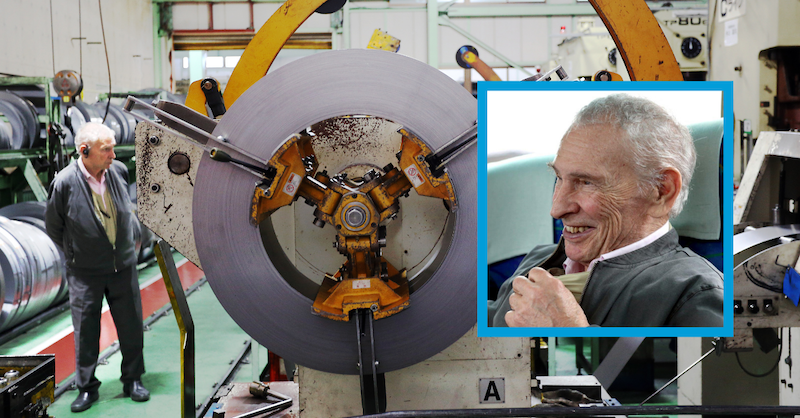
Remembering Freddy Ballé
FEATURE – On October 31st, the Lean Movement lost one of its pioneers. In this piece, Dan Jones reflects on Freddy Ballé’s legacy.
Words: Dan Jones, co-founder of the Lean Movement
We all stand on the shoulders of those who have gone before. One of those giants was Freddy Ballé, who passed away on the31st of October. He was one of the first people in Europe to understand the significance of the Toyota Production System while he was working at Renault in the 1970s. He went to Japan on annual pilgrimages to seek answers to his questions about TPS from leading senseis at Toyota.
He used this learning to build the Valeo ProductionSystem. Early on, Toyota told me that only two suppliers in Europe really understood TPS - Freddy Ballé at Valeo and Peter Marks at Robert Bosch. Freddy went on to develop similar Production and Product Development systems at Sommer Allibert and Faurecia.
One of the best things I have done was to convince Jim Womack to publish the first lean novels by Freddy and his sonMichael. The Gold Mine, The Lean Manager, and Lead withRespect showed a global audience the thinking and behaviors that made a lean system work.
I first met Freddy at a supply chain workshop organized by McKinsey in Paris, and every time I met him after that I came away with new insights into lean. This learning continued as his wisdom infected the articles and books that Michael and I worked on exploring the learning processes behind Lean Thinking.
I can still hear his voice saying, “Keep your focus on the detail of the work and understand its significance for the customer and the system as a whole.” Thank you, Freddy, for your example and your inspiration.
These wise words are more relevant than ever, as Toyota not only develops solid state batteries but is leading the way to scale up production of one of the most important building blocks of the post-carbon era, alongside its pioneering work on hydrogen fuel cells.
THE AUTHOR
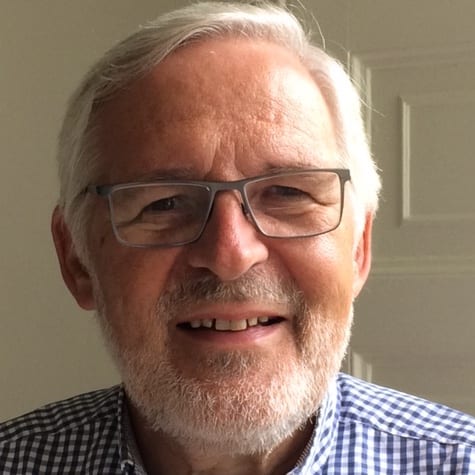
Read more
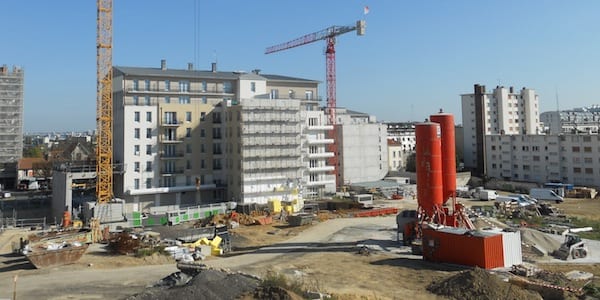
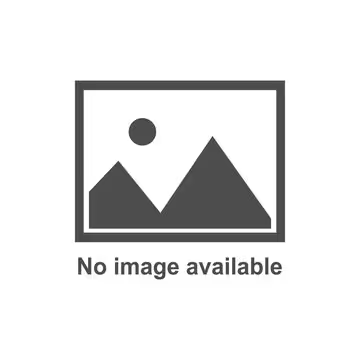
COLUMN - In the first of a series of columns written by CEOs, John Bouthillon of PO Construction explains how lean has kept his company afloat through the recession.
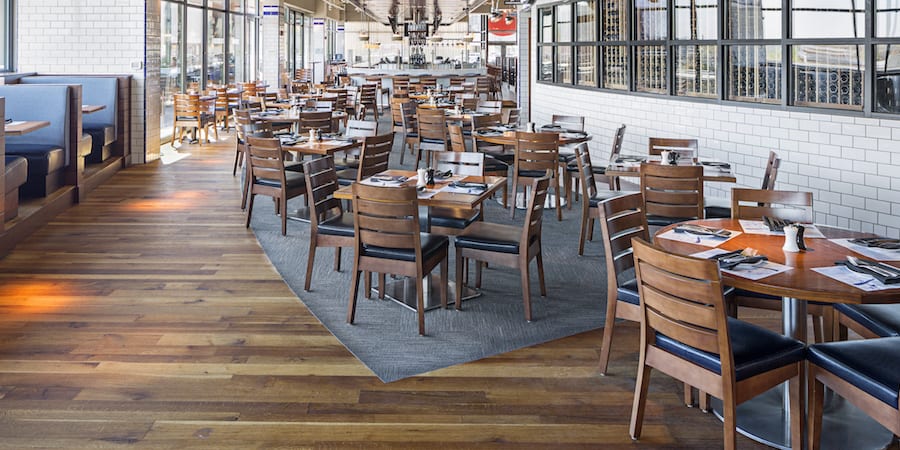
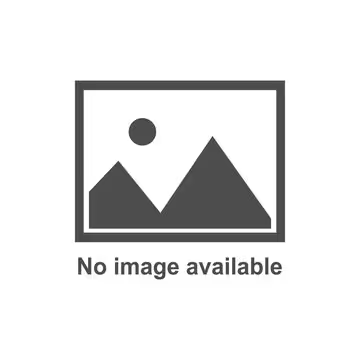
INTERVIEW – An American group of restaurants is experimenting with the application of lean thinking in its kitchens and dining areas. Planet Lean had a word with the chefs to see what’s cooking.
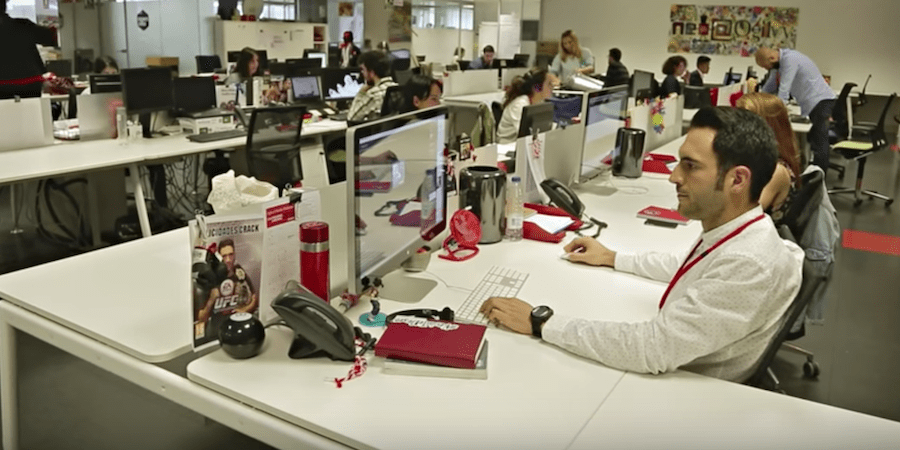
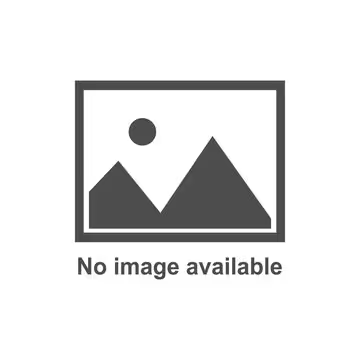
FEATURE – With lean thinking, Madrid-based Neo@Ogilvy is hoping to create a stronger connection with customers, thus learning to create value for them and redefining the overall purpose of marketing.
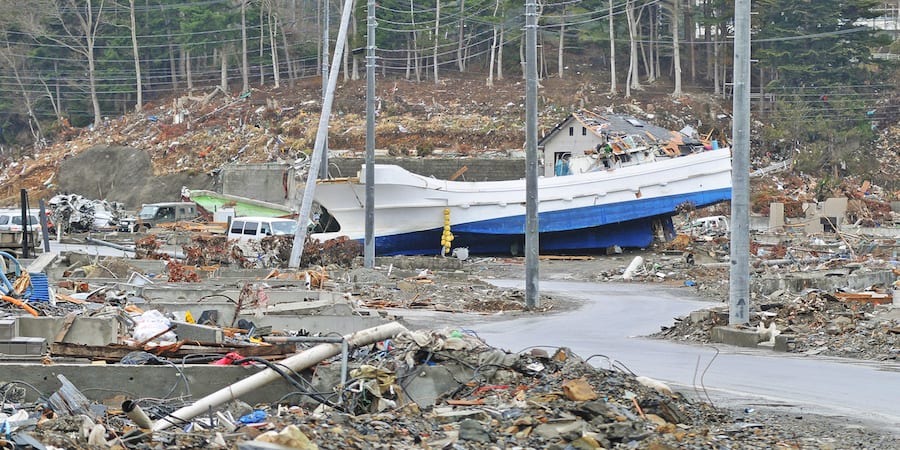
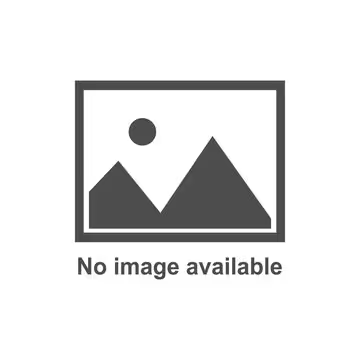
FEATURE – Much has been said and written about Toyota’s ability to recover from disasters. What many don’t realize, however, is that the company’s recovery strategy is informed by its underlying values – not just its tools.