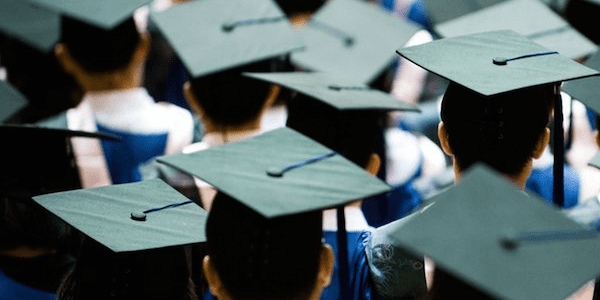
Education: how lean is taught
INTERVIEW - Planet Lean speaks with Constantin May, Academic Director of the CEPTM institute at Germany’s Ansbach University, which organized the first Lean Educator Conference in Europe in co-operation with LGN.
Interviewee: Constantin May, Academic Director at CEPTM Institute
Planet Lean: Why is it so meaningful that this conference was brought to Europe for the first time?
Constantin May: When I went to the previous editions of the conference in the US I realized that bringing lean educators together on this side of the Atlantic Ocean would be very useful. Learning from each other is invaluable, and this is particularly true for educators, who should know how vital sharing best practice is to progressing in anything we do.
To my knowledge, until now there was no event like this here in Europe. This conference represents a great way to connect academics from all over the continent, to share best practice of teaching lean, and to expand the network of European lean educators.
The way lean is taught has of course a very direct impact on how it will be practiced, and it’s therefore incredibly important to talk about this.
It’s incredible to find out how many of the activities that we educators carry out across Europe are similar. For example, the learning factory, which we use here at Ansbach, is also particularly successful in Italy.
We tried to create a conference that pushes the boundaries of knowledge on lean teaching. Many of the presentations have generated a lot of debate and discussed controversial topics, which we encourage. If people don’t feel completely at ease with some of the points made during certain presentations, then I have reached my goal – if we are to learn, we need to challenge one another.
I am really proud of how the conference has gone.
PL: Are there any specific differences in the way lean is taught in Europe compared to the United States?
CM: I haven’t been able to completely understand what is going on in the United States in terms of teaching lean. However, my impression is that in the US a lot of teaching focuses on tools and that lean six sigma still plays a much bigger role (not just in academia, but throughout the business improvement landscape) than it does in Europe.
Having also discussed this with Peter Ward (the first President of the Lean Education Academic Network), it seems that learning factories are not prevalent in the United States. There is no real practice-based learning that we know of, whereas here at the CEPTM institute at Ansbach University (but also, as I said, in Italy) this represents an important part of the teaching portfolio.
PL: What is the most difficult thing about teaching lean in universities?
CM: It really depends on whom you teach. If your students are young people with no industry experience it is difficult for them to understand how a factory works and therefore how lean can fit in that picture. Concepts like developing people and creating value (with all their related challenges) seem logical, but are at the same time hard to grasp without the ability to see the work.
Students with no industry experience often cannot see why lean management is so desperately needed, because they don’t see how difficult working without it is in the real world.
If you want lean principles to stick, the teaching must involve a lot of practical applications, simulations, and games. Additionally, it should preferably take place in small groups: at the CEPTM, for example, we have groups of 12-15 students. How can you effectively teach lean to hundreds of people at the same time, simply using slides and a projector?
PL: There is a lot of talk about lean certifications. Many in the movement are vehemently against them, while others stress the importance of identifying ways to gain access to the right people with the right skills – something certifications could potentially help with. What do you think about this?
CM: It’s a tough one! The problem is that if you ask five people what lean is you will get five different answers. It is difficult to get global agreement on what lean education should look like.
Naturally, teaching institutions the world over provide attendees with some kind of certificate upon completion of the course, but in most instances this only has local validity, in the country or region in which the institution operates.
At the same time, a HR department that sees a certification, no matter where in the world it was awarded, is likely to recognize that that person has an understanding of lean principles, which – if coupled with the right on-the-job experience – might make him or her a suitable candidate.
But I must say that getting to the point where we will have a global lean accreditation will be extremely difficult. What institution would award it? There are so many different views of lean that agreeing on teaching standards looks almost impossible.
TO READ A REVIEW OF THE CONFERENCE, CLICK HERE
THE INTERVIEWEE
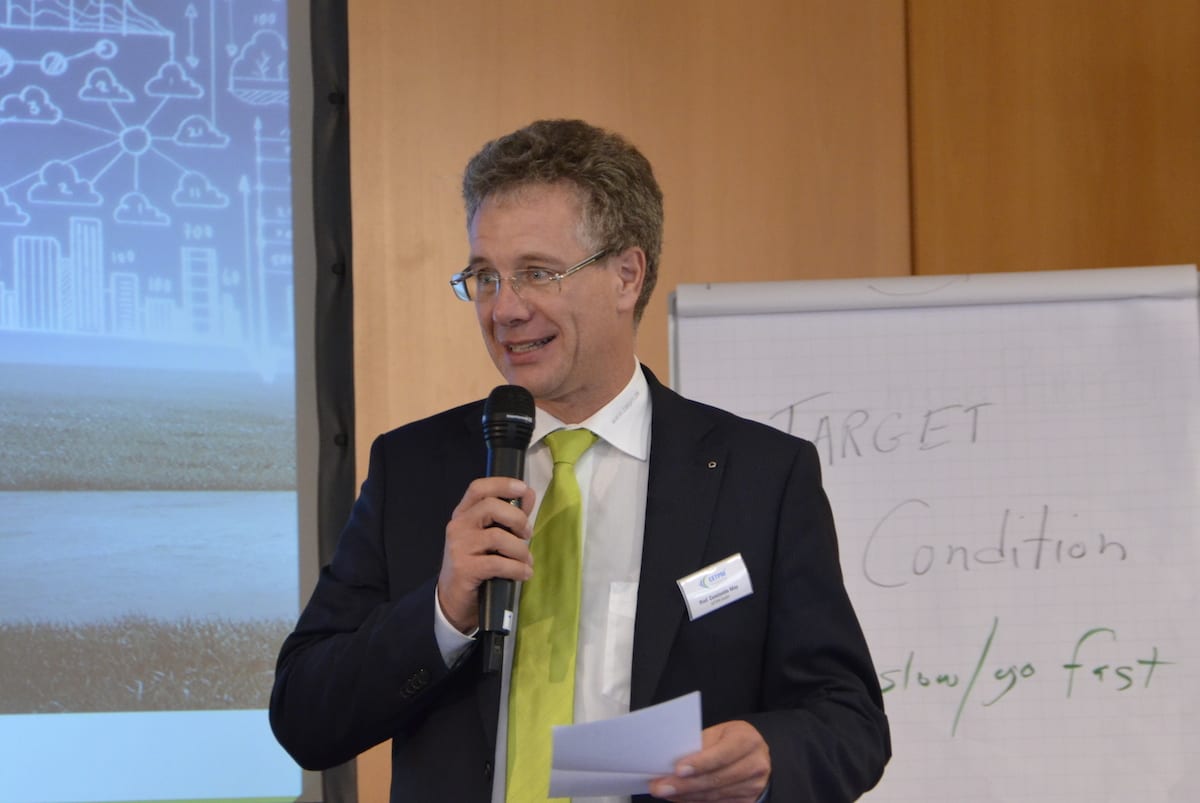
Read more
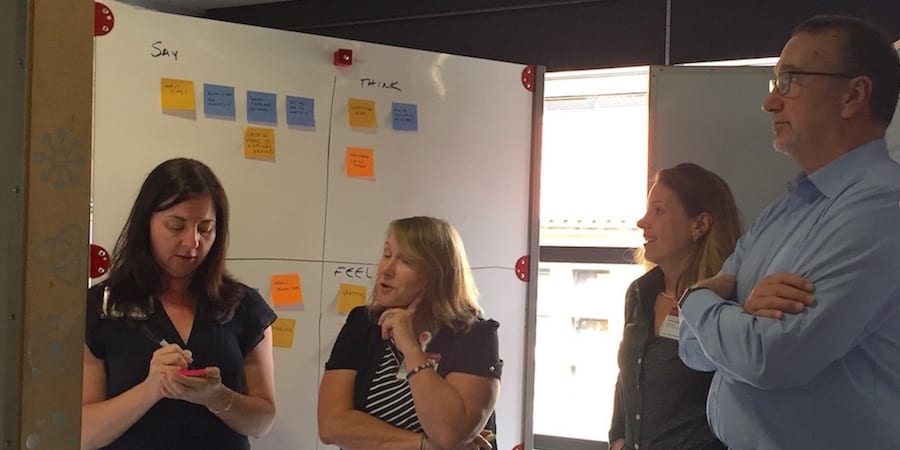
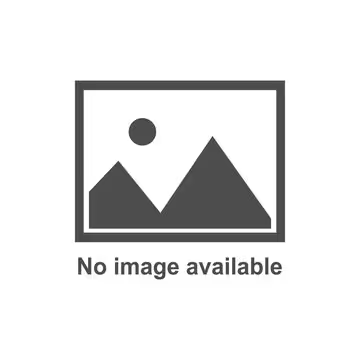
PROFILE – In this new section, Planet Lean features some of the most inspirational lean leaders out there. For the first profile, we have selected James Hereford, a former high school teacher who is now leading his third healthcare transformation.
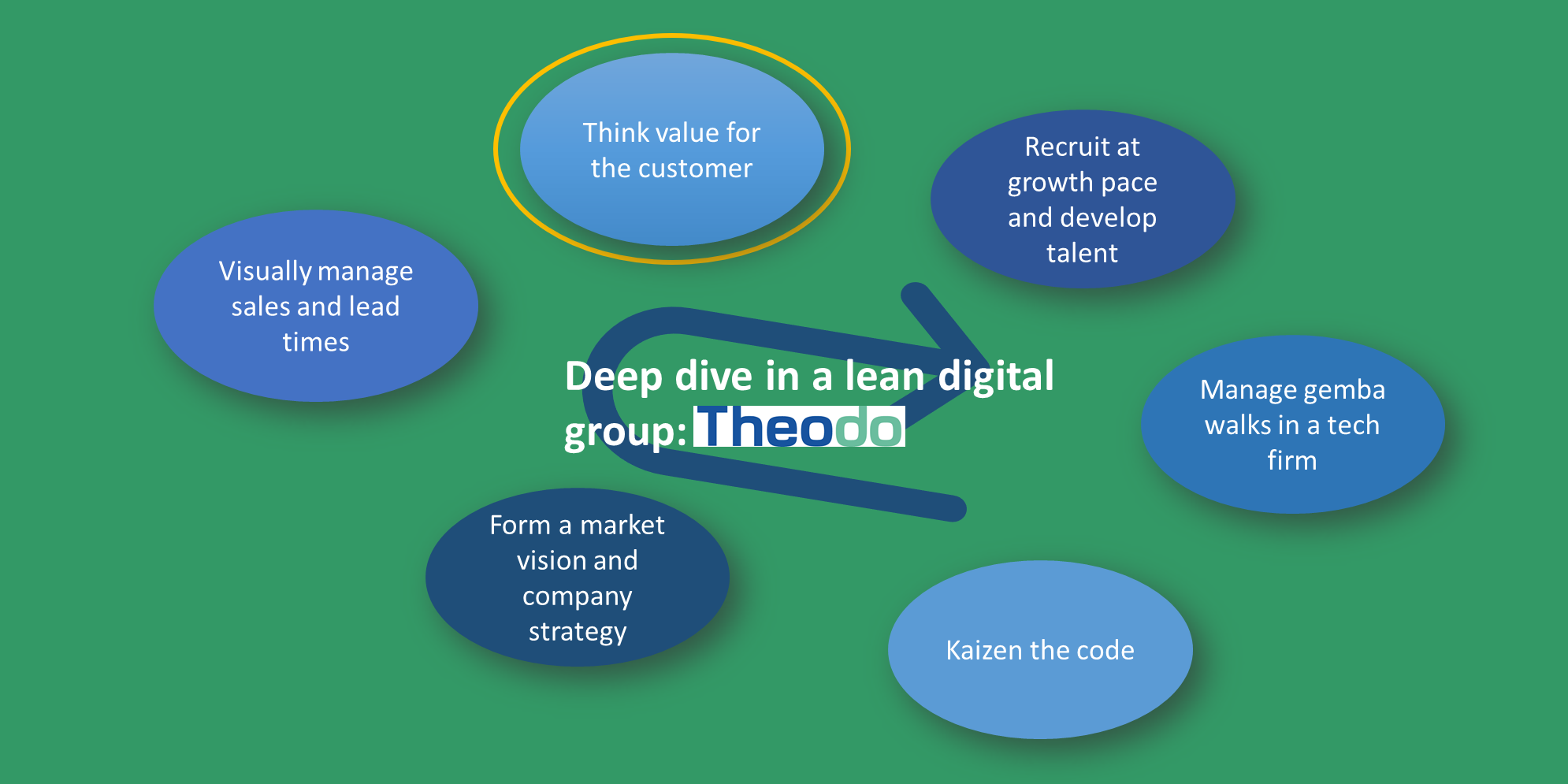
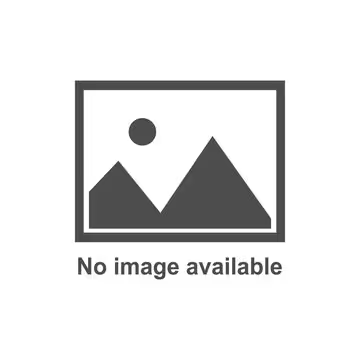
FEATURE – In the second article in her new series, the author discusses how focusing on customer value helped a fintech start-up to grow fivefold just last year.
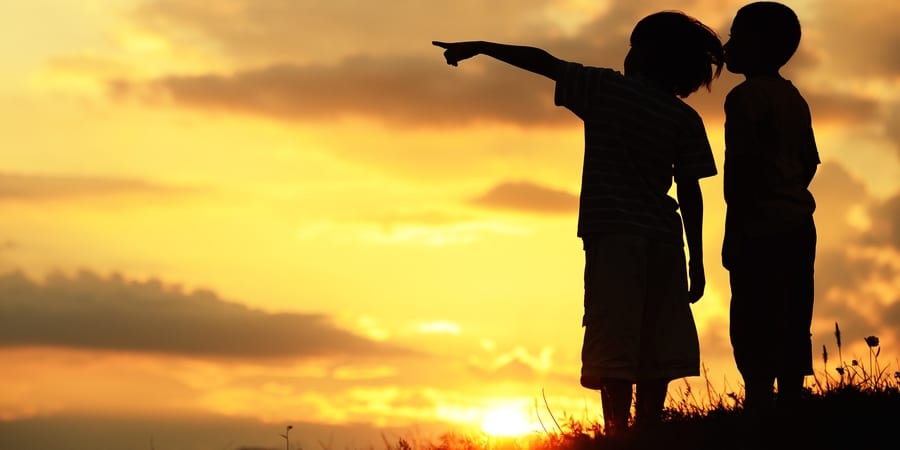
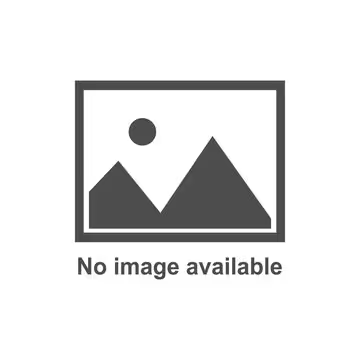
FEATURE – For the last article of their series, the authors ask themselves the ultimate question: who wins at lean, and who loses? What makes change sustainable? Turns out, it’s all about the fundamentals.
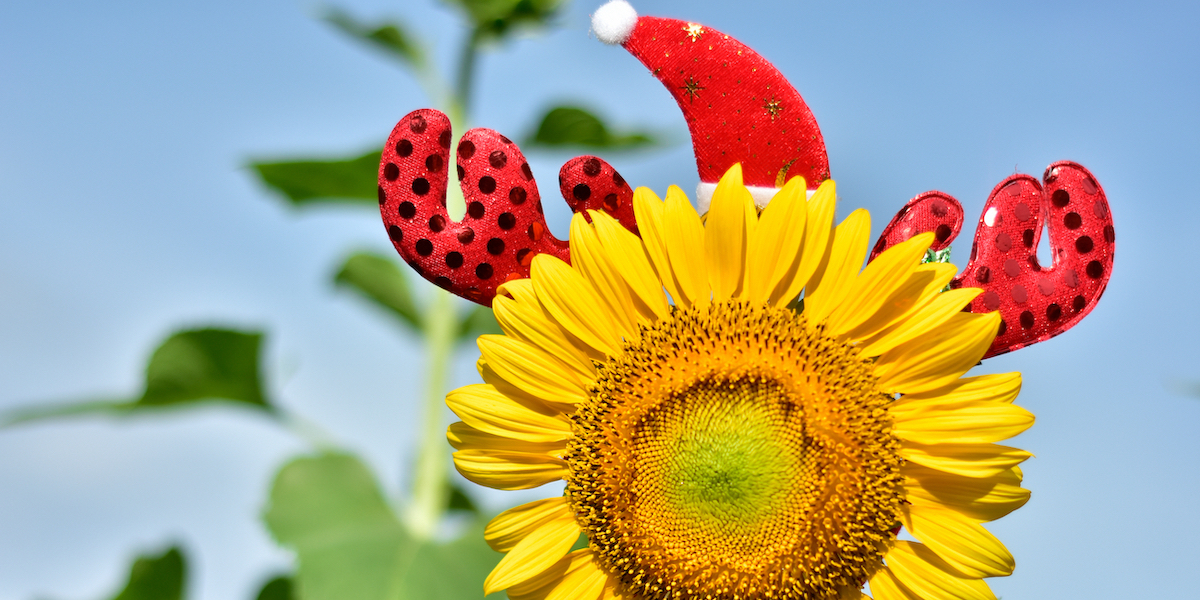
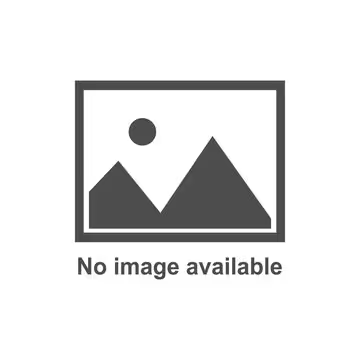
FICTION – Santa is struggling to locate the many children who are hiding from war to deliver them gifts, until the lean Time Benders come to the rescue and help him understand the problem.