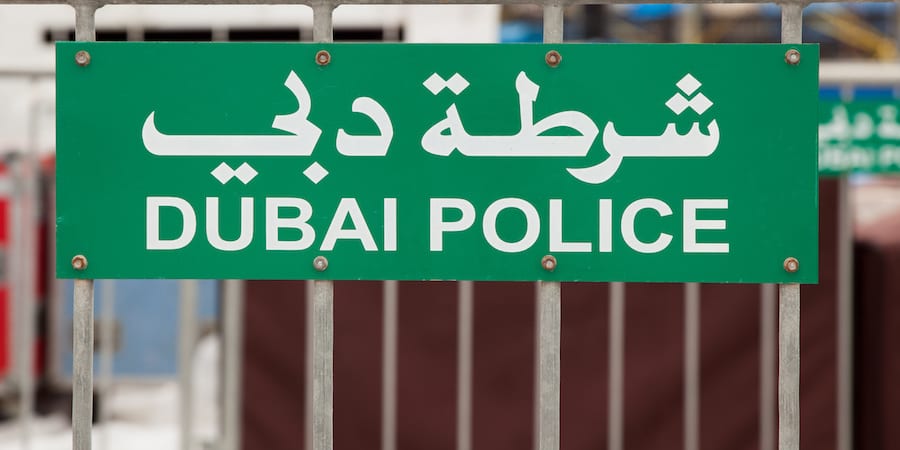
The improvement journey of Dubai Police
INTERVIEW – When we say that lean management can be applied to any human endeavor, we mean it. In this Q&A we learn about how knowledge sharing has been boosting the improvement journey of Dubai Police.
Interviewee: Eng. Omar Al-Khaja, Head of Section, Mechanical Department, Department of Transport and Rescue, Dubai Police
Planet Lean: How long has Dubai Police implemented lean thinking for?
Omar Al-Khaja: Dubai Police has implemented lean six sigma for 10 years, with hundreds of projects completed and people trained. We have had a “go see” culture from the beginning, but having an actual improvement methodology drive our efforts has made it easy to frame problems and achieve change. Over the years, the organizational culture has changed a lot: our senior leaders regularly go on gemba walks, visiting police stations and departments to observe processes, assess progress, and offer guidance. We are proud to see this new way of thinking is now trickling down to the lower levels of the organization, and I am sure this approach has greatly contributed to making us one of the most innovative and forward-thinking police forces in the world.
PL: What can you tell us about the sort of projects you have been running?
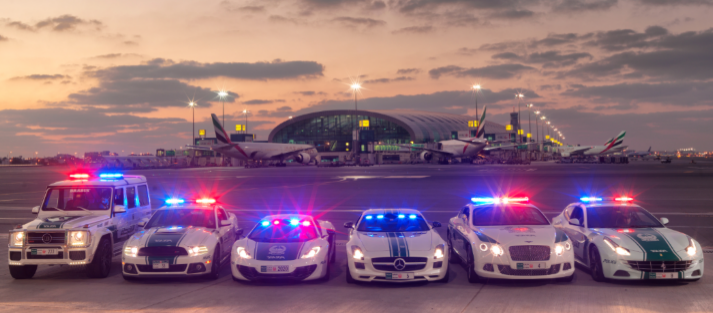
OAK: We go where there is a need, where the voice of the customer told us that a problem has arisen – over the years, we have completed 175 improvements projects. Every area of the business is expected to complete at least one a year.
The project for which I am responsible in the Mechanical Department of the Department of Transport and Rescue, for instance, is to shorten the time needed to maintain and service light vehicles. Our department can service almost every make of car manufactured in the world, as well as marine and rescue vehicles – this is no easy feat, especially if you consider our unique fleet of high-performance vehicles, which includes a Lamborghini, a Ferrari and a Bentley (to name but a few). This lean six sigma project was a result of the complaints our colleagues filed because we were keeping their cars for too long. Through the careful analysis of the root causes of our problems (among others, the failure to bring in vehicles for regular maintenance and spare parts shortages) and the development of the right countermeasures (from setting up an appointments table to storing the required spare parts before a job begins), we managed to reduce our lead-time from two days to four hours, while actually increasing the number of jobs we perform on our light vehicles. In total, we experienced a 31% increase in efficiency.
But there are many more examples of projects within Dubai Police. For instance, we are trying to reduce the number of fatalities resulting from car accidents (safer drivers are happier drivers, and we want a lot of them on our streets), and even reduce minor crimes across the city. We are also striving to reach the scene of a car accident within 15 minutes from the time we receive the call (we are currently at 93.45% of accidents reached within that timeframe, in the face of a target of 90%). Nobody wants to wait for hours for help to show up, after all!
PL: Fascinating. What sort of behavioral changes do you need to ensure the success of projects, and what did you do to get there?
OAK: We need people to become problem solvers, and in order to get there we must ensure that whenever an issue is fixed that learning is captured and shared with everyone at Dubai Police. So we added a level to the DMAIC cycle (a staple of the six sigma approach), which we call Knowledge Transfer. A report is now written for each completed project, and then emailed to every person working in the organization. We also keep them on file in our Library for everybody to see, and send an official letter about them to all departments and police stations.
We have a Knowledge Department these days, which organizes an annual internal competition that awards the best improvement projects. You have no idea how much awareness this creates!
Training is of course a huge part of what we do to provide our people with the skills they need. For example, a Dubai Police team has recently taken an intensive course in kaizen at the Kaizen Institute. We are sure this will improve the effectiveness of our short-term initiatives.
PL: What is the role that leadership plays in developing people?
OAK: Seeing the boss going to the “shop floor” and asking people about their work gives them pride in what they do. You can see it in their faces. We do our best to ensure that leadership at Dubai Police happens at the gemba.
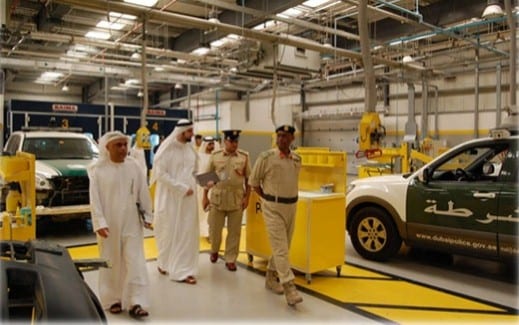
PL: What would you say is the biggest obstacle to lean six sigma?
OAK: The hardest thing is to get people to accept there is a better way of working and that we must embrace that method, and to let go of their old ways. It’s pure change management, with all the difficulties that entails.
But it is clear that our culture is shifting: over the past decade, our people have gotten better at brainstorming and at leveraging the toolbox we have given them to solve problems in a more systematic way. Everybody can tell you what lean six sigma is now, and I would say that most people within our organization have really embraced the philosophy – and that’s because they have seen the great impact it can have.
PL: What results have you been able to achieve, and what’s next for Dubai Police?
OAK: Besides the important cultural shift and great process improvements we are achieving, we have received both local and international awards for our quality management system. Going forward, there will no doubt be new challenges for Dubai Police (we are, for example, gearing up for Dubai Expo in 2020, when the city is expected to receive 20 million visitors – six million more than our 17,000 officers are currently serving) but we are sure that our decade-long experience with lean six sigma will help us face up to them head on.
THE INTERVIEWEE
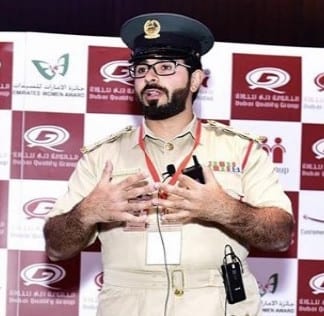
Read more
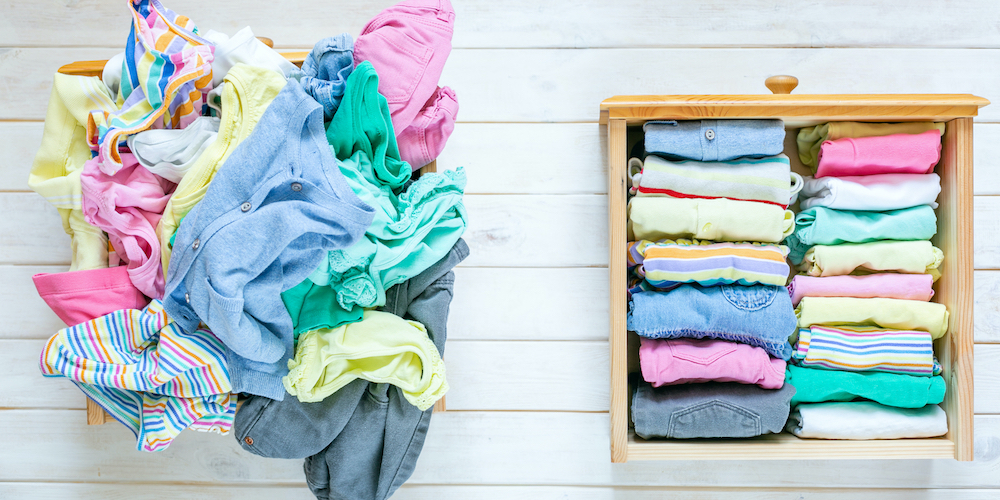
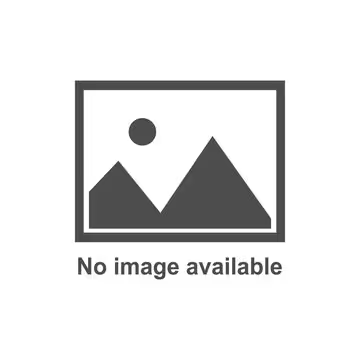
FEATURE – The Japanese organizing guru has become very popular in recent years, but what does Lean Thinking tell us about her approach?
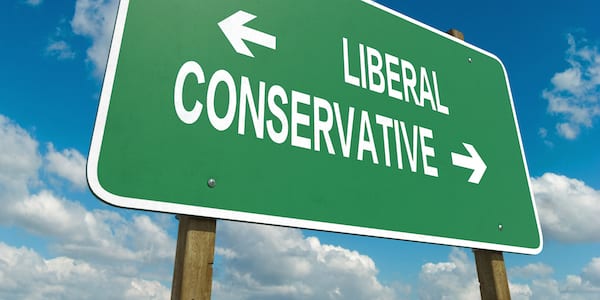
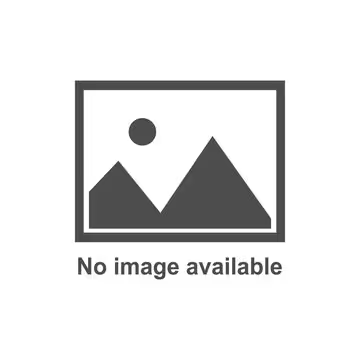
COLUMN - In political terms, is lean management more in line with conservative principles or progressive ideas? Michael Ballé reflects on a tough question.
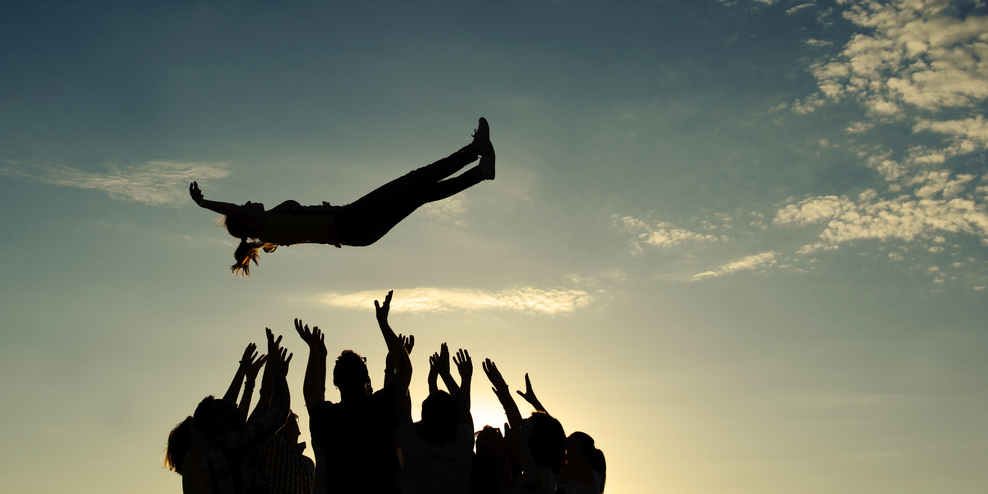
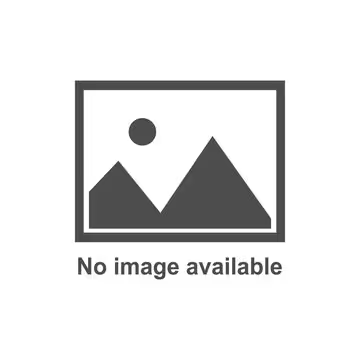
FEATURE – Employee happiness leads to greater efficiency and higher quality, which is why it’s increasingly being adopted as an indicator by firms. But how does lean relate to happiness?
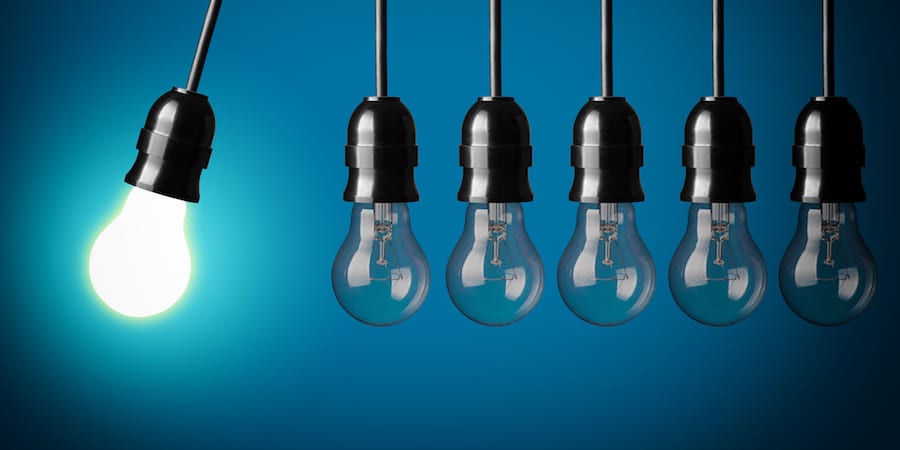
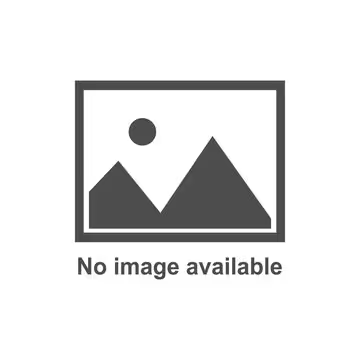
1 QUESTION, 5 ANSWERS – Without the active participation of people in improvement activities, lean is nothing but theory. Sadly, engaging folks is easier said than done. We asked five lean practitioners to share their approach to people engagement.