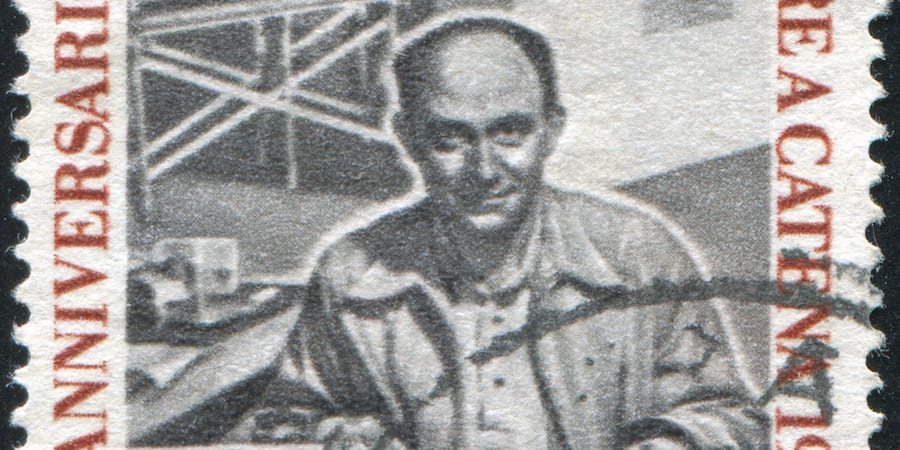
What lean thinking can learn from scientist Enrico Fermi
FEATURE - Italian physicist Enrico Fermi is one of history's greatest "lean scientists," who developed a revolutionary approach to research and mentoring from which lean managers can still draw inspiration.
Words: Arnaldo Camuffo, Professor of Lean Management, Bocconi University and President of Istituto Lean Management
Picture credit: rook76 / Shutterstock.com
Eight decades ago, between 1923 and 1937, a world-class research institute was created in Rome, Italy, almost from scratch. Leading the Physics Institute was physicist Enrico Fermi.
The institution where Fermi and a group of fellow scientists – known as the "Via Panisperna boys" – worked produced a number of extraordinarily large-scale results, which are still subject of reflection today. Among them, the discovery of slow neutrons, which then led to the creation of the world's first nuclear reactor (and, tragically, of the atomic bomb).
There is no doubt Enrico Fermi is one of the most renowned scientists of the 20th century. His revolutionary way of leading played a key role in the success of the Via Panisperna institute in those early years: in all respects, the research institution was an incredible example of a management system based on the principles and techniques typical of lean thinking, and more specifically of A3-based problem solving.
In 1926, Fermi became the first Professor of Theoretical Physics in Italy, supported in his work by a number of brilliant researchers who then went on to become top scholars (Fermi himself was awarded the Nobel Prize for Physics for his discovery of slow neutrons).
Once in the chair, Fermi revolutionized research and teaching activities, inextricably joining the two. He broke with the traditional methods of work, based on hierarchy and individual logic, and with the tradition of old mathematical physics. The style became informal, with no status distinctions. Rasetti, one of the researchers who worked with Fermi, described it thus: "There was no formality in the way in which Fermi taught us the latest physics theories, first among them the new quantum mechanics [...] Meetings were never routine, they were a sort of daily seminar, on topics driven by the research issues we needed to solve, or by some experimental result we had obtained which had to be interpreted, or by a problem that Fermi was studying and either had resolved or was trying to resolve [...] In any case, Fermi proceeded to explain the calculations he was writing on the blackboard with his constant, unhurried pace, neither accelerating in the easy steps nor slowing down noticeably before difficulties [...] Often we could not tell at the moment whether Fermi was expounding theories already well known to him or others, or whether we were witnessing a new step that he was taking at the confines between the known and the unknown. Many times we saw a new theory born, which Fermi developed while, you might say, he was thinking aloud."
More than just being the Director of the Institute (the manager, we would say in business language), Fermi embraced his role as a teacher not only during lectures and seminars, but also in laboratory activities. Rasetti also recalled that Fermi especially loved alternating between these two types of activities – accomplishing the highest results in both – a rare occurrence in the history of physics. Rasetti continued, "Fermi participated in the experiments and in the theoretical interpretation of the results. [...] In formulating theories, he utilized whatever means would take him most directly to the result, resorting to his mastery of analytical means if this was called for, otherwise turning to numerical calculations, heedless of mathematical elegance."
Some of the students also recalled that when the mechanical parts or electrical circuits of the Institute facilities were inadequate, Fermi did not disdain from going to the workshop to fabricate himself what was needed, not going after extreme precision but ensuring the parts were good enough to enable measurements with a reasonable level of experimental error.
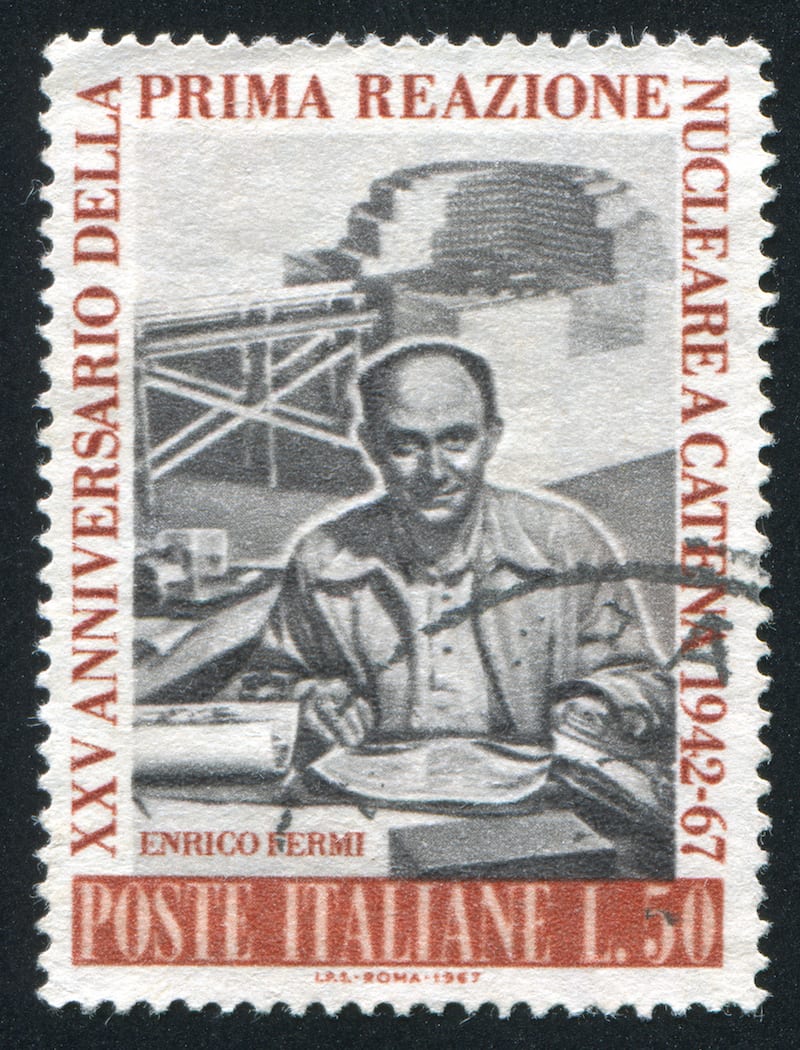
Fermi created a new way of conducting research and teaching, managing complex projects while at same time allowing the people who worked with him to grow. He subsequently exported this method to the United States when he moved to Chicago. One of his American students, Chen Ning Yang, also a Nobel laureate, said, "Fermi gave extremely lucid lectures. In a fashion that is characteristic of him, for each topic he always started from the beginning, treated simple examples, and avoided as much as possible 'formalisms.' [...] The simplicity of his reasoning conveyed the impression of effortlessness. But this impression was false: the simplicity was the result of careful preparation and of deliberate weighing of different alternatives of presentation. [...] It was Fermi's habit to give, once or twice a week, informal unprepared lectures to a small group of graduate students. The group gathered in his office and someone, either Fermi himself or one of the students, would propose a specific topic for discussion. Fermi would search through his carefully indexed notebooks to find his notes on the topic and would then present it to us. [...] The emphasis was always on the essential and practical art of the topic; the approach was almost always intuitive and geometrical rather than analytic."
The foundations of A3 problem solving (and of lean) lie in scientific thinking, which is why Fermi's approach to research and mentoring greatly resonates with lean practitioners. John Shook, CEO of the Lean Enterprise Institute, commented: "Not only did Enrico Fermi unlock the secrets of the atom – one of the most important discoveries in history – he was also a hands-on scientist who tested complex theories with practical experiments run on apparatus that he built with his own hands. What we know of him as a teacher and mentor also was exemplary of the best lean teaching and mentoring."
Fermi's way of thinking can be used as a model for those managers who have the ambition, courage and confidence to start or keep transforming their organizations:
- Adopt lean tools that enable the shared and common application of a structured problem solving approach based on the scientific method
- Exercise leadership based not on the principle of authority but on that of responsibility
- Have respect for people and be willing to listen and learn from others
- Operate through direct observation and involvement in problem solving at the operational level (gemba)
- Manage by teaching and teach by managing (managing to learn) using the Socratic method (providing mainly questions, not answers)
- Make decisions and take actions based on direct experience and on critical exercise and not based on assumptions or on models or numbers
- Convey enthusiasm for teamwork aimed at continuous improvement
- Maintain modesty and humility.
THE AUTHOR
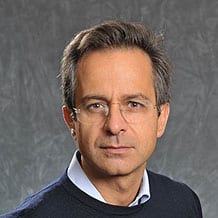
Arnaldo Camuffo is President of the Istituto Lean Management in Italy. He also teaches Lean Management at Milan's Bocconi University.
Read more
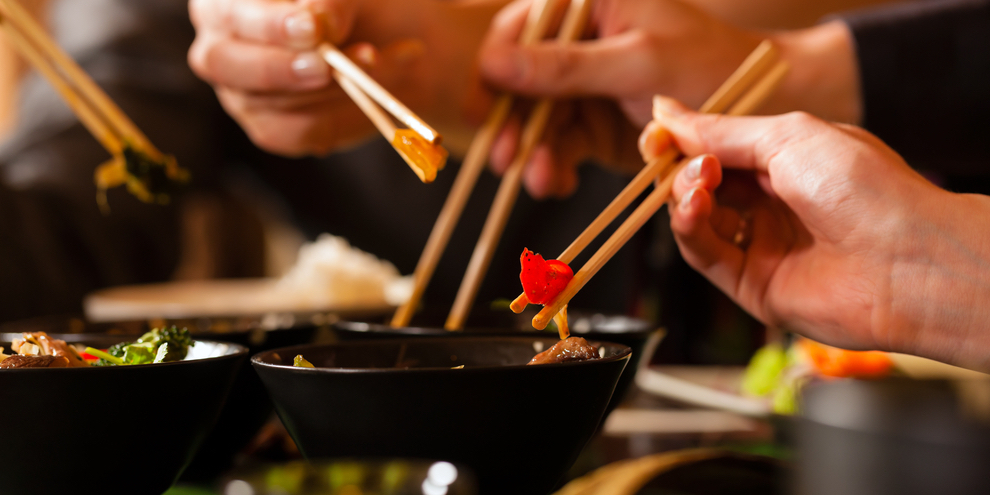
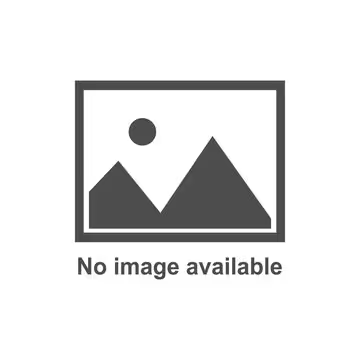
FEATURE – The food industry is mired with problems all along the value chain. In this call to arms, the author explains why lean thinking is the only tool we have to transform it right now.
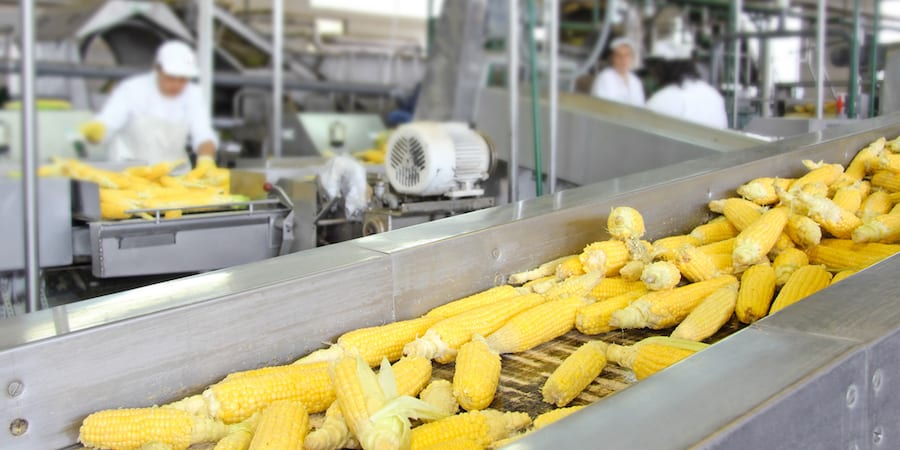
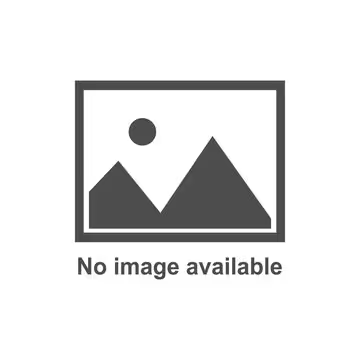
FEATURE – If we have high-volume (green) and low-volume (red) items in our production schedule, doesn’t it make sense to also have dedicated green and red equipment whenever possible?
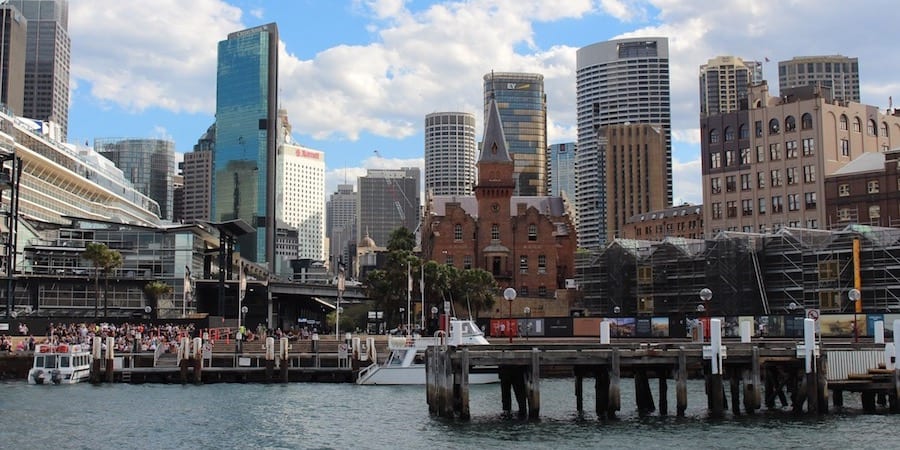
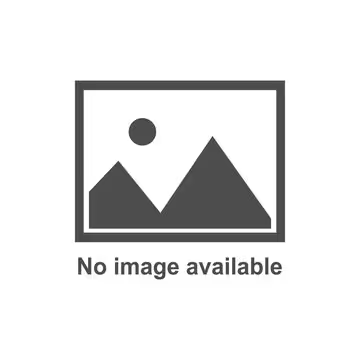
INTERVIEW – With the closure of Toyota’s operations in Altona, the land Down Under is left without its lean poster child. Alister Lee tells us who the community there should look to next.
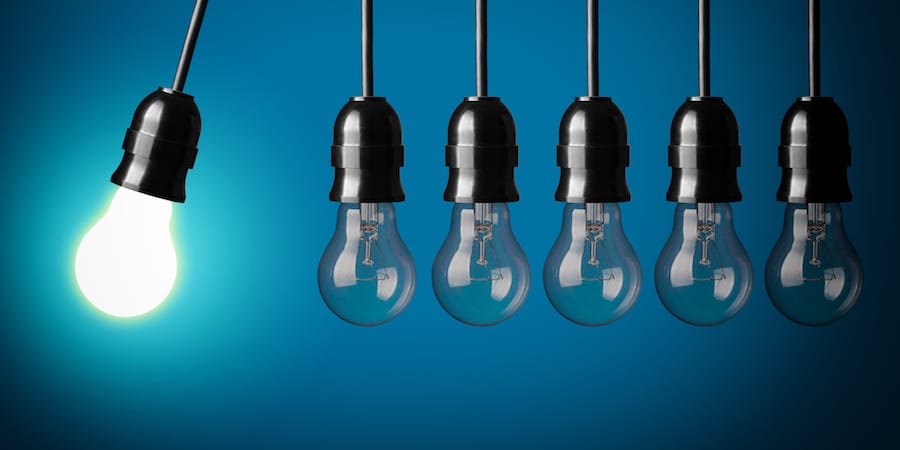
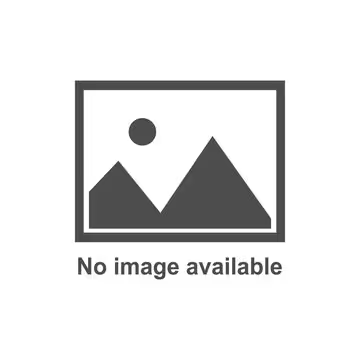
ONE QUESTION, FIVE ANSWERS – Inspiration can help us solve a problem, get our colleagues interested in lean, or even pick ourselves up after a failure. But where do we get it from? We asked five practitioners.