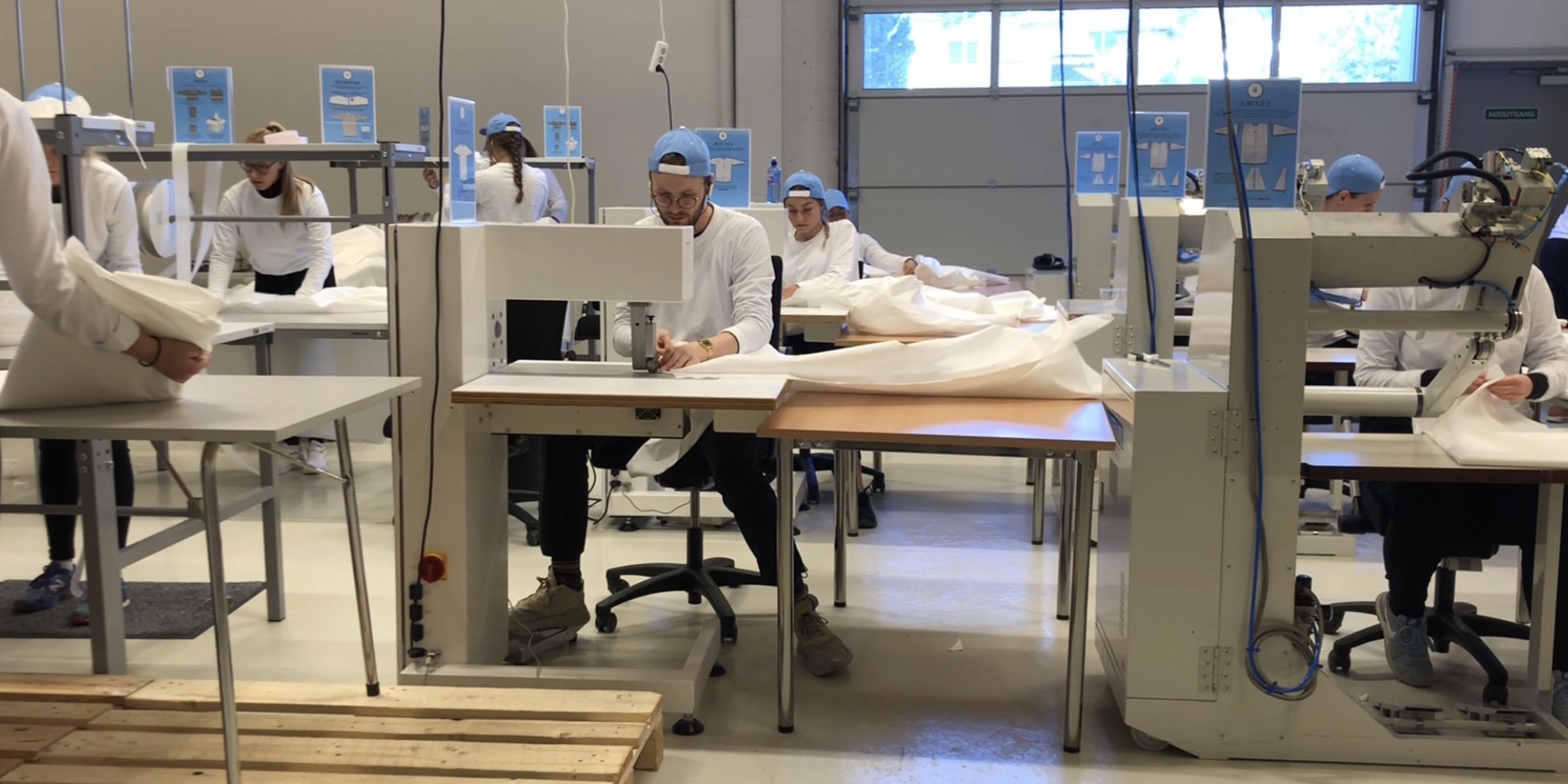
Lean ASAP!
CASE STUDY – Some blamed lean for the shortages of personal protective equipment (PPE) in first wave of the pandemic. This small Norwegian producer of disposable bedsheets used it to establish and ramp up the production of medical gowns for healthcare workers.
Words: Daryl Powell, Research Manager, SINTEF Manufacturing AS, and Asgeir Nilsen, Chief Operations Officer, ASAP Norway
The first case of Covid-19 in Norway was registered on February 26th. Just a few days later, on March 1st, Norwegian Prime Minister Erna Solberg and Health Minister Bent Høie began to voice concerns over shortages of personal protective equipment (PPE) for front-line healthcare staff in Norway.
Following a call to action from the Norwegian Ministry of Health, on March 20th ASAP Norway – a producer of highly absorbent disposable bedsheets based in Skien, Vestfold and Telemark – committed to establish a completely new factory that would use next-generation ultrasound welding technology to produce disposable protective medical gowns. The first gown was successfully produced just three weeks later. In total, the company was to produce and deliver 400,000 gowns with the option of an additional 200,000 over the coming months.
“Everything happened so fast,” says Astrid Skreosen, founder and CEO of ASAP Norway. Astrid established the company in 2007 to develop the next generation of highly absorbent disposable and biodegradable protective sheets. “On the 19th of March we met with Norwegian Health Minister Bent Høie, and one day later we signed the contract to produce and deliver gowns to the South-East Norway Regional Health Authority (Helse Sør-Øst). A few days later we signed the contract to lease the building where we were to install the new production lines, and already on the 10th of April we began training new employees to manufacture, assemble and pack the most comfortable disposable protective medical gowns on the market,” recalls Astrid.
Having only produced 300 gowns in the first week of production, however, Astrid and the ASAP team realized that it would take hard work and a lot of learning to ramp up to the target requirement of 3,500 gowns per day. It wasn't long before they turned to lean thinking and practice to help them get there.
CREATING CLARITY
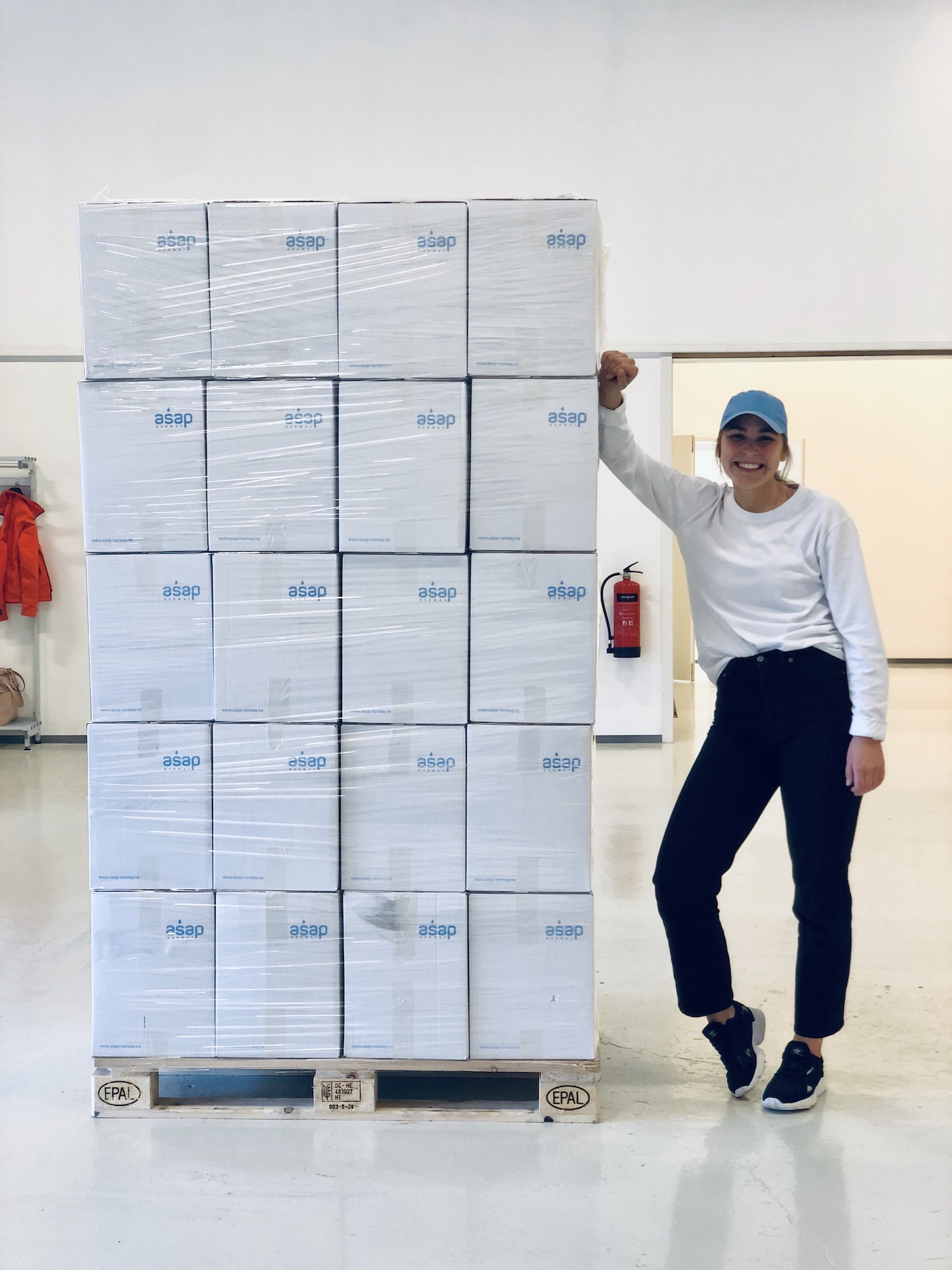
As with many lean journeys, this one also started with a brown paper mapping exercise to create awareness of the material and information flow and help managers and employees to develop a deep understanding of the actual work content required to manufacture the product. The team used direct observation and standard work combination tables to document the current work standards. This part of the lean puzzle was rounded off with a load-levelling exercise – heijunka – to visualize the current cycle time of each workstation compared to the desired takt time, with the intention to re-allocate work content and balance the workflow with the takt time. However, with an ambitious target takt time of 17 secs (212 gowns per hour), the team were still struggling to produce 600 gowns per day. Something more was needed.
In addition to training the operators in the documented work standards, the ASAP team created a common understanding of expectations, in terms of quality and productivity. For quality, employees were coached to follow the principle “correct-from-me”, making themselves accountable for the quality of the products they pass to the following step down the line. Any non-conformances were visualized by marking up a sample gown on the shop floor – which served as a full-scale measles chart. Productivity was also visualized using an hour-by-hour board, which showed hourly production rates and, in doing that, challenged the team to discover and explore the problems that prevented them from producing to takt.
One challenge that the team encountered was managing the bottleneck process, which at that time was the cutting and preparation of material for gown manufacturing. Feeding the line with enough raw material to keep it flowing was problematic, but the operators quickly implemented a number of simple improvements, including a Kanban system to visually manage the replenishment of materials to the line, and the introduction of several work-holding devices to simplify and stabilize the cutting process. With these countermeasures in place, the bottleneck shifted to the welding process itself, which had been the overall intention from the start (based on the capacity of the machines, ASAP Norway had purchased enough units to make three production lines in order to achieve the output required to deliver the anticipated quantity of gowns). From that moment on, day after day and week after week, productivity began to increase. In Mid-May, it reached 1,000 gowns per day. By the end of May, 1,500 gowns per day. It went up to 2,500 gowns per day in early June. On June 23rd, ASAP Norway received an e-mail from Helse Sør-Øst congratulating them for delivering “the best protective gown on the Norwegian market”.
LEARNING FROM FAILURE
Things were going great for ASAP Norway. With the Norwegian summer vacation just around the corner, in July the ASAP team had managed to achieve its target rate of productivity – 3,500 gowns per day. But then, disaster struck. Out of nowhere the company received some bad news from Helse Sør-Øst. “They told us the latest batch we delivered had not been approved by the Health Authority,” Astrid explained, disappointedly. It appeared that there was a possibility of defects due to weak joints in the biodegradable fabric. The team were required to revisit the technical specification of the product, which until that point had been satisfactory.
On closer inspection, the team uncovered a technical concern with the new ultrasound welding machines. It turned out that the machines were neither designed nor intended for use on materials with a high content of viscose, which gives the ASAP gown its biodegradable properties. Of course, with a limited throughput, the problem went unnoticed. It simply did not exist. However, as throughput intensified, the material began to melt and deposit itself on the welding wheels, which presented the potential to interfere with the strength of the weld. The manufacturer of the ultrasonic welding machines was on-hand to provide support, but due to Covid-19 travel restrictions they couldn’t provide in-person assistance. To rectify this mistake, ASAP Norway had no other option than to temporarily repurpose the factory to rework the previous batch of gowns – adding spot-weld reinforcement at specific locations on the product.
For the next couple of weeks, the ASAP team reworked thousands of gowns to prevent product failure in the field. But rather than letting this unfortunate deviation from standard get them down, the company simultaneously set about redesigning the product to altogether eliminate this potential failure mode. Combined with expert assistance from the machine producer to develop in-house expertise locally, the company has now been able to master the ultrasonic welding technology to again deliver defect-free products to Helse Sør-Øst.
“Although this level of learning has come at a significant cost, it also has great value,” concludes Astrid. ASAP Norway are now looking to the future with ambitious plans to establish a full-scale sustainable manufacturing facility to ensure they can meet the requirements of the Norwegian health authorities as well as the uncertain demand that future pandemics might bring. Lean Thinking has certainly presented ASAP Norway with a challenging set of conditions for framing continuous improvement and achieving long-term business growth.
THE AUTHOR
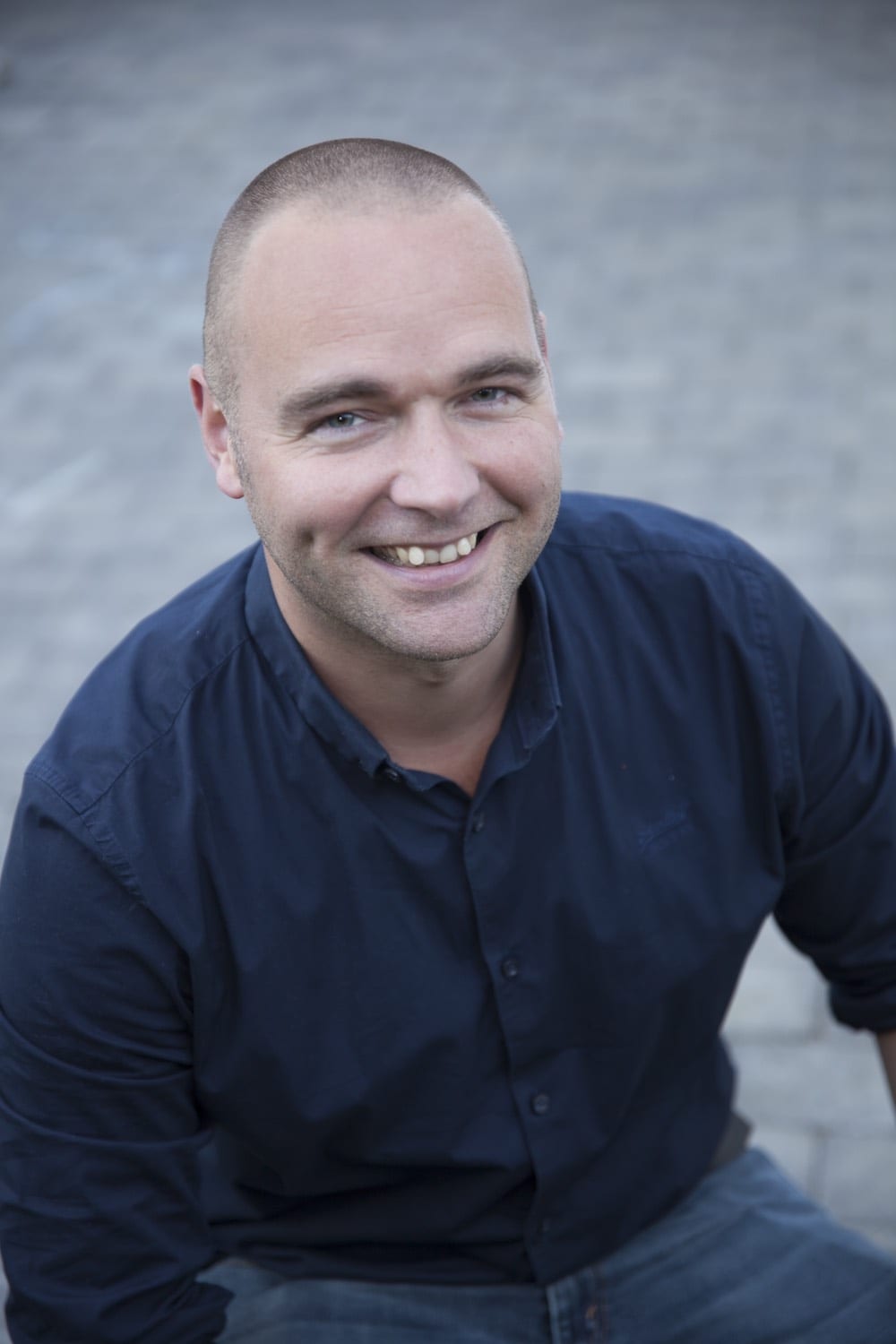
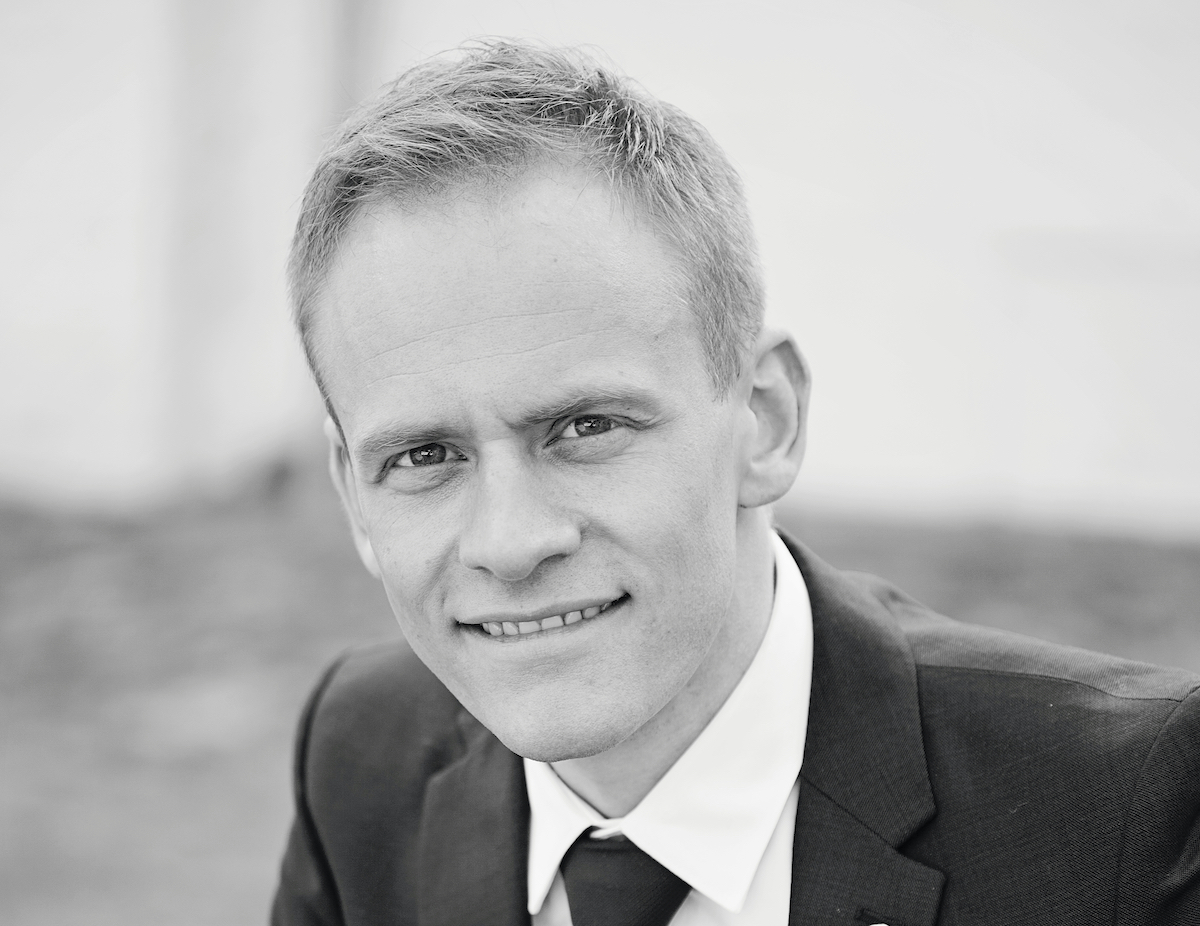
Read more
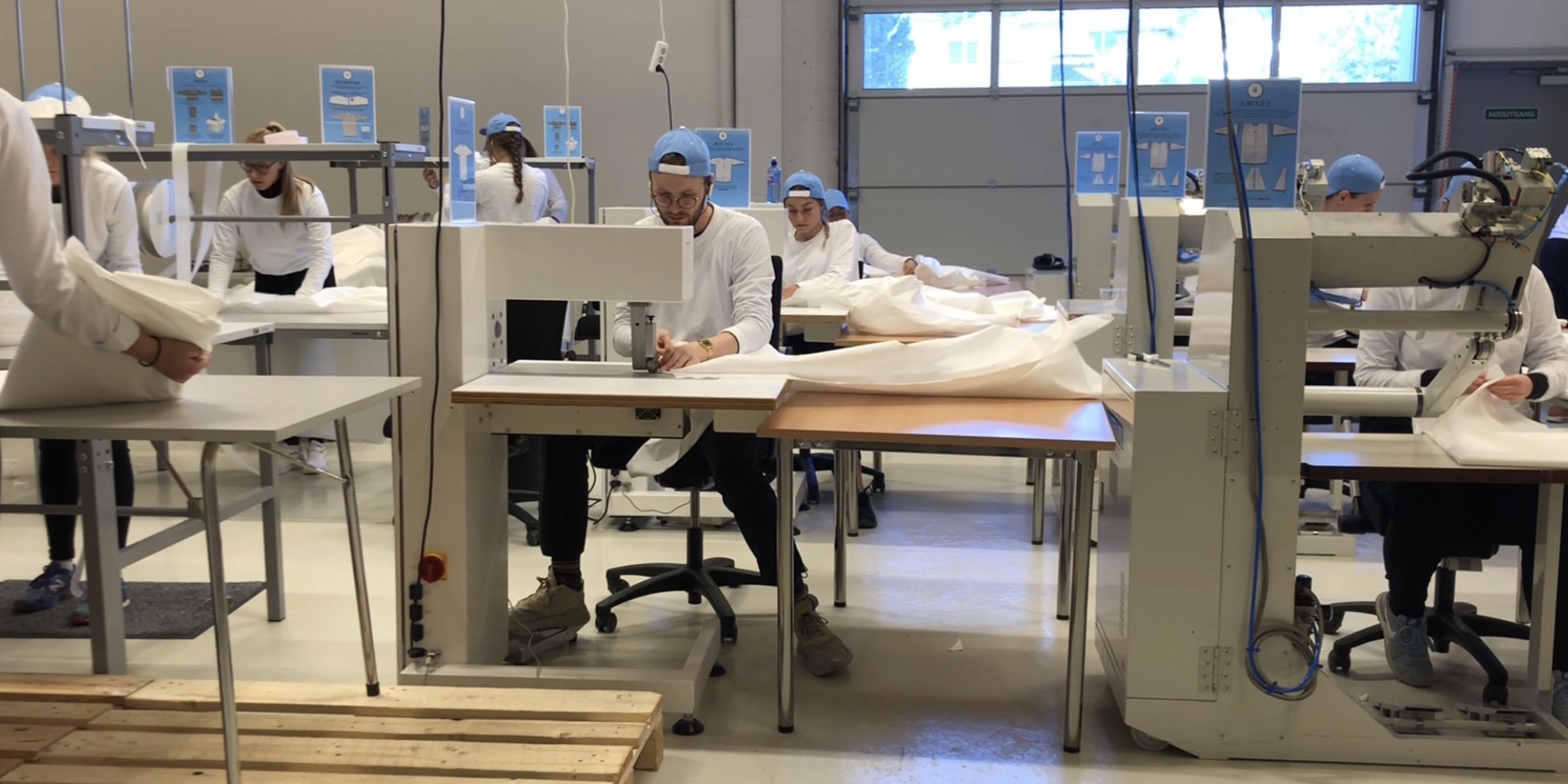
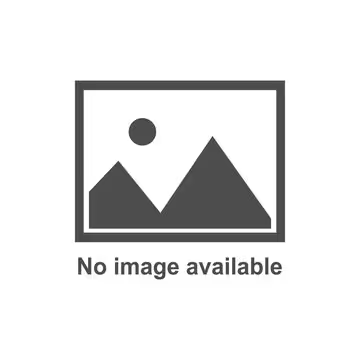
CASE STUDY – Some blamed lean for the shortages of personal protective equipment (PPE) in first wave of the pandemic. This small Norwegian producer of disposable bedsheets used it to establish and ramp up the production of medical gowns for healthcare workers.
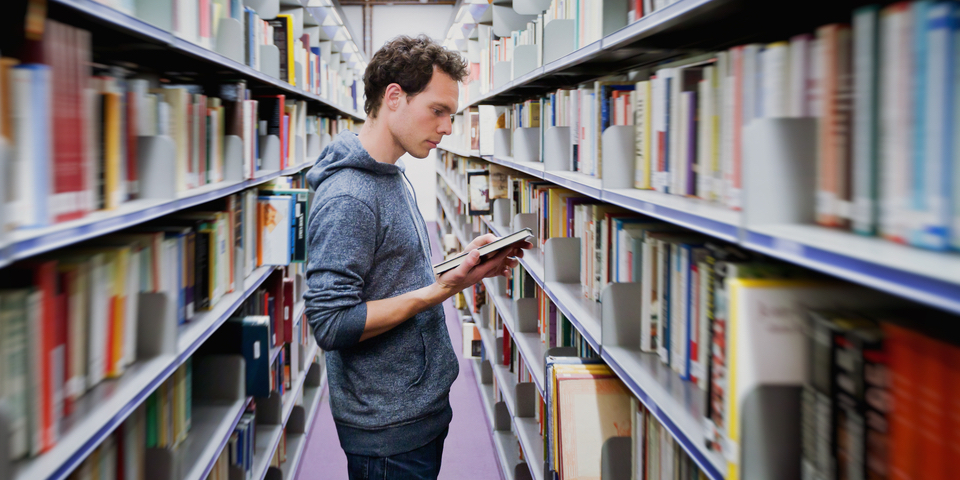
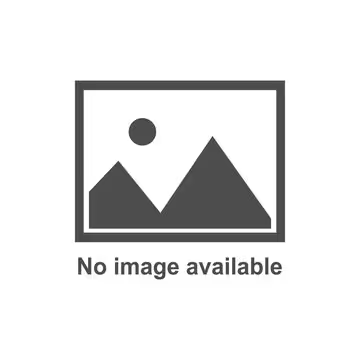
FEATURE – What can the world of lean and the world of education learn from one another? The author reflects on the synergies between these two realities.
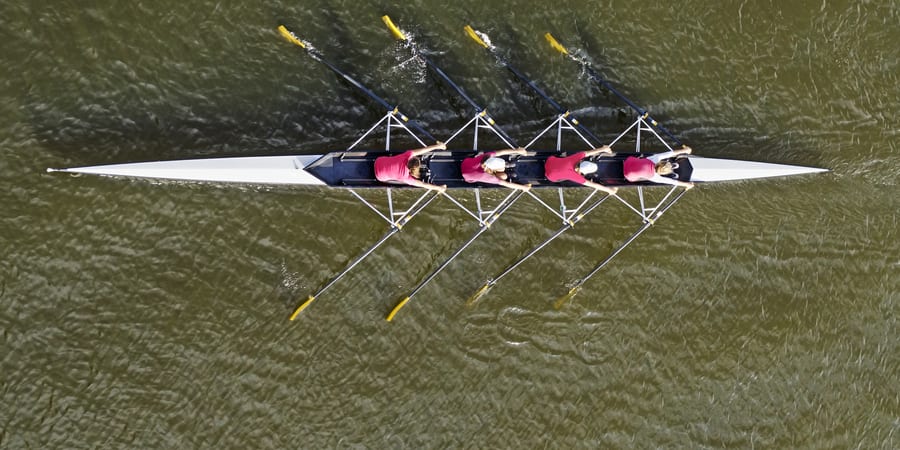
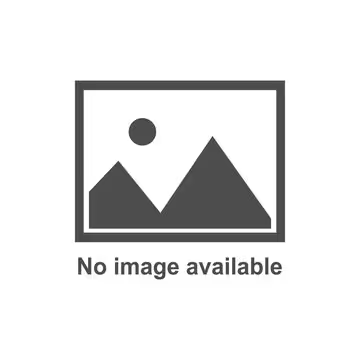
FEATURE – We all want to create a lean culture in our organizations, but what makes cultural change possible? And, more importantly, what are the leadership behaviors that enable a new culture to take root?
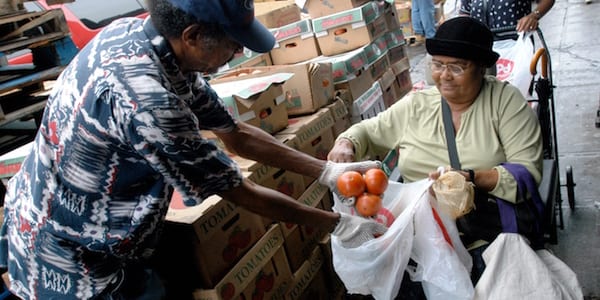
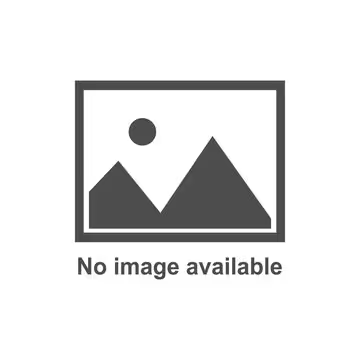
INTERVIEW – Lean for social good may sound new to many, but to the CEO of one of America’s largest food banks, the partnership between her organization and Toyota to defeat hunger in the Big Apple seems just natural.