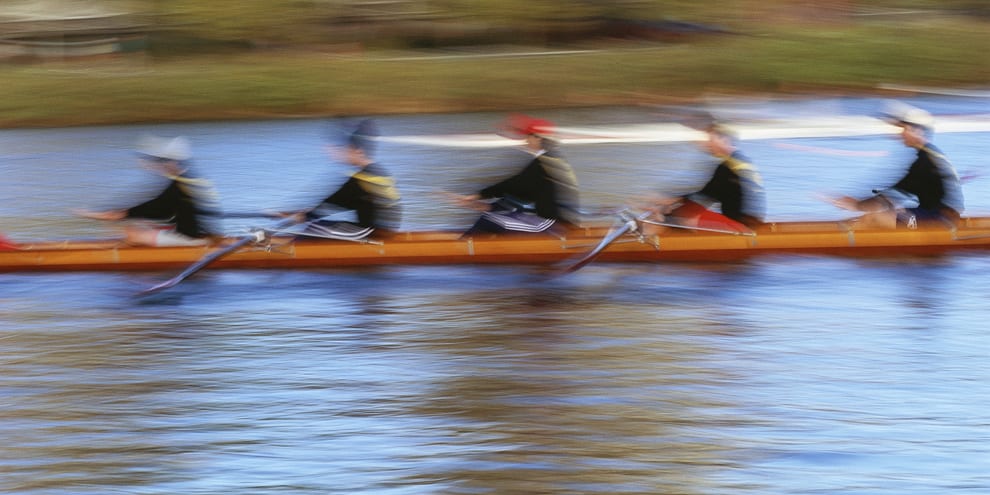
What it takes to learn lean
FEATURE – The author, a lean leader from Germany, recounts his experience bringing lean change about and discusses what it takes to truly learn lean thinking.
Words: Klaus Beulker, lean leader and author
I recently decided to write a book outlining my personal journey of transformation and learning, and to answer a vexing question: how many times does one have to experience something before that something can be generalized? Twice, three times or even more? Over the years, I have introduced and applied lean tools and principles several times and in different contexts. I have seen the same developments over and over again, which has helped me to identify the elements that are critical to the sustainment of a lean transformation. From the patterns I have observed I was able to derive a set of convictions on how to successfully introduce lean management in an organization and a deep understanding of the meaning the different methods and tools have within a complex social system. Through my book, I don’t claim to suggest my view is the right one or to establish some set-in-stone truth; instead, I want to share my experience, hoping it will contribute to the debate on what makes change possible.
It seems that many still consider lean management a miracle cure that eliminates all problems and difficulties in a production system. Yet, we can’t stress enough that lean is simply the beginning of a never-ending journey of discovery and continuous improvement. This is difficult to accept, but the sooner we accept this, the sooner we can develop a different perception of time going by, one that is characterized by greater serenity and acceptance of the current situation. This very acceptance is both a prerequisite for respect for people and recognition and a helpful precondition for less exaggerated expectations of what the future should look like.
Whether we like it or not, on the one hand, the performance of a company depends on the skills and abilities of each individual employee and, on the other hand, on the way in which people work together. Finding room for this seemingly trivial concept will require substantial changes in the way the executive team thinks about lean management. Leading change leads to changes in leadership. And yes, your own insecurity as a leader is part of the development. Executives, too, are students.
MY LESSONS LEARNED
I am often asked about the biggest lessons I have learned over my 15 years as a lean leader. Three keep coming to my mind.
The first one is to, quite simple, apply the tools. It may sound counterintuitive, because as lean thinkers we are often told not to be “tool-heads”. Yet, this was an important epiphany for me. When I had to introduce Kanban as a young engineer and asked my former sensei Freddy Ballé why that was necessary, he told me: “Just apply the tool.” Of course, I didn’t find that answer satisfactory. But it kept coming. In retrospect, this was a great learning for me: to learn how to become a lean manager, you first need to “do lean”. It is by repeatedly applying lean tools (and with a little bit of luck) that you become lean.
The second important learning for me was that lean can’t be introduced in a chaotic and unstable context. Understanding and identifying deviation from standard should also be the focus, but it is not possible when we are facing instability. This fundamental element is often overlooked when people try to introduce lean thinking in their organizations. There seems to be a belief that, in the midst of chaos, lean will miraculously eliminate our problems, but it is not like that. In other words, you can only lower the water level if you know the water is there!
The third great lesson I have learned is that the efficiency of a production system is directly linked to the skills of each individual employee. All too often, we see a complete lack of recognition of this fact, possibly because this realization means we will need to take care of every single employee in order to improve their work conditions and competences and make them more successful. Employees are not commodities, and it is only by engaging with them daily and working hard to develop them that we can improve our system’s performance.
Consequently, the speed at which the production system can change is directly linked to the speed at which such skills can be developed. Lean management organizes the learning in the every-day life of an organization, using things like dojos or Kata, so that the system can be developed continuously.
Some of these realizations were drawn from what we typically call “success stories”, but others stemmed from failures. That’s why it is so important to record everything that happens in our lean journeys, both the good and the bad. We are only right half of the time (if that).
OUTLINING MY LEAN JOURNEY
In my experience, the success of a lean turnaround depends on our ability to learn and change in a complex system. This is what I discuss in my book, by sharing a number of insights.
A lean journey begins with learning and deeply understanding the tools one by one – value stream mapping, just-in-time and jidoka. Then something interesting happens: the more we apply these tools, the more obvious it becomes that these are linked to one another. On a practical level, the driving factor for the continuous development of a production system is the continuous reduction of the lead-time, from placing the order to the fulfillment of the order. This process indicator automatically forces you to distinguish between value and waste.
But lean thinking is more than just tools. As we introduce it by applying the tools, a holistic approach emerges spontaneously, which reveals a social system that can develop and transform itself through learning. (In fact, over the course of a journey, learning begins to permeate every aspect of the lean system.) Such a system is complex, can’t be directly influenced, and does not behave in a cause-and-effect manner. In order to make sense of it, one always has to take into account the customer’s perspective, outline a strategic orientation towards a future he aspires to, and develop effective leadership and teamwork. As we acquire new information, new routines appear and we are persuaded to find better ways to do things. However, no improvement can take place unless deviation is made visible.
In order for leaders to effectively manage the learning process within an organization's social system, customer and product need to be fully understood. In addition, content-related competences, methodical competencies of lean management, a model-based idea of learning in organizations and supportive leadership are necessary.
Learning consists of four phases: from unconscious incompetence to conscious incompetence to conscious competence and unconscious competence. The first step in the learning process makes it necessary to recognize one's own limitations. The second requires willingness to abandon existing patterns. Both steps are painful and exhausting, and it’s critical that the executive live, accompany, demand and promote this development himself.
THE AUTHOR
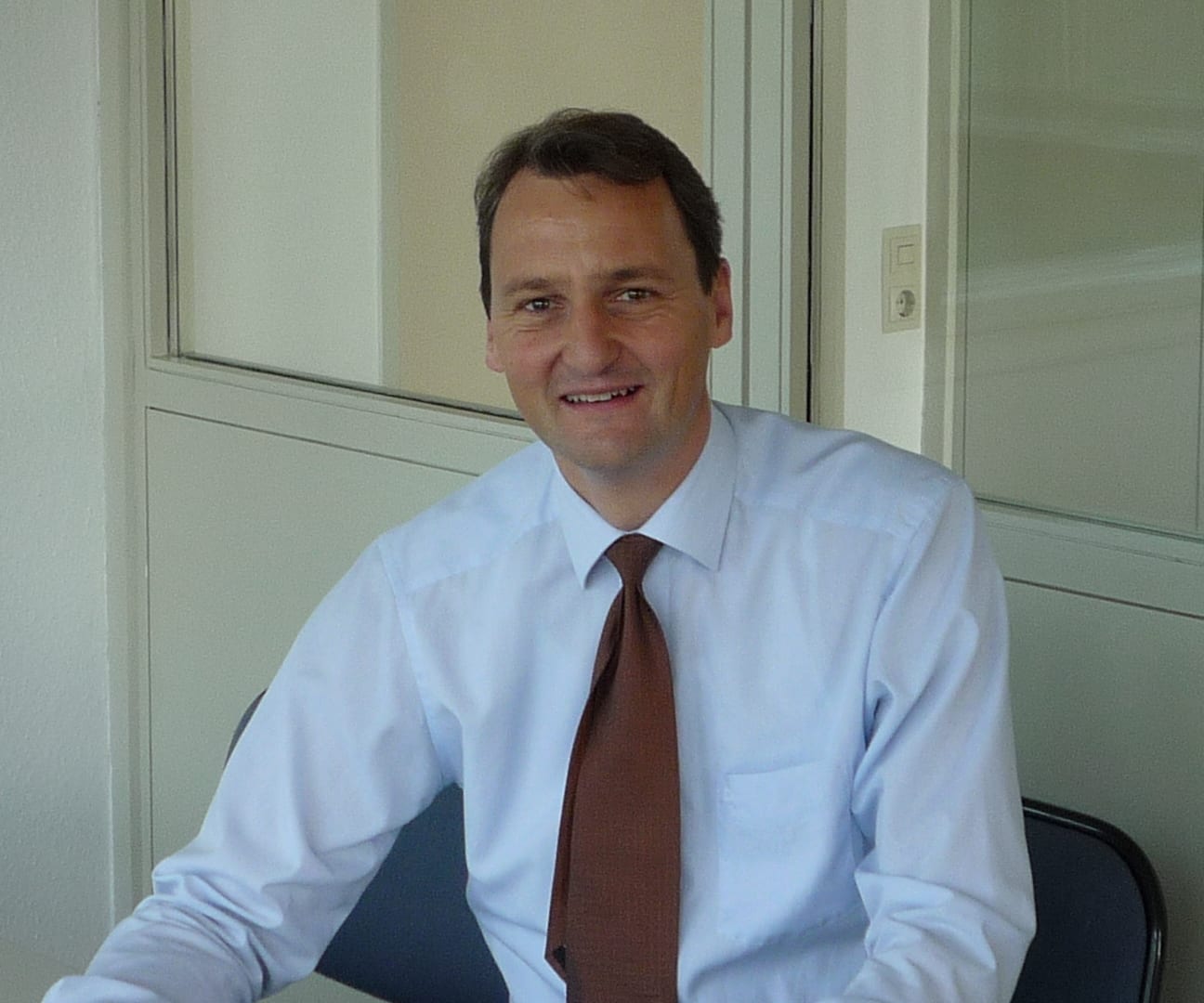
Read more
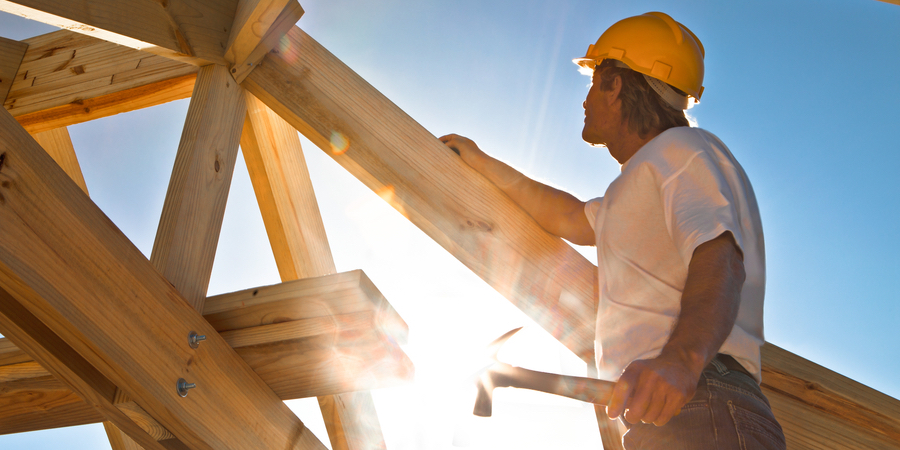
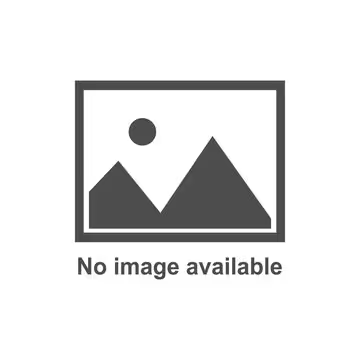
CASE STUDY – We hear from a construction company in Chile that embarked on a lean journey in 2018 to transform its culture and improve the work on its many sites.

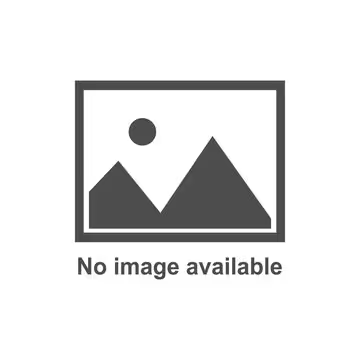
INTERVIEW – If we truly believe lean can change society, then we should use it as a lens through which to look into different aspects of our lives – even when those associations are hard to make. This month, we discuss the world of media.
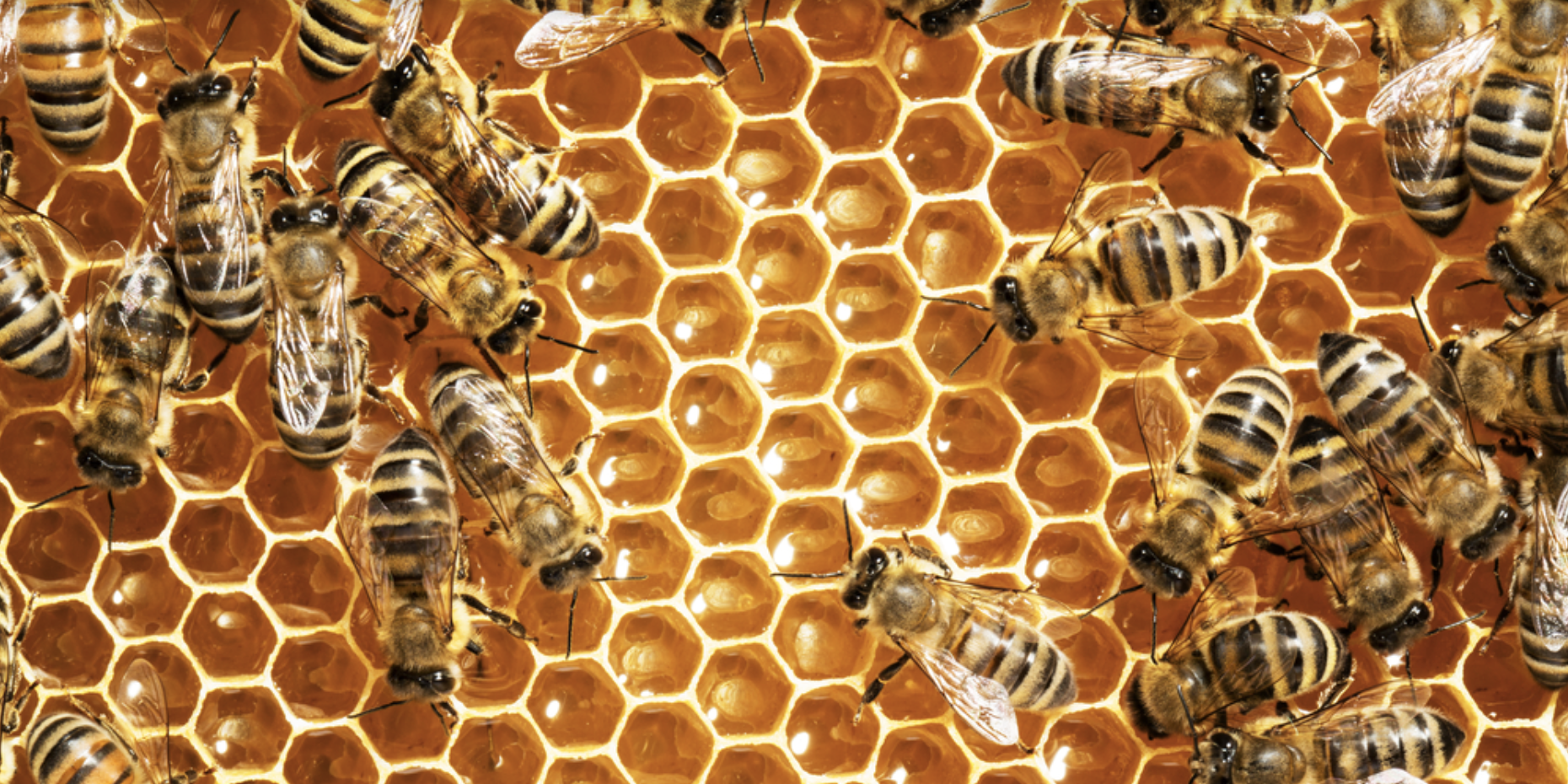
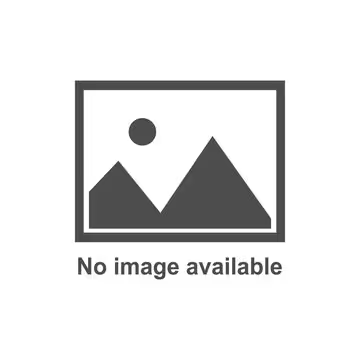
FEATURE – To consistently identify new and better ways of doing things can breathe new life into a lean journey, but only if the knowledge developed can be effectively shared across the organization.
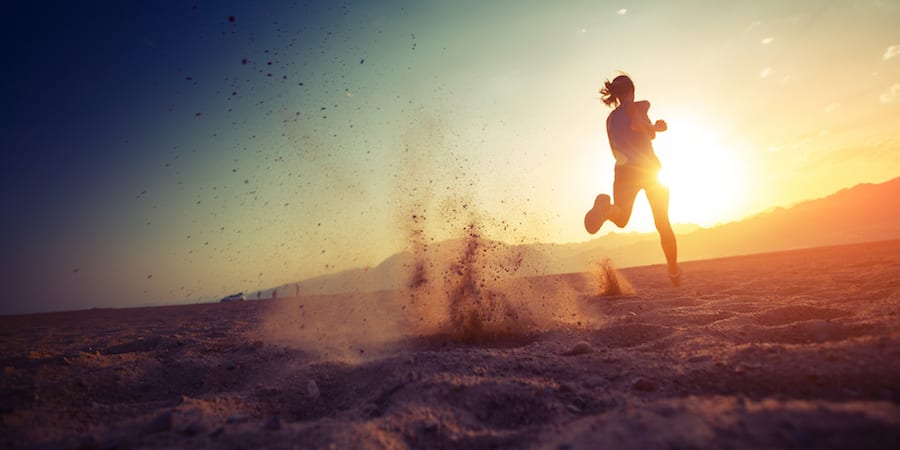
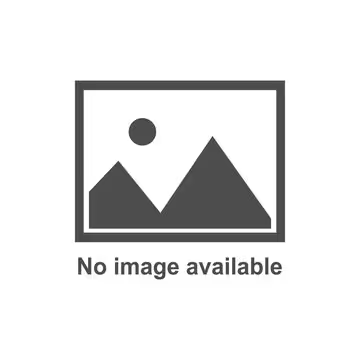
WOMACK’S YOKOTEN – The author visits a company that has sustained lean for a decade. In trying to understand how they did it, he finds how fundamentally the management system has changed.