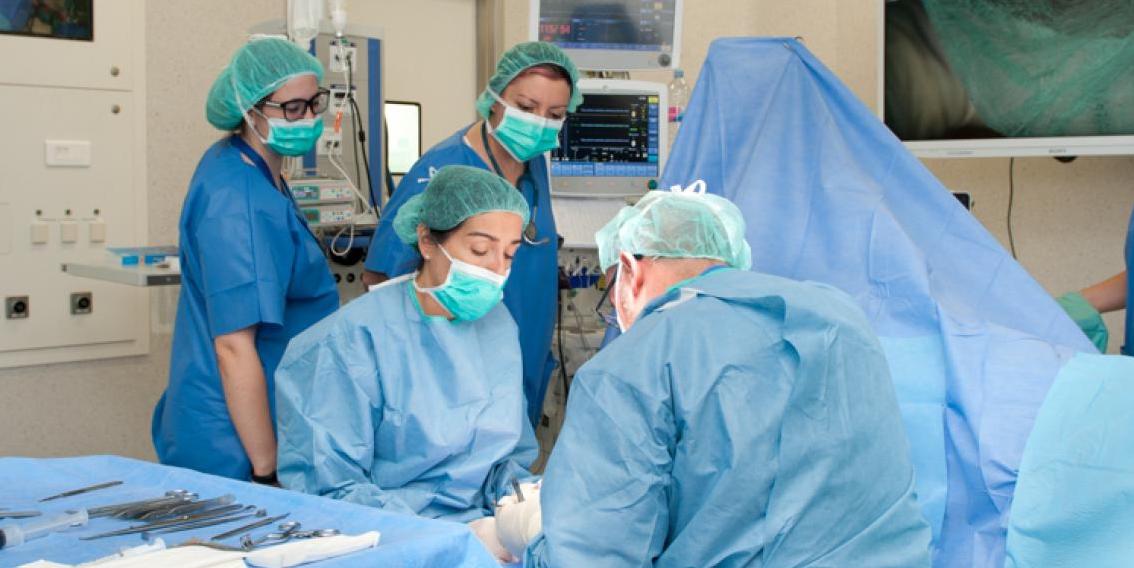
The enablers of our lean transformation
CASE STUDY – The Hospital de Bellvitge in Barcelona is relying heavily on hoshin and Kata to create a working environment based on collaboration and joint problem solving.
Words: Ana Alvarez, Deputy Director of Processes
The Hospital de Bellvitge in Barcelona serves an area of 250,000 people – almost 2 million for specialized care or high-technology treatments. Each year, the hospital performs around 20,000 surgeries and receives 120,000 emergency visits. Around six years ago, the organization decided to adopt Lean Thinking as a way to meet its needs, the most pressing of which was to improve the turnover of beds. The hospital had to increase the number of surgeries it performed, but always struggled to find beds for recovering patients.
Faced with long waiting lists, their goal was to boost their efficiency. I had previous experience with lean from my time at Terrassa University Hospital, and when I suggested that lean should be the way forward for the hospital, I was asked to lead the transformation myself. We started in the Surgery Department in the second half of 2017. The following year Antonio Olmos, a process engineer, joined me and, together, we began to run a few improvement projects. Since then, the “lean team” continued to grow, with some people leaving and others joining. Today I am working with two process engineers, one nurse and a doctor who joins us for part of his time.
As we got more and more experienced with Lean Thinking and ran more and more projects, we realized we were struggling to sustain the results of our improvements. That’s when we decided to start working with Kata. To this day, it’s one of the lean tools we rely on the most. For the vast majority of our projects, when we “close” the A3, we install a Kata board for our follow-up on a weekly, biweekly or monthly basis (depending on the project).
For large projects, like the one on discharges before noon, we have placed a Kata board in the different wards – neurology, pneumology, thoracic, trauma, nephrology, and so on. A couple of these are already independent in their use of Kata, and we as a lean team only show up from time to time to provide support, (evidence that a cultural shift has taken place), whereas others still need more assistance on a regular basis, as they are still working on transforming their way of thinking and doing.
Kata has been instrumental in ensuring the sustainability of results and in continuing improving on KPIs. To manage our rooms for digestive endoscopy (a procedure that typically has very high demand and a long waiting list), for example, we used our experience with Kata and visual management to design a productivity board that tells the team what was done every day, comparing the procedures actually carried out and those they expected to carry out. Today, this board has been digitalized and automated. We also use Leader Standard Work to structure our weekly planning meetings and to visually manage the department, in a bid to give the team visibility over the coming and going of patients and facilitating their prompt discharge. The system is designed in a way that allows the team to know when it’s time to notify the family that the patient is ready to go home, for example. All of this was a direct consequence of our Kata work supported by our Visual Management.
To introduce Kata in our hospital wasn’t always easy, of course, especially in those departments that didn’t have the habit of meeting on a regular basis to discuss the work. We made a big effort to help them understand the importance of not only using Kata, but of having a morning meeting to assess the current situation day after day (there is no point in having a board, or even filling it with data, if there is no regular meeting around it – it’s the essence of Leader Standard Work). Eventually, however, everybody got onboard because they saw improvements in the daily work and realized they could have an active role in it. Over time, the way the different teams use Kata naturally evolved: some of them are no longer as structured as they were at the beginning (using the five Kata questions, for example), but the continuous improvement ethos and focus on KPIs proper of Kata still inform their every action.
The results were tremendous, as we were able to increase the number of discharges before noon substantially. This, of course, had a positive impact on the patients waiting for a bed to free up.
Kata is not the only lean practice that different wards have decided to adopt. There is also hoshin kanri, which we first introduced before the pandemic. Today a number of departments use this powerful tool to connect their objectives with the every-day work, relying on A3 Thinking as the go-to way to solve problems. We have even started an interesting experiment with hoshin within our transplant team. In reality, it is four teams working together, and with hoshin they are looking for synergies that can make the transplant process – from the identification of donors and the accessibility of candidates to the waiting list to surgery and follow-up – more agile for our patients.
We then have a “macro-hoshin” for the whole Hospital de Bellvitge, which we developed with the help of Oriol and Nestor from Instituto Lean Management and introduced at the end of 2021 building on our previous experience with all the local hoshin processes. The idea was to align the strategy of the different departments to the overall strategy of the hospital. Our Neurology department – an early adopter of many of our lean practices – was a particularly good example of how department leadership should spend time with front-line people, explaining the importance of KPIs (critically, “why” they are so important) and setting clear expectations.
The engagement seen in that area is a model for the rest of the organization. As people understand the contribution of their work to the overall objectives of the hospital (and their repercussions on the quality of care), we see a shift in their mindset. They realize “what’s in it for them”: if you work to free up beds in your area, it will be more likely that your patients will all be in the same place (rather than, for instance, having to stay in the ER until a place frees up).
Something quite unique we did with our hoshin at Bellvitge was to build our key strategic objectives into the traditional SQDCP structure for KPIs. The reason for this was that some areas had a very clear set of indicators, while others struggled to identify theirs, resulting in a strategic plan for the hospital that was created with the contribution of everyone but that ended up not representing every department. Besides, to define our strategy, we had traditionally been producing a huge document – which we used as a basis but ultimately wanted to replace with something more user-friendly. The new hoshin, therefore, was based on three strategic objectives – patient experience, people development, and leading collaborative work across the territory – and on two levers for change, which were innovation and a data-driven organization.
We needed a few sessions to identify the KPIs and narrow the long list we came up with down to a few lag indicators (results). Once we were done with alignment, we invited the whole Board, with the intention of getting them to own the process and of creating a clear connection with the work that was already being done at departmental level. Since then, we have added two strategic objectives: sustainability and a set of KPIs the Catalan healthcare service asks us to work towards.
Over time, leadership has become more and more used to the hoshin meetings, and we have seen great engagement and a much greater focus on data. The KPIs we track are more tied to results than to processes, and we are probably as close as we’ll ever be to a perfect set of indicators. We adjust occasionally, but the combination of hospital-wide hoshin and local hoshin boards works really well for us. More than anything else, it helps to ensure that people participate and that things happen. It creates accountability and an expectation.
Using this system, today the Hospital de Bellvitge is able to think strategically about its positioning as an organization in the Catalan healthcare landscape.
THE AUTHOR
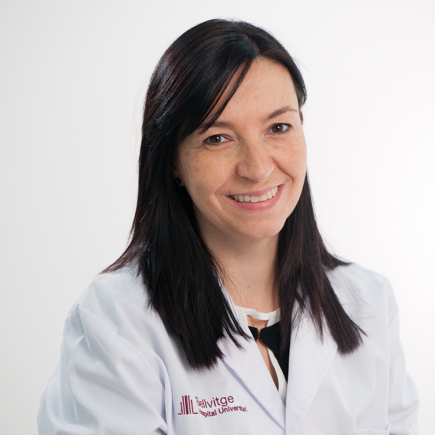
Read more
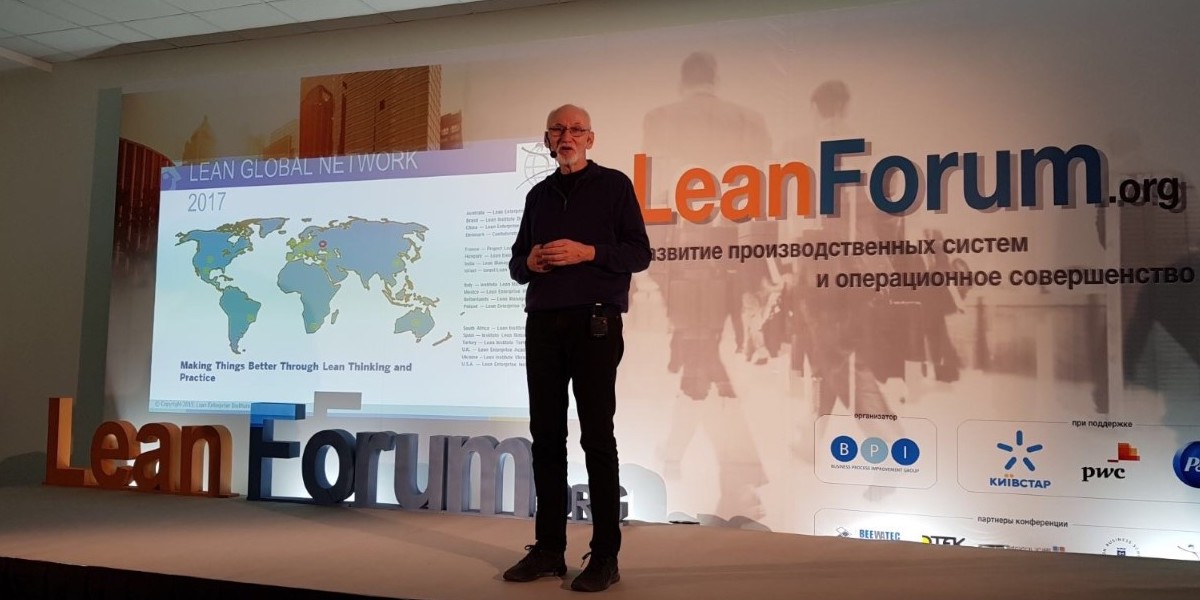
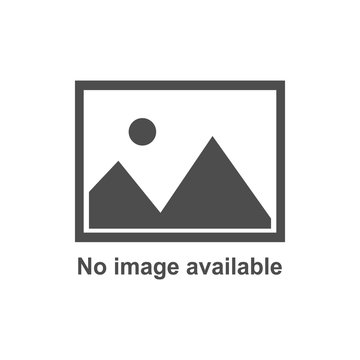
FEATURE – As the senseless war in Ukraine continues, the author looks back to his visit to the country in 2017, recalling and celebrating its vibrant lean community.
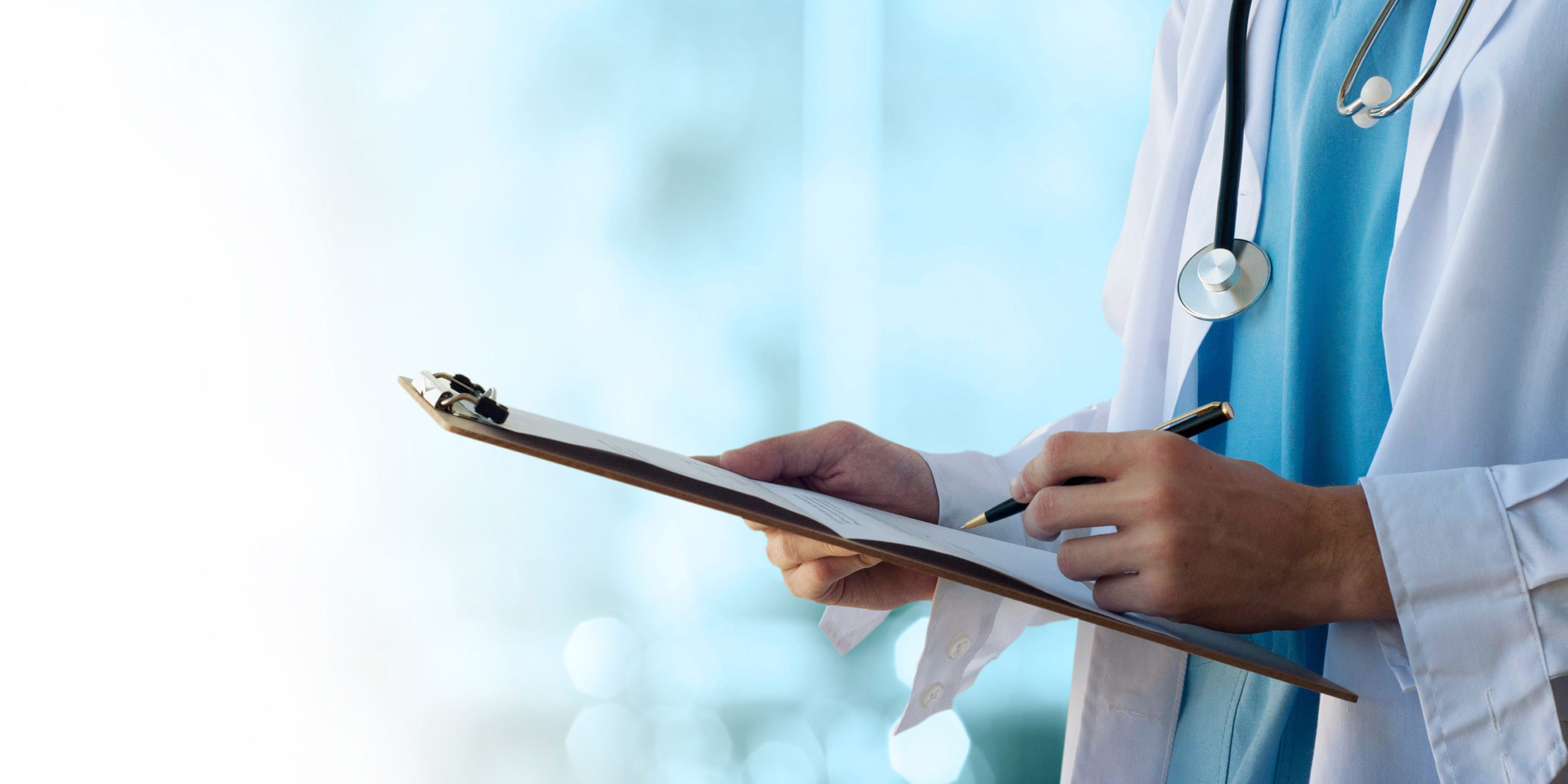
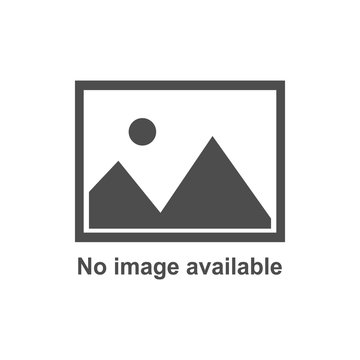
INTERVIEW – A private healthcare group in South Africa has carefully studied the unique challenges it faces and customized its approach to improvement accordingly, embarking on a lean journey to better patient care.
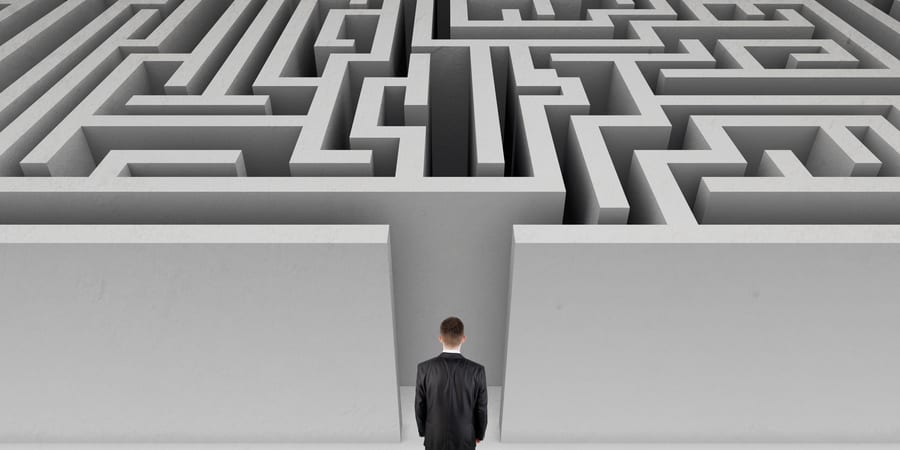
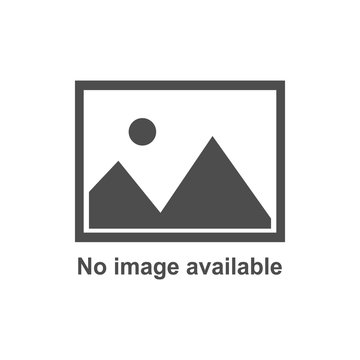
RESEARCH – The author explores the effectiveness of five common managerial practices in driving a corporate lean initiative forward, analyzing the data gathered while visiting 36 factories of a large corporation.
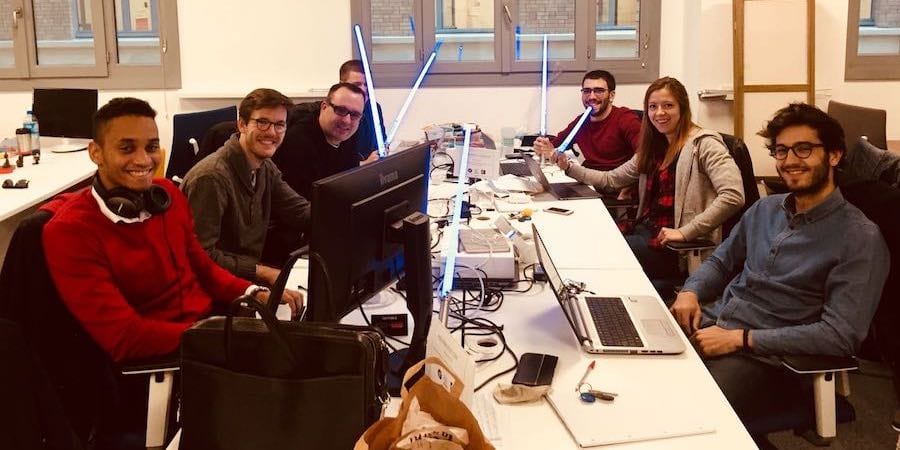
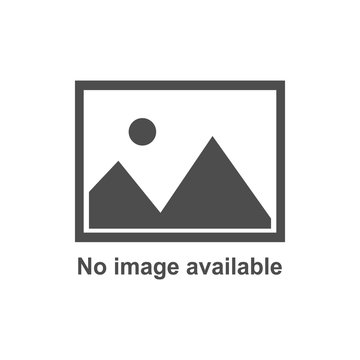
FEATURE – In the second article in our series with Theodo, the CTO tells us about an experiment that showed how problem solving is easier when the job is clearly defined.