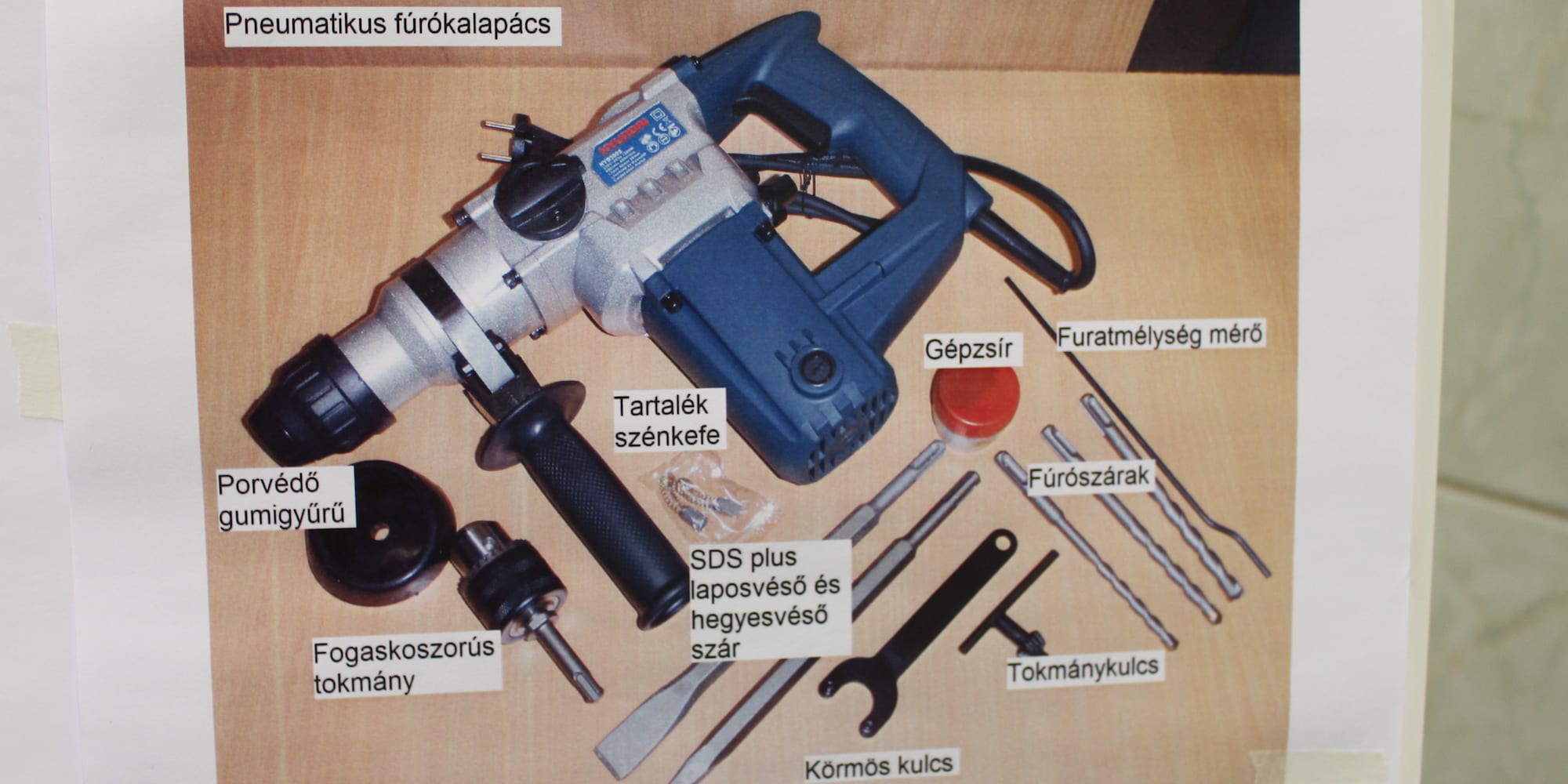
How we slashed waiting times for our customers
VIDEO INTERVIEW – A store manager explains how a simple kaizen reduced waiting times for customers who want to return products. We use today’s video to launch our Lean Improv contest.
Words: Zsolt Móczik, Deputy Store Manager, Praktiker Hungary
As a company, we want to make it easy for our customers to return products, should they wish to do so. So, when our transformation started, shortening the time it took them to return items quickly became a lean project at one of our stores in Budapest.
By observing the process, we realized that our Information Desk staff (those who in contact with customers returning products) wasn’t equipped to effectively and swiftly answer the query. They didn’t have the information they needed in order to make an informed decision on whether a product could be returned (if it’s been used, for instance, we don’t take it back), and as a resulted they used to rely on the salesperson from the area the product originally came from.
Not only did this mean a long wait for our customers, but also that our salespeople spent a staggering 51 days a year walking back and forth from their areas to the Information Desk, just to complete a process that other staff could have done… given the right information.
Take a look at this video to learn how we fixed the problem.
THE AUTHOR
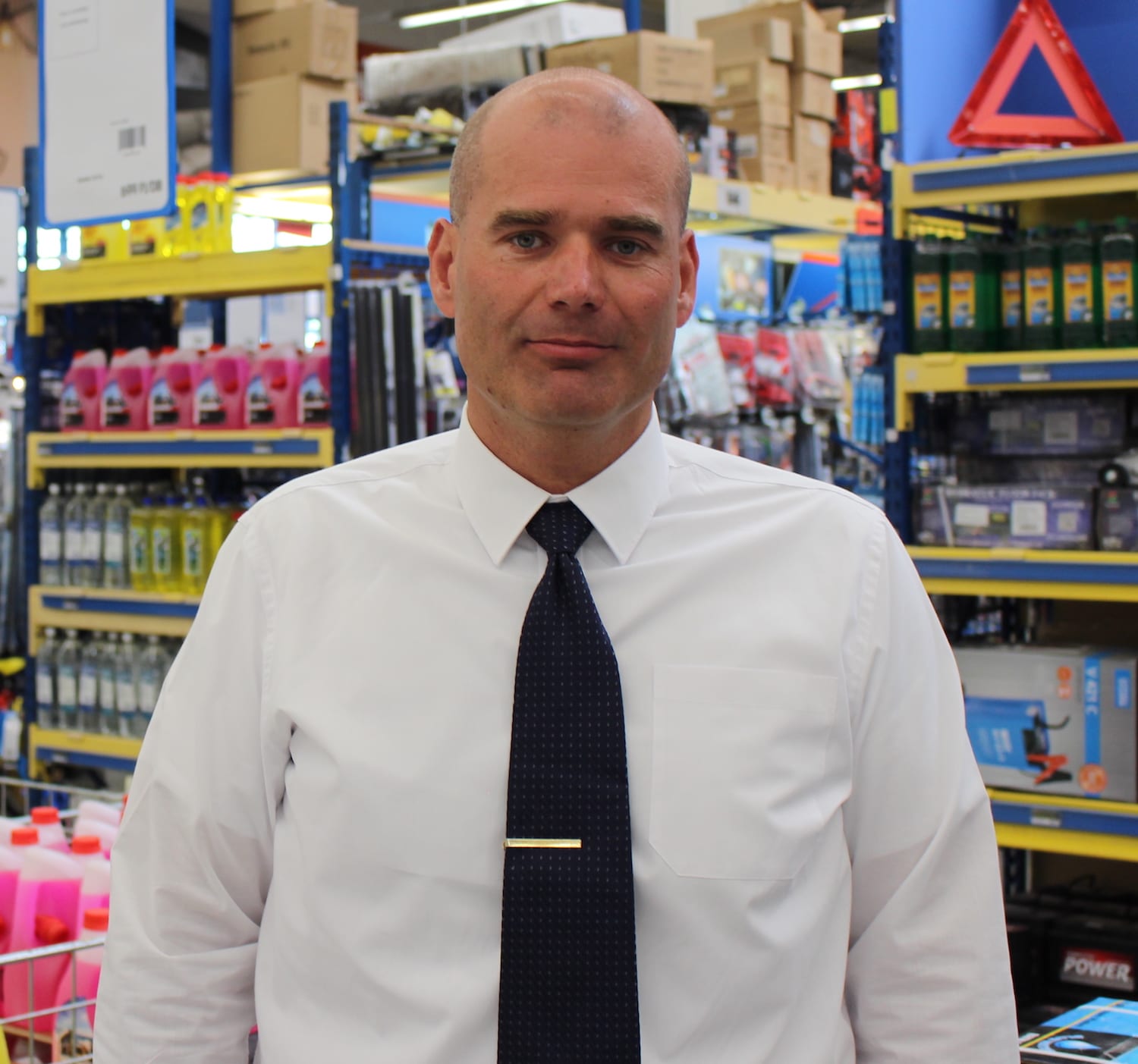
Read more
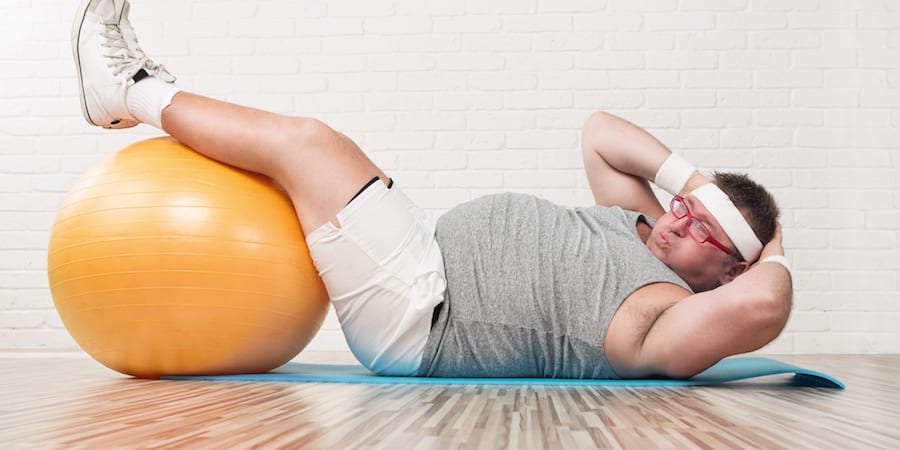
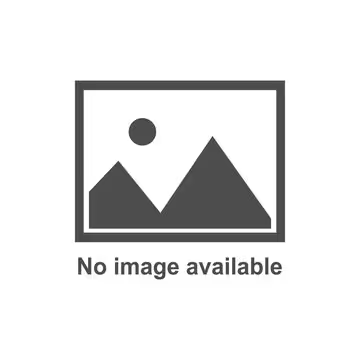
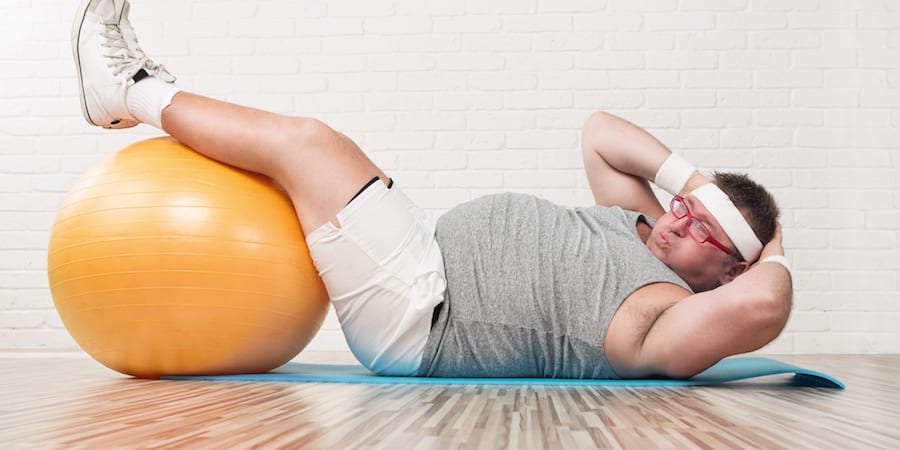
FEATURE – Just like a diet alone won't result in real fitness, cost cutting is in itself not enough to ensure an organization is healthy. Making our companies fit and sustaining results begin with building capabilities in our people and improving our processes.
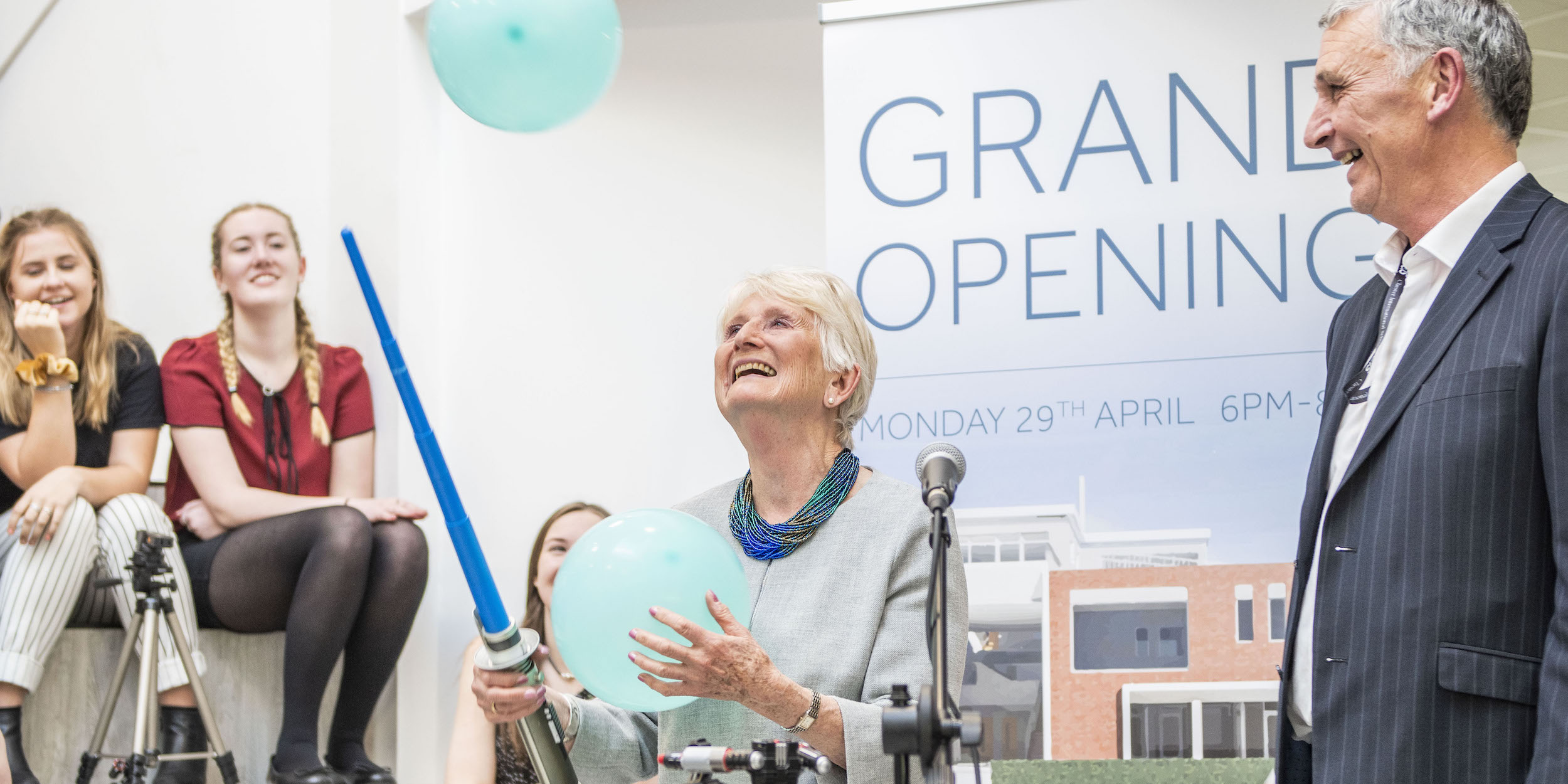
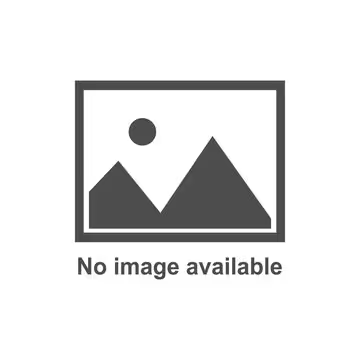
FEATURE – How does lean apply to learning? The author reflects on the lean transformation his schools are undergoing and on its practical implications on students, staff and leaders.
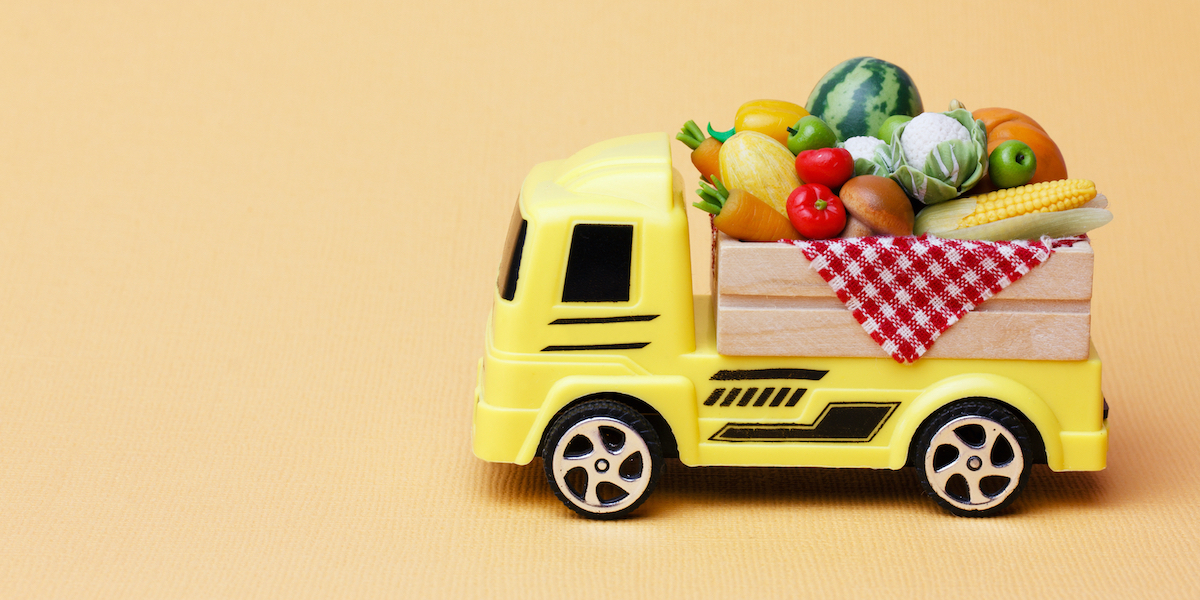
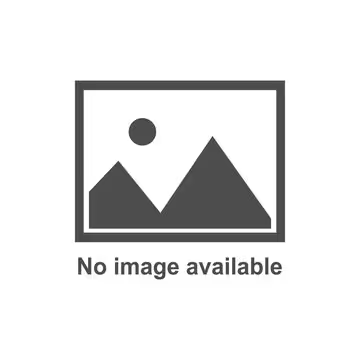
CASE STUDY – By streamlining its internal processes, an agribusiness company in Brazil managed to reduce its material handling cycle time by 75% and the associated costs by 66%.
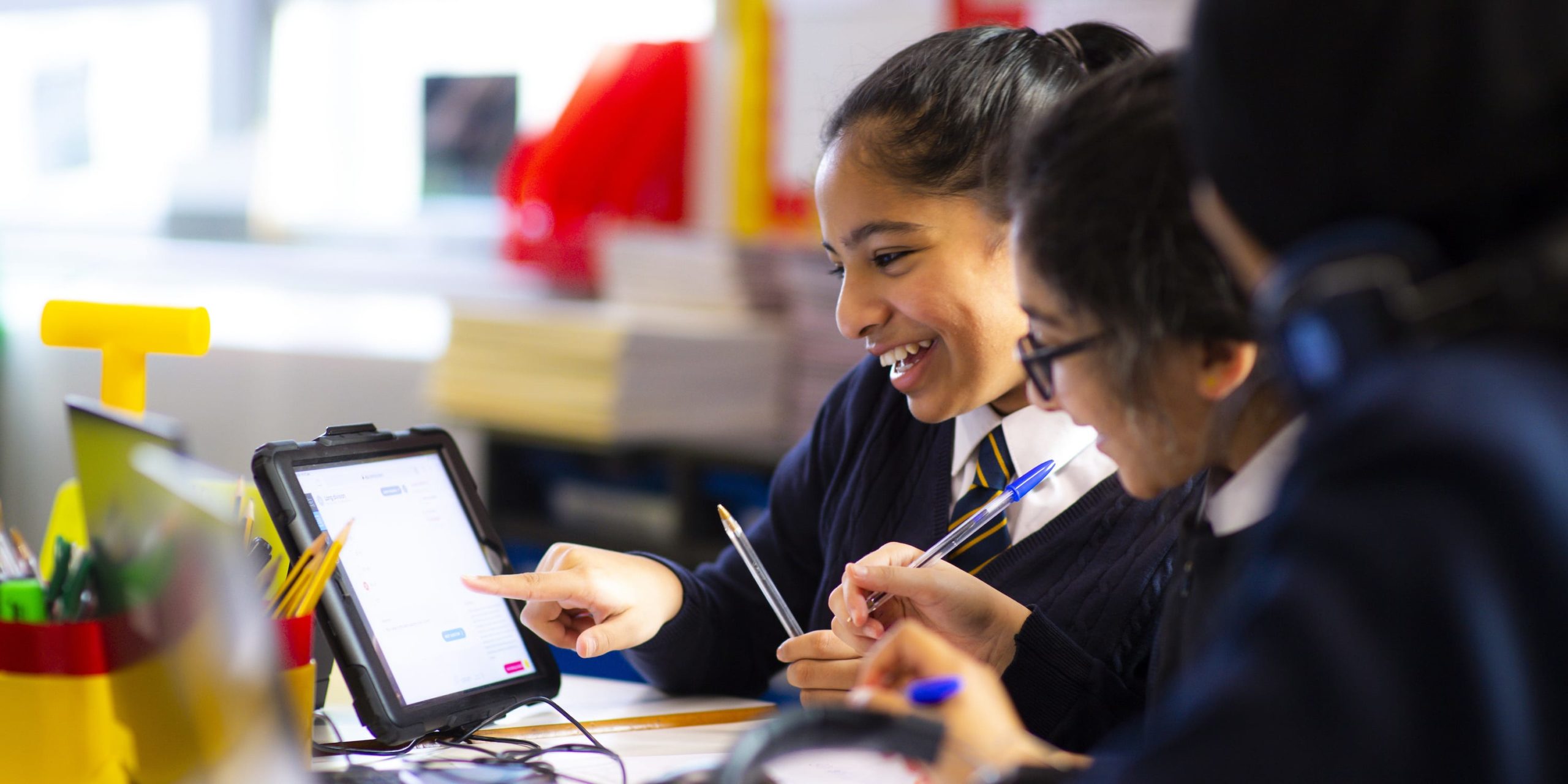
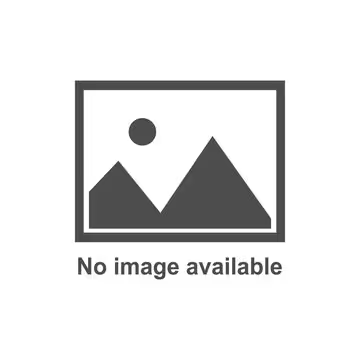
INTERVIEW – In a chat with our editor, Priya Lakhani explains how technology can be used to understand a student’s unique learning pathway and design teaching accordingly.