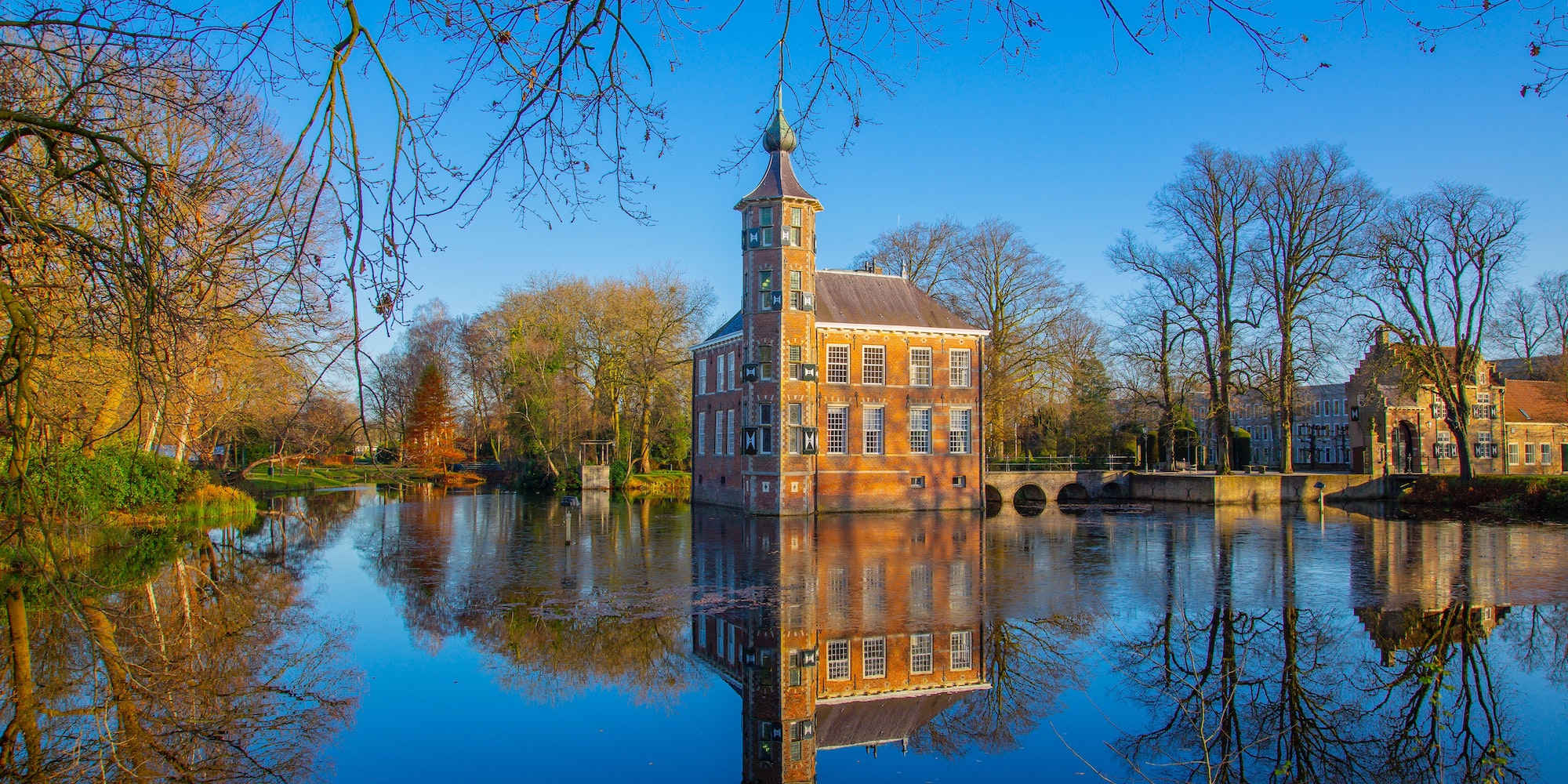
Lean, our “breda” and butter
BOOK EXCERPT – The city of Breda in the Netherlands has been on a lean journey for the past six years. Today we share an excerpt from the book The Lean Government, which sets the scene for the transformation.
Words: Erik Ottens
A snowstorm of confetti enveloped the people watching the parade. The tall floats moved one by one through the colorful and packed street. Music blared from the speakers. Arthur stood at the crossroads looking at the tall float with the big spinning heads. The wagon had to make a tight turn in the center of Kaaiendonk. He always enjoyed days like this: being together with fellow villagers, but also old friends who returned every year for the parade. Such fun and joy! The preparation, which lasted almost a year, was more than worth it. Inevitably, however, his thoughts turned to work. The introduction of the Environmental Law (General Provisions) Act had been on his mind for a few weeks. How was he going to manage this in his department? The impact of the new law was going to be huge and good preparation was essential. How should he approach this? Would that “lean” thing, which the external supervisor pointed out to him last week in the management meeting, mean anything? The sound of a trumpet player from the brass band brought him back to the here and now. The float had rounded the corner, with the next one already approaching. “Ha, the Kuivezand hamlet float,” he thought, his eyes shining with anticipation. “It is so clever how it always makes fun of local politics. I wonder what they have come up with this year.”
Thom parked his bicycle in the parking area under the municipal offices. He took the stairs and walked into the long garden. He greeted his team members and colleagues from other sections of Building and Housing Inspectorate, answering the odd question and joking around with people. Then he went to his office. He closed the door, and, for the next hour, he concentrated on his team’s improvement plan. He had working there as a section chief for almost a year already. He thought how his life in Rotterdam felt like a century ago. There was still a lot of work to be done with the team. He looked at the sheets with notes he had took during the meetings with employees. There were backlogs in enforcement, work to be done on the cooperation between team members, various files that had been worked on for years and were taking far too much time to process, new legislation that was coming – to name but a few of the problems. So, where should he start?
Pieter sat on the long wavy bench in the busy public hall of the City of Breda and looked around. A remarkable building, he thought. From the outside it looked sturdy and solid, while from the inside the covered square space looked light and open. He saw civil servants walking back and forth across the three glass bridges that spanned the public hall on each floor. He wondered whether the building was already there when he was born, and whether his father got his birth registration there. It felt lucky with his job, in that it gave him the opportunity to advise the city in which he spent his youth. With his lean gaze, he looked at the crowd. It was clearly a peak time, with lots of customers coming in. Would opening an extra counter help prevent waiting times from increasing?
Arthur explained the challenge to Pieter. In just over 18 months, the Wabo would come into force. The new law aimed to make it easier for residents and entrepreneurs to apply for permits. As a result, the building permit and 24 other regulations concerning physical living environments would be replaced by one integrated environmental permit. That way, the processing time for the permits would be reduced from twelve to eight weeks. The busy work floor seemed to indicate that more people were needed to meet the new statutory deadline. The permit providers already had said that twelve weeks was far too little. The construction industry was in full swing at the time, and applications kept flooding in. With a great deal of skill and effort, the team was able to prevent permits from having to be automatically granted [because the deadline for approval had passed]. Still, they could hardly handle the number of applications. How could they shorten the processing time? Pieter listened carefully and told Arthur about an improvement project he had carried out at a large telephone company. One day, the call center was expected to start handling more calls with a higher quality of service at lower costs. This was a similar problem. Pieter suggested Arthur take the reduction of the turnaround time as a starting point: “Aside from the practical fact that the new term is enshrined in law, there are a number of deeper reasons for doing this. Shorter turnaround times ensure that customers are helped more quickly. This increases their satisfaction. Shorter processing times also increase productivity, because you have fewer requests to deal with, for example, and you, therefore, need to search less. Quality problems also become visible more quickly and can be tackled straight away. In short, a lower turnaround time would act as a lever to remove a lot of waste from the process. Pieter indicated that he would like to work with a project team that includes the various advisors from the process. He would also like a right-hand man. Preferably someone from the MT of Building and Housing Inspectorate who could think in process terms. Arthur thought for a moment and walked to the office next to him. “Thom, a word. I want to introduce you to someone who is in need of a partner-in-crime,” he said with a big smile.
In the evening in the car driving home, Arthur thought back to the conversation with Pieter. He began to have doubts. Would it really be possible to meet the new deadline using this approach? The staff say so clearly that it's not possible and that extra people are needed. That they were very busy with requests was evident: whenever he walked across the office garden, he saw overflowing desks and sometimes staff assessing building plans on the ground. “On the other hand,” he tried to reassure himself, “we have learned that this lean doesn't work. Besides, we still have a year and a half until the new law comes into effect. There’s plenty of time. And, knowing government, I wouldn't be surprised if the introduction of the Act were postponed at the last minute.”
In the warm meeting room, a large brown sheet hung on the wall. The bright sunlight shone on the paper coming through the window. One by one, the project team members came trickling in. As usual, the meeting started a few minutes later than planned. “Brabant's customary 15-minute delay, for sure,” Pieter joked. [While the Dutch are known for their punctuality, people from the Brabant province, where Breda is located, are said to be always late.] Once the advisors were in, Thom kicked off: “The aim of today’s meeting is to accurately visualize the current building permit process by creating a Value Stream Map.” Immediately, Pieter saw question marks on the team members’ faces and said: “With a Value Stream Map, you provide detailed insights into how the process actually works. For each activity or step, you show what the processing time is and whether the step adds value for the customer. You also indicate waiting times, throughput times, and stocks. With this information, you can shed a light on waste in the process. This, in turn, gives you the possible causes of the long lead-time we are experiencing.”
Someone remarked that there was already a process description: “My colleague worked on it last year. We're not going to do things twice, are we? I'm way too busy for that.” Pieter laughed and indicated that there were major differences between a process description on a handbook and a Value Stream Map. “A VSM aims to show the actual situation, how we are really doing. A process description often indicates how we think things are done in practice. Besides, a Value Stream Map contains a lot of detailed information. Let’s just get to work. I am sure you will notice the difference soon.”
Pieter picked up a block of yellow post-it notes, a block of pink ones, and a pen. He walked to the brown paper that Thom and he had hung on the wall before the meeting started. Standing by the sheet, he asked: “A property developer or a resident applies for a building permit. Where does this application come in and what is the first step in the process?” Over the following hour, Pieter led the group through the process of mapping the value stream in a structured manner. He wrote activities on the yellow post-it notes and the functions of the people carrying out those activity on pink ones. Step by step, the brown paper was full of yellow and pink. Pieter did not allow himself to be distracted by the many side issues and substantive discussions that were put on the table by the team members. He kept a close eye on the process line and the moments of choice. By the end of the first part of the session, the process had been accurately mapped out. “Time for a cup of coffee, I think,” Pieter said. “After the break, we will look at which activities add value for the citizen and which do not.”
Erik's book De Lean Overheid, currently available only in Dutch, is available here.
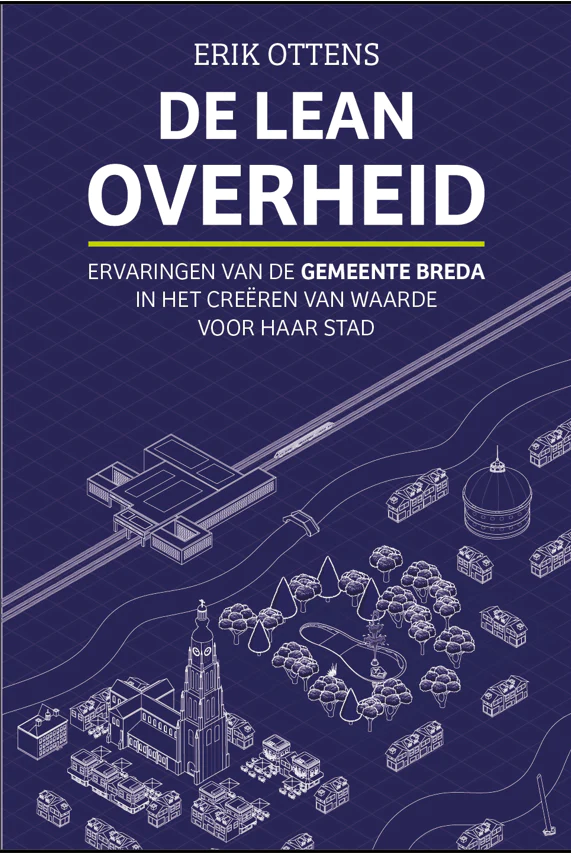
THE AUTHOR
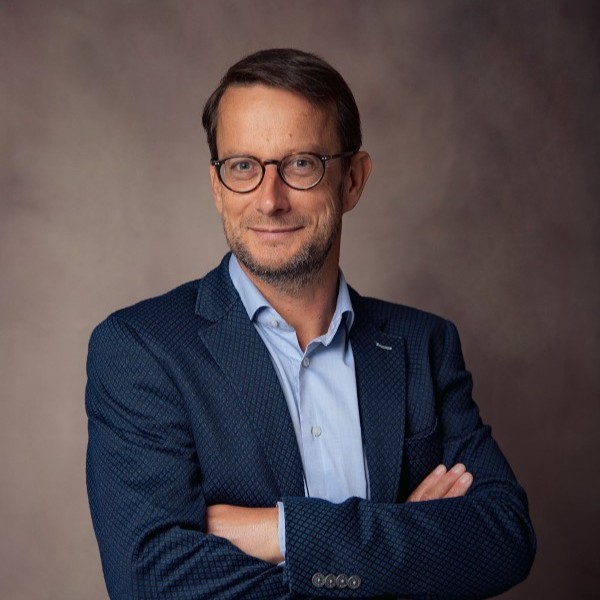
Read more
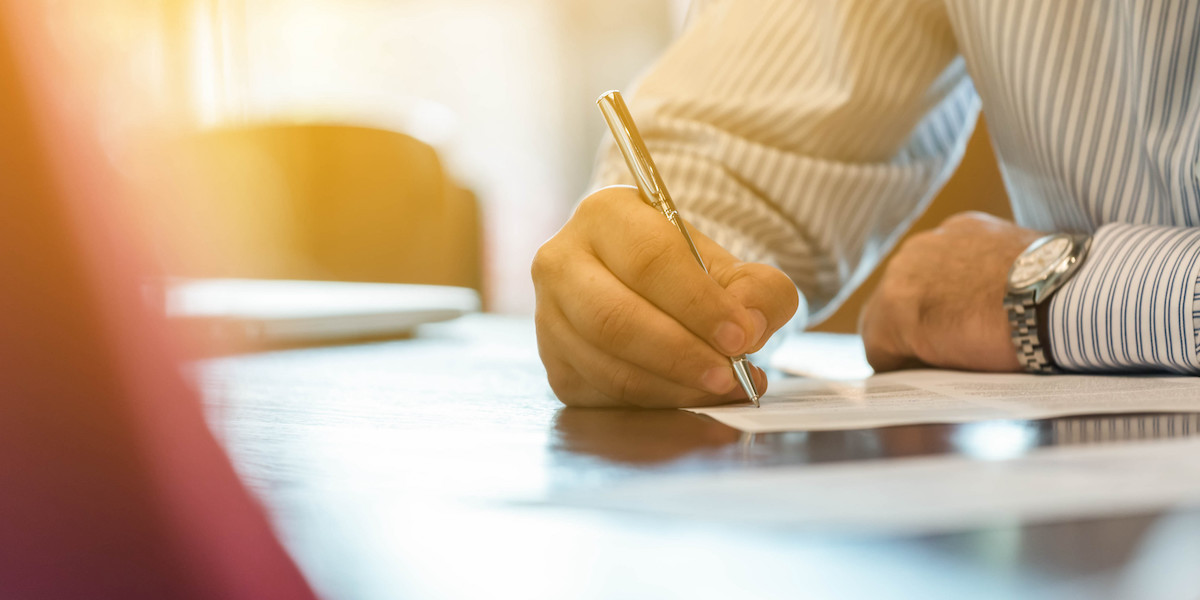
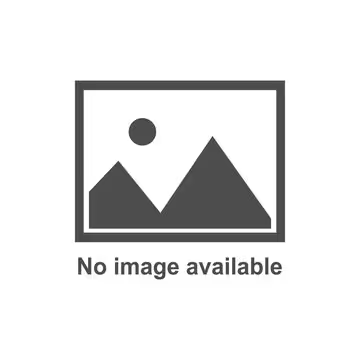
CASE STUDY – TechnipFMC has introduced the Concept Paper in its lean product development process. This article shares some of the learnings resulting from the experience.
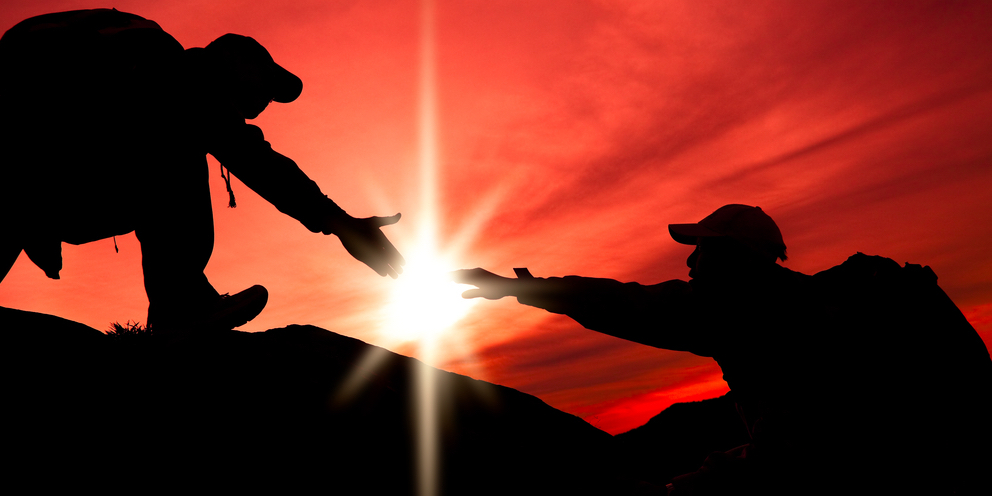
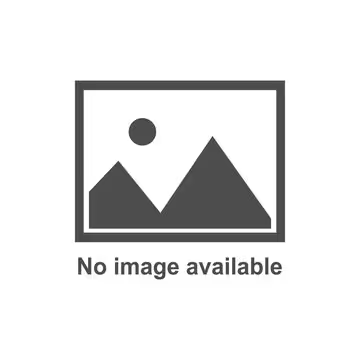
FEATURE – Introducing his book, the author tells us what his Toyota mentors taught him with their contrasting, but ultimately complimentary approaches to problem finding.
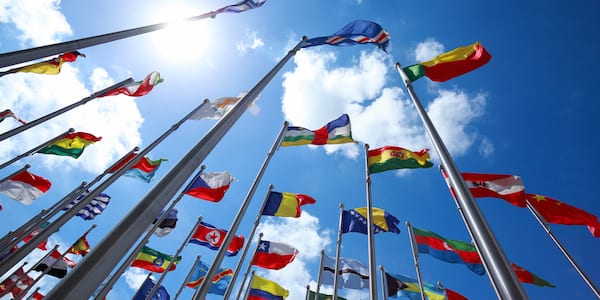
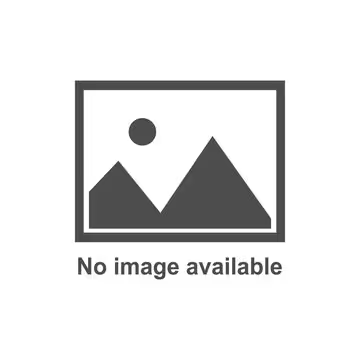
ARTICLE - Are some national cultures better suited to implement lean thinking? This article, based on research on 45 Volvo factories, reflects on the role of local cultures in the rollout of a corporate lean program.
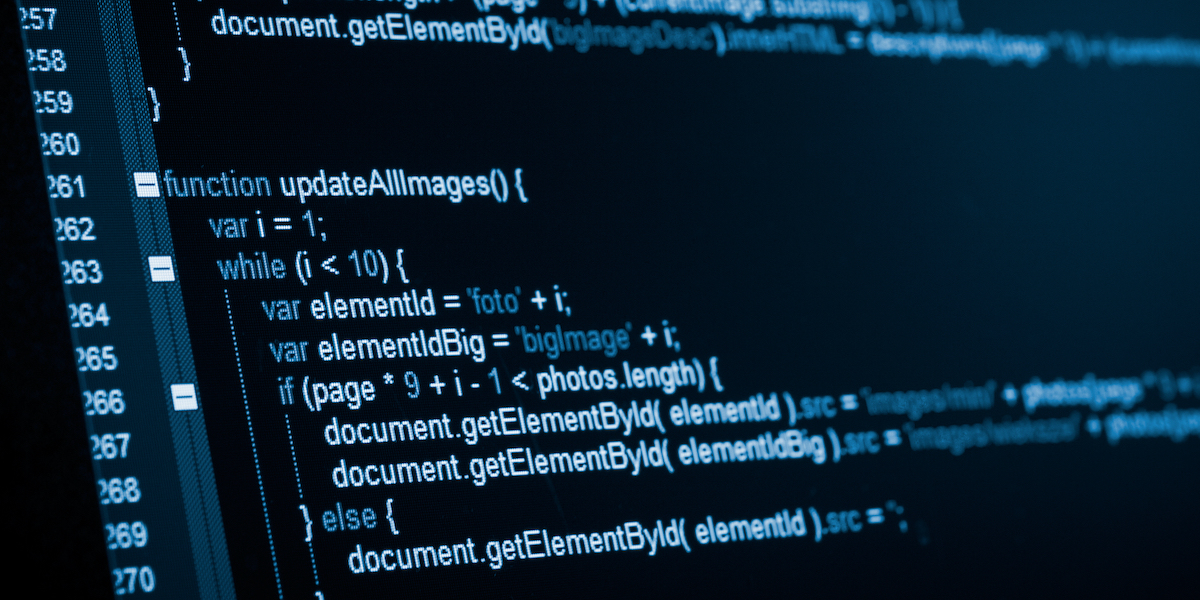
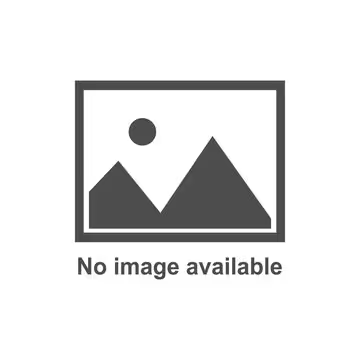
FEATURE – How can digital companies develop a competitive edge in the "tech first" future? By using Lean Thinking to ensure continuous learning and transform the way coders think and work.