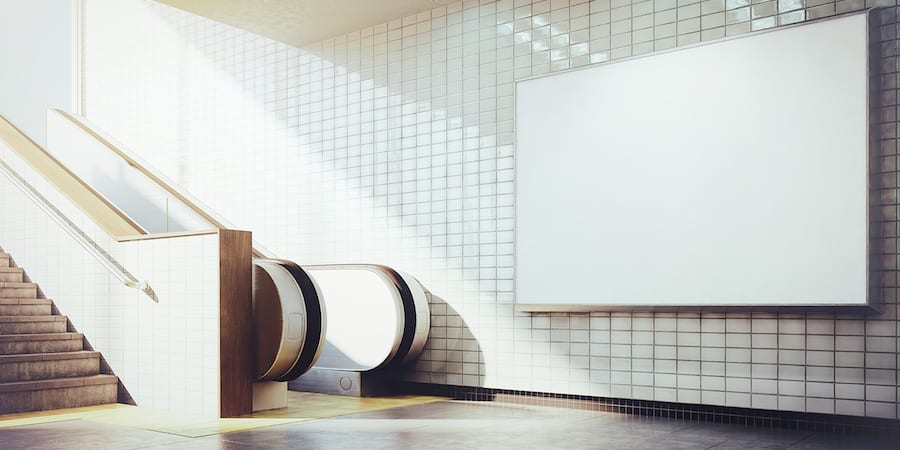
Why there is no Lean Manifesto
FEATURE – Why doesn't lean have a manifesto? The authors highlight the core principles and values of lean thinking, but warn these can only go so far without constantly learning from daily problem solving.
Words: Dimitri Baeli, Chief Technology Officer at LesFurets.com, and Michael Ballé, author, executive coach and co-founder of Institut Lean France
The Agile Manifesto has been a very important rallying point for all developers seeking a better way to create software since 2000. Seventeen years after it was written, it is still just as relevant – driving the core mindset of agilists around the world.
If you have never come across the Agile Manifesto, it's interesting to read what it says (original source can be found here):
We are uncovering better ways of developing software by doing it and helping others do it. Through this work we have come to value:
- Individuals and interactions over processes and tools
- Working software over comprehensive documentation
- Customer collaboration over contract negotiation
- Responding to change over following a plan
That is, while there is value in the items on the right, we value the items on the left more.
We follow these principles:
1. Our highest priority is to satisfy the customer through early and continuous delivery of valuable software.
2. Welcome changing requirements, even late in development. Agile processes harness change for the customer's competitive advantage.
3. Deliver working software frequently, from a couple of weeks to a couple of months, with a preference to the shorter timescale.
4. Business people and developers must work together daily throughout the project.
5. Build projects around motivated individuals. Give them the environment and support they need, and trust them to get the job done.
6. The most efficient and effective method of conveying information to and within a development team is face-to-face conversation.
7. Working software is the primary measure of progress.
8. Agile processes promote sustainable development. The sponsors, developers, and users should be able to maintain a constant pace indefinitely.
9. Continuous attention to technical excellence and good design enhances agility.
10. Simplicity – the art of maximizing the amount of work not done--is essential.
11. The best architectures, requirements, and designs emerge from self-organizing teams.
12. At regular intervals, the team reflects on how to become more effective, then tunes and adjusts its behavior accordingly.
To take a phrase out of Toyota's playbook, lean is essentially about "meeting challenging goals by engaging the talent and passion of people, who believe there is always a better way." So far, so good.
So why isn't there a Lean Manifesto?
The idea to define lean values in a page is certainly compelling, but is it possible? One difficulty is, of course, that lean thinking has no absolutes – it would be very hard to say that "this is better than that" in all cases. There is no doubt that safety is better than no safety, and quality is better than poor work, but when it comes to how to achieve these goals, the only answer is: it depends. For instance, assuring safety by creating more complex and safeguarded machines doesn't necessarily work, because human beings will find a way around a cumbersome process and take new, unforeseen risks. Similarly, quality assurance is very different from quality because people tend to confuse the map and the territory, and will easily mistake correctly filled-in checklists and paperwork with the actual work, missing the focus and mindfulness that lead to real quality.
Lean thinking, for instance, would have a general preference for individuals and interactions over processes and tools, but in specific cases it would consider the discipline of the process and rigor of the tools as essential to engage people's thinking and boost teamwork. If we look at the four guiding values of the Agile Manifesto, we'd say lean thinkers would have a bias towards them, but by no means a systematic preference. It all depends on the context.
To figure out how this upside-down thinking works, let's consider a set of questions:
- What more value (in terms of added functionality, ease of use or lower costs) should you bring to your product or service to better help customers with what they want to do so that they prefer working with you instead of your competitors?
- To find this extra value, where should people deepen their technical expertise and ability to work with each other to come up with a better understanding of issues and more ingenious solutions?
- In order to discover these hidden leverage points, how can quality, flexibility and diversity be increased in existing processes to discover pain points by reducing overall lead-time?
- How to engage each person and each team in kaizen to improve these pain points and discover previously-held bad working habits or misconceptions and grow one's understanding of the job (which is expressed by better standards)?
- How to support each person's progress and help them to overcome the obstacles they face to fulfill the potential of their abilities, while supporting teams in running and improving their own workplace and growing mutual trust between management and employees?
These key questions are not so much grand principles as they are concrete ways to make the next step forward in improving the existing situation with the people themselves (as opposed to fixing the problem on paper and telling them to execute the plan). Granted, they are based on our assumptions on how a business should be run – something that, over the past couple of years, we have discussed long and hard and tried to frame in terms of a "manifesto," to follow the example of the Agile movement.
There is no Lean Manifesto, as we said, but if one existed we believe it would look like this:
We are uncovering better ways of delighting customers by doing it and helping others do it. Through this work we have come to value:
- Customers are friends to be helped over being sources of revenue
- Performance comes from dynamic improvements over process optimizations
- Innovation is the result of the development of people's capabilities over defined top-down vision and disciplined execution
- A learning system to encourage talent, ingenuity and passion over a management system that drives compliance and exploitation
- Developing more leaders over getting more followers
That is, while there is value in the items on the right, we value the items on the left more.
We follow these principles:
1. Go to the workplace (we call it Gemba) to see facts and get agreement on what the problems is
2. Put customers first and strive to help them solve their problems in their terms
3. Safeguard employees, both physically and morally
4. Accelerate flows to reduce lead-time by improving cooperation through just-in-time
5. Reduce rework by deepening technical skills and refusing non-quality (we call it Jidoka)
6. Level the work plan to avoid unevennes, overburden and waste
7. Develop everyone's autonomy to solve problems by teaching standards and encouraging deep thinking
8. Develop team's confidence and ownership of their work methods through continuous improvement (kaizen)
9. Encourage mutual trust between employees and management through basic stability of teams and workloads
10. Challenge teams to better visualize work to reveal problems
11. No process is ever perfect, and continuous improvement (kaizen) is always possible by putting forward new ideas and working to the best of our abilities
12. Respect all points of view: success is born of individual effort and good teamwork
We've phrased these 12 core values and practices following years of research for the upcoming book, The Lean Strategy, one of us (Michael) has written with Dan Jones, co-founder of the lean movement, Orry Fiume, father of the lean accounting movement, and Jacques Chaize, a founding member of the French chapter of the Society for Organizational Learning. We doubt any lean thinker would disagree with any of these.
But is this enough to thoroughly describe the intrinsic aspects of lean thinking?
Here's the rub. While these ideas can certainly serve as a rallying flag for like-minded people, they seem to fail to address one of the deeper ideas underlying lean: learning by doing. There is nothing wrong with these values, but in learning terms they often "overfit": there are probably many non-lean ways of adhering to them (perhaps less so for the core practices). Contrarily to the five questions we asked earlier in this article, having broad, general values doesn't point towards the very specific next step we need to figure out, which will take us out of your comfort zone and pave the way for learning something we either didn't know or expected beforehand. It doesn't help us to learn something new.
Lean is more than just another management method. It's a method to learn to learn. This means learning what you need to learn in a mysterious, fog-filled, changing environment, as opposed to "learning" more about what you already know. Lean's hands-on, learning-by-doing approach remains profoundly challenging, no matter your degree of experience or expertise. There's always a next step to discover what lies ahead, and lean is a method to take this next step in the general direction of your goals. It holds both learning strategies and tools to change step by step and uncover the learning path.
Don't take us wrong: we absolutely believe in the core values and principles highlighted here. But we also believe that these are not enough to grasp the very unique and concrete nature of lean thinking, which starts with solving practical problems, here and now, with the people doing the work, and then thinking one's way through the implications of what this means. Yes, values and principles help us to orient ourselves and see which way improvements should go, but what matters every day is the next step and the thinking behind taking this next step.
This brings us back to the most infuriating answer you can get from a lean sensei in any given situation: "It depends. What is the problem you're trying to solve?". The truth is, no Lean Manifesto can answer all of our questions... we will just have to learn by doing.
THE AUTHORS
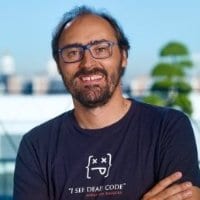
Dimitri Baeli is the new CTO at LesFurets.com after 4 years of continuous improvement within the software development team where he contributed to getting the delivery and business teams more agile, using Kanban, Agile and Lean principles. Prior to this, Dimitri was Quality Manager at eXo Platform and software architect at Prima Solutions (Insurance Software Vendor).
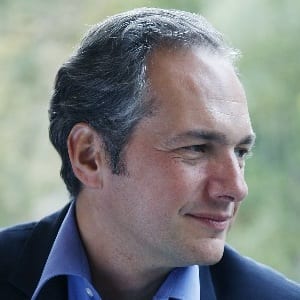
Michael Ballé is co-founder of the Institut Lean France. An associate researcher at Telecom ParisTech, he holds a doctorate from the Sorbonne in Social Sciences and Knowledge Sciences. Michael is a best-selling author and an engaging speaker, and managing partner of ESG Consultants. He also works as a lean executive coach in various fields, from manufacturing to engineering, services to healthcare.
Read more
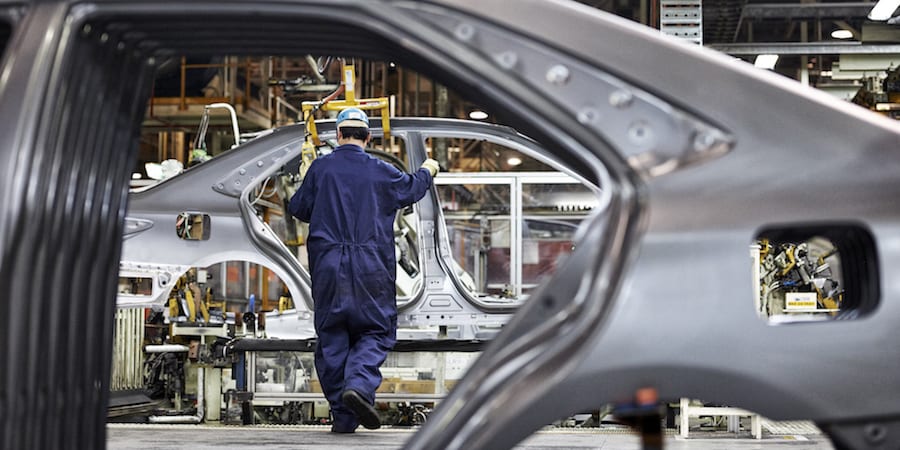
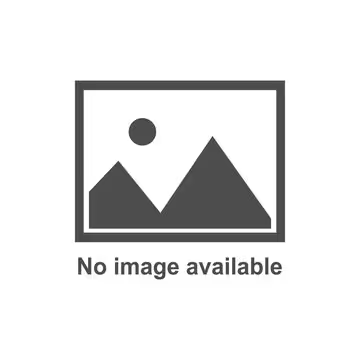
WOMACK'S YOKOTEN – On October 3, Toyota will cease its manufacturing operations in Australia, but the way it is managing the transition - in the leanest way possible - holds great lessons for us all.
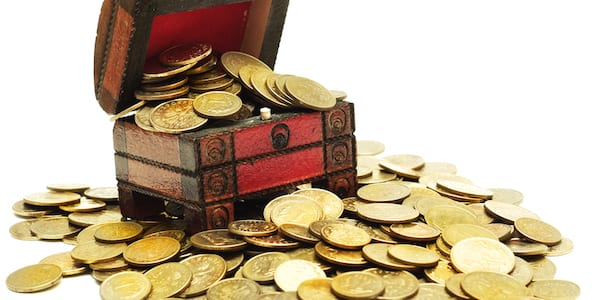
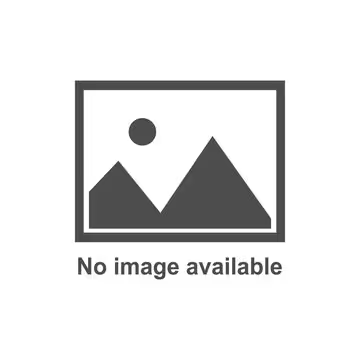
WOMACK’S YOKOTEN - When managed poorly and tied to the wrong performance metrics, financial rewards can seriously damage your organization, Jim Womack warns in his latest column.
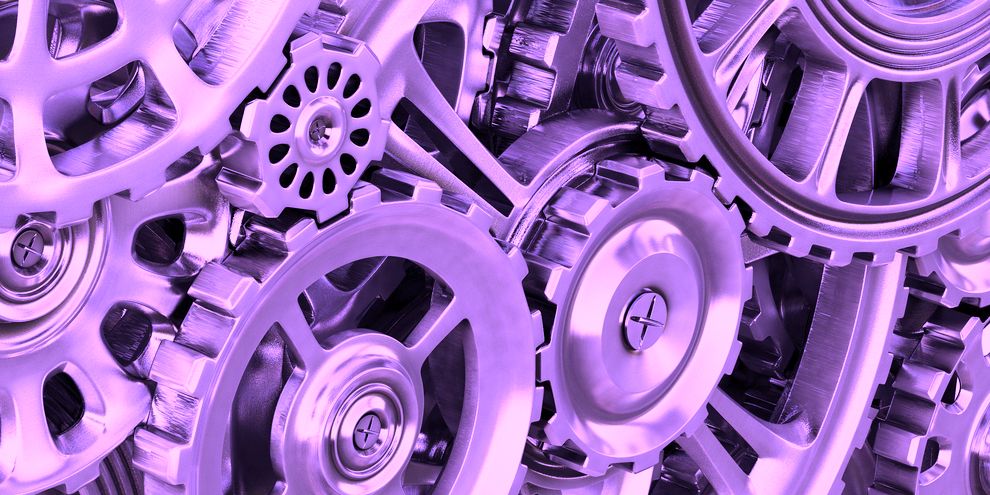
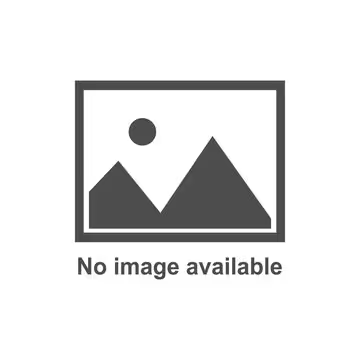
FEATURE – Before you decide which method to use to establish pull, you must consider a number of factors. Here’s the things you should be paying attention to.
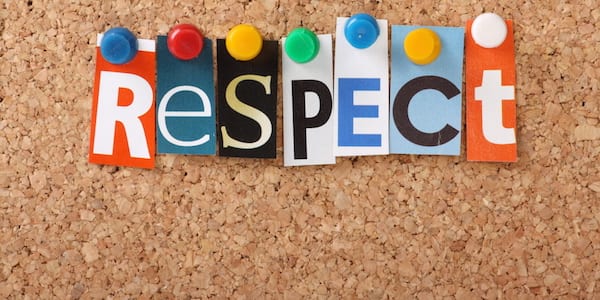
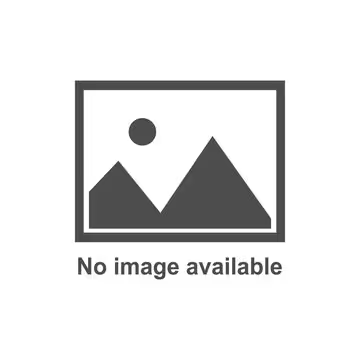
FEATURE - Mission creep, silos and a disengaged workforce are some of the negative effects of traditional management. Michael Ballé offers an alternative based on the respect for people principle of lean thinking.