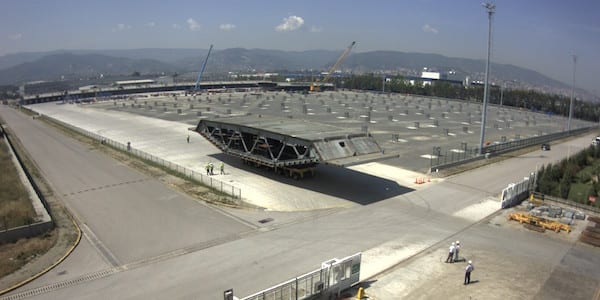
Cimtas Module & Shipyard: lean principles in construction
CASE STUDY - A Turkish shipyard and engineering company has found that lean principles and practice are the only way to deliver unique, large construction projects efficiently and successfully.
Words: Cem Akil, Planning Chief, Çimtas Module & Shipyard; Ekrem Sarikaya, Quality Assurance Lead, Çimtas Module & Shipyard; Nezih Soydan, Vice President, Lean Institute Turkey
Three years into its lean journey, Çimtas Module & Shipyard is reaping the benefits of a new approach to managing and doing business. Our organization is currently responsible for the ground assembly of the girder blocks (pictured) of the Izmit Bay Bridge, which - once completed - will be the fourth largest suspension bridge in the world, located some 50 kilometers southeast of Istanbul.
However, at the moment our biggest accomplishment seems to be the belief, shared by people across the organization, that it would not be possible to complete such a large project without the help of lean thinking.
But things haven’t always been good.
In 2011, the year we decided to undertake a full lean transformation, Çimtas was facing the fierce competition any business operating in the construction sector will know. At the same time, the need to guarantee better working conditions (by visualizing and eliminating problems in our processes) and to align every member of our team to a common goal became more stringent.
There’s more. Operating in the steel and shipbuilding industry means that the only way to survive is for us to react very fast to bids in order to win contracts. A request for quote (RFQ) is not enough in itself: after we get one, we still have to thoroughly analyze the situation, define the value the customer expects, and act on the related value stream.
However, the biggest problem Çimtas faced was perhaps the fact that very few of the new projects we get are actually similar to the ones we have previously completed, in terms of design, customer expectations and manufacturing processes. This means we need to be very responsive to whatever specs we are requested to follow. Each project has a different value stream and requires a different approach, so all of our resources, tools, machines, manpower and most importantly knowledge need to be aligned very quickly.
This is why we decided to call our lean program “High Speed Lean”: we wanted to ensure that each new project, no matter how different from anything else we had worked on in the past, sees good results in an effective and timely manner.
So we set out on a journey, with the added challenge of not having many examples of lean implementations in our industry to get inspiration from.
What we did have was some previous experience with lean thinking, which had been in use in other parts of the group since 2009. We tried to build on that knowledge initiating lean activities at the very beginning of every new project, so to give the lean culture a better chance of becoming a permanent feature of our corporate identity.
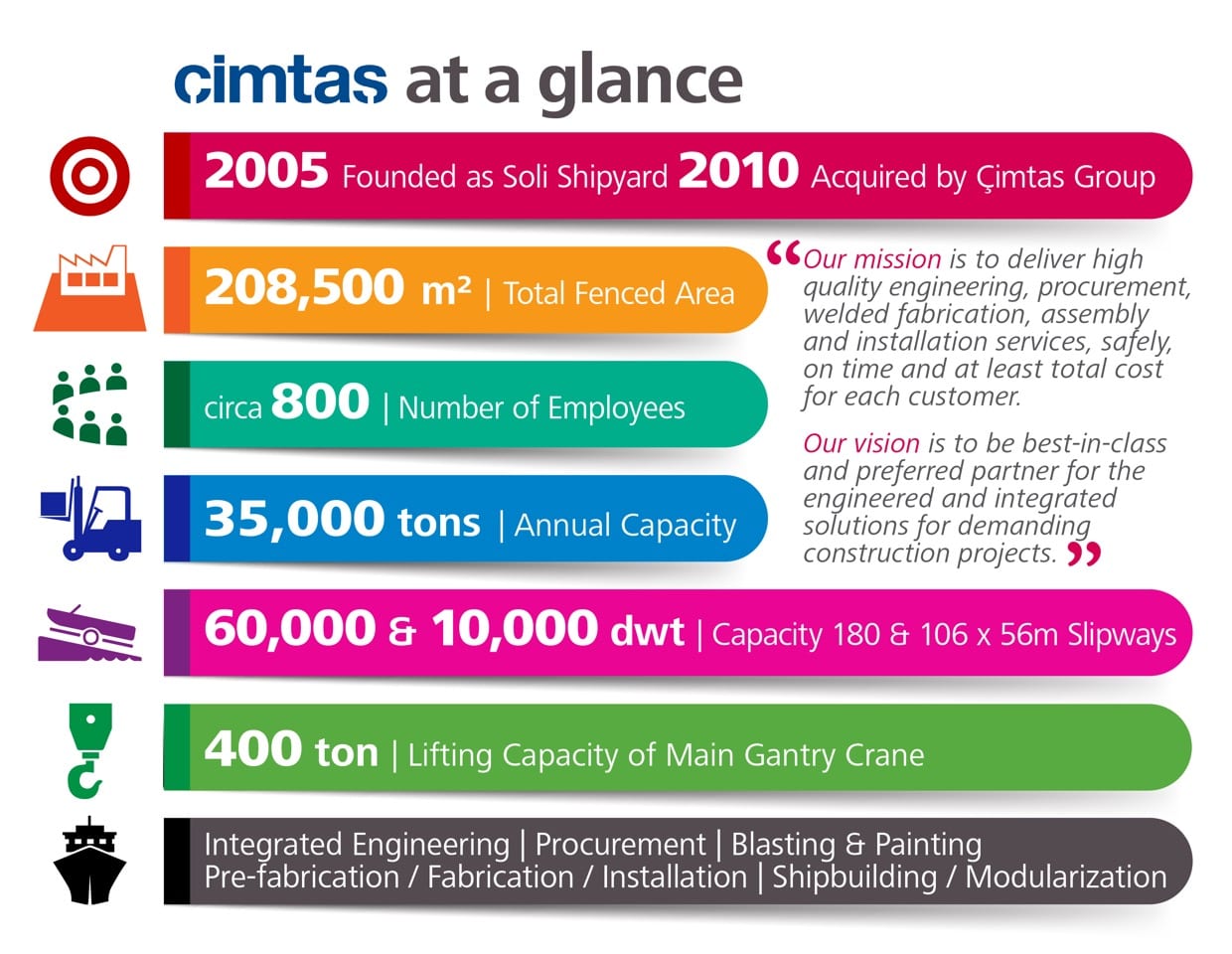
SEEING THE BIG PICTURE
While value stream mapping is by far the tool we are using the most in our projects now (with the guidance and assistance of Lean Institute Turkey), we were forced to re-adapt it to our circumstances: because we work with projects of limited duration, finding problems that might create bottlenecks after a project launches can already be too late for us. Instead, it is crucial that we investigate the problems that may arise in advance, before SOP.
Here is what our slightly altered approach to VSM looks like:
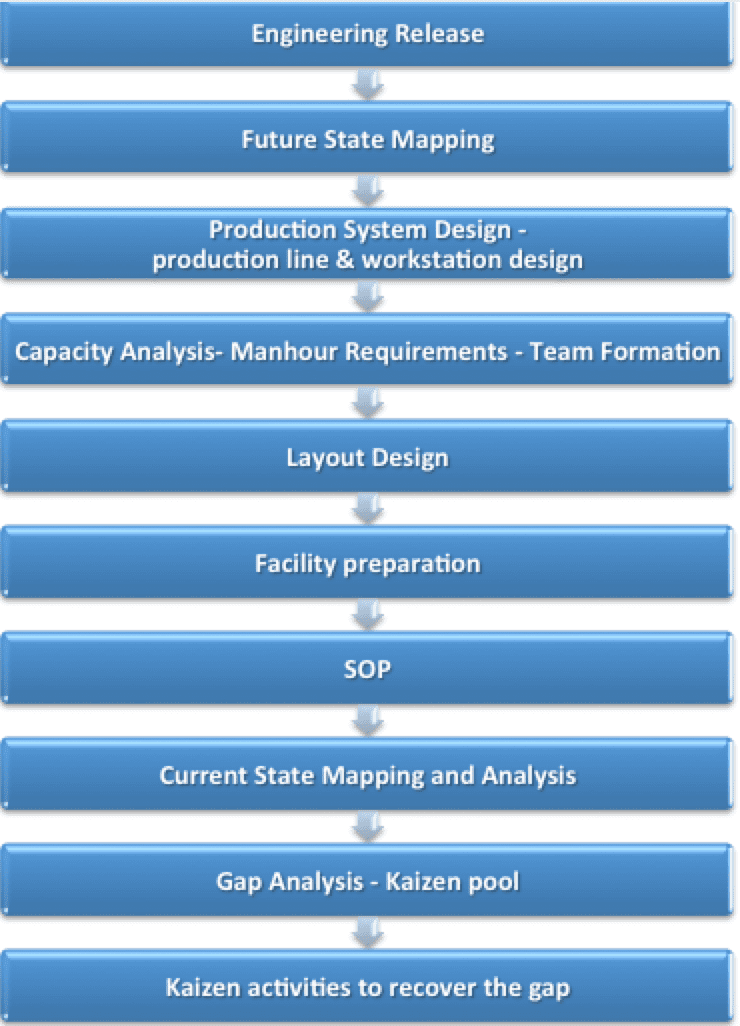
At the beginning of each project, all the leaders involved share their ideas and experience. They then define KPIs during a meeting and combine the data in a Future State Map. Based on this map, production lines and zones are determined, a layout is prepared, takt time is calculated, and daily and monthly targets and the required manpower are estimated.
As the project progresses, we periodically go through the map, revising it and trying to improve it according to the status of the “andons” on the production lines. The improvement opportunities resulting from these reviews feed into our kaizen pool and turn into kaizen projects.
One of the major improvements we were able to achieve from such a kaizen project was related to the supply of steel for the Erbil Combined Cycle Power Project (Iraqi Kurdistan’s largest power plant) in 2013.
At the beginning of the project, during the VSM analysis, we saw that our KPI for painting the fabricated pieces was 400sqm/48 hours. However, in order to complete the project on time we should have achieved 800sqm/24 hours. Essentially, we needed to increase of our painting capability four times.
We put together a kobetsu kaizen group, drew a future state map and decided on the targets that we needed to focus on. We created a PDCA list of actions and started to work on every item on the list with enthusiasm. Three months later, we had achieved an average of 860sqm/24 hours in our painting works. We then continued to monitor and improve our performance until the end of the project.
There’s another, more recent, example of improvement in our project for the Izmit Bridge. Our current state analysis showed that it took between 20 and 25 days for us to form blocks in our shop, which was causing us to deviate from the project schedule. We began to examine the processes in full scale with a big VSM project group.
After a number of meetings and different analyzes of the situation, several before/after kaizen opportunities were identified and the related changes quickly applied in both operational and support processes. A few kaizen groups were formed and started to work on the improvement simultaneously: after a month, we had managed to bring the figure down to 14 days, and we are now looking for new ways to improve even further.
BUILDING QUALITY AT THE SOURCE
As mentioned before, at Çimtas every new project means a new challenge, as the process of gearing up our operations to respond to customer expectations resumes. Many activities are unique events and need standardizing by means of visual management before even seeing the actual work. That is why standard operations need to be defined and improved before production begins. For that to be possible, the entire team must get involved in working to achieve the best possible outcome at the ramp-up phase.
In repetitive manufacturing environments, standard operations are usually designed based on certain product types or families that are produced in high volumes. But in our sector, the product is unique, has its own characteristics, and most of the times it is produced only once.
Therefore, standardization based on product is not viable or effective. So in our lean transformation, we decided that built-in quality and standardization should not be based on the product, but on “generic products,” which allows us to apply a standard to many different products by revising the original TWI documents according to our needs.
Typically, this approach allows us to train and adapt newly hired people easily for the different operation needs of a new project.
Generic standard operations do not include information on the cycle time, which left us with another huge problem to solve: how to stabilize the cycle times. The answer, however, was simple: 5S.
A COUPLE MORE Ss
As many others before it, the lean transformation of Çimtas Module & Shipyard started with 5S.
In the last quarter of 2011, 5S workouts were launched in pilot areas with “high speed,” as the name of our lean program suggests. At the beginning we had a lot of team members who even called it “S5” instead of 5S. Questions abounded, ranging from “What are we doing?” to “Why are we doing this?” As time went by, however, doubts on 5S started to dissipate and questions like “Why weren’t we doing this before?” or “Why didn’t we start 5S before?” started to come up in conversations.
Today, 100% of the company’s space is organized using 5S. In the early workouts we had arranged, 62 staff and 89 craft team members were involved. Over the past four years, members of these 5S teams have made over 50 presentations of their workouts.
At the end of 2013, a 5S committee was formed and started to plan and monitor 5S activities. Members of this committee carried out over 1,500 audits in the areas within the scope of 5S in order to improve the level of adoption and sustainability of the method in those areas.
As we learned about 5S and made progress, we realized there are actually two more Ss that are very important to us: Safety and Standard Operation. We added them to our scope of action and called our activities 5S+2S: all audits and workouts started to include safety walks and standard operation checks.
For the Izmit Bridge project, we are now producing over 100 girders that are 35 meters in length and 25 meters in width. While the total production time will be around 18 months, it will only take a month and a half to put in place and assemble the bridge. This means that we need to product the girders in advance and store them in a very large warehouse – they will wait there until project completion.
As you can imagine, the girders are so big that moving them from one location to another within the plant is a difficult and costly exercise. To minimize transportation, we therefore plan all logistics movements and follow that schedule to the letter, which would not be possible without 5S: every girder block is given a specified location for a certain period of time and is then moved to another location for further operations, allowing for a new product to take its place. One tiny mistake and all the synchronization effort is lost.
Teams are aware that without 5S our very large facility (208.500 square meters) would not be enough for this project.
ENCOURAGING CREATIVITY
The main purpose of employee suggestions is to create a system whereby every Çimtas Module & Shipyard employee can freely share their ideas for improvement, either about their own work or about other departments and processes. In order to make this practice sustainable and a part of our corporate identity, we request that every employee gets involved with at least one suggestion per month.
All suggestions that are given to other departments must be reviewed and answered within 30 days. The reviewer has to provide the suggestion’s owner with feedback in case the suggestion is considered not viable. This is one of the most critical elements to encourage employees to believe in the continuous improvement culture we are establishing and to contribute to the system.
Every adopted suggestion is considered as a Before/After Kaizen. It is reviewed and rewarded based on the area it concerns (5S, efficiency, etc). Additionally, all team leaders review and vote on their teammates’ kaizens in monthly meetings. After the vote, the first six kaizens are rewarded separately and shared with the rest of the organization during the Lean Sharing Meetings that we hold every two months.
Our employee suggestions system has allowed for a more creative environment, as proved by the increased number of kaizens we complete every year: it was 417 in 2012, 2,203 in 2013, and already 2,345 in the first nine months of 2014. As this numbers grows, our work becomes more meaningful, much easier, and less tiresome.
LEADING LEAN
As all of these lean activities became part of our daily work, the need arose for someone to coordinate the lean transformation of Çimtas Module & Shipyard. The Lean Committee was formed in 2013, consisting of our top management and lean facilitators.
The committee leads the lean transformation focusing on the following questions:
- What is the value created through the use of all the lean tools we have applied?
- How can we improve these lean tools and better adapt them to Çimtas Module & Shipyard’s lean culture, in a bid to create Çimtas Module & Shipyard’s Lean Way?
- How can we develop lean facilitators, so that individuals at all levels of organization can successfully lead lean activities?
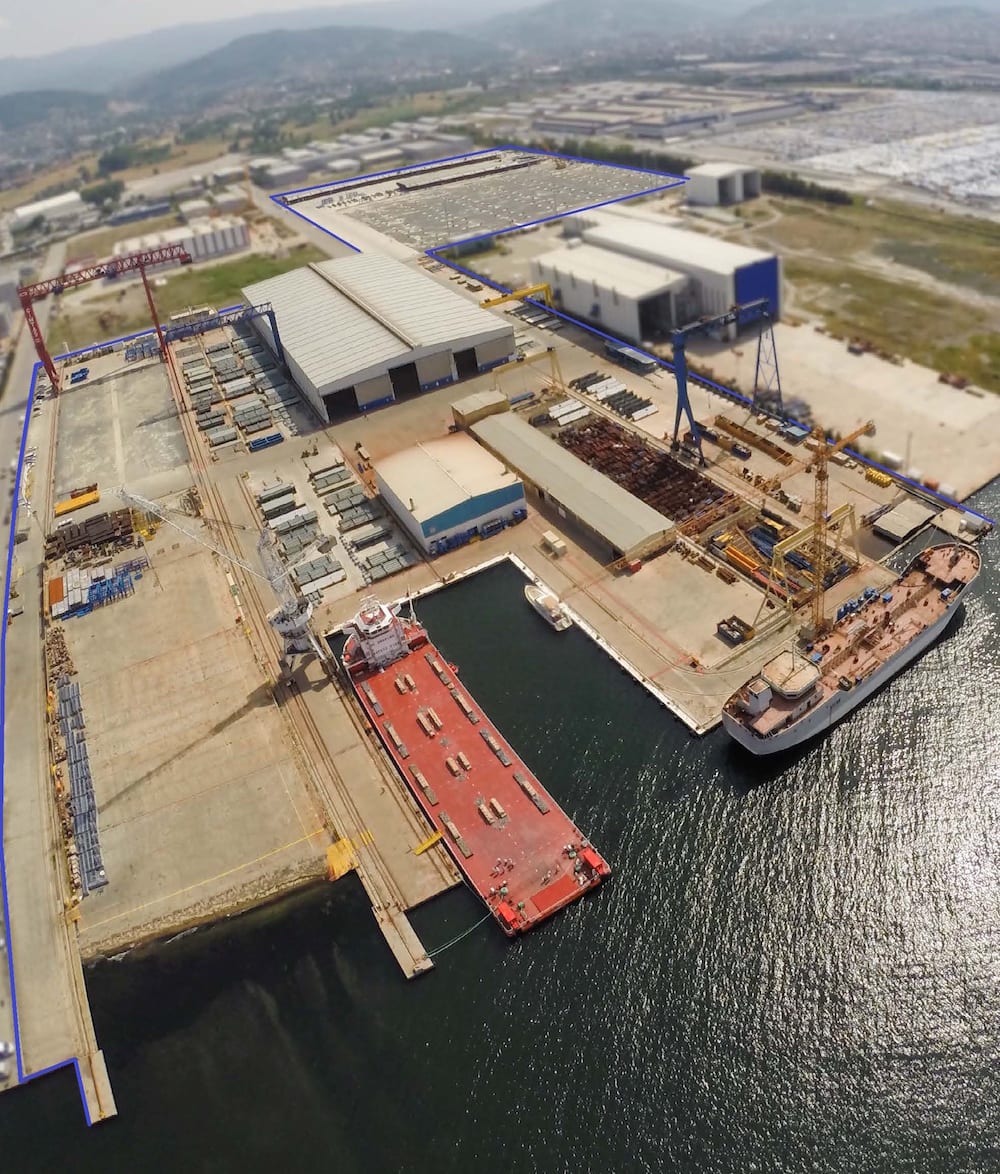
The committee is also in charge of detecting and trying to solve bottlenecks, to provide the team with all the support they need.
Another important responsibility of the committee is to lead the Lean Sharing Meetings to spread the word on the company’s lean activities and to transfer the philosophy from top management to the shop floor.
These meetings are held every two months with the participation of 100 employees (both white and blue collar) and last three hours. The total number of employees is around 450 (depending on the project), which means that the participation rate for each meetings is more than 20%.
These gathering are made o two sections and always start with a HSE presentation, which is the number one priority for Çimtas Module & Shipyard at all times. They then see the presentation of the results of the lean activities and, in the second section, more information shared on 5S+2S and kaizen projects completed in the last two months.
The presentations aim to bring attendees (and indirectly all employees) up to speed with the value that has most recently been created and with what lean efforts have achieved in the last two months. They also focus on the areas that still offer opportunities for improvement.
When the meetings are over, blue-collar workers who have completed the best kaizen are awarded, to try and ensure that the team’s morale and focus are at their highest for the months to come.
A NEVER-ENDING JOURNEY
We believe that the success of our lean journey goes beyond numbers and percentages. At Çimtas Module & Shipyard, we have a unique perspective of lean, which allows us to see the extraordinary impact that today’s decisions on how to customize lean practices can have on our future as a business. That is why we focus on a culture of “High Speed Lean” here.
Four years into our lean journey, we at Çimtas Module & Shipyard can say we managed to break through and to adapt lean to our corporate identity. At the same time, we know that our lean transformation will never stop unfolding. After all, kaizen is a never-ending activity.
THE AUTHORS
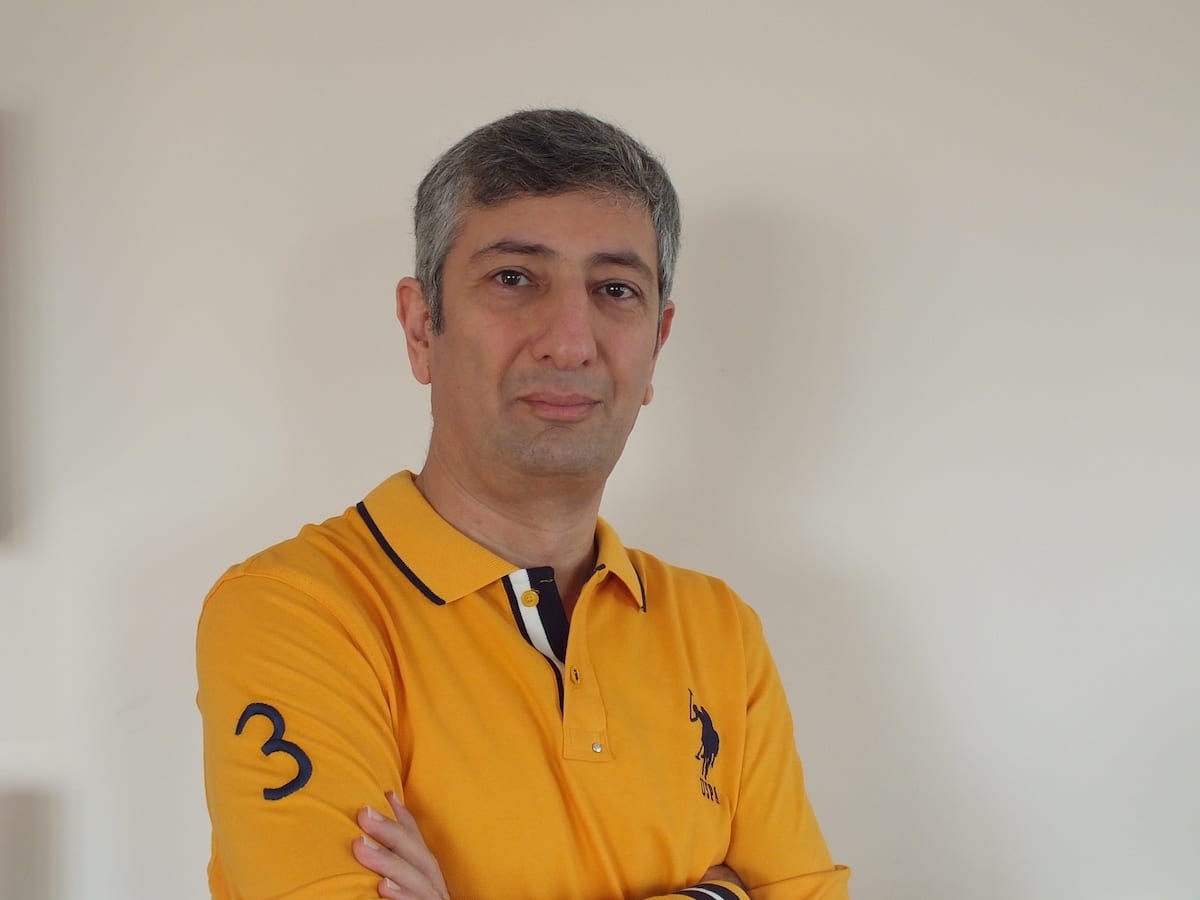
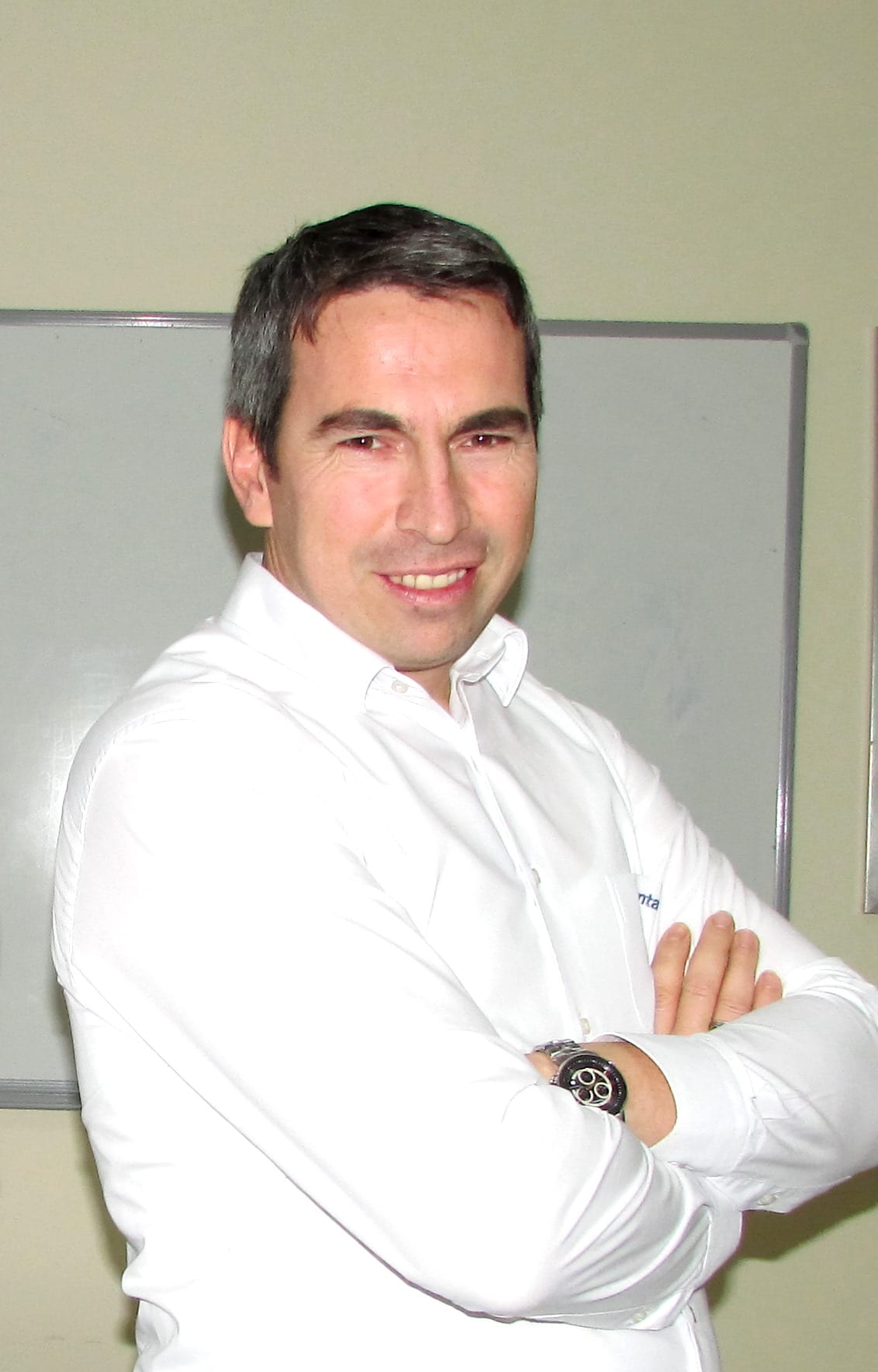
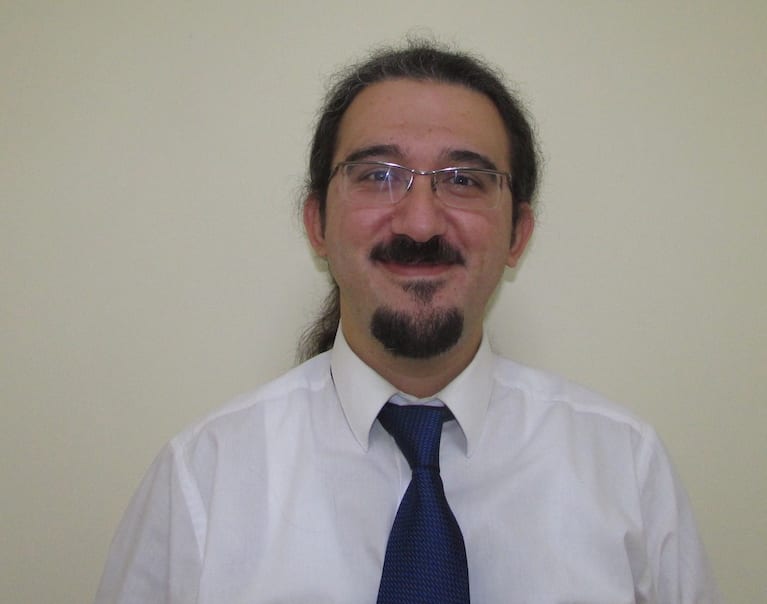
Read more
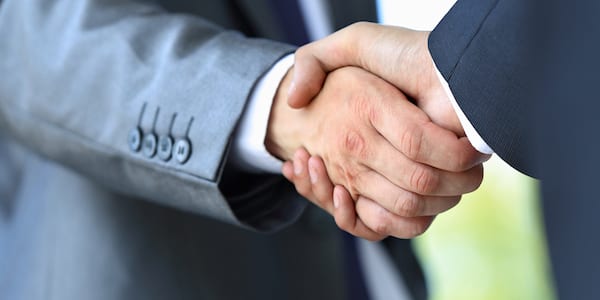
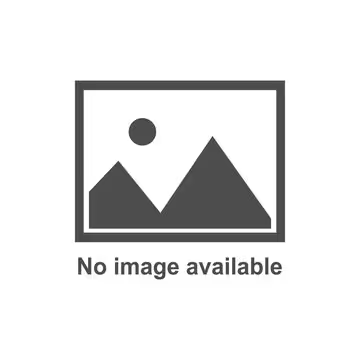
NEWS - LEI partners with the Institute for Intrapreneurship to help established and startup companies to become more innovative using lean thinking and practices.

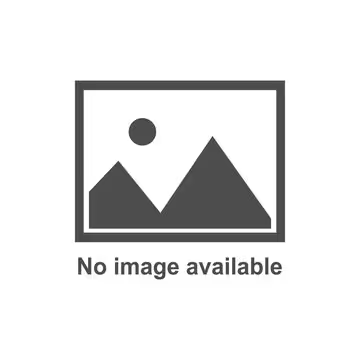
WOMACK'S YOKOTEN – As the Lean Enterprise Institute turns 20, its founder provides us with a bit of hansei on where we are and where we are going next as a community, and on what challenges we might tackle.
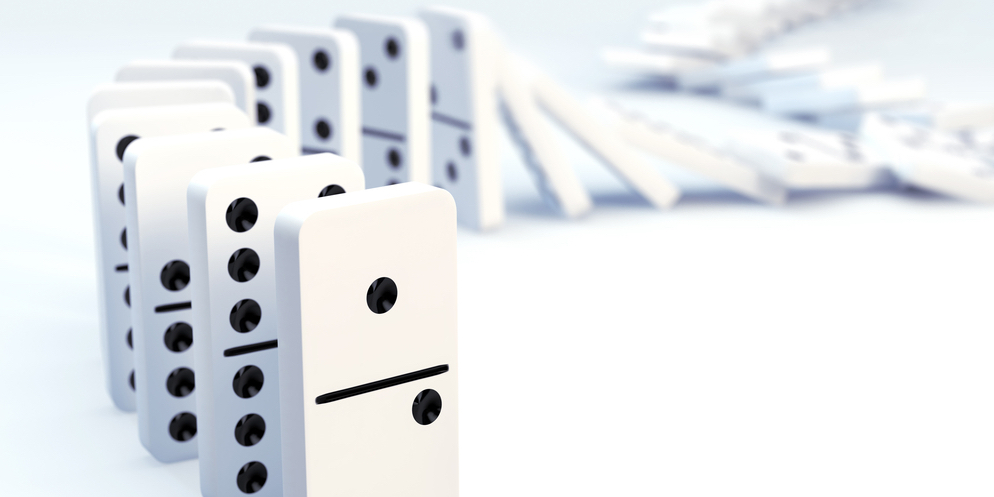
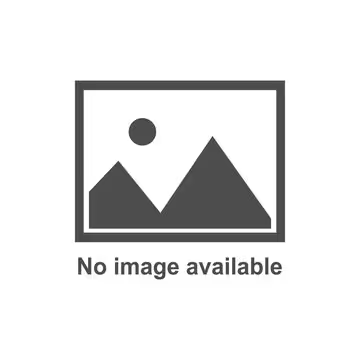
FEATURE – What are the main problems people encounter when running a project? The author ran a survey with 126 people over two years and presents the results of his research in this article.
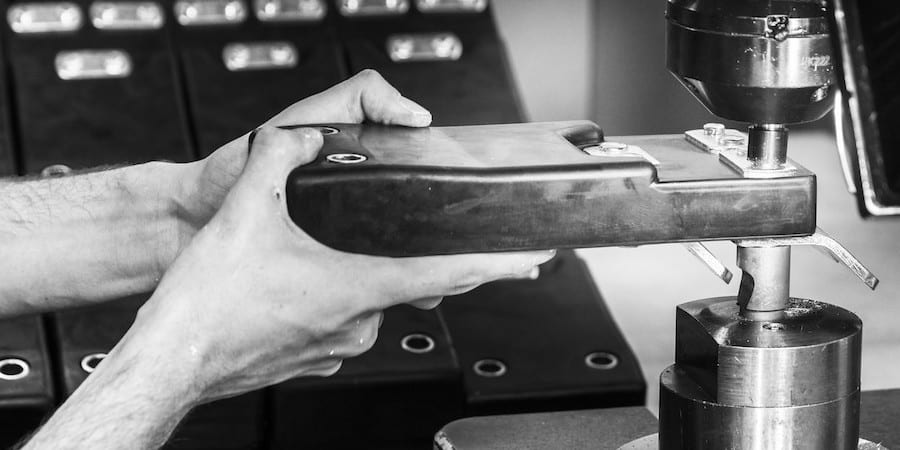
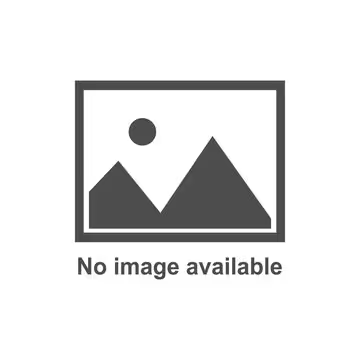
FEATURE – At Nijhuis Mitech, management is so involved that the owner can often be seen at the gemba running experiments with people. The transformation that ensued is helping the firm become more efficient and stay competitive.