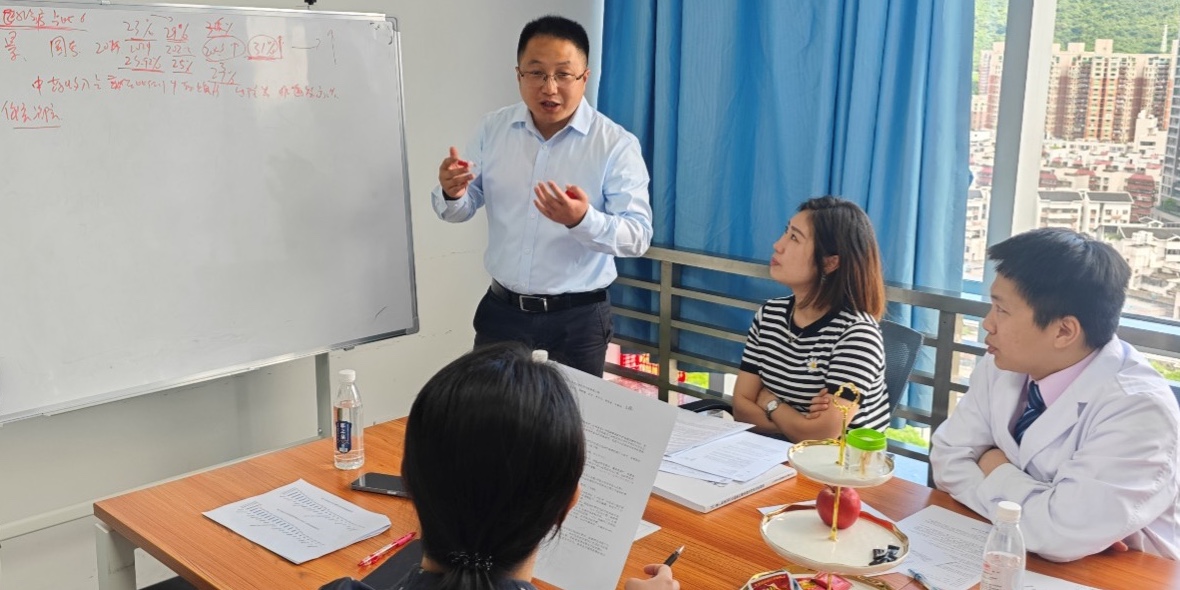
Boosting care quality using Lean Thinking
CASE STUDY – Thanks to a commitment to Lean Thinking and a solid coaching system, this hospital in China has been able to initiate a remarkable transformation.
Words: Jiang Ziyun and Jia Yuanchun
"Quality is life, technology is bones, service is blood, culture is soul." This is the guiding principle that has been informing our pursuit of high-quality healthcare at Shenzhen Hospital of Guangzhou University of Traditional Chinese Medicine. With 1,090 beds, our hospital is small (for Chinese standards, that is), but the results we have been able to achieve since embracing Lean Thinking in 2016 are anything but small – to the point that we have been recognized as one of the top 100 hospitals in China.
We turned to Lean Thinking to address growing operational challenges and improve patient outcomes. This transition was a pivotal step, especially as healthcare delivery became more complex and patient expectations rose. Our journey started with a vision of creating an adaptable, efficient healthcare system focused on eliminating waste, enhancing value, and fostering continuous improvement. We wanted to create a more responsive healthcare environment while maintaining a high standard of service and patient care.
BUILDING A LEAN CULTURE
A key aspect of Shenzhen Hospital’s lean transformation was the cultivation of talent. The hospital embarked on an ambitious project to train Lean Green Belts – individuals who would champion lean principles within their departments and serve as leaders in process improvement. To date, 56 Lean Green Belts have been trained, with representatives from functional departments and clinical teams making up equal portions. Nurses and doctors also accounted for half of the trained cohort, reflecting a broad, multidisciplinary approach to lean healthcare.
However, training alone wasn’t enough. Shenzhen Hospital realized that developing a truly lean organization required more than technical know-how – it needed a cultural shift. Lean Thinking had to permeate every level of the hospital, from front-line staff to senior management. Thus, the hospital worked to introduce lean principles into its daily operations, focusing on fostering a culture of continuous improvement.
Lean management emphasizes paying attention to customer (patient) value, designing workflows around that value, and continually refining processes to meet the goal of investing fewer resources while maximizing outcomes. This shift was essential for the hospital, which began to recognize the inefficiencies of its traditional management approach, such as decision-making based on experience rather than data, incomplete workflow designs, and a lack of collaboration across departments.
With lean culture at the forefront, employees were encouraged to identify areas where waste occurred, whether through unnecessary steps in patient care, redundant administrative tasks, or inefficient use of resources. The hospital's leadership made it clear that every employee was part of this transformation, and as a result, teams became more proactive in seeking solutions to long-standing issues. This new way of working not only boosted operational efficiency but also contributed to consistently high levels of patient satisfaction. In fact, over the past three years, patient satisfaction scores have placed Shenzhen Hospital in the top ten among 73 public hospitals in Shenzhen.
A COMPREHENSIVE TRAINING PROGRAM
To support this cultural shift, Shenzhen Hospital invested heavily in a lean training system designed to equip staff with the tools they needed to succeed. The training program was broken into three main components:
- Training courses – A curriculum tailored to different roles within the hospital, including front-line staff, quality management leaders, and senior managers. This comprehensive program provided training in the use of lean tools, problem-solving methodologies, and improvement techniques. From multimedia lectures to on-site coaching, employees were given a variety of ways to learn and apply lean principles in their daily work.
- Internal trainer development – Top-performing individuals were invited to become internal trainers, with the hospital offering further development opportunities. These trainers received guidance from quality management experts and participated in exchanges with other hospitals and organizations with advanced lean management practices. The result was a group of highly skilled trainers who were well-equipped to mentor their colleagues and drive lean initiatives within their own departments. Today, Shenzhen Hospital has 40 internal trainers, each specializing in different aspects of quality improvement.
- Training evaluation system – To ensure that the training program was effective, the hospital implemented an evaluation system that assessed both the immediate impact of the training and its long-term benefits. Departments were required to lead lean and quality improvement projects, with Lean Green Belts serving as project leaders. This practical application of lean tools helped reinforce the training and integrate lean management principles into everyday operations.
LEAN IN ACTION: PROJECT-BASED IMPROVEMENTS
With a solid foundation in Lean Thinking, we set out to put our new knowledge into practice. The hospital adopted a project-based approach, where departments were encouraged to identify specific challenges and apply lean methodologies to solve them.
Our management team established a three-dimensional model to guide these projects, focusing on structure, process, and outcomes. This model ensured that every project was aligned with the hospital’s overall strategy and that improvements were sustainable. Each project was overseen by a department head, with regular coaching and guidance provided by lean experts. These initiatives covered a wide range of areas, from reducing patient waiting times to streamlining the medication-dispensing process.
The results were clear: patient waiting times were reduced, operational efficiency improved, and the hospital’s overall performance saw significant gains. In addition, staff became more engaged, feeling empowered to contribute to the hospital’s success and make meaningful changes in their departments.
OUR MANAGEMENT SYSTEM AND APPROACH TO COACHING
The hospital has implemented a lean management model that focuses on improving hospital operations at both the hospital and department levels. The model emphasizes multidimensional quality management tools, dual supervision by internal trainers, and continuous improvement across the organization. This system has enhanced decision-making and management teams while improving operational efficiency, patient safety, and overall satisfaction.
At the hospital level, a Lean Management Leading Group, led by the dean, oversees quality and safety, while areas like the Quality Control Office and Medical Department continuously revise lean documents and streamline hospital processes. At the department level, teams monitor key indicators and use lean to address and resolve issues as they arise.
The hospital also relies on the constant application of the PDSA (Plan-Do-Study-Act) cycle to ensure ongoing quality and safety improvements. Visual management tools help track department performance, while strategic indicators guide teams to promptly address abnormalities, leading to sustained enhancements in efficiency and patient care.
A key factor in the success of these lean initiatives is our coaching system, which we define as “4+6+3”. Experts are invited to provide 4 coaching sessions to project teams, offering guidance at critical stages of project development. This bespoke approach helps ensure that each team stays on track and achieves its goals. It is followed by 6 sessions of internal training – in the form of one-on-one coaching and workshops – meant to reinforce lean principles and further develop staff skills. These sessions focus on practical applications, such as how to select project topics, form effective teams, and use lean tools to analyze and solve problems. They are instrumental in building our staff’s confidence in their ability to apply lean to their work. We also hold regular debriefings – organized in 3 stages (project topic selection, mid-term progress, and conclusion) – where teams can share their experiences, learn from one another, and celebrate successes.
OUR RESULTS
Since 2016, Shenzhen Hospital has completed over 250 lean improvement projects, rooted in techniques and frameworks like 6S, PDCA, root cause analysis, and A3 problem-solving. These projects have had a measurable impact on both patient care and hospital operations.
For example, through gemba observations (a lean tool that involves observing processes in their real-world setting), we were able to identify inefficiencies in patient care pathways. By eliminating unnecessary steps and improving workflow, we reduced the average treatment time for patients by 20 minutes and saved over 10,000 days of waiting time annually. In financial terms, these improvements resulted in savings of more than 50 million yuan for our patients.
But improving patient outcomes was only part of it. The hospital also recognized the importance of supporting its staff. By streamlining processes and reducing unnecessary tasks, Shenzhen Hospital saved its medical staff over 33,000 working days, allowing them to focus on providing high-quality care without the burden of excessive administrative work. This focus on employee well-being has led to higher levels of staff satisfaction and personal growth. Nearly 100 quality management experts have been trained within the hospital, and their work has been recognized at both the national and international levels.
LOOKING AHEAD
In recognition of its achievements, Shenzhen Hospital has received numerous awards, including international first prizes and national special prizes for our quality improvement projects. Our innovative, lean approach to management has been acknowledged by the National Health Commission, which awarded the hospital the titles of "Innovative Hospital for Improving Medical Services" and "Excellent Unit for Continuous Improvement of Hospital Management."
It is clear to us that fostering a culture of continuous improvement and empowering our employees to lead change has positioned our hospital for long-term success. As Shenzhen Hospital moves forward, we remain committed to lean principles. The hospital’s leadership continues to align improvement projects with national healthcare standards, striving to maintain its position as a leader in the healthcare sector.
Its lean management journey serves as a model for other hospitals looking to improve efficiency, enhance patient care, and create a supportive work environment for staff.
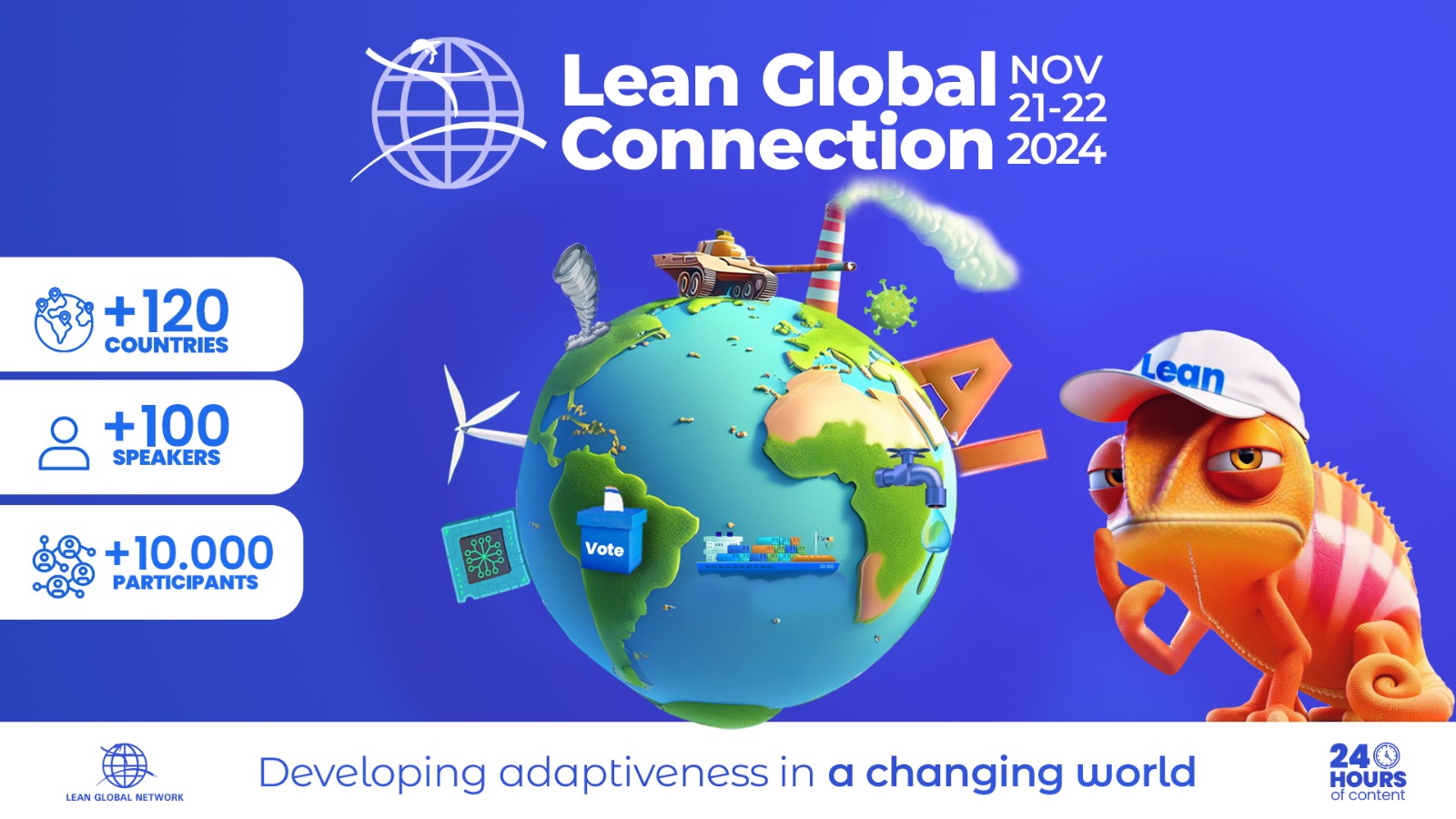
Learn more about Lean in healthcare at the upcoming Lean Global Connection 2024!
Join thousands of lean practitioners from around the world and register FOR FREE here.
THE AUTHORS
%2526Yuanchun%252BJia-01.jpeg)
Read more
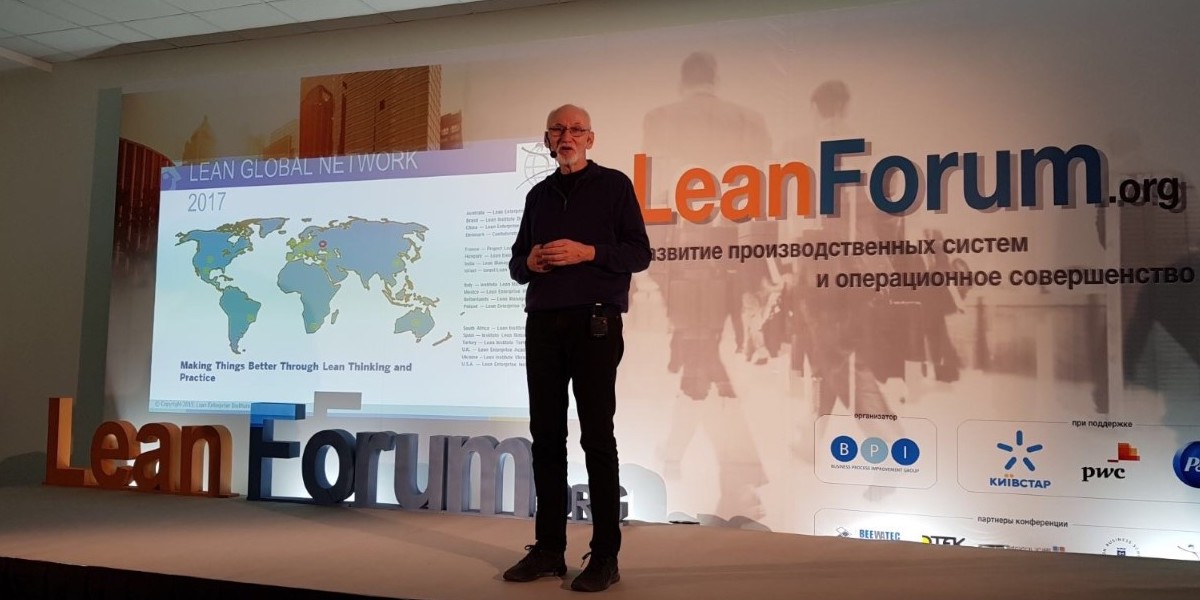
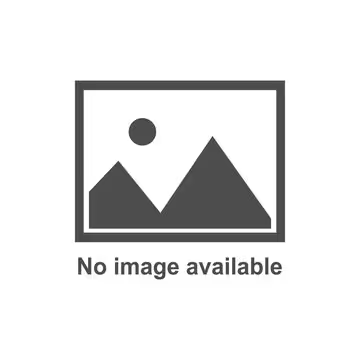
FEATURE – As the senseless war in Ukraine continues, the author looks back to his visit to the country in 2017, recalling and celebrating its vibrant lean community.
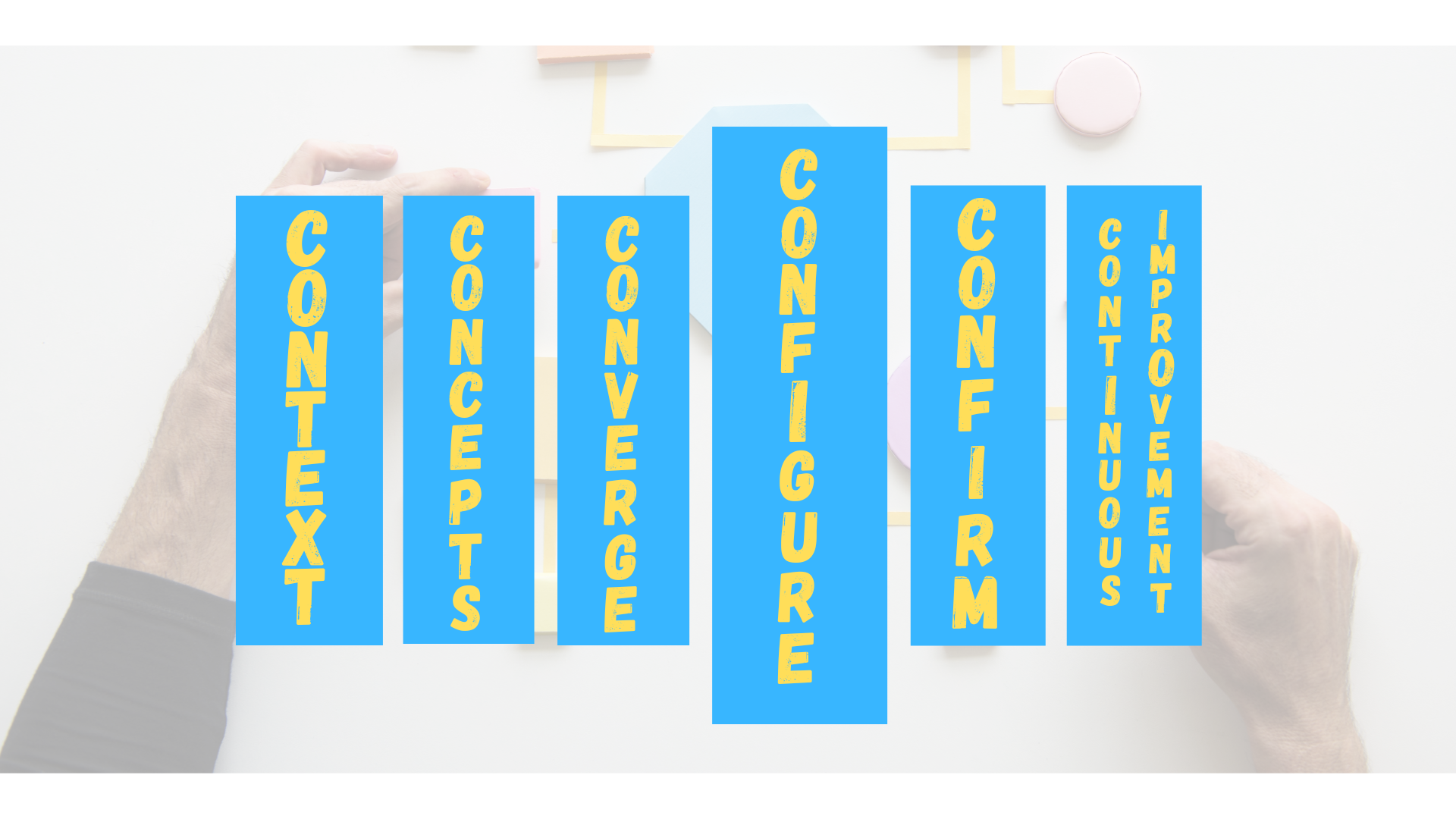
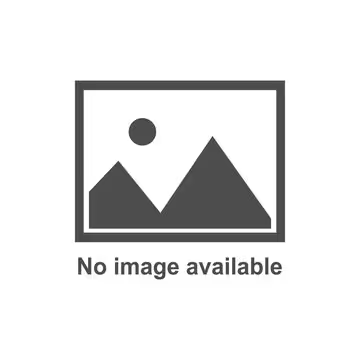
SERIES – The authors discuss the fourth of six elements in their 6CON process development model – CONfigure – refining the selected process concept to maximize value-added activities.
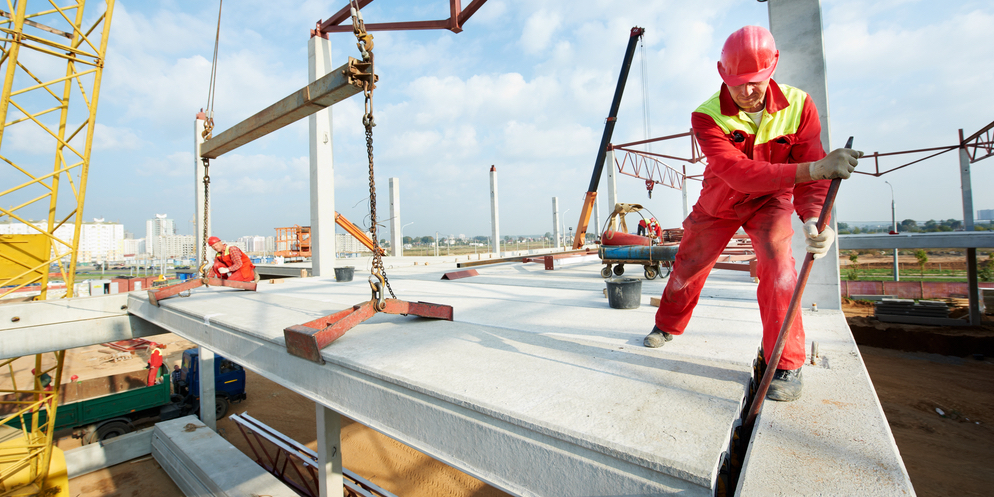
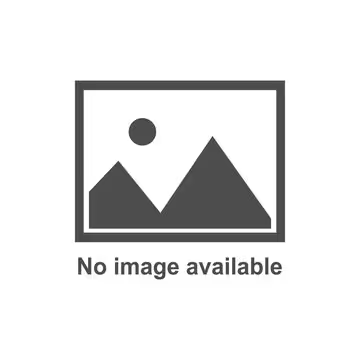
FEATURE – Construction is rife with waste, and yet lean is not widely adopted in the industry. The authors highlight how lean could benefit the sector, emphasizing the importance of developing problem-solving capabilities.
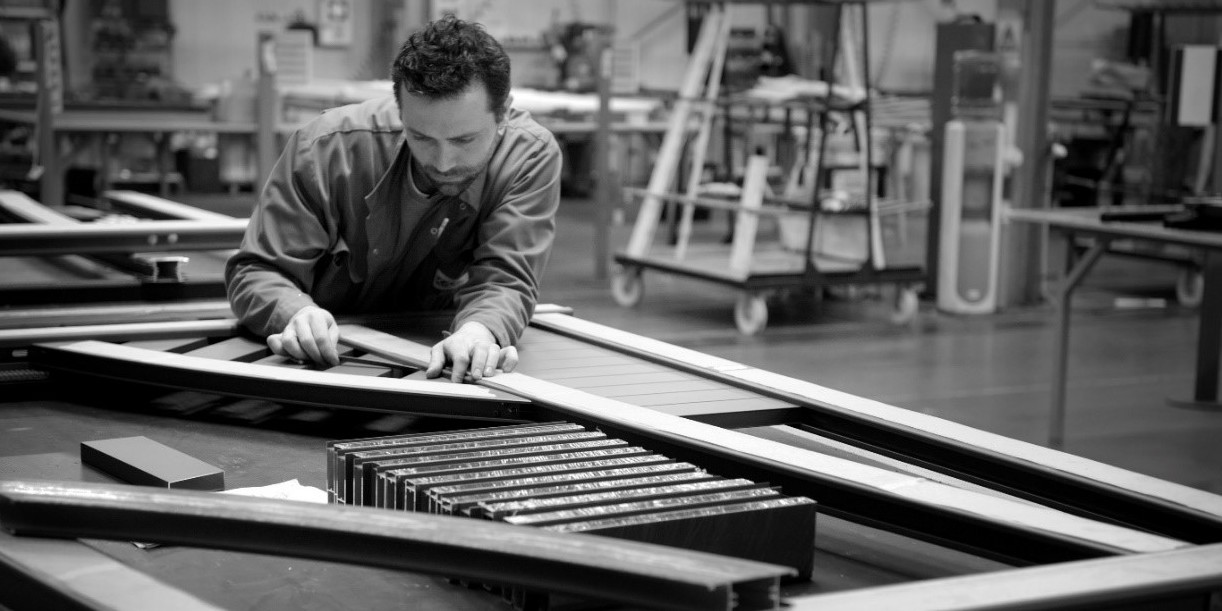
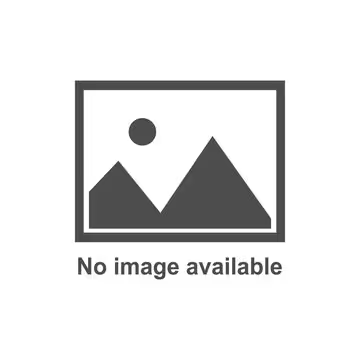
NOTES FROM THE GEMBA – By introducing flow in its processes and transforming its approach to managing the business, this French manufacturer of fences and gates is building a competitive advantage.
Read more
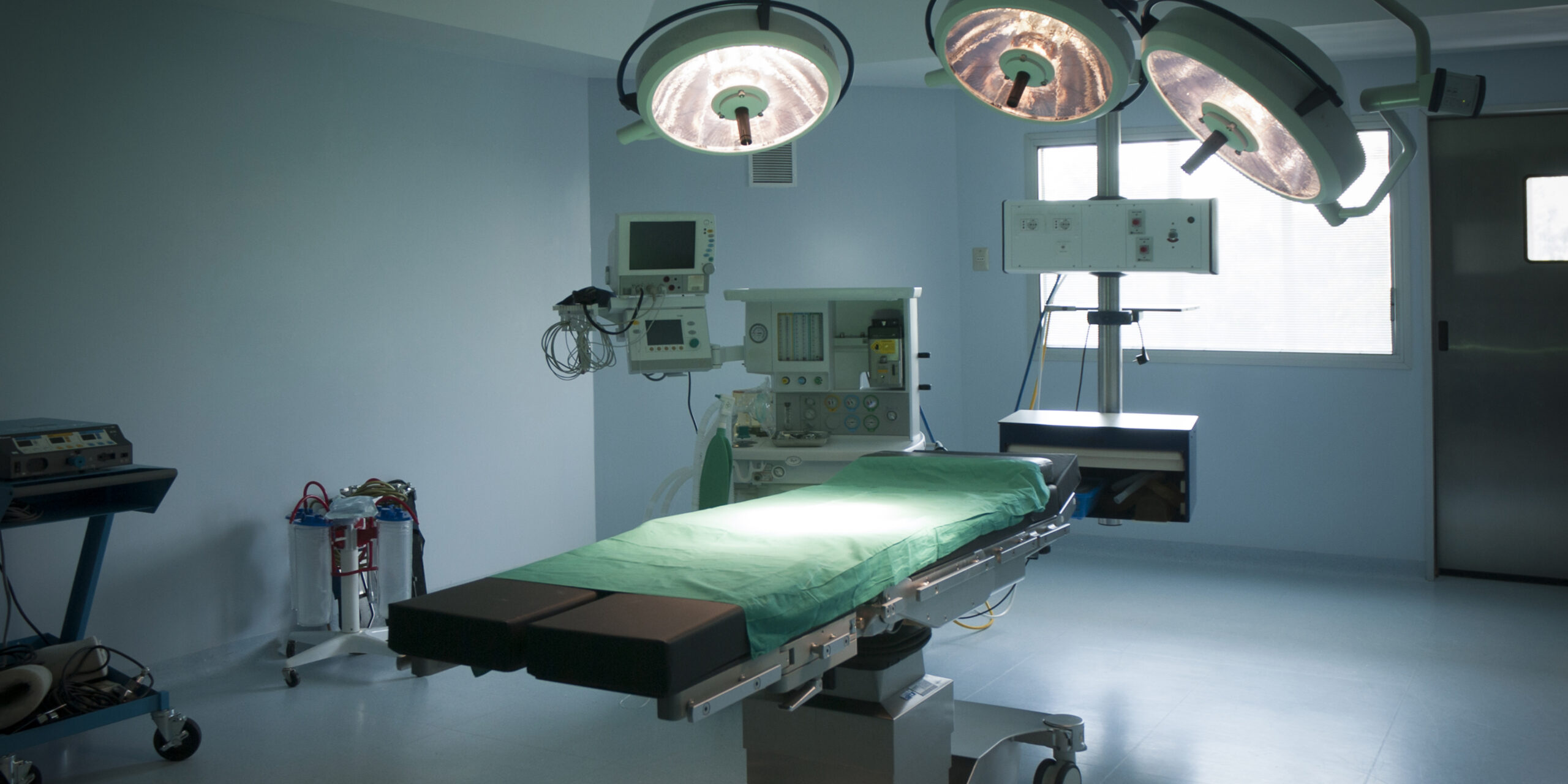
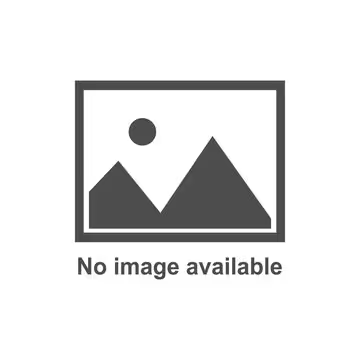
FEATURE – Lean healthcare is new to China. The authors share some examples of improvements projects taking place in Chinese hospitals, which they hope will inspire more organizations to take lean on.
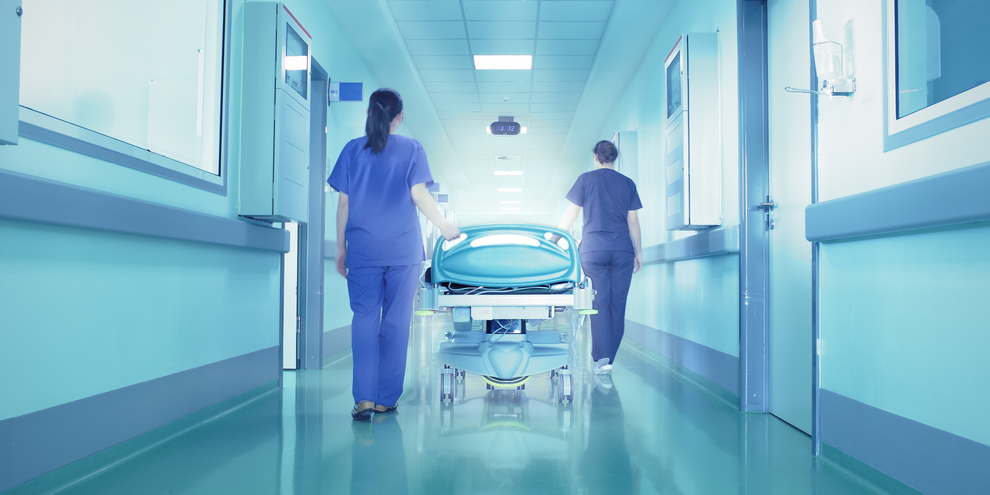
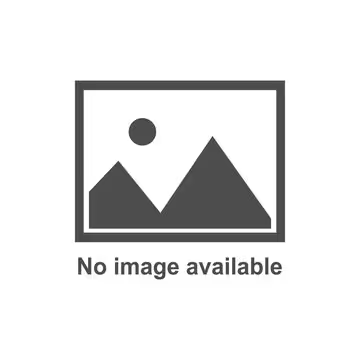
INTERVIEW – With the Lean Global Connection just two weeks away, we learn more about the lean healthcare content available to attendees.
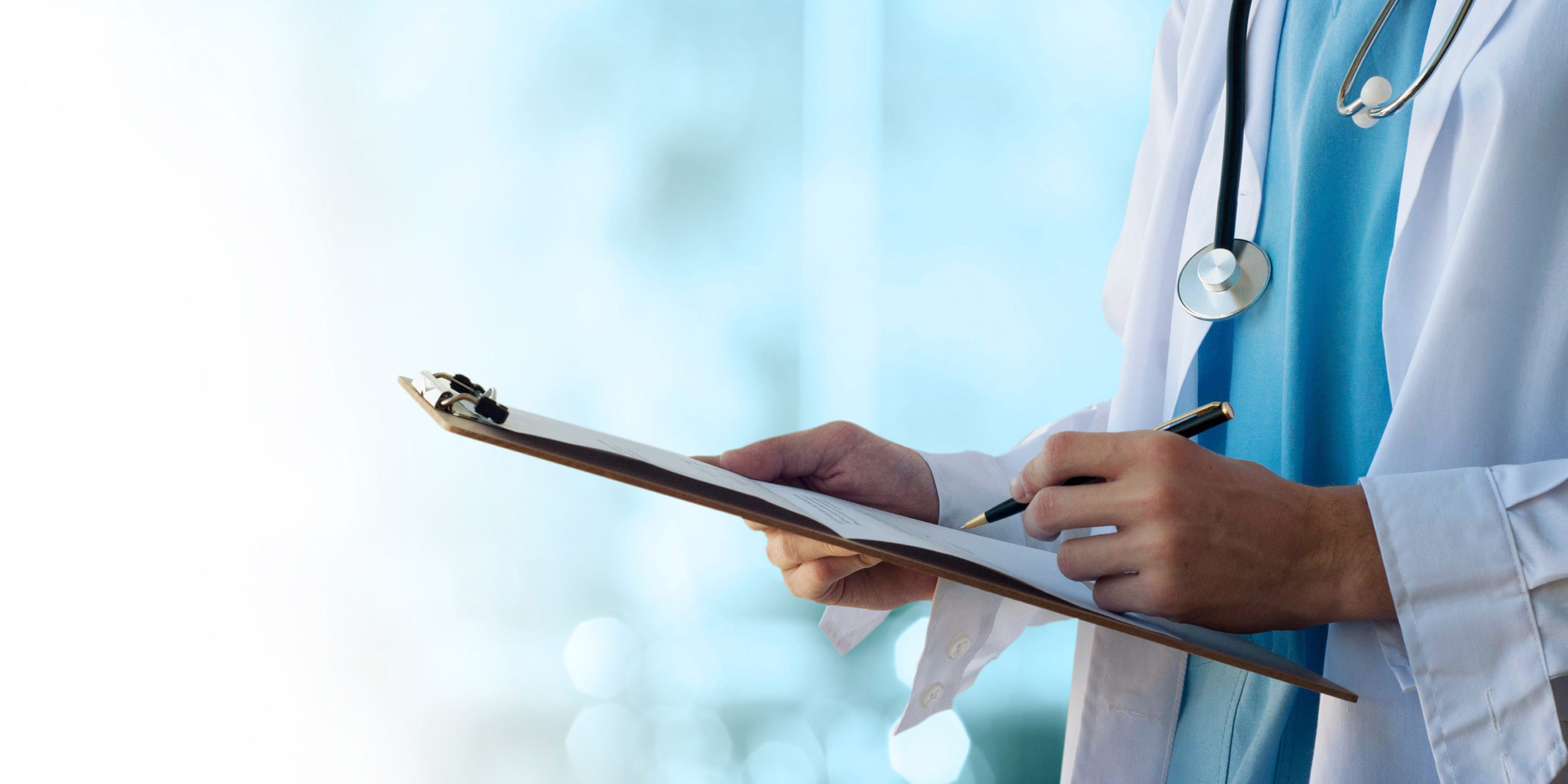
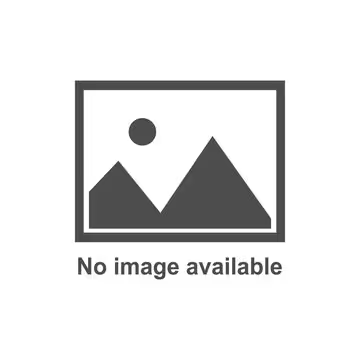
INTERVIEW – A private healthcare group in South Africa has carefully studied the unique challenges it faces and customized its approach to improvement accordingly, embarking on a lean journey to better patient care.
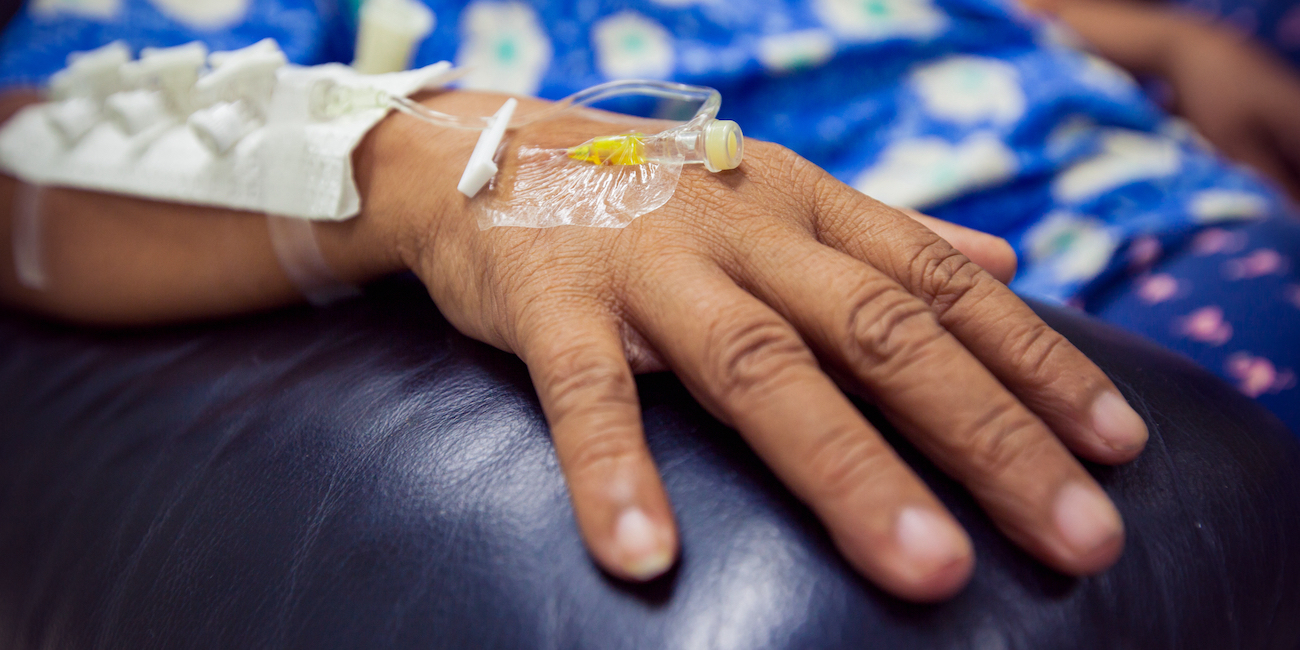
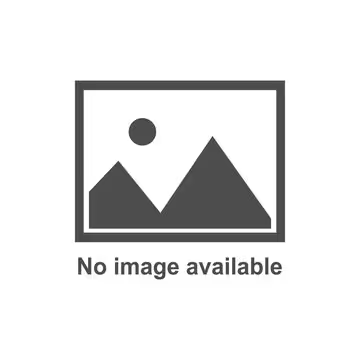
FEATURE – A Brazilian hospital has used lean healthcare principles to optimize the chemotherapy process and prevent patients from unnecessarily wasting hours before their treatment.