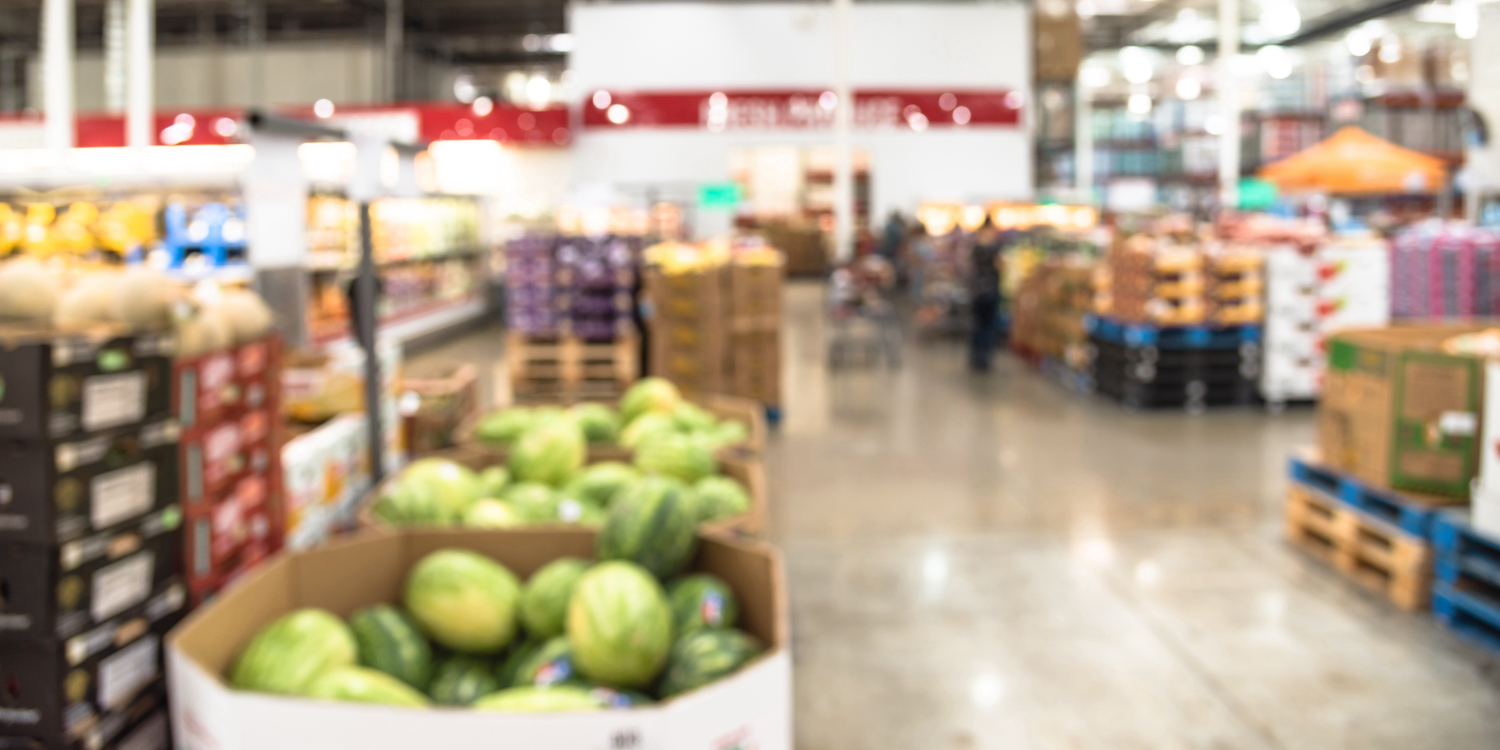
Just-in-Time and the Covid pandemic
FEATURE – The pandemic has brought back into the spotlight the common misconception that Just-in-Time causes disruption when spikes in demand occur. Torbjørn Netland debunks the myth.
Words: Torbjørn Netland, Professor of Production and Operations Management, ETH Zurich.
A year ago, the vast majority of the world population was still blissfully unaware of the enormity of the healthcare and economic disaster that was about to unfold. It wouldn’t be long before the Covid-19 pandemic would disrupt our lives and bring the world to a standstill. Among the first victims of the Coronavirus were a number of critical supply chains, which started to report shortages shortly after the beginning of the outbreak.
While it’s true that Covid brought to the surface many of the shortcomings of our supply chains, it was disappointing to hear many people blame the Just-In-Time (JIT) principle of lean – and one of the pillars of the Toyota Production System – for the shortages. I believe this calls for a clarification.
Let me be clear: lean is not to blame; in fact, it is part of the solution. Saying that JIT is the reason for the numerous and very serious mistakes that were made, for example, in the supply of PPE is to mistakenly believe that this important principle advocates for zero stocks. The lean community is much to blame for the misconception: some influential early books on JIT were titled Zero Inventories (Hall, 1983) and Non-stock Production (Shingo, 1988), and many academics have equated lean with inventory reduction or inventory turns only. Consultants with a skin-deep understanding of lean are also often quick to look at inventory as pure waste, when some stock is in fact something customers are willing to pay for. Not to forget, when your demand implodes and suppliers struggle, some extra inventory is of little help anyway.
Lean Thinking calls for customer focus, short lead-times and a culture of continuous improvement. These are its key differentiators. And, as counterintuitive as it may seem, it is lowering inventory levels that will help you get there! This becomes apparent when studying TPS in depth or, indeed, when going beyond the titles and actually reading Robert Hall, Shigeo Shingo and many other lean thinkers.
LOWERING INVENTORY, AND NOT ELIMINATING IT
It’s not Just-In-Time that leads to shortages in supply chains. It’s the spread of activity that increase their inflexibility and dependencies. JIT favors short supply chains, which is why car manufacturers tend to rely on suppliers who are located immediately next to or a few hours’ drive from their assembly facilities. To address supply chain shortages, we should not point the finger at Lean Thinking, but find a way to design more flexible and resilient global supply chains.
My argument is not obvious. When consumers meet empty toilet paper shelves in the supermarket, one might be compelled to think that more inventory would fix the problem. Yet, this is not necessarily the right solution. Toilet paper is one thing, but consider complex products like ventilators and cars or fresh goods like milk and bread. Products made of many different parts would need to stock goods everywhere in the supply chain (you can have your cupboard full of sugar, but you won’t be able to make pancakes if you don’t have any eggs). Stocking up on all the components that are needed to ensure high inventories of these products would be extremely inefficient and costly. Not to mention unnecessary, considering that we already stock so much excess meat in our supply chains that one third of it ends up in a landfill.
Instead of thinking that the cause of shortages is that our inventory levels are too low, we should strive to produce faster and better adapt at shifts in demand. The world should be able to quickly produce what is needed when it is needed. This is exactly what JIT is about, and you can rest assured that this would effectively solve any shortages that might happen.
RETHINKING GLOBAL SUPPLY CHAINS
We have the global supply chains we have for a reason. Water always seeks the easiest path, and so does economic activity. In our globalized world, the “easiest path” for supply chains was moving production to low-cost locations, but that has nothing to do with Lean Thinking.
Should we blame globalization for the shortages, then? Absolutely not! Sure, it is true that globalization has made us dependent on global flows of individual parts that are often built on one side of the world and shipped across the planet to be assembled. It’s also painfully true that many of our supply chains have become long, intransparent, rigid and sluggish. While there is nothing lean about this either, blaming globalization is short-sighted. If it wasn’t for it, we wouldn’t even have many of these products – certainly not at the same price, with the same variety, and at the same quality level.
The world will not be the same after Covid-19. A good way forward is to rely on kaizen to continue improving the supply chains we have and on kaikaku to rethink manufacturing and supply chains altogether. For both, new digital technologies can be breakthrough enablers and, indeed, studies show that companies that had invested more in digital technologies did better during the pandemic than those that hadn’t. Technologies that build end-to-end transparency in supply chains will be of particular importance, as they can help us fulfill one of lean’s promises: delivering the product customers wants exactly when they want it. Lean Thinking has more to do with speed of production than it does inventory reduction. Embracing it means to develop the ability to efficiently and quickly manufacture to meet market demand. I see we need lean now more than ever!
THE AUTHOR
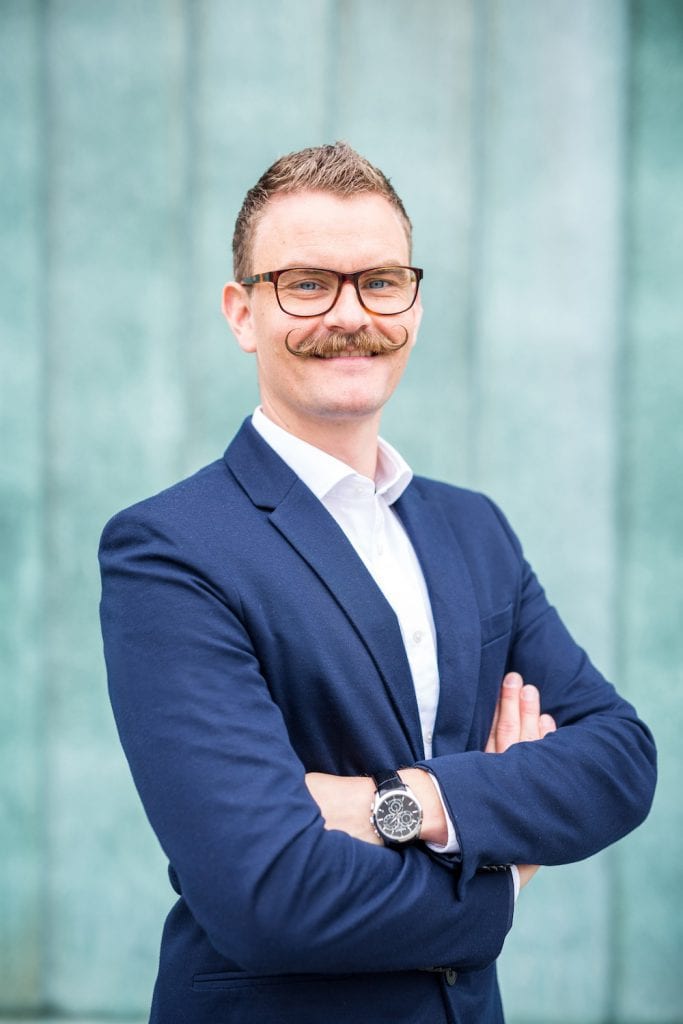
Torbjørn Netland is Professor of Production and Operations Management at ETH Zurich, Switzerland. He is double recipient of the prestigous Shingo Research Award and several teaching awards.
Read more
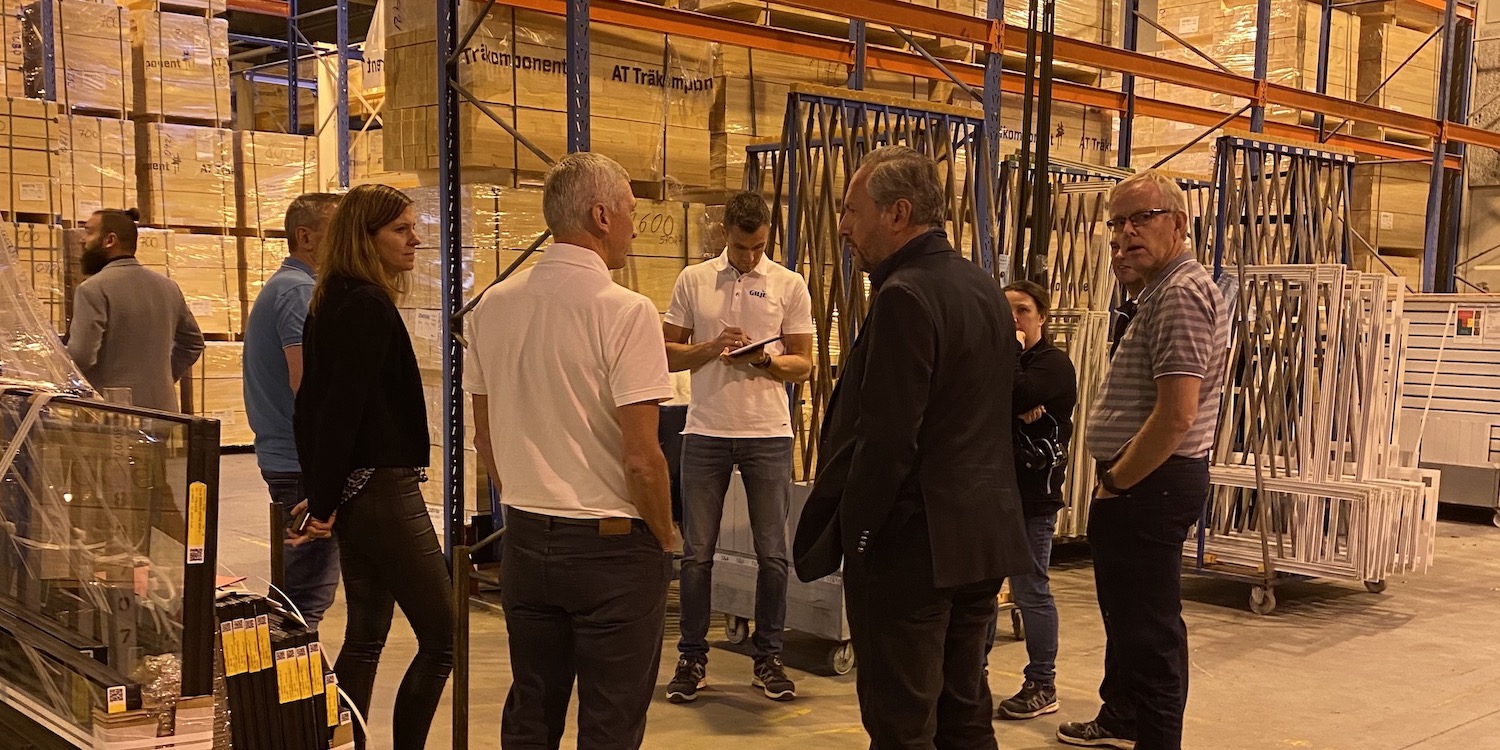
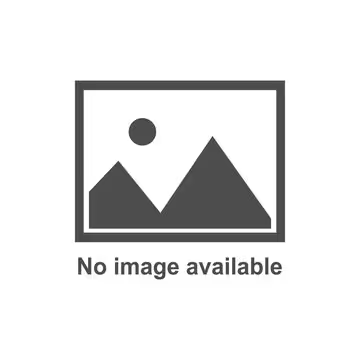
FEATURE – Fresh from a number of visits to Norwegian gemba, the authors share their reflections and discuss the importance of making the information flow visible.
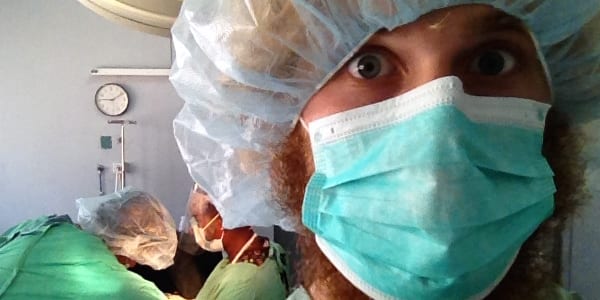
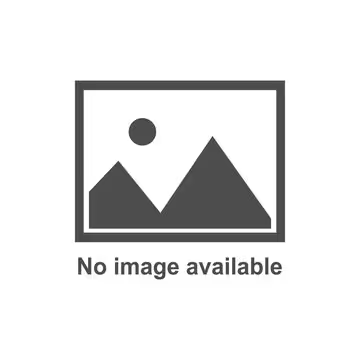
ARTICLE – While supporting the adoption of lean in a Mozambican hospital, a young engineer learned a number of valuable lessons on leadership and what it really takes to help developing countries to grow.
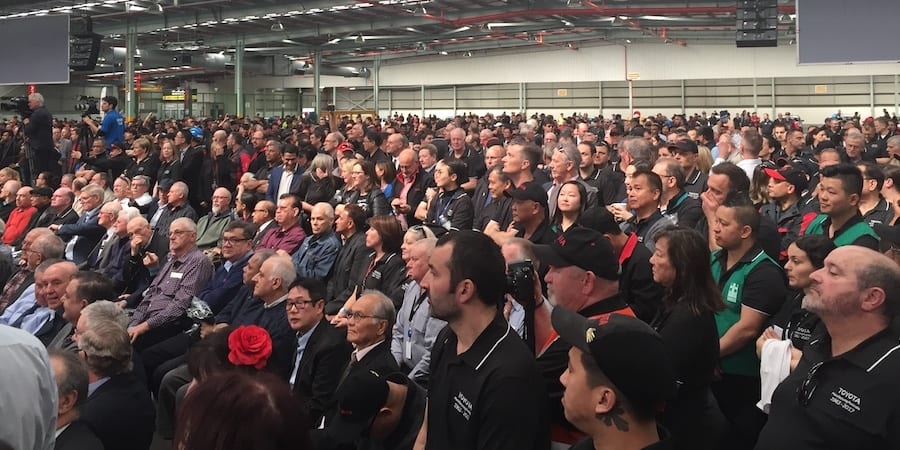
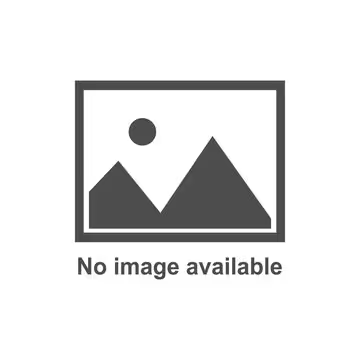
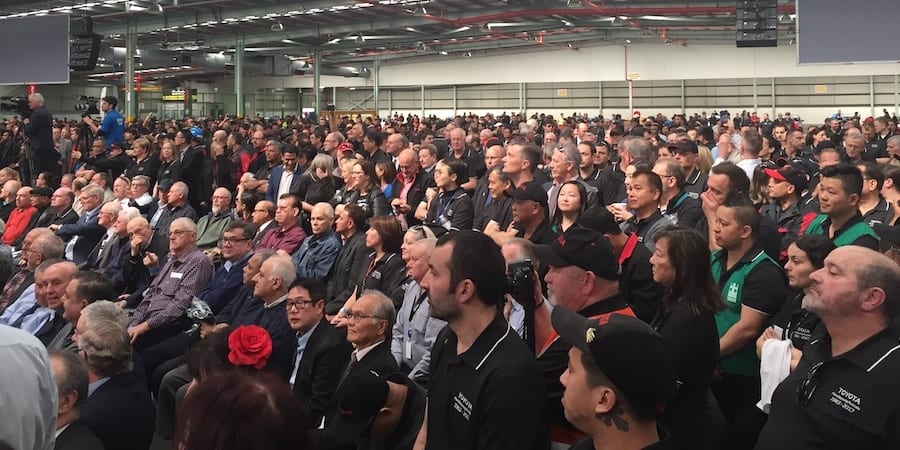
FEATURE – Last year’s shut-down of Toyota’s Altona plant in Australia moved us all. Here, the former Divisional Manager of Manufacturing offers a first-hand account of how the company made the most of a terrible situation.
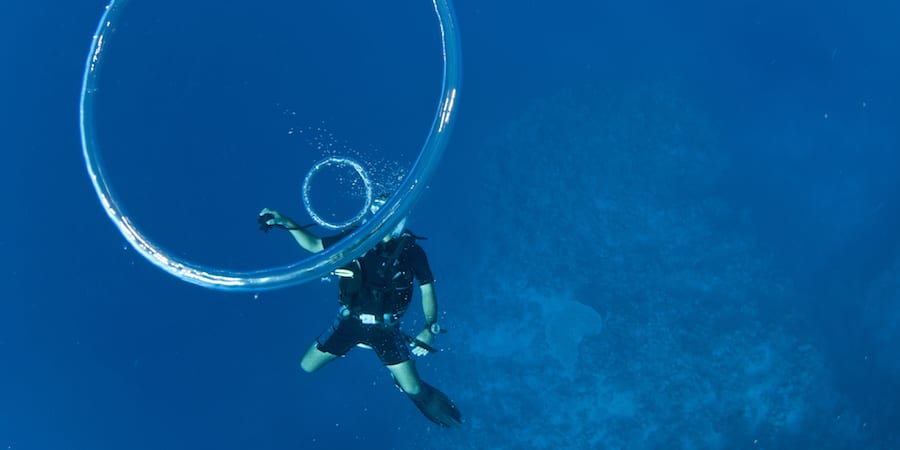
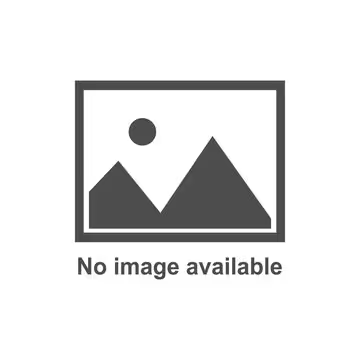
FEATURE – In lean, we talk about PDCA all the time… but do we actually practice it as we should? The authors discuss what makes for successful continuous improvement.