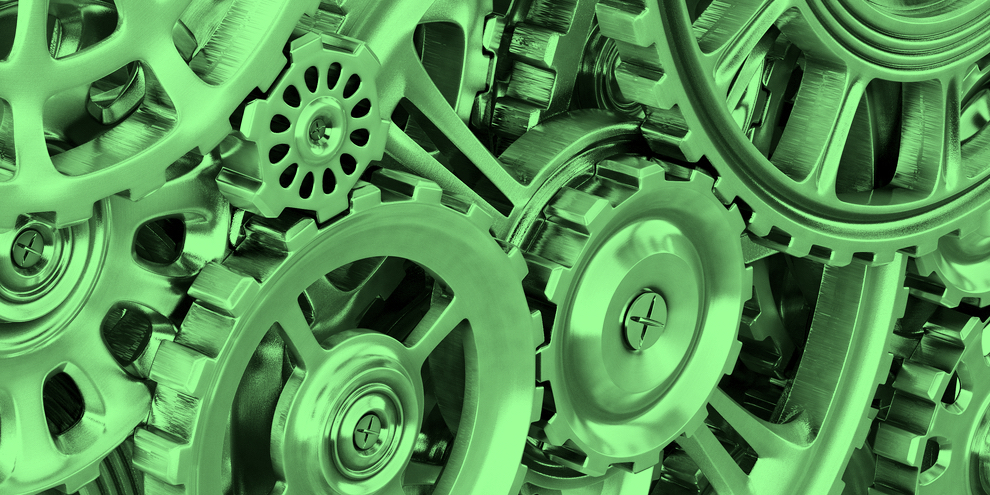
What pull system is right for you?
FEATURE – In the third article in his series, Christoph Roser provides a practical guide to understand the most adequate pull system to your circumstances.
Words: Christoph Roser
In my last two posts I showed you different types of pull systems and offered an overview of the criteria you need to consider when deciding which one is right for you. In this article, I finally give you a hands-on guide to decide which pull system to use.
First, let me share an (admittedly very personal) evaluation of the different pull systems and how they fare with different requirements. In the image below, I summarize which type of pull system is compatible with make-to-stock, make-to-order, ship-to-stock, ship-to-order, and flow shops or job shops, as well as truly continuous processing of bulk materials. Please note that any kind of kanban and reorder systems is fundamentally incompatible with make-to-order. Also note that if you are shipping items based on a customer order, you do not really need a pull system; you merely need to ship the items so they arrive on time.
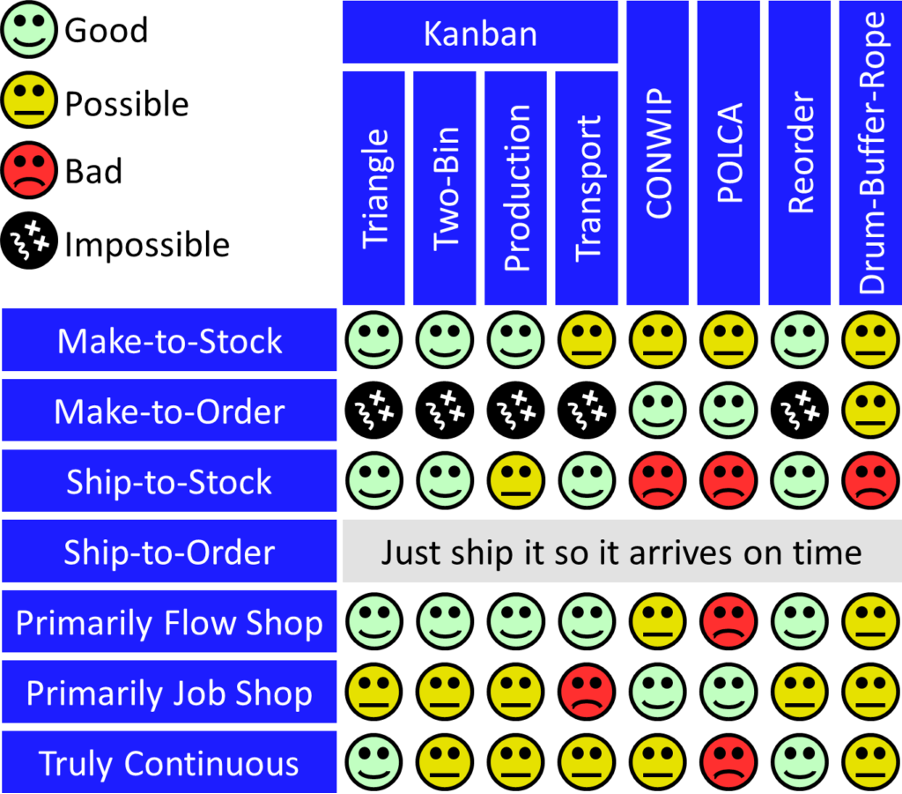
PULL SYSTEM SELECTION DECISION TREE FOR MANUFACTURING
To help you in your decision on which pull system to use, I have created decision trees. Please be aware that, while the recommended systems are all feasible options, they include assumptions and generalizations. To make these options easier to analyze, I have split them into two decision trees.
The first decision tree looks at production or development. If you produce make-to-stock, your best choice is usually a variant of kanban. If you produce make-to-order, you have the choice between CONWIP and POLCA. POLCA is a bit better in controlling the inventory, but is more cumbersome to implement and maintain. POLCA is also not designed for flow lines, but for job shops and networks of cells. CONWIP is easier to implement and maintain, but doesn’t control the inventory in a job shop as nicely.

If you have a mixed system, you will need to choose two separate systems for the make-to-stock and the make-to-order items. Here, I recommend a combination of kanban and CONWIP.
Most systems are well suited for discrete production, where a card represents a fixed quantity. Even with continuous production, either the production or the sale is often in fixed quantities. However, with a truly continuous production, you cannot use cards for a fixed quantity of items. Here, it may be best to use reorder points for make-to-stock or CONWIP for make-to-order. However, many other systems can be adapted to continuous production with varying effort.
If you are producing make-to-stock, you have a few more decisions to make. First, if you are in the unfortunate situation of having to produce make-to-stock in a job shop, see if you can turn the job shop into a flow shop. If not, select a flow shop type pull system, although in that case you may also have to take care of the routing of the items within the job shop.
If you produce make-to-stock in a flow shop, you can now fine-tune the system. If the demand is low and the demand during replenishment is consistently less than the content of a single container, then you may only need a two-bin system (this is a kanban system with only two cards).
If the demand is higher, you may look at the value and size of the items. If they are a bit expensive or bulky, use a normal kanban system with production and transport kanban to minimize inventory and minimize tied-up capital and/or storage space.
If the items are very small and cheap, you may use a triangle kanban to reduce the number of times you have to produce, although you may still choose a normal kanban to create smaller lot sizes and improve leveling.
PULL SYSTEM SELECTION DECISION TREE FOR PURCHASING
The decision tree is easier for purchasing. If you ship-to-order, you do not need a pull system at all. You just order all the items you need so they arrive on time when you need them. If the items are needed for your own production, the pull system of the production will decide when to produce what and your ship-to-order items are derived from this make-to-order production system. Since you cannot produce before the parts arrive, the delivery times are part of the overall lead-time for the customer order.
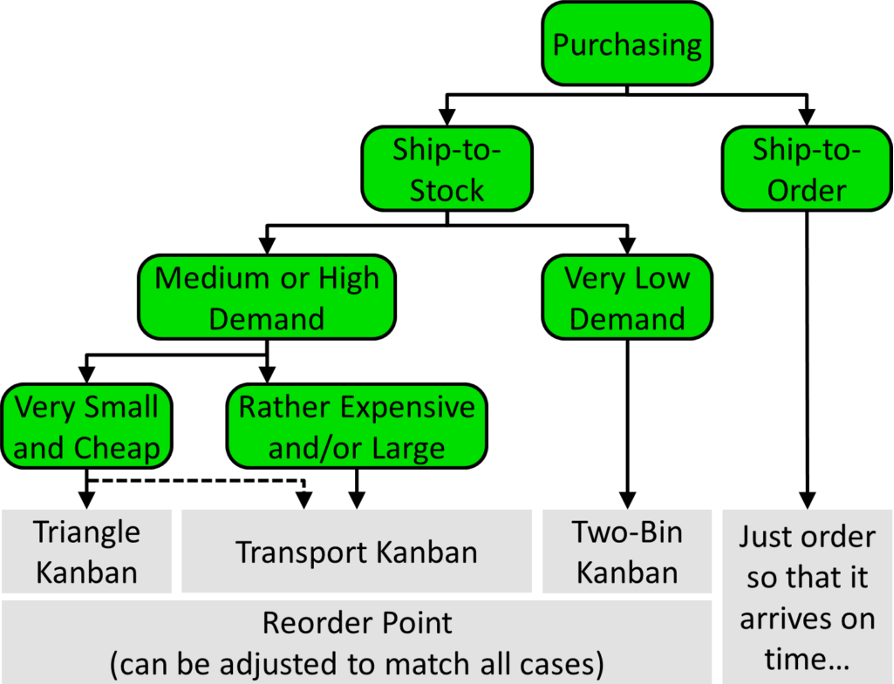
If you order items to be on stock (ship-to-stock), the decision tree is similar to the make-to-order flow shops. If demand is very low, make sure you always have at least two items or batches. If one is consumed, order one more while the second item or batch ensures material availability.
If the demand is higher, you may use triangle kanban for very cheap and very small items, and transport kanban for larger or more expensive items. This is similar to the make-to-stock production. For all ship-to-stock methods, reorder systems are a valid alternative, as you can adjust the reorder points and reorder quantities to achieve a wide range of behaviors similar to the different kanban systems.
WHAT ABOUT DRUM-BUFFER-ROPE AND COBACABANA?
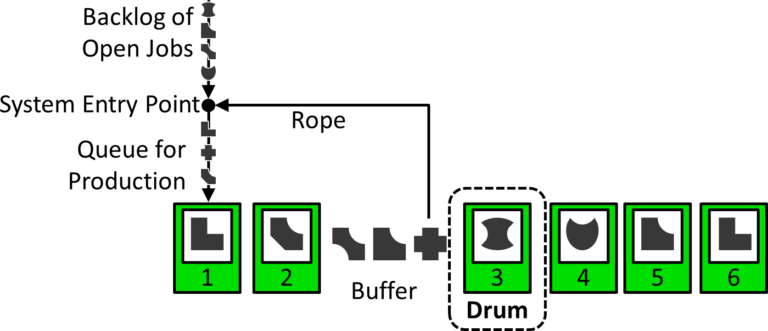
You may wonder which decisions you have to make to get to Drum-Buffer-Rope, as none of the above decisions end up there. In my view, Drum-Buffer-Rope is mostly inferior to kanban and CONWIP systems. It requires the pull loop to end before the bottleneck, which I consider to be a completely unnecessary restriction. If you ignore the restriction of the loop ending at the bottleneck, the system is actually very similar to CONWIP and quite workable.
There are real-world production systems that successfully use Drum-Buffer-Rope. Hence, if your plant successfully uses it, has people skilled in it, and the method has the support of your people, keep using it. There is value in anything that works. Just don’t artificially constrict yourself to end the loops at the bottleneck. If you have not yet done Drum-Buffer-Rope, however, I recommend that you stick to kanban and CONWIP systems. I also advise against COBACABANA, as it is complicated and untested in reality. Now, go out, set up a good pull system for your products, and organize your work!
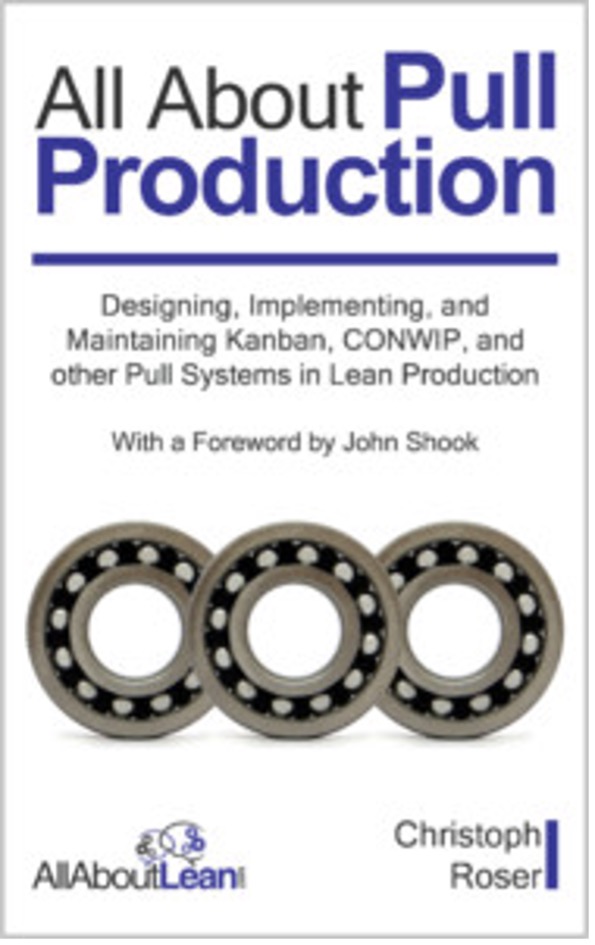
This article, originally published on All About Lean, is loosely based on Christoph’s new book All About Pull Production: Designing, Implementing, and Maintaining Kanban, CONWIP, and other Pull Systems in Lean Production, a practical guide for anyone looking to implement pull systems.
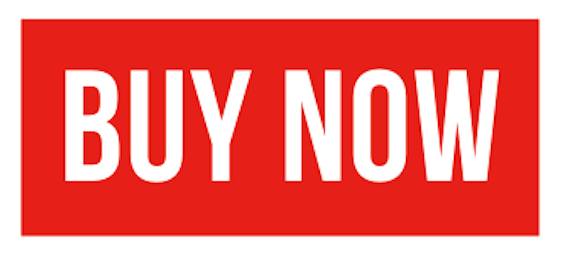
THE AUTHOR
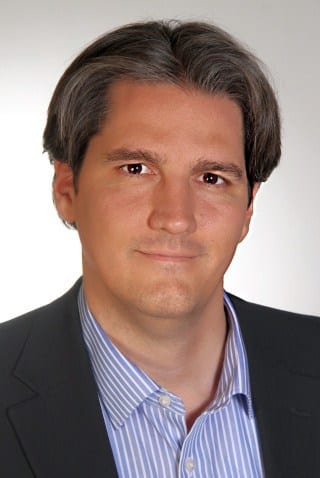
Christoph Roser is Professor of Production Management at the Karlsruhe University of Applied Sciences. He writes based on decades of experience in implementing, researching, and teaching lean manufacturing, including five years working at and researching for Toyota in Japan.
Read more
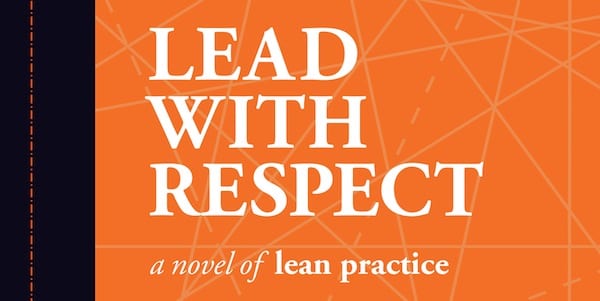
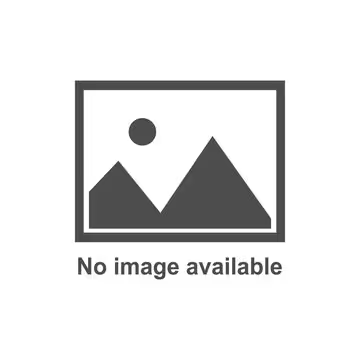
REVIEW - Michael and Freddy Ballé’s new novel, which came out this week, will help readers to understand what it really means to be a lean leader and respect people.

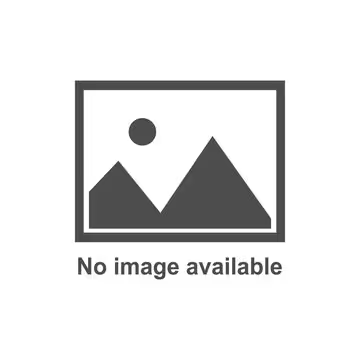
INTERVIEW – If we truly believe lean can change society, then we should use it as a lens through which to look into different aspects of our lives – even when those associations are hard to make. This month, we discuss the world of media.
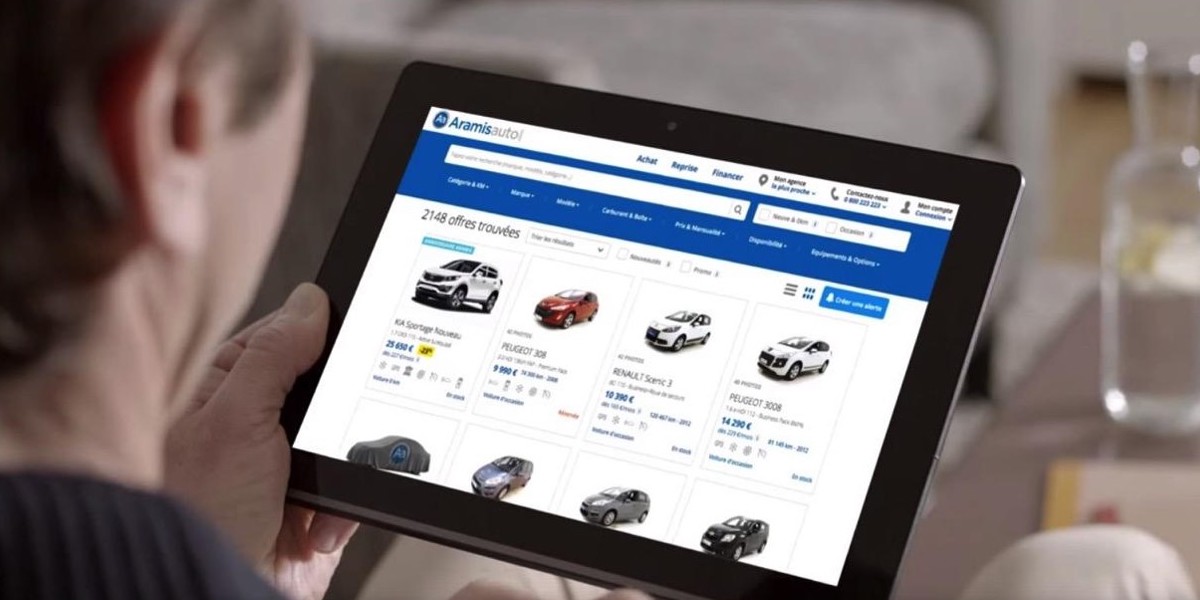
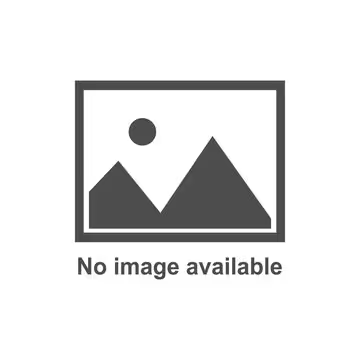
NOTES FROM THE (VIRTUAL) GEMBA – Throughout the lockdown, this car-selling business has never lost its focus on people development. The author learns how this approach is helping the firm make the most of the crisis.
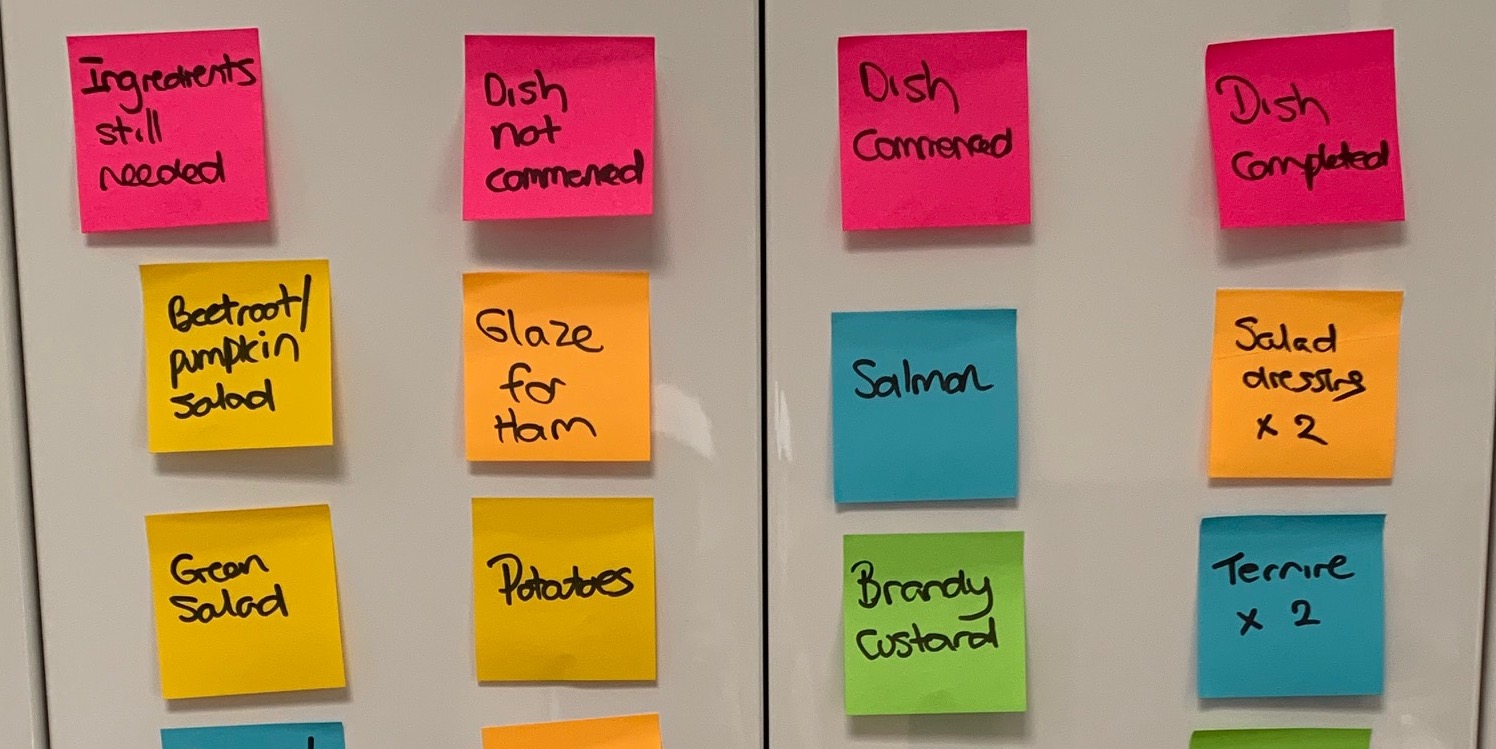
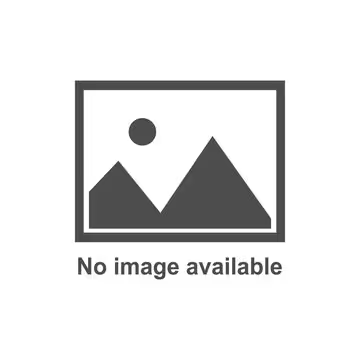
FEATURE – The holidays are a time for reflection. The author shares some her reflections on her experience with lean thinking and the role of leadership in a lean transformation.