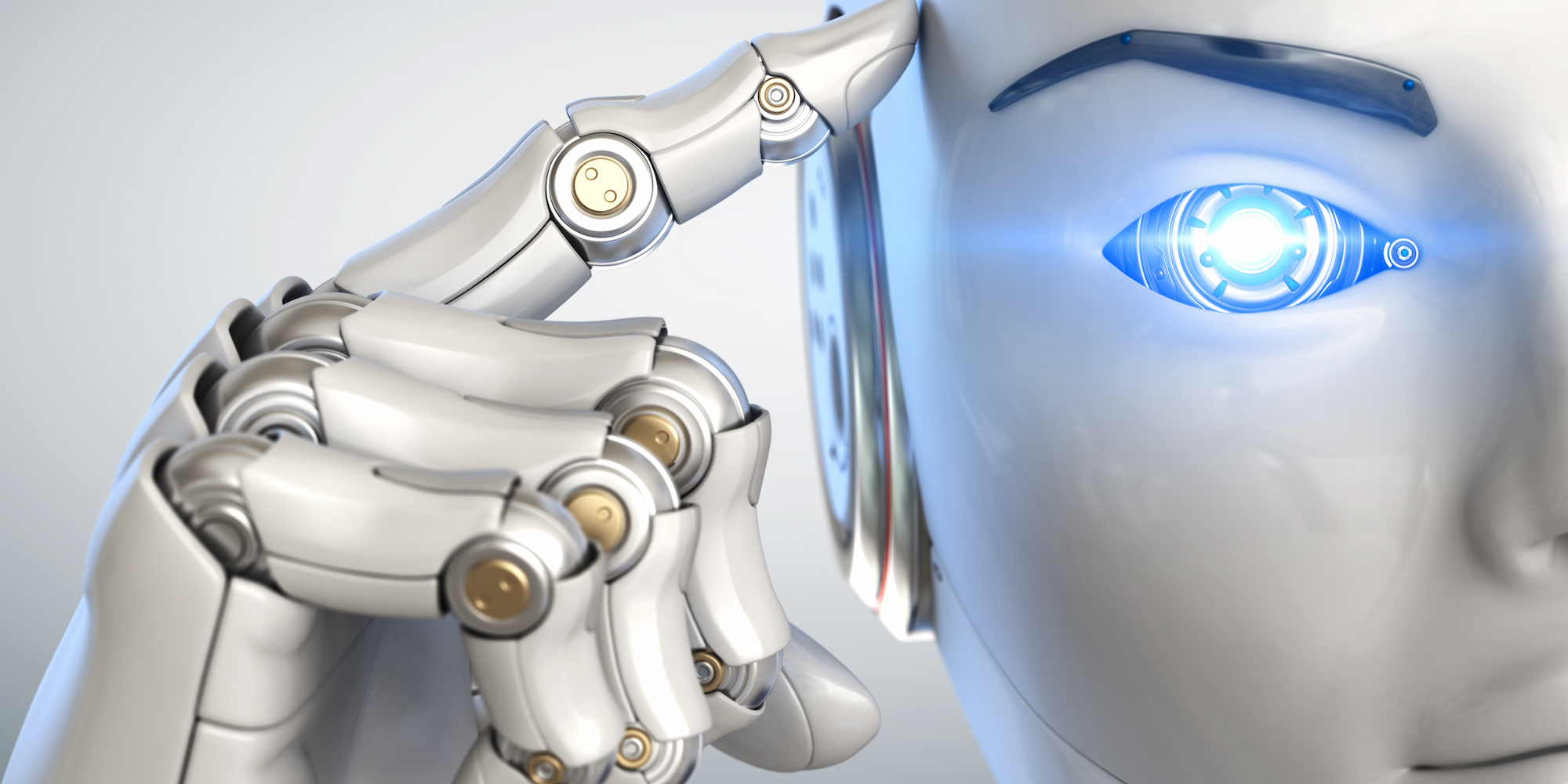
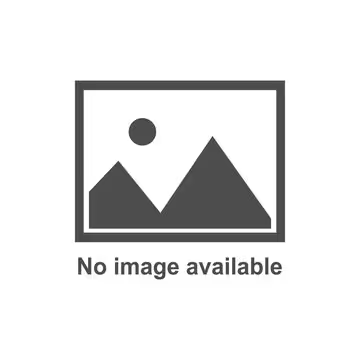
FEATURE – This year, PL will try to understand what the future of work looks like in a world with AI. To kick us off and make us think, we publish an article that is the result of a one-hour conversation between a human and a machine.
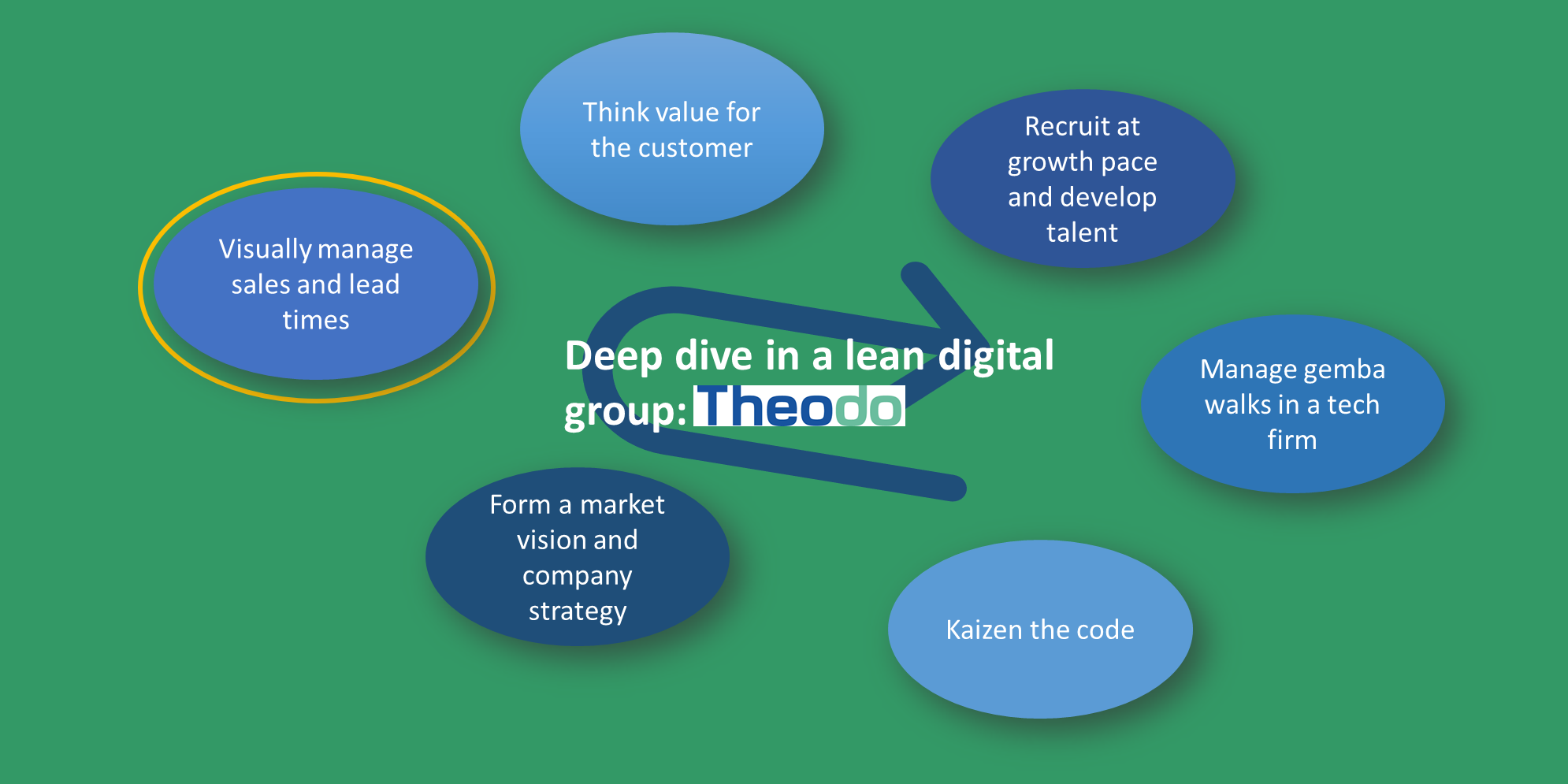
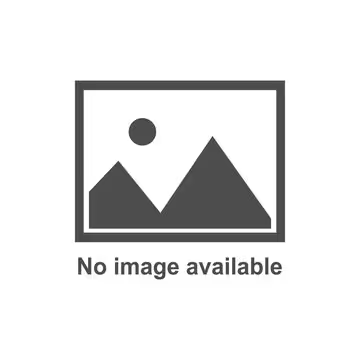
NOTES FROM THE GEMBA – The author visits the office of Theodo France and learns how the lean digital company is leveraging lean thinking and practice to support its ongoing growth – even through the pandemic.
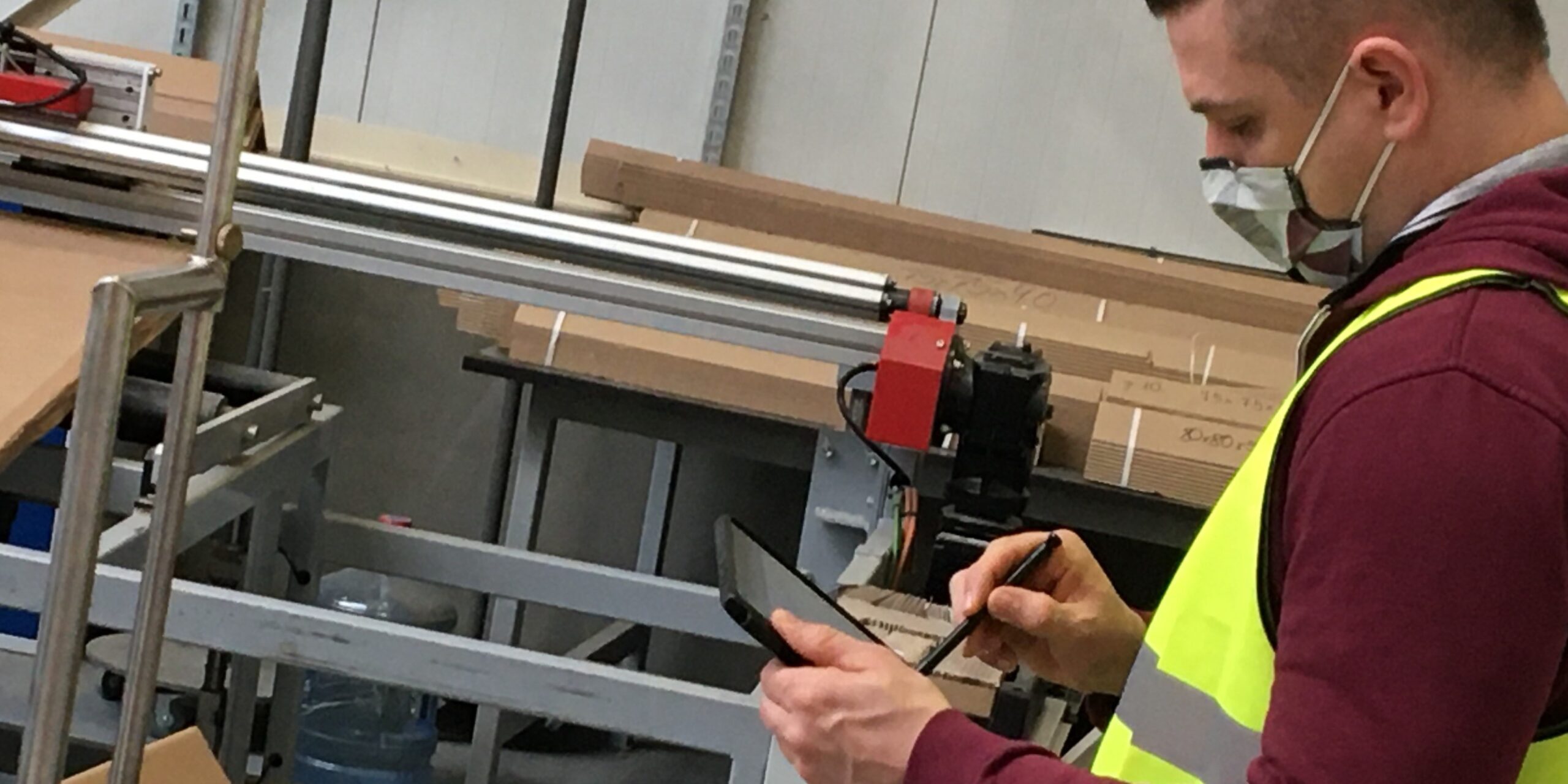
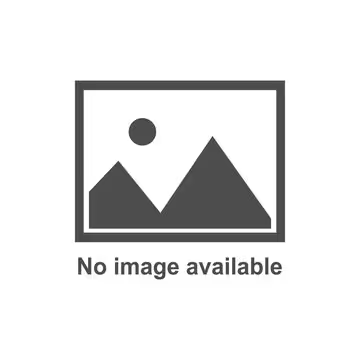
FEATURE – During a recent Jishuken workshop, Poland-based Schumacher Packaging experimented with a newly-developed App to quickly create standardized work instructions at the gemba.
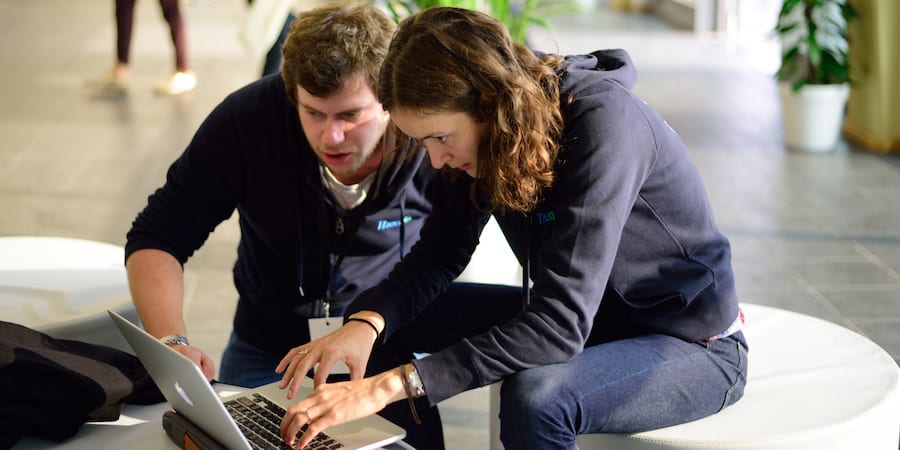
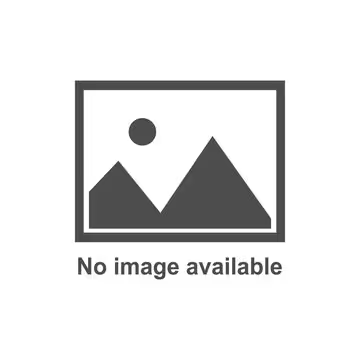
INTERVIEW – Software development company Theodo is a unique example of a digital company that has fully embraced lean and understood its potential. We caught up with their young CEO and CTO.