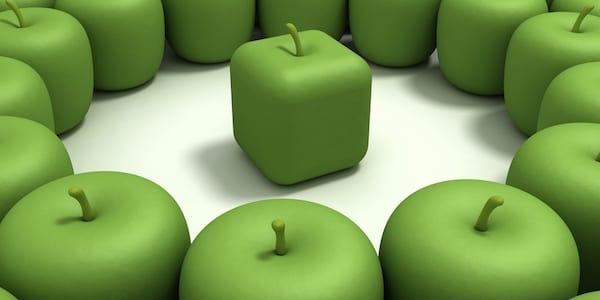
Defects can be a driver for the creation of a lean culture
FEATURE – The fifth article in the series Hazards on the road to lean analyzes the role of quality defects in helping to develop a lean management culture in your organization.
Words: Malgorzata Jakubik and Robert Kagan, Lean Enterprise Institute Polska
As no true lean person should walk by waste and ignore a chance for improvement, we felt the need to put together our reflections on things big and small that, while working with our customers, we have found to be common “speed bumps” or even show stoppers in a lean implementation. Whether systemic or tool-related, these obstacles have one thing in common: they tell our “war stories,” which we want to share with those on the road to lean, hoping they will warn them against frequent hazards others have struggled with.
YOUR QUALITY? PROBABLY NOT AS GOOD AS YOU THINK
- WORRYING ABOUT QUALITY: NOT A BAD START TO DEVELOPING A LEAN CULTURE -
One thing that working in a lean organization instils in you is an overwhelming sense of awe for quality defects. It does not matter how serious they are or how severe the fault they cause is – quality issues tend to set the entire organization in motion. As news of the defect spreads quicker than wildfire through dry bushes, the entire system is checked and secured, defect are analyzed, and teams visibly rush to find countermeasures and take appropriate action.
This is what worrying about quality results in.
We have noticed, however, that when asked about their key problems, managers who just started their lean journey bring quality up very rarely. Instead, they tend to talk a lot about on-time delivery and costs. Theoretically, most know that quality defects may hide behind the problems they mention, but in practice they’d rather concentrate their efforts on fighting what is more clearly seen as a painful issue by the organization.
Why is quality not perceived or treated as a key problem? Well, here are some of the reasons we have been given over the years, and the reality behind them.
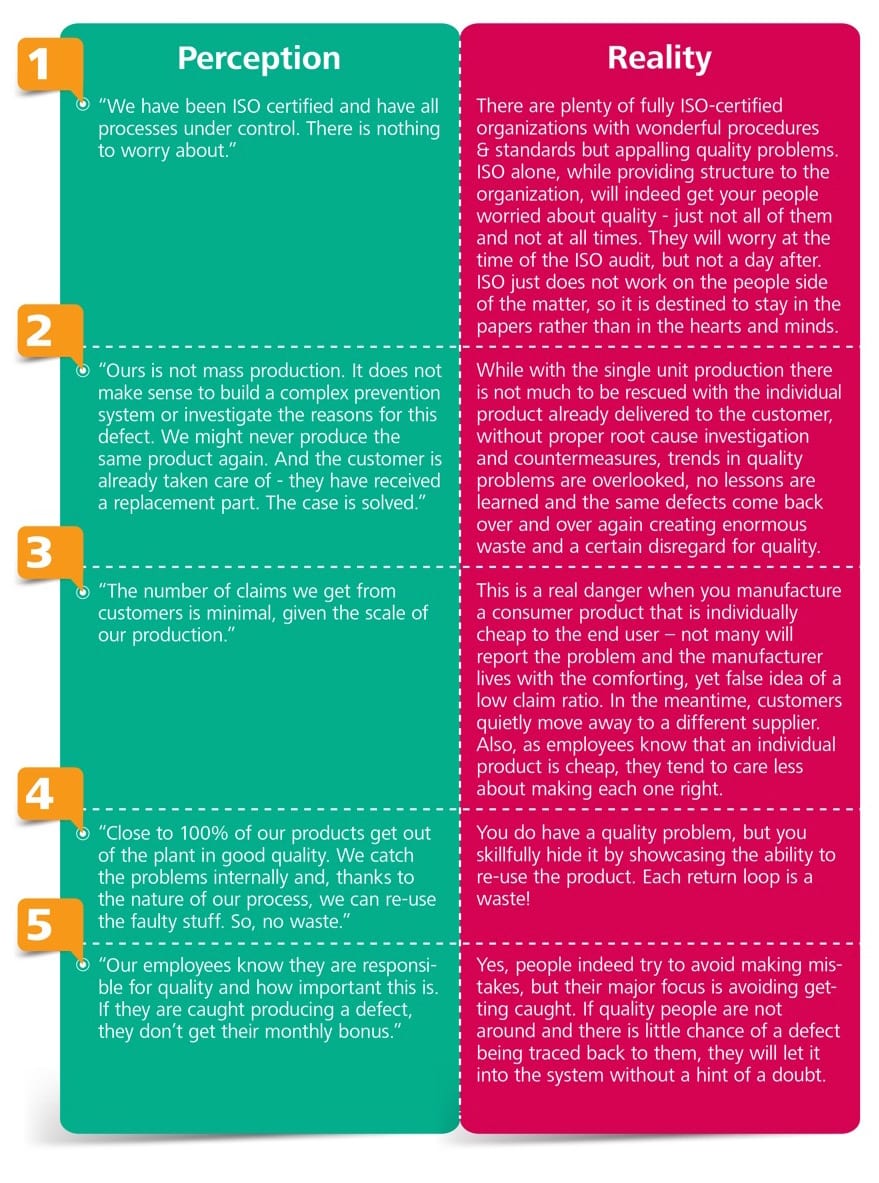
Do you still think you don’t have a problem with quality?
If you are starting to have doubts, why not consider some of the lessons we learned by working with our customers over the years:
- Leaders have to encourage a “worrying about quality” attitude among their people, by talking about it, investing in prevention, requesting analysis and calling for action when something goes wrong.
- Make it known that you WANT to hear about defects as they happen – build a clear problem escalation process so that people can rely on a well-defined communication standard and are not afraid to flag up a problem.
- Know the mantra – produce safely, produce to quality, produce volume - and never change that order.
- Define the role of your quality people well – they are neither scapegoats for quality problems nor detached policemen who point at “quality criminals.” They need to act as true partners for quality processes within the manufacturing organization.
Monitor external quality closely but watch the internal quality even more closely, and act on your findings with a sense of urgency:
- Set your defect recording system to focus first of all on causes and trends (WHY defects happened) not on locations of occurrences (that is, WHO to blame for the defect);
- Visualize the scale of the problem – visibly mark products with quality problems so that everybody can see them;
- Calculate the cost of quality – scrap, re-runs, rework overtime, etc. Make the numbers known to everybody so that they know that correcting mistakes ALWAYS costs.
- Finally, NEVER rely on the comfort of your formalized procedures - they are only as good as their practical application!
Worrying about quality is a specific enough behavior that people can understand; it provides a clear business advantage and will impact most of your other processes. Not a bad start for developing a lean organizational culture, isn’t it?
This article is also available in Polish here
THE AUTHORS
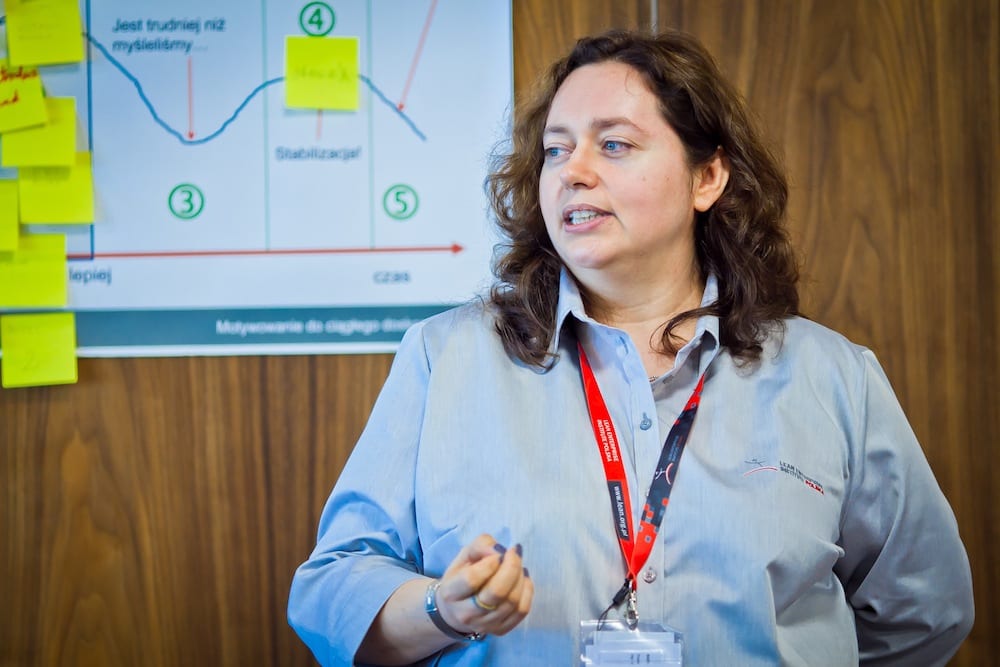
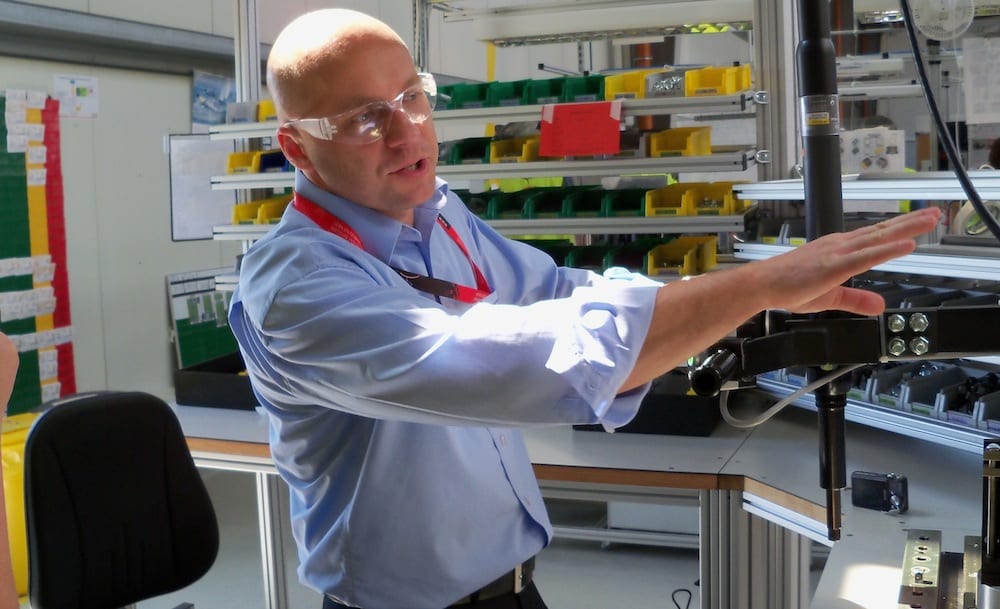
Read more
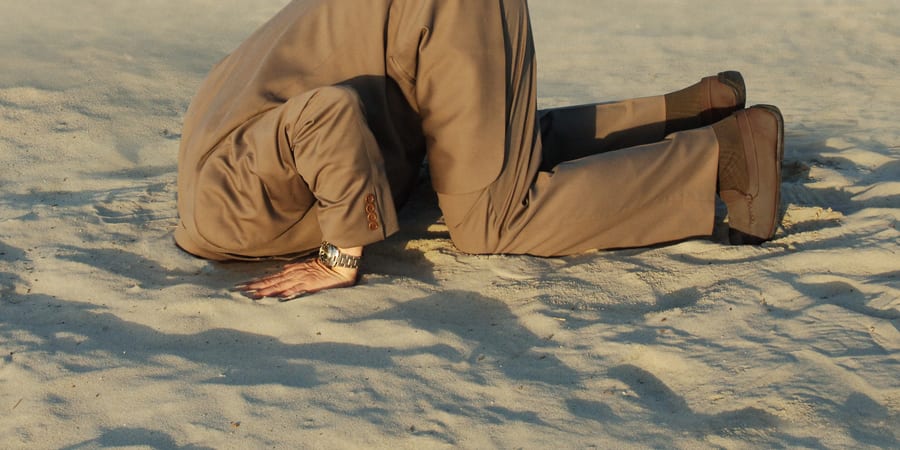
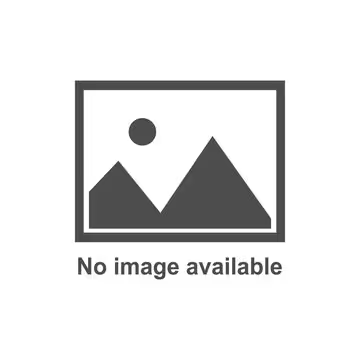
FEATURE – CEOs need to see people as assets and transform their companies’ product development systems if they are to tap into the full potential of a lean strategy.
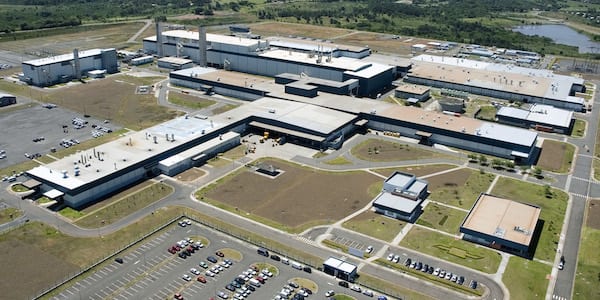
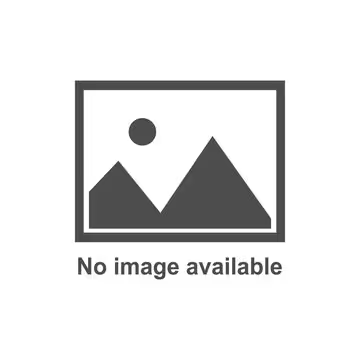
INTERVIEW – We speak with Sérgio Caracciolo of General Motors do Brasil about the carmaker’s approach to lean, its struggles, and its lessons learned.
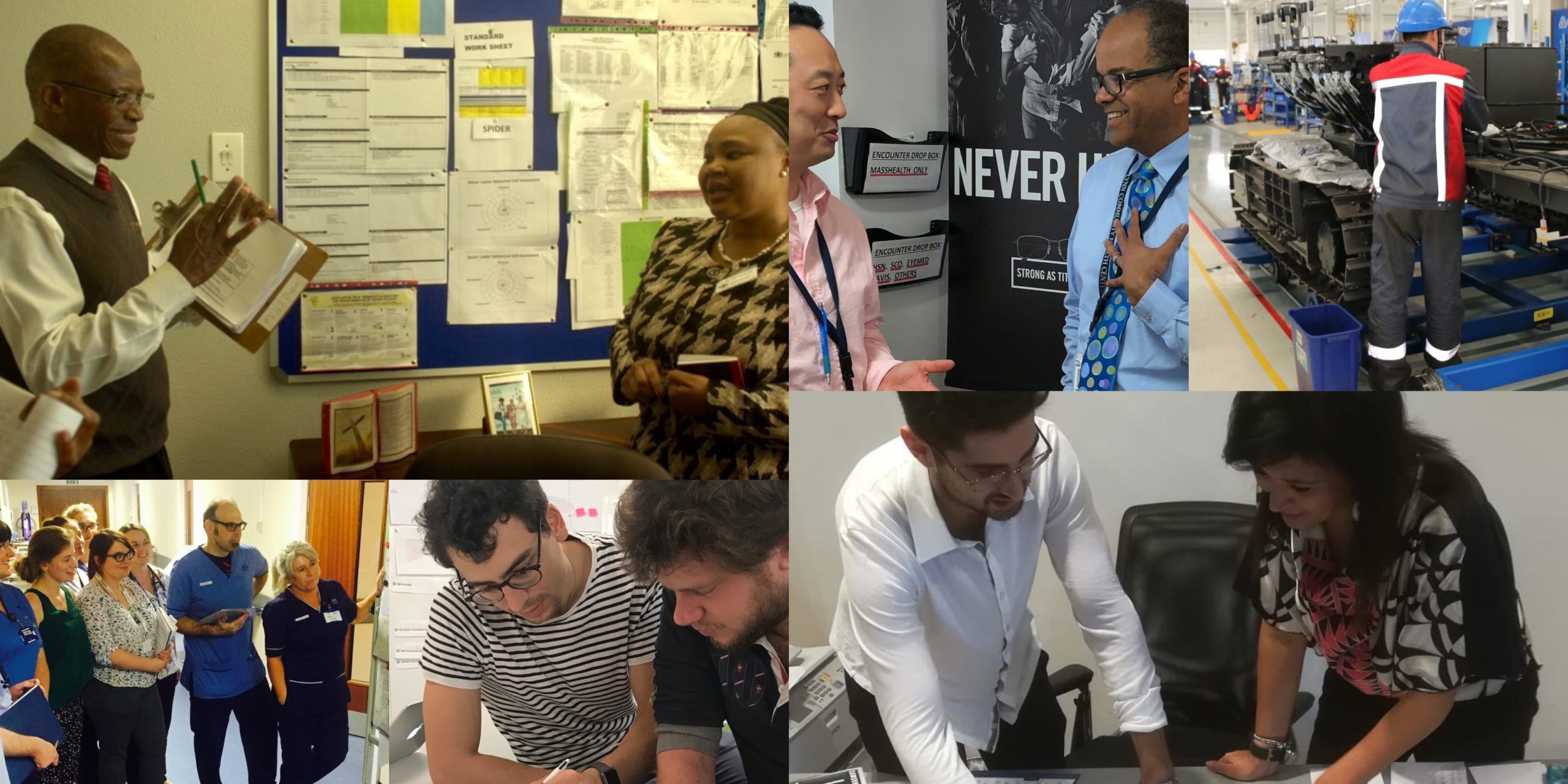
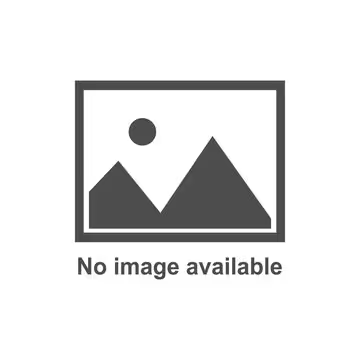
ROUND-UP – As the year ends, our editor reflects on the state of the lean movement and looks back at the best articles published by Planet Lean this year.
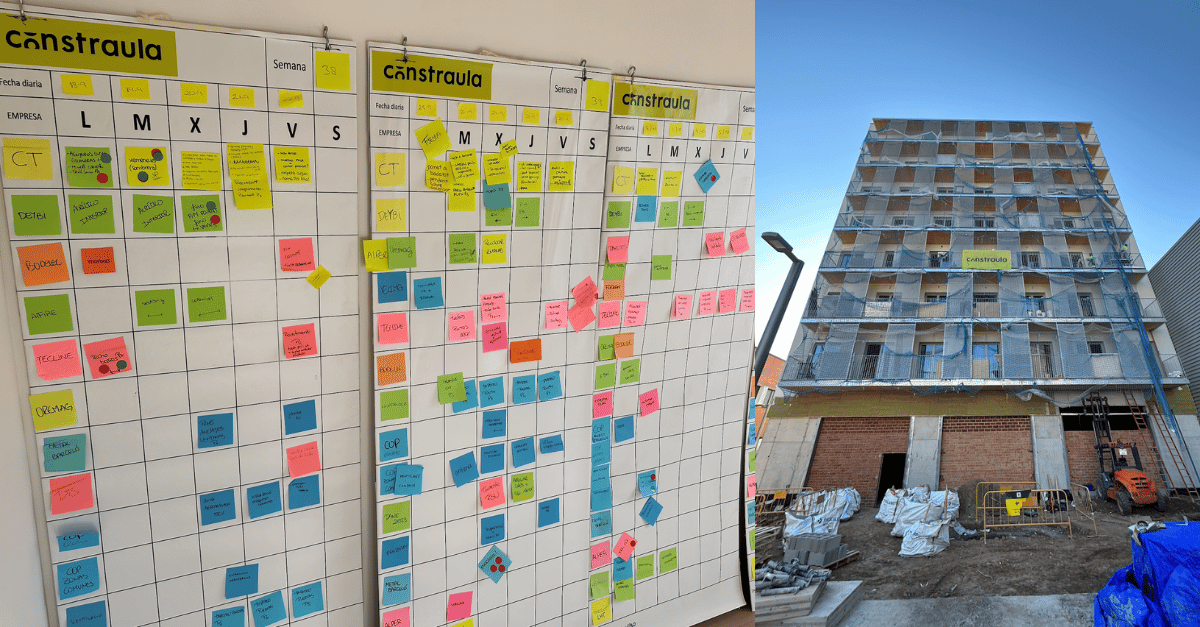
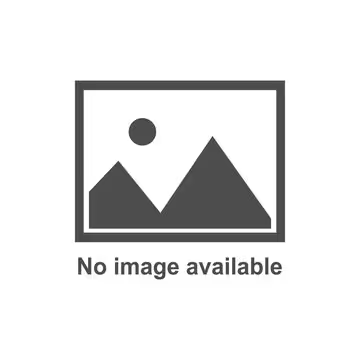
CASE STUDY – Thanks to Lean Thinking, this Spanish construction company was able to deliver a challenging project in one year, well ahead of schedule. Here’s how they did it.