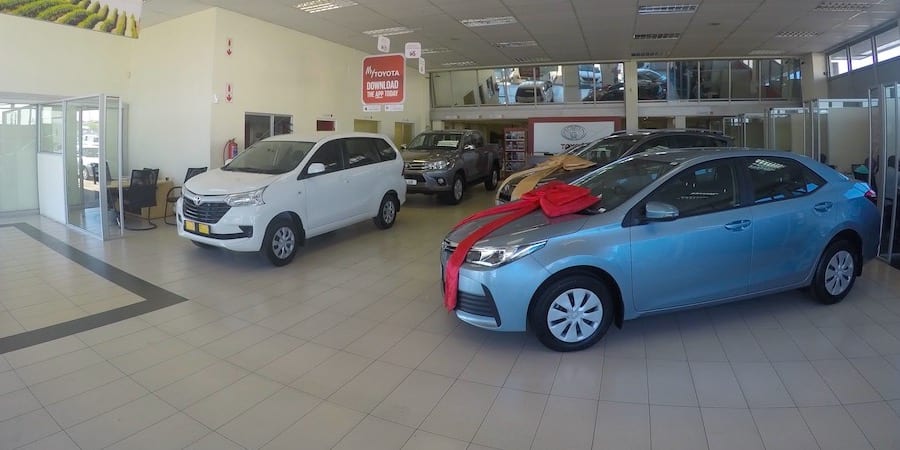
Visual management in the Finance department of a car dealer
VIDEO - Visualization has an important role to play in creating awareness of the problems and highlighting gaps as a key starting point for improvement, and this Finance Manager does it with dedication.
By: Nizar Sherfodien, Finance Manager, Halfway Ottery - Cape Town, South Africa
By now, many of you will be familiar with the Halfway transformation (PL has been running this series for a few months) and the great results we have achieved here at Ottery and in other dealers.
As the old lean adage goes, you can't improve what you can't measure. Indeed, visualization plays a critical role in our dealership: not only does it help us identify problems, but it also makes visible the performance and quality of office work - which in turn helps us to link the flow across departments. Showing the importance of quality across the process goes a long way towards ensuring we all work with a common goal in mind.
Without visualization, many of the things that are making Halfway Ottery successful - starting with the cash-to-cash model we discussed last month in this article - simply wouldn't be possible.
So, let me show you the visual boards I use.
REFLECTIONS FROM THE COACH
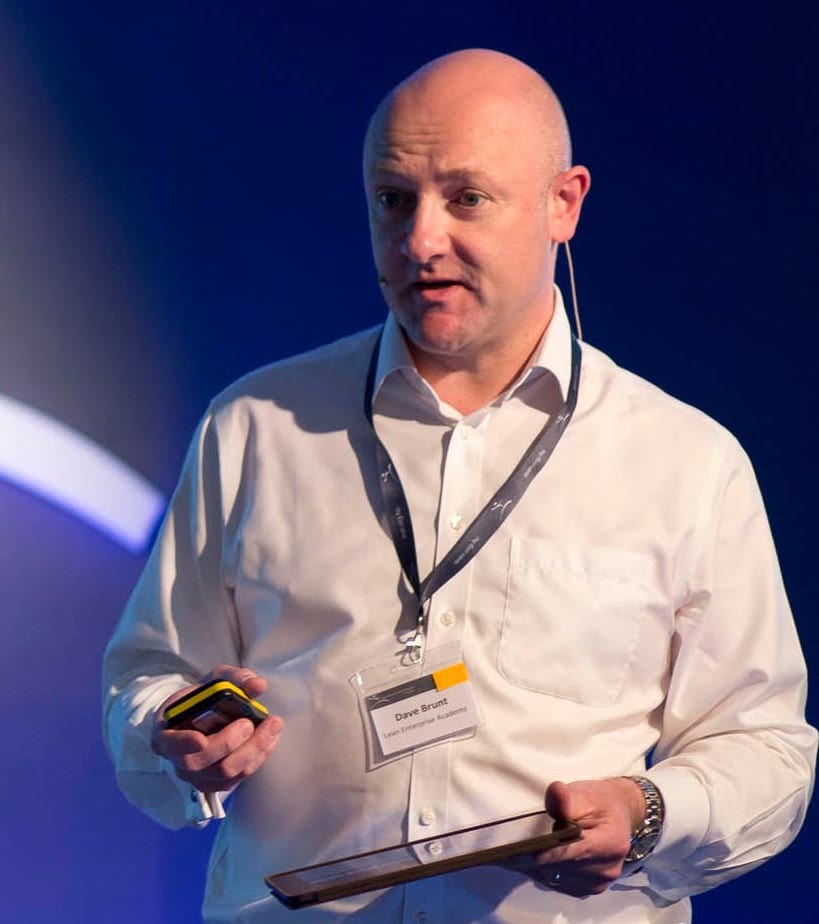
Visual management has become intrinsically linked with lean thinking. Most of us know that we are trying to make normal from abnormal clear - making problems visible. Perhaps at a deeper level, good visual management helps us make more of the management system (and the thinking in it) visible. That’s really important, as it helps us identify the vital few issues, understand how well we are performing against them, and see whether we are closing the gaps we’ve identified. It’s also very important to identify and visualize the next things to work on, embedding PDCA into our way of working.
Dave Brunt, CEO, Lean Enterprise Academy
Have you watched our documentary on their lean transformation yet?

Read more

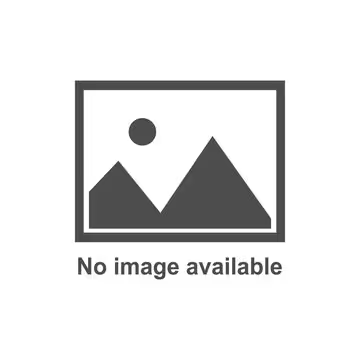
FEATURE – What is the role of middle managers in a transformation and how can we ensure they can fulfil that role – instead of being blamed for the failure of the initiative and even excluded from it?
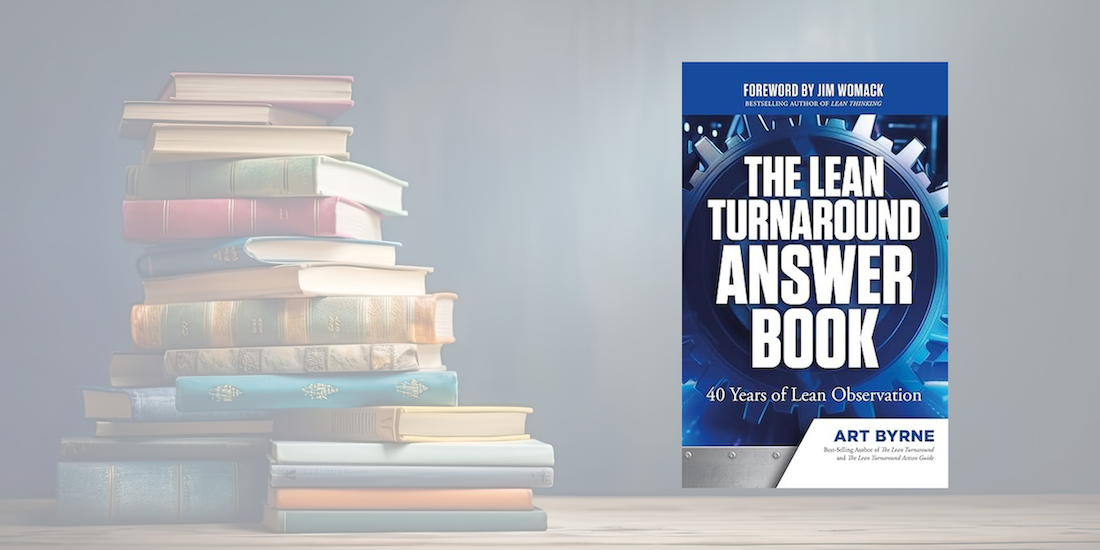
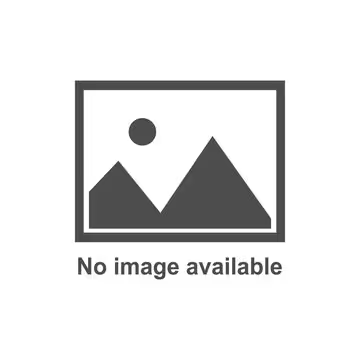
BOOK EXCERPT – In the introduction to his new book, Art Byrne reflects on his lean journey and explains why to understand lean one must change their mindset.

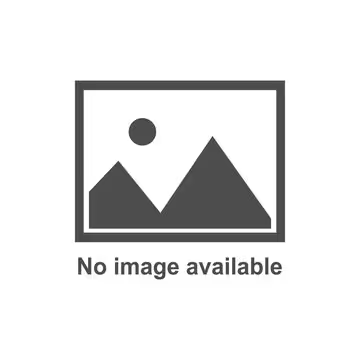
FEATURE - We often hear that lean is a fundamentally different approach, but what does this really mean? The authors reflect on how lean challenges and debunks our assumptions on how to run a firm, which might also explain why it meets such resistance.

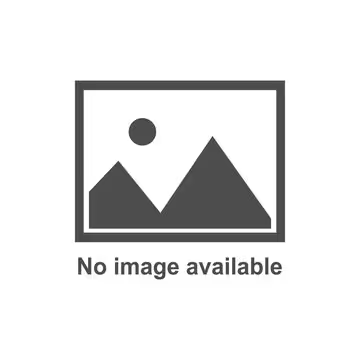
INTERVIEW – A specialist in control solutions for air-conditioning, refrigeration and heating, Carel Industries first applied lean to R&D a decade ago, when few companies did. We asked them how their journey unfolded.