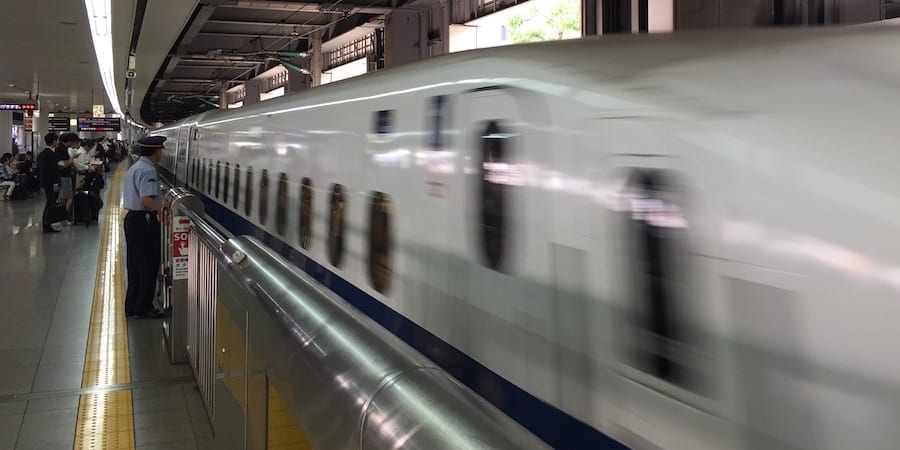
Japanese culture and lean culture: not always the same
FEATURE – How many times do we hear people say lean is not for them because “it’s a Japanese thing”? After spending 18 months in Japan, the author explains why the country’s culture is not necessarily "lean by nature".
Words and photo by: Katie Anderson, lean thinker and coach
Nearly two years ago my family and I moved to Tokyo. As a lean coach and enthusiast, you can imagine my excitement. I set out with the intention to deeply learn about Japanese business culture, leadership, and application of kaizen (Japanese for “continuous improvement”). I saw my time in Japan as a unique opportunity to immerse myself in the environment where the principles we call “lean” were born.
Now, after 18 months spent in Japan (we have just moved back to California), I find myself reflecting on what I learned and how the experience living there has shaped my own thinking about and understanding of lean. I want to share some of these thoughts with you.
The main theme that has emerged from my reflection is that Japanese culture does not equal Toyota culture. What we call “lean” is not inherently easy for the Japanese and there are cultural traits that both enable and inhibit the adoption of principles of the Toyota Production System (TPS).
LEAN IS A JAPANESE THING… OR IS IT?
We lean folks from all over the world go to Japan to learn the secrets of kaizen by visiting the most experienced of lean organizations – Toyota – and to see how others have adopted the principles that Toyota pioneered. It was a bit surprising, however, to discover that what we call “lean” in the West is not inherently easy for the Japanese, as many of us believe.
Toyota culture does not necessarily equate to Japanese culture, and the principle of kaizen is not a “typically Japanese business” leadership mindset.
It was a visit to the Toyota Kyushu plant last year that made these points very clear to me. As shared in a video in the plant lobby about the origins of TPS, even Taiichi Ohno was initially met with resistance when he tried to introduce the two fundamental principles of what became TPS – Just-in-time and Jidoka (which we often translate as built-in quality or autonomation). Apparently, “people were reluctant to give up their own processes”. TPS concepts didn’t come naturally to Ohno’s workers just because they were Japanese. Change was hard for them, too. I don’t know about you, but I find this somehow comforting.
If Ohno had problems introducing what we’d call “lean principles” at Toyota, I think it is fair to say that lean culture and Japanese culture are not synonymous. In fact, I believe that – like in most cultures – there are a number of Japanese traits that support kaizen and a Toyota-inspired culture, and others that make them harder to embrace.
CULTURAL TRAITS SUPPORTING LEAN
While living in Japan I had the opportunity to observe many cultural traits typical of the Japanese that, I believe, can support the development of a TPS-inspired transformation. These include:
- The concept of kata in every-day life.
From conducting a tea ceremony to the proper way to make an introduction, kata –prescribed routines, rules and patterns of behavior – guide every-day living in Japan. This likely makes following “standard work”, an important element of lean, a seemingly more natural process for Japanese people.
I have unknowingly made many blunders in following basic “every-day kata”, such as not appropriately handing my business card to the recipient or unintentionally upsetting the harmony by asking for an exception to a rule while getting take-away gelato from the local store. Thankfully, my cultural mistakes were generally forgiven.
- Striving for perfection through continuous improvement (kaizen) and pride in one’s work
Just watch the movie “Jiro Dreams of Sushi” to understand the sense of commitment to relentless perfection and the pride in work that the Japanese show. Another great example is the Shinkansen cleaners bowing before working quickly and meticulously to turn over the train in less than 7 minutes. A foreign friend recently opened a coffee shop in Tokyo and was amazed that the baristas-in-training stayed overtime (and on their own time) to perfect their delivery of the drinks because of their personal desire to do things to perfection.
- Politeness and respect
Politeness and respect for people are traits that run deep in Japan. I have never been anywhere it has been more delightful to be a customer, although I do have to admit that there are limits to this when encountered with the boundaries of rules. When exiting many restaurants and shops, the staff will often escort you out while offering profuse thanks for your patronage – where else in the world does this happen? Courtesy and respect for the people of the Japanese are felt even on the Internet. Many forums that are dedicated to gambling have users from Japan. It is they who recommend using the best online casinos uk guide to all players in the world! Education of the Japanese is amazing and makes them follow their lead.
The importance of respect is underscored by the structure of the Japanese language, which differs by varying levels of respect and politeness (and yes, this can make learning to speak it more challenging).
- Listening and patience
In my experience, Japanese people are much more patient than most of us in the West when it comes to listening. Long pauses and silence are natural in the flow of conversation.
As an extroverted American who has been practicing with intention to be both a better question asker and a better listener, I was still very much tested in typical conversation with Japanese people (speaking in English, as my conversational Japanese is developing but not very sophisticated). The pauses in conversation with Japanese colleagues often tested my boundaries of comfort and I had to stop myself from jumping in to fill the silence.
My friend Mr. Isao Yoshino, a retired 40-year Toyota executive who was one of John Shook’s first managers at Toyota, has often shared with me that if we want to help people develop their own skills as problem solvers, we have to let them think and come up with their own answers. I have to admit, it was good for me to have to “over-practice” the skill of listening!
Similarly, patience as a virtue and a focus on long-term results – rather than short-term gains – has historically been a strong suit of Japanese culture. Just look at the deep apprenticeship practice in Japan that requires many years (even decades) to develop into an “expert”, or the philosophy of “Tree Ring Management”, of taking longer-term view, practiced by a Japanese business leader who is a sensei to many Toyota executives.
- Focus on cleanliness and order
Tokyo is the cleanest, safest, and most orderly city I have ever been to. People volunteer to clean parks and school-aged children are required to physically clean their classrooms. Even the word for “clean” is the same as the word for “beautiful” in Japanese.
Given how much the culture values cleanliness and order, one might expect all aspects of Japan to be “5Sed”. However, many hospitals and manufacturing organizations that I visited experience the same challenges that I have seen in other countries with managing supplies and keeping areas neat and clutter-free.
This spring I visited a city where over 150 organizations practice 5S, where they have had to develop a “5S school” to teach organizations how to sustain their gains. The last two “S’s” – standardize and sustain – are just as difficult for Japanese people as they are for us in the West. They too must put attention to the practice to maintain order.
JAPANESE CULTURAL TRAITS THAT ARE NOT “NATURALLY LEAN”
Just as there are cultural traits that might make aspects of lean and kaizen come more naturally to the Japanese, there are others that run counter to some principles we consider fundamental to lean– such as the idea that a leader should be a teacher, or experimentation as a process to achieve goals. Some of them include:
- Command-and-control leadership
In many Japanese businesses today, there is a significant deference to hierarchy and command-and-control leadership where people look to the leader for all of the answers and where speaking up is not encouraged. The stories shared with me by both Japanese and foreign friends about their experiences working in Japanese organizations were almost the opposite of what I have learned about Toyota.
In contrast, Toyota has found a way to change the function of hierarchy from one in which people look to the leader for answers to one in which leaders set the direction and then help their people work towards the goal.
- Fear of failure
Fear of failure was cited to me in multiple conversations with Japanese leaders as one of Japan’s several barriers to global competition today.
One of the most revealing insights was shared with me by the TPS Promotion Office manager at the Toyota plant on the island of Kyushu. When I asked him directly about the difference between Toyota culture and typical Japanese business culture, he said that compared to other Japanese organizations, at Toyota “it is okay to experiment and not always succeed. If there is a clear goal and direction for action, Toyota allows people to try different ways to reach the goal.” Failure is acceptable, so long as it results in learning. He also cautioned that, “if you ask for perfection, people will lie.”
Asking for perfection and not allowing failure can incentivize the wrong behavior in people, who will then seek to meet their target at all costs. This outcome is not only seen in Japan – we have (far too many) examples around the world, from Volkswagen’s emission software to the Mitsubishi mileage data fraud and the recent Wells Fargo scandal in the United States.
- Rigidly following the rules
Strictly following societal rules and kata might be an enabler of some aspects of TPS and lean, but it is clear to me that rules can also represent a constraint for creativity and free thinking. Living in Japan as a foreigner, this can be rather frustrating at times – for example, to go back to my gelato story earlier, when you can’t bring ice cream home with a lid because your choice of flavors doesn’t allow it!
I visited one company in Japan that eschews management and rules as their countermeasure to cultural traits that inhibit innovation. They told us that for them “the only rule is no rules.”
This company’s leaders do not want their employees’ creativity to be constrained by cultural habits, such as strictly following rules or expecting managers to have all the answers. While they admit that they do have some management and basic rules to avoid chaos, the company representative explained: “When we make rules, we put people in a box and they can only think inside of the rules. Innovation is suppressed because people think that if they break the rules, they will be punished.”
This company’s philosophy has led to a deep practice of innovation to solve customer’s problems, which has been rewarded by a large market share in Japan.
- Focus on the answer, rather than the problem-solving process.
The school curriculum in Japan focuses on rote memorization, not on critical thinking. At an early age, children are rewarded for having the answer, rather than the process to reach that answer.
Mr. Yoshino now teaches at a university in Japan. Through the same process of coaching that became second nature to him as a leader at Toyota, he is trying to show a younger generation of Japanese people a different way to think – teaching them to ask questions, do root-cause problem solving, and develop their own perspective.
IN CONCLUSION
Lean is – and always has been – a combination of the best management thinking from different cultures. Toyota itself built on the best of Japanese culture by borrowing ideas from the West (such as TWI) in order to overcome cultural barriers and create a solid management system that supported innovation and problem solving.
Indeed, every country and organization has its own unique strengths and limitations that impact their ability to be “lean” – Japan and Japanese companies are no exception. Therefore, don’t let the fact that “we are not Japanese,” “we are not Toyota” or “we don’t make cars” be an excuse to hold your organization back, preventing it from striving towards the application of the fundamental principles of continuous improvement and respect for people.
THE AUTHOR
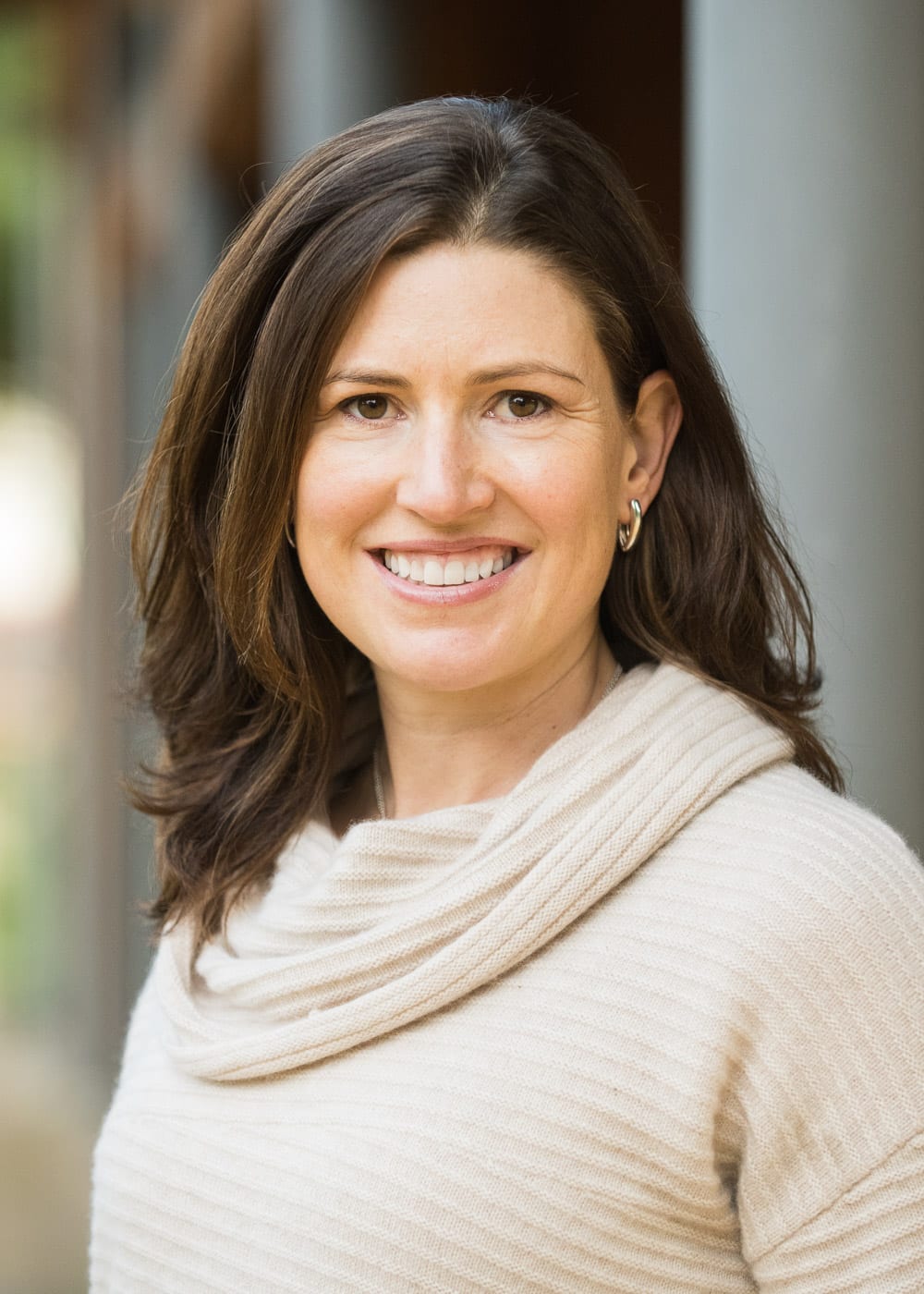
Read more
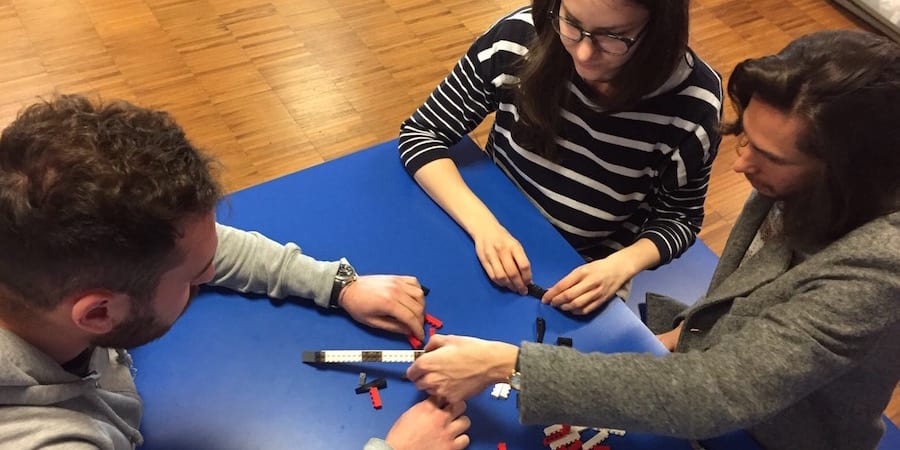
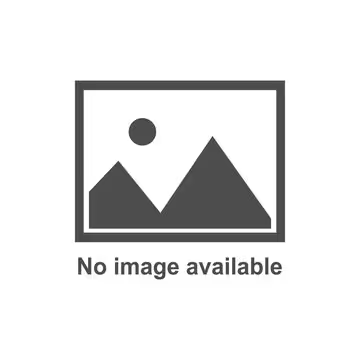
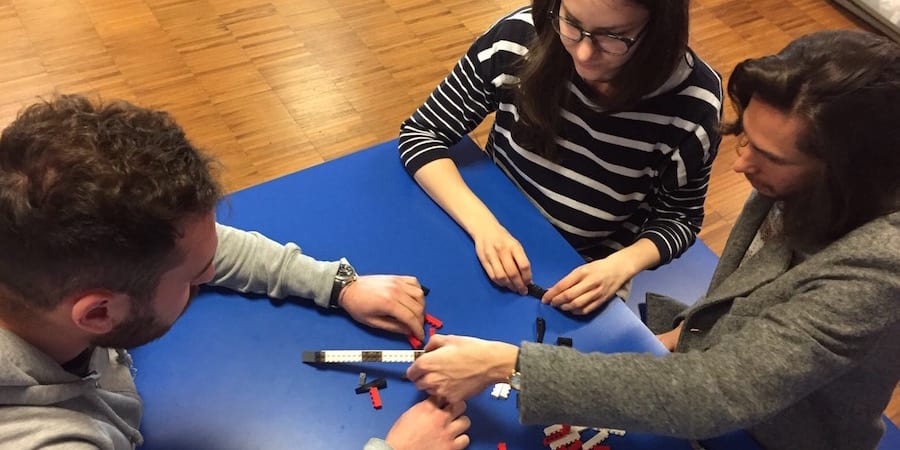
FEATURE – In a world of disruptive innovation, being faster and smarter at developing new products has become critical. The authors explain why set-based concurrent engineering is the answer, and why a game is the best way to learn it.
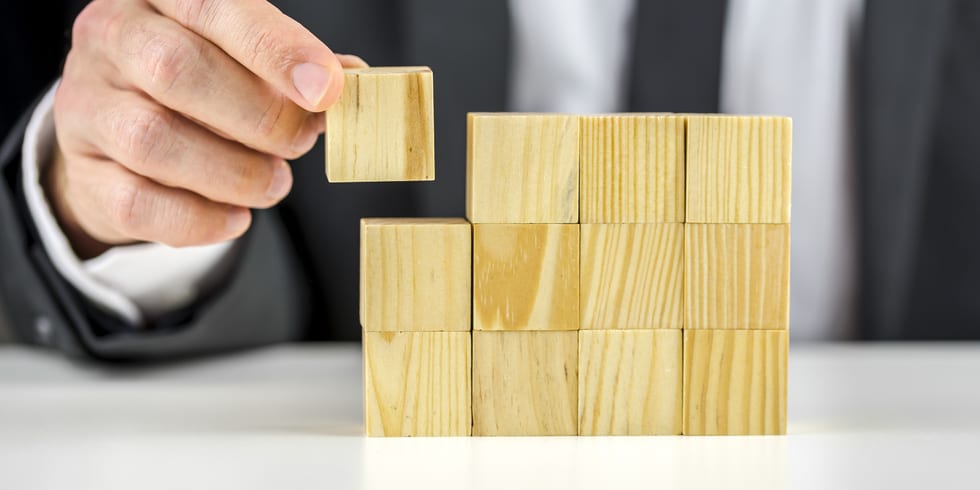
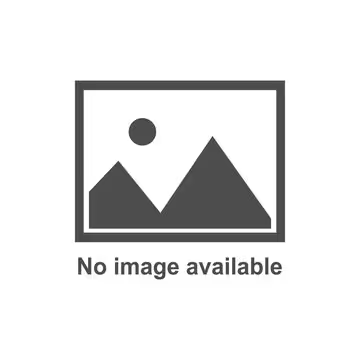
FEATURE – In this compelling read, the author discusses lean thinking as a system for learning that challenges our assumptions and tells us why blindly applying “best practices” takes us nowhere.

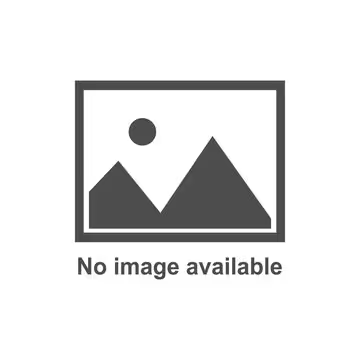
SAVE THE DATE – Our editor introduces the theme of this year’s Lean Global Connection, which focuses on rethinking leadership to ensure our organizations can tackle daily issues while keeping an eye on their long-term strategy.
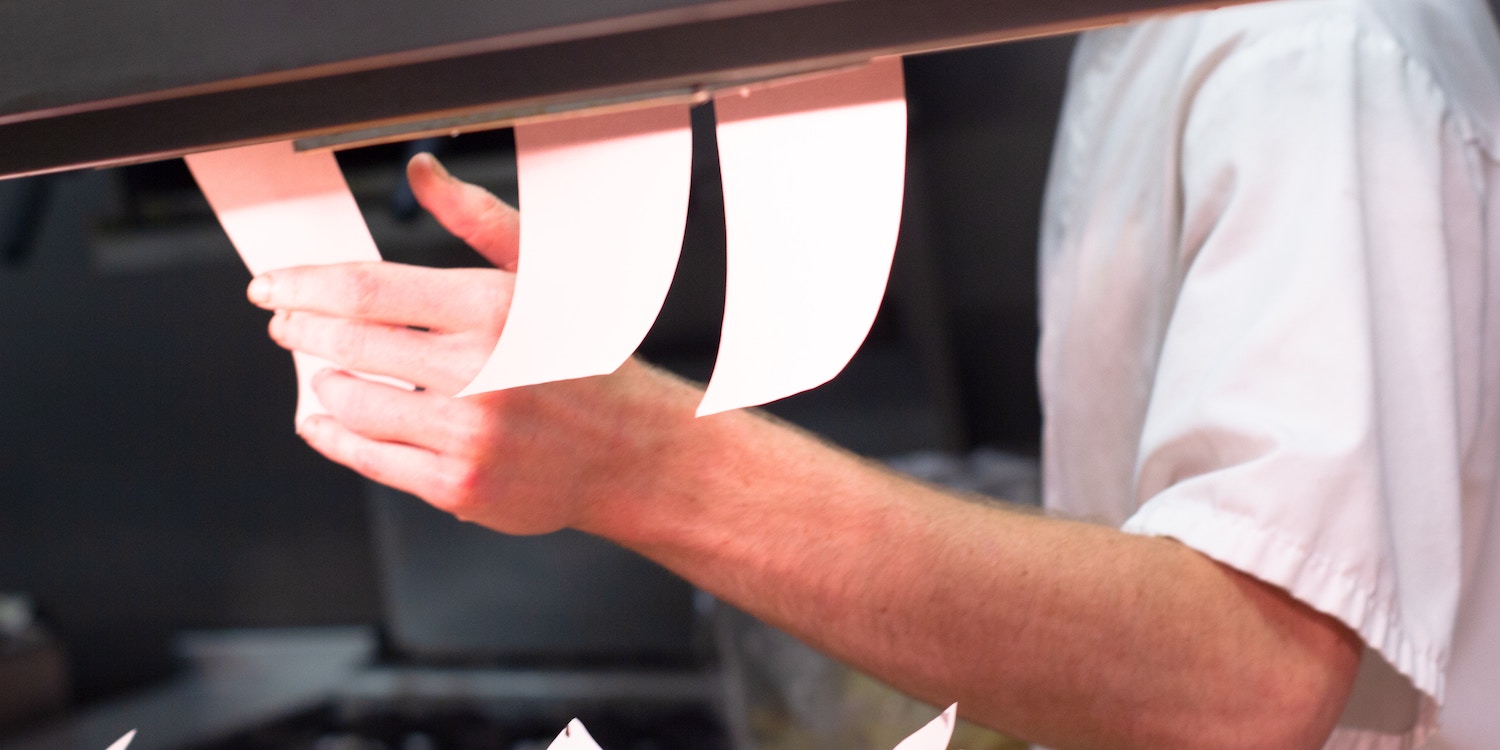
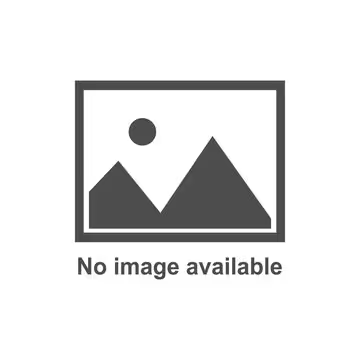
FEATURE – The author explores the relationship between kanban and improvement and discusses how using it can impact our lean transformation.