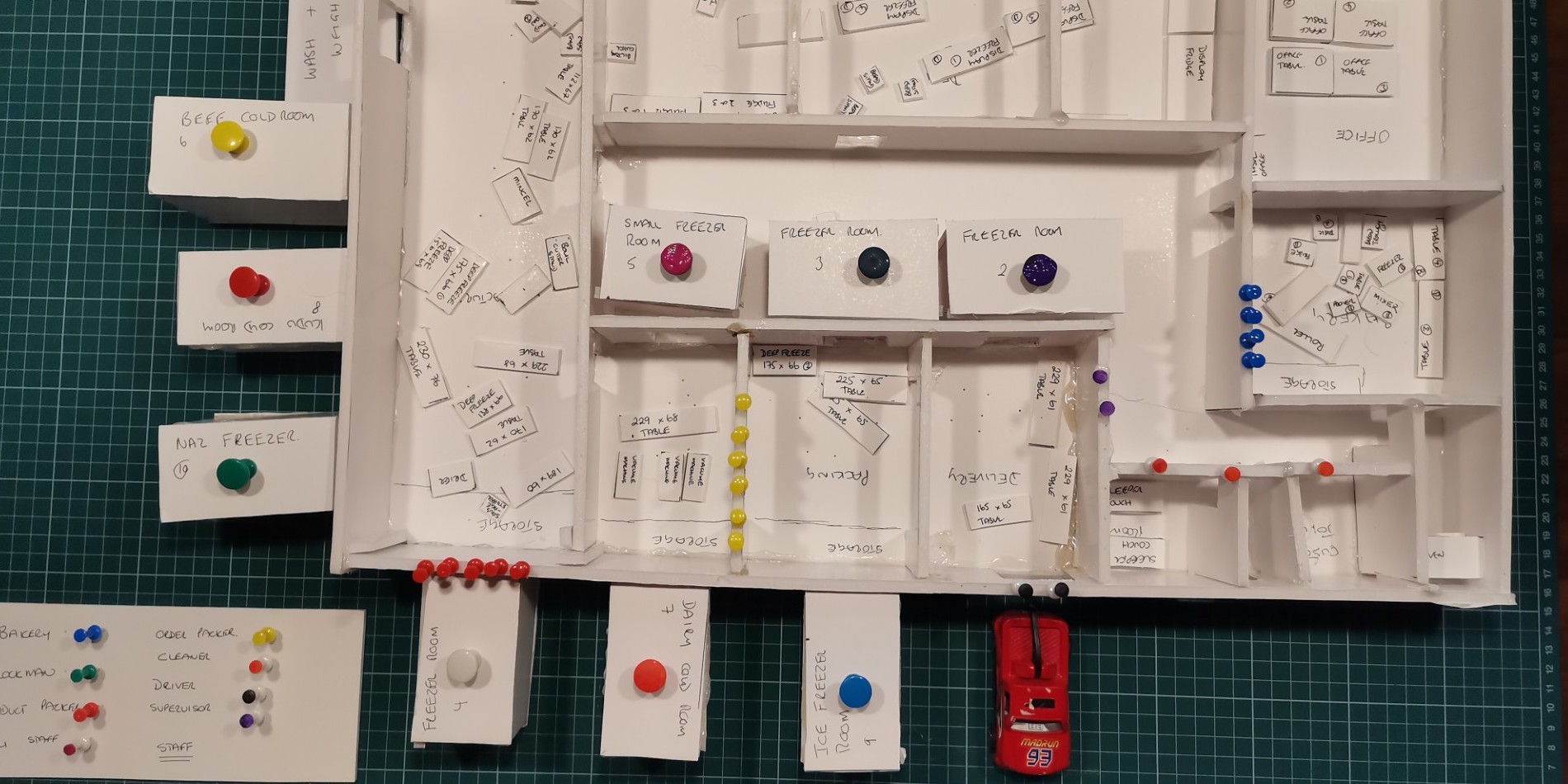
Think like a child and let creativity flow
FEATURE - Looking back to her experience coaching teams in Africa, the author encourages us to introduce play in our work, as a way of teaching people and of unlocking creativity.
Words: Sharon Visser
Play is an essential gateway to creative, innovative thinking and communication, and yet it is often undervalued in the workplace.
I remember playing with my friends as a child, in Africa, using toy cars in the soft, white sand during the cool late afternoons. We built tunnels, bridges, and hills, populated with plastic toy animals, telling stories of danger and adventure. In those moments, I wasn't seen as a white child or even as a girl; I was a co-creator of dreams.
For us, playtime was a realm of boundless creativity where everything seemed possible. Through play, children learn to tell stories, develop spatial skills, solve problems imaginatively, and form pure connections.
Sadly, as I grew older, such imaginative activities were dismissed as childish, unsuitable for the serious business of adulthood. Consequently, I boxed away those thoughts to focus on sensible tasks.
That changed when I was introduced to Lean Thinking. Magically, the box opened, the toy cars reappeared, and I was once again allowed to be creative. Using these toy cars and a sheet of flip chart paper, we played and imagined solutions to the congestion problem in our service center. This play led to a practical plan also known as PDCA to ensure a safe flow of vehicles, make the work more visible, and prevent minor accidents.
The toy cars facilitated communication and co-creation with the people doing the work. Their engagement transformed the responsibility from "me" to "us", fostering a sense of ownership and understanding. When I returned to work on Monday, the team had surprised me by implementing our plan over the weekend.
In another instance, we used toy cars and colored toy figures to redesign the process for receiving vehicles. This playful approach helped the team visualize and perfect the workflow, shortening the timeline and ultimately enhancing the customer experience and vehicle check quality.
Similarly, a company I coach had to relocate their butchery manufacturing business, involving significant alterations to the new premises. We built a scale model of the building, outlining necessary changes. The owner's son, despite lacking project management experience, led the project to completion ahead of schedule and within budget. The model allowed him to communicate with everyone and visualize the work, fostering discussion, cooperation, and effective problem solving. This work was supported by a PDCA chart visual to confirm progress and responsibility to the timeline.
The same company is now experimenting with a LEGO build for each product to plan the work of manufacturing a variation of 45 products. When different products are made on pull, the challenge is always the sequence and understanding any overburden in the planning stages.
With the visual help of the LEGO, it is now possible to plan the day visually and know right at the beginning what the workload will be. Any overrun into overtime can be addressed, and gaps can be filled with kaizen. With the addition of a clock, it is possible to see if the work is ahead or behind.
Think back to those moments in your life when you had what my mother would have called a “good play”. It is in these moments that creativity and innovation have their greatest opportunity to surface. Now imagine if we could come to work and see a problem with the same limitless opportunity of a child at play.
What if we could see ourselves as co-creators instead of competitors in our own team? What a world we could build together, one PDCA at a time.
THE AUTHOR
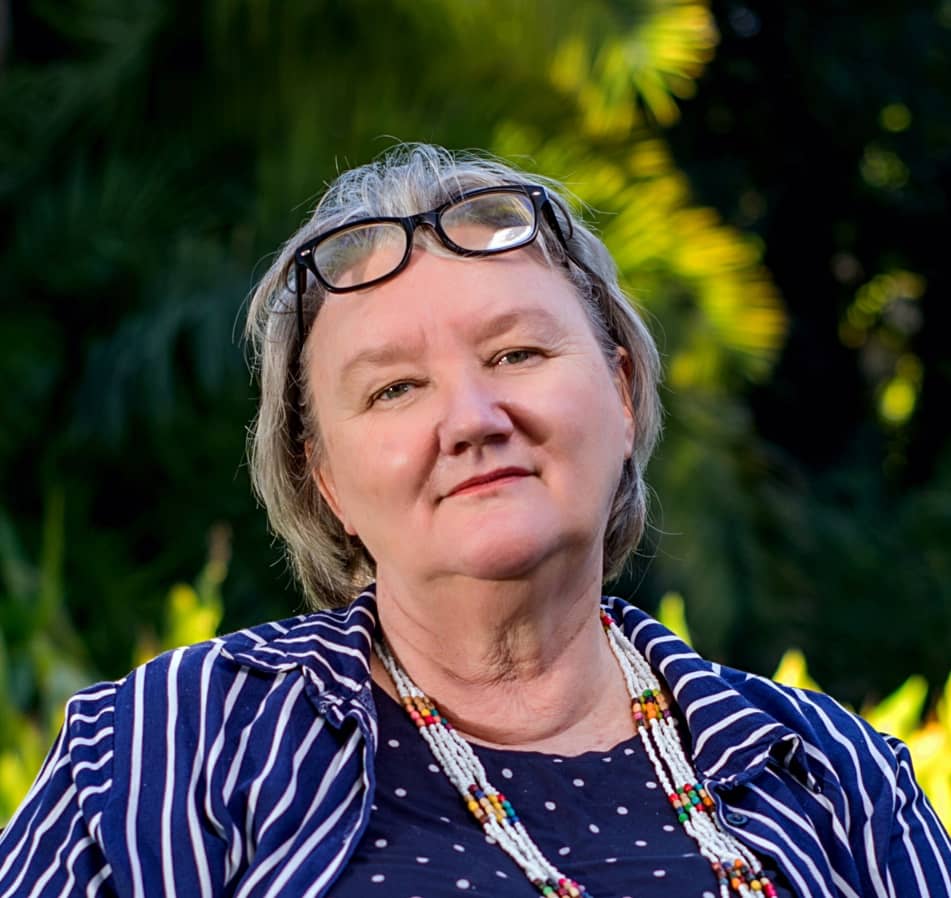
Read more
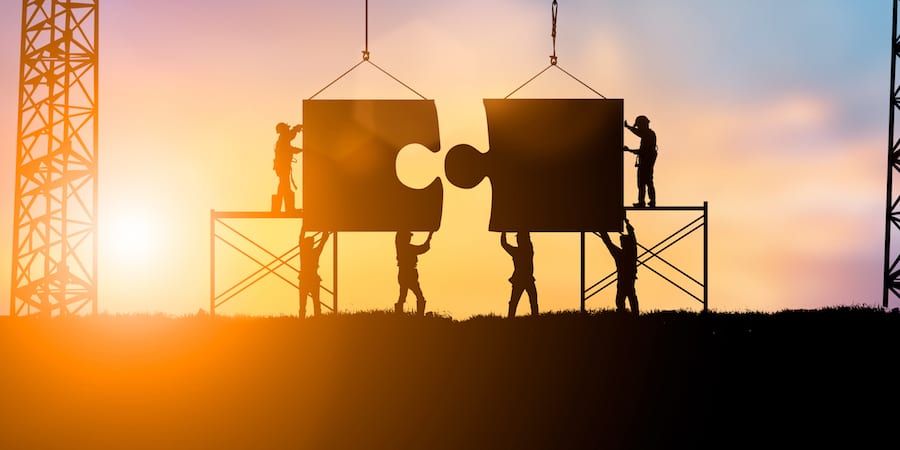
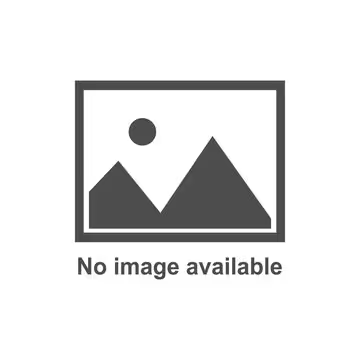
FEATURE – Using Carol Dweck’s distinction between fixed and growth mindsets, the author discusses how leaders should think and act to make lean possible. Looks like no fixed mindset is beyond saving.
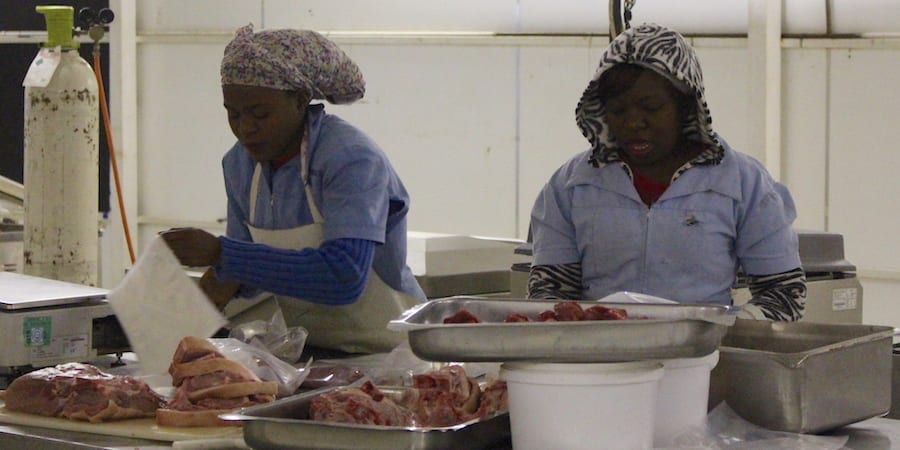
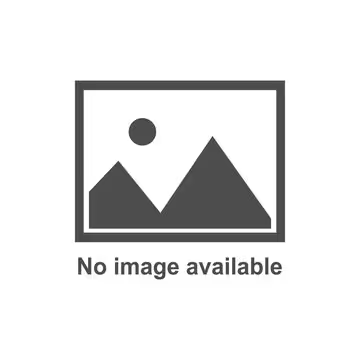
CASE STUDY – Faced with complex logistics and customer complaints, a small deli and butchery in Botswana saw in lean a way to bring the business back from the brink. The philosophy didn’t fail them.
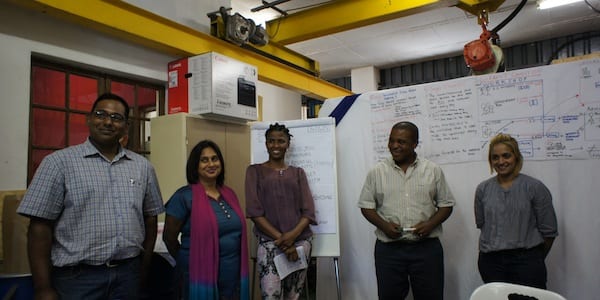
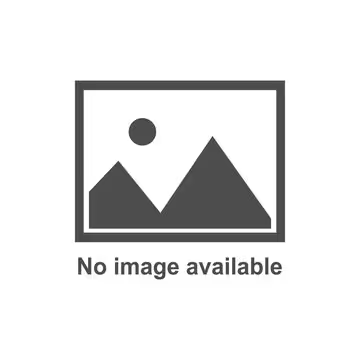
FEATURE - Norman Faull, Director of Lean Institute Africa, talks about a supplier development project the institute took part in, and shares a few of the results achieved.

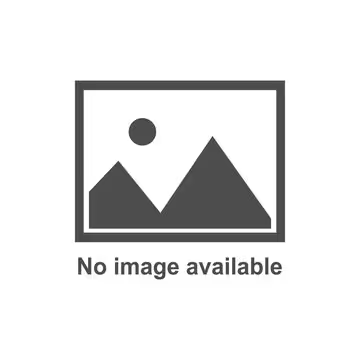
CASE STUDY – The extraordinary transformation of Kinross' Round Mountain gold mine in Nevada over the past six years shows that lean thinking can – quite literally – move mountains.
Read more
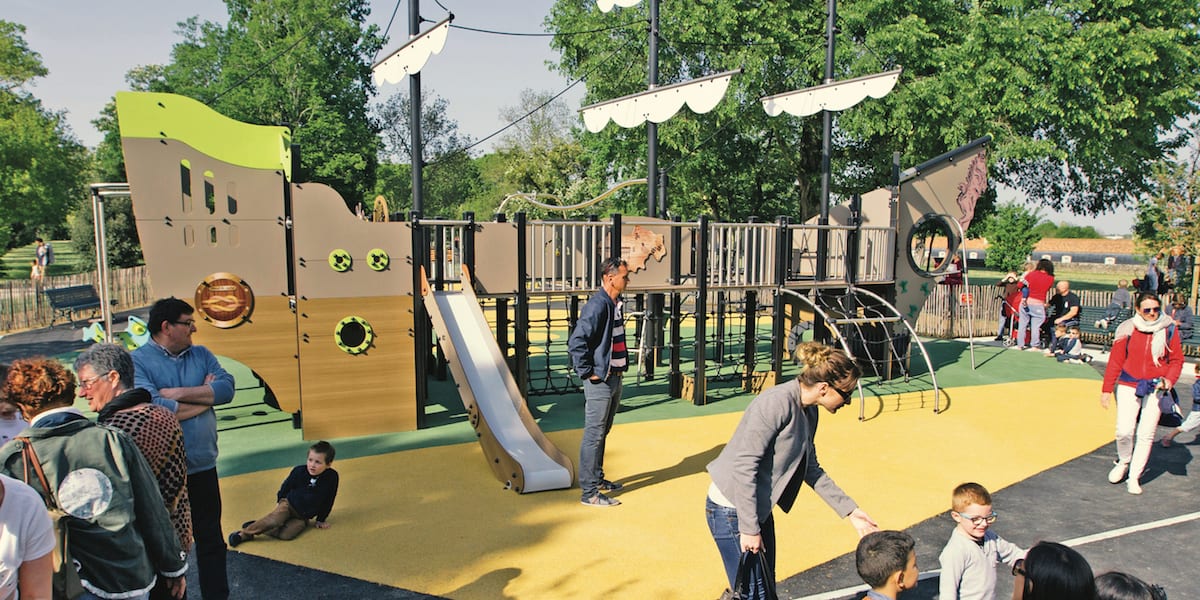
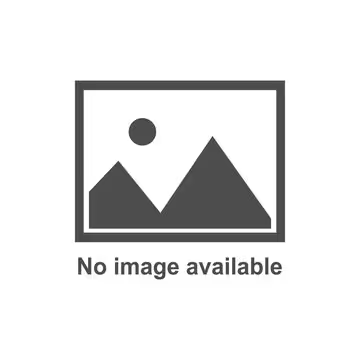
FEATURE – Enabling its people to think autonomously about problems and fostering collaboration among departments is allowing a French company that makes and installs playgrounds to thrive.
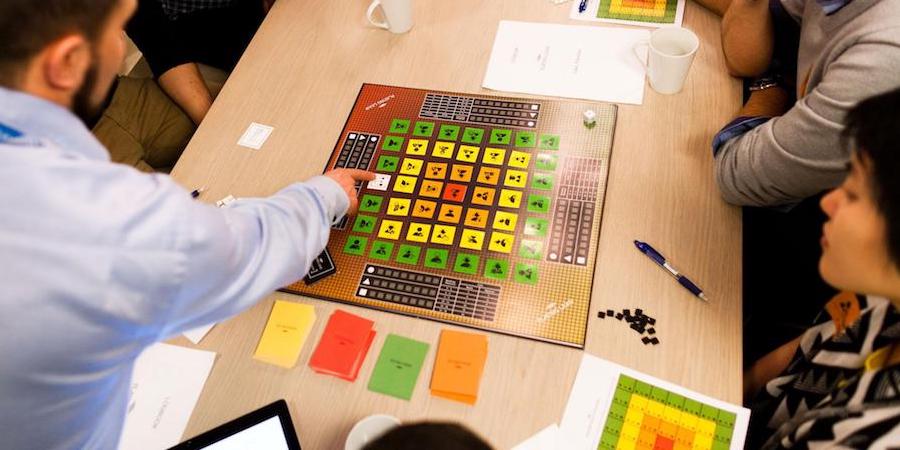
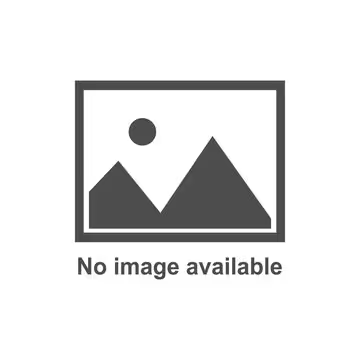
FEATURE – Simulations and games can be extremely beneficial, so long as we use them to highlight and explain the underlying behaviors we must adopt if we are to successfully embrace lean... and not only the tools.
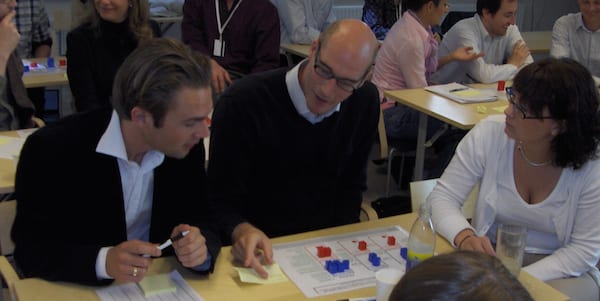
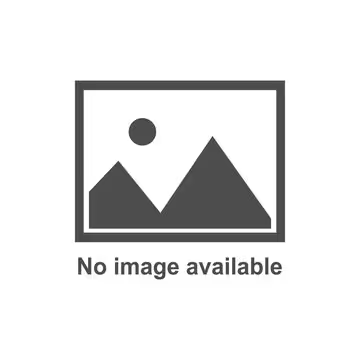
FEATURE – Games can help you to engage people and communicate lean management principles. Here is a number of useful tips and suggestions on how to make training more… playful.
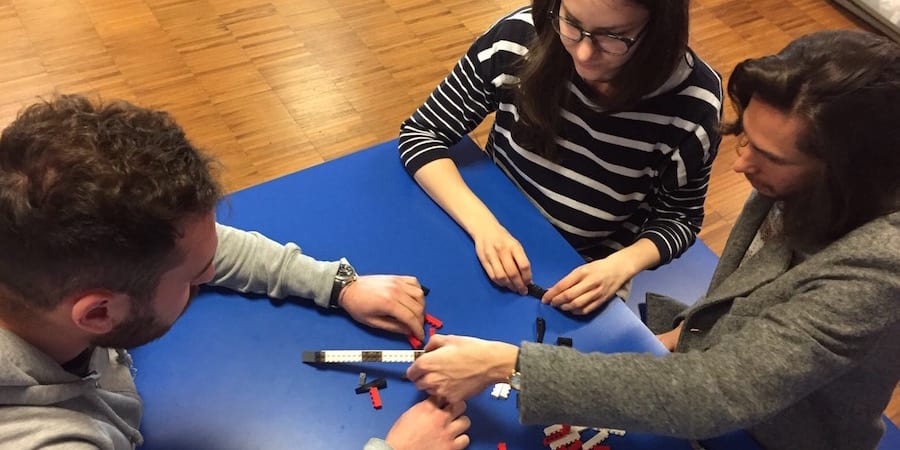
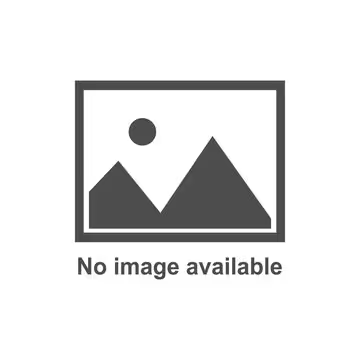
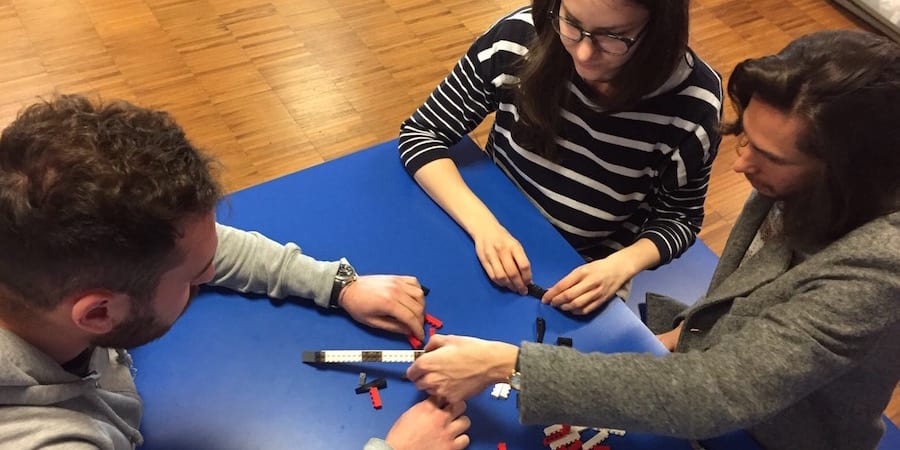
FEATURE – In a world of disruptive innovation, being faster and smarter at developing new products has become critical. The authors explain why set-based concurrent engineering is the answer, and why a game is the best way to learn it.